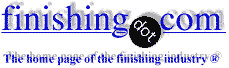
-----
CED coating has pinholes
Quickstart:
"CED" stands for 'cathodic electrodeposition', and means electropainting/electrocoating/e-coating. It involves immersing the article into a tank full of something which is sort of like paint but isn't quite paint yet. When the parts are made cathodic (connected to the negative side of a DC current) the electricity converts the solution which is touching the part into paint.
There are other steps required including pre-cleaning and curing, but the heart of the matter is that the electricity converts the solution into paint, which is an insulator, so the electricity then goes to any uncoated area instead of the paint building up. The result is a very thin paint with outstanding evenness of coverage.
While CED can be used as a final decorative finish (in which case people may call it "electrophoretic lacquer"), the most common use is as a primer. Almost all automobile chassis are primed this way.
Q. HI every one, and anybody support to me because I'm in working of CED PAINT SHOP. I want to learn and improve myself. I'm not fully learned but am needing to learn. Anyone have an idea help to me? And I need some documents of CED. (ex.: PT LINE, CHEMICAL REACTION NAME, AND WHICH TANK WHICH REACTION, AND ED LINE ALSO, Trouble shooting ALSO) ANY ONE INTERESTED GIVE THE DOCUMENT SIR.
Ajith Kumar Remployee - Anthra pradesh
April 5, 2025
for Shops, Specifiers, & Engineers
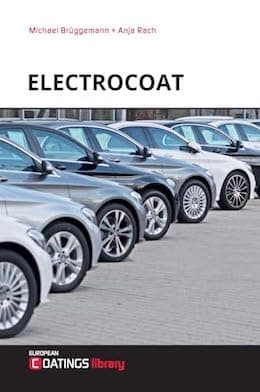
avail from eBay, AbeBooks, or Amazon
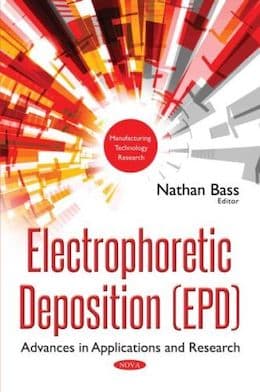
avail from eBay, AbeBooks, or Amazon
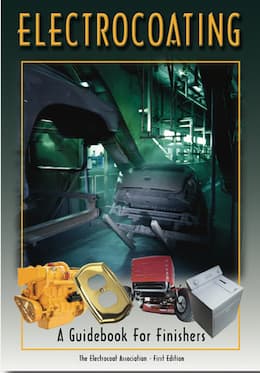
avail from AbeBooks, or Amazon
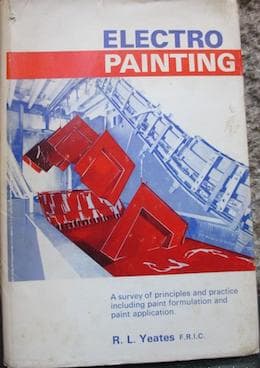
avail from eBay, AbeBooks, or Amazon
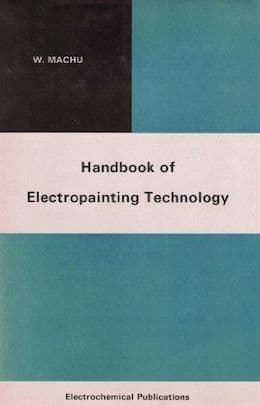
avail from eBay, AbeBooks, or Amazon
(as an Amazon Associate & eBay Partner, we earn from qualifying purchases)
A. Hi Ajith. If you have specific questions, I think people will answer them. If you just want to learn about it in general you can search the site with the search term "CED" and you'll see dozens (nearly a hundred) detailed discussions on various aspects of the process here.
But realistically, it can be difficult and inefficient to try to learn by bouncing around between aspects you already have read about a dozen times, and stuff you can't yet understand because you haven't yet learned the background stuff it assumes you know. So, when you are looking for general tutoring, there really is no good alternative to a book on the subject. The author spends months or years trying to make sure it is presented in the most understandable, tutorial fashion possible 🙂
At least one of these ⇨
will surely be available in a local public or university library.
Luck & Regards,
Ted Mooney, P.E. RET
Striving to live Aloha
(Ted is available for instant or longterm help)
finishing.com - Pine Beach, New Jersey
⇩ Related postings, oldest first ⇩
Q. I am a job CED coater. Recently a Zinc plated job has come to me for coating. After coating, all jobs were rejected due to PIN HOLE problem.
Can you help me?
Plating shop employee - Nasik, Maharashtra, INDIA
June 21, 2011
A. CED Can be done on hexavalent yellow passivated part. If it is as-plated or trivalent passivated, carry out tricationic phosphating, then go for CED Coating.
Nithin reddy- Bangalore, India
Q. Phosphating Zn plated part in my bath will lead to increase in Zn content in it. Won't that matter?
Avinash Vidhate [returning]- Nasik, Maharashtra, INDIA
Hi Avinash. Nithin suggests tri-cationic phosphating unless you are hexavalent chromating. You need to either chromate or phosphate, you shouldn't try to CED coat bare zinc. Thanks!
Luck & Regards,
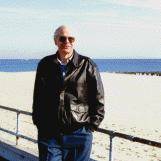
Ted Mooney, P.E.
Striving to live Aloha
(Ted is available for instant or longterm help)
finishing.com - Pine Beach, New Jersey
Pin holes on e-coat bottom surface
Q. Hi Sir,
I'm an employee of a plating house. Recently my company newly fabricated a 2.5 tonne e-coat tank to relieve some production capacity. Unfortunately, every model going through e-coat surely will have plenty of pin holes at bottom surface. Please be kind enough to give me some idea what setting has gone wrong in my tank. Thanks.
plating shop employee - Ulu Tiram, Johor, Malaysia
August 16, 2011
A. Maybe it's the angle from which the photo was taken... but I can't see a weir to remove the surface foam being produced by the coating process?
Terry HicklingBirmingham, United Kingdom
A. Bubbles on top of coating bath. You need a weir box to roll the top of the tank to. You also need to determine where the air bubbles are coming from.
Adam Adkisson- Mission Texas
A. Bubbles can be produced by cavitation in the main tanks pumping system.
Where a side tank is used for both collection of the e-coat tanks surface bubbles and the addition and mixing of new tank material, a bubble producing problem is possible if the weir shoot tank is:
a) Too small.
b) The rpm of the internal mixing system (normally a stirrer) is too fast.
c) Blades of stirrer are too low.
Birmingham, United Kingdom
Q. The foam issue is already resolved, mainly due to circulation pump choked by some cleaning cloth. However, the problem I'm facing is some pinholes due to gassing at bottom surface of raw parts.
Parameter of ED in spec; just pH slightly acidic (pH 4.5 - 5.0). What I'm curious is just whether tank either circulation is not enough or maybe in tank setting something has been neglected ... Maybe I'm wrong, kindly advise any eval'n that I can find out more.
Thanks
- plating shop employee - Ulu Tiram, Johor, Malaysia
August 23, 2011
A. Most important to avoid pitting at the bottom - clearance of work piece to bottom sparger pipes should be minimum 200 mm!
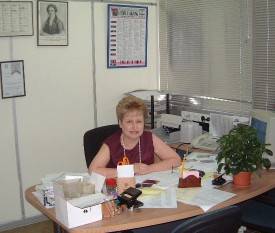

Sara Michaeli
Tel-Aviv-Yafo, Israel
A. Hi KC.
I once had the opportunity to look at an ED film (40X, I think) before the curing process and 'lo and behold ', they were full of pin holes! It is only through the curing process, the higher temperature makes the film more 'fluid', those pin holes were closed up, so to speak.
It may be possible your pin holes problem are curing oven-related rather than ED tank-related?
- Penang, Malaysia
A. First ensure that all the bath parameters are within specification and pH meter, Current-voltage meters are working properly.
Pinholes at the bottom of tank may be due to excessive gassing, i.e., due to high current density which further may be due to high solids content or suspended particles or too low pH.
Also, get solvent content tested by your paint supplier.
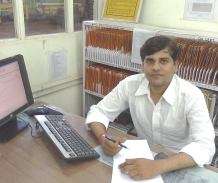
Manoj Kushwaha
plating & painting - Rampur, India
A. Check your solvent (BC) content. If it is on higher side it will definitely create pin holes. Check also ramp up time for rectifier voltage.
Manish Dhyani- Noida, India
? Kindly provide details of your pre-treatment process that is done prior to E-coat.
Have you checked the component after pre-treatment and before E-coat for presence of oil on its surface?
Mohali, Punjab, India
February 1, 2012
Hi Folks,
Thanks for your advice. I already went through all recommendations but it was not root cause. Thereafter, I changed existing circulation pump from Vertical to horizontal centrifugal type. Surprisingly, it resolved all those pin hole defects.
Anyway, thanks for ideas from all.
Regards
- Ulu Tiram, Johor, Malaysia
March 21, 2012
[editor appended this entry to this thread which already addresses it in lieu of spawning a duplicative thread]
Q. We have pinholes after applying the electrodeposition coat.
We think we have a problem in the activation process in pretreatment line. Please guide me.
Thanks
- Tehran, Iran
June 18, 2012
[editor appended this entry to this thread which already addresses it in lieu of spawning a duplicative thread]
Q. How to Solve Pin holes in CED paint plant. Please give detailed answer.
- Chennai, India
July 14, 2012
A. Hi Ashena, hi Senthil.
As you see, we attached your inquiries to a thread which already addresses the issue, hopefully helping you. If you wish to offer details which make your situation different than the previously posted ones, please do. Thanks!
Regards,
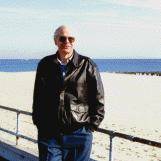
Ted Mooney, P.E.
Striving to live Aloha
(Ted is available for instant or longterm help)
finishing.com - Pine Beach, New Jersey
Q. Dear sir,
I am working as an Automotive CED Paint plant. In our plant daily pinhole, crater and white dot issues observed after oven; every day more rejections -- all parameters are within spec. So please give some ideas to resolve this issue.
- Chennai, India
November 16, 2012
Hi again cousin Senthil. 8 readers did previously offer specific suggestions on what needs double-checking. Please try to respond directly to those postings and you'll hopefully get a response and start making progress. Thank you!
Luck & Regards,
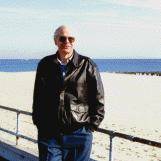
Ted Mooney, P.E.
Striving to live Aloha
(Ted is available for instant or longterm help)
finishing.com - Pine Beach, New Jersey
Q. I am working as line chemist of PT [pretreatment] and CED line. I have some problems after maintaining PT line.
Sir, please see and tell what is the problem and resolution. In this company we do coating of PT and CED on tractor spare parts.
paint shop - Panchkula haryana India
December 29, 2015
? Hi Virender. Is that a semicircular brown rust spot at 8:00 o'clock where the recessed diameter meets the ID of the flange or is it just a quirk of the lighting that makes it look like rust? If it is a rust spot, the pretreatment system needs to offer a properly prepared surface first. What is the substrate and the pretreatment please? Thanks!
Luck & Regards,
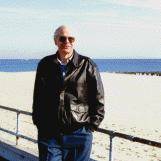
Ted Mooney, P.E.
Striving to live Aloha
(Ted is available for instant or longterm help)
finishing.com - Pine Beach, New Jersey
Q. Sir, I am working in paint shop which is doing PT and CED line of tractor spare parts. I am a line chemist. Images of rejected components:
But my question is not clear. Tell me what is name of problems, cause and action plan. There is no rust on components before PT line. Cleaning & Phosphate coating is okay. And my PT line is okay with standardized parameters. I have problems coming from CED line. Our CED line is not okay. Thanks.
Virender Singh [returning]paint shop - Panchkula,Haryana, India
December 30, 2015
? Hi Mr. Virender,
My questions:
1. Tried on other substrates or materials? same defect appeared?
2. Any solvent/oil floating on bath surface during ED process?
3. Ensure no stubborn oil & grease on part surface?
4. After rework process part proceed to ED happened same defect?
Above questions might lead you to certain ideas to proceed.
Thanks.
- Ulu Tiram, Malaysia
A. The problem is in the bath composition; you have to add hydrogen scavenger to the bath like nitroethane or hydrogen peroxide in the ratio 4% -- this is because hydrogen evolves during the process making film defects and the surface of the work piece not fully painted which causes free zones that makes rust and pits in the film so you have to eliminate defects by hydrogen scavenger.
Thanks
Ahmad abo awf
- cairo, egypt
[editor appended this entry to this thread which already addresses it in lieu of spawning a duplicative thread]
Q. Please tell me how eliminate the problem of pinhole on bars please tell me.
ganesh dede
- Pune, Maharashtra,and India
July 4, 2016
A. Hi Ganesh. We added your inquiry to a thread with great info on the subject. Please feel free to expand upon your question with additional or differing details if you wish. Good luck.
Regards,
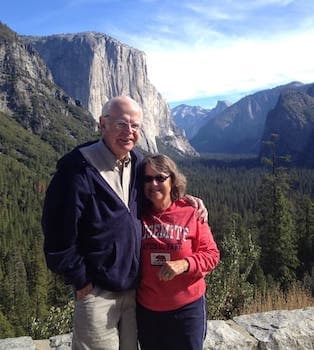
Ted Mooney, P.E. RET
Striving to live Aloha
(Ted is available for instant or longterm help)
finishing.com - Pine Beach, New Jersey
This meeting place welcomes Q&As, photos, history, & interesting tidbits.
Please engage with other posters
• When people show interest in each other's situations, the page quickly becomes a fun & informative learning experience for everyone !
• When people show no interest in other people's postings, and just post their own, it often quickly deteriorates into a string of unanswered questions 🙂
Q. Hi There,
I am working in a HDD manufacturing company in Cambodia; I am the e-coating manager.
Here we are facing very high fallout of hard blisters, soft blisters and pin hole voids (fish eye).
The pre-treatment is a very mild etching process.
Please advise me how can I solve this problem.
Thank you
- JOHOR BAHRU
November 11, 2016
Q. Dear advisor,
I am employee of CED coating system in johor malaysia. Now I have some problem on my ED coating part surface. My ED bath pH - 5.7, NV%-10.00, PB ratio - 0.095, bath temp. 25.0 °C. BC % - 1.25, HC % - 0.890. The part before ED I have been 100% confirm free from oil, but there is still pinhole defect ... but just one dot only. So how I can solve it? Please give me some idea or advice. Your cooperation will be highly appreciated.
best regards,
Jiwan RaiED coating jobshop employee - johor baharu, malaysia
March 16, 2017
Ed. note: Just to clarify, Jiwan, so there isn't a misunderstanding: this is not a consultancy, it's just readers trying to help each other :-)
Q. How important is it to drain permeate? Here where I'm working, no one drains it even a bit. And we frequently face the problem of pin holes on Cathodic electro deposited automobile bodies. My senior says it's due to high MEQ. Please shed some light on this for me.
Kasi Viswanath Boddeti- Andhra Pradesh, India
July 13, 2018
Pin hole on CED components on the bottom of the substrate
Q. Dear sir
I am employee of the CED Coating system in Chennai india. I have some problems on my CED coating pin hole issue getting on only bottom and curve of the components for all components where ever jigging. All the parameters are within spec and having sufficient agitation. Kindly guide me to resolve this issue and explain the root causes and action plan sir. We tried all trials as far as we know in all aspects.
Please find attached photos for your reference.
Regards,
Ganesan NallusamyShop employees - Chennai, Tamil nadu, India
August 26, 2018
Q. I am working in a e-coating plant Bangalore. Our pretreatment line is OK, but pinhole is coming in component. What shall we do? Please guide me?
Tekchand Patel- Bangalore, India
September 7, 2018
A. For the Pin hole problem:
1. check that all parameters are in range (PT line, voltage, ED temperature, pH, N/v content, conductivity, dipping time & cleaning frequency)
2. check the circulation in ED bath
3. check the hanging positions of part
4. check the proper insulation removed before part loading
To avoid this problem ... then install filtration method in ED bath.
- India, Maharashtra, pune
March 2, 2019
Q. Sir, I also encountered a pin holes issue. Our parameters are within the standard. In the end of the roof, it has many pin holes but in the front of it has nothing, it's good. And when we change the DI rinse water after phosphate, the pin holes decrease (we change when the conductivity of this tank approximate 1000, and when the conductivity of this tank is higher than 300 it has more pin holes).
So my question is why is this? can you explain this and how to solve it?
Thank you!
paint shop - Hanoi, Vietnam
July 26, 2019
A. Hi Ryan. Sorry, I don't understand what you mean by "roof". Are you coating individual parts or continuous reel-to-reel?
Also, you may be doing it differently, but conventionally, you don't fill a tank with DI water and dump it when it gets too contaminated. Rather, you constantly recirculate the water from the tank through a de-ionizing unit, and back to the tank so it remains de-ionized to the same degree all the time. You change the DI cylinder when it becomes exhausted, not the water in the tank.
Please clarify for me. Thanks.
Regards,
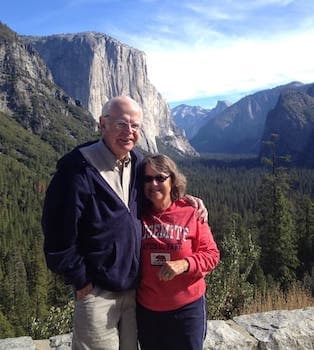
Ted Mooney, P.E. RET
Striving to live Aloha
(Ted is available for instant or longterm help)
finishing.com - Pine Beach, New Jersey
Q. Thanks sir. Sorry about my english, it's quite bad.
About the problem, we dip a car in the tank, so "roof" that I mention is the top of car. But when dip in ED tank it's in the bottom of tank.
The second question, yes it's a lot of pinholes by the end of this roof. It just stay in it.
About the DI water tank after phosphate tank, it has been designed. When water it bad, it will be replaced, not as you described. And the company does not allow modification, it will be in charge.
Paint shop - Hanoi, Vietnam
A. Hi again, Ryan. Thanks for the explanation about the roof, it is very clear to me now!
Hopefully someone experienced with that will help you.
If you know that the problem gets much worse as your DI rinse gets contaminated but you will neither fix the design, nor dump the DI tank, what can be suggested? Changing the electrocoating formulation or other parameters so it is more contamination-tolerant doesn't sound promising. Maybe another reader has an idea though.
Regards,
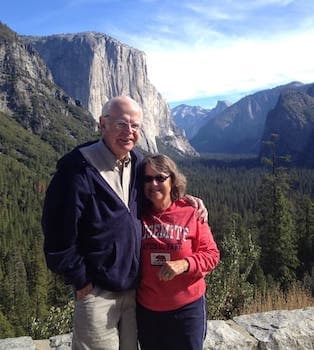
Ted Mooney, P.E. RET
Striving to live Aloha
(Ted is available for instant or longterm help)
finishing.com - Pine Beach, New Jersey
Q. But I can't explain why. What is mechanism of it? So I can more understand about it. And when I change the DI water, the pin holes just decrease, not disappear. And the flow of ED tank on top is left to right and in bottom is opposite, it make a circle, and I think it not strong like swirls to put the hydrogen on in the roof of car, is this right? Because I just graduated from university so don't have much experience. Thank you!
Ryan Nguyen [returning]Paint shop - Hanoi, Vietnam
by Larry Durney
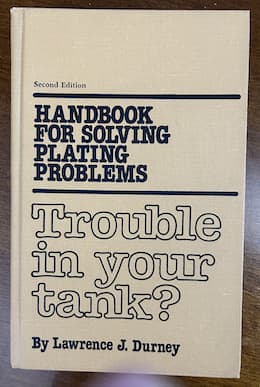
on eBay or Amazon
or AbeBooks
(affil link)
A. Hi again Ryan. Hopefully another reader will jump in because I don't know precisely what is causing those pinholes ... but contamination can aggravate them, as you already realize and have already demonstrated.
Why exactly a specific contaminant in the dirty rinse worsens the problem may not ever be known; some knowledge is empirical and can't be traced all the way back to first principals: it might be dirt interfering, it might be higher conductivity allowing galvanic currents, it might be a chemical reaction to a specific contaminant.
If you have another theory of what is causing it, and feel that a dirty rinse merely accentuates rather than causes it, okay, but ...
Wet metal finishing processes are very complex and as Larry Durney writes, an absolutely essential point in troubleshooting is "Obey the Letter of the Law!". When you already realize that contamination in the rinse tank aggravates the problem, you must start by fixing this contamination in the rinse tank; you can't let it slide :-)
Good luck!
Regards,
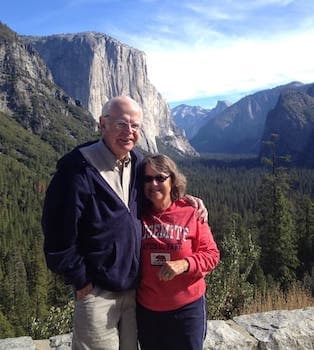
Ted Mooney, P.E. RET
Striving to live Aloha
(Ted is available for instant or longterm help)
finishing.com - Pine Beach, New Jersey
A. Hello Ryan. Change the dip D.I. water rinse to SPRAY rinse or Add fresh D.I.water SPRAY while taking out car body from the dip rinse tank. The sludge from phosphate tank remains at flat portion and that's the reason for pin holes (What I think is those are not pin holes but are CRATERS that formed due to impurities in the water.)
Avinash Vidhate- NASHIK, Maharashtra, India
Q. Hi I'm sunny. I have a CED coating plant and want to check my CED coating bath. Please tell me how to check it.
I have a problem with casting material. Pinholes is my big problem.
Sunny patel [returning]- India gujrat in Rajkot
February 19, 2020
A. Hi Sunny. The above discussion may suggest what to do next; or please send need photos and additional description. But also please clarify whether you mean cast iron parts, diecast zinc parts, or pressure cast aluminum parts. Thanks!
Luck & Regards,
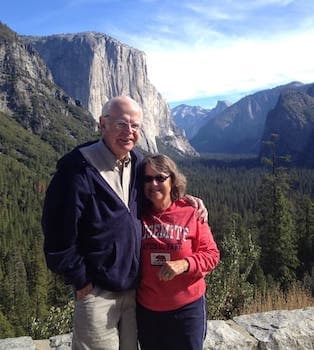
Ted Mooney, P.E. RET
Striving to live Aloha
(Ted is available for instant or longterm help)
finishing.com - Pine Beach, New Jersey
Q. Hello all, I have some problems with painting.
I have an E-coating line almost 3 years; everything was okay until last month. Problem is with non-painted small holes on the object. I think this is not a problem of pretreatment or air bubbles or racking.
My paint supplier suggested that I add more solvent, but this did not help. Does anybody have an idea what is the cause of this issue?
Nikola Djukic- Prnjavor, Bosnia
December 23, 2020
Q. Hi sir,
I am working PTED line and I am facing first time PINHOLE issue in full body. And then finding a root cause is ED Path problem. And how to solve this problem please give me an idea.
Thank you sir.
Production associate team leader (trainee) - Chennai, India
July 2, 2021
A. Hi cousin Govind.
Although there are several possible causes for pinholes (as you can review on this rather long dialog on exactly that subject), Larry Durney warns us in "Trouble in Your Tank" to remember that, if it used to work but now doesn't, it's because something changed :-)
He notes that in nearly every case it's much easier to figure out what has changed, than to start from scratch and re-develop a workable process. He says:
• Study the Records (personally!)
• Insist on the "Letter of the Law" for every parameter.
Only if, after doing those things, you remain unable to figure out what changed should you face the much bigger job of trying to redevelop a workable process ... but this page discusses several possible causes of pinholes if you can't restore the original process. Good luck!
Regards,
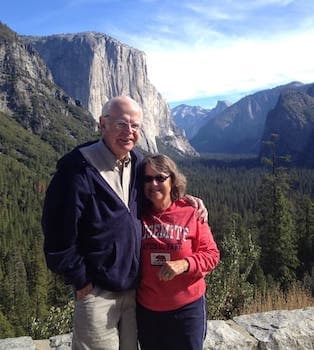
Ted Mooney, P.E. RET
Striving to live Aloha
(Ted is available for instant or longterm help)
finishing.com - Pine Beach, New Jersey
Q, A, or Comment on THIS thread -or- Start a NEW Thread