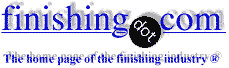
-----
Aluminum Anodizing vs. Powder Coating vs. Kynar vs. Clear Coating
1 2
Q. Hey, I wanted to know the ways (more than one) that one can tell the difference between Anodization and a paint coat.
Thank you
- Bangalore, Karnataka, India
October 17, 2014
A. Hi Anand. Appearance and x-ray fluorescence would be two non-destructive ways. You can easily sand painted lettering off of aluminum but will find it very difficult to sand anodizing off. Please give us your situation rather than an abstract question so people know whether destructive tests would be appropriate, and why the question arises, and how important it is that the answer be 100.00% accurate. Thanks.
Regards,
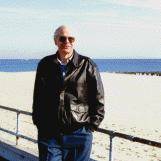
Ted Mooney, P.E.
Striving to live Aloha
(Ted can offer longterm or instant help)
finishing.com - Pine Beach, New Jersey
Q. I am trying to select a material for a fascia on a house in Southern California near the beach. I am going for a contemporary look and am considering aluminum with a kynar finish. Or possibly a galvilume. This will not be an area that will have wear and tear, but it will be exposed to sunlight and the house is 125 yards from the beach so is near salt water. I don't want to have to refinish it constantly. Any suggestions?
Omar Alam- Austin, Texas
December 20, 2014
A. Hi Omar. I think Kynar is ideal for this kind of application.
Regards,
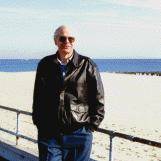
Ted Mooney, P.E.
Striving to live Aloha
(Ted can offer longterm or instant help)
finishing.com - Pine Beach, New Jersey
December 2014
January 4, 2015
Q. Dear Sirs
We are required to quote for a job of a few thousand metres of railings. The location is on the beach (high heat, humidity, salt spray, etc.);
the nature of the railing is such that it is continuous and requires welding at site.
The required specs are for anodising, but there will be many onsite welded connections. Is anodising really feasible in this case?
Is there any way to match the finish at the welded and ground joints to that of anodised coating considering that each continuous span will be about 30-40 mtrs?
Grateful for any help.
regards
Jeen
- Abu Dhabi UAE
A. Hi Jeenraj. If there is only one joint every 30-40 meters, and you are thinking of non-dyed, natural color aluminum, it may be practical to do localized "brush anodizing" touchup of the welded joints. If welding is required every meter or two, or you were thinking of dyed aluminum, then I think the touchup would be too labor intensive to be practical, and you'd want to go with powder coating or Kynar instead. Good luck.
Regards,
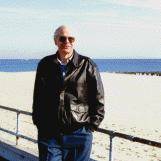
Ted Mooney, P.E.
Striving to live Aloha
(Ted can offer longterm or instant help)
finishing.com - Pine Beach, New Jersey
January 2015
Q. I'm starting a custom mailbox business using aluminum sheet as the main material. Would anodized aluminum be an appropriate choice in terms of long-term wear and corrosion resistance for a wide range of environments, especially coastal cities?
Brian Petras- Santa Monica, California USA
January 6, 2015
Q. What is the best way to make the aluminum casing scratch resistant? I have seen samples that had been anodized but still can be scratched... The aluminum sheet thickness is about 1.2 mm. Help!
Ken Robertson- San Jose, California
March 25, 2015
A. Hi Ken. There is nothing that is utterly scratch-proof, but anodizing is far more scratch resistant than powder coating, Kynar, or clearcoat. Perhaps you need a pattern or topography that makes scratches less obvious?
Regards,
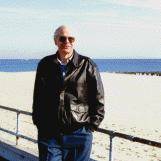
Ted Mooney, P.E.
Striving to live Aloha
(Ted can offer longterm or instant help)
finishing.com - Pine Beach, New Jersey
March 2015
Q. Quantitatively can it be proved that anodizing is cheaper than any other powder coating technology available?
Sanchari ChatterjeeResearch - Kolkata, WB, India
May 6, 2015
A. Hi Sanchari. No. Please explain your own situation though, and I'll bet we can help you.
Regards,
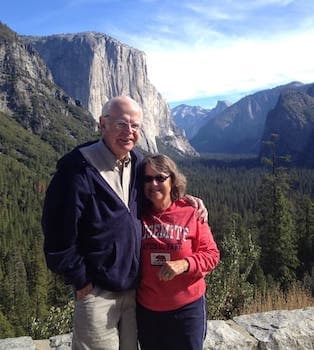
Ted Mooney, P.E. RET
Striving to live Aloha
(Ted can offer longterm or instant help)
finishing.com - Pine Beach, New Jersey
Q. The board of our HOA is in discussion for the best type of finish to replace two handrails and two guardrail fences in an underutilized park on the top of a ridge surrounded by the ocean in Hawaii. We have decided that aluminum is the best type of material to use in this corrosive environment (sun, heat, salt air and mostly a drier environment). However, we cannot move forward until we can agree on a finish (powder coating, kynar, anodized I or II). Please advise what is the most durable, low maintenance, long lasting and cost effective finish to use in the aforementioned environment. Thank you in advance for your response!
Lisa WestlyHOA - Honolulu, Hawaii USA
July 17, 2015
A. Hi Lisa. The reason there are so many finishes available is that none is "most durable", AND "low maintenance", AND "long lasting" AND "cost effective". As James Watts said earlier on: "Kynar filled the bill until you said cost effective."
So I would suggest getting a quote on Kynar painting and deciding whether you feel it is affordable. Good luck.
Regards,
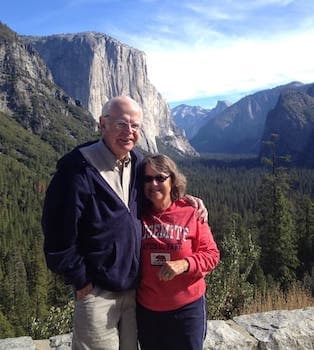
Ted Mooney, P.E. RET
Striving to live Aloha
(Ted can offer longterm or instant help)
finishing.com - Pine Beach, New Jersey
July 2015
A. Lisa, aluminium would not be my first choice due to the marine environment. That said, I agree with Ted's comments and add that powder coat might be acceptable if Kynar is too expensive for the budget.
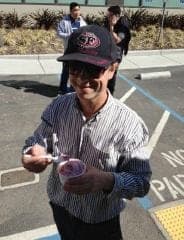
Blake Kneedler
Feather Hollow Eng. - Stockton, California
October 28, 2015
Q. Howdy!
Our company is moving into a new product line that includes the use of an aluminum extrusion. We sent out RFQ's but found we did not know the answers to some of the followup questions. Our design is 6061-T6, but we are unsure of anodizing or powder coating. The unit will be for indoor and outdoor use, and will typically be a permanent fixture that will only be interacted with during installation (so no wear & tear, except weather).
We are having a tough time deciding between anodizing or powder coating. From what I understand, anodizing should be fine but there are a very limited number of color options. Powder coating may cost more, but will allow for more color variation. The concern is can powder coating be done on only the exterior of the extrusion, as the inside must be fairly exact to fit interior components, and if so, will this affect the durability?
I appreciate any insight or assistance. We are having trouble answering these questions because we lack experience, and it seems some manufactures are not interested in helping unless you know exactly what you want.
- Pattison, Texas U.S.A.
August 2, 2016
A. Hi Joshua. Lots of anodizing colors are available for indoor use, but few are really stable for outdoor use. SO, unless there is a specific reason to anodize it, powder coating should be fine, and will offer some advantages in color choice.
You need to pretreat the aluminum for powder coating anyway, and a chromate conversion coating pretreatment will offer substantial corrosion resistance without affecting bore dimensions. It's usually possible to plug or otherwise mask the areas where you don't want the powder coating. Good luck.
Regards,
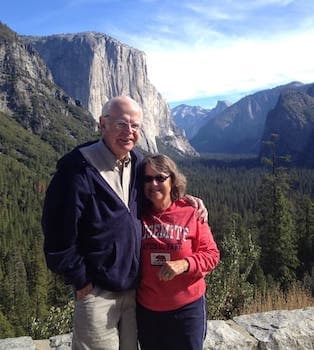
Ted Mooney, P.E. RET
Striving to live Aloha
(Ted can offer longterm or instant help)
finishing.com - Pine Beach, New Jersey
August 2016
Q. The product is an aluminium frame made out of 6061-T6 1 1/2 pipe, that is strapped to rafts, kayaks, Paddle Boards, canoes, etc. The company is Hammocraft, Jackson WY. The frame has steel connection joints (304 stainless steel corners with black UV resistant powder coating). The frame is used to support up to 5 Hammocks for hanging out on the water with your friends.
The question is: would anodizing or powder coating be the better finish for the aluminum pipe, and why?
John DolanHammocraft - Montgomery Village, Maryland, USA
June 3, 2017
Q. Hi All, I am looking at garage doors and am choosing between anodized aluminum versus powdercoated steel. The color will be bronze. You may have seen garage doors with 16 big windows (a grid of 4 by 4) in it and this is what we want. The garage will be 16' by 8' and facing south and get tons of sun. We also live 4 blocks from the ocean. Which will hold up better? I am concerned about fading, rust, scratching, denting. The aluminum costs more but I hope to have this door for 30 years.
Thanks!
- San Jose, California usa
October 6, 2017
A. Hi Jeff. You wouldn't have such choices if one were all around manifestly superior to the other. Aluminum is probably going to dent easier. I'm not sure that the aluminum one will last 30 years, but the steel one won't; I'd go with the aluminum one. Good luck.
Regards,
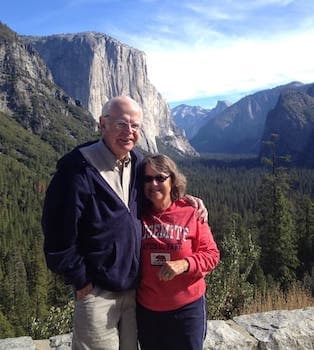
Ted Mooney, P.E. RET
Striving to live Aloha
(Ted can offer longterm or instant help)
finishing.com - Pine Beach, New Jersey
October 2017
A. Re. garage doors near the ocean, steel vs. aluminum. Most steel garage doors I've seen are galvanized, then coated. If the steel doors are galvanized, they probably will last 30 years. But an even better option is to use fiberglass or other synthetic material doors. You can easily repaint them if they get faded or scratched up over time. They are also more resistant to denting, but will break if hit hard enough.
Peter KurzenhauserPeteK, car nut - Great Falls, Virginia USA
May 9, 2018
Q. What is the best protection method for a 6063 aluminium cylindrical housing used in an autonomous underwater robot?
Anodizing? painting? other?
Thanks a lot for sharing your knowledge!
- barcelona, Spain
January 12, 2018
A. Hi Alonso. Everything depends on how valuable this item is, and how often you can maintain or re-coat it of course, but ...
If this is a really expensive component which must survive long periods without maintenance, and if cost is not a major consideration, I think an unsealed hardcoat anodizing followed by painting would be good. I think, but am not sure, that even with the highly insulating hardcoat anodizing it would be possible to apply a nylon, vinyl, or teflon thermoplastic powder coating in a fluidized bed. This would give you a long lasting waterproof coating, plus a base that would be able to resist any bumps or abrasions which might damage the plastic coating. Only a theory though.
Regards,
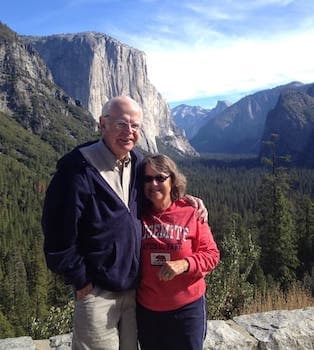
Ted Mooney, P.E. RET
Striving to live Aloha
(Ted can offer longterm or instant help)
finishing.com - Pine Beach, New Jersey
January 2018
silly :-)
Try fish scales
Mark Lees- cold and windy rock in the irish sea expecting snow
Q. My company makes specialized aluminum handles and grab bars for use in showers in behavioral health facilities. Sometimes I see pictures from our customers where the powder coating is bubbled or flaking off, particularly in locations with hard water. I'm not sure if I'm using the best coating for the application. My options are:
-powder coating (color w/ clear top coat)
-paint (polyurethane enamel with clear top coat)
-clear anodize
I use various subcontractors. I'm not sure about the specifics of their processes (preparation, etc.) I should add that I have powder coated and painted samples in my office over 10 years old with no signs of corrosion. The problem is solely due to the wet environment. Please advise.
Odd Ball Industries - Greenlawn, New York
February 4, 2018
A. Hi Chris. Although it's true that a wet environment is more corrosive than your office, any of the three finishes ought to be okay ... but the first and second require proper pretreatment. Paint and powder coatings are not shrink wrap, they need to have proper adhesion to the substrate via surface preparation and chromate conversion coating of the underlying aluminum. Good luck.
Regards,
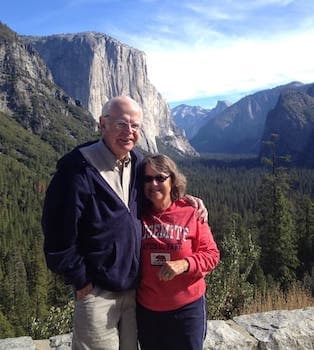
Ted Mooney, P.E. RET
Striving to live Aloha
(Ted can offer longterm or instant help)
finishing.com - Pine Beach, New Jersey
February 2018
![]() |
February 8, 2018 Q. Ted - Thanks for the response. While waiting for feedback, I've been conducting an experiment to test the various coatings, and I'll share the results. Odd Ball Industries - Greenlawn, New York A book could be written on this subject. trainer - salamander bay |
A. Hi Chris,
Just to add a little more dye into the water...
Might it be worth trying to Hard Anodise them which would be a little thicker and more corrosion resistant? Will probably add a little bit of an extra cost but surely cheaper than the cost of replacement.
Electroless Nickel is sometimes used in offshore/subsea applications and will coat evenly on your component no matter its shape. This is not a particularly decorative finish however.
Bronte Precision Engineering - Bradford, West Yorkshire, UK
February 21, 2018
A. Hi Chris,
Another consideration is imposing a standard requirement for your corrosion protection process. You would be likely paying a premium for a supplier that is compliant but your expectations can be higher as a result.
Examples include AAMA 2603 through 2605 (it's the exterior architectural aluminum standard with 2603 being the base and 2605 requiring corrosion protection upwards of 10 years) for powder coating and a similar variant for anodized architectural aluminum. Another venue is specifying how long the coating is supposed to last in Neutral Salt Spray (since your experiment used CaCl2, I assumed you believe Chloride is an issue as all of the pitting on your samples came from Aluminum and Chloride, else I recommend repeating the experiment with Calcium Carbonate (CaCO3))
Cheers,
-Erick
Vapor Bus International - Buffalo Grove, Illinois
February 27, 2018
Q. I have a set of Porsche 911 wheels I want to hard anodize silver. These are the Fuchs forged wheels, so they do not have the porosity or crystalline structure of casting. I do not know what alloy they are, but since they are forged and high strength alloys, I expect a 6000 series. They are currently polished, but I'm tired of trying to keep up with waxing and polishing them. I don't know if this question is appropriate on this site, but can anyone recommend an anodizing business in the Washington DC or northern Virginia area? Thanks.
Peter KurzenhauserPeteK, car nut - Great Falls, Virginia USA
May 9, 2018
Ed. note: This RFQ is outdated, but technical replies are welcome, and readers are encouraged to post their own RFQs. But no public commercial suggestions please ( huh? why?).
A. Hi Peter. Please see our "Introduction to Anodizing" which explains the difference between hard anodizing and conventional anodizing. Even though your wheels are forged, I doubt that you will be happy with the appearance after anodizing. I think clear coating will work better.
We don't post recommendations of shops or other commercial suggestions in the public forum for a number of reasons including the spam explosions and phony testimonials it leads to on this no-registration-required site, but hopefully someone will contact you in private if you are still interested in having them anodized.
Regards,
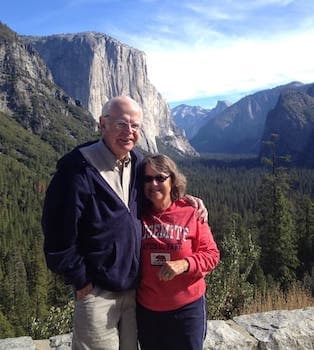
Ted Mooney, P.E. RET
Striving to live Aloha
(Ted can offer longterm or instant help)
finishing.com - Pine Beach, New Jersey
May 2018
Q. Ted, thanks for the reply. I know that anodizing will not give a bright polished finish, but the wheels were originally anodized from the factory, with a satin finish, so that's what I want to get back. I checked with a local refinishing shop that specializes in powder coating. They do not clear powder coat wheels because the coating does not adhere well to the polished aluminum. Instead they recommend a color powder coat, because then they media blast the surface to get better adhesion. So, I'm back to anodizing. The original anodized finish held up for many years.
Pete Kurzehauser [returning]PeteK, car nut - Great Falls, Virginia
May 9, 2018
Q. My situation: Hi, is it good enough to use silver anodized aluminium 6063 alloy in C4 corrosion class indoor environment or I should use powder polyester coating for it?
Keem Pava- Warsaw, Poland
July 16, 2018
A. Hi Keem. From the other questions you asked in the last couple of days (topic 0702 and 11789) it seems that you are referring to an indoor swimming pool environment. Although anodized aluminum ladders and railings are sometimes used in swimming pool and wastewater treatment areas, anodizing is really not ideal in a chlorine environment and the powder coating is probably better.
But remember that the "C4 corrosion class" guidelines tend to be for building work, rather than product design. If you are designing a product rather than doing general corrosion resistant coating work for a building, you'll want to consider a number of other factors. Good luck.
Regards,
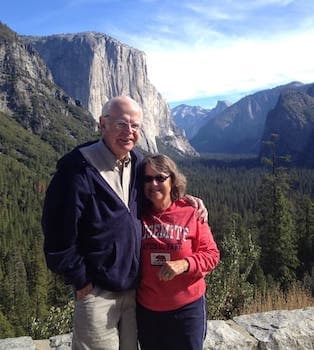
Ted Mooney, P.E. RET
Striving to live Aloha
(Ted can offer longterm or instant help)
finishing.com - Pine Beach, New Jersey
July 2018
Q, A, or Comment on THIS thread -or- Start a NEW Thread