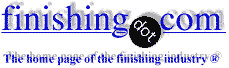
-----
Zinc-Nickel Plating Intro, What & Why

Quickstart:
Zinc-nickel is an alloy plating of zinc, with about 5% to 15% nickel depending on the formulation.
Zinc-nickel is an upgrade from zinc plating because of its significantly increased corrosion resistance. It's now very widely used on automobiles in place of plain zinc plating.
Alloy plating is generally difficult because we need to deposit the desired proportion of alloying materials while the electromotive series is working against us, trying to deposit only the more noble metal. So the chemistry is complex and usually proprietary rather than home-brew.
Q. Good morning. When we crimp the ZnNi ferrules/bushings a lot of metal dust is generated. I did some checks and it is not sealant but metal. Is it possible to find a remedy to eliminate it?
by V Narasimhamurthy
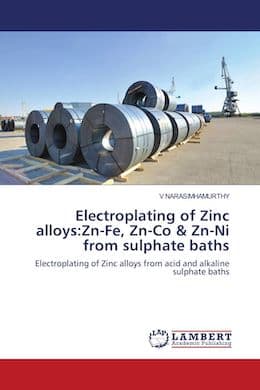
on eBay or Amazon
or AbeBooks
(affil link)
- Italia
November 20, 2024
Tip: This forum was created to help build camaraderie through sharing tips, opinions, pics & personalities.
The operator & those readers who want that might not engage with anonymous posters.
A. Hi Anna,
Although it's possible that the plating does not have enough adhesion, it seems more likely that it's too stressed and brittle. Is it possible to reduce the amount of brighteners or other organic addition agents which harden the plating?
Luck & Regards,
Ted Mooney, P.E. RET
Striving to live Aloha
(Ted can offer longterm or instant help)
finishing.com - Pine Beach, New Jersey
Q. I want to install electro zinc- nickel plating for mild steel fine gauge wires for glossy bright wire stationery bent & formed articles. Is zinc with 10% nickel better for silvery finish, and ductile for wire forming machines like paper clips and spirals.
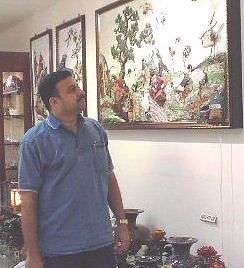
ESMAIL T. GODHRAWALA
wire drawing & plastic coating - MUMBAI, Maharashtra, INDIA
March 19, 2025
A. Hi Esmail.
Let's see what other readers have to say, but in my opinion it will not be brighter nor more ductile. It's big advantage is additional corrosion resistance but the increased cost may be a difficult sell in the mild environment of paper clips and stationary products.
Luck & Regards,
Ted Mooney, P.E. RET
Striving to live Aloha
(Ted can offer longterm or instant help)
finishing.com - Pine Beach, New Jersey
⇩ Related postings, oldest first ⇩
Shortcuts to specific Q&A's about Zn-Ni Plating:
•E-coating on Zn-Ni is blistering
•Adhesion problem on stainless
•Interpretation of spec
•Parts are failing salt spray
•Base Metal Erosion
•Best temp. for alkaline plating
•Pitting problem
•Parts & Hull Cell Panel Are Dull
•Is 25µ okay or too thick?
•Organic sealant prevents insertion
•Honda specs
•Black spots from cutting oil
•Black patches in alkaline Zn-Ni
Q. Sir,
We want to know about the process of Zinc-Nickel Plating. Can you please give us the process. Waiting for your reply at the earliest.
plating shop - Hyderabad, AP, India
2004
A. Zinc/nickel alloy plating formula:
zinc chloride 130 gm
nickel chloride 130 gm
potassium chloride 230 gm
pH 5-6,temp.24-30 °C
separate zinc and nickel anodes.
Good luck!
- Cerovski vrh Croatia
by Abner Brenner
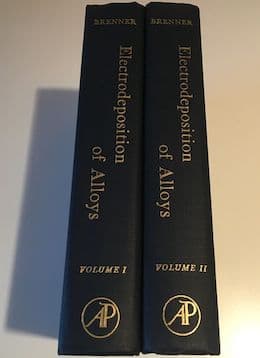
on eBay or Amazon
or AbeBooks
(affil link)
A. Hi, Ramarao. Zinc-nickel plating deposits are made of zinc with a few percent of nickel in it (often about 6%). The idea is that this plating still offers sacrificial protection to steel like zinc plating does, but due perhaps to incapsulating itself in more stable corrosion products it does not corrode as quickly as zinc, and thereby provides substantially more corrosion resistance than an equivalent thickness of zinc electroplating. It is available as either an acid or an alkaline proprietary process offered by several suppliers in your area.
Although Goran is kind enough to offer a formulation, and although the process is discussed in Brenner,
... the robust electrodeposition of alloys like this requires specialized chemistry, and plating shops generally do not attempt to formulate such processes themselves. It is one thing to plate one small item in a laboratory from a generic formula, but quite another to do zinc-nickel plating in a production environment. Good luck.
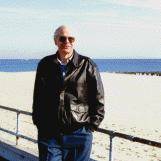
Ted Mooney, P.E.
Striving to live Aloha
(Ted can offer longterm or instant help)
finishing.com - Pine Beach, New Jersey
A. Mr Rama Rao Yellamanchi
Namaskaramandi.
Zinc Nickel Plating is used for automotive components which are exposed to higher temperatures as found in engine components where other alloys such as Zinc Iron fail easily or Zinc Cobalt does not withstand the tempering caused by engine temperatures.
Zinc Nickel stands Salt Spray 500 hours to white rust and more up to 1000 Hours to red rust with the right passivate.
Processes to plate Zinc Nickel are available within India. Alkaline processes are preferred over acid systems due to the superior distribution and even alloy content all over the component. Cosmetic brightness is possible.
You will need a lined tank, a filter 4-5 times/hr bath capacity, rectifier 6 volts, cathode movement, and a good pretreatment line as if you were doing Nickel. The Passivates are not the common ones used for regular zinc. All colors are possible.
Lastly Zinc Nickel costs 5 to 7 times that of regular zinc, micron for micron over a unit area.
Regards,
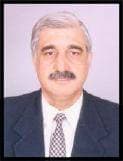
Asif Nurie [deceased] [deceased]
- New Delhi, India
With deep sadness we acknowledge the passing of Asif on Jan 24, 2016
A. Agree with the three previous responses. Use the low pH version of Zn-Ni only if you need shorter dwell times in the plating bath or more ductility.
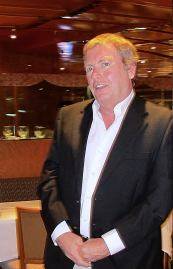
Randy Lalande
- Hitchcock, Texas
E-coat is blistering on zinc-nickel plated parts
by Electrocoat Association
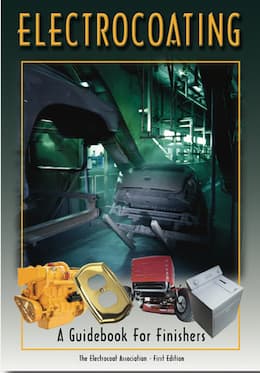
on eBay or Amazon
or AbeBooks
(affil link)
Q. Hi, I have a part that has zinc-nickel plating on it. We have an 11 stage immersion pretreat/e-coat system. I ran these parts thru our system in plant water and RO water (rinses only) I did not run them thru our alkaline cleaners because of removing the plating. So I just rinsed the parts and coated them with an epoxy e-coat. When the parts came out of our cure oven set at 375 °F for 45 min. to an hour they had small like popping (BBs) all over the part. I am wondering if the plating was breaking down because of the oven temp. or if there was some contamination on the plated part that caused this. I also had different part that had a cadmium plating on it, ran it the same way thru our system and had the same look to it. Any ideas what may have caused this? Need help. Thanks
Ken Cundy- Mayville, Wisconsin, USA
July 25, 2012
A. Hi Ken.
Three things to try immediately are:
1. Put some plated parts in that oven or another oven for 45 minutes at 375 °F to see if the temperature alone causes the plating to blister.
2. Pop a few of those BB-sized blisters to see what is on the underside of the blister, and on the part underneath the blister to determine what is separating from what. First guess is the plating is separating from the substrate.
3. I suspect that the parts are not clean enough. Scrub some samples with a tampico scrub brush
⇦ on
eBay or
Amazon [affil link] and a solution of pumice
⇦ on
eBay or
Amazon [affil link] with a little detergent before running them through your 11-stage system and let us know if they still blister.
Some things to consider are that the plating ought to be able to withstand this temperature, and parts are often baked at this temperature as a QA test to try to make them blister immediately, rather than later.
Regards,
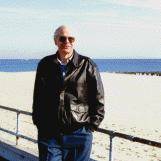
Ted Mooney, P.E.
Striving to live Aloha
(Ted can offer longterm or instant help)
finishing.com - Pine Beach, New Jersey
Q. Dear sir, please give me the formula of zinc nickel bath and others parameters. Thanks and regards.
Muhammad Amir- Karachi, Pakistan
January 31, 2013
A. Hi Muhammad. We searched the site and appended your inquiry to a thread which we think answers it, but please post again if you have remaining questions.
Regards,
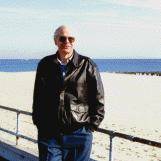
Ted Mooney, P.E.
Striving to live Aloha
(Ted can offer longterm or instant help)
finishing.com - Pine Beach, New Jersey
Q. Dear sir, please give me the chemical composition of zinc nickel bath and others parameters. I use acid zinc additive of above plating. Thanks and regards.
Muhammad Amir [returning]- Karachi Pakistan
Regards,
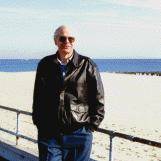
Ted Mooney, P.E.
Striving to live Aloha
(Ted can offer longterm or instant help)
finishing.com - Pine Beach, New Jersey
Zinc-nickel plating on 17-4 parts takes too long and blisters
Q. I have a Zinc Nickel line that does mainly Aluminum Bronze and 17-4 parts (aerospace). The Aluminum Bronze parts have no issues with adhesion and plating thickness. The 17-4 parts take twice as long to plate and then at post bake they start to flake or blister. Ideas?
Craig Hutchins- Fort Worth, Texas, USA
February 5, 2013
A. Hi Craig,
Have you always had a problem with adhesion on 17-4PH steels, or is this something that has developed over time?
My initial thought was that the activation of the steel is insufficient to give good adhesion, but it is difficult to tell with the limited information that you have provided.
If this is a problem that has built up over time I wonder if you have had a build up of copper in the tank from the Aluminum Bronze and that this is depositing on the surface of the steel, causing problems.
Aerospace - Yeovil, Somerset, UK
A. Hi
Craig Hutchins
To avoid problems of blisters you need a nickel strike before Zn/Ni plating for SS material (17-4, 15,5), it is recommended for 52100 material (high carbon) also.
Good luck!
- Tecate, BC, Mexico
Interpreting thickness and salt spray specifications for zinc-nickel plating
Q. For zinc nickel plating what should be the correct criteria to determine the correct plating thickness? The spec. is 8 microns minimum. The process is rack plating.
My current supplier is taking 3 readings from the part and reporting an average of 12.8 microns; but from these 3 readings one of the readings is below the 8 microns due to the geometry of the part and variation of the thickness. Some areas are as low as 5 microns but the highest areas are 14 microns. Is this a correct criteria to determine the part meets the minimum thickness required of 8 microns or any point inspected should be above the minimum required?
The position of my supplier is that if the part is plated to achieve the minimum of 8 microns in the lower value areas the areas where more plating is deposited might go too high to 16 / 18 microns and create a chip / flaking issue.
Also the SST requirement is 480 hours salt spray for no rust. The parts are showing slight red rust at 480 hours. Should this be considered as a failure or pass?
Thanks for your help!
Ebe Salinas
- San Antonio, Texas USA
March 21, 2013
A. Thanks for an interesting one, Abe :-)
First, if your spec is 8 microns minimum, that's what it says and that's what it means, and parts with 5 micron thickness are not meeting it (usually though, a spec will call for the minimum thickness to apply only to surfaces that can be touched by a 3/4" diameter ball). Of course, that doesn't mean that your plater is necessarily wrong about the parts chipping or flaking if they go to 8 microns minimum :-)
If you are the end customer, you get to decide how thick is thick enough, and how many salt spray hours is enough. If you are happy with the parts and are having no problems in the field, I see nothing wrong with reducing the spec to 5 microns minimum and salt spray hours to 432 hours rather than 480 hours in lieu of developing a whole new process. But if you are a subcontractor yourself, parts that measure 5 microns do not meet an 8 micron spec, and parts that show red rust in 480 hours do not pass a 480 hour test. But you should try to find a recognized international standard and require compliance with it; it will reduce such questions and contract disputes.
Good luck.
Regards,
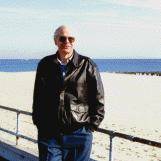
Ted Mooney, P.E.
Striving to live Aloha
(Ted can offer longterm or instant help)
finishing.com - Pine Beach, New Jersey
Q. I have a current assembly with one material type 304 stainless steel and the other is 1008-1010 low carbon steel plated with zinc nickel chromate plus topcoat 8 µm. The assembly needs to pass 336 hours of salt spray, but can only achieve 50% of the required hours. I have attempted to have the 304 stainless steel nickel struck and then plated with zinc nickel chromate, but this did not improve the salt spray performance. I can change plating on the low carbon steel material, but the costs need to be similar to the current plating. Any suggestions on options for either component as far as plating that could offer 336 hours of salt spray performance?
M GerkenProduct Designer - Toledo, Ohio, USA
May 16, 2013
A. Dear Mr. Gerken,
First of all, you should put ONLY THE ZINC-NICKEL PART in salt spray and see the results to compare. If the results are good (more than, I say, 336 without white rust is fair), you have problems only with the assembly:
If the red rust appears in the contact surface or around it, we can think of galvanic corrosion (although you considered that when you zinc-nickel plated the SS304 part) or stress corrosion (if the parts are clamped or bent when assembled).
If it is the first one, you can try using a non-conductive lacquer or topcoat (if the one you are using is conductive) over the zinc-nickel part. This can prevent galvanic effects.
If it is accelerated corrosion by stress the problem, you can try some other chromate conversion coating, there are many vendors, and some top products can withstand up to 600 hours to white rust in salt spray ASTM B-117 for only-zinc-nickel-parts. Assemblies are a world apart.
AND... If you must, or want, to reduce costs and maintain corrosion resistance, you should try some organometallic coating on the low-carbon steel part. These products are conductive, compatible with stainless, corrosion resistance up to 1000 hours in salt spray, and the costs are, I think, lower than alkaline zinc nickel + topcoat. See for yourself!
Regards and good luck!
- Cañuelas, Buenos Aires, Argentina
Q. Our supplier plated Zn-Ni with the average thickness of about 14.1 micron with 13.6% nickel. As per our customer requirement, the part should withstand 720 hours to red rust. But, we checked, the part got white rust at 240 hours and red rust at 552 hours. What is the reason to get rust before 720 hours.
Manikandan Arumugam- Bangalore, Karnataka, India
May 22, 2013
A. Hi Manikandan. 552 hours is not horrible, and not cause for embarrassment, so communication is key.
Try to find out from your customer where this spec came from. If other plating shops are achieving it on these parts for your customer, you probably need to as well. But sometimes specs just come from a designer reading sales pap and not realizing that the highest salt spray hours come only on ideal parts. Or using the salt spray hours s/he previously obtained on a totally different part. So it may simply be that 720 hours isn't reasonable on this particular part.
Regards,
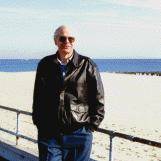
Ted Mooney, P.E.
Striving to live Aloha
(Ted can offer longterm or instant help)
finishing.com - Pine Beach, New Jersey
Q. Hi Ted,
Thanks for your valuable answer. The same part from other plating shop is achieving 720 hours of SST as per our customer spec. If you give related answer for my query in finishing.com, I feel happy. Thanks a lot.
- Bangalore, Karnataka, India
A. Hi again. 552 hours is not an embarrassing number, so it's hard to tell precisely why one shop got this while another has managed 720. But it seems that it can only be four possible things: they weren't tested in the same cabinet, or their chromate is better (which I tend to doubt), or their plating is either thicker than the minimum or more evenly distributed, or the composition of their alloy is slightly more corrosion resistant (less zinc).
Of these things, after assuring consistent testing, the easiest fix would seem to be to slightly increase the thickness of the plating if the customer does not object. Good luck.
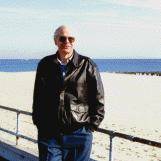
Ted Mooney, P.E.
Striving to live Aloha
(Ted can offer longterm or instant help)
finishing.com - Pine Beach, New Jersey
A. Hello Manikandan,
I think that 14 microns of zinc-nickel (13% Ni is a really good alloy) should not show red rust in 500 hours of salt spray. Therefore, I think you should look for spots where the zinc-nickel is not 14 microns thick, and tell your supplier to achieve a minimum of 5 microns (or what it says in the spec you have) everywhere in the part to reach 720 hours of salt spray.
It is important to know (for me, at least) if it is a barrel-plated or rack-plated part. Barrel-plated parts have a more leveled thickness than rack parts, as the last ones don't move in the process.
As Ted mentions, the part is not achieving the corrosion resistance as spec, but it is not "horrible"! Your supplier must improve in leveling thickness (in my opinion, 14 microns even without conversion coating must last more than 400 hours) and maybe add some sealer over the conversion coating to get the white rust above 300 hours.
Hope you can solve this issue! Regards,
- Cañuelas, Buenos Aires, Argentina
Good point, Daniel. A good sealer over the chromate may be the difference.
Regards,
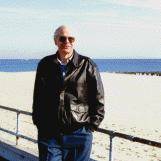
Ted Mooney, P.E.
Striving to live Aloha
(Ted can offer longterm or instant help)
finishing.com - Pine Beach, New Jersey
This meeting place welcomes Q&As, photos, history, & interesting tidbits.
Please engage with other posters
• When people show interest in each other's situations, the page quickly becomes a fun & informative learning experience for everyone !
• When people show no interest in other people's postings, and just post their own, it often quickly deteriorates into a string of unanswered questions 🙂
Graphite Contaminating Zn-Ni Plating Baths
Q. Hi,
We are facing problems in plating of Hot Forged Components. The manufacturer uses Graphite as a lubricant during manufacturing of components.
Hot forged parts are porous in a microscopic level and graphite gets embedded within the component during the forging process.
The graphite does not get dislodged during Hot Soak Process and comes out only during Anodic cleaning process.
A layer of graphite starts to float on the bath which will carry over to subsequent baths as well.
Presence of graphite causes black patches on plated parts as well as it causes material erosion in some cases.
Please provide a solution for this problem.
Thank You
Roopak
- Bangalore, Karnataka, India
October 5, 2013
A. Hi Roopak,
Your electroclean tank should be equipped with a grease skimmer/grease trap arrangement. This consists of a separate overflow compartment with a pump which returns the solution to a perforated pipe which skims the floating graphite into the trap.
Luck & Regards,
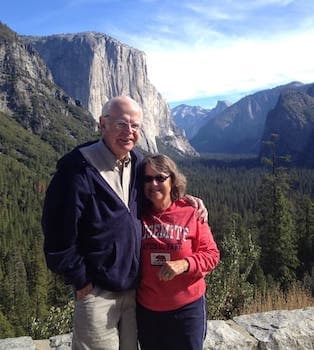
Ted Mooney, P.E. RET
Striving to live Aloha
(Ted can offer longterm or instant help)
finishing.com - Pine Beach, New Jersey
Base Metal Erosion due to Zn-Ni electroplating
Q. We have a hot forged and controlled cooled micro alloyed steel component.
Only 30% of the surface is machined and remaining is as forged surface.
We are doing Zn-Ni (Non cyanide alkaline bath) electroplating on the component.
Base metal erosion is happening on the machined surface after the plating process.
Pre part is not having any such erosion and plating thickness and Ni % is ok on the eroded surface.
Forging process: We are using graphite based forging lubricant.
Plating Process: 2 X degreasing --> Anodic Degreasing --> Pickling --> Anodic Derusting
--> Mild acid dip --> NaOH activation --> Zn-Ni electroplating -->
DM water dip --> Iridescent passivation (High Co & low Cr3+) -->
Dewatering Oil dip --> Oil dripping.
Plating is done in fully automated line with SCADA system.
Suggest us with the possible causes for the metal erosion defect.
- Bangalore, India
October 7, 2013
A. Hi Srin,
I have never seen erosion like that before. A few guesses:
I think that you are having an interaction of some of your chemicals on the pre plate steps. There are some strange combinations of chemicals that can become extremely aggressive. Think of aqua regia for example. Makeup chemicals are not terribly aggressive but together they can dissolve gold.
A touch of fluoride can make a world of difference in an anodic bath.
When you say alloyed steel, what alloy?
That said, I cannot think of any steel that you can activate with NaOH.
- Navarre, Florida
A. Hi Srinivasan. I think the part hit the anodes in one of the electrified tanks.
Regards,
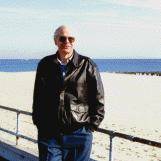
Ted Mooney, P.E.
Striving to live Aloha
(Ted can offer longterm or instant help)
finishing.com - Pine Beach, New Jersey
Q. Dear Mr.James,
We are using graphite based die lubricant in forging of this component. Can this lead to this kind of defect if it is carried over to pre cleaning tanks like anodic?
Also If HCl is carried over through the pin holes and punctures in the rack insulation to anodic derusting tank after that, will it lead to this kind of defect?
Dear Mr.Mooney,
Apart from contact point in rack, we have supporting hook (306 stainless steel) near top and bottom of the part where we predominantly see this defect. This is not insulated, not supposed to touch the part but if touches will this kind of defect can happen?
Alloy of the base metal used is 38MnVS6 and it is controlled cooled immediately after forging to get the required hardness.
Please provide your respective suggestions.
- Bangalore, India
A. Hi, Srinivasan. I appreciate the rack sketch, but I'm not there and can't explain what may have happened. But I persist that this doesn't look like chemical attack to me -- it definitely looks like an electrical burn from a short circuit, with this area of the part touching an anodic or grounded item. Good luck.
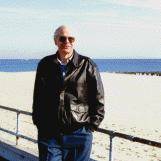
Ted Mooney, P.E.
Striving to live Aloha
(Ted can offer longterm or instant help)
finishing.com - Pine Beach, New Jersey
A. Dear Srinivasan,
Zinc Nickel plating is one type of zinc alloy plating which is having high temperature & corrosion resistance among zinc alloy plating.
Zinc nickel ratio composition in zinc nickel alloy chemical (bath Solution) is Zn:Ni = 10:01 and normally bath parameters range is Zn (8 to 12 grams/litre) Ni (0.8 to 1.2 grams/liter which is controlled by AAS
⇦ on
eBay
or
Amazon [affil link] method or XRF method.)
zinc nickel plating ratio deposition in zinc nickel alloy plating is Zn (85 to 90 %) Ni (10 to 15%) which is high resistance.
While nickel percentage is more than 18% in deposition and zinc percentage is less than 82% in deposition, during environmental tests ( salt spray test) direct appear red rust. Salt spray corrosion resistance is less when nickel % is more than 18 in deposition.
Process Engineer - Tumkur, Karnataka, India.
Temperature for Zinc Nickel Plating bath
Q. Hi,
May I know the suitable temperature for zinc nickel solution to achieve best plating parts.
The higher the temperature will cause the higher the time to plate?
by V Narasimhamurthy
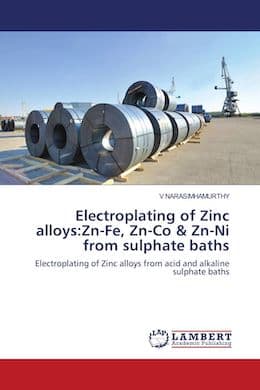
on eBay or Amazon
or AbeBooks
(affil link)
production engineer - johor bahru , johor. malaysia
November 18, 2014
? Hello Norazma,
Are you plating with an acid or alkaline Zn - Ni solution?
Process Engineer - Phoenix, Arizona USA
Q. Hi,
Alkaline zinc-nickel.
production engineer - johor bahru , johor. malaysia
A. Hello Norazma,
Most alkaline Zn - Ni baths run at about 25 °C (77 °F). The best bet is to consult the Tech Data Sheet for the bath from your Zn - Ni supplier. If you don't have one, ask your bath supplier. Proprietary plating solutions dictate temperature ranges. As far as the second part of your question, higher temps would normally speed up the deposition process. Are you having trouble maintaining the bath temp? Keep in mind higher bath temps will have an effect on the final finish cosmetics. Good solution movement, cathode bar agitation, and maintaining tight bath temp ranges is the key to consistent plating.
Process Engineer - Phoenix, Arizona USA
Q. Hi
I'm Venugopal working in R&D department. I need the details of how zinc nickel forms on steel component? What is chemical formula of zinc nickel plating? Normally in zinc nickel coating zinc percent is higher -- then why white rust is not forming as in zinc plating?
Regards
- Chennai, India
November 17, 2014
Q. My problem is that there are no suppliers of the chemical "RODIP ZNA YELLOW" in my region; please help.
RAO FARMAN ALI- islamabad Pakistan
May 16, 2015
A. Hi Rao. That product is a powdered chromate formulation from Atotech for bronze iridescent chromating on zinc-nickel plating. Other suppliers such as Macdermid and Enthone presumably can offer equivalent products if access to Atotech products is not possible in your region. Good luck.
Regards,
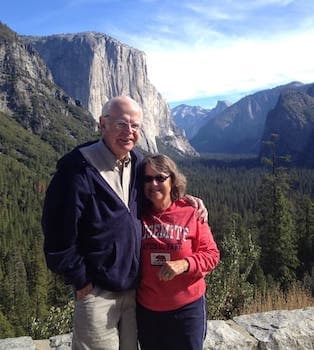
Ted Mooney, P.E. RET
Striving to live Aloha
(Ted can offer longterm or instant help)
finishing.com - Pine Beach, New Jersey
Adhesion Problem with Zinc Nickel on Stainless Steel
Q. Hello everyone.
We are having problem with adhesion with Alkaline Zinc Nickel on hardened stainless steel. The problems occur on hardened martensitic stainless steel. For Copper or Al or Be alloys, plating works wonderfully, also on 4130 steel. Adhesion is not a problem on those base metals.
We also CAD plate the stainless steel, and we do it well. The only problems we have on stainless steel is with Zn-Ni. I have read the other inquiries on here, but have not seen a response from the original question starter with results.
I think, like many, that it is a surface pretreatment issue with this, but why would Cadmium plate adhere well and Zn-Ni won't?
We have tried different activating methods, lower amp and longer nickel strike, different nickel strike rations, NiCl:HCl 2:1, 1:1, and still the same.
The method I use to test the pieces is by getting around 5-7 pieces and shake them in my hand. They hit each other, and the plating comes off. If I do this with Zn-Ni plated on bronze alloys, the plating will not come off(peel off.) If I do this test with cadmium plated stainless steel, the plating will not come off either. Only on Zn-Ni plated stainless steel.
I have recently tried a little coat of Electroless Nickel after my nickel strike, then plate Zn-Ni, and the plating still comes off. It comes off in a finer dust, but it is still coming off.
This has been problematic for us, we have done it in both acid and alkaline baths, and same results on stainless steel.
Can anyone that use to have similar problems help me out with this???
Btw, the composition for our S.S is :
Carbon 0.07 maximum
Manganese 1.00 maximum
Phosphorus 0.04 maximum
Sulfur 0.03 maximum
Silicon 1.00 maximum
Chromium 15.00 - 17.50
Nickel 3.00 - 5.00
Copper 3.00 - 5.00
Columbium plus Tantalum 0.15 - 0.45
Please help, is driving me nuts!
Somethings to look at: successfully remove passive oxide film on the stainless steel to be able to plate Ni strike followed by Zn-Ni. But HOW? have tried 5 minutes in 30 percent HCl, and it flaked off less, but still flaking/plating coming off.
Thanks!
Employee - San Diego, California
May 26, 2015
by Jack Dini
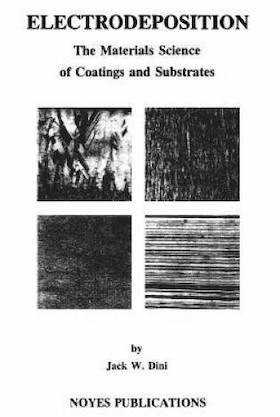
on eBay or Amazon
or AbeBooks
(affil link)
A. Hi Oscar. I think it should be possible to determine whether the nickel strike layer is peeling from the stainless steel substrate, or the zinc-nickel plating is peeling from the nickel strike layer. The corrective action would differ based on where the problem originates.
If the nickel strike is not sticking, I suppose it's possible that the parts aren't really clean. Try to get a look at Dini's "Electrodeposition", which has a chapter on "Adhesion" with lots of good data on nickel striking of stainless steel .
If the nickel strike is sticking, but the zinc-nickel plating doesn't stick to it (which seems to be what you are reporting) there may be too long a delay between the strike and the plating. The strike is a nickel-rich surface which rapidly passivates. Possibly the cadmium plating is better at dealing with this marginal passivation of the nickel strike. You may learn something from plating "stress tabs" in a Hull Cell ⇦ huh? . Good luck.
Regards,
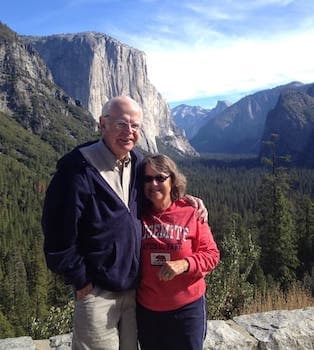
Ted Mooney, P.E. RET
Striving to live Aloha
(Ted can offer longterm or instant help)
finishing.com - Pine Beach, New Jersey
Pitted zinc-nickel plating
Hello everyone again!
Our zinc-nickel treatment has some problems lately. We are doing some parts for automotive clients that are getting pitted after the zinc-nickel plating bath.
The raw materials of the parts (that we made) are 10B22 in both cases. The first one (hexagonal) is hardened and tempered 8.8 (27-29 HRC) and the second one (plastic thread) is cemented, quenched and tempered (530 HV in surface and around 40 HRC in core). This I explain is because of the low efficiency of the bath in the second case. We need to plate for around three hours to get a 10 micron layer.
Both parts are pickled in hydrochloric around 10% (1/3 diluted 32%), rinsed and dipped in caustic soda ⇦liquid caustic soda in bulk on
Amazon [affil link]
before the plating bath. Our plating bath is a barrel semi-automatic one, with 30 kg barrels. Our zinc-nickel plating bath is a proprietary formula alkaline one, 12-15% Nickel. Later, the parts are blue chromated and ready to go.
Good parts, and two examples of bad parts.
Click pictures for high resolution photos.
We are experiencing this pitting for third time in the 6 years I am in this company, and we never got to know why.
I bring this to you, because many heads think better than one. Has someone seen anything like this?
Thank you in advance, and best regards!
Daniel
- Caneulas, Buenos Aires, Argentina
March 9, 2016
? Good day Daniel.
I have been following this thread as I will soon be implementing the process.
I do not have any experience as yet with the process, but I am doing research.
My question to you is, "Both parts are pickled in hydrochloric around 10% (1/3 diluted 32%)".
I would believe this is a 33% HCl solution.
What are the process parameters for pre-dip?
Regards,
Aerotek Mfg. Ltd. - Whitby, Ontario, Canada
Q. Hello Eric!
You are right, it is a 33% HCl bath, but we chemists sure are complicated: As the "pure acid" is not 100% but 32%, a 1:3 dilution will be 10,7% HCl, but for all practical purposes it is correct to say it is a 33% HCl bath.
Pre-dip is as follows:
-HCl 25-40% 20 min (with wetting agent and Fe inhibitor)
-Rinse
-NaOH 30% 30 min (it doesn't have to be this amount of time, but it depends on how much time the parts are plating).
Then it goes right into the plating bath. We don't believe it is an acid pitting because of the way it appears: On the head and the point, always from the middle to the edges. We think it could be some noise in the electric circuit that could make the current flow the other way... We are trying to test it now, as it happened again today.
If we have more data I will be posting it on Monday or Tuesday. Thank you in advance!
Best regards,
- Cañuelas, Buenos Aires, Argentina
A. The localized attack to the ends of the parts could suggest something in the material. Is this limited to one coil/material of manufacture? I know it is the same material.
If you rule that out, I could be an End grain pitting/inter-granular attack. Is your acid inhibited? Are the pits visible prior to plating? Post acid activation? Inspect the barrels after every operation to help with trouble shooting.
- Toronto, On, Canada
Q. We are facing pit mark problem in zinc-nickel plating process, please share the causes path details
Lokesh Naik- Bangalore Karnataka, India
June 9, 2023
A. Hi Lokesh. You can read the above for some ideas, but for substantive help you'd need to share significant data rather than just an abstract question, e.g., Is this a new installation not yet plating satisfactorily, or an existing installation that went bad? Acid or alkaline? Barrel plating or rack? Any Hull Cell panel info to share? What kind of parts, what kind of steel? Frequency and timing of the pitting, i.e., 100% of the parts all the time vs. 1% of the parts on the night shift. Gas pits (bright, hemispherical) or acid attack pits? Have you looked at parts after the acid dip and before plating? Photos to mooney@finishing.com for posting here if possible please. Thanks!
Luck & Regards,
Ted Mooney, P.E. RET
Striving to live Aloha
(Ted can offer longterm or instant help)
finishing.com - Pine Beach, New Jersey
Q. Dear sir, we doing in alkaline zinc nickel plating and material condition is low Carbon steel, Rack plating. We are facing after plating pitted mark problem in the parts surface. Pre -cleaning - 2 water rinse - anodic cleaning -2 water rinse - acid pickling 10-15% HCl(33%)- 2 water rinses.
And neutralization is -5% (NaOH), then main bath. This is our process flow, please suggest how to control the pit marks in process.
- Bangalore, India
June 10, 2023
(You're on the 1st page of this topic) Next page >
Q, A, or Comment on THIS thread -or- Start a NEW Thread