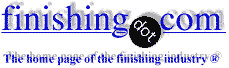
-----
Current density required for chrome plating
Current question and answers:
⇦ Tip: Readers want to learn from your situation;
so some readers skip abstract questions.
Q. Can we give 60 Amps/dm2 for 7.06 dm2 surface area part?
Does this affect the part?
- India Bangalore
April 14, 2021
A. Hi. 60 Amps/dm2 is a very high current density for most plating, so can we assume you are doing hard chrome plating? I believe that proponents of the reversible rack system say it's okay even with a straight Sergeant's bath with the chrome tank running at a high temperature. Tell us the details of your plating installation for a proper answer. For conventional decorative chrome plating this would probably be too high to be feasible.
On the other hand, if this was a typo and you actually meant 60 Amps total for a surface area of 7.06 dm2, then no, that's unlikely to be enough current to get any chromium to deposit at all.
Please tell us who you are, what your job is, what the situation is that prompted you to ask this question.
Luck & Regards,
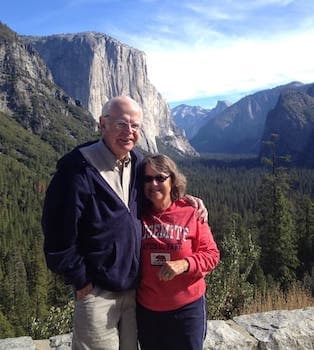
Ted Mooney, P.E. RET
Striving to live Aloha
(Ted can offer longterm or instant help)
finishing.com - Pine Beach, New Jersey
Q. It is engineering chrome plating as per AMS2460 and I am working in one of reputed aerospace company. The required chrome plating thickness before grinding is 250-400 microns and the base material of the part is 15-5PH steel.
We decided to go with 60 amps/dm2 for part's surface area of 7.06, and the total current which we have given to the part is 420 amps. The reason behind going with 60 amps/dm2 is chrome plating cycle time which was 18-20 hrs when we gave 40-50 amps/dm2. moreover AMS2460 doesn't say anything about current density; even I couldn't find anything in the web about current density limitations for chrome plating and I don't know what is the technical reasons behind not to go with 60 amps/dm2.
We have validated the 60amps/dm2 through testing like porosity, adhesion, hardness and hydrogen embrittlement on panel as per AMS2460 which are passed. Sorry I couldn't reveal the concentration and temperature of the bath due to some restrictions.
The valuable feedback appreciated well.
- India Bengaluru [returning]
by Clarence H. Peger
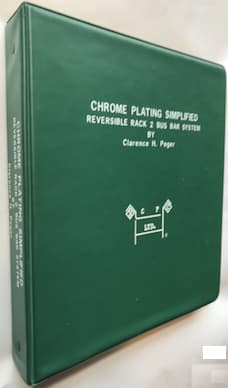
(copies are avail. in select libraries)
Very rarely available from
eBay or Amazon
or AbeBooks
(affil link)
A. Hi again, cousin. Thank you for the excellent reply. I assume you realize that temperature is central to the answer though. The allowable current density at 143 °F is way higher than at 130 °F let alone lower temperatures.
The upper limitation on current density is the point at which "burning" occurs. If you are not experiencing burning, I think all is well. Although 60 A/dm2 is higher than most installations can achieve, it is not unprecedented -- Clarence Peger advocated his 'reversible rack' chrome plating system for decades, operating at higher than conventional temperatures, with conventional Sergeant plating bath but higher than usual concentrations, and current densities in this range.
If you can find some of Peger's writings it should help re-assure you that your results are feasible. His book, "Chrome Plating Simplified" is not currently available for sale anywhere in the world according to Worldcat, but there are 4 or 5 libraries claiming to have copies (https://www.worldcat.org/title/chrome-plating-simplified-reversible-rack-2-bus-bar-system/oclc/2399195?referer=di&ht=edition).
You can try contacting Hard Chrome Plating Consultants, Inc. in Cleveland, OH but I am not confident that they still exist because their website looks to not have been modified in the last 4 years. Continued good luck!
Regards,
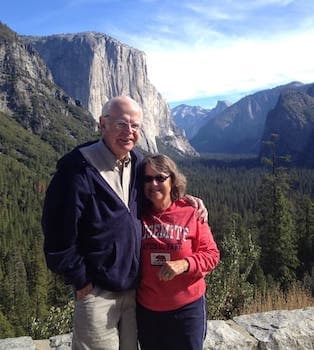
Ted Mooney, P.E. RET
Striving to live Aloha
(Ted can offer longterm or instant help)
finishing.com - Pine Beach, New Jersey
⇩ Related postings, oldest first ⇩
⇦ Tip: Readers want to learn from your situation;
so some readers skip abstract questions.
Q. What is the current density for chrome plating?
Thanks,
Francisco Hernán LedesmaFacultad de Ingeniería - Buenos Aires, Argentina
2003
A. Hi Francisco. It is always difficult to put limits on an answer like this, due to variations in temperature, agitation, anode-cathode spacing, etc.; guidebooks will tell you 0.25 to 6.0 amps per square inch. But I have personally never seen chromium plated either at 0.25 or at 6. If this is decorative rack plating, and nothing unusual, you should probably aim for more than 1 but less than 2 amps per square inch and you should be okay. Best of luck.
Regards,
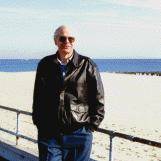
Ted Mooney, P.E.
Striving to live Aloha
(Ted can offer longterm or instant help)
finishing.com - Pine Beach, New Jersey
2003
A. The current density will vary with the conductivity of the solution and the distance of the anode from the cathode. The further they are apart, the more resistance there is and the more electricity is turned into heat versus conversion of the chrome ion to chrome metal. The max current that you can apply before "burning" is dependent on the temperature of the bath. Obviously, there is a minimum amount to have it plate, but a higher minimum to have "good" plate and a higher amount for a better plate rate. Ted's 1-2 ASI is a good middle of the road set of numbers for many applications.
James Watts- Navarre, Florida
2003
Q. I'm a student in production engineering department, and I have a question in how to get the optimum current density for chrome plating and the heating temperature of the solution. These are by calculation or is it by experience? Thanks in advance.
Ahemd Saad- Egypt
January 30, 2013
A. Hi Ahemd. It's probably a bit of each. There is science available, like Faraday's Law and Ohm's Law which apply to plating. But there are also things that are beyond our present analytical capacity, so empirical knowledge is used.
For example, while Faraday's Law says that one gram equivalent weight will be reduced for each 96,485 coulombs, we know empirically that most of that current is wasted to the liberation of hydrogen and only 10 to 25 percent of it actually goes towards deposition of chrome -- but I don't think we fully understand the science of why.
Similarly, we know that higher temperatures mean greater ion mobility and allow faster plating, but I don't think we can yet really calculate exactly what will go on in the boundary layer. Rather, we determine the maximum rate at which we can plate without burning from experience rather than formulas. Good luck.
Regards,
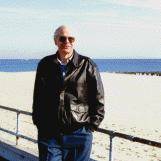
Ted Mooney, P.E.
Striving to live Aloha
(Ted can offer longterm or instant help)
finishing.com - Pine Beach, New Jersey
⇦ Tip: Readers want to learn from your situation;
so some readers skip abstract questions.
Q. So can you tell us what a current density should be if the bath operates at 40-45 °C?
Bojan Koren- Bovec, Slovenia
August 24, 2014
A. Hi Bojan. 40 °C (104 °F) is a pretty low temperature. I'm not familiar with going lower than 110 °F (43 °C) even for decorative chrome. As James observes above, it depends on spacing, concentration, etc., but I'd guess that it could be 1-2 Amps per square inch unless you are using a reversible rack system.
Regards,
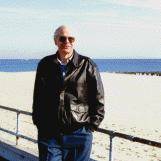
Ted Mooney, P.E.
Striving to live Aloha
(Ted can offer longterm or instant help)
finishing.com - Pine Beach, New Jersey
Q. Why it's too low? From decorative chromium the temperature it's around 45 I haven't seen that it's over 50. Here we keep temperature at 45 for chrome and 55 for nickel bath. Current density in nickel is 2.2 A/cm2^dm2 [ed. note: 2044^20.44 Amps/square foot] and in chrome is 9-10 A/cm2^dm2 [ed. note: 8361-9290^83.61-92.9 Amps/square foot].
- Bovec, Slovenia
A. Hi again Bojan; I think we may be having some language difficulties. I did not say that 45 °C was too low, I said I haven't seen less than 43 °C. Upon looking at your numbers a second time, I should probably have suggested that I think the temperature range seems too wide or loose, rather than saying that the low end sounds too low.
I think there is an error in your Amperage figures, as they seem impossibly high.
Regards,
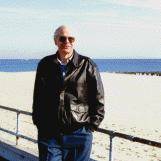
Ted Mooney, P.E.
Striving to live Aloha
(Ted can offer longterm or instant help)
finishing.com - Pine Beach, New Jersey
Q. Yes I made a mistake on current densities for nickel we have 2.2 A/ dm2 not cm2 and for chromium is 9-10 A/dm2
Is the temperature and current density ok for chromium? We sometimes get whitewash on plated parts, but I think it's something wrong with with current, maybe its not always DC but also AC current? Only my opinion. Have to check the sulphate content next week when I get barium chloride.
- Bovec, Slovenia
A. Hi again. I am not a chrome plating expert, and we already have many threads on whitewash in chrome plating, so it might be productive if you put "whitewash chrome" into the google custom search engine to read some good discussions.
Typical current densities for decorative nickel-chrome plating are about 40 amps/sq. ft. for the bright nickel and 150 amps/sq.ft. for chrome. So now I think your current densities are on the low side. I don't know for sure what will work best in your specific case (your particular parts might have have sharp corners that will burn at higher current density), but if you run some Hull Cell ⇦ huh? panels, I think you'll possibly see that your current density can and should be increased by about 50% or a little more.
Regards,
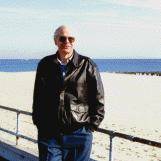
Ted Mooney, P.E.
Striving to live Aloha
(Ted can offer longterm or instant help)
finishing.com - Pine Beach, New Jersey
A. Current Density required for chrome plating, 150 amps per sq.ft at 110 °F Temperature .
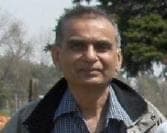
Popatbhai B. Patel
electroplating consultant - Roseville, Michigan
Q. For decorative chromium?
Bojan Koren [returning]- Bovec, Slovenia
A. Yes
Regards,
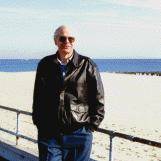
Ted Mooney, P.E.
Striving to live Aloha
(Ted can offer longterm or instant help)
finishing.com - Pine Beach, New Jersey
Q. We operate at 9,5 A/dm2 and 45 °C. I know this is very low current density, but they are working like this for many years and I came to this company only a few months ago. Don't know why they chose so low current density.
Bojan Koren [returning]- Bovec, Slovenia
A. Hi. That's 88 ASF, and sounds very low for chrome plating, but depending on the shape of the articles maybe it's not outrageous.
If it's working well, it's fine :-)
Regards,
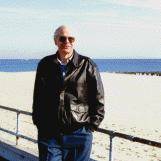
Ted Mooney, P.E.
Striving to live Aloha
(Ted can offer longterm or instant help)
finishing.com - Pine Beach, New Jersey
A. For each makeup of a chrome plating solution there is an optimum parallelogram shaped box on a temperature vs amperage graph that gives the best plate.
At your temperature and amperage, you are probably getting smooth uniform bright plate. BUT, you are on the very edge of getting either soft or whitewash plate on portions or all of your part.
A slightly higher temperature would allow you to carry a bit more amperage and still get smooth plate.
For zero reason that I can understand, the cooler tank actually has a bit higher deposition rate for any given amperage.
- Navarre, Florida
Q. Now I checked the current density from last month and I realized that the men who was in charge he didn't use constant current density for chrome. He was changing current density for chrome.
The maximum was around 230 ASF to 75 ASF :)))
Now I know why the workpieces were yellow -- 75 ASF is way too low for chromium!
The temperature is constant, but he always changes current density; that's not good.
I have one question: few days ago the workpieces had dull and milky deposit. The temp was kept at 45 °C and the current density was 102 ASF. Reason for this is low current density, am I correct?
- Bovec, Slovenia
A. Hi Bojan. Unfortunately, plating can be complicated and it is little more than guesswork to try to attribute a verbally described defect to a given cause. But, yes, no chrome deposition at all takes place below a threshold low current density, and the surface will be relatively "yellow" because chromium is significantly "bluer" in comparison to nickel plating.
Lots of things can cause a milky deposit, from passivated nickel to incorrect catalyst ratio, to excess brightener in the nickel tank, to burning being mislabeled as a dull or milky deposit.
I think what may be missing here is a "hanging Hull Cell" which would allow you to see the effect of varying current densities. And, of course, double-checking the numbers you are being given! -- as we see above for several months now, the numbers you've given have been wrong time and again :-)
Good luck.
Regards,
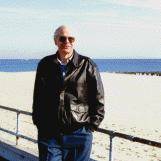
Ted Mooney, P.E.
Striving to live Aloha
(Ted can offer longterm or instant help)
finishing.com - Pine Beach, New Jersey
A. Hi all,
Ted says he's not a chrome plating expert...but his reply above shows otherwise.
Bojan, you are advised to go through those contents with a fine piece of comb....
Good Luck.
- Penang Malaysia
Q. Hello thanks for your opinion.
I don't have hanging hull cell, but I made a hull cell test of chromium bath and I can see at which current density the plating begins. Above 7 A/dm2 [65 ASF] the plating begins and in the range from 7 to 10 or 11 A/dm2 [65 ASF to 93 or 102 ASF] the deposit is white, cloudy. From 12 A/dm2 on [111 ASF] the bright deposit is plated. So from this hull cell test I think the reason for milky deposit of workpieces was too low current density.
What did you mean by this "burning being mislabeled as a dull or milky deposit"?
At current density 10 A/dm2 the deposit could not be burned. Or am I wrong?
Burned deposit should look like grey stain and rough when you touch it. This I read in one book.
- Bovec, Slovenia
A. Hi Bojan. Everything you said sounds right, and you apparently do not have any burning.
Regards,
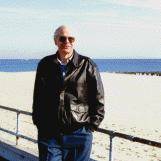
Ted Mooney, P.E.
Striving to live Aloha
(Ted can offer longterm or instant help)
finishing.com - Pine Beach, New Jersey
A. Hi.
For the benefit of Bojan, for decorative chromium plating, using a mixed catalyst bath, I have plated using 30 A/dm sq., 40 °C bath temperature, plating time 5~10 seconds (important) ... I was pleasantly floored it could be done that way. Good Luck.
- Penang Malaysia
Q. I never heard about this to plate only 5 to 10 seconds??
We use SRHS chrome bath and we plate always for 4 min at different current densities from 9 to 25 A/dm2
- Bovec, Slovenia
Q. I've never heard of plating for 5 to 10 seconds either, Cheah, and I'm not confident that it offers much corrosion protective value.
Per the MFSA Quality Metal Finishing Guides, required chrome plating thickness ranges from 0.1µ for mild interior exposure to 0.3µ for severe service. But 4 minutes sounds long; I would have expected about 30-45 seconds for mild service and 2 minutes for severe service to be typical.
Even at a full 30 A/dm, I figure you'd need 15 seconds to get even 0.1µ at an estimated 18% efficiency. Can anyone quote a chrome plating time or thickness from a current automotive spec?
Regards,
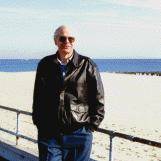
Ted Mooney, P.E.
Striving to live Aloha
(Ted can offer longterm or instant help)
finishing.com - Pine Beach, New Jersey
A. Hi.
I know ... I have plated decorative chrome for many years using the standard 40~45 °C, 10~20 A/dm2, plating time 1~3 mins. What I'm saying is that, I've tested and run using above unusual current density and plating time, the decorative chrome looks similar to that of the standard parameters...
Of course, as Ted suggests, the chrome deposit may be thin (less than 0.1µ) and corrosion resistance may suffer.
Regards.
- Penang Malaysia
Thanks for the insight into this approach, Cheah. We all continue to learn from each other.
Regards,
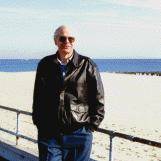
Ted Mooney, P.E.
Striving to live Aloha
(Ted can offer longterm or instant help)
finishing.com - Pine Beach, New Jersey
Mixed catalyst chrome burns at low current density one day, and not another
Q. Hello again.
Im getting confused with this current density for decorative chrome.
Yesterday we plated workpieces at 13 A/dm2 [120 ASF] and became burned at so low current density? Confusing is this that last week my colleague was plating at 19 A/dm2 [175 ASF] and the workpieces were okay.
Can anybody help me with this strange situation? Why some workpieces get burned at very low current density and other are not burnet at even higher current density?
He use chromium bath with two catalysts, sulfur and fluoride, at temperature 43-45 °C, 320 g/L [43 oz/gal] of chromic acid.
- Bovec, Slovenia
November 14, 2014
![]() |
A. Because of the low efficiency of chrome plating it is extremely line of sight. simply change the position of your anodes relative to the edge that is burning. - Navarre, Florida November 14, 2014 A. Hi, - Penang Malaysia November 15, 2014 November 16, 2014 A. HI,BOJAN ![]() Popatbhai B. Patel electroplating consultant - Roseville, Michigan |
Q1. What is current density for hard chrome plating at 55 °C [131 °F] temperature?
Q2. We are not getting required deposit rate in hard chrome plating if we give current density and time as per technical data.
sudhakar chavan- pune Maharashtra
December 23, 2017
A1. Hi cousin Sudhakar. If you can tell us whether you are using reversible rack system, and thieves in the high current density areas, and whether you are using Sergeant's, SRHS, or HEEF bath, people may have further comments in addition to the input offered above. But a hanging Hull cell in your own tank would probably be the best way to know the acceptable plating range. Good luck.
A2. Hello again, I got/saw your 2nd posting after answering your first one. So I appended it here. What current density are you applying and what deposit rate are you getting? Efficiency as low as 10-13% is possible for some baths some times, and up to 25% for HEEF. Posting abstract questions when you obviously have actual data available to post isn't an efficient way to proceed; please tell us what deposit rate you are getting that you consider too low, and the current density and time rather than just saying they are as they should be :-)
Regards,
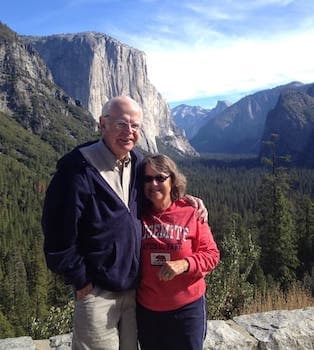
Ted Mooney, P.E. RET
Striving to live Aloha
(Ted can offer longterm or instant help)
finishing.com - Pine Beach, New Jersey
December 2017
Chrome plating a 75 mm dia. x 4 m long shaft in a facility built for shock absorber pistons
Q. I run hard chrome plating shop and do piston rods for shock absorbers. now I want to do hard chrome platting on a shaft of 75 mm dia. and length 4 meters. My rectifier can deliver max 1200 Amps @ 12 V. Can we do it horizontally with conforming anode of lead of dia. 125 mm and length 400 mm with multiple holes.
I am able to move above anode at very very slow speed longitudinally over the shaft.
Is shaft rotation a must? What is the minimum current density required so that plating happens. Thanks.
- Indore, MP , India
July 1, 2020
A. Hi Jagdish. The surface area of that shaft is about 94 dm^2 (10 ft^2), so your rectifier is on the small side but probably just barely workable. But I would be very dubious about the chance of success with that anode or with horizontal plating without rotation. Very few things are actually impossible, but I think you will regret it if you accept this job unless the volume of the order justifies building a proper facility to do the job right :-)
Luck & Regards,
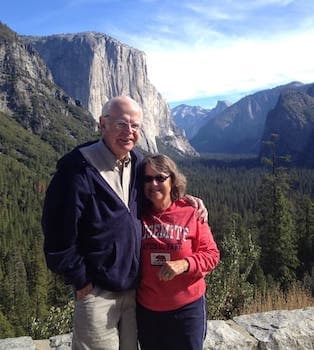
Ted Mooney, P.E. RET
Striving to live Aloha
(Ted can offer longterm or instant help)
finishing.com - Pine Beach, New Jersey
July 2020
Q, A, or Comment on THIS thread -or- Start a NEW Thread