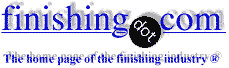
-----
Consumption of nickel anodes
adv.: Supplier of Copper Anodes, Nickel Anodes, Bismuth Metal, & Other Metal Products for Industry & The Arts
Q. Hi
I have Watt's Nickel tank and my question is: the rate of nickel anode consumption is very high -- so how I can control the rate of nickel anode consumption? And what is the optimum rate of consumption in g/m2 of nickel anodes.
Thanks,
- Giza, Cairo, Egypt
2003
A. Mr. Gomaa,
Unless something is very unusual with your nickel plating process, all of the nickel that dissolves from the anodes goes onto the parts. So you need to approach it from the other direction, i.e., you have to decide how thick the nickel plating must be. Then however much nickel you plate is how much nickel anode you will consume.
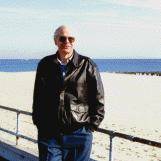
Ted Mooney, P.E.
Striving to live Aloha
(Ted is available for instant or longterm help)
finishing.com - Pine Beach, New Jersey
2003
A. Theft
Robert Stewart, CEFScientist - Venice, Florida
August 8, 2023
Q. Hi sir,
First I know when the nickel anodes are dissolved the nickel ions go to the cathodic parts. But you do not understand what I mean: the rate of nickel anode dissolution is very high which increases the nickel content in solution over the optimum point and decreases the area of anodes compared to the area of the cathodic parts. There is no equilibrium between the nickel consumption by parts' area -- and anodes dissolve, so I tend to add new anodes to adjust the ratio of area between anode and cathode. So maybe the pH needs adjustment or the brighteners need adjustment too? But I need first the optimum rate of anode consumption with thickness 15 microns at current density 5 amp/dm2 finally.
Thanks,
- Giza, Cairo, Egypt
2003
QUICKSTART:
Michael Faraday discovered the interesting and essential fact that the amount of electroplating that occurs is exactly proportional to the applied current. If you know the current and the length of time it was applied for (the ampere-seconds or 'coulombs'), you can calculate exactly how much plating will occur.
To understand why very simply, just recognize that what happens in electroplating is you use a battery or power supply to pull electrons from the anode and pump them over to the cathode through copper wire or bussing. And what happens within the plating tank in response is that the atoms on the anode, which have now been stripped of their valence electrons, dissolve into the plating solution as positively charged ions ('cations'), and migrate through the solution towards the negatively charged cathode. When the cations reach the cathode they rejoin those electrons and become atoms again.
Faraday's Law says that 96,485 ampere-seconds will move 1 gram equivalent weight of metal from the anode to the cathode. If you know the atomic weight of the metal and its valence (the atomic weight of nickel is 58.69 and it ionizes in the plus 2 state) you know how many grams you move: 29.85 grams of nickel for every 96,485 ampere-seconds. Since you know the density of nickel and you now know the mass you'll move, you know the volume of nickel you'll move. And since you know the surface area, you can divide the surface area into the volume to know the thickness. All issues of the Metal Finishing Guidebook have an appendix called "Electrochemical Equivalents" which can save you time working through those conversions and directly give you the required ampere-hours per square foot for 0.001" deposit of each metal.
One tweak may be necessary though. Sometimes the excess electrons you pump over to the cathode won't patiently wait for positively charged metal ions to get there. Instead those electrons will react with the water in the plating solution and release hydrogen gas:
2e- + 2H2O => H2^ + 2OH-
The percentage of the applied electricity which actually goes towards depositing metal rather than generating hydrogen gas is termed the efficiency. The efficiency of nickel plating is probably about 95% under normal circumstances. Some plating is virtually 100% efficient. Chrome plating is notoriously only about 15% efficient.
A. Hi,
I'm with Ted on this one. The rate of anode dissolution is determined by Faraday's law, same as the rate of nickel plating. Anode current efficiency can be calculated the same as cathode current efficiency (actual weight dissolved/weight predicted by Faraday's law).
The pH, etc. has very little to do with the rate of anode dissolution. The corrosion of nickel in an anode basket is electrolytic, not chemical. One caveat to all of this: If, for some reason, your nickel is not corroding properly, you may be generating large amounts of anode residue, rather than having the nickel dissolve. Then you would need clean your basket more often and add more nickel squares, or whatever form you are using.
- Thompson, Manitoba, Canada
2003
A. As I understand your problem, you are dissolving more nickel from the anodes than you are depositing onto the cathodes. As everyone above has said, nickel dissolution and deposition follows Faraday's Laws and both sides of the chemical reaction are pretty close to 100% efficient. If we assume your bath composition is basically in specification, then it must mean that your anode and cathodes are electrochemically out of balance. If that is not the case, then you must be depositing nickel onto something other than your workpieces. Have you checked for any unwanted nickel deposits in the tank caused by stray currents - if you have any, this will affect the apparent efficiency of your process tanks, because you will be applying a lower cathodic current density to what you were aiming for. Consequently, you will be taking out less nickel from the tank than you originally thought (and calculated for) and so when you calculate what you are actually taking out and what you are actually putting in, there will be a difference. Similarly, if you are only partially dissolving the nickel and getting lots of sludge in your anode bags, you will be losing more nickel from the anode than you are putting down on the cathode. However, if the concentration of nickel ions in solution is increasing, then you must be either dissolving the nickel anodes chemically, which is most unlikely if the electrolyte is in specification, or you have a stray electric circuit with a cathode that does not let the cations deposit onto it. Finally, are you sampling your bath at the correct tank volume - if there is a lot of water evaporation, which in Egypt I would suspect there is, you must make sure your tanks are kept at the correct volume or you will get misleading concentrations for all components of the electrolyte(except water!).
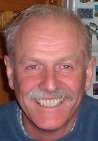
Trevor Crichton
R&D practical scientist
Chesham, Bucks, UK
2003
Very good answer, Trevor. Thanks!
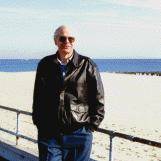
Ted Mooney, P.E.
Striving to live Aloha
(Ted is available for instant or longterm help)
finishing.com - Pine Beach, New Jersey
A. Dear Aly,
What is the concentration of chloride ions in your bath check it. If you want to know with out analysis. Check the stress of your deposition if it high chloride is too high.
- Cairo, EGYPT
A. Dear Sir,
Hi I think maybe you have a problem in your bath which leads to passivation of articles at cathode during plating. For ex. in case you have more brightener or overdosing in the bath the cathode will become passive very fast. So instead of nickel deposition the Hydrogen will involve at cathode so anode dissolves correctly but the deposition of nickel ion at cathode is not according Faraday law. please check the sign of passivity on nickel for ex. the chrome deposition, white stain,.. The other possibility can be stray current in the bath. if you have stray current in bath maybe instead of nickel deposition on some metallic device ( heater, heating coils,..) the hydrogen gas forms.
electroplating - Tehran, Iran
2003
Q. Hello to everybody!
Does nickel anode dissolve if there is no electric current running through the cell?
I have high nickel concentration in my nickel bath. We have two lines one is running every day all the time, this one is ok. Other one is only running few times a month and in this one I have higher nickel concentration. Is it anode dissolving also when there is no current passing through? Thanks for answers!
- tolmin slovenia
June 19, 2014
A. Yes, the nickel will dissolve in the acid portion of the solution. You should notice a rise in the pH.
Remove the anodes when not in use. I like to store them in a plastic drum of water with a few drops of whatever acid you use in the tank. This will keep them from oxidizing or going passive.
For the tank solution, I would decant whatever % it is in excess and store it for required additions or eventually a new makeup. The decanted tank then needs to have the necessary amount of water wetting agent and acid to bring the tank up to normal.
You could use insoluble anodes for plating out of the high nickel tank, but this will affect internal stress and the pH.
- Navarre, Florida
A. Hi Bojan ,
Yes Yes Nickel anode dissolves, if there is no electric current running through the cell.
Approximately one gram of nickel anode is dissolve in one litre of nickel (at ambient temperature, pH - 4.5 to 4.9) plating solution in one day.
Remove the nickel anodes when not in use or while the concentration of nickel content is maximum in the bath.
Regards,
Process Engineer - Tumkur , Karnataka , India.
Hi, thanks for answers!
It's not so simple to remove anodes all the time. They are quite heavy and it takes much time to move them.
The bath is set to have 65 g/L of Nickel now it has 71 g/L .This week it will run for a few days I will check the nickel content at the end of the week.
- tolmin slovenia
Q. Hello,
I am studying nickel anodes in nickel electroplating bath. I have seen this thread and I am a bit surprised. The nickel anodes (Nickel pellets in Ti basket) dissolve in the bath without current? Can anybody explain this please?
I thought Ni anodes dissolve only electrochemically!
In my bath, I suspect this phenomenon as my Nickel concentration increases too much in the bath.
Thank you for your help
Best Regards,
- Berne, Switzerland
December 13, 2019
A. Hi Thomas. I would start by simply reducing the number of anode baskets slightly. We put your inquiry on this thread, where you posted it, because you refer to this thread's other comments, but thread 7124 addresses nickel concentration rise more directly, as you probably know because you've discussed it on that one previously. Good luck.
Regards,
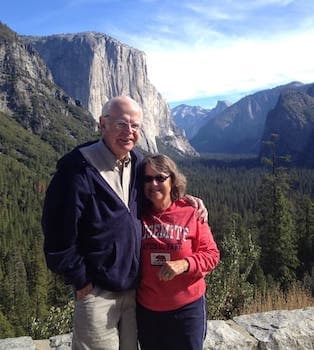
Ted Mooney, P.E. RET
Striving to live Aloha
(Ted is available for instant or longterm help)
finishing.com - Pine Beach, New Jersey
A. Nickel anodes dissolve at 98-100% Faraday efficiency but plate out at only 95-97% efficiency. This discrepancy can lead to nickel growth in the plating tank if not reduced by dragout or decanting.
Lyle KirmanConsultant - Cleveland Heights, Ohio USA
![]() |
- Berne, Switzerland December 17, 2019 A. All of the above is technically correct, but, let's also point out that the concentration level of the chloride greatly affects the dissolution of the nickel metal. Also the kind of anode is a factor in dissolution. ![]() Robert H Probert Robert H Probert Technical Services ![]() Garner, North Carolina ![]() |
Q. Hello everybody,
Thank you for your reply Robert. Okay, so there is a chemical dissolution of the nickel anodes in a nickel bath. The rate of this dissolution is a function of the Chloride concentration and the type of anodes (pure Ni, Ni-S...)
If I reduce my number of anodes, I should reduce this chemical dissolution, is it right?
Thank you again,
Best Regards
Thomas
- Berne, Switzerland
December 19, 2019
A. Hi plating people.
A high or rise in nickel concentration is from chloride and sulfuric. But it come from the the nickel if it does not have 100 percent plating efficiency, that is if it only has 80-90 percent.
Best regards,
4 generation plating engineering
Sweden
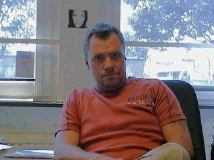
Anders Sundman
4th Generation Surface Engineering
Consultant - Arvika,
Sweden
Q, A, or Comment on THIS thread -or- Start a NEW Thread