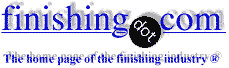
-----
Nickel Buildup In Bright Nickel Solutions
[an error occurred while processing this directive]Q. We are experiencing build up of nickel in our bright nickel electroplating solutions. As a result we have to remove solution and dilute intermittently. What causes this and what can we do to get a balance?. We are unable to return dragout to the tank due to this buildup. We use nickel anodes in titanium baskets.
Bert J. Sherwood- Los Angeles, California USA
2001
![]() |
A. The reason nickel conc. increases is due to the difference in efficiency. The nickel dissolves from the anode at 100% efficiency whereas the nickel deposits on the cathode at 95% efficiency. Thus the increase in nickel in your solution. One way to minimize this increase in nickel concentration is to use insoluble anodes for some of the soluble anodes but the anodes need to be separated from solution by a membrane or your plating solution will get out of balance. There are proprietary systems out their that can solve your problem. ![]() George Shahin Atotech - Rock Hill, South Carolina 2001 |
A. Your anode efficiency is greater than your cathode efficiency. Either raise the cathode efficiency (could be a contact problem or a chemistry problem) or lower the anode efficiency (less surface area). Another point: is this a new problem, or one you've had for a while? Has anything changed?
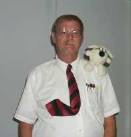
James Totter, CEF
- Tallahassee, Florida
2001
A. We have experienced this problem in the past and remedied it by decreasing the anode area by removing a basket.
E. MacKenna- Houston, Texas
2001
2001
A. Hello:
You have got some good replies for your query. I will try to tackle it in a slightly different way. Mostly when nickel solution builds up, it is Nickel sulphate which increases. The simple reason being the difference in anode and cathode efficiencies and the general habit of adding sulfuric acid for pH adjustment.
What happens in these build up problems, we stop adding nickel sulphate but we still add nickel chloride because it goes down as the bath plates.
We can manipulate a little here, instead of adding sulfuric acid we can add hydrochloric acid which further replenishes the required nickel chloride and also adjusts pH. But we do not end up increasing the nickel metal concentration in the bath as we are not adding any nickel salt. So now you have 3 options or I would prefer a combination of all 3:
- 1. Adjust your anode to cathode ratio (also you want to see if all anodes and cathodes are getting the right amount of current).
- 2. Use some insoluble anodes.
- 3. Start using hydrochloric acid for pH adjustments.
- 2. Use some insoluble anodes.
If I were you I would prefer a combination of 1st and 3rd approach.
Regards,
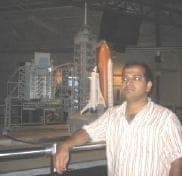
Hemant Kumar
- Florida, USA
Q. Hi, Mr Hemant Kumar Bansal
I have read your article and I find it very interesting about the nickel sulphate increase and nickel chloride decrease. I am not quite sure how does it work, is that like nickel chloride will use up in the plating process, therefore more nickel chloride will need to add to the solution, and that causing the nickel build up?
Other thing is that where did the chloride go? Do they become chlorine gas and release to the atmosphere?
Thanks
Chi Cheng- Baltimore, Massachusetts
2001
A. Hi Chi Cheng
I am not saying that in nickel plating, nickel sulphate increases and nickel chloride decreases.
Because generally we add sulfuric acid to control the pH of the bath so it creates more sulphate ion in the bath which eventually end up in increasing the nickel sulphate concentration. Whereas nickel chloride is consumed as chlorine is evolved at anode and at the drag out(basically nickel chloride's function is to provide solution conductivity whereas nickel sulphate is the primary source of nickel ions, essential in the plating).
As we do not add hydrochloric acid so we end up going down in chloride concentration and we have to add nickel chloride and not nickel sulphate.
Here is a danger. Each addition of nickel chloride is further increasing NICKEL ION as well which reacts with sulphate ion of sulfuric acid and create more nickel sulphate within the bath.
These situation worsens if we have minimum drag out.(Principally we try to reduce drag out but it does not help if we have already high nickel concentration).
To be short, I think sometime we may add hydrochloric acid instead of sulfuric acid. But be careful it reacts faster.
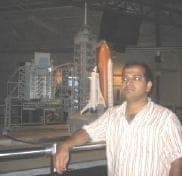
Hemant Kumar
- Florida, USA
2001
Q. Thanks for your response, it really gives me a much clearer idea now. But you mention about the adding of HCl will have a faster reaction, would you tell me more about that? Is that the pH will drop faster? A stronger exothermic reaction? Is there any problem to do it in practice?
Also how much should I put in? Can I use a simple mass balance to calculate the amount to add?
And for your solution 1, about the efficiency, how can I find out/calculate the efficiency of the system? Is that based on surface area, is that a book I can read?
Again, thanks a lot!
Chi Cheng [returning]- Baltimore, Massachusetts
2001
![]() |
2001 A. Dear Chi Do not worry about HCl additions. In Nickel plating you can start adding it without any difficulty. pH drops little faster but you can continuously measure it to see how much you need. The efficiency of Nickel plating you can generally assume at 95%. Its hard to check the efficiency in the lab but you can deposit some plating on a mandrel and measure the weight deposited versus ideal deposition (based on Faraday's laws).That is your % efficiency. Regards ![]() Hemant Kumar - Florida, USA 2001 A. I do not know of anyone else with your problem. At 140 °F, a bright nickel bath will usually have enough evaporation to allow replenishment with some of the dragout. Everybody adds liquid to a nickel tank because the solution level falls; do you have a leak in a steam coil, or something like that? (rain leaks from the ceiling, etc.) If you can increase your temperature to 145, you will use less brightener. I don't understand how adding hydrochloric acid will help your problem, and you can only add so much before your chloride will get too high. Is there something unusual about the way you are running this nickel? What kind of dragin/dragout do you get with your parts? Do you have a drip cycle going in that is longer than the drip leaving the tank? ![]() ![]() Tom Pullizzi Falls Township, Pennsylvania |
Q. Dear Hemant Kumar Bansal
I have checked the previous data, there wasn't any example we added in nickel chloride to increase the chloride level, therefore I guess it is not the reason in our case.
About the efficiency, I didn't know much about the Faraday's law. Also is that right to calculate the efficiency by a lab experiment? Isn't there any effect by the actual plating tank itself, I mean the surface area, the nickel bag...etc.
Also, is there any possible effect from chemistry composition in the plating solution?
And again, if the efficiency is the main factor of this problem, what should I do?
Thanks
Chi Cheng [returning]- Baltimore, Massachusetts
2001
Q. Hi. Everyone
I got the same problem for "Nickel Buildup In Bright Nickel Solution", I adjust pH use sulfuric acid or Hydrochloric Acid based on the nickel sulphate or nickel chloride Concentration. But the problem still here. Thanks!
- Midland, Ontario, Canada
February 17, 2011
July 12, 2011
A. Warning! too much chloride is not good for the ductility of the deposit.
In this way: as chloride increases the
tensile strength goes up
Hardness goes up
ELONGATION GOES DOWN
INTERNAL STRESS GOES UP
For some applications one has to be careful; for example, on parts where welding is necessary, firearms, parts exposed to heat or parts which receive some kind of bending.
I suggest finding the cause of the build up if that is a problem.
Actually I don't know why the nickel build up is a problem or its consequences.
without measurement is difficult to say how much is too much.
- Bucaramanga Santander Colombia
Q. We use R-round`s on bright Nickel. What should be the proper relation between cathodic-anodic area?
Thank you so much
Process Engineer - Guadalajara, Jalisco, Mexico
August 30, 2011
A. Hi, Bernardo.
Approximately 2:1 anode:cathode ratio is typical. Good luck.
Regards,
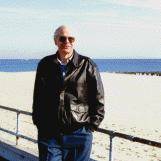
Ted Mooney, P.E.
Striving to live Aloha
(Ted can offer longterm or instant help)
finishing.com - Pine Beach, New Jersey
August 31, 2011
Too many anodes in my Nickel electroplating tank?
Q. Hello,
I'm working on Nickel electroplating. I have a big tank (400 L) with a rack with a lot of parts. I have also some anodes (Ti baskets with pure Nickel pellets). I'm studying the ratio anode/cathode surfaces and the effect of the number of anodes.
So my question is : Is there a risk to have too many anodes in my nickel bath? So, if my ratio Anode/Cathode surfaces is very big, it should be fine. In my situation, I find a ratio of around 5.
Thank you for your help! Let me know if you need more information.
Best Regards
Thomas
Engineer - Switzerland
November 14, 2019
A. Hello Thomas,
Most nickel baths require an anode to cathode ratio of 1:1 minimum. I have found that a 2:1 ratio works well. What you have to consider however is that the baskets face the parts and cover most of the cathode area. I have also found it is beneficial to have the outside of the rack extend 1.5" beyond the outside edge of the anode basket. The reason for this is that the high current density area is the outside of your rack(s), and this technique will help you with a tighter distribution thickness throughout the rack. If your nickel metal concentration in the bath is not climbing with the current ratio, and Your deposit thickness is where it should be, I really wouldn't be too concerned.
Retired - Winston Salem, North Carolina USA
November 20, 2019
Q. Hi,
Thank you very much for your reply. So it is not a problem to have too much anode surface compared to the cathode surface. I thought it was not very good because it could affect the dissolution efficiency of the anode if the current density was not enough. But it should be as you told me.
I completely agree with you Mark, the geometry and placements of the anodes are important to ensure a good thickness distribution on the cathode. For that I use a software to simulate my electroplating process.
My question was initially on the effect of the number of anodes. I have seen a lot of topics on the numbers of anodes but only in the case we have NOT enough anodes. I wonder what can do too many anodes in a nickel bath.
Best Regards
Thomas
- Berne, Berne, Switzerland
November 21, 2019
November 2019
Here are two things that occurred to me, which might not apply to your situation, but might help us not mislead other readers ...
1. Plating is complicated, and thumb rules sometimes apply only to very specific things. Excessive/insufficient anode area can cause problems in some types of plating, but it can be complex. For example, in hexavalent chrome plating, different anode-cathode ratios can cause reduction/oxidation of chrome between hexavalent/trivalent and can be a major design issue. In copper plating it is my understanding that excessive anode area (and/or use of non-phosphorized anodes) can cause passivation via a build-up of a less-conductive copper-rich film around the anodes, whereas in nickel plating passivation of the anodes is more likely from insufficient rather than excessive anode area. Nickel plating usually uses sulfur-depolarized anodes to aid dissolution, and sometimes controlled amounts of chloride as well. As Mark says, excessive anode area can lead to too much dissolution and thus a rising nickel concentration -- which brings me to thought #2 ...
2. As I've learned from thousands of amateur and hobbyist Q&A's here, non-optimum operational parameters don't always manifest themselves as poorly plated parts, but sometimes simply as difficulty in maintaining the equilibriums we need for production plating. A hobbyist may successfully plate a part and call it done, and claim it was easy ... whereas the production plater is concerned not just with that one part, but the condition he has left the plating tank in when he finished. Thus, you might be able to successfully plate a part in a plating solution with higher concentration than the readers suggest, but if such operations result in leaving the tank with an ever higher concentration of nickel and ever higher pH, or whatever parameters are creeping up or down on you, you may not consider it okay even if you're doing satisfactory plating over the short run :-)
Regards,
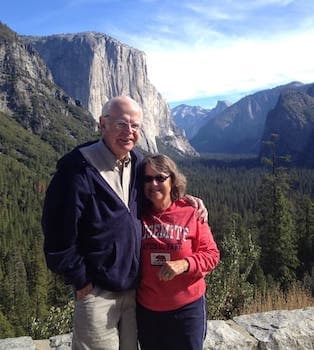
Ted Mooney, P.E. RET
Striving to live Aloha
(Ted can offer longterm or instant help)
finishing.com - Pine Beach, New Jersey
November 22, 2019
Q. Hello,
Thank you for your reply Ted. I totally agree with you with your comments but I have little questions on them.
First point :
You write : " in nickel plating passivation of the anodes is more likely from insufficient rather than excessive anode area."
Why insufficient anode area could cause passivations of the anodes? Just because the current density can be excessive in some areas of the anodes and the anodes can be passivated in these areas, is it right?
And you write too: "As Mark says, excessive anode area can lead to too much dissolution and thus a rising nickel concentration". Why an excessive anode area could produce too much anodic dissolution? If I have too much anode surface, the local current density at the anode should be lower and produce a good dissolution at an efficiency of 100%. I can't have a dissolution more than 100% of efficiency, is it right?
For you second point, you are right! I have been working in a plating shop for 10 years and your comment is exactly what I see everyday. It is the first time I study the effect of the anodes in a nickel bath. Until now all is ok with our nickel baths but to study the anodes could help us to improve the process: maintenance, cost of the anodes, cleaning.
I have a second question in my mind! If a nickel bath is not in use for few weeks or months, is it better to remove the anodes from the tank? Is there a risk to leave them in the bath like chemical dissolution, passivation?
Thanks again,
Best Regards
- Berne, Switzerland
A. Hi again Thomas. My knowledge comes only from books, hanging around plating shops, feedback from consulting assignments, and curating this site for 25 years -- not from actually doing any plating myself. So there is a lot of stuff that I'm not qualified to comment on, but this thread 7124 offers lots of interesting perspectives & experience on this issue of nickel anode area earlier on in the discussion.
As for removing nickel anodes when not in use, it is recommended for Wood's Nickel Strike tanks because it is vital to hold the nickel concentration and pH low. But in working with many hundreds of nickel plating shops over my career, I've never seen one that routinely removed their anodes when not in use. However, if a tank is not going to be used for extended periods of weeks or months, I would expect problems like the anode bags clogging from disuse, the need to sand the contact hooks and anode bars, the desire to "magnet" the tank against fallen parts, etc., ... so maybe adding the removal/reinstallation of anodes to the periodic maintenance program makes sense anyway :-)
Regards,
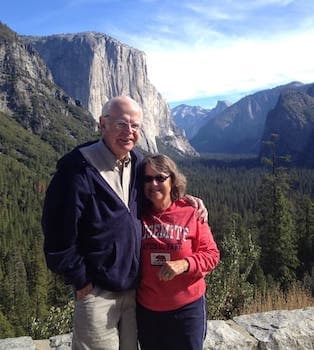
Ted Mooney, P.E. RET
Striving to live Aloha
(Ted can offer longterm or instant help)
finishing.com - Pine Beach, New Jersey
November 2019
Hello everybody, hello Ted,
Thank you for your new comments! As I have already seen through many messages you post, you have a long experience in the surface treatments :).
Ok for the removing of the anodes. It is not really necessary if the bath is used regularly. It could be removed if not used for a long period!
About the anodic surface, if anybody has comments, suggestions... let me know please!
Thank you
Thomas
- Berne, Switzerland
November 26, 2019
adv.: Supplier of Copper Anodes, Nickel Anodes, Bismuth Metal, & Other Metal Products for Industry & The Arts
Q, A, or Comment on THIS thread -or- Start a NEW Thread