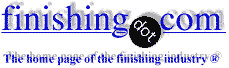
-----
Electroless nickel plating onto stainless steel Q&A's
Quickstart:
Stainless steels & high chromium steels acquire a passive oxidation layer nearly immediately. To successfully electroplate on them requires a proper "strike", the most commonly used of which is "Wood's Nickel", a plating solution with very high acidity and low nickel content. This solution simultaneously dissolves that oxide layer while depositing a thin layer of fresh nickel. That fresh nickel -- if not allowed to passivate -- is a good base for further plating.
Q. Hello, I am having adhesion issues between the nickel strike layer and electroless nickel. The substrate base material is a high chromium(~25%) alloy.
What nickel strike thickness should I am for? and would too thin of a thickness be causing the adhesion issues?
supplier quality - South Gate, California
December 12, 2024
A. Hi Robert.
The experiments referenced in the Jack Dini book mentioned on this page employed 2 minutes of striking in one chart he presented and 5 minutes in another, and produced shockingly good adhesion. Mallory & Hajdu mention 2 minutes at one point in their book. If you are at 2 minutes or more I don't think inadequate thickness is the issue. I would suspect that perhaps the nickel strike layer had been allowed to passivate before electroless nickel plating? It should be strike, quick rinse, electroless plating.
Luck & Regards,
Ted Mooney, P.E. RET
Striving to live Aloha
finishing.com - Pine Beach, New Jersey
Q. According to the Supplier's process steps, they seem to nickel strike less than 30 seconds, at 30 amps. They are achieving a 40-45 [µ" ? ⇩] on a SS coupon, but achieving less on the high chromium alloy, 25-34 [µ" ? ⇩].
Robert G- SG, California
Ed. note: Gibberish came through the email rather than a 'micro' symbol and 'inch' symbol ... we're just guessing.
A. Hi again. 30 Amps isn't usable info until we know the surface area of the component so the current density can be determined. Where did this nickel strike spec of 30 seconds come from -- it does sound awfully low to me.
We'll be glad to try to help ... but honestly, trying to troubleshoot based on what you tell us that your supplier's manager told you, based on what the plating foreman told him, based on what the operator told him, isn't often successful. Due to the interaction of so many steps, "walking the line" can often be the only practical way to fix things. Process instructions save us a lot of trial-and-error in duplicating or re-establishing a process, but they usually aren't detailed enough nor followed closely enough to be trusted for troubleshooting.
As Jack Dini notes in his book: "electroplating ... is one of the most complex unit operations known because of the unusually large number of critical elementary phenomena or process steps ... drawing on many scientific disciplines."
Luck & Regards,
Ted Mooney, P.E. RET
Striving to live Aloha
finishing.com - Pine Beach, New Jersey
⇩ Related postings, oldest first ⇩
Q. We have been asked if we can plate electroless nickel onto 'duplex' stainless steel.
We currently plate all of our processes onto the many different varieties of stainless steels that come our way -- usually without any particular problems. We use a high chloride nickel strike.
Our customer informs us that adhesion appears to be a problem (at another plater) so I am keen to get as much background information as I can.
I look forward to any suggestions.
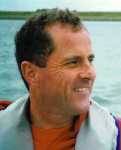
David Grimes
plating company - Farnham, Surrey, United Kingdom
1999
A. I have never heard of "duplex SS". Do you have a more common name for it?
With proper activation of the SS, proper maintenance of the strike solution and no delay getting into the follow on plating, you should not have a problem plating any SS.
Activating some metals like waspalloy, require that attention be paid to the activation step prior to the strike, which is an additional activation as well as the strike.
- Navarre, Florida
A Duplex stainless steels are those with ferritic/austenitic microstructure. The nickel or chromium coatings should be applied in order to obtain a local hardness of 50-60 HRC (for seat of rotating seals). Ceramic coating should be avoided. The candidate material is EN 1.4462 whose % composition is: C 0.030 max - Si 1.0 max - Mn 2.0 max - P 0.030 max - S 0.015 max - Cr 22 - Ni 5.5 - Mo 3.2 - N 0.18. Thanks.
Pasquale cirese [returning]aerospace mfgr. - firenze, Italia
2002
Q. I am looking for a solution for plating electroless nickel on Stainless Steel. I am currently doing electroless nickel on mild steel. I don't know the right procedure to plate on Stainless Steel. I appreciate your guidance. Thanks.
Nirav Mehta- Ahmedabad, Gujarat, India
1999
A. The exact alloy of the stainless will have an effect on the exact preplate chemicals, but it will basically run thru a suitable cleaner, an etch, Wood's Nickel strike and then the EN.
Time between rinses and process tanks must be an absolute minimum or you will have passivation and poor adhesion.
- Navarre, Florida
Q. Thank You James Watts for your speedy reply. There are two types of SS on which electroless nickel is required.(1) SS 316 & (2) SS 410. If you can give more details on composition as well as parameter of Wood's nickel Strike and EN, it will be highly appreciate.
Thanks you once again.
- Ahmedabad,Gujarat, India
A. An intermediate layer of a Wood's Nickel strike can lead to pinhole corrosion due to the high chloride content. An intermediate layer of a suitable strong acid gold strike bath minimizes porosity and leads to a better corrosion resistance (stainless steel and electroless nickel are quite precious compared to the nickel out of the Wood's nickel strike bath).
Uwe Manz- Aalen, Germany
A. Never had a problem with a Wood's strike. You can find the formula for a Wood's strike in nearly any plating book. I preferred to run it at the lower end of the nickel and the middle to slightly higher end of the HCl range in any formulation that I have seen. 316 SS can stand a lot stronger etch than 410SS and will normally need a longer time in the etch than 410.
James Watts- Navarre, Florida
Thanks Uwe!
Although I agree with James Watts that Wood's Nickel strike has been successfully used on countless millions of parts for many decades, I will certainly keep this idea of a gold strike in mind for special cases!
Luck & Regards,
Ted Mooney, P.E.
Striving to live Aloha
finishing.com - Pine Beach, New Jersey
Q. Jim, I have seen quite a few formulations to strike nickel with 120-240 g/l nickel chloride and 4-10% v/v hydrochloric acid. What is your best shot for plating on SS?
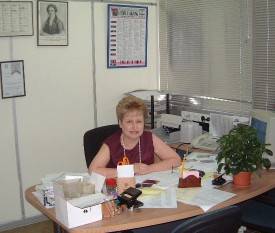

Sara Michaeli
Tel-Aviv-Yafo, Israel
by Jack Dini
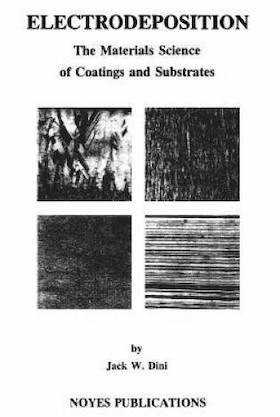
on eBay or Amazon
or AbeBooks
(affil link)
A. Hi Sara. I'd say the ideal composition is 240 g/l nickel chloride and 120 ml/l HCl. The reason I'd call it ideal is because, according to the Adhesion chapter in Dini's "Electrodeposition" ⇨
adhesion values of an incredible 70 to 80,000 psi were found to be possible with it.
Regards,
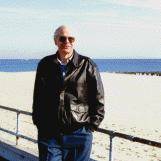
Ted Mooney, P.E.
Striving to live Aloha
finishing.com - Pine Beach, New Jersey
Multiple threads merged: please forgive chronology errors and repetition 🙂
Q. Is it possible and recommended to make an electroless nickel coating (about 10 micrometers thick) over AISI 329 (duplex stainless steel) parts?
Is it possible and recommended over stainless steels parts in general?
Is possible and recommended to do hard chromium plating (150-200 micrometers thick) over AISI 329 and/or stainless steels in general?
Thanks and best regards,
aerospace mfgr. - firenze, Italia
2002
A. It is possible to plate either EN or chrome on any stainless. Some are easier than others. Why would you want to do it or is it practical would depend on what you wanted it to do, which you did not say.
James Watts- Navarre, Florida
A. In order to plate electroless nickel or another metal deposit one must use a good alkaline cleaner, rinse, acid dip, rinse, and then Electroplate in a "Woods nickel strike" or a low pH sulfamate nickel strike, then plate in the desired plating solutions.
(a Woods nickel strike consists of 240 g/L nickel chloride and 10% by vol. hydrochloric acid. Plate at 40-100 amps/sq.ft.)
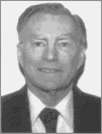
Don Baudrand
Consultant - Poulsbo, Washington
(Don is co-author of "Plating on Plastics" [on Amazon or AbeBooks affil links]
and "Plating ABS Plastics" [on Amazon or eBay or AbeBooks affil links])
High phosphorous electroless nickel plating flakes off of stainless steel
Q. I am trying to apply electroless nickel on stainless steel (316 steel type). The nickel I'm applying is high phosphorus and I'm currently dealing with the nickel cracking on some areas of the parts. Is there an additional step or process I should be doing besides the cleansing process to help adhere nickel with out it flaking or cracking? By the way, all the copper I'm plating has no issues with cracking or adhesion. I would appreciate the help out there.
Hector AmbrizResearcher - Albuquerque, New Mexico, USA
2006
A. 316 is a bit harder than 304 to activate but not that hard.
You fail to mention a nickel strike. 316 needs to have a proper Woods Nickel Strike and to not let it passivate before you get it into the EN tank.
- Navarre, Florida
by Sha, Wu, & Keong
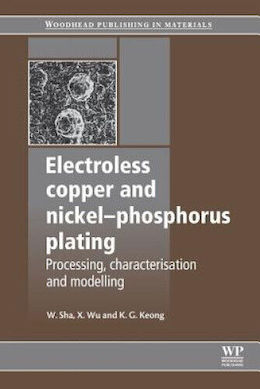
on eBay or Amazon
or AbeBooks
(affil link)
Q. I am using a high phosphorous electroless nickel system. On MS substrate the system is working great.
But as substrate turns to be stainless steel, the system fails to plate, plateout is issue and plating is irregular.
Could anyone suggest why there is irregular plating.
My plating conditions are as follows
Ni : 5.6 - 5.8 gpl
Hypo : 35 - 38
pH : 4.8 - 5.1
Temp : 87 - 90 °C
- Pune, India
April 8, 2014
A. Hi Yogesh. We appended your inquiry to a similar thread where you will learn that electroless nickel directly on stainless steel will likely be unsatisfactory. You must do a Wood's Nickel strike first. Good luck.
Regards,
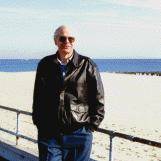
Ted Mooney, P.E.
Striving to live Aloha
finishing.com - Pine Beach, New Jersey
Q. I came to know from market that certain processes are available which will not require Wood's nickel strike for plating on Stainless steel. SS316 too.
Any input from experts?
- Pune, India
A. Hi again, Yogesh. Yes, there are alternatives to almost anything, including Wood's Nickel strike. Uwe Manz suggested a gold strike, and sulfamate nickel strikes are also possible. But your posting remains too cryptic for me to follow :-)
You're apparently trying to do high phosphorous electroless nickel directly onto type 316SS and it is not working. I and many others here have said that we wouldn't expect it to work without a Wood's nickel strike. But you seem to be saying it should because of something you "came to know from the market"?
Please try to clearly state what it is that you believe you heard so that we can discuss it less cryptically. Are you arguing that we're wrong and electroless nickel should work directly on your 316SS even though several of us said it won't, and it's also not working for you either?
People can't do a core dump of everything they've learned from decades of experience, covering every possible scenario -- you'll need to clearly state your question or hypothesis please :-)
Thanks!
Regards,
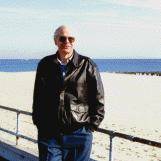
Ted Mooney, P.E.
Striving to live Aloha
finishing.com - Pine Beach, New Jersey
Q. How can I activate 316L stainless steel before electroless Ni plating?
How can I increase pH of a Ni electroless solution which I have bought? Is it possible?
- Tehran, Iran
May 6, 2014
A. Hi Mr. Reza. We appended your inquiry to a thread which explains the activation of stainless steel for electroless nickel plating. You can probably increase the pH by an addition of ammonium hydroxide, but it depends on the bath formulation. But a solid knowledge base is advisable, as even the reliable measurement of pH in an electroless nickel bath can be difficult, let alone the beneficial adjustment of it :-)
Luck and Regards,
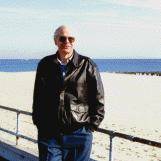
Ted Mooney, P.E.
Striving to live Aloha
finishing.com - Pine Beach, New Jersey
Need instruction for electroless nickel and nickel-chrome electroplating, step by step
Q. Hello sir
I am starting an electroless Ni and a Ni-Cr electroplating plating plant in Surat.
So give me a proper idea and full proper process steps one by one.
heat engineering works - Surat,Gujarat, India
June 3, 2014
A. Hi Gosai. Please start with our " Understanding Chrome Plating" article, which I hope you find interesting!
If I asked for step by step instructions for a heat engineering works you'd tell me you couldn't possibly cover that in a forum response, and I'm in the same position. Sorry! You should retain a plating consultant to get started in such an enterprise; and also hire experienced platers. If you can't do that, you should at the least review several of our "must have" plating books. I'd suggest starting with the Metal Finishing Guidebook, followed by Electroless Plating - Fundamentals & Applications by Mallory & Hajdu [on
eBay ,
Amazon, or
AbeBooks affil links]
. Best of luck!
Regards,
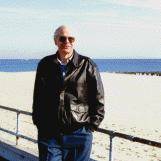
Ted Mooney, P.E.
Striving to live Aloha
finishing.com - Pine Beach, New Jersey
How to electroless nickel plate a low-carbon steel + stainless steel weldment
Q. I have a low-carbon steel (Consumet iron) part welded to a 304 SS part. The welding material is either 310 or 312 SS. To prevent corrosion to the iron part, I have to electroless nickel plate the whole assembly. I wonder if this is possible?
Dan Bui- Milpitas, California, USA
August 28, 2015
A. Dan,
I usually see people recommend a Woods nickel strike in order to plate anything onto stainless. Though I wonder, if the electroless nickel plates onto the carbon steel and ignores the stainless, does that still accomplish what you are really after, preventing corrosion on the carbon steel?
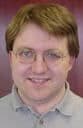
Ray Kremer
Stellar Solutions, Inc.

McHenry, Illinois
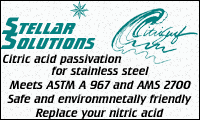
A. The EN will plate on the SS without a woods strike, but the adhesion will be unsatisfactory for most.
James Watts- Navarre, Florida
A. Most important - the strike nickel should have no more than 100-150 ppm iron, otherwise the adhesion will not be good.
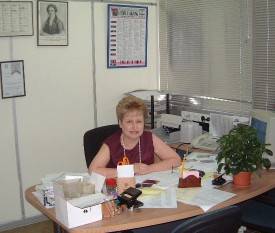

Sara Michaeli
Tel-Aviv-Yafo, Israel
Q. I am in the process of Electroless Nickel Plating SS 316 metal. I have been unsuccessful this far.
I believe that I am missing a chelating agent. These are the conditions I am using. 50 ml Deionized water, pH ~5, 90 °C, with the following chemicals.
Nickel sulphate Hexahydrate 1.3g
Glycolic Acid 1.25
Sodium Hypophosphite 1.250
Is this process accurate? If not, kindly advise me how to fix the problem.
Thanks!
Student - Austin, Texas
September 17, 2016
A. Hi Randal. Is the object of your work to develop your own unique plating process, or is the object of your work to do something with that electroless nickel plated stainless steel object? The reason I ask is that students often assume that the way one obtains a plating solution is by mixing commodity chemicals together -- but in fact "nobody" in the Western world ever does that ... rather, we buy proprietary plating processes that are the result of decades of careful development effort, and which contain small amounts of numerous trade secret chemicals.
Again, there is absolutely nothing wrong with a project aimed at developing specialized plating chemistry ... more power to you! But if you're just trying to get the darned thing plated, mixing up raw commodity chemicals is not the way.
I'm not sure exactly what "unsuccessful" means. It's not sticking, it's not thick enough, the vessel spontaneously plates out, or nothing is happening whatsoever? But the first issue to address is that you probably can't successfully plate electroless nickel onto stainless without preceding it with a Wood's Nickel Strike. So you might as well do things in that order from the start. You'll find numerous threads about Wood's Nickel on this site if there isn't enough info on this thread. And are you positive that the article is spotlessly clean to a waterbreak-free condition before you are attempting to plate it? Good luck!
Regards,
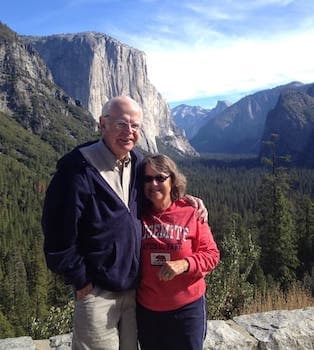
Ted Mooney, P.E. RET
Striving to live Aloha
finishing.com - Pine Beach, New Jersey
![]() |
Q. I am facing problem -- please help me all if you can. I will be very grateful to you all on this act of kindness. Ittehad traders - Peshawar Pakistan October 12, 2016 A. Hi Syed. Although electroless nickel might possibly work for a little while, it would be an outrageously expensive approach. If you cannot use a plastic tank in the sink, you can "line" the sink with vinyl tank lining sheets. Plastic (vinyl, polypropylene, polyethylene, teflon, vinyl ester fiberglass), not metal, is the first thing to consider when handling acids. Good luck. Regards, ![]() Ted Mooney, P.E. RET Striving to live Aloha finishing.com - Pine Beach, New Jersey |
![]() |
Electroless Copper plating on Cr/Ni Alloy?Q. I am working on plating Electroless copper on Cr/Ni Alloy. Currently I am facing an adhesion problem, as it was easily removed after wipe off. Any help on this is highly appreciated. Prabuddha SampathProduct designer - Sri Lanka May 4, 2017 A. Hi cousin Sampath. You may know ten times as much about electroless copper plating as I do (that wouldn't be hard), or you may be clueless so far -- and unfortunately I can't tell from your posting :-( You are talking about actual autocatalytic electroless copper plating ... you're not talking about a copper sulphate immersion deposit? Have you activated the alloy first by plating it with Wood's Nickel? Regards, ![]() Ted Mooney, P.E. RET Striving to live Aloha finishing.com - Pine Beach, New Jersey Q. Hi Ted, - Sri Lanka A. Hi Sampath. If you review the rest of this thread you will see that Electroless Nickel won't stick either. The problem is an inert film which forms instantly on the Nickel-Chrome alloy. You need a Wood's Nickel Strike before the electroless copper. The strike is a very dilute and very acidic solution which simultaneously dissolves that inert film while replacing it with fresh nickel. Regards, ![]() Ted Mooney, P.E. RET Striving to live Aloha finishing.com - Pine Beach, New Jersey |
Electroless Nickel Plating on 316SS Electrolyser Electrodes
Q. Hi there
Have been running a prototype of water electrolysis cell stack with SS316 electrodes and now is the time to try something different. Looking into Nickel plating as Nickel is inert vs. aqueous based solutions, so it is a technique of interest since we can improve the longevity of this stack to work for longer.
The SS316 electrodes have been previously pickled with citric acid, passivated with pure oxygen and then followed an activation method that involves electrical charging, see method below:
https://docs.google.com/document/d/1A1U3taekgloAkZ_chJCYF8rObBb4srBnc3Qni-9Ca3E/edit?usp=sharing
From reading a few posts in here, it seems that this method is not something common here among finishers, loading the metal finishing book now to grab some more info on procedures.
The electrodes have been bathing in work solution that is aqueous 10% Potassium Hydroxide since that procedure was run a few months ago. So they are very clean.
Is it worth to consider a HCl activation from where we are at? or Wood's strike? Or would that be an overkill? Or start again with pickling? And passivation again?
Have acquired an electroless nickel plating kit from a hobby plating supplier.
Just want to make sure we get it right first time as it is a long process to pull all the electrodes out of this stack.
Let us know if we are or aren't on the right track.
Much appreciated. RGK
- Brunswick Vic, Australia
May 12, 2017
A. Hi Renaud. My personal opinion is that there are a couple of problems here. First is the expectation that without prior experience you can "get it right the first time", on a self-supervised training exercise. I think that's optimistic and would suggest that as a minimum you plate & test a variety of scrap and sample parts before you "pull all the electrodes out of this stack".
You haven't mentioned yet whether this is a hobby project or a business project, but it is usual to send such parts to a plating shop with proven competence, rather than attempting to plate them ourself unless there are reasons to the contrary.
It may be a semantics issue rather than people in the plating industry being unfamiliar with a successful method for "activating" the stainless steel; the people writing in the blog you mentioned seem to have a meaning in mind about "activating" the electrode for its ultimate use, whereas when platers speak of "activating" metals they usually mean for subsequent electrodeposition onto them.
Yes, I think you should first do a Wood's Nickel or equivalent strike; I don't think it likely that the electroless nickel plating will properly adhere to these 316 SS electrodes without it. Good luck!
Regards,
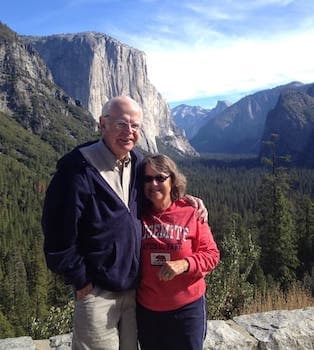
Ted Mooney, P.E. RET
Striving to live Aloha
finishing.com - Pine Beach, New Jersey
Q. Dear Mister,
I don't think you have much understanding on how many hybrids of types of projects out there and where you draw your line between "hobby" or "business", this is plain retarded, and I have no business in answering to this attack.
We have plenty of time at hand as the longer we spend developing our own techniques that keeps our engineering interns busy, the more money we get out of our R&D grant.
Therefore, what advantage would we have in shoving our budget into any of these, inefficient, money hungry "local businesses" that in the end spends it all in real estate scams, when we can empower ourselves with new knowledge in metal finishing for example. Metal finishing ain't rocket science, it has to be done right, just like about anything technical.
We will indeed test on some samples, we are not that stupid.
So are you only experienced in giving advice just to the guys that make metals look pretty or are you going to help us save some time on this plating job on these electrolytic active parts, or is that p'haps too challenging for you old timer?
By the way, congrats for your web interface it's just such a remarkable platform by its simplicity and its technicality, a pleasure to work with that.
- Brunswick Vic, Australia
Hi again. You seem to need an anger management course, and that's not our bailiwick so I'm done here thanks.
Luck & Regards,
Ted Mooney, P.E.
Striving to live Aloha
finishing.com - Pine Beach, New Jersey
"So are you only experienced in giving advice just to the guys that make metals look pretty or are you going to help us save some time on this plating job on these electrolytic active parts, or is that p'haps too challenging for you old timer?"
Nobody knows everything, but when it comes to Ted and the others who participate on this site, collectively there is more knowledge than you will ever acquire in a lifetime.
I suggest you take your offensive attitude and go away. Far, far away.
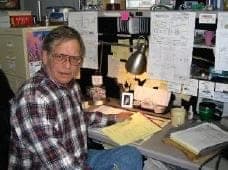
Jeffrey Holmes, CEF
Spartanburg, South Carolina
! Certainly a unique style of asking for advice!
I'm sure that Hydroxygas PTY would be unimpressed with how you present yourself in a public forum. Certainly somewhat less artfully than a "Marketing" person should!
The take home message is "politeness" especially when asking for advice, will always lead to better results!
- Ontario, Canada
February 28, 2023
! Thank you Finishing.com for all of your useful information. Your website is my final resource for finding practical solutions to my plating problems.
masih ghorbanArjan Co. - Tehran, Iran
June 20, 2017
Thanks for the kind words, cousin Masih. Please remember that trying to teach can be the best way to learn, especially when you surrounded by your peers on this site. I have many times confidently posted something here, only to be corrected by others -- and learned a lot from my ignorance :-)
Regards,
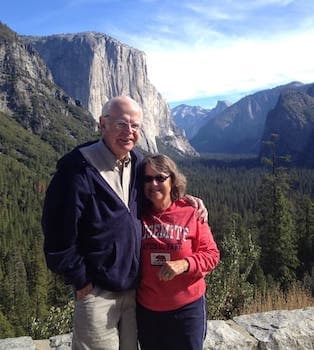
Ted Mooney, P.E. RET
Striving to live Aloha
finishing.com - Pine Beach, New Jersey
Flaking Electroless nickel on 304 Stainless
Q. I had some parts returned to us from our customer with flaking Electroless coating.
The material is 304 stainless that has a drawing requirement of "Electroless Nickel Plate IAW AMSC26074, Class 4, Grade C." While I understand that Class 4 is an incorrect callout for stainless steel, and a Grade C (0.0015) thickness may be risky, our Plater tells us that they processed the parts as stainless regardless of the drawing callout. He also tells us that a 0.0015" won't work on stainless steel.
Can someone recommend a Class and Grade more suited to this material?
Quality Engineer - Centennial Colorado, USA
February 2, 2018
A. Hi Michael
The purpose of any spec is to ensure that the finish meets design requirements. You cannot change a spec just because it is easier to achieve and we have no way of knowing what is appropriate. There has to be some reason why 304 needs additional plating.
You need to ask the design engineer why the original spec was called for.
You would not believe the number of times I have found a spec called .."because that is what the last part had".
Or it could be for a very good reason.
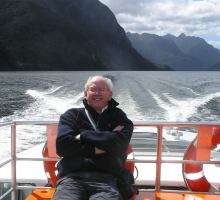
Geoff Smith
Hampshire, England
Thank you Mr. Smith.
I spoke to engineering and the reason for the nickel plating is to prevent galling in a threaded bore.
Hope this helps.
- Englewood, Colorado USA
A. I always question the wisdom of plating on stainless, since the point of the alloy is its enhanced corrosion resistance without the need for a coating, and the surface must be activated (the opposite of corrosion resistance!) in order to make the plating happen.
It stands to reason that a less expensive steel could be substituted as the substrate with no effective change to the final plated surface.
I'm not sure if the thought process is "but we always use stainless for this kind of part", without realizing that the need for plating negates the original purpose of using stainless.
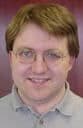
Ray Kremer
Stellar Solutions, Inc.

McHenry, Illinois
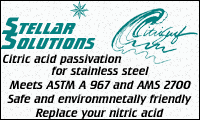
A. Hi Michael. The plating shop is probably right that 0.0015" inches is awfully thick for such an application and may be contributing to the problem of flaking. But I would start by determining for fact that the plating shop did perform the Wood's Nickel strike step, and any related processes that may have affected things, rather than simply accepting "we treated it as stainless steel even though you didn't tell us to".
Luck & Regards,
Ted Mooney, P.E.
Striving to live Aloha
finishing.com - Pine Beach, New Jersey
Q. WHEN AN ELECTROLESS NICKEL PLATED 430 STAINLESS STEEL PART HAS CONTINUAL IMPACT, SUCH AS A SPRING RETURNED PLUNGER, THE PLATING TENDS TO PEEL.
THE REASON FOR THE ELECTROLESS NICKEL PLATING IS THAT THE FERRIC STAINLESS STEEL WILL CORRODE EVEN WHEN PASSIVATED. THE PART IS CONTINUALLY IN CONTAMINATED POND WATER.
PLEASE SUGGEST A SOLUTION TO THE PEELING.
- LAWRENCEVILLE, New Jersey, USA
April 17, 2018
A. Hi Anthony. Why not make the plunger out of type 316 or other stainless which can withstand the pond water exposure?
Although it's possible that the adhesion is not good enough (thus explaining why plating is being knocked off), it sounds equally likely to me that the impact may be 'denting' the softer stainless steel and you are getting an eggshell effect, or as our friend Guillermo expressed it on a different thread, a sheet of glass on a soft sofa. If you can't make the plunger out of a better grade of stainless, perhaps you could make it of a heat treated plain steel, to which the electroless nickel plating would adhere better as well?
Regards,
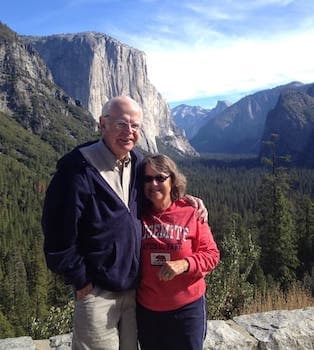
Ted Mooney, P.E. RET
Striving to live Aloha
finishing.com - Pine Beach, New Jersey
Injection mold tooling plating delamination issues.
Q. Stainless is the injection molding tooling material, teflon impregnated nickel is the electroless plating material. Would possible cause of delamination be brief use of PTFE mold surface release agent on the tooling "prior" to plating - to get first parts for inspection? The theory being that the PTFE would be difficult to clean off the tool surfaces 100% prior to plating.
There are non PTFE mold releases like Zinc Stearate spray ones that might be easier to clean off 100%.
engineer - San Jose, California, USA
September 26, 2018
A. Hi Joe. If you're saying that that's what was done, sure, it would be a major problem!
But if you're just starting to speculate about possible causes of poor adhesion, it is very hard to get reliable adhesion onto stainless steel and it probably requires a Wood's Nickel Strike before the electroless nickel. Good luck.
Regards,
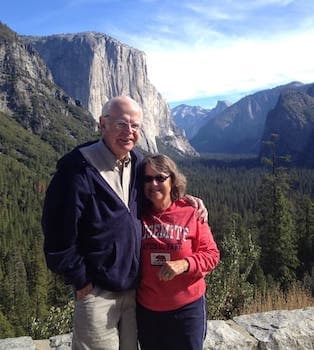
Ted Mooney, P.E. RET
Striving to live Aloha
finishing.com - Pine Beach, New Jersey
Teflon/ electroless nickel plating of 420 stainless mold tooling issues
Q. We have a 420 stainless injection mold insert with many pins vertical in a 16 x 24 array. The tops of these pins are lapped. Post lapping the perimeter of the pins are razor sharp. I know... not generally a good idea but for various processing reasons we have started that way. Not my choice.
We definitely have a plating delamination issue just under the tops of these pins on just a few pins (6). Could be the usual reasons for delamination not related to sharp edges but maybe the sharp edges starts the delamination.
However, some of these sharp edges themselves may have delaminated resulting in plastic degradation via very high shear stress on the plastic. The plastic being molded is polypropylene.
Questions:
1. What are the usual reasons for EN delam on SS?
2. The plater may be using a strike layer for good adhesion. My guess is sharp edges may cause problems with the strike layer resulting in edge delamination of the EN. Possible?
I will be doing my best to get the molder to break those sharp edges. Stubborn molder.
engineer - San Jose, California, USA
March 7, 2019
Ed. note: This RFQ is outdated, but technical replies are welcome, and readers are encouraged to post their own RFQs. But no public commercial suggestions please ( huh? why?).
Q. Electroless Nickel, copper and silver on stainless steel 316
Dear experts,
I found this thread is very helpful and informative.
My project will use the electroless plating method to coat Nickel, copper, and silver on SS 316. As experts recommended, Wood's Nickel should be conducted before electroless plating. Are there any other steps that I should do in the procedure?
Would you like to advise a specific Wood's Nickel formulation for SS 316? And which article or book I can find the step-by-step process?
As my application is under severe fluid flow conditions, adhesion is the most important issue. Could I do the heat-treatment to enhance coating adhesion?
Thank you so much and I highly appreciate any advice.
Incheon University - Incheon, Korea
March 11, 2020
by Jack Dini
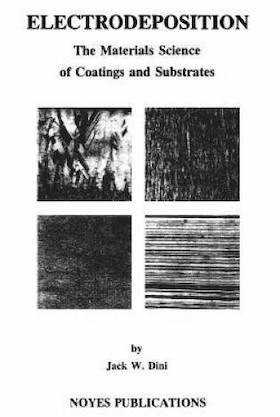
on eBay or Amazon
or AbeBooks
(affil link)
A. Hello Ho,
In my opinion the best discussion of Wood's Nickel and adhesion is in Jack Dini's "Electrodeposition" ⇨
and getting good adhesion between the Wood's Nickel and the stainless substrate is the most critical interface. But after a quick rinse, you must immediately do the next steps of Electroless Nickel and Copper plating because nickel plated surfaces passivate quickly. You might want to research whether a silver "strike" bath is required between copper plating and silver plating. Heating treating at any point will deactivate the surface and ruin the adhesion.
I'm not sure which steps in your project you are required to do personally, but just a reminder in case you didn't know it: plating is very jobshop oriented and the usual practice is to send parts out to a plating shop for plating. Becoming good at SST pretreatment, then Wood's nickel strike, then electroless nickel plating, then copper plating, then silver striking/plating is fodder for at least thesis projects, not one :-)
Regards,
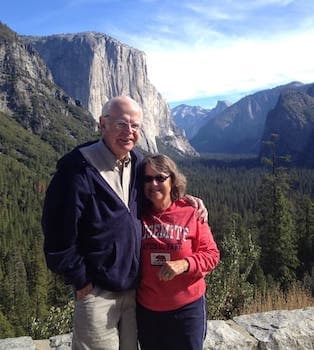
Ted Mooney, P.E. RET
Striving to live Aloha
finishing.com - Pine Beach, New Jersey
Q. Hello Mr. Mooney. Many thanks to your helpful advice. I tried to call many companies and shops in Korea, unfortunately, they do not cover all kinds of plating metals that I need. It requires many works as you mentioned, but I have no choice ;-). It would be very helpful please give me advice on the below issues.
1.In Woods strike step, the book said anodic 30-60 sec then turn to cathodic 2-6 min. What is anodic and catholic and how to set up? Could I apply Wood strike by brushing the solution on substrate?
2.Could you explain why heat treatment will ruin adhesion?
3.I have gathered and compared the information of electroless plating procedures of Ni, Ag and Cu plating on stainless steel 316 substrate as follows:
Nickel plating procedure: 1. Cleaning-> 2. Etching ->3. Woods nickel strike-> 4.Electroless Nickel plating
Copper plating procedure ver.1 : 1. Cleaning-> 2. Etching ->3. Catalyzing by Palladium-tin colloidal solution-> 4.Electroless copper plating.
Copper plating procedure ver.2 : 1. Cleaning-> 2. Etching ->3. Woods nickel strike -> 4.Electroless copper plating.
Copper plating procedure ver.3 : 1. Cleaning-> 2. Etching ->3. Woods nickel strike->4. Catalyzing by Palladium-tin colloidal-> 5.Electroless copper plating.
Silver plating procedure: 1. Cleaning-> 2. Etching ->3. 4. Catalyzing by Palladium-tin colloidal -> 4.Electroless Silver plating.
AMONG 3 versions of Copper plating procedures which one is correct/ or best work on SS 316? Do we need to do both Woods strike and Catalyzing by Palladium-tin colloidal?
FOR Silver plating procedure why we do not need Woods nickel strike?
- Incheon, Korea
A. Hello again, Ho.
Note that palladium seeding applies to non-conductive substrates, not metallic ones -- forget that completely.
Your second posting is now making me think that you are saying you have to build 3 of something for some reason -- one each with electroless copper, electroless silver, and electroless nickel (because I've personally never heard of doing electroless nickel followed by electroless copper).
Please start with a half page description of exactly what you want to build and why because all we're doing is confusing each other when I don't correctly understand what it is that you want. Thanks!
Regards,
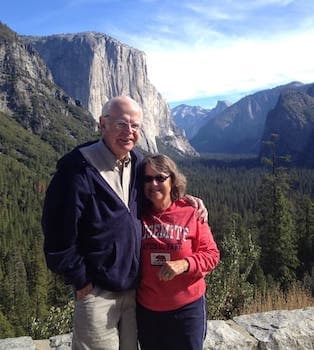
Ted Mooney, P.E. RET
Striving to live Aloha
finishing.com - Pine Beach, New Jersey
Q.
Dear Mr. Mooney. I am sorry for mixing things up at the beginning. You are right, I would like to do electroless plating of Nickel, copper, and silver SEPARATELY on three stainless steel 316 substrates.
FOR Nickel plating, I will do as following steps: Cleaning-> Etching ->Woods nickel strike-> Electroless Nickel plating.
FOR copper plating, I gathered info from research papers and books e.g. 'Electroless Copper and Nickel-Phosphorus Plating Processing' and 'Electroless Plating: Fundamentals And Applications' There are three different procedures:
1) Cleaning-> Etching -> Catalyzing by Palladium-tin colloidal solution-> Electroless copper plating;
2) Cleaning->Etching ->Woods nickel strike ->Electroless copper plating;
3) Cleaning-> Etching ->Woods nickel strike->Catalyzing by Palladium-tin colloidal->Electroless copper plating.
The books always recommend to do Catalyzing by Palladium-tin for Stainless steel substrate. I am confused which procedure is the best one?
FOR silver plating the book also recommend catalyzing by Palladium-tin as follow the procedure: Cleaning-> Etching ->Catalyzing by Palladium-tin colloidal -> Electroless Silver plating. Do we need to do Woods strike here?
IN ADDITION, In Woods strike PROCESS, the book said current density 'ANODIC 1A/dm^2 in 30-60 sec' then turn to 'CATHODIC 1A/dm^2 in 2-6 min' What is ANODIC and CATHODIC and how to set up?
Finally, I should not do heat treatment after plating as you advised. Could you explain why adhesion will be ruined by heat treatment?
This discussion is very helpful to me. Thank you so much for your enthusiastic advice.
Best regards,
- Incheon, Korea
March 18, 2020
A. Hi again. Stainless steel instantly forms an oxide layer on it, and electroplating with ideal adhesion requires the formation of metallic bonds between the substrate and the electroplated coating, which can't happen with an oxide layer in between them. Wood's Nickel Strike is a way of hopefully dissolving that oxide layer in acid and replacing it with nickel. Therefore (to my understanding) it is always required when plating on stainless steel (although there are alternatives like other nickel strike formulations or striking with gold).
Anodic and cathodic cycles mean, respectively, running the power supply with the workpiece being the positive electrode and the negative electrode. Yes, some sources suggest a short period of anodic current first; but many shops do not do it, and that single question of whether the anodic is necessary or beneficial could probably justify it's own research project :-) I'd simply skip it.
As previously mentioned, personally I think the best explanation of Wood's Nickel Strike is in Dini's "Electrodeposition" ⇨
I am not personally familiar with the use of palladium-tin catalyzing on stainless steel; I have only heard of it being used on non-conductive substrates. To summarize, I think the right thing to do is to clean and Wood's Nickel Strike all three of your pieces, then make sure nickel is catalytic (initiates the deposition) for your electroless copper and electroless silver, and to proceed to deposit the three electroless plating solutions onto the nickel strike.
Regards,
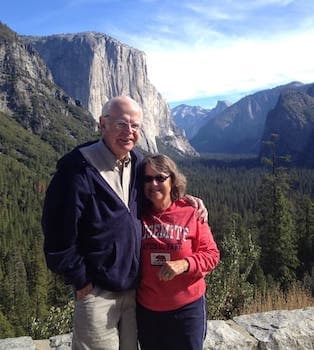
Ted Mooney, P.E. RET
Striving to live Aloha
finishing.com - Pine Beach, New Jersey
A. As others recommended, you need a nickel strike prior to the EN.
No need for anodic/cathodic, only cathodic.
The Palladium-Tin is used for non conductive substrate.
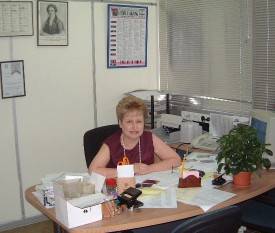

Sara Michaeli
Tel-Aviv-Yafo, Israel
⇦ on eBay or Amazon [affil links]
Q. I'm trying to something similar to a lot of others in this post. I have an assembly that is copper and 304SS that are brazed together using a CuSil (copper silver alloy) and a gold copper alloy. We have to plate high phosphorous electroless nickel because of its non magnetic properties.
The problem we have faced on this for a long time is peeling nickel on the stainless steal portions. After years of asking I finally have it approved to apply an acid gold strike. So I'm bead blasting the parts before plating, cleaning in alkaline cleaner, activating in a sodium fluoride activator, and then performing an acid gold strike at 100 ASF. This seems to have some success. I have some parts that have no flaking or peeling at all and others that are peeling on the stainless steel still. Any ideas what I could be doing wrong or better to obtain adhesion?
Ben Hartford- Laurens South Carolina
November 19, 2020
A. Hi Ben. The first thing I'd try is higher current density.
Luck & Regards,
Ted Mooney, P.E. RET
Striving to live Aloha
finishing.com - Pine Beach, New Jersey
Q. I appreciate your comments on electroless plating onto Stainless Steel but I wonder if you have any thoughts on plating onto atomized stainless steel?
Is it possible?
Ultimately, this is for a SS sintering project.
Thanks
Doug
- Hamilton, Ontario
February 23, 2023
A. Hi Doug. I'm not sure of the full implications of the term "atomized stainless steel", but I want to warn readers about conducting chemical operations on powders and powdered metals!
Some of the operations that we think we are quite familiar with will proceed hundreds of times faster, releasing heat & hydrogen explosively or almost explosively, when conducted on powdered metals because of their huge surface area compared to their volume. And, of course, the high heat they quickly generate can accelerate the reaction into a runaway. Please conduct any such experiments on very small volumes, and behind a shield inside a laboratory fume hood. Things can proceed very differently than our prior experience :-(
I'm not sure how you will electrolyze the powder for Wood's Nickel plating, but I wonder if the alternative -- sintering first, then vacuum impregnating and plating -- might be better.
Luck & Regards,
Ted Mooney, P.E. RET
Striving to live Aloha
finishing.com - Pine Beach, New Jersey
Q. Thanks for your response.
The idea behind plating first was to facilitate the sintering process.
That being said, I was asking about electroless rather than electroplating, although your cautions on reaction rates are appreciated.
"Atomized" stainless steel is more on the level of macroscopic pellets than say of the "Raney Nickel" surface areas :)
I was more asking if there is/was a discipline of plating powdered metals.
Thanks again for your response.
Doug
- Hamilton, Ontario
February 27, 2023
A. Hi again. The reference to electroplating was due to the fact that as discussed on this thread, Wood's Nickel strike or a similar electrolytic process seems to be required for adhesion of electroless nickel onto stainless steel. If the particles are microscopic, it is possible that the whole concept of adhesion strength loses its significance.
I am personally not aware of books or chapters or conferences about electroplating or electroless plating onto powders, but I'm confident that there are individual research papers. Scholar.google.com or www.finishingpublications.com might help.
Luck & Regards,
Ted Mooney, P.E. RET
Striving to live Aloha
finishing.com - Pine Beach, New Jersey
Thanks Ted,
The atomized particle size is, ironically "macroscopic" ie quite coarse.
That being said, I gained one particularly valuable bit of insight into plating in general -- that actually helped answer a question I had from my Grad Student days in Chemistry -- and that was why our senior tech bought prepared plating solutions (yet still referred constantly to Spon's Workshop Receipts) when building our dielectric cells.
The chemistry of plating is only a small, but complicated part of the process. It's the Art of Plating that makes this especially challenging. Commercial products solves at least one of these variables.
- Hamilton, Ontario
February 28, 2023

Q, A, or Comment on THIS thread -or- Start a NEW Thread