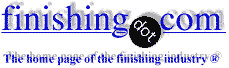
-----
Stainless Steel vs. Galvanized vs. Zinc Plated Fasteners
Q. Hi
We are selecting lockers for use inside the changerooms of an indoor saltwater pool. The lockers themselves are plastic but the hinges will be heavy duty zinc plated. We originally specified powered coated aluminum. How long would the zinc plated hinges last in this environment? Thanks
- Ontario, Canada
May 24, 2024
A. Hi SD. It's difficult to predict the life of things even in well known environments. Even tougher when we don't really fully appreciate the nuances of the specific installation. Zinc plated hinges could last 10 years if you're lucky ...
... but users may or may not hang damp salty towels on the doors, dripping onto the hinges; janitors may or may not wipe the lockers with bleach. Although salt water pools don't use chlorine to my limited knowledge, vapors may or may not be an issue. Managers may or may not store pool chemicals in some of the lockers.
Bare zinc plating is probably inappropriate for moist, salty environments, and will probably show rusting soon in such cases. Instead of zinc plating, I think ideally the hinges should be phosphated, e-coat primed, then painted.
Luck & Regards,
Ted Mooney, P.E. RET
Striving to live Aloha
finishing.com - Pine Beach, New Jersey
⇩ Related postings, oldest first ⇩
Q. My company is developing an outdoor product line which is primarily made up of 6063-T5 aluminum extrusions. We decided to switch to all 18-8 stainless steel fasteners for corrosion resistance, but there has been some second guessing as to why we didn't decide to use zinc plated steel fasteners. One reason for the questions is because of the higher cost of the stainless fasteners. In our application, a hex bolt is slid into a channel in the aluminum extrusion, and a the assembly is fastened together with stainless steel brackets. The concern that we have is with the potential for galvanic corrosion due to the fact that we have dissimilar materials in direct contact with each other.
My question is, would zinc plated fasteners be a suitable alternate to the stainless steel fasteners? How would the appearance of the bolts (rust) compare to that of stainless over a period of years in an outdoor environment? How much galvanic corrosion would we see with the zinc plated fasteners as opposed to with the stainless steel?
Thanks for any help you can provide?
- Milwaukee, Wisconsin
2002
A. I have seen stainless fasteners used on architecturally anodized aluminum in outdoor exposure without any substantial problems, and suspect that it will be acceptable. I am a bit confused by your somewhat offhand reference to stainless steel brackets because these would (theoretically of course) cause the aluminum to galvanically corrode regardless of the fastener material, and being bigger in surface area than the fasteners should probably be a bigger concern.
You probably know that, were it not for its toxicity, the ideal fastener material is cadmium plated steel. It is so close to aluminum on the galvanic scale that there is no galvanic corrosion, it is corrosion resistant itself, if thick enough, and it has great lubricity. Nonetheless, cadmium is a cumulative poison, should be reserved for only the most critical applications, and even there is being rapidly phased out.
The next best material is aluminum plating or coating, again because the galvanic potential is zero. You can investigate Ivadizing for vapor deposition of aluminum, or AlumiPlate for electroplating of aluminum. But I fear that you may find the cost unacceptable for anything but airplanes.
All of the above not withstanding, you didn't mention how the aluminum is corrosion proofed, so the question remains a bit open. But zinc plating is not a good idea in my opinion, and I think it will be short lived. Stick with the stainless :-)
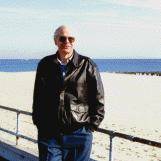
Ted Mooney, P.E.
Striving to live Aloha
finishing.com - Pine Beach, New Jersey
Q. What is the difference in years of exposure between stainless steel and zinc plated steel? We produce outdoor signs and am considering using zinc plated steel fasteners instead of stainless steel for cost savings. These fasteners are all used to hold down PCB's that are housed inside a waterproof enclosure. The sign is convection cooled so the internal air is continually exchanged with the outside air. These signs are sold primarily in the United States coast to coast.
Greg Schleusner- Milwaukee, Wisconsin
2003
A. Moving from SS to zinc plating is a big transition. It would be fair to use zinc-alloy plated fasteners with zinc-cobalt or zinc-iron, which will have an equal if not better service life of SS.
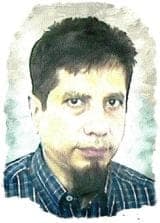
Khozem Vahaanwala
Saify Ind

Bengaluru, Karnataka, India
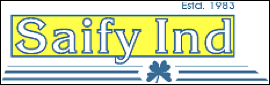
Q. I have heard many different answers from people who seem to know what they're talking about, but I would like to post this simple question here. What are the basic differences between Zinc plated, Stainless Steel, and Galvanized when speaking about fasteners (screws, lag bolts, etc)? How do the manufacturing processes differ, and which is more resistant to water?
Ron ClarkHardware store employee - Austin, Texas
2003
A. Stainless steel fasteners are made of solid stainless steel, not coated with it. So if the type of stainless steel chosen is corrosion resistant to the environment it is placed in, it can last essentially forever. The better grades of stainless, like 316SS, can hold up indefinitely in most environments. Even 303 stainless is an excellent choice much of the time.
Zinc plated and galvanized fasteners are made of steel with a sacrificial zinc coating. That coating is eventually consumed. Galvanized coatings are almost always several times thicker than electroplated coatings, so galvanized fasteners greatly outlast zinc plated fasteners.
I would like to agree with my extremely knowledgable friend Khozem, but can only do so with the qualification that his answer applies to Greg's question (which he was addressing) -- but not necessarily the general case.
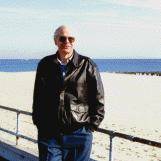
Ted Mooney, P.E.
Striving to live Aloha
finishing.com - Pine Beach, New Jersey
Q. My company is producing small gasoline engines; we sell our product to Southeast Asian for the long tail boat. Recently we met a serious corrosion on outside fasteners produced by zinc plating; the material of fasteners is low carbon steel. It is been use for affixing some steel stamping parts and plastic panels. I am not sure if there are some galvanic corrosion between fasteners and other dissimilar parts, considering from cost, do we have any other proper choice or solution?
Nick Lu- ChongQing China
July 30, 2009
A. Hi, Nick. There are many choices for fastener coatings including galvanizing, organic coating, mechanical plating, electroless nickel plating, zinc alloy platings, aluminum Ivadizing, and so on.
But I'm afraid that I don't understand your question, and don't understand the application in a "long tail boat" -- is this a small boat with a small outboard motor mounted on a long stick-like lever on the back of the boat? You need to determine whether there were or weren't galvanic compatibility issues (and you haven't told us what other metals are involved), and you have to determine whether the plating was defective in this particular case, or whether zinc plating is a bad specification. Zinc plating is rarely sufficient for exposed outdoor use, especially in a marine environment. For underwater use forget it.
No other corrosion resistant coating will be as inexpensive as zinc plating though.
Regards,
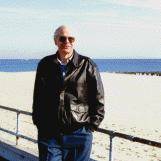
Ted Mooney, P.E.
Striving to live Aloha
finishing.com - Pine Beach, New Jersey
A. No doubt that Zinc plated fasteners are a cost effective solution. But during the acid dipping process prior to plating Hydrogen will penetrate into the fastener surface and shall remain entrapped due to Zinc plating. This will make the fastener brittle and is called HYDROGEN EMBRITTLEMENT. This will create micro cracks on the surface of the fastener which will propagate over a period of time, which will lead to failure of the fastener after a long time (say 6 months to one year). Hence you need to ensure that the plated fastener has undergone hydrogen de-embrittle treatment prior to use.
SANDEEP VIJAYAKUMAR- Bangalore, KARNATAKA, India
August 6, 2013
A. Hi. While Sandeep is right that the fasteners -- unless they are cheap unhardened low strength steel -- are subject to hydrogen embrittlement and require baking, and we appreciate that warning ... his post seems to imply that zinc plated fasteners would otherwise be satisfactory. I think they won't be. I feel Nick's poor experience is probably not an anomaly, but what is to be expected from zinc plated fasteners in many situations of outdoor exposure.
Regards,
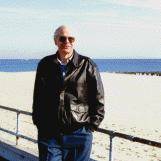
Ted Mooney, P.E.
Striving to live Aloha
finishing.com - Pine Beach, New Jersey
Q. Hello. I am currently reviewing products provided on a large project in Honolulu. The equipment in question will be located semi-outdoors and will be exposed to wind, some rain, and is located close to the Pacific Ocean (Salt Air) as they call it. The specification called for stainless steel fasteners yet the equipment provider took exception to that and is providing zinc/galvanized fasteners and brackets. I realize the Zinc plated fasteners are less expensive, but will the zinc plated fasteners provide the expected 25 to 30 year life span the equipment is expected to last?
Mike Stevensarchitect/product designer/regulator - Bellevue Washington, United States
June 11, 2014
A. Hi Mike. Hot dip galvanized coatings are typically several to many times heavier than zinc electroplated coatings. Hot dip galvanized brackets and fasteners with a heavy zinc coating will probably hold up; zinc electroplated brackets and fasteners, especially with thickness unspecified, will likely not.
If someone wants to offer a substitute to your spec, though, you should probably require a specification number for your consideration rather than letting them be loosey-goosey about it with slang. Zinc electroplating can be spec'd at 5, 8, 12 or 25 microns in thickness, and lots of hardware is not spec'd and is plated to less than 5 microns. With a sacrificial plating like zinc, lifetime is essentially proportional to the plating thickness. Good luck.
Regards,
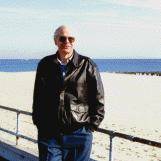
Ted Mooney, P.E.
Striving to live Aloha
finishing.com - Pine Beach, New Jersey
Q. How corrosion resistant is Zinc Chromate finish? It is an internal component and subject to oily residue as the external components will be more exposed to the salty air and moisture environment?
Mike Stevens [returning]architect/product designer/regulator - Bellevue Washington, United States
A. Hi again Mike. Unfortunately "Zinc chromate" is an ambiguous phrase. Some say it refers to the zinc chromate primer ⇦ on Amazon (affil link)] paint that was once popular, whereas others will say it means zinc electroplating followed by a chromate conversion coating (zinc electroplating is virtually always chromate conversion coated).
The steel and cast iron innards of automobile engines don't rust -- because oil is not corrosive. Zinc electroplating with a chromate conversion coating is probably suitable for parts that are not exposed to the moisture and salt air, but most won't last long if they are exposed.
Regards,
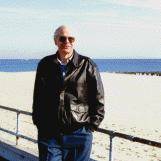
Ted Mooney, P.E.
Striving to live Aloha
finishing.com - Pine Beach, New Jersey
Surface treatment of packaging machinery hardware
Q. We make packaging machinery for various industries. Like Detergent, Fertilizer, etc. We use Hardened hardware of Steel (low carbon). Can you guide me, what should be the ideal surface treatment for these fasteners?
Vivek Ingle- Pune, MS, India
July 4, 2014
A. Hi Vivek. Those materials are corrosive, and most plated fasteners will not be resistant. I would consider zinc plating and chromating, then painting the exposed surfaces after assembly with an acid and alkali resistant paint or perhaps epoxy.
Regards,
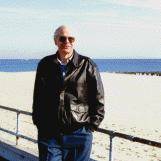
Ted Mooney, P.E.
Striving to live Aloha
finishing.com - Pine Beach, New Jersey
Q. Hi Ted,
I could not understand you.
1. Do you think I should do Zinc Plating and chromating. - If yes, then what will happen to HYDROGEN EMBRITTLEMENT due to Zinc Plating. It will lower the strength of the bolt.
2. You advice that the open surfaces like Head of the fasteners to be painted. But what will happen next time I have to unlock it?
3. What do you think about Hot Dip Galvanizing. If the fasteners are mechanically cleaned by sand blasting or etc., to avoid acid cleaning (and then hydrogen embrittlement)
- Pune, MS , India
July 8, 2014
A. Hi again.
1. Billions of fasteners are zinc or zinc alloy electroplated followed by chromating. Although hydrogen embrittlement is an issue to be dealt with, in most cases it's simply a matter of immediately and properly baking the parts for embrittlement relief, and this is a highly routine regimen.
2. If loosening the bolts for disassembly or adjustment is a frequent thing, painting the exposed parts becomes less practical.
3. It's possible that zinc plating or galvanizing will be reasonably resistant to some of the materials you are handling. But not to dishwasher detergent (which is extremely alkaline), nor highly acidic fertilizers like ammonium sulphate ... and no one can offer a general solution to "etc." :-)
Are stainless fasteners prohibitive cost-wise or strength-wise? If so, I'd just use zinc plated and chromated fasteners and replace them when necessary; it seems that you will be removing them frequently anyway. Good luck.
Your concern about hydrogen embrittlement is noted, but with the exception of ultra high strength steel, routine baking for hydrogen embrittlement relief is all that is usually needed. Some aerospace parts require sandblasting in lieu of acid cleaning, but I would find it strange for packaging equipment fasteners to require exotic surface coating procedures.
Regards,
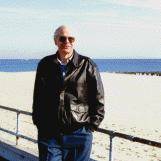
Ted Mooney, P.E.
Striving to live Aloha
finishing.com - Pine Beach, New Jersey
Q. Hi Ted,
How will you compare Zn Plating & Zn-Nickel Plating. The Hydrogen embrittlement issue in both cases. But as you said it can be removed with proper baking. But Zn Nickel Plating has got brighter and steady finish,
- Pune, MS, India
A. Hi again cousin. I do not agree that zinc-nickel plating is brighter than plain acid zinc plating. But it is more corrosion resistant (and more expensive).
The idea is that if you add the right amount of nickel (something like 6%), the surface becomes slower to corrode (probably partially due to greater nobility and partially due to "tighter" corrosion products) -- but it is still active enough to cathodically protect steel. Yes, hydrogen embrittlement is usually manageable in hard and high strength steels, but not in the very hardest and highest strength steels.
But zinc-nickel being longer lasting in plain water and slightly salty water, for the reasons explained, does not guarantee that it is resistant to the chemicals you may be packaging. Good luck.
Regards,
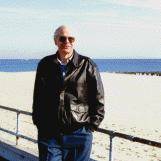
Ted Mooney, P.E.
Striving to live Aloha
finishing.com - Pine Beach, New Jersey
Stainless fasteners on zinc plated purlins are corroding
Q. We use stainless steel fasteners on zinc plated purlins and some structures where we use zinc coating/HDG.
My problem is within six months out [there is] fastener corrosion in nut and bolt.
It's galvanic corrosion? How to prevent it?
Any coating there on stainless steel?
It's a passivation problem?
Please help me.
- Mumbai, India
August 12, 2014
A. Hi Paresh. It's not galvanic corrosion because stainless steel is cathodic to zinc plating, not anodic to it. I suggest that you double check the specifications for your fasteners because properly passivated fasteners of a proper type of stainless steel should not be corroding. Do you know what type of stainless steel you are using?
Regards,
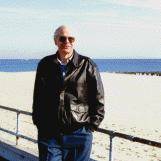
Ted Mooney, P.E.
Striving to live Aloha
finishing.com - Pine Beach, New Jersey
Stainless fasteners gall -- can we switch to zinc plated?
Q. We manufacture cargo racks for pickup trucks and ship them throughout the U.S. for carrying ladders, lumber, canoes, kayaks, etc. Our truck racks are clamp-on systems, thus our customers frequently put them on and take them off their trucks. Therefore, some of our screws are tightened and loosened repeatedly. We have used stainless steel screws for many years, but have had numerous complaints from people about the screws spalling during removal and having to be cut off. We have supplied customers with grease packets, and instructed them very clearly that grease must be applied, but we continue to have this problem frequently go the great frustration of our customers. Using zinc plated screws with stainless nuts does not cause this problem, and we are thinking of going to zinc plated screws. What alternatives are there?
Christopher Green
Truck Cargo Rack Manufacturing - Madera, California, USA
September 8, 2014
A. Have you thought about using a heat cured epoxy based dry film lubricant such as MIL-PRF-46010
[from DLA]
? Using a spin dip application can get you a thin coating on all surfaces of the bolts and nuts that will stay lubricated but doesn't require any preventative maintenance. (Tip: Don't use one that contains carbon black as the graphite will accelerate the corrosion greatly)
While zinc could work as it will provide lubricity, there may be issues with zinc corrosion product that could lock the nuts onto the bolts due to the voluminous nature of the corrosion product.
- Rock Island, Illinois USA
Justin-
Thank you. I'm investigating that now. It looks like this might be the solution.
Christopher Green [returning]
- Madera, California, USA
A. This is a common problem if the bolts and the mount that they are screwed into are the same alloy of stainless steel.
It is less of a problem if two different alloys are used, for example, use 316SS for the bolts and 304 for the mating thread.
consultant - Cleveland Heights, Ohio
Justin-
You were correct; the MIL-PRF-46010 has worked very well. We have just dipped and baked the liquid onto our screws in our powder coating oven. We are using that on all of our SS screws now. Thank you. - Chris
Christopher Green [returning]
Truck Cargo Rack Manufacturing - Madera, California, USA
Q. Which is the most suitable product (S.S. or Zinc plated ) to fasten galvanized metal (20 ga. z-bars) onto a concrete surface.
Brian Mcgee- Toronto Canada
October 29, 2014
by Stephen Yeomans
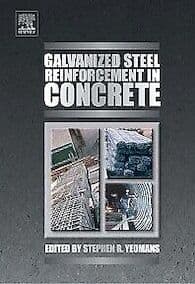
on eBay or Amazon
or AbeBooks
(affil link)
A. Hi Brian. Best fasteners would be hot dip galvanized if the z-bars are actually hot dip galvanized (I doubt it since the z-bars are only 20 ga.); zinc plated fasteners might be adequate if the z-bars are actually just zinc plated (electrogalvanized).
Regards,
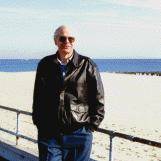
Ted Mooney, P.E.
Striving to live Aloha
finishing.com - Pine Beach, New Jersey
Q. Hi,
I'm having issues with the threaded inserts used in some of the plastic components on my motorcycle. The threaded insert appears to be made of Brass and has a hexagonal outer profile. This type of insert is set into the plastic of the air box, fuel tank and some other locations.
The problem seems to be that the bolts are corroding (or in some other way seizing) to the brass insert. When one tries to undo the the bolt from the threaded insert, there is sufficient friction between the mating threads to instead turn the threaded insert inside the plastic housing, preventing the bolt(s) from being removed.
I'm not sure what the current bolts are made from, but it appears to be a some variety of stainless steel. Can you suggest any bolt materials that I might use to prevent this issue?
Note: These particular bolts are not structural or load bearing, just holding on various lightweight plastic bits and pieces.
- Sydney, NSW, Australia
November 23, 2014
A. Hi Kris. Before attempting to remove bolts, you should apply WD-40 ⇦ on eBay or Amazon [affil links] to the area if geometry allows and tap it to try to vibrate it into the joint, then let it sit for an hour or so. It makes a big difference. When you re-assemble, use some teflon thread sealant. If it's a poor design for a corrosive situation, I think you just want to minimize the problems it causes you, rather than trying a custom re-design for less corrosion and galvanic issues :-)
Regards,
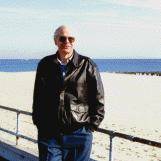
Ted Mooney, P.E.
Striving to live Aloha
finishing.com - Pine Beach, New Jersey
A. Good advise from Ted. A dab of anti-seize when reinstalling is a good idea. Plain old Vaseline will do the job.
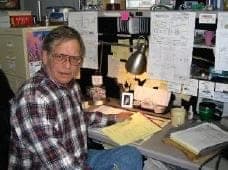
Jeffrey Holmes, CEF
Spartanburg, South Carolina
Q. We are assembling a green house frame (used) and trying to decide whether to use zinc plated bolts or to go the higher $ for the galvanized. If I correctly understand some of the above conversation, it is technically the same material, but the galvanized is hot dipped and thicker vs. (application type) and a thinner coating. So, the zinc plated might last ... how long? Versus almost indefinite on the hot dipped??
Around here it is approximately double the price for the galvanized, and we are on a tight budget -- so just trying to decide if the zinc would get us going for at least a couple years. . .?
Produce Grower - Henryetta, Oklahoma, USA
December 30, 2014
A. Hi Rachel. Yes, zinc plating is galvanically similar to galvanizing but thinner. I think the zinc plating will last at least several years in your non-seaside environment -- but don't let pressure treated wood be in contact with it or it won't last a season.
Regards,
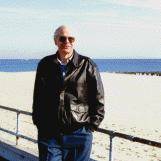
Ted Mooney, P.E.
Striving to live Aloha
finishing.com - Pine Beach, New Jersey
Q. Hello: we are designing a 28,000 sf pet adoption facility in the Rio Grande valley located in south Texas. We are using a Varco Pruden pre-engineered building. At the front of the building, we will have (3) large 11'-0" high "animal cut-outs" as a design feature. These will be etched out of 1/4" thick mill-finish aluminum with a water jet, then powder coated with a white color.
I had a question regarding the fasteners that would attach the cutouts to the 24GA steel Varco Pruden "Tech Four" wall panel and into the cold-formed steel Z-girt. This area is very humid and we need a corrosion resistant fastener that is compatible with the aluminum, powder coating, and the VP PEB. please see the attached 3D renderings and the diagrammatic section sketch. Thanks in advance for your help. We appreciate any assistance you are able to provide.
Abbie de leonboultinghouse simpson gates architects - mcallen, Texas, USA
March 27, 2015
Q. Hi,
I am researching on fastener finishes industry. I am just wondering, besides the process involved, what is the real difference between plating and coating. What are the pros and cons of plating vs. coating.
Would appreciate any explanation or references to this.
Thanks and Regards,
Hitesh
Financial Services - Mumbai, Maharashtra, India
April 20, 2015
A. Hi Hitesh. Those terms are not specifications and it's hard to put a fine point on slang. "Plating" usually is an abbreviation for electroplating, which is the electrodeposition of a metal coating onto a substrate. But coating is a term with almost no delimitations -- fruit can have a coating of chocolate, a road can have a coating of ice, and a fishing net can have a coating of algae or slime.
Coatings made of metal tend to have better adhesion to metal substrates than paints or plastics do. If a metal plating is anodic to the substrate it can afford it sacrificial protection; if a metal plating is cathodic to the substrate it can accelerate the corrosion if there are scratches or porosity. If there is no abrasion or scratching action, an organic coating like paint will often outlast a metallic coating; if there is abrasion or possibility of scratching, a cathodic metal coating will usually offer more corrosion protection than painting.
High quality organic coatings are probably usually better than plating for wood screws, but often aren't applicable for traditional nut & bolt construction because of clearance issues, vibration, a need for repeated unfastening & refastening or other issues.
Regards,
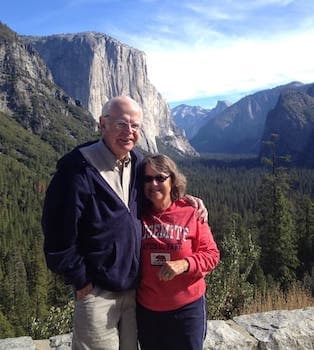
Ted Mooney, P.E. RET
Striving to live Aloha
finishing.com - Pine Beach, New Jersey
Ultimate corrosion resistance finish for custom set screws
I am looking for the ultimate corrosion resistant material and/or coating to use for custom setscrews we need for our products.
We have a few scenarios and would like to get a single solution if possible, but understand this may not be ideal.
Scenario 1: We have a setscrew going through an aluminium magnesium alloy casting and fastening against a 6106 T6 aluminium extrusion. A 316 stainless setscrew I would think would be the most corrosion resistant but could cause bimetallic corrosion, with the 6106 aluminium. Is there a coating we can use on the 316 setscrew to form a barrier between the two materials, and if there is, is there a worry about cavity corrosion of the stainless setting in? Or could you advise a better material to use.
Scenario 2: We have a setscrew going through a malleable cast iron casting that has been HDG, and fastening against HDG pipe. Again looking for the most corrosive resistance in the setscrew. Is it ok to put a mechanical galv coating over a stainless setscrew? Or again could you advise a better material or coating to use.
Many Thanks
- Melbourne Australia
May 5, 2015
A. Hi Steve. I think I'd use the 316SS for the aluminum situation, although you could perhaps order the set screws to be Ivadized or electroplated with aluminum. For the galvanized situation, I'd probably use galvanized steel setscrews. I don't think it's possible to galvanize stainless steel, but it can be electroplated with zinc if you wish. Good luck.
Regards,
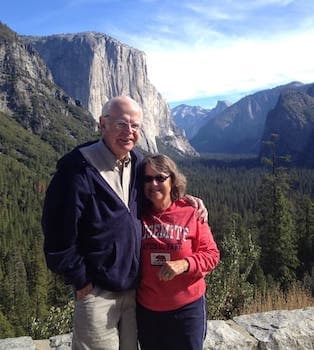
Ted Mooney, P.E. RET
Striving to live Aloha
finishing.com - Pine Beach, New Jersey
? Will the applications allow the use of nylon set screws?
Regards,
Bill
Trainer - Newcastle, NSW Australia
Q. Hello Bill, I am interested in your comment on Nylon setscrews. The setscrew is a M12 x 1.75 thread x has to reach and maintain a 30kN holding force. Is there a nylon out there that can do this without stripping the thread or the drive?
Regards
Steve
- Melbourne, Australia
A. Hi Mate,
I do not have to hand the mechanical properties of nylon fasteners.
Your first point of reference could possibly be a Blackwoods catalogue to identify Aussie manufacturers?
Regards,
Bill
Trainer - Newcastle, NSW Australia
Q. Hello,
We are contracting to provide and install a powder coated aluminum railing system constructed with 6061 T 6 aluminum. The designers call out 1/2 Stainless Steel anchors for the base plate connections [and require a bituminous paint on concrete to base plate interface]. They have omitted the fastener call out for the connection between railing panel sections. We have proposed using a 3/8" HDG A307 bolt to connect the railing sections. The application is an outdoor environment next to a busy road along a sidewalk. Each panel has 3 horizontal rails that will connect with a through bolt to a welded aluminum clip on the next post. All aluminum will be powder coated [approximately 6-7 mils]. Is our proposal for the HDG A307 bolts the best choice or will we be better offering stainless steel for the connection bolts?
Thank you in advance.
fabricator - Tacoma Washington USA
May 27, 2015
A. Hi Jim. I doubt that it's critical, and suspect that galvanized bolts would be okay, but stainless just sounds like a nicer idea, especially considering that the system is going to have some stainless fasteners anyway.
Regards,
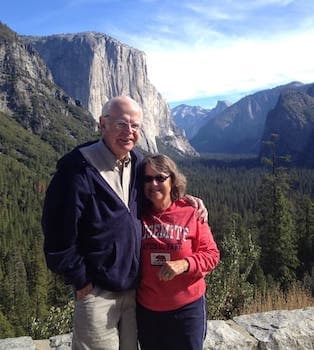
Ted Mooney, P.E. RET
Striving to live Aloha
finishing.com - Pine Beach, New Jersey
A. Mr. Jim King, according to Mr. Mooney hot dip galvanising is okay, but further a 5% H3PO4 dilute coating shall convert zinc into zinc phosphate coating, which has a long shelf life in mud & rough environment.
chennamallu prakashamconsultancy of ep&mf - Chennai, tamilnadu, south India
Q. Great thread! Question for you experts: I have a custom-made aluminum (alloy of some type I'm sure) door to hand on an outdoor shower. The door weighs ~17 lbs, so I'll need some hefty through-bolts & hinges. Would stainless be the best choice for the hinges and bolts?
Sounds like 'yes' from the previous discussion above, but I see that stainless is quite far from Al on the galvanic chart. Wondering if I should put some rubber or plastic barrier between the Al and mounting h/w wherever possible....
Any suggestions or comments would be much appreciated. Thanks!!
- Ormond Beach, Florida, USA
June 4, 2015
A. Hi Chris. Insulation is always a good idea because if there is no metallic path between the two metals to convey the electrons from one to the other, there can be no true galvanic corrosion. The more common question is whether it is truly necessary when it isn't easy and practical :-)
Stainless steel fasteners are a commonplace on aluminum and experience seems to show that it's not much of a problem for non-critical applications like shower doors. Galvanic accelerated corrosion is not the only corrosion through. Even anodized aluminum sliding shower doors for indoor use, and all-aluminum patio chairs eventually start corroding.
Regards,
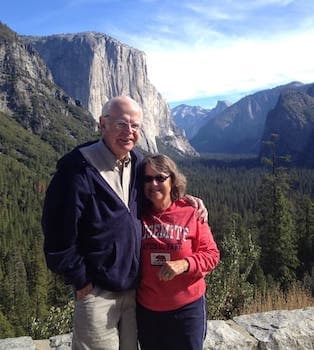
Ted Mooney, P.E. RET
Striving to live Aloha
finishing.com - Pine Beach, New Jersey
Q. After reading through these threads, this is a comparatively pedestrian and goofy question. I am working on my screen porch. The house is old, 1888, and I never want to have to go back and replace. So, I am searching for stainless steel, flush, screen clips. I can find zinc cast. I can find galvanized. I can find plastic. And I can find stainless steel from a manufacturer in New Zealand! But, given the material and the shipping, they are a FORTUNE!
Are there any manufacturers in the US that make stainless screen clips? I really don't want to use plastic. Metal appeals to me, much more.
Thanks
Flush Screen Clips in Stainless - Woodbury, New Jersey USA
June 18, 2015
Q. @ P Wood,
I'm looking for reasonably priced ss restoration screen hardware also -- did you find any?
Thank you,
greg
- Oakland, California, USA
A. I found stainless bolts, nuts, and cap nuts off the internet. I could not find any stainless turn buttons. I found them in nylon and tried them. Unfortunately, they all broke. I ended up settling for zinc plated turn buttons on eBay from the closing of a hardware store in Florida. They work fine, just not exactly what I wanted.
P Wood [returning]- Woodbury, New Jersey USA
Best hardware/screws/fasteners for installation of aluminum roof in wet/humid climate
Q. Hello--Installation of what we hope is a long-lasting roof is scheduled for this weekend.
I'd much appreciate any thoughts regarding whether stainless or galvanized screws/fasteners would be best for aluminum standing seam (.032 aluminum Shur-Lok with Durapon 70 coating by HPM Custom Metal Roofing)? This is for our 2,500 sf residence in a wet/humid tropical climate.
Supplier says galvanized would be better than stainless steel--something to do with positions on a galvanic table. I'd just like more opinion from experts on this question about stainless vs. galvanized fasteners for an aluminum roof. I did read on this forum that there's a difference between zinc coating and hot-dipped, with the latter being superior. Any further counsel would be appreciated! Would stainless be better than galvanized for an aluminum roof?
Thank you.
N/A - Honolulu, Hawaii USA
September 16, 2015
A. Hi Elton. Theoretically, aluminum screws or aluminum plated screws would be the first choice because they'd be galvanically compatible, but aluminum screws might not be strong enough and aluminum plated are not very available (pretty much restricted to aerospace uses). Second choice traditionally was cadmium plating, but this is toxic and restricted these days to critical applications (if any).
So you are right that your practical choices are hot dip galvanized or stainless steel. Galvanized would be less expensive and probably approximately as good, so that's what I'd probably use for large fasteners as suggested. But if the hardware is smaller than about 1/4", it's probably zinc electroplated rather than hot-dipped even if it says galvanized because the thickness of the zinc plating on a small screw is limited -- so I'd probably use stainless steel.
Regards,
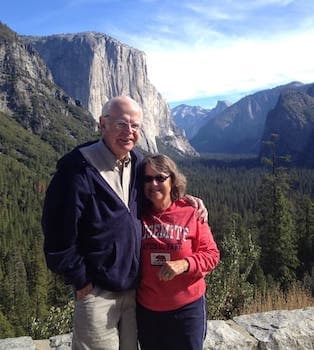
Ted Mooney, P.E. RET
Striving to live Aloha
finishing.com - Pine Beach, New Jersey
Q. Many thanks, Ted.
Looking into the possibility that thin nylon washers (or some other material?), on the pancake screws that will secure the aluminum standing seam to the hot dip galvanized clips, might at least help minimize the area of contact between the stainless steel screws and the aluminum.
I'd really value your opinion on the use of such washers for this purpose.
- Honolulu, Hawaii USA
A. Hi Elton. I am no roofing expert and there seem to be variations in these standing seam roofs -- but isn't it the case that the aluminum roofing snaps directly onto galvanized clips, so there is no preventing the dissimilar metal-to-metal contact anyway? Insulating is not always done in the case of dissimilar materials, but it is always recommended. If you have true insulation (no metal-to-metal contact), you can't get galvanic corrosion -- but a washer alone (no bushing/tubing) will not prevent metal-to-metal contact unless the hole is oversized and the screw is centered with no movement.
I'm having a hard time envisioning how you prevent metal to metal contact, and I thought the idea of pancake screws was to prevent an impression in the panel above it, which a washer under the screw head would seem to aggravate. I can talk about galvanic corrosion, but I can't talk knowledgeably about that roof :-)
Regards,
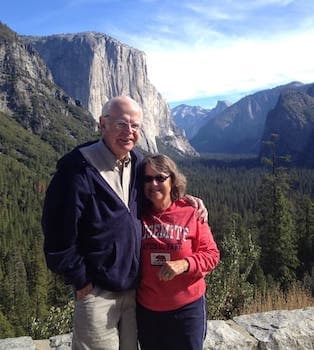
Ted Mooney, P.E. RET
Striving to live Aloha
finishing.com - Pine Beach, New Jersey
Q. Hi,
We are manufacturers of standing seam metal roofing here in Hawaii, and I often get the question of whether it is better to use stainless steel, or galvanized clips and screws with .032 thick aluminum panels, 3105 alloy. The aluminum is coated with a polyester paint backer, and the top surface is a Kynar 500 paint system. The industry standard is stainless steel clips and screws, but on the galvanic chart, it seems like G90 galvanized clips with zinc plated carbon steel screws would be closer in compatibility. The clips typically should not be exposed to moisture since they are concealed under the panels, however, Hawaii is a damp environment to begin with, and improper installation could allow moisture to get under the panels and contact the clips and screws. In this case, I have seen the screw heads corrode through the aluminum panels when using stainless. Any insight you have on this would be very much appreciated, I am always interested in how to give customers the longest lasting roof possible.
Thanks
HPM Building Supply - Honolulu, Hawaii, united states of america
September 17, 2015
A. Hi Andrew. If you could get aluminum or aluminized clips, and aluminum plated or aluminized hardware, that would be the ideal solution. Short of that, or cadmium plating which is no longer available due to toxicity, you have galvanic incompatibility whether you choose galvanizing or stainless, and it becomes a matter of avoiding the one which is worse :-(
The thing is, there is far more aluminum area in the roof than galvanizing or stainless steel, so it's generally considered best to make the larger area component the anode, because that way the corrosive current can be diluted over a large area than concentrated on a small area. That's why stainless (cathodic to aluminum) is probably better for small fasteners and clips -- just book knowledge, and would be happy to hear from roofers with contrary experience.
Regards,
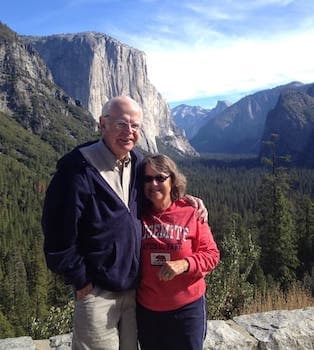
Ted Mooney, P.E. RET
Striving to live Aloha
finishing.com - Pine Beach, New Jersey
Q. Dealing with the compatibility of metal fasteners against galvanic corrosion such as galvanized steel, zinc plated and stainless steel, which metal fasteners can be used together? Thought I saw a sign in Home Depot that read "Do not use galvanized steel with stainless and zinc" or one or the other. Found out that using zinc plating in marine use is not good. Used one on a stainless swim platform and one on a jet ski port which have rusted bolt heads. Recently bought two galvanized dock cleats and galvanized lag screws so those should be okay. Stainless steel fasteners are not made in bulk. They mostly come in individual packages and limited to certain sizes.
Richard Brooks- Montgomery, Alabama U.S.A.
August 1, 2016
A. Hi Richard. Galvanizing and zinc plating are essentially the same material on the surface so they are galvanically compatible. But one problem is that zinc plating tends to be rather thin and therefore not suitable for service in an aggressive environment. Hot dip galvanizing tends to be significantly thicker and therefore significantly more suitable. A second problem (which may relate to the Home Depot sign) is that, because galvanized coatings are so heavy, the threads are cut differently and non-galvanized nuts don't fit galvanized screws and vice versa.
But even hot dip galvanized fasteners may not last long in marine service joining stainless parts together. The zinc is sacrificial to the stainless, and the small amount of zinc on a bolt, even if applied as a heavy coating, cannot sacrificially protect a large stainless item for long. If you must use galvanized hardware on stainless steel in a wet and salty environment you really need to isolate the hardware from the joined parts with plastic washers and bushings so there is no metal-to-metal contact.
Regards,
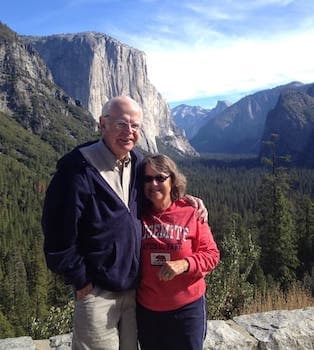
Ted Mooney, P.E. RET
Striving to live Aloha
finishing.com - Pine Beach, New Jersey
Q. We use 304 SS fasteners on aluminum hulls. The tapped holes are painted, however the paint cracks when the fasteners are installed.
As a result, two problems occur.
one being the water starts to get underneath the paint in tight area around the fasteners ( this area is deprived of oxygen), which then causes crevice corrosion.
The second issue is due to the paint failing at the threads, causing the stainless steel fastener to come into contact with the aluminum surface which initiates galvanic corrosion.
So now we have aluminum corroding away and paint that is blistering and peeling off.
Can anyone think of a solution to this problem? We are currently considering aluminum fasteners in low load areas, and using an anti corrosive compound to bed the fasteners such as Duralac.
Any thoughts?
- Surrey, BC, Canada
September 21, 2016
Q. I am replacing Mild Steel set screws in a cast iron solid fuel stove [ originals so rusted they had to be chiseled out and holes re taped. What material should the new screws be ? coated mild steel - stainless steel - brass / bronze bearing in mind the high temperature and any reactions to the cast iron
David Bailes- Sligo Ireland
October 19, 2016
Best finish for fasteners in heavy truck applications, when trucks are acid washed
Q. What plating has the best corrosion protection for use in heavy truck applications, where the trucks are periodically acid washed.
Rob GlassQuality Manager - Columbus, Ohio US
December 7, 2016
A. I've noticed in the on-going discussion of Fasteners and the subsequent prevention of corrosion in all forms one method of coating isn't mentioned that I've noticed.
Zinc Thermal Diffusion.
Although the process has it's roots in Sherardizing historically, there have been developments to diffuse zinc into substrates below the melting point of zinc. Process temp typically around 300 °C.
When combined with passivation, and if necessary a topcoat, performance is well in excess of 1,000 hours of salt spray and also prevents the following:
- Galvanic Corrosion of dissimilar materials
- Hydrogen embrittlement since the process naturally includes a baking element to it.
Performance per dollar ratio against Stainless and other high grade coatings is quite good as well, typically with sufficient economies of scale (i.e., decent volume).
And to be quite honest I am now working for a company that is bringing their technology to North America so I am biased to a degree, but I also have data that supports the above statements.
- Jackson, Missouri, USA
Hi Ted. Thanks. Yes, thermal diffusion went unmentioned on this thread previously, as did the very popular zinc-rich dip-spin coatings and a number of other technologies. When "acid washing" is involved, as in the most recent posting, we should probably emphasize electroless nickel plating since zinc coatings have no acid resistance. Each technology has disadvantages to go along with their touted advantages, which is why no method has obsoleted the others.
Regards,
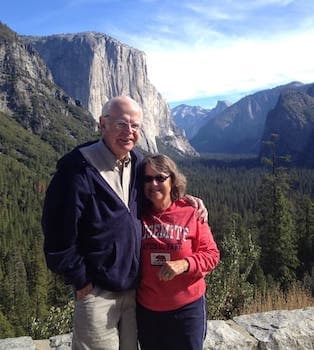
Ted Mooney, P.E. RET
Striving to live Aloha
finishing.com - Pine Beach, New Jersey
Q. Aloha,
We are attaching fascia to 4x6 rafter tails. Both materials are fir PT with Borates. Directly over the fascia will be copper gutters. The fasteners for the fascia will be countersunk and puttied over so there should be no contact between the copper and the fasteners unless the fastener corrodes. My question is what is the best fastener for this application, (whether screw or nail), to make sure that there is no corrosion of the fasteners. The area is very wet and has considerable salt in the air. While the top of the fascia is covered by the roof, we have had a problem in the past with galvanized nails corroding after a few years and staining the fascia. Thanks.
- Honolulu, Hawaii, USA
January 24, 2017
Q. I need to strap plastic barrels onto my cedar swimming raft. What would be the best strapping material? I was thinking of using galvanized metal strapping with galvanized screws.
Joe Happe- Buffalo Minnesota
March 12, 2017
A. Hi Joe. Galvanized should be okay, but not as good as stainless.
Regards,
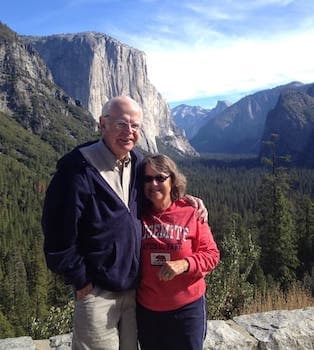
Ted Mooney, P.E. RET
Striving to live Aloha
finishing.com - Pine Beach, New Jersey
A. Plastic strapping is strong enough for most purposes, doesn't rust, and is less expensive than steel strapping and much, much less expensive than stainless steel.
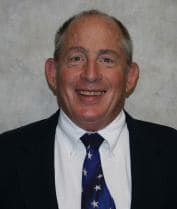
Tom Rochester
CTO - Jackson, Michigan, USA
Plating Systems & Technologies, Inc.

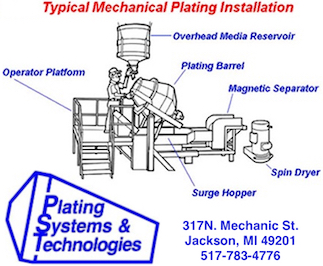
A. This answer really applies to many of the questions here. In the late 90's I began testing various Stainless bolts while attached to aluminum. The results were staggering. You should never use raw stainless steel bolts with aluminum. If you do need to use stainless steel to connect to aluminum, it should be coated with a coating specifically designed for this type of connection. My company uses millions of 410HT SS screws for an aluminum connection due to the very high strength of this alloy. 410 does however contain carbon and will surface rust over time. This is generally cosmetic and the coating takes care of that as well as the dissimilar metals and galvanic reaction. Using 304 SS is the most common but you need to know that 304SS is 20-35 weaker than the standard carbon steel generally used for bolts and 304 is one of the most corrosive alloys when combined with aluminum.
On a separate note, I have never seen any galvanized bolts last 20 years in a salt water environment without constant maintenance. If you are dealing with salt water, stick to Stainless if you do not want to do the maintenance.
My last thought is that if you are having an issue with Stainless and aluminum on bolted connections and you have to remove the nut on a regular basis, try Tef-Gel ⇨
I believe it was developed by an engineer working on the space shuttle program specifically to stop galvanic corrosion between dissimilar metals. I have used on my boat and had no issues removing bolts years old. Just my two cents...
- Pensacola Florida
Q. Hi, I have a 1970 Shasta travel trailer and am replacing the butyl putty tape around all windows and body seams. The window frames appear to be aluminum and all of the original screws are completely covered in rust. I want to replace all of the screws but not sure if stainless steel is needed or zinc coated will be ok, or a better choice..... I need approximately 550 of them so cost is a consideration.
Terry Higginsretired - Rolla, Missouri USA
April 13, 2017
A. Causes and Control of Fastener failures .
Galvanic corrosion- HASCC- Hydrogen Assisted Stress Corrosion Cracking- dissimilar metals-Delayed failures
Fastener manufacturer - Decorah, Iowa USA
Q. Hi,
What would be the ideal treatment for the screws used to fasten PCB (without any copper pad below - just the FR4) to meet 240+ hours of salt fog test. PCB's are enclosed in mechanical housing (not sealed - has multiple pockets through which fog can move)
What would be the ideal treatment for the screws used to ground PCB (ENIG Finish on PCB) with same 240+ hrs of salt forg requirement.
Regards
Subash
- Bangalore, Karnataka, India
October 2, 2017
A. Hello,
Zinc flake coating would suit your function.
Regards
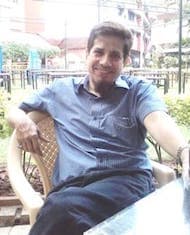
Khozem Vahaanwala
Saify Ind

Bengaluru, India
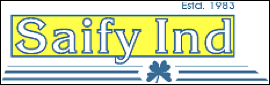
Q. Hello, I'm trying to figure out what the best fasteners would be for an assembly of aluminum framed windows and doors. I try to get 18-8 stainless steel whenever possible. But sometime the choices are 410 Stainless steel or Zinc plated steel.
My questions is what will last longer in terms of corrosion, 410 or zinc plated?
Some of our products will be used on the coast so I would like our fasteners to hold up as long as possible. Any info would be greatly appreciated.
Thank you.
- Palm Desert, California, USA
January 3, 2018
A. Hi Jeromy. Although it is possible to electroplate zinc fasteners for severe or very severe service, the zinc fasteners you are liable to find will surely have the minimum zinc plating thickness, 5 microns or perhaps not even, and would not be suitable for such service even if there were not a galvanic compatibility issue (which there is).
Regards,
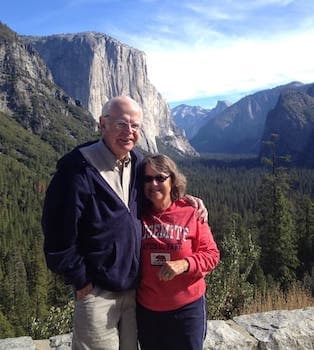
Ted Mooney, P.E. RET
Striving to live Aloha
finishing.com - Pine Beach, New Jersey
Automotive fastener plating
Q. Hi, I'm a perfectionist who's locked up and needs help! I am restoring a car for eventual daily use in Florida Environment. I have powder coated frame ready to assemble the chassis with parts and was going to have all fasteners (below grade 5 due to H embrittlement ) cad plated with conversion coating for best corrosion resistance. Appearance isn't an issue since not visible and I rather like the gold appearance of passivated cad anyway. Though this sounds great for corrosion resistance of the fastener itself it may not be great due to possible galvanic corrosion when connected to the steel frame (assuming the frame is steel!) or the parts being attached. Some fasteners will go into a threaded hole in the steel frame, others might just go through a hole and the threads are in the actual part being attached.
I realize teams of engineers designed the car and I'm just a dentist so what do I know, I don't want to re-engineering the car but the car probably wasn't designed to last more than a decade and I would like to improve upon it since I will have my lifetime then the kid's plus this is an expensive project taking years. This site is largely where I have learned so much about this and thank you!
Amateur auto restorer - Oklahoma City, Oklahoma
January 19, 2019
A. Hi Doc. Cadmium is not considered environmentally friendly, but if you can get the plating done, cadmium plus gold colored chromate is probably perfect. It is galvanically protective for the bolts and the steel, it's compatible with aluminum if there is any, it's less susceptible to hydrogen embrittlement than zinc or zinc alloy plating, and it's consistent torquing characteristics make it ideal for auto fasteners.
As for its 'environmental unfriendliness', don't feel too guilty. The government's response to the twin scandals of solid cadmium children's jewelry and cadmium paint on children's drinking glasses was just partial & ineffective recalls (see thread 57468 and 58085). Since an ounce of cadmium can promote sustainability by protecting a ton of steel from having to be re-mined, re-smelted, re-cast, re-fabricated, re-heat treated, re-finished, re-sold, and re-landfilled, I say go for it. Good luck!
Regards,
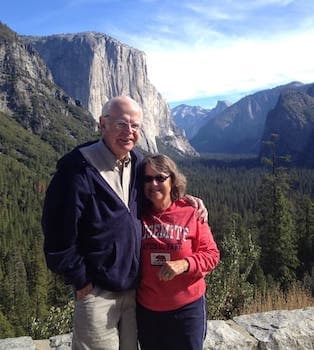
Ted Mooney, P.E. RET
Striving to live Aloha
finishing.com - Pine Beach, New Jersey
Q. Thank you so much for the response, after reading through so many articles on this forum throughout the last year and learned so much I had settled on cad with conversion plating. I then looked at a galvanic comparability chart and noticed that when cad fastener and steel or cast iron base were in contact that the cad fastener would corrode; so you are saying that the galvanic interaction is at an acceptable level? I guess I was looking for no corrosion but that may not be practical? Thanks again, Jackson
Jackson sullivan [returning]- oklahoma city, Oklahoma USA
A. Yes, the cadmium plating is sacrificial to iron, that's the main reason it's used (to protect the steel from corrosion). Nothing last forever, and eventually all of the cadmium can be consumed, so you can arrive at bare steel ... but if a lot of the iron & steel is painted, the corrosion is slower; and under-hood components tend to be oily and don't stay wet, so that helps, too, because an electrolyte (salty water) is required for corrosion.
Regards,
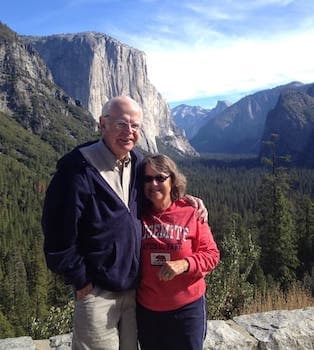
Ted Mooney, P.E. RET
Striving to live Aloha
finishing.com - Pine Beach, New Jersey
Q. Last question ... is there a specific Cad plating thickness required and hex chrome or tri chrome if I can get it? And thank you so much for the advice and also the education I have received on this forum ... AWESOME SITE!
Jackson sullivan [returning]- oklahoma city, Oklahoma USA
A. Hi again. Common thicknesses are 5, 8, or 13 microns of cadmium. I'd try to get the 13 if possible, and wouldn't settle for the 5. Chromates usually aren't specified by thickness but only by color. Tri-chrome is not (to my knowledge) available for cadmium, so it would be gold colored hexavalent.
Thanks for the kind assessment.
Regards,
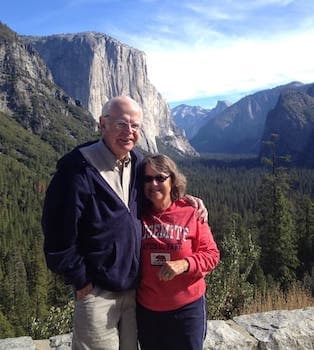
Ted Mooney, P.E. RET
Striving to live Aloha
finishing.com - Pine Beach, New Jersey
Q. My name is James Donnelly, I am an Electrical Inspector for Mining, in Saskatchewan Canada.
We find we have early corrosion and failures of electrical equipment and wiring support structures in dry fertilizer storage buildings. We have found plated screws corrode and electro-galvanized clamps corrode. SS304 seems to be an issue around moisture.
Can you provide / suggest an appropriate metal to use for screws , fasteners, cable trays, cable straps, etc.
Electrical Inspections - Mining - Melfort, Saskatchewan, Canada
May 7, 2019
A. Hi James. Of the materials you mentioned, 304SS would be the most expensive but the most corrosion resistant. Somewhat more expensive and more corrosion resistant would be 316SS. There may not be a practical plating/coating metal to completely stop the corrosion, but if the screws and other items are large enough for hot dip galvanizing, that would be a lot more corrosion resistant than plated/electrogalvanized finishes because the zinc coating is much thicker.
The multi-layer metal+paint coatings typically used on deck screws and similar construction fasteners probably offer the best corrosion resistance but may not be acceptable for electrical applications because of poor grounding capability (you could check with the manufacturers about that).
Regards,
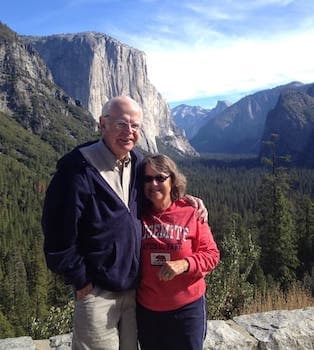
Ted Mooney, P.E. RET
Striving to live Aloha
finishing.com - Pine Beach, New Jersey
Thank you Ted, appreciated very much!
I will contact the manufacturer for his advise as you suggest.
Take Care out There.
Inspections - Melfort , saskatchewan, Canada
Q. Wonderful thread! I just time-traveled through them all! I'm custom making exterior raised garden beds for my community. What sets my boxes apart are the three thick galvanized carriage bolts I place in each corner after boring holes into a 4x4 corner post for increased stability of the 2" thick untreated Doug Fir (and Cedar). The add'l cost of this stability is worth the lower profit margin, but to be wise, I'm seeking lower cost bolts without compromising strength. My lumber yard charges me $1.50 for 3/8" x 6" galvanized carriage bolts + nut + washer. On Amazon, I found a source for 150 of each for a total of $65. Great price, but they are green and quote "triple coated to outlast hot-dipped galvanized bolts". After searching, I can't find any information on this miracle process. [deleted by editor] is noted in some places, but no definitive info. Your advice on whether these green triple coated carriage bolts will serve our vegetable boxes well would be greatly appreciated.
Joe Wachs- Maplewood, New Jersey, USA
May 21, 2019
A. Hi Joe. We deleted the specific brand name of the fastener coating (huh? why?) but there are a good number of suppliers of generally similar coatings, and there is no reason to believe that this one is better or worse.
If you go to a hardware store you will see deck screws and such with generally similar multi-layer organic or organic/inorganic coatings. My opinion is they are probably superior to galvanizing for this application, where the screws are in wood (and cedar is considered a corrosive wood). When bolts are used in metal, in applications where we need all of their strength, or where vibration might chip away organic coatings and expose the substrate to corrosion or make the fit too loose, pure metallic coatings can be better than organic coatings. But this application, in deliberately wet wood, even though it uses nuts, seems like a case where deck screw style coatings would be better than galvanizing.
Regards,
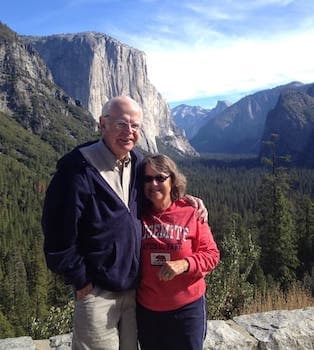
Ted Mooney, P.E. RET
Striving to live Aloha
finishing.com - Pine Beach, New Jersey
Thank you! Considering I already bought 150 count, your response is greatly appreciated. Best,
- Maplewood, New Jersey, USA
May 30, 2019
Q. I"m having a new pool installed and I don"t know if I should have stainless steel screws or regular screws used in my screen enclosure. Stainless screws are so expensive. What should I choose?
robert montesarchio- Nokomis florida
April 27, 2021
Q, A, or Comment on THIS thread -or- Start a NEW Thread