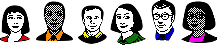
Metal finishing Q&As since 1989
-----
How to plate onto tungsten carbide

Q. Hello, I would like some help on this problem. I'm using a Woods Ni Strike to plate a 10% cobalt Tungsten Carbide. We do an alkaline cleaning, DI water rinse, HCl bath, DI water rinse, followed by Ni strike, DI water rinse, Ni plating, DI water rinse an then onto electrolytic gold.
We keep having problems after the gold plating due to poor adhesion but only in one specific part of the piece. After the nickel strike and the Ni plating it seems to turn out good, no bad adherence nor peeling, but right after we finish the gold plating we see peeling on the bottom of the part.
We have looked at the pre cleaning part and made sure all the steps are followed correctly; however I suspect that a change in the Ni strike configuration is causing the problem.
We used nickel anode plates covered with anode bags and now we have changed to titanium baskets with S-nickel pellets covered with anode bags and have seen that the nickel content rises and the pellets get burned if we do not use the bath. As a countermeasure we are taking out the baskets after we finish plating and putting new S-pellets but we keep getting the same problem after 2 batches.
Could the problem be the change of anode? And if so, can I find a way to work with the baskets and get a good outcome?
- Merida, Mexico
October 3, 2023
A. Hello Mariella, you note that the parts have good adhesion after Ni Strike and Ni plate. So if the peeling is gold only (no nickel present on the underside). The nickel plate may be passive in the problem area that you speak of. A lot of shops will use a nickel activator then rinse before gold. It's beneficial to go into the tanks with live current. The current can be less than the normal cycle, and adjusted accordingly when all the parts are in the tank. I don't think the anodes are causing the problem, but you may want to check your anode to cathode ratio in the Ni plate. 2 or 3:1 is plenty. Also make sure your HCl in the nickel plating tank isn't too high.
Mark L Baker- Cazenovia, New York USA
October 7, 2023
![]() |
Q. Hello Mark, thanks for your reply, I will look into the HCl concentration for our Ni Strike bath. However, we have tested the adhesion after Au plating and find that sometimes the peeling is only gold and other times the peeling has also nickel, so probably the adhesion isn't even good after the first nickel. - Merida, Mexico October 10, 2023 A. Tungsten carbide tools are TiN (yellow) coated by PVD process to enhance the working life of the tools. It looks almost like gold, but not quite. I don't know what is your application. If required you can do a gold coating by PVD process over TiN or directly on carbide. - Bangalore Karnataka India October 10, 2023 |
⇦ (tip: readers rarely show interest in abstract questions, but people's actual situations usually prompt responses)
Q. Is the Wood's Strike proper for tungsten carbide?
Rafael ChozaStudent - Merida, Yucatan, Mexico
February 22, 2024
A. Hi Rafael,
Yes, Wood's nickel strike is probably an appropriate step for plating onto tungsten carbide, but Wood's nickel alone may not give reliable adhesion on tungsten carbide. Please review the rest of this thread and the linked threads.
Luck & Regards,
Ted Mooney, P.E. RET
Striving to live Aloha
finishing.com - Pine Beach, New Jersey
Gold Plating is peeling
Q. I have plated tungsten carbide pieces with gold after nickel plating. The issue is that the gold is peeling even with nickel layer.
If I try to peel the nickel plated layer before gold plating, you can't remove the nickel, only after gold plating I can remove easily the gold and nickel layers.
What could be the reason?
Rafael Choza [returning]Student - Merida, Yucatan, Mexico
February 27, 2024
A. Hi Rafael
How thick is the nickel plating? And what is the chemical basis of the gold plating solution ... cyanide? It sounds to me like the nickel is porous or pin-holed and the gold plating is attacking the tungsten carbide substrate.
Luck & Regards,
Ted Mooney, P.E. RET
Striving to live Aloha
finishing.com - Pine Beach, New Jersey
A. Thank you for the response. The thickness of nickel layer is between 0.00005" to 0.0001". The chemical used is sodium aurocyanide.
Rafael Choza [returning]Student - Merida, Yucatan, Mexico
February 28, 2024
A. Hi again. That's an awfully thin layer of nickel and unless the substrate was super-polished I would expect porosity. I would suggest that you run a few sample parts with 10X that nickel thickness and see what you learn when the nickel is no longer likely to be porous.
Luck & Regards,
Ted Mooney, P.E. RET
Striving to live Aloha
finishing.com - Pine Beach, New Jersey
⇩ Closely related postings, oldest first ⇩
Q. I would like to know how to plate onto Tungsten-Carbide.
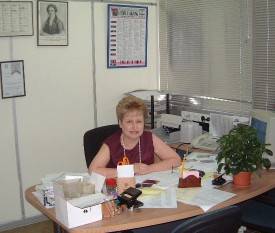

Sara Michaeli
Tel-Aviv-Yafo, Israel
1996
A. Wouldn't we all, Sara . . . wouldn't we all . . .
Seriously, I hope a reader can help us!
Meanwhile, readers may wish to consult the ASM Metals Handbook, Vol. 5, "Surface Engineering" [affil link to this on
eBay,
AbeBooks,
Amazon
]
as it has a chapter on activation cycles for preparing tungsten and other refractory metals for plating.
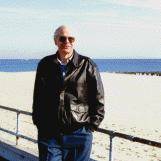
Ted Mooney, P.E.
Striving to live Aloha
finishing.com - Pine Beach, New Jersey
Ed. note: Other threads about plating onto Tungsten-Carbide include:
Thread 0950, "Electroless Nickel Plating on Tungsten-Carbide" and
Thread 20001, "Hard Chromium Plating on Tungsten"
A. Plating of WC-Co;
A lot depends on the cobalt content and distribution in the part to be plated.
HIP, or Hot Iso Static Processing will cause the Cobalt to migrate to the surface of the parts. An almost pure FCC cobalt surface can be obtained to conventional plating by using HIP processing. This can be done for almost all grades of WC-Co.
Ion implantation can be used to impart a plating like look to WC-Co and certain materials like TIC or TAC will actually improve certain surface properties.
- Columbus, Ohio
Multiple threads were merged: please forgive repetition, chronology errors, or disrespect towards other postings [they weren't on the same page] :-)
Nickel plating of tungsten carbide
Q. We manufacture small, precision tungsten carbide parts on a subcontracting basis. We have a long-term order to supply large quantities of electrolytic nickel -plated tungsten carbide pellets. We are looking for a plating company to provide this service, or alternatively, to purchase a small plating line for in-house production (because of the large volume and unique application). The following is a description of the part to be coated: Material: 10% cobalt-binder tungsten carbide. Dimension: 1.32 OD x 2.1 mm (0.052" OD x .083" long) The edges are slightly rounded.
Unit Weight: 0.043 gram (0.0015 oz) each. Quantity: About 2-3 million parts per month Coating: 3 to 7 micron thickness. The coating is intended to facilitate joining the pellets to a steel strip in a resistance-welding process performed in an argon environment.
The parts must go through a post-coating embrittlement relief process to improve adhesion quality. To test the adhesion quality, the parts are heated to 800 °C in a vacuum furnace and are then examined under a microscope to see whether entrapped bubbles have emerged from a void between the coating and the carbide. Such a part is considered unsatisfactory.
Our results to date with local suppliers have not been satisfactory. We still have the bubbling problem and less-than-desirable adhesion quality. Thus we are looking for new alternative solutions. We would appreciate if you could help us with experience you may have with such an application. Can you offer coating services, or preferably, could you design and provide us with a small coating line? Do you think our problem may be due to preplating preparation of the parts? Can you provide us insight into your recommendations for solving this problem? If you would like to work with us on this project, we would be happy to send you samples for testing. If you cannot, we would appreciate if you could provide us with the name of someone in the industry that might be interested.
microtools - Israel
1996
Ed. note: Sorry, this RFQ is old & outdated, so contact info is no longer available. However, if you feel that something technical should be said in reply, please post it; no public commercial suggestions please ( huh? why?)
A. I got involved in plating on tungsten carbide a few years ago on missile parts, we found that a high chloride nickel strike (Wood's) after anodic sulfuric etching gave satisfactory adhesion, although we were plating with 0.0003"- 0.0005" ENP rather than electrolytic nickel.
Regards
- Lowestoft, U.K.
1996
A. We have successfully nickel plated tungsten carbide inserts that were subsequently brazed onto machine tools. And we have successfully nickel plated small cobalt pellets used in x-ray machines. We have not, however, plated small tungsten carbide parts as you describe.
Kent
Fort Worth, Texas, USA
1996
Multiple threads were merged: please forgive repetition, chronology errors, or disrespect towards other postings [they weren't on the same page] :-)
Silver plating of Tungsten carbide microspheres
Q. We have a challenging problem. We need to coat tungsten carbide microspheres (approx. 635 micron diameter) with silver. We have been sputter coating but adhesion is not good. Currently wondering if an initial layer of electroless nickel my act as a tie layer to get the silver to adhere. Initial cleaning/surface prep. of the tungsten carbide still a challenge Anybody out there think they have a solution? We have to coat millions of these things. Thanks.
Malcolm Heavenmedical technology - Irvine, California
1999
books by
Donald Mattox ...
"Handbook of Physical Vapor Deposition (PVD) Processing" (2010)
on
AbeBooks
or
eBay
or
Amazon
The Foundations of Vacuum Coating Technology (2018)
on
AbeBooks
or
eBay
or
Amazon
(affil links)
A. How thick a coating do you need? How many pounds of these spheres do you plate in a year? We could look into it. We use another PVD with higher energy that helps adhesion.
Mandar Sunthankar- Fort Collins, Colorado
1999
A. Malcolm
Nickel is good since it is the universal "glue layer" that alloys with silver and forms a carbide. PVD chromium is probably better since it does not have the outgassing problems of EN.
Society of Vacuum Coaters
Albuquerque, New Mexico
"Handbook of Physical Vapor Deposition (PVD) Processing" (2010) [on AbeBooks or eBay or Amazon affil links]
and "The Foundations of Vacuum Coating Technology" (2018) on AbeBooks or eBay or Amazon affil links]
Q. Is it possible to achieve similar results to Tungsten Carbide plating by using the proper welding rod, if surface finish is not an issue.
Stacey J Walker- New Iberia, Louisiana
2000
A. Hi Stacey. I think that requires some clarification. The idea of covering a tungsten carbide surface with another metal by slathering it with welding rods sounds impractical to me.
Regards,
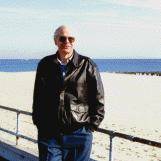
Ted Mooney, P.E.
Striving to live Aloha
finishing.com - Pine Beach, New Jersey
Q. I've spent many a late night researching plating on your site and can say confidently that it is the most informative and liberal source of information I have found. I read that many others feel the same and I thank you for the time you selflessly dedicate to the requests of others.
I have one question for you and it does not include a plea for process or constituent. Is it possible in your experience to copper or nickel plate tungsten carbide?
I thank you for your time.
- Sydney, NSW, Australia
2001
A. Thanks so much for the kind words, Dean, they are really appreciated. But 'selfless' is way too strong -- this is my job, and although the posters don't pay for the postings or answers, we get revenue to run the site from our supporting advertisers and affiliate links :-)
Tungsten and other refractory metals can be plated, but only with substantial difficulty. Volume 5: Surface Engineering of ASM's Metals Handbook [affil link to this on
eBay,
AbeBooks,
Amazon
]
offers the methods.
I recognize that you actually asked about tungsten carbide. "Transactions", vol. 66, page 144 (1988) has an article on "Nickel Electroplating onto Tungsten Carbide Powder", and the Shop Problems column in the July 1980 issue of Metal Finishing magazine describes an expired patent on anodic treatment at 1-5 ASI, 68-140 °F, 100-250 g/L sodium pyrophosphate to etch the surface before rinsing and nickel plating.
And we combined your posting with other threads on the subject which suggest that a Wood's nickel strike following anodic sulfuric acid etching, among other things, can work.
Caution! Be very careful in attempting to apply any technology to plating onto powder though (if that is your situation)! The huge surface area of powders can make the processes extremely active -- even explosive. Just as powdered metal can explode in air because of the high surface area, it can react in liquids far differently than a solid chunk of metal would. Best of luck.
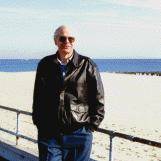
Ted Mooney, P.E.
Striving to live Aloha
finishing.com - Pine Beach, New Jersey
2001
Nickel plating on WC alloy
Q. I have a problem in nickel plating. Nickel plating on WC (Tungsten Carbide) alloy easily goes off from the surface. I'd like to know the possible reasons. The WC alloy includes some Cobalt (Co).
I would appreciate it if you could let me know some ways to have longer lifetime of the nickel plating on the WC alloy.
Sales person - Osaka, Kinki, Japan
2004
A. The WC is inert ---the plating will sit on the surface but has no bond strength. The surface must be activated.
What is your cleaning / activation cycle. I have successfully coated Tungsten in the past but it is an involved activation process.
- Hobart, Tasmania, Australia
2004
A. What is your plating approach? What it temperature when nickel drops off?
I think there are two possible reasons. First one, nickel does not wet surface of Tungsten Carbide and second case thermal expansion coefficient of WC and Ni too different.
I think you can solve problem if will add a little salt for changing wetting character of nickel.
Or use any metal with nickel whose thermal expansion coefficient placed between thermal expansion coefficient of WC and Ni.
I Chemical Physics - Yerevan, Armenia
2005
Multiple threads were merged: please forgive repetition, chronology errors, or disrespect towards other postings [they weren't on the same page] :-)
Q. What is the best way to electroplate Nickel to Carbide? It also needs to adhere very well for the after process.
Rick ShornakPlating shop employee - Novi, Michigan, United States
February 27, 2012
A. Hi Rick. We appended your inquiry to an earlier thread. I can't say what's "best", and have never done it, but it sounds like Wood's Nickel Strike after anodic sulfuric etching is a good method to try. Good luck.
Regards,
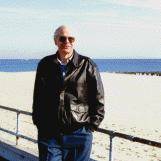
Ted Mooney, P.E.
Striving to live Aloha
finishing.com - Pine Beach, New Jersey
Q. Can I use heat treatment for electroless nickel coating on WC-Co substrate to improve adhesion by solid state diffusion? Knowing that the process will involve heating and cooling.
Hassan AbdelkarimPhD student - Johor-Malaysia
April 3, 2012
Q. I am using a woods Ni Strike to plate a 6% cobalt Tungsten Carbide.
After alkaline cleaning the parts are rinsed, and placed in 25% HCl, rinsed in DI water, then into the Ni strike.
Should the surface be activated using HCl or H2SO4 prior to the strike?
Following the activation, product is rinsed in DI water, then into the Nickel Chloride strike.
After the nickel strike we rinse in water, then into electrolytic Ni sulphate; following this rinse in DI water and then into electrolytic gold.
Should there be an activation prior to the electrolytic nickel and an activation following this prior to gold?
- Morrisburg Ontario Canada
February 25, 2014
Q. If you use H2SO4 as an etchant for Tungsten Carbide no current, what would be a recommended % and time?
Rob Sachs [returning]- Morrisburg Ontario Canada
February 27, 2014
A. We just electroplated Ni and trivalent Cr onto steel parts with tungsten carbide inserts without any special activation steps. Everything came out perfect.
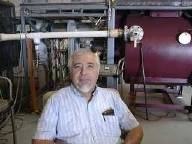
Jim Treglio - scwineryreview.com
PVD Consultant & Wine Lover - San Diego,
California
February 28, 2014
Depositing Copper onto Tungsten Carbide
Q. Greetings,
I am working on some prototyping efforts to make Tungsten/Tungsten Alloys more viable and economical as a material for firearm ammunition. It's unique characteristics, primarily strength and density, make it particularly well-suited compared to commonly used materials. Lead and Depleted Uranium are other "popular" materials with obvious environmental/health risks. The primary issue is that Tungsten is incredibly hard and very expensive. Making Tungsten barrels would be prohibitively expensive and standard steel barrels will wear out at a significantly faster rate.
Jacketing with a softer material is a common solution to this problem, however machining a jacket takes up space that could be the denser Tungsten. Depositing the copper via electroplating would be much better if possible. I am somewhat familiar with electroplating but have no prior experience with Tungsten, however online research shows it poses some unique challenges. I have AC/DC power sources and am willing/capable of working with some of the hazardous substances that are commonly used. My workspace is small and unsophisticated so particularly dangerous materials need to be avoided. I would prefer the safest method, with a reasonable batch cost (Not looking for manufacturing scale pricing, but can't spend thousands on prototypes), and I was wondering what my options are?
I would be working from Tungsten-Carbide powdered-sintered blanks for making machine tools. Unless I am unaware of a more suitable option. I am open to doing an intermediate plating like Nickel. As long as I can get at least half a thousandth of an inch this should be good enough for prototyping and testing. More would be better for testing. Thank you for your time and in advance for any input.
Best Regards,
Blake
- Belleview, Florida
October 13, 2020
A. Hi Blake. We appended your inquiry to a thread which indicates that, although it is difficult to plate onto tungsten and tungsten alloys, it is possible -- probably by following the aggressive activation methods described here and in the referenced ASM Handbook [affil link to this on eBay, AbeBooks, Amazon ] , followed by a Wood's nickel strike, followed by copper plating.
Luck & Regards,
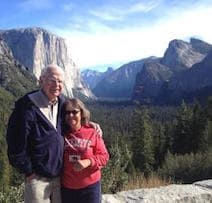
Ted Mooney, P.E. RET
Striving to live Aloha
finishing.com - Pine Beach, New Jersey
October 2020
A. Hi Blake
Tungsten cored ammunition has been around for a very long time and is common. I have a .55 Boys at round marked 44 W for 1944 tungsten and .303 rounds with similar markings. None have been plated -- the tungsten penetrator being simply pressed into a standard cupro nickel jacket. In larger rounds, the APFSDS, Armour Piercing Fin Stabilised Discadding Sabot is a standard anti-armour round and does not itself contact the barrel.
You mentioned the possibility of a tungsten barrel. There are many reasons why that is impractical, not least weight, although I know of stellite insert being used as a liner in the throat of a machine gun barrel to combat erosion at that point.
You may find useful information on current ammunition at https://ordnancesociety.org.uk/
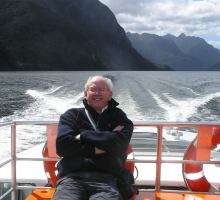
Geoff Smith
Hampshire, England
Q, A, or Comment on THIS thread -or- Start a NEW Thread