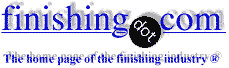
-----
Problems with tin plating over copper or brass

this text gets replaced with bannerText
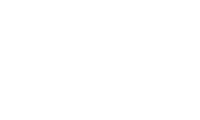
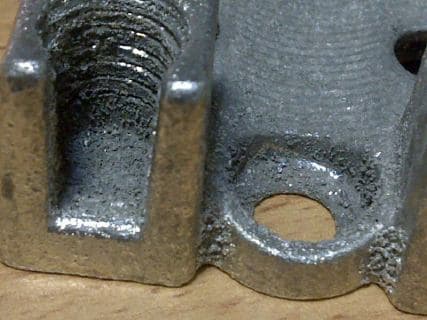
Probable cause: zinc & copper from brass casting dissolving in tin plating bath, then plating out at low current density.
Q. Respected sir,
I m using Copper cyanide as base coat, over which I plate Tin (MSA based). But within a few days I'm facing peel off problem of Tin from copper after oven at 180 °C. Parts are okay at 80 °C.
Oven temp. 180°C is standard. Previously parts were ok with these parameters. I analyzed the bath chemical at my lab as well as outside lab.: no major change observed. After cyanide copper I used 10% & 20% sulfuric acid activation for 1 to 10 min on a trial basis; as well, I used electrolytic activation in 10% sulfuric bath for 3 to 10 min. at 5 to 10 Amps.
Made a new bath of copper & tin also.
But result is same.
Now peel off percentage is 100%.
My base material of parts is M.S.
SHOP EMPLOYEE - PUNE, MAHARASHTRA , INDIA
June 21, 2022
⇩ Related postings, oldest first ⇩
Q. I've been trying to tin plate some brass pieces in order to reduce soldering times. However, when the part is heated up in order to receive the solder, the tin layer starts "bubbling", leaving a very bad finish. It is necessary for our process that the surface of the part after soldering remain smooth. We've gone to several platers, and all methods utilized have the same result. One of them suggested silver-plating instead of tin-plating.
I would appreciate any advice on the matter.
Arthur F. Allen- Barcelona, Spain
2001
A. You cannot plate tin directly on brass, you need a barrier like a copper deposit or nickel deposit between the brass and the tin.
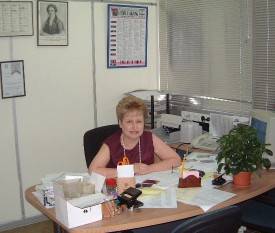

Sara Michaeli
Tel-Aviv-Yafo, Israel
Q. Sara, thanks for your response. We do use a flash of copper over the brass before tin-plating, and the "bubbling" continues. Because of the electrical properties of nickel (since the part is for RF use, this is very sensitive) we have decided not to use nickel before tinning, although I understand the tin adheres better to nickel than it does to copper.
Arthur F. Allen [returning]- Barcelona, Spain
A. Please can you ask if the suppliers are using acid or alkali tin plating solutions?
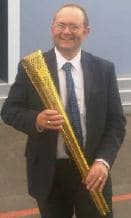
Martin Trigg-Hogarth
surface treatment shop - Stroud, Glos, England
A. Mr. Allen,
Use Tin/Lead to resolve your soldering and appearance issues.
Regards,
Joel Garcia- McAllen, Texas
A. Try asking your supplier about "Dull Tin". We use it and it passes solderability. You still have to have a copper or nickel barrier but it works very well.
Kevin Gendron- Trenton, Ontario, Canada
A. If you already have a copper underlayer, the recommendation for DULL or Matte tin should solve your problem.
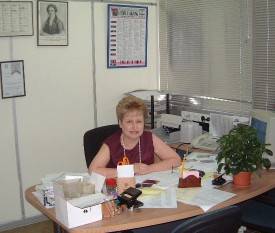

Sara Michaeli
Tel-Aviv-Yafo, Israel
A. Everyone is giving good advice. Always remember there is more than one correct answer to a question. The more plating experts you get, the more answers. One reason you may be experiencing problems with your present process cycle is that you say you are applying a copper flash. I assume this is from an alkaline bath. You need to plate sufficient thickness to overcome the amount of the copper plate which will be absorbed (not the technically correct phrase but descriptive). Try doubling or tripling the thickness of the copper flash. Also check your copper plating chemistry to insure that you are not depositing excessive organic compounds.
Good Luck,
Gene Packmanprocess supplier - Great Neck, New York
2001
A. If you are using bright tin plating and having blistering try adjusting time and temperature in the reflow process and make sure your reflow material is fresh. Use to more then twice.
If that doesn't work, switch bright tin to matte tin plating.
Or try copper flash, nickel, then matte tin plating.
Definitely use matte tin, stay away from bright.
Stamper tool and die guy - New York
October 8, 2021
Q. We are having exactly the same problem that Mr. Allen has - The tin plating 'bubbles' off during soldering. The substrate is MS58 brass and we have an intermediate layer of copper. Could someone explain why the tin 'bubbles' off and why a matte layer of tin should solve this problem? If the copper layer is not thick enough, what would be the right thickness?
Regards,
Mark Asciak- Zejtun, Malta
2001
A. The bubbling could be outgassing from organics in the tin OR the copper plate. Check with the supplier that they are using a pure matte copper and a pure matte tin. Also, the copper should be 100 microinches (2.5 microns) thick. If you are using a nickel barrier, the industry standard for the barrier thickness is 50 microinches (1.25 microns).
This is because the CuTin intermetallic grows at a much faster rate than NiTin intermetallic. The CuTin intermetallic is detrimental to reflow and solderability, whereas the NiSn intermetallic is not.
I worked at MacDermid Inc as a research chemist and tech service engineer for 11 years; my area of expertise was tin and tin lead plating over connectors. If you can switch to nickel, it will improve the lifespan of your parts and minimize whisker growth on connectors.
I hope this info is helpful.
- Devens, Massachusetts
June 10, 2008
Q. I am having a similar issue.
We have: Zinc with Ni underplating, and Sn finish.
The tin has visible "bumps" after reflow (lead-free process, 260 °C max temp). These bumps are solid Sn (cross sections confirmed no air or anything else under them - EDX).
The Sn plating is ~2.3 µm, but the thickness at the 'bump' is ~23 µm (EDX)
What would cause this Sn to want to 'gather' together and from a bump?
- San Jose, California
September 9, 2009
Q. Is it true that Zn in the brass (CuZn) would migrate into Sn layer, when there is no Ni barrier or Ni layer is too thin, say <0.5 micron?
John Li- Melbourne, Vic, Australia
March 4, 2010
Q. I am looking into lead-free soldering processes and I have found visible "bumps" on connector pins after reflow (260 °C max temp).
Brass pin with Ni underplating, and Sn finish.
Seems the surface tension is gathering the melted Sn into bumps. How to minimise the amount of "free" Sn to limit this? Or would that directly cause fretting issues?
- Gothenburg, Sweden
March 16, 2010
A.
1. if the etching process is with current, you may try to setting the current to 0.
2. set up acid active process with sulfuric acid after Etching process
- Singapore
Q. I face high carbon and oxygen content on tin plated surface (with copper underlayer) by SEM-EDX analysis. The black area is unsolderable during reflow.
I used hot air blower and performed manual soldering; I able to re-solder it again.
The tin plating is matte tin.
Any possible cause for the black residue?
- Melaka, Melaka, Malaysia
January 6, 2014
A. Hello Vincent,
The 3 major causes for carbon to be present in the tin deposit is storage conditions, and excessive organic additives in the bath and bath impurities. Because you are using a Matte Tin Bath, you can pretty much rule out the organic brighteners. Are these parts stored at room temperature right after tin plating, up until the point of soldering? What about humidity and the general atmosphere where the tin plated parts are kept?
Here is a test you can run... Plate the parts in tin normally. Be sure you have good rinsing and clean drying techniques. Wrap parts in sulfur free paper, or just a plastic bag and store in a room temperature environment. Wait the usual time before soldering. If you still have the problem, the tin bath should have a full analysis including metallic impurities. It would also benefit you to put a few carbon filters in your filter system for a few hours apiece in case you are dragging in organics during your plating cycle. Good Luck.
Mark BakerProcess Engineer - Malone, New York, USA
Tin electroplating on brass problem: oxidation
Q. Dear sir,
We have a problem of tin plating on brass part after few days of electroplating (acid solution).
Can you find a solution for this problem? We put tin directly on brass part.
Please see photos.
Best regards,
Faouzi Hmaied- Grombalia, Tunisia
September 23, 2014
A. Hi Faouzi. I'm not sure if you're saying that the plating solution goes bad after a few days and starts making bad parts, or whether you are saying that parts which looked okay coming out of the plating tank start turning bad in storage a few days later. It would make a big difference in my answer. I'm also not sure of the scale of these photos; a measuring tape would help. But it looks to me like you have a huge "particulates" problem, with loose fines attaching to the parts and getting occluded into the plating as extreme roughness.
Do you have anode bags on the anodes and continuous filtration in the plating bath?
We appended your inquiry to a previous thread which suggests the need for a barrier layer of copper or nickel before the tin plating, but I don't think that's the main problem here :-)
I, too, would like to hear from tin plating experts though because I find this issue very strange! Although, as I say, it looks like particulates to me, they seem to be exclusively in low current density areas. Why? Maybe I'm wrong and it's a reaction between very thin plating and the brass substrate? Those are mighty rough castings.
Regards,
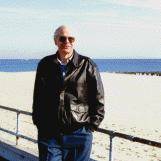
Ted Mooney, P.E.
Striving to live Aloha
(Ted can offer longterm or instant help)
finishing.com - Pine Beach, New Jersey
A. Faouzi,
It's nothing else but you are stripping Zn and Cu from the brass from which impurities increase daily. You move ahead and it's getting plated in low current density areas. Initially few hours or days you must be getting good results.
As suggested by Mr. Ted, you need barrier layer before entering Acid Tin bath.
- AJMAN UAE
A. Hello Faouzi,
The 2 previous responses revealed some good points. In troubleshooting plating problems I have always employed the process of elimination to get to the root of the problem.
1) As Ted mentioned you want to rule out particulate matter. Check the filter tubes to see if they contain insoluble matter. Anode bags must be used, and replaced when they don't drain the solution at at good rate. Pure tin anodes should be used, and they are supplied with a certification of purity.
2) Make sure you have adequate solution agitation to ensure the tin ions are being replenished at the cathode (parts).
3) In addition to a routine bath analysis, have the tin bath checked for metallic impurities such as zinc, copper and lead (if plating leaded brass). If you don't have the means to do this, send a sample out to a lab or supplier of your tin bath.
4) Be sure you are maintaining additions of your bath additives, whatever they may be.
5) Make sure your rinse tanks prior to the tin bath are clean and not loaded with metallics.
This may seem a lot to verify, but if a malfunction in the process is found, you will know how to correct the problem if it re-occurs. Good Luck!
Process Engineer - Phoenix, Arizona USA
A. Hi, Faouzi! After long years of experience: Never do tin plating directly on brass ... if you do you will meet such problems after a few days.
You should have copper plating first before tin plating.
I hope your problem will soon meet the answer.
Regards.
- Bekasi, Indonesia
Q. Hi,
In FPCB, Tin plated on Cu.
Customer found dewetting issue & cross-section shows a kind of a corrosion in Tin layer.
Almost 50% of Tin thickness from outside has turned to black (not shiny) and rest is intact with Cu layer.
Please advise what could be that black layer which is causing dewetting during soldering.
Thanks.
- Penang, Malaysia
June 14, 2016
Q. I want to set up a small and not very expansive electroplating unit to plate brass strips of 20 to 26 gauge with dimension 10 mm x 50 mm, approximate number 30,000 to 50,000 per month. I want a plating that will use less soldering material and will not tarnish and will keep looking good with time. Right now I am getting it done from out side source, who does copper plating and then tin plating, but results are not very good and quality is not consistent. Can some one suggest me as to what I should do.
AMIT MATHURMatman Plastics, Making Junction Boxes for Solar Panel - New Delhi, India
Q. I'm facing Cu frame exposed on the bending lead after Trim and Form process.
How can I solve this?
Lead frame type: Cu-Ni-Cu
Plate : Sn 100% plate (solder thickness ~11um)
Process : Mold -> Sn plate -> Trim n Form
Semiconductor Industry - Melaka, Malaysia
September 20, 2016
Q. Tin plating over terminal brass is not being successfully done; some places we find still unplated surface especially inside feed terminal mainly of small terminals like multi lock ones.
SURESH REDDY- DELHI, India
June 2017
A. Hi Suresh. Unfortunately I don't think you've actually provided any info yet from which people can use to help you try to troubleshoot. You are the plater? Send a picture of the part if you can; tell us what the tin plating process is; barrel plating vs. rack plating, etc. and we can perhaps get started. Good luck.
Regards,
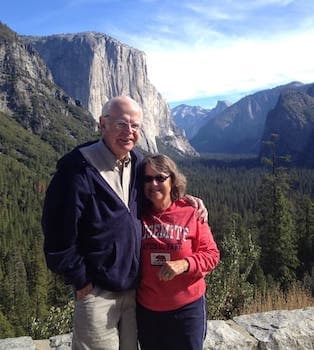
Ted Mooney, P.E. RET
Striving to live Aloha
(Ted can offer longterm or instant help)
finishing.com - Pine Beach, New Jersey
June 17, 2017
Q. We are observing bubbles and surface blackening after soldering for copper, barrier nickel, flash tin plating. Can anyone guide us to resolve the issue?
Narayan Chavan- Bangalore, Karnataka, India
July 5, 2017
A. Hi Narayan. Well, you can break some of the blisters and look at the underside of the blister and the surface they detached from, and tell us whether the nickel detached from copper, nickel delaminated from itself, or tin detached from the nickel -- and we can proceed from there. You can also send pictures of the blackening to mooney@finisihng.com, because cosmetic/aesthetic issues are difficult to cover with words alone. Good luck.
Regards,
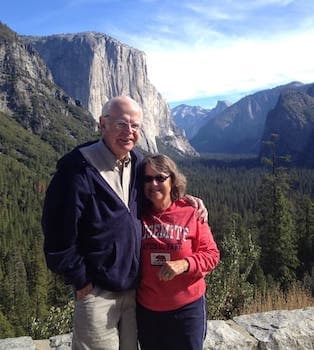
Ted Mooney, P.E. RET
Striving to live Aloha
(Ted can offer longterm or instant help)
finishing.com - Pine Beach, New Jersey
Q. Hello Everyone,
We are continuously facing an issue of soldering in a terminal. We are having brass terminal & undercoat of copper which have 2 microns thickness is done over brass & after that tin plating of 7 to 9 microns is done over copper. At the time of soldering dry soldering issue is faced by us. We have checked everything. Cleaning & plating thickness all are as per specification. Can anybody advice me on this issue??
- gurgaon, Haryana, India
July 24, 2017
Q. Hi, we do tin plating on brass components, but in bend test some parts get flaking off, plating gets flaking off. Supplier does flash of copper before tin plating but problems not solved yet.
Sandip RajputService in private sector - Jamnagar, Gujarat, India
May 12, 2018
A. Hi Sandip. You can review this page and maybe get some ideas regarding what your supplier might be doing wrong, but the chances of solving your supplier's problem for him this way are low. Usually your only realistic alternative is to try a different plating shop. But best of luck.
Regards,
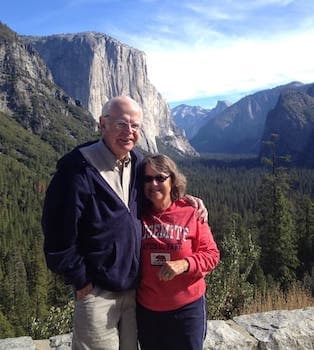
Ted Mooney, P.E. RET
Striving to live Aloha
(Ted can offer longterm or instant help)
finishing.com - Pine Beach, New Jersey
A. Find out whether the brass is leaded. If so, dip in 30%/vol commercial fluoboric acid, then copper strike in copper fluoborate. This is because lead is insoluble in other mineral acids and cyanide copper will not stick to lead salts. The plumbing industry knows all about this.
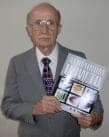
Robert H Probert
Robert H Probert Technical Services

Garner, North Carolina
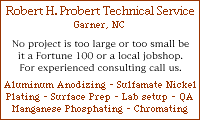
Plating solder over brass
Q. I would like to know if plating solder on brass is possible?
If yes, I'd like to know how I can do it.
Thank you.
- tabriz, Iran
August 17, 2018
A. Hi Rana. Yes, you can do tin-lead plating on brass. It's best and may be necessary to copper plate it first, before doing the tin-lead plating.
… but please introduce yourself! We don't know if you are a highly experienced tin-lead plater who just hasn't happened to try plating onto brass yet, or a young student wanting to do a science project for school. There are entire books on solder plating, so it is very hard to tell someone how to do it in a paragraph or two until they tell us their situation so we understand what they actually want to know. Thanks!
Regards,
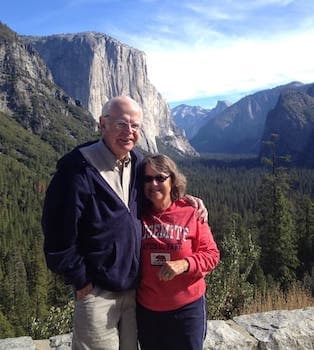
Ted Mooney, P.E. RET
Striving to live Aloha
(Ted can offer longterm or instant help)
finishing.com - Pine Beach, New Jersey
Q. Hi to all.
I work over 15 years with same tinning bath. Now I have a problem when I changed the bath -- putting in some new components.
I have a problem with tinning brass terminals. It seems that after 5 days tin is not shining on terminal and after one month terminals are all black.
The bath is good; tin is shiny on tester but when I go to tin the terminals I have a problem. About 8 min terminals is in bath and I think that is okay time to tin on brass terminals. And terminals are shiny maybe too shiny --maybe that is a problem? Someone have any idea what to do?
Thank you
private - Uzice Serbia
May 21, 2019
A. Hello Marko, when you say you changed the bath, adding new components, I would assume it's a brand new tin bath, not a slide conversion attempt? Have you measured the thickness of the tin deposit? If you have had success in the past with plating directly on brass. The bath should undergo a full chemical analysis, and deposit thickness verified. Your tin bath supplier should become involved as well.
Mark BakerElectronic Plating - Winston Salem, North Carolina USA
A. It is common to take the finished tin deposit back thru a mild soak cleaner to remove the tin solution. Otherwise the deposit turns gray/black in a few days.
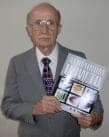
Robert H Probert
Robert H Probert Technical Services

Garner, North Carolina
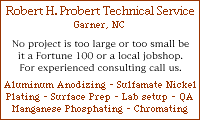
Q.
Dear All, I have to solder brass-zinc plated contacts & copper-tin plated contacts together. Is it possible or not? Kindly give your comments.
- Chennai, tamilnadu, India
June 8, 2019
A. Hi Yuvaraj. Your question is too abbreviated for me :-(
Are you saying that you have brass contacts that have been zinc plated, and copper contacts that have been tin plated? And these 'contacts' are for conduction of electricity? ... because I've personally never even heard of a zinc plated electrical contact, and even googling for that topic comes up empty. Maybe you have a zinc plated brass chassis and you trying to solder a grounding lug to it?
Please follow up with the full details of your situation, rather than an abstract proposition :-)
Thanks & Regards,
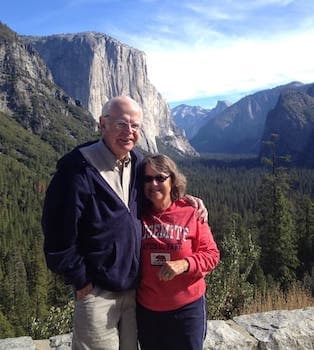
Ted Mooney, P.E. RET
Striving to live Aloha
(Ted can offer longterm or instant help)
finishing.com - Pine Beach, New Jersey
Q. Yes, we want to solder a diode which is tin plated to the zinc plated screw.
Kindly give a suggestion is this possible to get a perfect soldering?
- Chennai, tamilnadu, India
June 10, 2019
A. Hi Yuvaraj. Please just get a tin plated screw.
Regards,
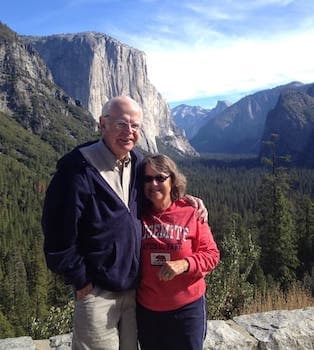
Ted Mooney, P.E. RET
Striving to live Aloha
(Ted can offer longterm or instant help)
finishing.com - Pine Beach, New Jersey
Nickel and Tin Plating Fails Humidity Test
Q. Terminal material BS36 was underplated with Nickel and top plated with Tin. Terminals were exposed to humidity during tests and it resulted in ugliness -- platings seemed removed and terminal base material exposed. Can anybody tell me, does humidity affect plating? Or what could be the best way to pass humidity test after plating?
Sukhram MandalGentherm inc - NORTHVILLE TW Michigan USA
July 3, 2019
Ed. note: This RFQ is outdated, but technical replies are welcome, and readers are encouraged to post their own RFQs. But no public commercial suggestions please ( huh? why?).
A. Hi Sukhram. Sorry, I don't recognize "BS36" -- can you be a bit more explicit please? The plating should withstand the test, of course, and the fact that the base material was exposed tells us that the problem started early in the process -- the parts either not being clean, not being properly activated, or the nickel plating too thin or too poorly done.
Regards,
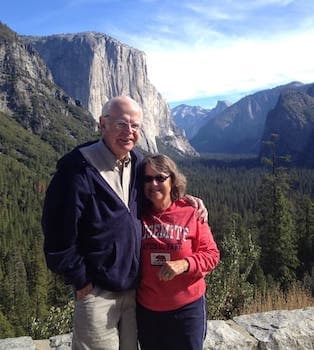
Ted Mooney, P.E. RET
Striving to live Aloha
(Ted can offer longterm or instant help)
finishing.com - Pine Beach, New Jersey
Solderability of tin plate containing intermetallic compounds
Q. We are having solderability issues with the following:
(Ground rule: the design cannot change.)
Item: Circa 1980 machined 2024-T854 aluminum chassis, approximately 0.08" at the solder point.
Finish: Copper Plate 0.00010/0.00025 thick per MIL-C-14550 Class 2 followed by tin plate 0.0003/0.0005 thick per MIL-T-10727 Type I Matte finish (alkaline type electro-deposited tin only)
Solder: Sn63Pb37
We need to solder a grounding tab of a component to the inside of the chassis but the solder will not wet to the tin plate of the chassis. (The component is new; the chassis is 40+ years old.)
1. Since we are trying to solder to an efficient heat sink, we are working to verify that we are getting the solder point to the correct temperature. We have used up to 300W soldering irons with heat gun
⇦ on
eBay or
Amazon [affil link] support. An oxyacetylene torch was also tried for brute force but the solder balled up. We have used several fluxes with varying activity levels, but no success.
2. We are wondering if the copper has diffused into the tin creating IMCs which are impacting solderability. Does it seem plausible that after 40 years a majority of the tin layer could be consumed by Cu-Sn IMCs? Some internet research indicates it may be.
2.a. Is it possible to spot re-plate the tin onto the IMCs to "refresh" the tin at the solder point? We would prefer to not have to strip and re-plate the entire chassis.
The minimum solder point is approximately 1" x 1/4".
Many Thanks!
- Heath Ohio
October 8, 2020
A. Tim, You raise some interesting points here. Firstly, since the substrate is old, it will be heavily oxidised, so I presume you are using a good flux before applying the solder - the oxide surface will be resistent to wetting by the solder, so it needs to be thoroughly and carefully prepared to make it wettable. Secondly, you are correct in that copper and tin readily forms intermetallics - under low temperatures only two are formed (Cu3Sn and Cu6Sn5), but at over about 400 °C other ones are formed (Cu10Sn3 and Cu41Sn11). Maybe heating the surface to over 400 °C is resulting in a tenacious oxide film that is preventing the solder wetting the surface. My first guess would be that you need to make sure your surface is clean and free of oxidation, because I would not expect IMCs to inhibit the surface wettability by the solder.
I am not sure if the following is relevant to you, but many years ago I worked on another tin based IMC - iron-tin intermetallics and these are commonly seen in tinplate. There is a range of them (FeSn2, FeSn, Fe3Sn2 and Fe2Sn3), but the only one found under normal conditions is FeSn2 - the others are thermodynamically unstable and will break down to FeSn2 and Fe. Furthermore, under conditions up to about 450 °C, the only initial IMC formed is FeSn2, but once the tin source is exhausted, the other compounds start to form as the tin diffuses deeper into the iron. It is hence possible to get all 4 Fe-Sn IMCs, but if they are left alone, they will all break down to FeSn2 and Fe.
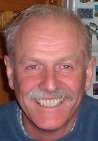
Trevor Crichton
R&D practical scientist
Chesham, Bucks, UK
Q. Dear sir/madam
We are doing dull tin barrel plating for electronic components with base material copper. Thickness about 5-8 µm, without underlayer. We did soldering pot test, the result was lumpy. Temperature of the pot 260 °C, and immersion time 10 seconds. What is the potential root cause of this issue?
We already did some trials to enhance pretreatment, plating with low current density (0.3 A/dm2 instead of 0.8 A/dm2), heating the part before plating, even after plating we heat up to 150 °C for 2 hours. There is no improvement.
What is the potential root cause for this solderability issue? We are facing this issue since the beginning.
Your kind advice will be very appreciated.
Employee - Batam, indonesia
December 9, 2021
Q, A, or Comment on THIS thread -or- Start a NEW Thread