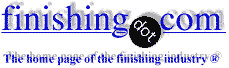
-----
Zipper plating processes: Q&A Problems & Solutions
Q. I AM WORKING IN A ZIPPER MANUFACTURING INDUSTRY. WE ARE DOING DIFFERENT TYPES OF DECORATIVE PLATING LIKE BRONZE, NICKEL, BRASS, ANTIQUE FINISHING AND PAINTING. WE WANT TO KNOW INTERNATIONAL STANDARDS AND TEST METHODS FOR DECORATIVE PLATING AND PAINTING. PLEASE ADVISE A SUITABLE BOOK.
THANKING YOU
ZIPPER MANUFACTURING - CHENNAI
2005
A.
For an introduction to all sorts of finishes, the Metal Finishing Guidebook is a great start and it includes appendixes listing many of the relevant standards.
Thousands of plating and finishing standards are available from at least a dozen different standards bodies, and almost none of them are free, but perhaps the simplest and least expensive approach is to get a copy of the "Annual Book of ASTM Standards -- Metallic and Inorganic Coatings" *.
It's a handy book of about a thousand pages which will include most of the standards you need at a lower cost than buying them individually.
Ted Mooney, P.E.
Striving to live Aloha
finishing.com - Pine Beach, New Jersey
2005
Ed. note: ASTM produces an 80-volume set of standards, but exactly which standards they put in which volume (how they are combined) will vary over the years much like the aisles of a supermarket may be rearranged -- so you should purchase a volume by an applicable title rather than by its volume number. If you happen to know anyone on ASTM Committee B08, which is responsible for Metallic and Inorganic Coatings, they will be able to advise what volume(s) to get in any given year.
Process sequence for tin or brass on zinc zippers
Q. We are zipper manufacturer. We want to plate Tin & Brass on our zinc die cast zipper samples. what are the process sequence we will follow to get good results.
SATHISH . GTextiles Exporter - India
2007
A. Hi Sathish,
After mechanical pretreatment you would need to soak clean, electroclean, acid activate, neutralize, cyanide copper strike, cyanide copper plate, and then tin plate or brass plate. Contacting a supplier of plating chemistry would probably be a good first step if you want to do this in-house, but contacting a plating jobshop might be a better idea still. Good luck.
Electroplating is complex, and people spend decades learning it well. So we're happy to offer a general process sequence as I did, and we can also answer quite specific questions ... but explaining the entire process in sufficient detail for you to "get good results" is no more realistic than you giving me the process sequence to manufacture diecast zippers in sufficient detail that I will get good results :-)
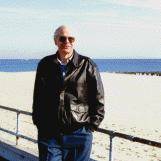
Ted Mooney, P.E.
Striving to live Aloha
finishing.com - Pine Beach, New Jersey
2007
Using nickel-plated hardware on items to be laundered
Q. I'm starting a bag business and am confused about appropriate hardware to use on the bag straps. I've found "nickel-plated metal rings and slides." These bags will be laundered, so I'm worried the nickel-plated hardware will rust from being washed in water. Stainless steel hardware is significantly more expensive.
Someone told me to try putting a strong magnet up to the nickel-plated hardware: If the hardware is strongly magnetic, it will probably rust. If it's not strongly magnetic, the hardware should be OK through washings. Is this true?
One of the samples I got was not magnetic. The other two samples were VERY magnetic.
Please help! I don't want my products to end up with rusty hardware.
Thanks so much.
bag designer - Los Angeles, California, USA
January 29, 2008
![]() |
A. Why don't you try specifying lacquered nickel plated hardware which will pass a laundry test. I unfortunately do not have access to my old notes right how but I do know that there are launderability specs from the clothing industry that applies to plated zippers, buttons, etc. process supplier - Great Neck, New York A. Susan, Process Engineer - Syracuse, New York |
Thank you so much, Gene & Mark! Unfortunately, the sales reps that I've been in contact with don't know what type of plating was used on their hardware. They just know it's "nickel-plate." Haven't come across any lacquered nickel plate options so far, but I'll try to find out more about launderability specs.
So, Mark ... you think the non-magnetic nickel plate slide would be safe to launder? The rings, unfortunately, are super-duper magnetic.
I may just have to bite the bullet and buy the stainless steel hardware to be safe. ** sigh **
- Los Angeles, California, USA
A. Hi Susan,
Mark is one of the most knowledgable plating experts I know, but I don't think I agree with him in this case because, while a magnet can detect non-magnetic coatings from magnetic coatings, the substrate may be magnetic (iron or steel) or non-magnetic (brass, zinc, aluminum). I suspect the magnetic item was made of steel and the non-magnetic ones made of zinc or brass.
I think the chances of general nickel plated rings and stuff being launderable are slim because people usually limit their costs by doing no more than the necessary, and a very thin, porous, and cheap nickel plating may be fine for many circumstances but not for launderability.
Unfortunately, when you need quality sufficient to meet special needs you usually have to pay for it. Your choices would seem to be to have the stuff plated to your needs, or to find someone who has already plated them to your needs and will surely announce their quality and launderability, or to apply some sort of launderable clear coat to them yourself.
Luck & Regards,
Ted Mooney, P.E.
Striving to live Aloha
finishing.com - Pine Beach, New Jersey
Black nickel look for brass zippers
Q. Hello!
We are a brass zipper manufacturing company and we want to know the cold water chemical process that will help us to give our brass zipper the shining black or black nickel color.
buyer - Ludhiana, Punjab, India
May 22, 2008
A. Hi, Ashish. Brass can be darkened with simple formulations like copper sulfate/selenium dioxide brass darkening solutions
⇦ on
eBay
or
Amazon [affil links] . However, this will certainly not offer the durability of nickel plating (see thread 6651 for complaints and discussions about that approach).
Further, nickel plating can be self-leveling and impart brightness and shine, whereas the simple blackening process you seek will only blacken. If you want the finished part to be shiny without nickel plating you must buff it before blackening -- the blackening process will not 'level' the surface, which is what is needed for shine. Good luck!
Regards,
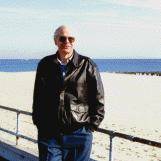
Ted Mooney, P.E.
Striving to live Aloha
finishing.com - Pine Beach, New Jersey
Zinc Die Cast Zippers: Improving washing performance
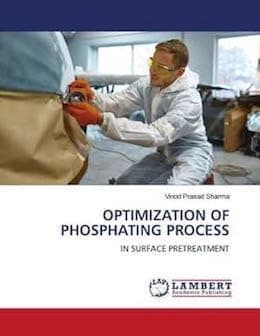
avail from AbeBooks, or Amazon
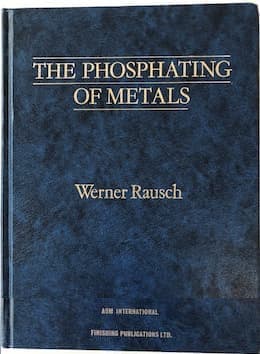
avail from eBay, AbeBooks, or Amazon
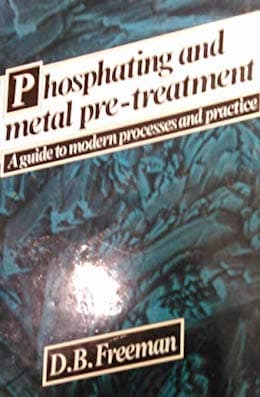
avail from eBay, AbeBooks, or Amazon
(as an Amazon Associate & eBay Partner, we earn from qualifying purchases)
Q. We manufacture zippers with zinc die cast components. After painting with epoxy, when the zippers are attached to the clothes like skirts, cushion covers, etc.. they are subjected to domestic laundry washing process, paint is chipping off happens and runability of pullers also suffers. Can anyone suggest a better way or improve the resistance of epoxy paints on zinc die cast components
KP UnniProduct designer - Chennai India
February 1, 2010
A. Hi, KP. Zinc is a poor surface for paint bonding. Proper zinc phosphatization would probably go a long way toward improving function and adhesion. Electrocoat priming on top of the zinc phosphate would be even better.
Regards,
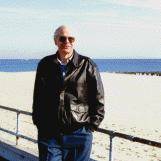
Ted Mooney, P.E.
Striving to live Aloha
finishing.com - Pine Beach, New Jersey
Identify this finish from the picture
Q. I am sending you image of part and please suggest what types of plating or coating is there on material. Either it is having satin nickel, with electrophoretic lacquer or it is having PU Coating, or is it pearl chrome plating; base material of part is zamak.
Please suggest.
ASHOK THETEplating shop employee - NASHIK, MAHARASHTRA, India
August 17, 2017
A. Hi cousin Ashok.
Let's hope that some finishes are so well proven in the zipper industry, and others so thoroughly unworkable, that someone with broad zipper industry experience will be able to tell you what this is, simply based on what is universally done.
But as a general rule, trying to determine what a finish is from its appearance in a photograph is unworkable. Sorry. Good luck.
Regards,
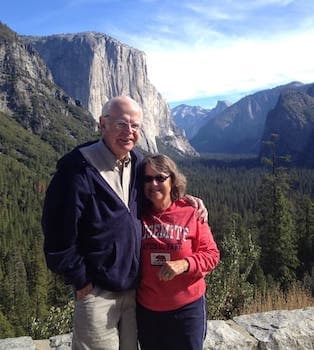
Ted Mooney, P.E. RET
Striving to live Aloha
finishing.com - Pine Beach, New Jersey
Need harder nickel-free plating for zipper sliders
Q. Hi All,
Love the forum and all your work!
I make leather accessories, and source hardware from China and Italy and Japan.
This enquiry relates to our zipper sliders which are the little carriage that combines and separates the zipper teeth.
They are die cast from zinc, and then electroplated to our desired colours.
Those colours being rose gold (I assume bright acid copper) with a lacquer, a gold colour (Not a straight brass, but I'm not sure of what colour) and a silver colour that is called nickel-free.
Over the last couple of years with our current supplier, we have found zippers that are opening behind the slider as the zipper is pulled closed.
The obvious culprit would be teeth wear, but this is not the case. While the teeth do wear over time, it is always the slider that has worn on the internal surfaces and is no longer combining the teeth correctly. (*On a 10+ year old zipper it might be the teeth, but the slider would have likely gone first)
We are seeing this in as little as 6 months in high use items with 20 odd openings/closings per day.
We make our items to last, and ideally want a minimum life of 3-5 years, so a slider failure after 6 months is a disaster from a reputation standpoint.
(We don't claim 3-5 years and only offer a 12 month warranty, but we fix anyone's bags for free for life basically [within reason]).
So when anyone presents with this fault, we replace the slider and problem is (temporarily) fixed.
Problem is, We sell to tourists and many of those will not be able to come back, and if they have the problem, they may just assume our product is not good and write us off.
Our old supplier's slider did not have this problem, and I still occasionally see them at 10 years old and going strong.
I have asked our current supplier about why, and they have no idea ... initially I thought changing sliders would solve the problem. As it must have been something about the internal geometry that was different, and causing the problem, but in the middle of the night I was lying there thinking about it, and it occurred to me, that the thin plating they put on the current sliders has very little abrasive resistance, and the same would likely be true of the inside.
In basic tests I have tried previously, the current pullers (the tab attached to the slider) which are plated while attached to the slider, in as little as 6 short pulls across a green scotch brite pad, it would already be worn through the silver colour, to the copper underneath, and quickly through that and to the zinc... the old puller could go more than 40 pulls of the same nature and not get through the silver.
So ... cutting an extremely long story short, I think this lack of thickness, and possibly hardness, is the reason for the premature failure of the sliders.
Now to my question!
I want to get my supplier to get some sort of harder and thicker plating down on the initial raw/polished slider, before it is sent to the decorative plater.
I should have mentioned before that they are rack plated, not barrel.
So my question is, what sort of hard coating would be ideal? Nickel? And if yes, what thickness would provide some good wear resistance, and still be achievable for these kind of low cost items?
I know there are lots of ways to get a hard finish, but I need a simple affordable solution. I don't have contacts over there who can manage this issue unfortunately, and my contact would be one of the the only ones who can speak english in the company. He also knows nothing about electroplating.
Getting them plated here is not an option unfortunately either.
To give you an idea, the slider and puller combined are a USD$.05 item, and the highly polished rack plating with lacquer takes that cost to about USD $0.30 in total, plus the zipper and assembly etc. I understand that this extra process will cost more, and happy to pay to improve our product, but it definitely can't increase the cost by $1, as our margins would not allow that.
I think the hard base plate would solve our issues, and be achievable for those platers, or another plater in the region, but I lack the technical knowledge to ask for what I need or source another supplier, so any advice anyone can offer would be greatly appreciated.
Thanks in advance,
Ben :)
Btw, old supplier's zippers were not up to scratch and they would not give me the details of just their electroplater.
Owner/ maker /product source - Sydney, NSW Australia
January 28, 2020
A. Hi Ben. I think there is a little misunderstanding here which should be sorted out before we proceed. "Nickel-free" is not a color, it means that there is no nickel in the part (some people get a skin rash from contact with nickel). So if you solve the problem by nickel plating you cannot call it "nickel-free".
I'm not sure why you must do rack plating, which probably does not offer as good plating on the internal areas as barrel plating would.
You could be right that your nickel-free plating is not hard enough and that a harder nickel-free plating material is available, but I'm not personally familiar with the practicalities of such; you could certainly have chrome plating done, which is an exceptionally hard metal (but it would be hard to put other decorative plating on top of it).
To me the more promising possibilities while remaining nickel-free are thicker plating or harder die castings.
Regarding logistics, while feeling Australian costs are too high, you are concerned about the communication difficulties with China ... so, have you considered the possibility of manufacture in English-speaking India?
Regards,
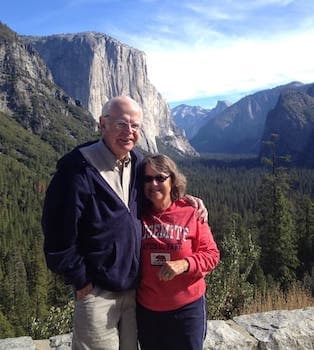
Ted Mooney, P.E. RET
Striving to live Aloha
finishing.com - Pine Beach, New Jersey
Q. Hi Ted,
Thanks so much for replying.
I was possibly not clear about the "Nickel free" finish. The Term nickel free is used by a few suppliers I have dealt with as the name for the silver colour.
I am aware it is not a colour, and is just a term for nickel free plating, but that's not how they use it, and for brevity, I probably glossed over that bit.
I do not require these items to be nickel free, as they are not in direct contact with the skin (and we don't sell anywhere in Europe), so I thought that the actual nickel plating would likely be harder than whatever silverish alloy they call "nickel free", and probably a simple solution, as finding a plater to plate nickel might be easier than the r & d of trying to get a chrome base to work.
My understanding of why we rack plate is that we require a highly polished finish on a small item with tight angles, and barrel plating will not give the desired results as polishing stones can not get in to all the little crevices etc.
Changing to another zipper supplier is unfortunately not an option, as it took me 10 years to find the current supplier, and I have not been able to find any others who can match their quality in terms of teeth, and finishing.
An Indian plater would be an option, but that would require shipping the sliders to India, and hopefully getting the desired result, then shipping them back to China for finishing and assembly.
I feel a much simpler option would be to get the existing plater to do the existing plating thicker or to put a thicker layer of actual nickel. Or to get them to find another plater nearby who can do what we need, so I want to be armed with the specific of what I need before asking again to improve the plating.
I should have mentioned previously, that we are talking about 5000-10,000 units per annum of a small component of a small (but important) part of our bags, and therefore this is not something that I could justify flying to china to take care of.
Also, I have previously asked them to increase the plating thickness, and they have said the only option is to run the parts through the whole process twice, as our plating run is way too small to be done on its own... It's put in with tens of thousands of others.
So, to cut an extremely long story short again, my question is; Is nickel plate likely much harder than most silver colour "nickel free" finishes used in decorative plating of small inexpensive items? (excluding Chrome of course).
And what sort of thickness should I be requesting? Would 5 or 50 microns of nickel be suitable, and would it be a reasonable request? And if Nickel is not harder than the alloy currently used, what thickness of that should I ask for.
I will definitely take your advice re the barrel plating, and see if that's an option for the slider itself, and maybe they can get the desired smooth finish.
... and I just read the title of my post and I know see why it looks like a wanted a nickel free plating option... face palm emoji.
Thanks again for your advice Ted,
Ben :)
- Sydney, NSW, Australia
A. Without knowing all the ins and outs of your relationship with your plater, I'll make a few comments:
It should be possible to barrel plate to good appearance and adequate thickness to prolong useful life, and it should cost less than rack plating.
You could also use electroless nickel applied in barrels or, possibly baskets. Properly done, electroless should have a good bright appearance, and is a bit harder than electroplated, possibly providing longer wear.
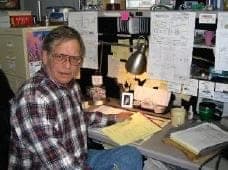
Jeffrey Holmes, CEF
Spartanburg, South Carolina
Q, A, or Comment on THIS thread -or- Start a NEW Thread