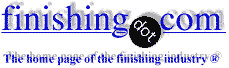
-----
Rainbow effect / defect on anodized aluminum?

Quickstart:
Readers unfamiliar with aluminum anodizing may wish to start with our Aluminum Anodizing: Intro & FAQs.
The aluminum oxide created by anodizing is transparent/translucent, and whenever anything has a very thin clear coating, it can create rainbow patterns (as witness a drop of oil in a puddle, carnival glass, or the reflections from a DVD). This is due to part of the light which hits it reflecting off the top, and part of it penetrating the clear coating and reflecting off the substrate, so the two portions travel different distances, are therefore out of phase, and interfere.
Such rainbow patterns on anodized surfaces indicate that either the anodizing is very thin or there is oil on the surface.
The normal colors of anodized aluminum are not from such interference coloring but from organic or metallic dyes. Thicker anodizing has deeper pores and absorbs more dye than thinner anodizing, so lack of color saturation is often an indication that the anodizing is thinner in that area.
Q. Hello, we do anodizing in 15000 ampere 200 gr/l sulfuric acid baths. We have 3 anodized baths. Last month, we sent two of our rectifiers for revision. After they arrived, rainbow problems began to appear on the aluminum profiles coming out of these rectifiers, especially at the ends. 10 to 15 micron size shouldn't be a problem. We don't understand it, but it does it from time to time, we couldn't find the reason, I would be glad if you could help.
Update: Hello, we have been facing this problem for a long time. Our anodized rectifiers have been revised with the new Munk brand. We experience this problem in all anodizing baths. I'm looking forward to your help. Your advice is very valuable to me.We were working with 1.5 A/dm2, we reduced it to 1.3, we solved the situation temporarily, but the anodizing times were extended. The revisions you made, the anodizing rectifiers and cathodes were replaced, the bath parameters are normal.
MahoCalisan - Turkiye
November 27, 2024
Tip: This forum was created to help build camaraderie through sharing tips, opinions, pics & personalities.
The operator & those readers who want that might not engage with anonymous posters.
A. Hi Maho.
The pictures don't seem to have enough resolution for me to see rainbows, but it does look like the color is much darker near the middle of the profile than at the ends -- which makes me suspect that the anodizing thickness is indeed too low at the ends.
Can you please measure the thickness of the anodizing on a few profiles close to the ends and close to the middle, and give us the average?
Luck & Regards,
Ted Mooney, P.E. RET
Striving to live Aloha
(Ted can offer longterm or instant help)
finishing.com - Pine Beach, New Jersey
Q. Hello, the problem still persists. All the profiles in our anodized products are coming out like this. This is also evident when they are put into the color bath. There is a significant deviation at the ends of the bars coming out of the anodized product. The microns are 11.12 microns, the average microns are no different. Both ends are coming out like this after the color treatment. The photos in the picture are from black color studies.
Maho [returning]Anodizer - Turkey
July 21, 2025
A. Hi. If I had no information but the picture, my guess would be that your cathodes don't reach close enough to the ends of the components, and the anodizing time and current is insufficient, such that the thickness on the ends isn't enough for full saturation.
Sadly, there is too much guessing and extrapolation on my end, and the info is too little and too unclear, to make much progress.
1. Are you saying you never had this problem until you changed the anodizing rectifiers and you are sure you have changed absolutely nothing else? Do the rectifiers have some sort of program control, or just constant current?
2. Are you saying that you have measured the thickness at the ends where there is insufficient color saturation, and the thickness at those faded ends is the same as at the middle?
3. Tell us about the "color treatment". Is it an organic dye or are you doing some sort of electrolytic coloring? If electrolytic, what are you actually doing and did those rectifiers change as well? Thanks.
Luck & Regards,
Ted Mooney, P.E. RET
Striving to live Aloha
(Ted can offer longterm or instant help)
finishing.com - Pine Beach, New Jersey
Q. We didn't change the distance between the profiles to be anodized. The distance between the cathodes is 15 or 20 cm, and there are no problems with our microns. Our colored rectifiers have been overhauled, but we didn't experience this problem with the older, non-overhauled rectifiers. After the new rectifiers arrived, we also replaced the old cathodes. The colors we use consist of electrolytic tin sulfate and nickel sulfate. After the busbars were anodized, a slight yellowing is observed at the ends. I wonder if the looseness in the cathode connections caused the screws to tighten. Could this be a problem, but the microns are normally as desired. The anodizers operate in current-control mode with a constant current of 18.19 V.
Maho [returning]Anodizer - Turkey
A. Hi again. Sorry but I'm still having a hard time trying to understand. So, okay, you replaced the 3 electrolytic coloring rectifiers. But surely they follow some sort of AC program don't they?
Your anodizing rectifiers apparently operate at constant current, voltage limited at 18-19 volts. Did you also replace all 3 anodizing rectifiers? What about the previous statement that you replaced only 2 of the 3 rectifiers ... 2 of the 3 anodizing rectifiers or 2 of the 3 coloring rectifiers? ... but it sounds like you later replaced the 3rd one with the same rectifiers that were causing you problems?
The parts you are anodizing are surely not busbars.
Looseness in the cathode connections caused what screws to tighten?
If the parts you are anodizing are indeed slightly yellow at the ends, something sounds quite wrong in the anodizing tank or prior to it, but sorry I don't know what might cause the ends to turn slightly yellow.
Can you scrub a few sample parts with a scrub brush and a bucket of powdered pumice and detergent before racking them just to make sure the problem is not related to cleaning or possible extra handling of the parts from their ends?
Luck & Regards,
Ted Mooney, P.E. RET
Striving to live Aloha
(Ted can offer longterm or instant help)
finishing.com - Pine Beach, New Jersey
A. Are doing a 2-Step Colouring? DC Pre-Treatment and AC Treatment in the Tin bath or do you go straight into the AC Treatment from the anodizing rinse?
Having a DC Pre-Treatment in the Coloring bath can help "normalize" the pores before coloring.
Also, the way the miscolouring arches in towards the center of the bath at the top and bottom of the bath is interesting. It's almost like you have the inverted "sun" when you place two plates back to back when doing Tin coloring. A curious phenomenon.
As for the Cathode distance, I don't think that's it. The transition from dark to light is too small.
Yellowing at the ends after anodizing however, along with a rainbow-y look, that is a typical sign of parts having no connection in the sulphuric acid.
Production Technician - Horsens, Denmark
August 5, 2025
⇩ Related postings, oldest first ⇩
Q. I'm getting rainbows on my 2024 bare T-3 sheets. Some get it some don't. I cannot figure out how to control the process where I don't get rainbow effect. Also, is the rainbow effect detrimental to prime adhesion? If you have any experience with this please let me know.
Bryan M [last name deleted for privacy by Editor]- san diego, California
2000
A. Rainbows sometimes appears if you have a high pH in your sealing tank. But only (as I know of)when sealing dark colors. I have had this problem when sealing deep black MLW (10 g/l), bronze 2LW (3 g/l) the alloy was 6063-T6.
Martin Dehlin- Sweden
A. Rainbow (or iridescence) on clear anodize is sometimes due to thin coating thickness. A coating thickness check on rainbow vs.non-rainbow should tell you if you're heading in the right direction.If it is coating thickness differences, there are many possible causes. Verify first, then we'll discuss further later.
Victor Waldman- Naugatuck, Connecticut
Multiple threads merged: please forgive chronology errors and repetition 🙂
Rainbow Defect in Bright Anodized Aluminum
Treatment &
Finishing of
Aluminium and
Its Alloys"
by Wernick, Pinner
& Sheasby
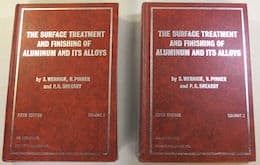
on eBay or Amazon
or AbeBooks
(affil link)
Q. We are facing problem of double refraction leading to rainbow defect after bright anodizing reflector grade Aluminum Alloys. Request help in knowing the reasons for such a defect & how to avoid such defects.
Shankar Nayak K. M.Hindalco Industries Limited, Taloja - Navi Mumbai, Maharashtra, India
2005
A. Shankar
Check your coating thickness. My guess is that you do not want a very thick coating, but by going to the other extreme, you could be getting the rainbow.
The only time I have seen rainbow on parts is when they lost contact early in the anodize process, and had almost no coating.
- Colorado Springs, Colorado
Q. We do the anodizing process for cosmetic industry and our Chinese factories are having problems; producing pieces with a rainbow effect in the color anodizing and often in plain silver color anodizing. We are looking for help to resolve.
Sandrine DesideratoJanuary 21, 2011
A. Hi, Sandrine.
Although it is difficult to troubleshoot from many miles away, rainbow 'iridescence' is a phenomenon that is sought in such fields as carnival glass and the anodizing of titanium jewelry, and it is achieved by applying a transparent/translucent coating of partial wavelength thickness. In such cases, part of the light bounces off the outer surface of the coating, and part bounces off the inner surface, and it interferes, canceling out some wavelengths.
So two possible explanations include:
1). The anodizing is very thin, only partial wavelength thickness.
2). Somewhere in the post-anodizing steps, an oily film has been deposited.
If you can attach some photos someone may recognize the situation. Good luck.
Regards,
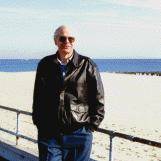
Ted Mooney, P.E.
Striving to live Aloha
(Ted can offer longterm or instant help)
finishing.com - Pine Beach, New Jersey
A. Current/voltage and anodizing solutions being proper, there could be two possible reasons.
The jigging of the parts is probably causing them to loosen during the process and hence get improper electrical contact resulting in poor anodizing.
The time for anodizing is insufficient. Increasing the time could give better results.
Hope this helps.
- Bombay, India
A. Make sure the temperature of your tank is within the range.
Muhammad Umair Khan- Lahore, Pakistan
A. I think that the original post wanted to have a rainbow effect. That is normally a result of a very thin anodize which will not take color very well for dye, and probably the same for two step.
James Watts- Navarre, Florida
Here is what I learned on anodizing.org:
Why do aluminum parts I send to be black anodized sometimes come back with a purple hue, and how can this be avoided?
There are a number of possible causes of the film. One is sealing smut. Hot water sealing blocks the pores of the anodic coating, thus improving its weathering resistance, reducing its adsorptive properties, and sealing in any pigment. However, some sealing product forms on the outer surface of the anodic coating. This is sealing smut. It consists of very small, needle-like crystals of aluminum hydroxide. They act as a thin film that can generate iridescent colors. Anti-smut additives for sealing baths are available, which minimize the problem. The formation of smut can be favored by high pH. The bath chemistry should be controlled as recommended by the supplier of the sealing additive. Alternatively, the smut can be wiped off. Before the invention of anti-smut additives, people used to wipe down parts with lanolin in white spirit. This temporarily masks the smut as much as it removes it. Manual removal is time-consuming and can be hard work.
Anodizing under conditions that are too aggressive can lead to iridescent effects. In particular, if the bath temperature is too high, the surface region of the porous anodic coating (the part of the coating that was first formed during anodizing) can be dissolved in the acid solution to the extent that it is very much more porous. This is called a "soft" coating. In general, anodizing at over 75 °F for more than 45 minutes can produce a soft coating. A simple abrasion test to detect a soft coating is described in British Standard BS 6161-18:1991."
Sandrine Desiderato [returning]
- Woodland Park, New Jersey, USA
Multiple threads merged: please forgive chronology errors and repetition 🙂
Q. We are experiencing a rainbow sheen on 6061 alloy parts that we are anodizing. The parts receive 1 mil of anodize in a ambient temperature anodize tank. They then receive 5 minutes in the black dye, which upon pulling out of the dye look extremely black. However, when we seal them in DI hot water they come out still black but with a purplish, rainbow sheen on them.
We have tried sealing at 190 °F and 200 °F, both created the same effect. We have tried sealing for 30 and 45 minutes, both had the same effect. The pH was measured to be 7.8 but I'm afraid to adulterate the DI water with acid.
Any ideas on how to get rid of the rainbow effect?
- Davenport, Iowa, USA
October 25, 2012
![]() |
A. For a dyed anodize, you'll want to use a nickel acetate type seal. I would not use a DI seal, as eventually you'll be leaching your dyestuff into the seal. If you insist on using a DI seal, you'll want to lower the ph to around 5.5-6.0 using acetic acid ⇦ on eBay or Amazon [affil link] . Even at that pH range, you'll still have a seal smut problem (which is what I think you are seeing now with the "rainbow"), which would be eliminated if you used a nickel acetate bath. ![]() Marc Green anodizer - Boise, Idaho ![]() Aluminum How-To "Chromating - Anodizing - Hardcoating" by Robert Probert Also available in Spanish You'll love this book. Finishing.com has sold almost a thousand copies without a single return request :-) A. Did you MEASURE "1 MIL" thick or did you merely specify 1 mil. Low thickness with most black dyes comes out with a blue-purple shade. You did not say what the seal was so: (1) if mere hot water -you cannot seal colors with only water - the dye will bleed, and (2) pH 7.8 is too high for either hot water sealing or nickel acetate sealing - the oxide is partially stripped at that pH and temperature. Go back and drop the pH of the seal to 6.0 and see if the purple goes away, then switch to a nickel acetate seal to prevent any dye from bleeding. ![]() Robert H Probert Robert H Probert Technical Services ![]() Garner, North Carolina ![]() |
Thank you for your responses.
The plan is to switch to a nickel acetate sealer, it is just slow going getting there. As far as the 1 mil, it was a measured 1 mil. We will lower the pH of the DI water with acetic and see what we come up with.
Upon further investigation, when we run 6061 vs 7075 same procedure and same thickness, we only get the sheen on the 6061 parts.
Thanks!
- Davenport, Iowa USA
Q. I have some parts that were anodized by a supplier. The appearance in one area has a "rainbow" appearance on the surface.
This part and the area will be primered and painted. Will this possible issue affect the integrity of the anodize?
David Torresquality inspection aerospace - Huntington Beach California
August 20, 2015
combo magnetic & eddy-current coating thickness tester
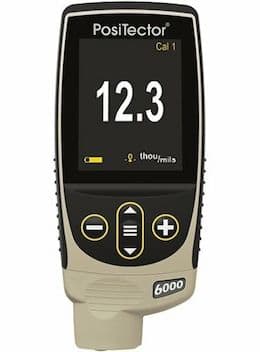
on eBay or Amazon
(affil link)
A. Hi David. Rainbow coloration -- whether it be on a puddle of water, or in carnival glass, or on anodized aluminum -- is almost always actually due to a transparent or translucent film which is so thin and variable in thickness that light bouncing off the top of the film and the bottom of the film "interferes", causing the various colors. It is possible that the film is a dye-smut "oil" on top of the anodizing, or that the film is the anodizing itself being too thin in that area. I think it's easily checked with an eddy current thickness tester. Good luck.
Regards,
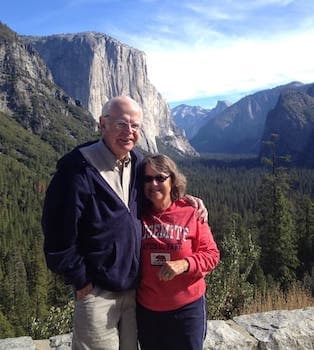
Ted Mooney, P.E. RET
Striving to live Aloha
(Ted can offer longterm or instant help)
finishing.com - Pine Beach, New Jersey
Q. Sir, I am facing problem on alloy 6063 having rainbow shades on it. What are the reasons for rainbow shades and what are the ways to control it?
nawaz sharif- lahore Punjab Pakistan
November 20, 2015
A. Hi cousin Nawaz. We appended your inquiry to a thread which discusses the possibilities in good detail. Most likely, either the anodizing is extremely thin due to a bad connection or other issue, or an "oil film" from a dye smut or other post-anodizing tank has been deposited onto the parts. Good luck, and forward a photo of the problem to if you can.
Regards,
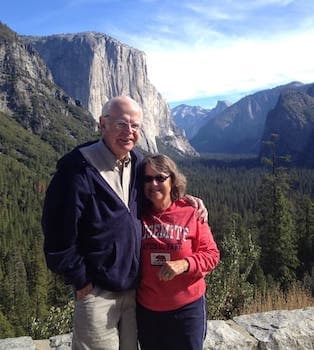
Ted Mooney, P.E. RET
Striving to live Aloha
(Ted can offer longterm or instant help)
finishing.com - Pine Beach, New Jersey
Q. We have this 6061-t651 part for Hard clear Anodizing with Hot DI Water Seal for 160 mins.
But we are getting rainbow surface and white patches after the treatment.
Any suggestion how to prevent this? We appreciate your feedbacks. Thank you.
- Jurong, Singapore
February 11, 2016
The Sulfuric Acid Process"
by David LaPlantz
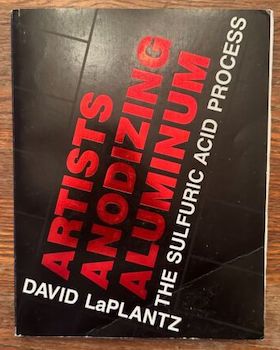
on eBay or Amazon
or AbeBooks
(affil link)
Q. Hi - I do want the rainbow effect to stay!
I am an artist. Do any of you have experience? Will it stay for years to come ?
Excited artist in Norway anne katrine
Anne Katrine Dolvenartist dolven - Bostad, Norway
August 10, 2016
Q. Why rainbow color is observed on Aluminium anodized profile with colonel 3175 as coating, after it is exposed to heavy rain?
Asif Sange- India
February 24, 2017
Purple film during anodizing process
Q. Hello, I am new to the anodizing process. The trouble I keep having is a purple film on both the cathode and part being anodized. I am using aluminum sheets for the cathode. Amps are low, around 1 amp. Your help or ideas would be greatly appreciated.
Thank you
Hobbyist - Los Angeles, California
March 19, 2017
A. Hi Karima,
My first guess is that it's just a partial-wavelength interference film as discussed on this thread. But the same film on anode and cathode sounds a bit strange. Are you sure your power supply is okay? BTW, giving the amperage without the area of the part doesn't help much, since we can't determine the current density without the area :-)
Luck and Regards,
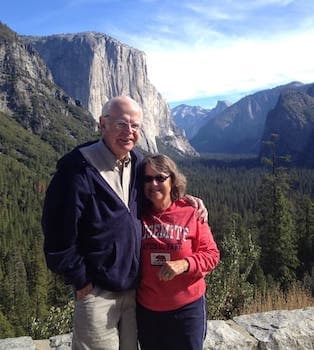
Ted Mooney, P.E. RET
Striving to live Aloha
(Ted can offer longterm or instant help)
finishing.com - Pine Beach, New Jersey
Rainbow Smut on Black Anodizing
Q. In our anodizing process we are experiencing rainbow colored smut/leaching of the dye after sealing. Has anyone experienced this issue and what is the best way to solve it.
Neville FranksonProcess Technician - South Africa
August 26, 2017
A. Rainbow major cause is low micron and loose jigging or loose tying of parts. Just make sure your parts are tightly held is anodising process or try to increase the micron with help of increasing current density or time in anodising tank.
Hope it serves.
N M Coating - Ahmednagar Maharashtra India
A. Neville
Your rainbow appearance might be from localized overheating, typically a result of inadequate anodize solution agitation.
- Green Mountain Falls, Colorado
A. Check/measure your coating thickness after anodizing. First reason for rainbow appearance after anodizing: low micron thickness (under 4).
alaattin tunaakpa aluminium - TURKEY,sakarya
Q. In an attempt to get the least amount of clarity loss on brushed aluminum 6060 I've tried anodizing for just 5 min. at 10 ASF and 5 min. at 5 ASF
Longer would always make the parts lose their beautiful fine brushed titanium appearance, turning too light grey and dull.
The rainbow effect only seems to be show unpleasantly under artificial light, in daylight it doesn't seem visible at all.
Parts are used for car interior accessories and should only be protected just enough to prevent minor scratching and fingerprints/stains.
Does this make sense and if the parts are optically looking good (in exposed daylight which is most important) and provide enough protection should I have nothing to worry about or is the rainbow glow reason for worrying either way?
Small business owner, automotive interior parts. - Assen, Drenthe, The Netherlands
August 16, 2019
A. Hi Frits. What actually causes rainbow coloration, whether it be carnival glass, an oil-slick on a puddle of water, a DVD-ROM, anodized titanium, or your anodized aluminum, is a very thin (partial wavelength) transparent or translucent coating. Incident light reflects off the outside of the coating and off the substrate (or some would say the inside of the coating) and, since one path is longer than the other, the two reflections are out of phase and interfere, augmenting one wavelength (color) and attenuating another.
The coating which is causing the interference can be either a very thin anodized film, or a film of oil. In your case it is apparently a thin anodizing layer rather than an oil.
Potential solutions which may or may not be inapplicable for you include using a different alloy which produces a clearer anodized layer so that you can go thicker; with slight simplification, the purer the aluminum and the finer the grain, the thicker you can go. Electropolishing or chemical polishing (bright dipping) may allow a thicker anodized coating without dulling than buffing.
Hopefully a reader can relate anecdotes of rainbow coloration being a problem or not being a problem in your industry. Sorry, I can't offer any assurance about that myself and it seems that there will always be at least one customer who will complain :-)
Regards,
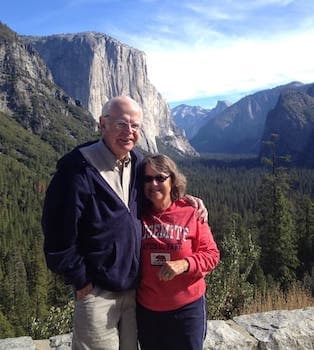
Ted Mooney, P.E. RET
Striving to live Aloha
(Ted can offer longterm or instant help)
finishing.com - Pine Beach, New Jersey
Q. Thanks Ted for your reply.
I was under the impression 6060 would be very suitable.
Better options are not easy to come by in my region at an acceptable price.
However I can't think of one that should give significant better results?
I will try to extend anodizing time (or raise the ASF) up to the point where the rainbow glow isn't occurring and see if the clarity is still at an acceptable level.
Is there in theory a best way of practice to achieve this in regards of more time with less ASF or less time with higher ASF?
Thanks again for your help.
Small business owner, automotive interior parts. - Assen, Drenthe, The Netherlands
A. Hi Frits. Type 6xxx aluminum is generally quite acceptable for anodizing. But when we want the anodized layer to be as transparent as possible, for reflectors and mirrors for example, very pure 1xxx aluminum is better. 5 to 10 minutes of anodizing at 5 to 10 ASF is not uncommon for such applications, but I don't have any personal experience regarding whether, for example, 5 minutes at 10 ASF or 10 minutes at 5 ASF is better for your requirement.
Regards,
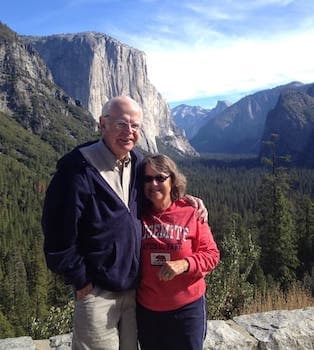
Ted Mooney, P.E. RET
Striving to live Aloha
(Ted can offer longterm or instant help)
finishing.com - Pine Beach, New Jersey
Q. Hello
I want to get a Rainbow finish on an Aluminium Base. This can be done on Titanium based on my research, but not on Aluminium. Does anyone know how to do this?
- Delhi, India
September 25, 2019
A. Hi Deepu. This thread, plus four or five others on this site, explain what generates the rainbow, but generally discuss the rainbow look on anodized aluminum more as a defect more than as something sought after. However, I would think that if you mirror polish the aluminum and then apply a very thin anodizing or clearcoat, you may be able to achieve a rainbow finish that pleases you.
I doubt, though, that it will ever be as impressive as a titanium rainbow finish because titanium is a harder metal with a more consistent oxide film.
Regards,
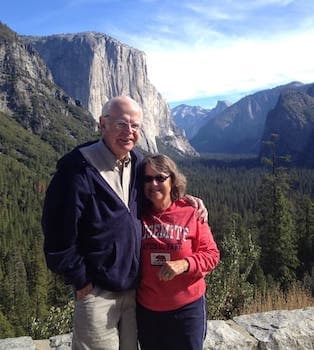
Ted Mooney, P.E. RET
Striving to live Aloha
(Ted can offer longterm or instant help)
finishing.com - Pine Beach, New Jersey
Q. Thank you Mr. Ted. We will try this out.
We are looking to do it as a colour option for a consumer product made in Aluminium, hence it is a desired effect for us.
Is it feasible to deposit Nickel onto Aluminium and then depositing Titanium to the Nickel to give it an even better rainbow appearance?
Best,
Deepu
Consumer Products in Grooming - Delhi, India
A. Hi Deepu. Although it's possible, it may not be practical or cost competitive depending on what the article is, its size, thickness of material, etc., because color anodizing of titanium is very easy and low cost.
Why try to imitate titanium with aluminum? Have you considered multicolor anodizing (beautiful examples on Thread 48706), "splash anodizing", or other decorative aluminum effects?
Regards,
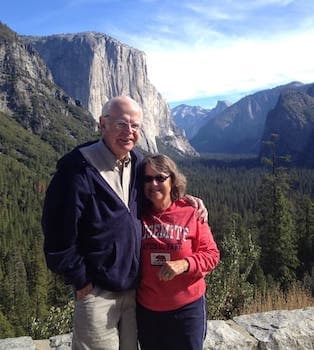
Ted Mooney, P.E. RET
Striving to live Aloha
(Ted can offer longterm or instant help)
finishing.com - Pine Beach, New Jersey
Q. I encountered a problem in the aluminum profile holes after anodizing.
- Some lines appear as faint rainbow lines (acceptable), others appear as solid black lines, like the scratches of an EE pencil. (unacceptable)
- The exterior of aluminum after anodizing is normal. Only in the grooves is a problem.
- My aluminum profile has a thickness of 3 mm, a hole height of 1 cm, and a hole length of 4 cm.
Chemist - Thailand
June 13, 2024
Ed. note: 'a picture is worth a thousand words'; please attach a pic in email to mooney@finishing.com if you can.
Q, A, or Comment on THIS thread -or- Start a NEW Thread