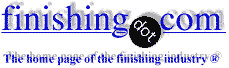
-----
Two-color anodizing
finishing.com is possible thanks to our supporting advertisers, including:
Current Q & A's:
Q. Hello finishers!
We have a part for a telescope that needs to be anodized. the trick is that overall part needs to be anodized (type II) black and a single surface on the part needs to be anodized (type II) clear. This is for optical and thermal reasons.
normally we would mask the area for the clear and leave it for alodine/irridite/chem film....but in this case it needs to be clear anodize....chem film is not good enough.
Is there a way to do this?
- Boise Idaho
January 25, 2022
A. Hi J. We appended your inquiry to a thread with beautiful pictures of parts processed per your needs, and at least some general hints how to do it :-)
Luck & Regards,
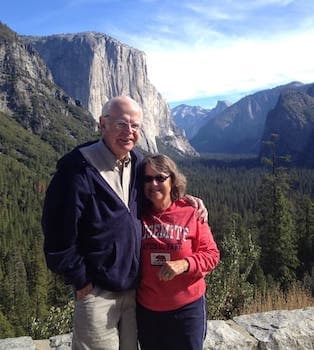
Ted Mooney, P.E. RET
Striving to live Aloha
(Ted can offer longterm or instant help)
finishing.com - Pine Beach, New Jersey
February 2022
Q. Ok, I have a motorcycle that I made a part from 6061 aluminum but I wanted to do something different than just leave it as a plain old aluminum part with circles cut out for the apathetic value . So I found a picture of an American flag blowing in the wind that matches the shape of this part I made pretty closely (I just had to mill in some recesses and such. But what I was wondering is it possible to put the red, white and blue into an anodized part of aluminum 6061? It's only about 4 x4 inches or so, not square though.
Coby Hosford- Elko Nevada
January 22, 2022
A. Hi Coby. There are pictures of some really beautiful 2-color anodizing on this thread, but there are several problems ...
First, I don't know if three colors is truly practical in very highly decorative anodizing such as is in the pictures.
Second, white anodizing is a problem just by itself; it's not impossible, but is a specialized rarity.
Third, you have to find someone to do it; and one of a kind artistry is very expensive :-)
Luck & Regards,
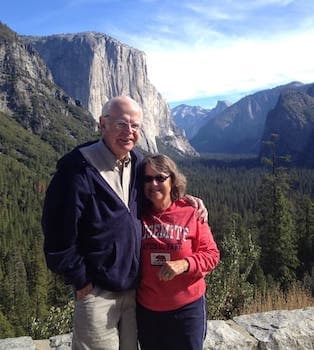
Ted Mooney, P.E. RET
Striving to live Aloha
(Ted can offer longterm or instant help)
finishing.com - Pine Beach, New Jersey
February 2022
A. I think that you can use epoxy based cold enamel for jewelry. If you really want to use anodizing then special anodizing pastes can be used, but that's not simple and easy process. Hope it helps and good luck!c
Goran Budija- Cerovski vrh Croatia
February 15, 2022
⇩ Related postings, oldest first ⇩
Q. I am currently working on some custom aluminum link bracelets and would like to anodize the 6061 material. However, after anodizing I would like to pencil blast a pattern onto the surface, removing the anodized color. I would then like to re-anodize the parts so a different color can be added into the blasted pattern.
I have three questions:
1. What is the best media to use for blasting the aluminum so not to leave foreign material in the aluminum (aluminum Oxide, glass, etc.)?
2. Once blasted, can the part be dyed and sealed again or does the part need to be acid etched again and if so will this remove the original anodized color?
3. If the part can be re-anodized, will the sandblasted texture be too rough to accept the dye properly?
I would greatly appreciate any insight into this process.
artist - Minneapolis, Minnesota, USA
May 5, 2008
Treatment &
Finishing of
Aluminium and
Its Alloys"
by Wernick, Pinner
& Sheasby
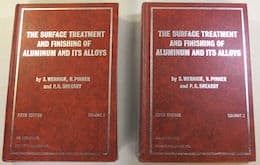
on eBay or Amazon
or AbeBooks
(affil link)
A. Hi, Nate. What you want to do can be done. In fact, very exotic multicolor anodizing can be done -- visit the paint ball gun section of a store for examples. But sandblasting is not the way for most. Instead, maskants are usually used. Mask the area , and anodize and dye and seal the rest. Then remove the masking, do your pencil blasting, and anodize and dye and seal that area. It would be best to mask the original area when you anodize the blasted area, but it may not prove necessary.
Most people don't encourage sandblasting of aluminum because it's so soft, so you might consider chemical etching as an alternative way to get a matte area. Possibilities include caustic etch and ammonium bifluoride etch.
Regards,
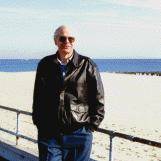
Ted Mooney, P.E.
Striving to live Aloha
(Ted can offer longterm or instant help)
finishing.com - Pine Beach, New Jersey
May 6, 2008
Ted, I appreciate the prompt reply and the information. I will explore masking techniques and pencil blasting further in order to achieve what I am looking for.
Thanks again for your thoughts.
- Minneapolis, Minnesota, USA
May 7, 2008
Anodizing aluminum, machining it, and re-anodizing it for multiple colors?
December 18, 2015Q. Hello, everyone. We're designing the aesthetic of some machined aluminum products and our local metal finishing facilities have told us this is impossible: we want to machine an aluminum surface, anodize it, and then machine other features and re-anodize to accomplish the aesthetic of the following three examples:
from m.aliexpress.com/item/535828802.html,
www.goldsprintshop.com/bilder/produkte/gross/Sugino-MC130NC-double-anodized-Bahnkettenblatt-130BCD-1-8_b3.jpg,
and www.aliexpress.com/item//32338438490.html respectively
If anodizing/re-anodizing isn't the process, what is this process? How is it accomplished? What should we be asking for to accomplish this?
We have a facility capable of machining parts like this, but we have no experience with these kinds of metal finishes (we outsource this), and this is a baptism by fire situation. Our attempts at asking our local metal finishers (they're great, but very old school) have left everyone scratching their heads.
Thanks in advance.
- Lehi, Utah
A. Practically it is almost impossible; however, it is theoretically possible. First the first anodize must be completely sealed but most job shops never completely seal anything after the first day because their seal is contaminated or they use a so-called low temp seal which never works even the first day. If you get by the first seal, then the next problem is how to prepare the surface, after machining, for the second anodizing. Use a cutting fluid that is water soluble and find a way to get it off without harming the first anodizing, probably with solvent cleaning and water rinsing. Then, the same day you did the machining. before it sets a hard weathered oxide, dip it briefly in a ferric sulphate based deox, experiment with the max time you can use without leaching the previous dye, anodize and dye, good luck with that. It can be done. People who do splash gun dyeing, keep it secret, but many secret processes are out there.
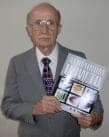
Robert H Probert
Robert H Probert Technical Services

Garner, North Carolina
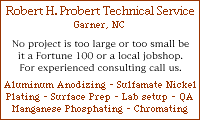
December 20, 2015
A. Hi Thomas. As the three examples show, people are doing two-color anodizing in production. I have no inside information on it, but my guess is they are doing it by anodizing the whole part, then selective masking and into the first dye tank and seal, then removing the masking and going into another dye tank and seal. A second masking step before the second dye might be required though.
If I ran an anodizing shop and had a regular customer who wanted two-color anodizing I would certainly take that opportunity to figure out how to do it rather than let my business seep away to bolder shops.
Regards,
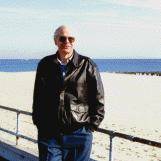
Ted Mooney, P.E.
Striving to live Aloha
(Ted can offer longterm or instant help)
finishing.com - Pine Beach, New Jersey
December 2015
A. Thomas
The Sugino chain ring appears to have been black anodized, machined, then red anodized where the machining was performed. Not too sure about the other two items.
Robert is correct that if the seal is less than perfect, you won't be pleased with the results. Typically, the lighter shade is applied after the darker, as lighter shade doesn't require the coating thickness of the darker, and the immersion time in the anodize bath is shortened.
Masking the first coat and re-anodizing is an option but in most cases not cost effective. I have seen Ted's suggestion used where the article is anodized completely then masked for dyeing, with mixed success.
- Colorado Springs, Colorado
December 22, 2015
December 23, 2015
I appreciate everyone's thoughts on this. Thank you for helping us figure this out. This is tremendously helpful.
To Willie's point, "Masking the first coat and re-anodizing is an option but in most cases not cost effective."
This was our thought, as we can build silicone molding to form fit, but it seems to be overthinking it; even perfectly built silicone molding for masking doesn't create a perfect seal, and the examples we're seeing quite literally have the color transition immediately at the tooling line -- that's incredibly precise for any hopes that an injection molded mask could ever deliver.
This leads us to believe these specific processes aren't being masked; it seems unlikely that a mask could so accurately begin the color transition at precisely the tooling line where the chamfers begin.
That being the case, we've deduced from what we've observed on the parts, and with the helpful responses so far, that the anodized part must be perfectly sealed and then remachined and reanodized for this effect to be manufactured so consistently and precisely.
We'll begin testing with a few metal finishers soon and call out some processes; any ideas on what to call out specifically to ensure the parts are completely sealed and ready for a second phase of machining?
A tremendous thank-you to Robert, Ted, and Willie for all of your thoughts on this so far.
- Lehi, Utah
A. Hi again. I'm not looking at actual parts, only photos (and with the large number of postings to deal with, not even looking closely at the photos). So if you can see machining transitions precisely at the color change lines, my revised theory is that they were anodized, dyed, and sealed all over, then masked completely all over with a dipped, brushed, or sprayed masking material rather than using a reusable mask. Then the masked component is machined (it may be necessary to remove the masking at a few points for accurate jigging). If any masking was removed for the jigging, those points could be easily repaired with a brushable maskant without any need for precision, then the part (with the existing masking everywhere but on the newly machined areas) goes to anodizing, dyeing in the second color and sealing.
Regards,
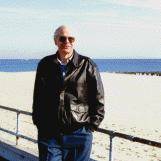
Ted Mooney, P.E.
Striving to live Aloha
(Ted can offer longterm or instant help)
finishing.com - Pine Beach, New Jersey
December 2015
Q. Hi again, Ted!
"... my revised theory is that they were anodized, dyed, and sealed all over, then masked completely all over with a dipped, brushed, or sprayed masking material rather than using a reusable mask."
This is an interesting thought! What masking materials are we talking about in this scenario? Would a first anodization that's properly sealed not work well for masking; meaning we should definitely be seeking out this spray-on/brush-on masking material?
We're very interested in finding this masking material to test, but we'll need to know what it is to call it out for the manufacturing process (four local metal guys are unaware of this stuff, so it's fascinating to learn that it exists!).
Thanks again for your very helpful responses.
- Lehi, Utah
December 28, 2015
A. Hi again. Sorry for the delay in posting your question and my response. Yes, well sealed anodizing can be used as a maskant to prevent further dyeing, but there might be limits to its total effectiveness. The masking I was speaking of is simple elastomer dips and brushable stop-off solutions made for the purpose. Even dipped wax may be useable if you are not doing heated cleaning or sealing, and only warm dyes. Where it suits, plater's tape can be used; it's similar to black electricians's tape except usually heavier and in colors like green (whether the adhesive is actually different, I don't know).
In the meanwhile, the below response came in from Geoff Smith, who is relating some actual experience in a similar process, rather than just book knowledge :-)
Regards,
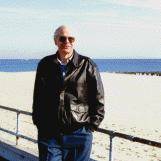
Ted Mooney, P.E.
Striving to live Aloha
(Ted can offer longterm or instant help)
finishing.com - Pine Beach, New Jersey
January 2016
finishing.com is possible thanks to our supporting advertisers, including:
A. Hi Thomas
I don't know if this helps but it could be worth passing on to your anodiser
Back in the 1970s at Kodak we developed multi colour anodising.
Standard sulfuric anodise but do NOT seal
Dip in methyl cellulose solution (common wallpaper glue)
Dry. This fills the pores in the oxide layer but prevents it sealing.
Print an image in resist - we used photoresist but you could screen print or paint an image. Dye the first colour. We probably cold sealed at this stage. Remove the resist with suitable solvent. Dry. Repeat the process with resist now coating the dyed area and producing another image on the undyed part, etc. We were able to produce a full colour image, yellow, cyan and magenta with a black overprinter of near photographic quality. The main application of the process was for the label industry.
All our work was on flat sheet but possibly it could be adapted.
If you would like to go the machining route, I must disagree with Robert Probert. There is no need to use cutting fluid for the light cut needed. Use modern carbide or ceramic tools dry and with a slow feed rate.
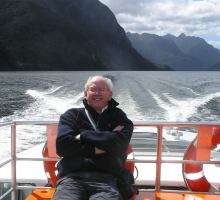
Geoff Smith
Hampshire, England
Ted,
Thanks for the update on the masking; this will help as we experiment.
Geoff,
Wow! This was a really great response. I think this gives us enough with which to experiment. Thank you.
I want to give out a tremendous thank-you to everyone who has contributed in the thread. The responses have given us a good place from which to begin testing with some local finishers.
- Lehi, Utah
January 5, 2016
A. I would attack this differently. I would apply the darker anodize coating first. Then clear coat the entire unit with a good polyurethane. Machine the surfaces requiring the lighter anodize and then apply another coat of the clear coat as the final finish.
Ed Peters- Frederick, Maryland USA
March 16, 2016
Want dyed & clear polished areas on same aluminum motorcycle wheels
Q. Hello,
My name is Mark Curtiss. I work for a motorcycle parts manufacturer. We have several lines of motorcycle wheels, rotors, hubs, pulleys, breathers, etc. on the market. We recently came out with a new finish. Our wheels are very detailed and require very clean polished edges around anodized areas. We currently are have to go back and machine cut and then polish edges after anodizing to achieve a nice finish.
I am looking for masking suggestions. This is aircraft grade aluminum. A good spray on or brush on would really speed up our process. We would like to polish the entire wheel, apply masking, trim and then anodize. Afterward we would like to be able to peel without having to re-polish. Any suggestions.
Thanks.
- Charlestown South Carolina
January 13, 2019
Ed. note: This RFQ is outdated, but technical replies are welcome, and readers are encouraged to post their own RFQs. But no public commercial suggestions please ( huh? why?).
A. Hi Mark,
There's a thread going on this topic that you might find helpful:
https://www.finishing.com/583/16.shtml
I strongly recommend a liquid maskant that has fluorescent dye in it so when you trim/peel it off, you can stick it under blacklight to be 100% certain there's no residue, including fingerprint residue from maskant contaminated gloves, due to the obvious value and time commitment of each individual wheel.
Also, get ready to buy or build a pretty good sized UV curing box. And lastly, have the techs PRACTICE, PRACTICE, PRACTICE on similarly contoured scrap parts. Application of brush on maskant can be a frustrating art! It's gooey and sticky and gets absolutely EVERYWHERE. But when you get good at it, the results are totally worth the learning curve!
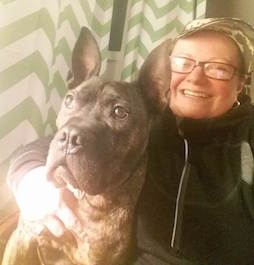
Rachel Mackintosh
lab rat - Greenfield, Vermont
January 16, 2019
Q. I want to use a black anodized belt buckle (from GRIP6). Coat the surface with wax, use a laser to etch my pattern (remove the black and the wax). Clean it then re-anodize the newly exposed surface with a gold anodize (without disturbing the wax). The pattern is a celtic symbol. Very ornate. I think it would look great with the gold on black.
If wax isn't practical what else could I use to mask off the buckle?
I want to pass the information on to a company which can do the actual work for me.
Cheers!
hobbyist - Calgary, Alberta
November 26, 2021
A. Hi Donald. You can probably use wax, but a maskant made for the purpose might be better because after that laser engraving you might need to re-clean or re-etch or seal at a temperature a bit high for wax.
Although myself and others with some anodizing and metal finishing experience may make some good guesses, you would probably be better off, if possible, sending your buckle to an anodizing shop with two-color experience rather than trying to advise a shop 3rd hand how to do something neither they, nor you, nor probably we responders, are experienced in :-)
Luck & Regards,
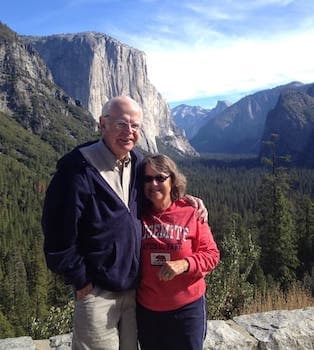
Ted Mooney, P.E. RET
Striving to live Aloha
(Ted can offer longterm or instant help)
finishing.com - Pine Beach, New Jersey
November 2021
Thank you for the feedback. You are right. As long as it is possible I only need to find someone to do it. Perfect.
Thanks again.
hobbyist - Calgary, Alberta
November 29, 2021
Q, A, or Comment on THIS thread -or- Start a NEW Thread