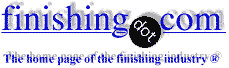
-----
Plating Racks and Vinyl Plastisol Coating
Q. Hello, We are in the process of making stainless steel racks to hold aluminium products for nickel plating. Our old racks had a coating on them, but the manager wants to skip this step. Will this cause problems with adhesion? Thanks in advance.
rob hofs- Waalre brabant, Netherlands
Q. We are looking for a chemical powder to put on the Plating Racks in order to protect the Plating Racks from Acid (Nitric Acid) and Alkali Attacks or Corrosion.
The chemical powder should also prevent electrical currents passing through the plating racks.
Please advise which chemical to use, and companies who supplies them.
It would be tremendous help to us.
co-operative co., China
1998
A. Leo,
Why powder?
Plastisol has been used for years for this purpose. There are dip and no heat products like Tolber's Super XP 2000 that are very good if several coats are put on. There are some new water based, heat set, masking materials that are a little easier to get off when you want to re-coat the rack.
Powder coat is going to be thinner, but I guess multiple coats could be put on. A plain epoxy or polyester will not hold up to both acid and caustics for the length of time you would desire. A vinyl or a composite powder might.
- Navarre, Florida
1998
Need material most suitable for chrome plating fixtures
Q. Looking for information on types of material to make chrome plating fixtures out of?
David Shealy- Columbia, South Carolina, USA
2002
A. Look around and see all the chrome being used right now for decorative purposes - and then see if you come up with any novel ideas, because these are taken. You can plate chrome on just about any metal but chrome as long as your substrate is properly prepared. Consult a good plating handbook to start out.
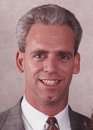
Tom Baker
wastewater treatment specialist - Warminster, Pennsylvania
2002
A. I think David is speaking of plating racks when he says "fixtures", Tom.
For decorative chrome plating the racks are usually made of plastisol-coated copper with stainless steel tips, David.
The Electroplating Engineering Handbook ⇦ this on
eBay,
AbeBooks, or
Amazon [affil links]
has a very good chapter on the subject.
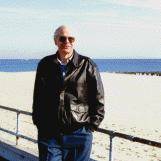
Ted Mooney, P.E.
Striving to live Aloha
finishing.com - Pine Beach, New Jersey
Need polymer or plastic to coat cathode and contacts used in plating
Q. Hi, I'm a plating engineer,
I'm looking for chemicals, polymer, rubber or plastic used to coat the cathode or contact in metal finishing/plating industries. Normally it's been used to coat the Cathode Work or finger.
Does anyone know who can supply this material?. Can I have the contact number?
Regards
semiconductors - Seremban, N.Sembilan, Malaysia
2000
A. Hi cousin Misri. Are you referring to vinyl (PVC) plastisol coatings that are typically used on plating racks?
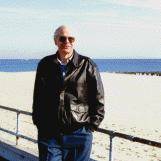
Ted Mooney, P.E.
Striving to live Aloha
finishing.com - Pine Beach, New Jersey
2000
A. Plastisol is the most durable. There are numerous air dry vinyl coatings available that will do quite well for less demanding operations. Cheaper and easier to apply.
James Watts- Navarre, Florida
2000
Need Ausimont Halar 6014 ECTFE Powder Coating
RFQ: Need halar coating for plating racks -- any idea.
Arcelia G [surname deleted for privacy by Editor]Plating - San Diego, California, USA
2005
Ed. note: This RFQ is outdated, but technical replies are welcome, and readers are encouraged to post their own RFQs. But no public commercial suggestions please ( huh? why?).
A. Hi Arcelia. The usual material is vinyl plastisol. I am not familiar with the use of Halar powder coating on plating racks, but if you have some experience with it please let us know.
Luck & Regards,
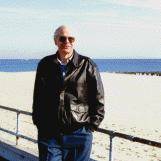
Ted Mooney, P.E.
Striving to live Aloha
finishing.com - Pine Beach, New Jersey
Plastisol patching
Q. Hi,
There is plastisol coating on our brass plating racks. But they are cracked with the passage of time. I'm looking for plastisol patching material and method. Is it possible to patch plastisol? Could you please help me with your suggestions?
Thank you,
quality engineer - Turkey
2006
A. Hello Sema,
There are companies that supply plastisol patch exclusively for plating racks. Some require only air drying one hour between coats. A simple internet search of "plastisol patching" will get you started. Good Luck!
process engineer - Malone, New York
2006
Multiple threads merged: please forgive chronology errors and repetition 🙂
Coating Plating Racks with insulating stop-off?
Q. I have a plating fixture made primarily out of Cu-Be sheet-spring metal and need to find a low-porosity durable dielectric coating that will prevent plating onto the fixture itself when used to plate the work-piece.
I have tried "Teflon-S" 2-mil powder coating but it peeled off and plated through. There are better and thicker Teflon coatings that are cured at up to 500 °C, but I am concerned about degrading the spring properties of the Cu-Be spring-metal.
I am considering having the fixture aluminum plated followed by anodization and teflon coating. I do not know how well this coating will work as an insulating layer on plating fixtures
Another idea is to simply coat the fixture with either thermal spray coated or CVD Ti - and rely on the "non-platability" of Ti
Please give me your insights on these options!
Thank you,
Technology Development - Milpitas, California, USA
January 18, 2011
A. The cheap way is to cover it with vinyl tape with a 50% overlap. This will get most of the fixture and is quick and a lot cheaper.
A do it yourself would be to coat it with a primer and then Super X_P 2000 from Pyramid Plastics, in Arkansas, a div of Michigan Chrome and Chemical.
Long term is to have it plastisol coated by a professional company. You can do it yourself if you have a low temp oven. There is a learning curve.
Last option is several coats of a proper stop off lacquer available from many companies.
- Navarre, Florida
A. Dear Brother,
Please use shrinkable sleeve on fixtures. This shrinkable sleeve gets shrunk at 125 °C. After shrinkage it will take shape of the base material. It is cheap too, you can change it again and again. These sleeves are used in electronic industries.
I am using these since last 8 months in Tri Nickel Chrome Plating Racks. This has reduced wastage as excess build up of Nickel on contact points. This has also eliminated Nickel plating peel-off issue.
- PUNE, Maharashtra, India
February 22, 2013
Q. Sirs,
We are doing the Inner hard chrome plating for the values.
For that we made the copper jig to give the cathode connection. Our problem the copper pieces are frequently dissolved in the bath; it leads to problems in the bath also.
Is there any alternate material is available to do the jigs like SS? What grade: 316/304?
I need the help regarding this one.
With regards,
plating shop employee - Coimbatore, Tamilnadu, India
A. Hi Sakthivel. The copper needs to be plastisol coated.
Regards,
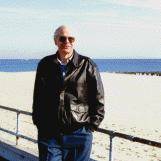
Ted Mooney, P.E.
Striving to live Aloha
finishing.com - Pine Beach, New Jersey
February 24 , 2013
Q. Dear Sir,
We are facing issues in Plastisol coating quality for our Electroplating jigs.
We want to know the complete process and inspection procedure and test method.
Please help me.
Regards,
- Vadodara, Gujarat, India
July 29, 2014
January 29, 2020
Q. Hi,
I'm also working on a plating fixture which uses a stainless spring material and I'm looking for a durable dielectric coating that will prevent plating onto the fixture too.
I've come across a few products like these:
Liquid Rubber Waterproof Sealant/Coating and
Dura Rubber Liquid Rubber.
Have anyone on this forum heard of using these types of products? I honestly don't know much about plating, and I wonder if these products would be compatible with the chemicals involved with electroplating in general?
LEISURE BATHS LTD. - BURNABY, BC, Canada
A. Hi Jonathan. It would be better to contact a plating process or equipment distributor, or google 'plating rack manufacturer'. The "standard" coating on plating racks for decades has been dipped vinyl plastisol applied by the rack manufacturers and baked.
Air-dry plastisol touch-up coatings, maybe not dissimilar to the products you mentioned, are sometimes used to temporarily repair a cut or nick in plastisol coatings, but don't have the adhesion and durability to be a good answer as an original coating -- plus you need to be concerned about contaminating the plating tanks with organics if you're not sure about these specific coating materials.
Also, plan from the get-go to have carts or an area on a wall where you can hang the racks. Standing or laying them on a concrete floor will abrade them and require too much maintenance.
Regards,
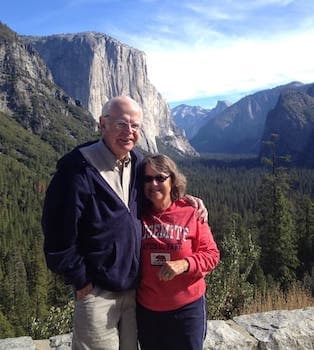
Ted Mooney, P.E. RET
Striving to live Aloha
finishing.com - Pine Beach, New Jersey
January 2020
Using uncoated stainless steel racks for nickel plating of aluminium
September 30, 2020A. Hi Rob. I could be misunderstanding you, or you may be misunderstanding the manager, but there is zero possibility of using uncoated stainless steel plating racks for nickel plating.
Luck & Regards,
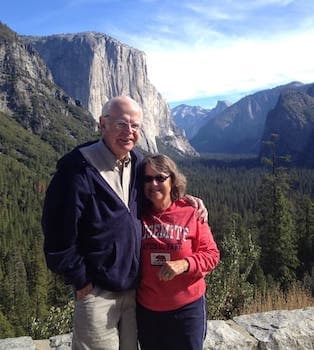
Ted Mooney, P.E. RET
Striving to live Aloha
finishing.com - Pine Beach, New Jersey
October 2020
finishing.com is possible thanks to our supporting advertisers, including:
Q, A, or Comment on THIS thread -or- Start a NEW Thread