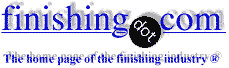
-----
Nickel plating has white patches and milkiness
Q. Sir, I am doing Sulfamate nickel plating on copper strip (reel to reel. Total nickel 85 to 95 gm/ltr, pH is 4.0, temp 58 to 60 °C.
I am having the problem of non-uniform finishing on coil, please suggest. At top, bright nickel; and at middle dull finishing is observed
Pravin Sahane
Shop employee - Mumbai, India
June 3, 2024
A. There are a million factors that can possibly be contributing to your low current fogging or low current area dullness. I am unaware of any brightener systems commonly used in a sulfamate bath except the non pitter and grain refiners typically used in them that do have an effect on finish. Low current fogging could be metallic or organic contamination. You provided very little info about your solution and process. The grain refiner (usually a trade name but typically comprised of trisodium salt naphthalene) has the greatest effect on brightness in the deposit. You are going to want to determine if you have contamination or another problem starting up first. Otherwise the grain refiner will just be masking the problem and it will likely return. Good luck.

Chance Dunstan
Electroplating/Forming/Coating Manager
Placerville, California USA
⇩ Related postings, oldest first ⇩
Q. Hi, I am a materials technician and I am trying to get our automatic plating line working properly. Currently it is outputting parts which are quite significantly covered in a white, milky deposit. It does not come off if you scrub it and very wide spread. Our chemical bath analysis has come back as fine with the exception of high levels of brightener. Any ideas how I could fix this?
Mark McKinnon
Technician - Rugby, Warwickshire, United Kingdom
November 11, 2010
A. Mark,
Assuming your bath is Watt's bright Nickel, white/milky deposits are due to :
1. Too low temperature during plating.
2. Too low current during plating.
SK Cheah
- Penang, Malaysia
A. High brightener in Nickel baths may cause white patches at part surface after chrome plating.
The rinsing process can't remove the excessive brightener retain on part surface.
These organic matters were seen as white patches after chrome plated.
EC Lim
- Johor, Malaysia
![]() |
? Hi Mark, Just a few questions. A. You mentioned that you have too much brightener, but there are two types of nickel brightener in the solution: |
A. White spots have different sources.
Brightener breakdown produces organic contamination there are many sources that could lead to this type of white spots, what Mrs Sara said is interesting and she always give the right answer besides teaching new aspects about plating.
But if you want to solve the problem attack the two types of sources.
Carbon treatment for organics
High pH treatment for contamination of metals (i don't think its the cause but just to be sure)
correct pH
Dummy plating for copper and clean the bath
... and if that does not work and the lab test are showing good numbers the reason is not on the bath
Daniel Hernandez
- Bucaramanga Santander Colombia
Thank you to everyone for your help with this.
Q. The milky coating is not uniform over the entire part, however it is widely prevalent. The part itself is a thick boss circular boss in the middle surrounded by a much thinner flange. The boss' tend to be fine, while the flange is in a much poorer state. Their also appears to be cleaner spots toward the bottom where the liquid temporarily pools when the flight bars are lifted.
The bath composition is Nickel Chloride, Nickel Sulphate, Boric Acid and a HS-Nickel Sulphamate additive. The brightener levels have since been reduced back into its specified level, but with no improvement in coating. Plating time is 7 minutes, at 60°c and with air agitation. The components themselves are copper, with a copper/silver braze used to join the boss to the flange.
The filtration we have is a Siebec MC-10 filter, and in order to be thorough we have recently changed the filter, in addition to changing the anodes and anode bags.
I do not know if this is important but in order to rule out some things I have attempted some strenuous hand cleaning with no effect. However it has been found that cleaning the copper with either copper-bright or brasso SIGNIFICANTLY improved the coating we could put down.
Further to the above information, we are currently looking at whether our electrolytic cleaning is not working properly. The chemistry has come back alright, but we're not convinced it is working effectively. What is a foolproof way to check? How much effervescence should be given off? It doesn't appear to be very vigorous currently.
I sincerely appreciate all the time everyone has contributed to this.
Mark McKinnon [returning]
- Rugby, United Kingdom
December 7, 2010
? Hi Mark,
Thanks for getting back to us. Can you send us photos to show what the problem and parts look like.
Also, are you using a wetting agent in the bath? If you are, is this wetting agent recommended for air agitation
Did you contact the vendor who supplied the bath chemistry?
Maurice Mason
- Danbury, Connecticut, USA
I have submitted some photos to be attached to show you some examples of the finish we are getting. I'm not sure if it's helpful or not but the finish in the top right of the image (the portion that is different to the rest)is at the bottom of the component as it is jigged up, and as such is where the liquids pool. To reiterate, our bath is made up of Nickel Sulphate, Nickel Chloride, Boric Acid, and this HS-Nickel Sulphamate additive.
- Rugby, United Kingdom
![]() |
A. From the pictures, the first thing that I would do is to increase the agitation in the plating tanks. That is a quick and relatively cheap check. A. Hi. A. Thanks for the photos. Based on these photos, the problem seems to be happening mainly on one side of the part.
Now, some more questions. A. Mark, |
Thank you to everyone for all of your help. As it turns out it appears our copper supplier is at fault. We have run samples of copper down as we receive it which came out contaminated. We then asked for a sample of copper as our supplier receives it from THEIR supplier. When we subsequently attempted to plate this it came out perfect. It would seem therefore that something in their process is causing our issues.
Mark McKinnon [returning]
- Rugby, United Kingdom
Q. I'm suffering from the white spots during nickel plating.
What to do to solve this problem?
Pradeep singh raghav
Jaydeep Industries - Vadodara, gujarat, India
July 21, 2019
? Hi Pradeep. Such problems have multiple possible causes as you can see on this page or by searching the site. Please start by trying to answer the questions that were posed to Mark, or comment on the possible solutions that were offered to him, and tell us how your problem differs if it does. The readers are usually helpful, but they don't want to pull teeth posting the same questions; please tee up the problem as best you can :-)
Thanks!
Pics to mooney@finishing.com for posting here please.
Regards,
Ted Mooney, P.E. RET
Striving to live Aloha
(Ted is available for instant or longterm help)
finishing.com - Pine Beach, New Jersey
Q. Hi Sir,
Following plating after nickel tank treatment I got white or milky spots on my Mild steel circular 31 mm diameter rod.
Everyone is talking about white spots, but my issue is, how can I remove the white or milky spots on the components after electro nickel plating after generating white spots or milky spots on my 31mm rod face surface?
- Andhra Pradesh, India
November 17, 2022
A. Hi Srikanth. I personally have never heard of removal of nickel plating discoloration as bad as this. I feel you have a problem which must be rectified in the plating process, not cosmetically fixed after plating.
Unfortunately, troubleshooting plating problems is usually not a quick "this is what the parts look like, so here is the correction" that we'd like it to be, but can require quite a bit of digging and data. You posted another "white spot" problem 2-weeks ago as topic 41922 and received suggestions. Please try your best to answer some of the insightful follow-up questions our readers have asked, and hopefully we can get to the root of the problem. Thanks!
Luck & Regards,
Ted Mooney, P.E. RET
Striving to live Aloha
(Ted is available for instant or longterm help)
finishing.com - Pine Beach, New Jersey
A. White/milky spots in nickel plating could be caused by high organics and/or high current density. Have you checked if the same problem appears in a Hull Cell panel?
You could carbon treat your bath to see if the problem disappears.
As for removing the spots, there are proprietary products that can remove the plating without affecting the steel below, so you can replate your parts when the problem is solved.
Regards,
Pedro Franco
- Rio de Janeiro, Brasil
November 21, 2022
[editor appended this entry to this thread which already addresses it in lieu of spawning a duplicative thread]
Q. Hello,
We are having problem with white patches/dots that appears a few days after plating. The white fields seems to be growing by time.
Some facts:
- Hardened steel product (shot blasted, tumbled (trowalized) and alkalic washed after hardening).
- The white spots are alkaline when tested.
- Able to remove the patches/fields/dots with citric acid
⇦ on
eBay
or
Amazon [affil link] but it reappears after a few days, now some areas of the surface may appear blackish.
- We are using two different plating companies and the problem only appears from one of the companies.
Please help me find the root cause to this problem.
- Eskilstuna Sweden
July 27, 2023
A. Hi Tomas
We added your question to a thread on a very similar topic which should provide good food for thought about such possibilities as excessive nickel brightener.
But realistically, you may need to find another supplier for that part because it is very difficult for a customer to solve a problem at one of their supplier's plating plants.
Luck & Regards,
Ted Mooney, P.E. RET
Striving to live Aloha
(Ted is available for instant or longterm help)
finishing.com - Pine Beach, New Jersey

Q, A, or Comment on THIS thread -or- Start a NEW Thread