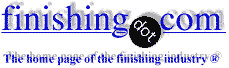
-----
Blue or yellow passivation better after Zinc plating?
(to provide context, hopefully helping readers more quickly understand the Q&A's)
Zinc plating virtually always needs & receives a subsequent "chromate conversion coating" (sometimes called 'passivation') to deter white rust. In the 'old days', pre-1990s, there were two types:
1. a very robust hexavalent chromate which was usually yellow/golden. Hexavalent chromate is inherently yellow, so the yellow color had a cause and a meaning.
2. a much less corrosion resistant trivalent chromate which was usually clear or blue.
As many of us now know and accept, hexavalent chromates are toxic and carcinogenic, so there has been worldwide pressure to reduce or eliminate their usage, and many rules have been established (RoHS, REACH, and automotive standards for example) which restrict or forbid hexavalent chromates.
Fortunately, new developments in the late 1990's and beyond have now made proprietary trivalent chromates (usually with an additional 'sealant' step) the equal of hexavalent chromates, at least in salt-spray test corrosion resistance. Many of these proprietary trivalents are inherently clear or almost clear such that a yellow color usually only indicates the presence of dye, not additional corrosion resistance.
Q. Dear Sir,
We are doing low cyanide Zinc plating on steel parts of our that are exported to Europe. Due to REACH law we cannot do hexavalent Chromium Passivation. We have therefore used a special (branded) passivation with trivalent chromate + Silica nano particles. Before 96 hrs NSST (ISO-9227 ) there is white rust and black spots on the parts (see attached picture). What is the reason for these black spots and white rust? Some of the other parts we do zinc plating and hexavalent passivation do not show any black spots in SST. Does Silica nano particles cause this black spots ? Please provide your opinion and feedback regarding this. What can we do to avoid this problem? Our target is no black spots / white rust for 96 hrs in SST.
Best Regards
Yasir Khan [returning]Manager Electroplating - Karachi, Pakistan
September 2, 2021
A. Hi Yasir. I don't have any insight into the electroplating process supply situation in Pakistan, but it does seem like the trivalent chromate available to you is simply not up to the job.
![]() | I know it can be hard for people from countries where names are not in english to always use the same anglicized version of their name, but it is helpful to know when people have long-running problems, so please try. For example, we see that you are the same person as 'Yasir Zoha', and have been having this problem for two years now. |
Luck & Regards,
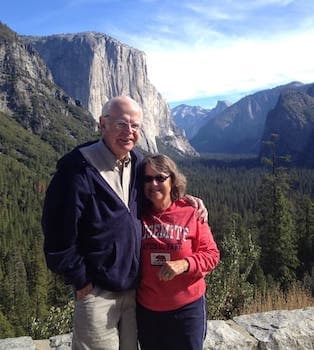
Ted Mooney, P.E. RET
Striving to live Aloha
(Ted can offer longterm or instant help)
finishing.com - Pine Beach, New Jersey
September 2021
"REACH: Proposition 65 on steroids and suffering steroid psychosis" :-)
A. Hi Yasir,
As Ted mentioned, the tri-chromate you are using just isn't good enough. Nano-silica chromates are a well-established technology and work fine up to 240 hrs of white rust resistance in salt spray test (at least for us, for an acid zinc plating line). No black spots and white rust for 96 hours should be easy-peasy for them.
I suggest you talk with your vendor and try to adjust the process parameters. Or, try another vendor, if they can't help you.
Best of luck!
Daniel
Quality Manager - Cañuelas, Buenos Aires, Argentina
October 4, 2021
Q. Dear Daniel Montañés & Ted Mooney,
Thanks for your feedback and time. I just wanted to have an opinion from the experts.
Another food for thought -- does cyanide in the alkaline zinc cyanide plating have effect on the subsequent silica trivalent passivation? If we do Non-cyanide alkaline zinc plating will it be able to strengthen the subsequent passivation and give better corrosion resistance (no white rust / black spots after 96 hrs SST).
Thanks
Manager Electroplating - Karachi, Pakistan
October 5, 2021
A. Hi Yasir. Alkaline non-cyanide zinc is more difficult to passivate than cyanide zinc (see thread 2222 and thread 47757). But your posting does introduce the thought that perhaps improving the steps between plating and passivating may help. If it is practical for you to experiment, you could take a part after plating, rinse it, then dip it in 1% nitric acid, then rinse it again, and chromate it and see if that solves the problem (you'll probably need that step anyway if you switch to alkaline non-cyanide plating).
Luck & Regards,
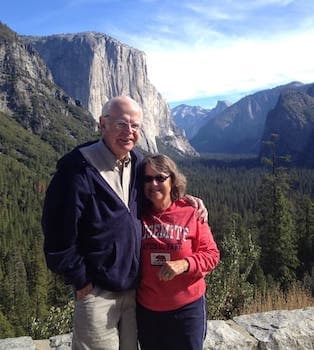
Ted Mooney, P.E. RET
Striving to live Aloha
(Ted can offer longterm or instant help)
finishing.com - Pine Beach, New Jersey
October 2021
A. Hi Yasir.
As Ted mentioned, nitric acid dip is mandatory (for a good chromate) after plating (rinse-rinse-nitric-chromate is a good option). For good chromate, cyanide zinc is the easiest to go, then non-cyanide alkaline, then acid zinc (I think chromates have a though job with acid zinc plating). BUT alkaline has the alkali to neutralize prior to chromate, and this could be your problem (or just the product not working well enough).
If you want more info, we need more info from your side! Share and I think the community will share with you. At least, works for me.
Best of luck for you.
DM
Quality Manager - Cañuelas, Buenos Aires, Argentina
October 5, 2021
A. My understanding of REACH is that hexavalent chromium is only a problem if it constitutes 0.1% w/w of the total weight of the part or more. Have you evaluated the quantity of hexavalent chromium compounds on the surface of the part? Or are you eliminating all hexavalent chromium just to be safe and stay ahead of future regulation?
Q. Maybe I am misunderstanding REACH. If so, hopefully some one can clarify, but to me it does not seem that hexavalent chromium has to be completely eliminated to be in compliance with REACH, other than in concrete and leather goods.
Ken KirbyMaterials Engineer - Kenosha, Wisconsin, USA
October 19, 2021
A. Hi Ken. You might be right about REACH; but other regulations like RoHS may be applicable ... and I know that in that one the plating layer plus the chromate are considered to be 'homogeneous' and the percentage of hexavalent chromate in just the coating is regulated.
Luck & Regards,
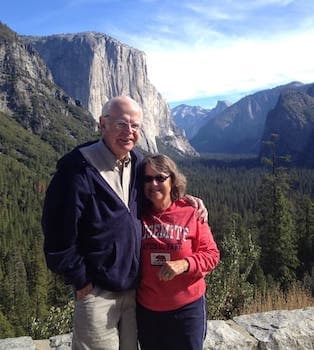
Ted Mooney, P.E. RET
Striving to live Aloha
(Ted can offer longterm or instant help)
finishing.com - Pine Beach, New Jersey
January 2022
A. I agree with the thread, to end Hexavalent chromium you need to be careful. Our tests show Trivalent to be acceptable. we are also looking into Zi-Ni with Trivalent in place of Cadmium with HexChromium, that in salt fog looks great, but you must have the Trivalent chromium on top of the Zi-Ni.
Kirk W. OlsenAerospace Design Engineer - Erie Pennsylvania
January 3, 2022
![]() |
But a note to readers so they don't jump to conclusions: corrosion resistance is not usually the main parameter that dictates/dictated cadmium plating. Lubricity, malleability, freedom from stick-slip, compatibility with aluminum, and lack of gummy or bulky corrosion products are often equally important factors. Luck & Regards, ![]() Ted Mooney, P.E. RET Striving to live Aloha (Ted can offer longterm or instant help) finishing.com - Pine Beach, New Jersey January 2022 |
⇩ Related postings, oldest first ⇩
Q. Dear Sir,
I want to know the comparison between blue and yellow passivation in Zn plating and which is the best one to follow. Explain me with some justification. Do the needful in this regard.
Regards,
QA/QC Engineer - Riyadh. Kingdom of Saudi Arabia
July 13, 2010
July 13, 2010
A. Hi, Hari. A few years ago the answer would have been that yellow chromate is heavier and contains more hexavalent chromium, and offers about 2-1/2x the corrosion resistance.
But today, what with RoHS standards, most "chromates" are trivalent and basically colorless, and most of the color you see is just dye. Further, the chromates are virtually all proprietary and based on several different technologies: thin film vs. thick film, sealer vs. no sealer, etc. One of the minor pieces of fallout from this generally beneficial change is that the color gives you no indication at all of the corrosion resistance.
Regards,
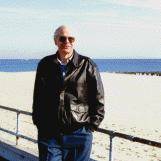
Ted Mooney, P.E.
Striving to live Aloha
(Ted can offer longterm or instant help)
finishing.com - Pine Beach, New Jersey
A. Welcome all
You can use yellow but if green available you can use it also.
Regards,
steel factory - Cairo, Egypt
September 19, 2010
Zinc Plating: clear, blue, yellow, green passivation differences (trivalent or hexavalent)
Q. I want to know about the processing of zinc plating, different types of passivations (clear, blue, yellow, green), (trivalent or hexavalent), how this is being processed also their advantages and disadvantages.
Himanshu Vashishtha- Gurgoan, Haryana & India
September 9, 2018
September 2018
(affil links)
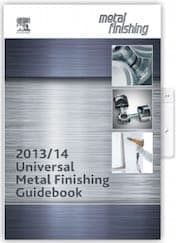
free pdf is currently available from academia.edu
A. Hi Himanshu. These days you usually must use trivalent chromates because hexavalent chromates are not RoHS compatible. There is usually very little difference in the chromates except for their color, as it is usually just dye, although there are exceptions like proprietary thick-film trivalent chromates.
If you tell us who you are, what you do, why you want to know, and what kind of parts you have in mind we can probably help you arrive at some decisions. But without that it's hard to get started ... books about zinc plating are hundreds of pages long and we have a hard time knowing whether to start with a discussion about rack vs. barrel plating, cyanide vs. acid vs. alkaline zinc plating, pretreatment for plating, chromates & sealers, or what. Thanks.
Regards,
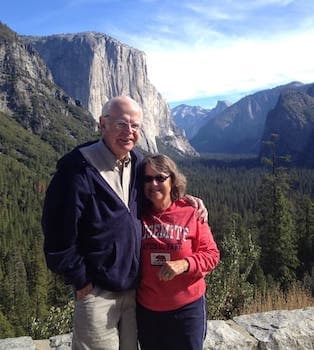
Ted Mooney, P.E. RET
Striving to live Aloha
(Ted can offer longterm or instant help)
finishing.com - Pine Beach, New Jersey
What treatment should we give to pregalvanized EMT conduit?
Q. The same question for our EMT Conduit Tubes made out of pregalvanized steel sheets. Which passivation should I use to give it anticorrosive properties as well as a clear surface keeping its shine?
Amed HassanEl Delta El Masreya - Cairo Egypt
January 20, 2019
Ed. note: This RFQ is outdated, but technical replies are welcome, and readers are encouraged to post their own RFQs. But no public commercial suggestions please ( huh? why?).
A. Hi Amed. The appropriate chromate quench or clear chromate conversion treatment will have already been applied by the galvanizer. It may be difficult or impractical to apply a chromate a substantial time later because the conduit is no longer clean and active -- and to the best of my knowledge it is not done.
I think you dare not apply an organic clearcoat because you will be defeating the expectation that galvanized conduit is conductive.
If I am misunderstanding, and you are fabricating EMT conduit in house from pre-galvanized material, there will be no zinc left at the weld line, and the whole surface is likely to be dirty and inactive after fabrication; so I think you need to clean, activate, zinc electroplate, and chromate post-treat it after fabrication. As for which chromate, you probably should use a RoHS-compatible proprietary clear chromate. There may be ASTM, ISO, UL and similar standards for EMT tubing that dictate what must be done. Good luck.
Decades ago I worked for a company which manufactured conduit plating machines and I saw them in the field, but I was never personally involved in designing them and I don't know exactly what steps they executed, how thick the plating was, or whether they started with pre-galvanized material. That 'they exist' is about the limit of my knowledge on that subject :-)
Regards,
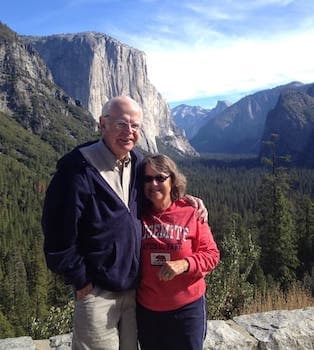
Ted Mooney, P.E. RET
Striving to live Aloha
(Ted can offer longterm or instant help)
finishing.com - Pine Beach, New Jersey
January 2019
Q. Trivalent chromium Passivation was invented and used for more then 10 years now but still its corrosion resistance is very weak as compared to that of Hexavalent Chromium? Is this true? And if yes why is this so ?
Yasir ZohaAlsons Group - Karachi, Pakistan
September 3, 2019
A. Hi Yasir. No, I don't think that's true. Although trivalent chromium conversion coating is not as simple, reliable, and overall robust as hexavalent chromium, I think the corrosion resistance of today's proprietary trivalent chromium conversion coating processes is just as good as hexavalent chromium.
Regards,
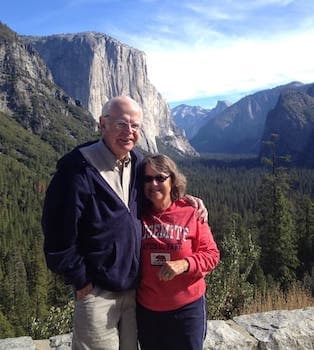
Ted Mooney, P.E. RET
Striving to live Aloha
(Ted can offer longterm or instant help)
finishing.com - Pine Beach, New Jersey
September 2019
Ok Thanks Ted
Alsons Group - Karachi, Pakistan
September 4, 2019
A. High cobalt base trivalent passivation gives good corrosion protection.
Devikant Choudhary- Pune, Maharashtr, India
May 31, 2020
Q, A, or Comment on THIS thread -or- Start a NEW Thread