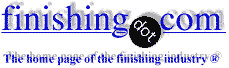
-----
"Dot Skip" Problem in Plating of ABS Plastic
Current question and answers:
Q. I am facing problem called skip plating, as some of the parts (approx. 10%) skip to plate at some areas.
Vikram jhaa- Chennai, Tamil Nadu, India
February 4, 2021
February 2021
? Hi Vikram. We assume you're dealing with plating on plastic because that is where the term "skip plating" is predominantly used, so we attached your inquiry to a long thread with lots of instruction regarding what you can do next. But give us some details please. Thanks.
Luck & Regards,
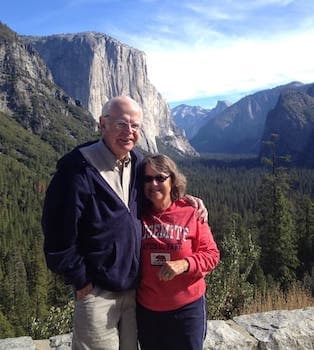
Ted Mooney, P.E. RET
Striving to live Aloha
(Ted can offer longterm or instant help)
finishing.com - Pine Beach, New Jersey
Q. Dear sir,
You are right that I am doing plating on plastic.
Previously I faced skip plating problem, now resolved up to some extent.
One thing I want to know is if my activator (Pd) tank contains chrome and iron impurities, then how can I resolve it. Any treatment procedure with help of chemicals is available? Please let me know.
Regards,
- Chennai Tamil Nadu, India
February 22, 2021
A. Hi Vikram. We moved your question about contamination of Pd activator tank to thread 56574 rather than have this thread wander. While we await answers on that new one, please tell us what you did to resolve those skip plating issues. Thanks.
Luck & Regards,
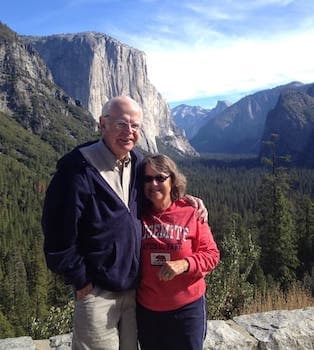
Ted Mooney, P.E. RET
Striving to live Aloha
(Ted can offer longterm or instant help)
finishing.com - Pine Beach, New Jersey
February 2021
A. Hello sir,
For skip plating problem solution I took some steps as below-
1) Reduce the temp. of etching ( 3-4 °C)(for instant result only)
2) changed water rinse and dragout after etching.
3) Strengthened neutraliser and pre dip( Make new if possible)
4) Slightly increase tin and Pd( ppm) in activator.
5) Keep focusing on etching chrome -- must not travel up to activator tank.
So these were the steps I took to resolve my skip plating problem.
These steps I took according to my understanding.
Q. Please discuss more and share your experiences and views for more learning.
This is the also the reason I am searching methods to reduce Chrome contamination in activator (Pd) tank.
Suggest me if I am going wrong.
Regards,
- Chennai Tamil Nadu
April 20, 2021
A. Let's start with the chromic/sulfuric etcher.
CHROME Trivalent should not be higher than 25 g/l.
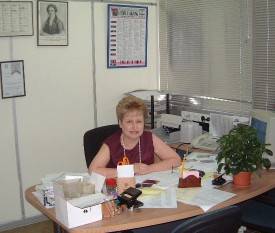

Sara Michaeli
Tel-Aviv-Yafo, Israel
⇩ Related postings, oldest first ⇩
Q. Hey friends, Am working with an automotive company in India (down south at Chennai). Been trying to develop decorative Chrome plating on some ABS (natural - plating grade) with a Supplier. Been having a couple of problems on the process with getting the perfect finish.
The problem is that we get some small (up to 2 mm dia.) dots of skip plating (we call it "dot skip") on the A surface (appearance face). It happens on almost all parts in the jig and hi rejection on this. They have got a bath of capacity of 10 parts (300 grams each approx. weight) with a 35 step process including all the swills and washes. But not able to fix the problem.
We guess it must be something to do with the etching process at the beginning stage of process, but not much works on getting this fixed. Anybody with ideas or prior experience or suggestions?
Urgent requirement to solve this issue - so please get to me fast. Thanks, Babu. R
Babu R- Chennai, Tamil Nadu, India.
2000
A. If the small skips appear only on the outer surface it is probably caused by "chrome mist". The chrome mist in the air comes from the conditioner or from the decorative chromium solution. The mist is in the air and when it comes in contact with the parts that come out of the palladium bath, it causes a small dot. The brownish colour of the palladium disappears as a result of the chrome in the air and this dot cannot be plated with electroless nickel.
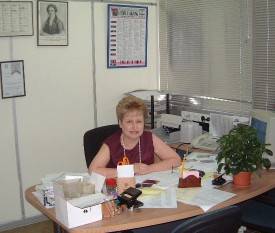

Sara Michaeli
Tel-Aviv-Yafo, Israel
2000
A. Dear Mr Babu,
A dot - skip plating has to be seen or explained more fully in order to pin point the source. You have to be able to determine it this is a pitting problem or skip plating.
From what I have heard, your spec calls for a high thickness of Copper and also a high thickness of Nickel plating , both processes which are pit prone.
In addition to Chrome mist, also look out for HCl mist, and ensure perfect degreasing before the Chrome etch right at the very beginning, because if an Air bubble sticks on to the plastic on account of Oil on the component surface or in the etch bath. regards,
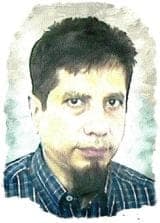
Khozem Vahaanwala
Saify Ind

Bengaluru, Karnataka, India
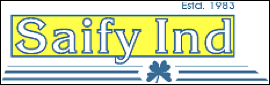
2000
2000
Q. Hello,
Got your feedback - thanks for the information. I need to check it out with my Platers and awaiting their response. But couple of queries...
- Will the Decorative Chrome batch generate the Chrome mist? And which conditioner you refer to? Can this be avoided or reduced to maximum extent?
- How to control the Chrome mist - would separators work (screening the Pd bath from the rest or screening the Chrome bath from the rest)?
- Or could you suggest some absorbent or adsorbent agent for the chrome mist?
- Have you encountered this problem and what means you took to solve this?
Thanks for your prompt response and looking forward to more information ASAP.
Babu. R [returning]- Chennai, Tamil Nadu, India.
? Are you saying that when the problem occurs on a jig, almost all the parts on the jig are bad, and other jigs come out without the problem?
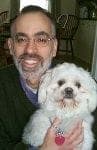

Tom Pullizzi
Falls Township, Pennsylvania
2000
2000
A. Conditioner is the chromic acid plus sulfuric acid solution. How to avoid chrome mist, well you can use in the decorative and in the conditioner a wetter that creates a foam layer. Ask your suppliers for it. It has to be a special wetter that is not decomposed by the strong oxidizing power of the chromic acid. To begin with you can even use polypropylene balls but they are not effective enough. ...also close the windows as the wind will increase the effect of the chrome mist.
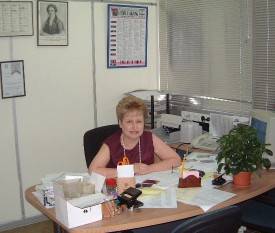

Sara Michaeli
Tel-Aviv-Yafo, Israel
by American Society for Electroplated Plastics
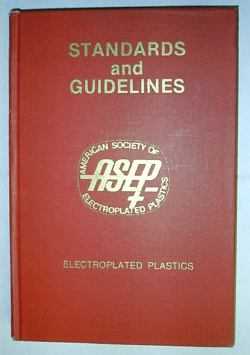
on eBay or Amazon
or AbeBooks
(affil link)
Q. Dear Mr. Pullizzi,
From the observation, I cannot attribute to jigging because some components do come out well. It happens on all the jigs being processed and not concentrated on one jig.
I have been suggested to check out for 'Chrome mist' or some other mist particles which affect the part before the E-Ni. Could it be that bubbles settling on part during these stages leads to spots not getting activated? Thanks, Babu. R
Mr. Vahanwala,
Thanks for your response. Will be looking into it. We have been clear that it is 'skip' plating because the virgin plastic skin is visible on this area (dots of max 2 mm).
Felt that air bubbles may not be an issue as the chrome etch tank is constantly agitated and air bubbles get removed. Thanks, Babu.
Babu. R [returning]- Chennai, Tamil Nadu, India.
2000
A. The etching solution is agitated and the air bubbles get removed as you mention but each bubble takes a little chromium into the air... think about it. Other things that may cause skips are: Too high Chrome plus 3 in the conditioner (over 30 g/l); too low pH in the EN; Not enough time in the accelerator (or too weak accelerator); Too short dipping time in rinses (mainly after Pd and after accelerator).
But none of these can explain why your skips are only in the outside and not in the inside of the parts. The only strong explanation to the one sided skips is the chrome mist.
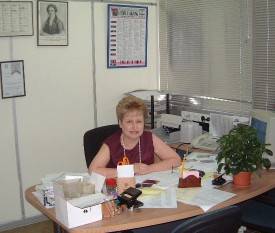

Sara Michaeli
Tel-Aviv-Yafo, Israel
A. Babu
My first thoughts are that you are getting chrome mist blowing off your etch tank or bright chrome tank onto the surface of the work after the neutralizer tank.Could there be any cross drafts from open doors etc that could blow the mists in that direction. (you may be able to check this by setting up a sheet of white paper, leaving it there for the day and checking for orange chromic spots). Secondly, do you have mechanical agitation in the activator, accelerator and electroless tanks? If there are any concerns about bubbles forming on the surface of the product causing skip, mechanical agitation will shake the loose. Is there any chance that oil form the likes of a compressed air supply could be sprayed onto the work, this could cause skip. Finally in the moulding process are the molders using any silicone based mould release agents, not necessarily on the machine that is manufacturing your components but maybe somewhere in the process they are getting overspray form another machine. (silicone mould releases are a not to be used for products to be electroplated. I hope this is of some help. Whatever is causing the problem is either already on the product or is happening between the start of the line and the electroless tank. Regards Tim
- New Zealand
2000
A. Dear Mr. Babu:
All the suggestions that you have received are very nice.
I support the chrome-mist theory the most. Actually we are running an ABS plating plant in Delhi itself, so we keep on facing this thing very often. Well this problem may arise due to improper strength of activator also.
Well Mr. Babu have you ever tried to redo the electroless process on the defected pieces? I mean dip the pieces in the accelerator(HCl)again and leave the jig for 5 minutes and then dip that jig into the activator and redo the process of electroplating. I hope that the skip plating holes would get ok this time.. do tell me about this thing as earliest.
Thanx and regards,
Sandeep Jain- Delhi, India
2001
Multiple threads merged: please forgive chronology errors and repetition 🙂
Problem in ABS Plating: "Dot-skip" plating
2001
Q. Dear sir,
We have started an ABS plating plant (Nickel, gold & chrome plating) one year back. Since we are new we are facing lots of problems with etching, Pd, and electroless nickel. We are plating onto writing instruments.
Problems such as :
1) Lots of dot skips.
2) If forcefully electroless nickel with excess chemicals lots of problems from copper.
3) Kindly let us know timing factor in etching tank since we cannot fix the same and face various types of finish from electroless nickel tank. ( Our temperature is maintained 48 °C). Chromic 350 - 450, sulfuric Acid 250 -300, Trivalent 22 at present. At the time of process the temperature is maintained at 70 °C and timing to the job is approx. 20 minutes. Any suggestion if required.
4) Our electroless nickel bath decomposes every day or two. (Any kind of stabilizer available to avoid the same?).
Materials used in electroless nickel are :
* Mixture of Nickel Sulphate (3 kgs) & Sodium Succinate (250 gms) plus 11 ltr of water which we call as A.
* Mixture of Sodium Hypophosphite (3.5 kgs) & Sodium Citrate (1.5 kgs) plus 11 ltr of water which we call as B.
* Lacquer ammonia ⇦ on eBay or Amazon [affil link] Acid.
* As far as required temperature in the bath, it is around 40 °C. We are not using sulfuric Acid. We heat with the help of a heater water to water i.e. tank filled with water is heated & our EN tank is placed into water that is heated.
* Since our electroless nickel bath decomposes every day or two we prepare a quantity of bath (approx. 10 ltr water, 2 ltrs of A, 1 ltr of B & 1 ltr of liq. ammonia as and when required we keep on adding proportionally til decomposes. Kindly give suggestion for the bath if needed.
5) To remove plating from rejected goods is a headache. We use nitric acid; suggest if any other process can be for the same.
Awaiting for an early reply. We appreciate your efforts towards trouble shooting looking forward to you web.
Thanks.
Mr. Sunil JhaveriPLATERS - Mumbai, Maharashtra, India
A. Mr. Jahveri:
Could not understand all your questions completely, but it sounds as if you are trying to develop your own Plating On Plastic (POP) process. This has taken years and millions of dollars to chemical suppliers around the world. Why don't you approach a well recognized Co. I will only answer to question 4: Thiourea ⇦ on eBay or Amazon [affil link] is a known stabilizer of EN, it is also a poison and can kill reaction.
Guillermo MarrufoMonterrey, NL, Mexico
2001
2001
A. Plating on ABS is a complicated and delicate process and one should try to purchase the electroless solution from a supply house that can provide you with the right answers. Anyhow I will try to assist you:
1. Adhesion problems in POP processes are connected to the conditioner and skips are connected to the EN.
2. Your formula of the EN is not a balanced one, try to find a better formula in the Metal Finishing Guidebook. A balanced EN solution can work for months without decomposing.
3. The EN should operate at about 35 °C and the pH should be about 9-9.2.
4. If the EN is OK parts should be covered in about 20-30 seconds.
5. Rinses, they are very important. Prior to EN the parts should be in water for at least 60 sec.
6. Last but not least, the accelerator between the palladium and the EN should be at the right concentration and changed once a week.
Let me know how are you getting on.
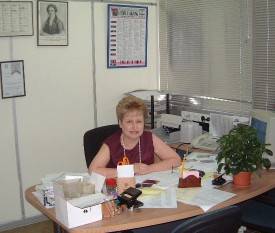

Sara Michaeli
Tel-Aviv-Yafo, Israel
A. Dear Mr. Jhaveri,
As has been mentioned by many experts the ABS plating is a tricky process and you must approach reputed companies like Atotech, Enthone, etc. for the complete solutions to your problems. Until and unless complete process audit is done at your works it would be very difficult to suggest any single remedy.
Thanks,
G.S._SHARMA- MUMBAI, India
Multiple threads merged: please forgive chronology errors and repetition 🙂
2007
Q. We are in the process of development of badges; wherein we are facing skip plating problem
as below.
Part Application:Automotive (Exterior)
Base Material:ABS-EP 200 Natural
Part Dim.:l=245 ,w=25mm T= 6 mm
Plating layers:Cu=18micron Ni=20 micron , Cr=0.18 micron
Part Geometry: Lettering "Di TURBO" letter badges wherein plate =2 mm ,letter height=10 mm
------------------------------------------------------------
DI TURBO
------------------------------------------------------------
Skip Area observed:
at inside corners of letter "D" ,"B","R" predominantly.
Can you please clarify my following doubts
1)Is it because of process parameters, methods
2)Is it because of product design
3)Is it because of viscosity of Electroless nickel
4)Is it because of part loading direction
I request you all to kindly give your remarks & suggest us solution.
With Warm Regards,
Product Development Engineer - Pune, MS, INDIA
A. Skip plating of ABS can be due to many factors, including poor moulding, poor etching, poor rinsing, poor activation or poor electroless bath control. If the moulding is not done correctly, the surface can be depleted of butadiene and this will result in an inability to etch the surface and subsequent loss of plating nucleation sites. Similarly, if the surface is not adequately etched by the chromic acid, it will not plate. Even if the surface is etched properly but it is not rinsed properly, the chromic acid will kill any further processing, so good neutralisation and rinsing is essential. Once etched, the surface needs activating and if the palladium/tin is not working properly, no electroless metal deposition will take place. If the electroless bath is not in spec, you haven't got a remote chance of getting it to plate. From the brief description you have given I would suggest you are possibly suffering from inadequate rinsing, but the other possibilities above are still valid.
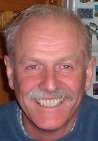
Trevor Crichton
R&D practical scientist
Chesham, Bucks, UK
2007
2007
A. Hmmm...all kinds of reasons are possible.
But because you gave a good description of the problem area I think the most likely explanation can be found in the distribution of butadiene in the SAN matrix (styrene acrylo nitril). It are the butadiene spheres which get etched out leaving cavities behind for activation and adhesion of the metal layer.
Your metallisation process works well on other areas of the letters.
Maybe you should try a few tests with different molding conditions...less pressure, less hot plastic.
No, personally I would not make any changes in the metallization parameters...not my first choice to seek the answer in the plating...it works on other areas of the letters you plate.
Have fun.
Warmly,
- Venlo, the Netherlands
A. You probably have a "scum" on the top of your etch solution. When you introduce the racks, it holds the scum in the "pockets" as it enters. (I bet this is the case.)
Either move your solution better, or program the equipment to go up and down as introduced to the etch.
Regards,
Warren, Michigan, USA
2007
Multiple threads merged: please forgive chronology errors and repetition 🙂
Q. We are facing problems of skip plating on our abs plastic components. the process is soak degrease - rinse - etching (chromic & sulfuric) - neutralise - activator (tin & palladium) - acceleration (HCl) - electroless nickel (nickel sulphate & sodium hypophosphite). But all of the parts are not covered with nickel. we want to know how to prevent this skip plating?
thanks in advance
regards,
process operator - Jeddah., Saudi Arabia
2007
2007
A. Dear Sir,
Skip plating is due to
1-degreasing is not perfect
2-reduction of chromium after Etching is not sufficient
3-activation time is not adequate or solution is out of balance
4-acceleration [time and solution]is not suitable use NaOH instead of HCl
Good luck,
plastics Electroplating - Cairo, Egypt
Multiple threads merged: please forgive chronology errors and repetition 🙂
Q. Respected Sir,
We are in POP for the last 6 months and plating jobs for MNCs. we also face the same problem of skip plating. as Mr Jain has suggested, we redo the process from activator and 40% time the job is good. Extra dosings in HCl neutralizer after etching, activator, EN plating has helped reduce this problem.
But I am also lost as to why this problem can occur. Chrome mist if it is a problem can be provided with forced ducting (venting) of etching / decorative chrome arrest this problem.
Be kind enough to help us out of this ASAP.thanks.
- PONDA- GOA, INDIA
January 2, 2010
Q. DEAR Mr. BABU,
I TRIED FORCED VENTILATION ON CHROME ETCHING SOLUTION, PLUS I TRIED TO ISOLATE THIS BY PUTTING A PARTITION. FURTHER MY COPPER TANK WAS CLOSE BY THE ACTIVATION TANK; THIS AREA WAS ALSO FORCED VENTILATED AND YOU KNOW WHAT, 90% OF MY SKIP PLATING PROBLEM GOT SOLVED.
BUT BECAUSE OF THIS FORCED VENTILATION MY CONSUMPTION OF ENP CHEMICALS, ammonia HAVE SHOT UP. WE ARE STILL WORKING OUT THE EXACT DOSING PATTERNS.
THANKS TO ALL FOR RESPONDING TO THIS PROBLEM.
- PONDA- GOA, INDIA
January 7, 2010
Multiple threads merged: please forgive chronology errors and repetition 🙂
May 17, 2011
Q. Hi there,
My name is Krisztian and I am working for a plastic plater company.We have been having a pretreatment problem for a week that could not be solved so far.
Our pretreatment is the following:
-Degreasing
-Etching
-Chrome reductor
-Pre-dip
-Activator
-Accelerator
-Electroless Ni
-Pre Ni (Watt's Ni)
So we can see open sharp edged dark grey spots on surface after Pre Ni.First we thought we had a problem between electroless Ni and pre Ni (maybe chrome aerosol)that made the surface passive before pre Ni but after cross section it turned out we had no covering in those spots at all.So if anyone could have a look on the photos and tell me an idea how to get rid off them, that would be a great help.
Thanks a 1.000.000.
Plating shop assistant - Jaszbereny, Hungary
May 23, 2011
A. Well, there are a lot of possibilities here.
When you say that there is no coverage, do you mean that there is no electroless nickel?
Chrome aerosol can cause this kind of skip plating. By skip I mean that there are spots with no plating at all.
I assume that you use a suitable wetting agent in the etcher to prevent aerosol problems. You can check whether you have aerosol problem by using big filter papers dipped in diphenyl carbazide solution. If you put a paper close to the EN solution and you get purple spots on it, it means that you have chrome in the air.
BUT, there are a lot of other possibilities :
How much trivalent chrome do you have in the etcher?
The rinse time prior to the EN should not be just a short dip. This rinse must rinse of SN+4.
And the most important -the quality of the water you use. The water for ALL stages, including rinses should be RO.
A viszontlatasra
Sara
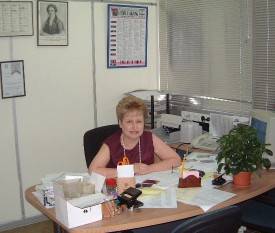

Sara Michaeli
Tel-Aviv-Yafo, Israel
June 2, 2011
Q. Hi Sara,
many thanks for responding on my topic. Yep I meant there is no EN layer on it. We do use wetting agent for etching. We have already done carbazide indicator test and have chrome mist in the air.
-Trivalent chrome should not be so high as we have been having it for a bit more than two months./but not checked/
-Rinses before EN we have three cascades, with a dipping time of 30,15,15 sec.
We have no RO water rinses.
So I checked other issues and find a similar one.
Mr Babu from India came up with the same defect. I had read many interesting responses, suggestions after.
-So what do you think is it possible that we get aerosol on surface when jigs coming out of activator and that makes dot skip plating?
I found a trouble shooting list for activator made by Mr. Lai Kok Wai from China, and it says it is a chrome mist defect /dot skip/ when you having it on areas of parts facing up typically.
-Some people offers kind of Chrome mist suppressant and forced ventilation at chrome etch.
What is your opinion on that?
There is a letter for Mr Babu's issue by Mr Sandeep Jain from India who recommends him to redo the process with defected parts, first in accelerator than activator and keep going with the process till it is fixed.
Can it be working?
Please answer if you read that.
Minden jot :)))
- Jaszbereny, Hungary
June 14, 2011
A. Hi,
1. If you have a positive carbazide test, it means that the wetter you are using in the etch is not doing a good job. It is either an non adequate wetter or the amount is too low.
2. Trivalent chrome - I understand that this is a new solution. Trivalent in high quantities causes problems but if it is zero, it is a problem as well. You need a minimum of 3-5 g/l trivalent chrome in the etcher. Chromic acid concentration should be 420 g/l and sulfuric 170 cc/l = 313 g/l.
3. I don't know how big are your parts and what is the volume of your solutions. In order to evaluate whether the cause is a result of chrome mist, I would try to etch parts in the plating line,(only the etch, not the following rinses) and perform the post etch sequence in another room on lab scale, in small scale of course. This way you can eliminate the chrome mist and see whether your problem is solved.It is imperative to eliminate the chrome mist on lab or small scale in order to be sure that this is the root cause.
4. Water - you wrote that you have no RO water. I hope that all water used is DI including make up of ALL solutions and ALL rinses.
5. Facing up areas - Your remark regarding facing up areas is mostly correct. Is your problem mainly on facing up areas?
6. Mist suppressant is a wetter.
7. Forced ventilation is a must - first of all to ensure safe working area for the employees.
8. Are you sure you etch the parts properly? The ABS has a kind of glassier which make parts look bright. After the etching and rinsing, parts should look MAT or DULL.
9. Initiation - how long does it take (in seconds) since the parts are immersed in the EN till the reaction starts?
10. Last but not least - the molding. If the molding is not perfect, you will have spots. Are you familiar with the acetic acid
⇦ on
eBay
or
Amazon [affil link] test to evaluate the quality of the ABS?
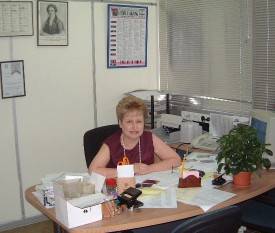

Sara Michaeli
Tel-Aviv-Yafo, Israel
Multiple threads merged: please forgive chronology errors and repetition 🙂
Q. Hi,
I'm a process engineer for a new plating on plastics plant. We plate ABS parts of Copper-nickel-chrome process for Automotive industry. Currently, we are facing a problem with our plated parts. A defect called "White Dot" layer occurred after parts finished plated. We had done everything but still the defect can't resolve.
Please help.
Thanks.
Hun
plating shop engineer - Malaysia
October 6, 2011
October 7, 2011
A. Hi Hun,
If the "White Dot" didn't show up after nickel plating but appear after chrome plating, then possible causes are:
1. High chrome bath pH;
2. Low wetting agent;
3. Low chrome complexing agent;
4. Low chrome concentration;
5. Lead contamination;
6. Poor activation after nickel plating or parts dries prior to chrome plating.
Regards,
David
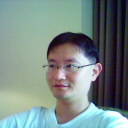
David Shiu
- Singapore
Coating the surface of the point opening on ABS plating
Q. Hi;
I have an important problem in ABS plating process. We are dealing with this problem for a long time: a large opening in the coating surface is observed, looks like a big bubble but we think no palladium is there.
For this reason we tried a lot of methods -- we made a new activation bath, chromium sulfuric bath, acceleration bath , electroless nickel bath ... but we were unable to reach a conclusion. We don't know where does it get this error. We do not have much ideas anymore. Thank you in advance for your help.
hasan ibekchemist - Izmir, Turkey
December 29, 2015
Q. We have an specific problem that we can not find a solution for the moment.
In all the pieces with letters or logos in relief, randomly appear points up to 2 mm in diameter without chrome in the vertices, both in the interiors and in the exterior of the letters. These vertices do not form sharp edges, but ratios have been made according to the correct constructive rules of the mold.
I hope you have understood me well.
Can someone suggest a solution?
- San Martin, Buenos Aires, Argentina
March 7, 2018
----
Ed. note: I think a picture would be worth a thousand words, Andres.
![]() |
Q. Dear sir, I'm working in automotive company going on 3 months. I'm dealing with a problem called "warpage after plating". - Pune, India May 9, 2018 May 2018 A. Hi Mohit. Do you have any reason to suspect that it the jigs rather than improper operation of the plating process or improper design of the ABS parts which is the chief problem? For example, have you plated these same parts without warpage previously? Have other shops successfully plated them? Thanks. Regards, ![]() Ted Mooney, P.E. RET Striving to live Aloha (Ted can offer longterm or instant help) finishing.com - Pine Beach, New Jersey |
Q, A, or Comment on THIS thread -or- Start a NEW Thread