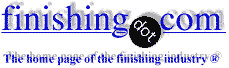
-----
Finished color for MIL-A-8625 Type III anodize on 7075-T6
Q. Extreme discoloration of 7075-T6, Type III, C1 Hard Anodize from new supplier
Hello ... Mechanical Engineer here investigating Quality rejections of a new Aerospace Vendor. New parts have come in a very light pale & creamy grey color.
The machine shop material certs are 7075-T651, but the familiar dark bronze color is now a light marbled mess. The plating vendors shows a hot deionization water seal for 15-20 minutes on the process router which we did not specify on the Engineering drawing or PO. Would like to use them if the discoloration can be explained without impacting abrasion resistance. A simple file test appears to be equal between the old and new. Any help appreciated to understand what I have in hand.
Scott Toews- Wichita, Kansas
October 12, 2021
for Shops, Specifiers & Engineers
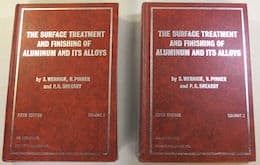
avail from eBay, AbeBooks, or Amazon
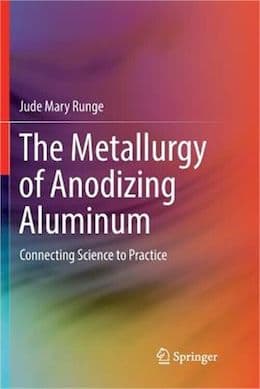
avail from eBay, AbeBooks, or Amazon
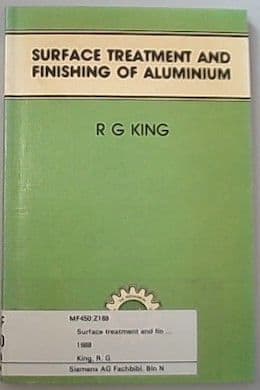
avail from eBay, AbeBooks, or Amazon
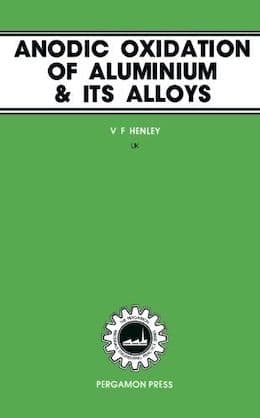
avail from eBay, AbeBooks, or Amazon
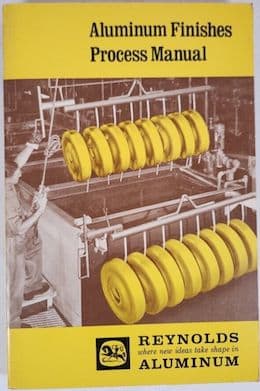
avail from eBay or Amazon
(as an Amazon Associate & eBay Partner, we earn from qualifying purchases)
A. Hi Scott. Hopefully experienced anodizers will chime in with what they have found to be a usual range of color, but the first thing I would do is check the anodizing thickness on both parts.
Luck & Regards,
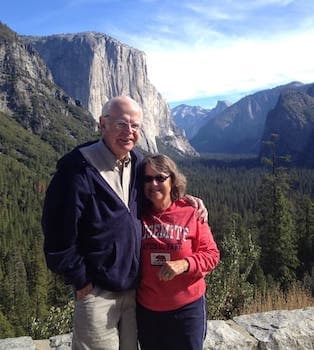
Ted Mooney, P.E. RET
Striving to live Aloha
(Ted can offer longterm or instant help)
finishing.com - Pine Beach, New Jersey
A. Scott,
The top two pics look to be in the typical color range for 7075 material. There may be lighting issues with the two bottom pics but the one on the left could resemble the charcoal brown color of 6061. The one on the right really looks as though it may have been dyed black but again, it may all be related to the lighting in the pics. i would also contribute that the parts having been treated with a hot de-ionized water dip; depending on the duration and the temp may have lost a little with regard to the hardness/abrasion properties that hard coated parts would normally provide.
supervisor - Cicero, Illinois
Saporito Finishing Co.

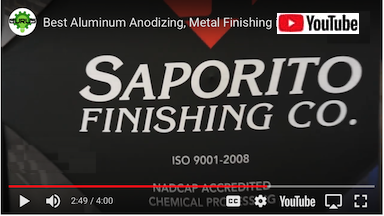
A. Sealing of hard coat converts the aluminum oxide to hydrated aluminum oxide which is softer, hence reducing the abrasion resistance.
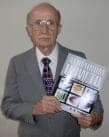
Robert H Probert
Robert H Probert Technical Services

Garner, North Carolina
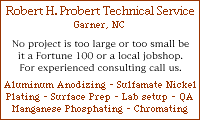
A. Scott
The new supplier's parts look characteristic of 3-4 mil thick anodize from a conventional hard anodize operation. As mentioned, consider having the thickness verified.
I agree with Phillip that your original supplier's parts appear to be dyed black.
With respect to the hot water immersion / seal, MIL-A-8625 / MIL-PRF-8625
[⇦ this spec on DLA] requires hard anodize to be rinsed in cold water and dried.
- Green Mountain Falls, Colorado
A. The parts supplied by the legacy provider appear to be either sixty series alloy or black dyed. The new supplier's parts look more like hardcoat on seventy series alloy. However, sealing of type III hardcoat is only permitted if called out on the PO or drawing. Sealing results in lighter appearing coatings on seventy series. Coating thickness and/or electrolyte temperature could also explain some of the color difference from the new supplier.
Chris Jurey, Past-President IHAALuke Engineering & Mfg. Co. Inc.

Wadsworth, Ohio
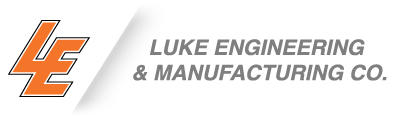
Chris... Thanks for the reply. There was a 3rd comparison part from our legacy supplier that is 6061-T6.
As you can see by my new pictures the 6061 does indeed turn out more towards the black shade. None of these parts are dyed.
Scott Toews [returning]Mechanical Engineer - Wichita, Kansas
October 20, 2021
A. It has been my experience with 6061, 6082 and 7075, that none of them turn completely jet black when hard anodized (I had achieved max 70 micron thickness), 6082 would be the darkest of them all, dark brown, but certainly not jet black like in the picture
I suspect that your legacy vendors were dyeing those parts to avoid color variation and possible rejection, this way they always supply black part regardless of how that particular batch of 7075 came out of the mill.
Standard for Type III as far as I remember allows for color variation, but QC people may follow their own beliefs regardless, even if you try to wave the printed out standard in front of them ... and perhaps that has led to the legacy vendor choosing to dye the parts (I'm 99,99999% convinced they are dyed, judging from the photos).
- Riga, Latvia
A. Hi Scott,
Please have your supplier provide 2 4x4" test coupons ~.042" with a quarter inch center hole, run documented on a parts load, to send for abrasion testing to confirm they are meeting requirements. If your supplier agreement includes right of access to documentation, you may ask for relevant recent test reports. If the P.O. calls out abrasion resistance, and they can hit it, they have fulfilled the P.O.
I have lots of conversations with customers about spec requirements vs aesthetics... That being said, I would bet my weekly coffee money that they aren't meeting spec running 7xxx hardcoat through a HWS.
I would also bet that your previous supplier was giving you some dyed parts. I'd like to see Taber test results from them, as well! Yikes. Taber abrasion on Type III Cl2 is so unusual that my Nadcap shop has never been asked to do it in 20 years, because... it's not normally a Thing. Corrosion? Sure! Every month, baybeee! Abrasion? Scuse me, WHY? That will be a fun chat between their QM and your purchaser. Get your oldest grumpiest engineer in on that call.
My big advice here is to lay down the law in your purchase orders. If you have to spell out, "parts shall be capable of passing [test] and test reports shall be provided upon shipment", it is totally within your authority as the paying customer to do so. It will come with a cost, which you will include in your evaluation of the quote. If you add, "parts shall pass test and conform to a visual standard ", provide a specimen and work with your supplier to see if they can match it and meet spec.
I hope this helps... I think you have gotten two funky deals back to back, and it's complicating your approach.
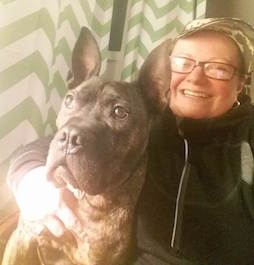
Rachel Mackintosh
lab rat - Greenfield, Vermont
A. Abrasion resistance and color are functions of anodizing temp, concentration and current density. Almost every shop has a different result. The darker color was probably lower temp and or lower concentration and or higher current density and certainly has better abrasion resistance. One additive vendor touts hard coat at 70 °F, but the colder the harder. Max abrasion resistance is at 32 °F, but I have one client who does hard coat at 20 °F on cylinder heads.
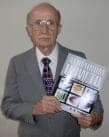
Robert H Probert
Robert H Probert Technical Services

Garner, North Carolina
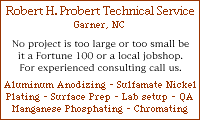
December 28, 2021
⇩ Related postings, oldest first ⇩
Q. We have been having a problem with hardcoat anodizing of 7075-T651 aluminum. We're specifying type III hardcoat, clear/undyed. I know the vendor has been sealing our parts but I'm not sure by which method. Our print does not specify.
The problem we're having is blotchy color. Our parts used to be greenish/gold that is common with hardcoated parts. At some point we asked the vendor to make the coating thicker, from 2 mils to 3 mils total. (We grind our parts flat after anodizing and were breaking through at 2 mils.) The color of the parts changed to light gray with the thicker coating.
Our most recent batch of parts came out gray, as usual. They were gray after grinding. At some point after we shipped the product they became mottled with the grey/gold finish in places. Rubbing them with isopropyl alcohol seems to worsen the effect. We ship our products with a plastic wrapper. Could there be some interaction? The surface appears to be sealed in both the gray and green/gold areas (marker comes off easily). The vendor looked at the parts and had no explanation. Also, he said the coating was up to 4 mils.
Cosmetics of our products are critical to us. Any ideas on what is going on and how to get consistent coloration?
Thank you.
- Minneapolis, Minnesota
1999
A. Dear Jon,
It sounds to me like your grinding process may be removing the seal provided by your finisher. The hot aqueous sealing process on anodized aluminum works by converting the small aluminum oxides at the surface to a much larger hydrated aluminum molecule. This
"swelling" of the surface molecules effectively closes the porosity resulting in a seal.
If you remove the surface molecules, you remove the seal leaving the porosity open to take-up contaminants. Thus the appearance of the finish will continue to change over time.
You might try one of the impregnation processes. These seal the entire depth of the pore with an organic. Loctite comes to mind.
- North Dakota
A. Hardcoat anodize is not normally sealed, as this reduces its wear resistance. However, 7075 alloy results in a coating which is highly absorptive. It actually feels sticky as it pulls water and oils from your hands. Thicker hardcoatings increase this effect. You could be absorbing oils from your grinding and/or packaging. A good seal eliminates this problem. Thicker coatings require longer seal times. The MIL-Spec states Type III hardcoatings shall not be sealed unless specified. Your hardcoater should not be sealing without your knowledge and approval. So as to not violate the spec, he may be "drying" the parts in hot water to help with your spotting problem. This is not the same as a full sealing process.
Chris Jurey, Past-President IHAALuke Engineering & Mfg. Co. Inc.

Wadsworth, Ohio
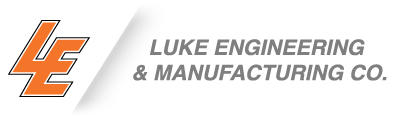
A. I wasn't going to comment on this because Chris gave some very appropriate comments. For sure, if you are working to a normal hardcoat spec., the coating should not be sealed. I could add to his comments that in going from a 2-mil to 3-mil coating you have made the anodizer's job much harder in delivering uniform coatings. Beyond 2 mils the anodizing voltage climbs very rapidly and climbs to much higher voltages than going from 0 to 2 mils, making racking more critical, and making it more difficult to maintain the tank temperature and part temperature, hence more difficult to deliver a good hard, uniform coating and subsequent uniform color. But the major comment I wanted to make is, have you ever considered grinding your parts flat BEFORE anodize? As you have found, I'm sure, hardcoat is a very hard, very wear-resistant coating ("file-hard" is a commonly used term) and very difficult to grind down. (That is usually why aluminum is hardcoated in the first place.) Aluminum is often selected as the metal of choice because it is a soft metal and relatively easy to machine. If at all possible, at least do the majority of grinding on the bare metal. I have heard of lapping or honing hardcoat to improve the RMS finish or to get an exact thickness, but grinding through 2 mils of hardcoat must wear out a lot of grinding tools.
Phil Johnson
- Madison Heights, Michigan
Thank you all for your comments. I not mentioned that we grind our part flat before hardcoat anodizing and the remaining grinding is a touchup to maintain our flatness spec.
The problem isn't 100% solved yet, but we're making successful parts. The long-term plan is to use a black coloration. The marketing guys haven't yet blessed the new look. In the meantime, we determined that the blotchy grey/green or all grey parts had a much thicker hardcoat layer than we specified. The vendor is controlling thickness more carefully so we have enough thickness to grind flat without breaking through the hardcoat yet not so thick that the hardcoat transitions to the grey color.
Thanks for the help.
Minneapolis, Minnesota
Anodizing 7075 to achieve a natural grey color
Q. I am the General Manager of an anodizing facility in N.W. FL and I would like to know if anyone has any information on anodizing 7075 Aluminum in a sulfuric bath, Type II, Class 1, and the color of the part is grey. If so, I would very much like to learn what could cause this, because each time I anodize 7075 it is a shade of gold. I look forward to some insight to issue.
Lamar Jacksonanodizing shop. - Fort Walton Beach, Florida
2000
A. Hi Lamar,
Interesting thought, I'm in the same situation as you, I have yet to see a 7075 material turn any shade but bronze or gold. Do you have a copy of The Surface Treatment and Finishing of Aluminum and Its Alloys by S. Wernick, R. Pinner, P.G. Sheasby? There might very well be something in there. Off the top of my head the things that would make a difference would be
- 1. Acid concentration 5-10-15-20% solutions make a huge difference in the tones achievable on a finish.
- 2. Temperature - It makes a huge difference in hardcoat anodizing (not to mention its physical properties that it holds).
- 3. Obviously additives and whatnot can also affect the coloration of a finish (oxalic acids, or anodizing additives will change colorations dependent upon their quality)
- 4. Thickness - With 7075, the thicker you anodize, the darker the tones, possibility that they are only putting a few .0001's on it?
- 5. What about the finish the part has, sand/bead blasted, polished, brushed, time-save finished, etc.
There are really IMO an infinite number of possibilities as to why it may occur that way.
Matthew Stiltnerplating company - Toledo, Ohio
Q. What's the color of 7075-T6 Al anodization per MIL-A-8625 TYPE III Class 1?
Gong KearnyProduction Engineer - Shanghai ,China
March 16, 2008
A. Type III will be a light to dark gray.
James Watts- Navarre, Florida
Thank you so much.
According to your opinion, I made several experiments, and the result is below:
the cosmetic appearance is light yellow when coating thickness is less than 80 µm, but gray when more than 120 um
Production Engineer - Shanghai ,China
Multiple threads merged: please forgive chronology errors and repetition 🙂
Q. My company manufactures a light business jet aircraft. We have some baggage compartment tiedown fittings made by a supplier from 7075-T651 aluminum. Our drawing specifies anodize per MIL-A-8625F Type III, class 2, dyed to a specific color chip per Fed Std 595. The color is supposed to be a medium-dark grey (Fed Std 595 #36118). A shipment of parts we just received included certification documents from the anodizer that states they complied with our drawing requirements. However the parts are black in color rather than the gray (way darker than the specified paint chip). My research indicates the normal undyed color will vary based on the type of alloy. I'm wondering if we are asking the anodizer to produce a lighter color that is impossible for him to achieve. If the undyed parts would normally come out black, is it indeed possible to dye the parts a lighter, gray color?
Craig ColemanQuality Engineer - San Antonio, Texas, USA
May 5, 2010
A. The color before dyeing is a function of alloy, heat treat, free acid concentration, dissolved aluminum, current density, temperature, and thickness (which was not mentioned). In most cases it is dark gray right out of the anodizing tank without dye. Type III, hardcoat, is not normally dyed ANY color, because the pore is too small to adsorb the dye; however, many shops get around this problem with varying temperature and other parameters. Your color CAN be matched, but it is not a first day thing, it is a Research and Development project. NO, you cannot dye it gray and make it lighter color.
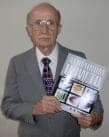
Robert H Probert
Robert H Probert Technical Services

Garner, North Carolina
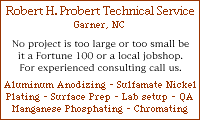
A. Yes, you are correct. The Mil-Spec default is .002" as specified. The alloy will be a near black at that thickness and cannot be dyed a lighter color. 7000 series is a greenish color at thinner thicknesses, if you want a grey color resulting from the Hard Anodize process a 6000 series might be advised.
Bill GraysonMetal Finishing - San Jose, California, USA
Q. We currently anodize some items made of 7075 aluminium alloy. The last batch came out with a different visual aspect: anodization is complete and uniform but something is wrong according to visual inspection, since brightness and color is slightly different from usual.
Composition and microstructure of the material prove to be compliant. What may we check to try and solve the problem?
Thanks
R&D - Carpi, Italy
October 19, 2010
Q. Hi there, we are doing natural anodizing on machined aluminium (7075) extruded shafts.
The problem is that on the same jig there is about 4 shafts, and after anodizing 3 of the shafts are perfect, like 7075 would anodize, and 1 of them is different (blue in color)
We have tested it with a multimeter, and it is anodized, but we think it's just not as thick.
We are using sulfuric acid to do our anodizing.
Our seal tanks are filled with R.O. water.
It is the first time in 20 years that we are getting this problem.
Your answers would be appreciated
- Potchefstroom, North West, South Africa
March 13, 2014
A. Hi Jan. Yes, I believe you have properly analyzed your problem and that it is a very thin anodized layer due to poor contact of that piece on that jig. If the contact is fixed, I think it will go away.
You may have seen color anodizing of titanium, or you may have titanium jigs that discolor in your anodizing process. That kind of discoloration has nothing to do with contaminating ingredients, but is iridescence from the light bouncing off the top of the very thin anodizing layer "interfering" with the light bouncing off the bottom, and canceling certain wavelengths. When you see a "blue" anodized layer on your parts, I suspect it's probably the same phenomena of a very thin anodized layer.
I suspect that the reason the earlier posters see gold anodizing of 7075 is that their voltage is high enough to anodize other alloys, but not enough to build an anodized layer on 7075 of proper thickness. Now the people who have actual experience anodizing 7075 can point out the silliness of my suspicion :-)
Regards,
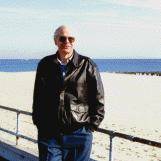
Ted Mooney, P.E.
Striving to live Aloha
(Ted can offer longterm or instant help)
finishing.com - Pine Beach, New Jersey
Q. Thank you for your answer.
I'd like to know, most of the people I have spoken to tell me it is a contact problem on my titanium jigs.
How or what is the best way to properly strip the jigs so I can get the best contact possible?
- Potchefstroom, North West, South Africa
A. Hi Jan. The BEST way to fix the problem is new rack tips because they may be thin, or have lost their spring, in addition to having acquired an insulating coating. Please see thread 52477, "Stripping of titanium oxide layer on aluminum anodizing jigs" and, if it does not answer your question, post a follow up there (so this thread doesn't wander too far from its title topic). Thanks.
Regards,
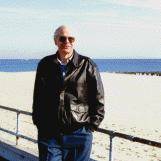
Ted Mooney, P.E.
Striving to live Aloha
(Ted can offer longterm or instant help)
finishing.com - Pine Beach, New Jersey
Q, A, or Comment on THIS thread -or- Start a NEW Thread