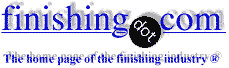
-----
Electro-polishing pipe bores

Q. Hello all - I am working on smoothing and polishing the inner wall of a tig-welded stainless steel tube, but I keep seeing these imperfections after electropolishing. They are not passivated and lead to rust later on. Any ideas what could cause this?
The process is:
- tig weld pieces together
- grind down inner weld with a flap wheel
- electropolish smoothed inner wall with a wand-type polisher (Walter brand)
I am unsure if the electropolishing is causing the imperfections alone, because the strip of marks are localized to the welded area. Any ideas & feedback are appreciated!
- Philadelphia, Pennsylvania
January 30, 2024
A. Hi Amy.
I am unfamiliar with wand-type electropolishing, so I can't help much, but it is well-known that attempting to electropolish at a current density which is too low will cause etching, so that is what I would expect to be the problem.
If your picture illustrates the full length of the component, it seems that tank electropolishing with an internal anode would be relatively easy and would give more consistent results.
Luck & Regards,
Ted Mooney, P.E. RET
Striving to live Aloha
finishing.com - Pine Beach, New Jersey
Q. Hi Ted, thank you for the feedback!
To expand on this, the marks are usually visible after the grinding step, before e-polishing. The e-polishing step just makes them worse.
So, if the mechanical grinding of the inner wall is causing the damage, do you think a passivation bath would be able to repair the passivation layer and fix the surface finish? I've read that too much thermal or mechanical damage can permanently damage the passivation layer...
- Philadelphia, Pennsylvania
A. Hi again,
My experience is in metal finishing rather than machining, but if the problem is apparent after grinding, I'm not understanding why that is considered acceptable. Isn't honing or another machining step available?
Electropolishing can remove tiny burrs & asperities but cannot (within my understanding) smooth out waves. The analogy I have always heard and found is that electropolishing can remove the clods in a plowed field, turning the field into ocean swells, but will not remove those swells.
I'm not understanding what is causing the verticality of the striated finish if it's not etching.
I don't know whether the logistics involved are workable, but I'd suggest sending a sample ground part to an electropolishing shop to see what happens when reliable and proven electropolishing is done on parts received from machining in this condition.
Good Luck,
Ted Mooney, P.E. RET
Striving to live Aloha
finishing.com - Pine Beach, New Jersey
⇩ Related postings, oldest first ⇩
Q. We are polishing small bore stainless tube which has been slotted. Can anyone advise on reasons for some defects we experience:
- General pitting defects on the inner and outer surface.
- A single deep pit on an otherwise perfect surface.
- A rippling effect on the inside of the tube.
- An orange peel effect on the outer surface.
Are these more likely to be caused by the raw material or the process parameters?
Thanks
Henry Lupton1998
A. Dear Henry:
Pitting problems are difficult to trace by remote control. The problem can be caused by any step in the operation, including the choice of the metal, the mechanical finishing, the cleaning and descaling, the physical electropolishing setup, and the condition of the electrolyte. We do trouble-shooting of electropolishing problems by a process of elimination, not by speculation.
Ed BayhaMetal Coating Process Corporation - Charlotte, North Carolina
--
by Larry Durney
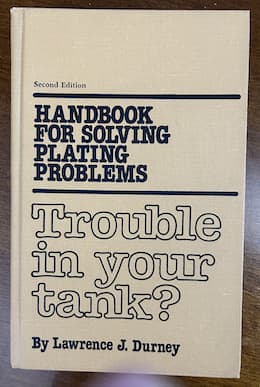
on eBay or Amazon
or AbeBooks
(affil link)
A. Ed: Yes it is difficult to troubleshoot a process from a distance, even with the parts sitting right in front of you, let alone from photos of the defects, let alone from a verbal description of the problem without even a photograph. Still, if we believe in process of elimination, there should be a suggested step 1
Henry: There are some good troubleshooting hints in the electropolishing chapter of the Electroplating Engineering Handbook ⇦ this on eBay, AbeBooks, or Amazon [affil links] , edited by Larry Durney. And his book, "Trouble in Your Tank" is the industry's definitive guide to methodical troubleshooting. Good luck.
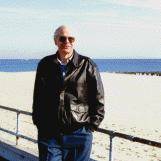
Ted Mooney, P.E.
Striving to live Aloha
finishing.com - Pine Beach, New Jersey
and Chemical Polishing
of Metals in
Research and Industry"
by W.J. Tegart
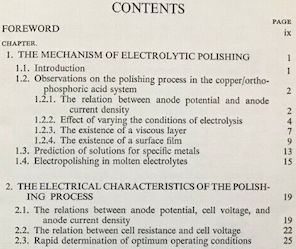
on eBay or Amazon
or AbeBooks
(affil link)
A. The problems you describe could be related to the method used to manufacture the tubing, the electropolishing process used, or a combination of the two.
Stuart Spars1999
A. Let me answer your questions one by one.
Please inform, is it a straight tube, welded or seamless. If seamless, has it been cold Drawn / Pilgered?
1. The Pitting is due to high current and the inclusions in the stainless Steel that has created Galvanic Cell.
2. I have to see the sample. Can't answer.
3. It can be if it is a Pilgered Tube where the reduction of OD and wall thickness is of different factor. We call it 'Q' Factor.
4. It seems that the pipe is Seamless as during Direct Extrusion, there is "ORANGE PEEL" surface generated due to use of Glass as lubricant during extrusion. Further, if it was Cold drawn / Pilgered, the reduction percentage was not sufficient to remove the "ORANGE PEEL" surface.
- Ahmedabad, Gujarat State, India
2005
Q. I am trying to electropolish the inside of stainless steel tubes 12 m long by 40 mm diameter. Has anyone done this before?
Colin Scott- Pietermaritzburg, South Africa
2002
![]() |
A. Electropolishing Stainless internal pipe & tube bores is now a standard process available worldwide. Internally electropolished tubing is commonly used for semiconductor gas manifolds. It is indeed tricky when you consider that the surface, depending on material grade, can require 300 - 1000 Amps per square foot, and inside the tube there is precious little volume of electrolyte to run these amps through. So equipment & techniques to do this job have been the subject of numerous patents that you can read about. Some involve pulling a plug of sorts on a line through the tube. The plug contains an electrode, solution inlet and outlet, and a control volume. The control volume is entirely sized by the power supply used. Simple process on paper...but actually doing it will not be so simple. ![]() Dave Kinghorn Chemical Engineer SUNNYvale, California 2002 A. We routinely electropolish the ID of 300 series stainless pipes for various industries that are approximately that size. Dan Weaver- Toccoa, Georgia 2002 |
RFQ: We require SS-304L/316l Electropolished Inside Seamless Tubes, in various sizes & length, please contact us with details i.e sizes, specifications, etc.
Ashwini K [last name deleted for privacy by Editor]Mfg - Kolkata, West Bengal, India
2004
Ed. note: This RFQ is outdated, but technical replies are welcome, and readers are encouraged to post their own RFQs. But no public commercial suggestions please ( huh? why?).
Can we electropolish without mechanical polishing?
Q. We would like to eliminate/reduce the need for mechanical polishing of 304 seamless stainless steel tubing prior to electropolishing.
We are making an assembly which requires SEAMLESS 304 STAINLESS STEEL TUBING 1.0" O.D. X .93" I.D. The tubing sections are approximately 7.799 long. We have been purchasing standard lengths of tubing, and using our laser tube capability, we have been cutting holes and slots into the tube and then laser cutting them to length. After welding 3 other components to this tube section, the assembly must be electropolished. We must manually deburr and polish the assembly before electropolishing due to the dull, hard, extruded finish on the seamless tubing. Even with the time consuming manual polishing the tubing does not always electropolish to our customers requirements.
As others have mentioned in this forum, we would like to proceed with a process of elimination approach this issue. The assembly must electropolish well for the beverage industry.
Any suggestions as to how we must specify and order this tubing? Bright solution annealed possibly?
Thank you.
- Rockaway, New Jersey
2005
Better process for stainless fork tubes for 3-wheel motorcycles?
Q. What material and process of a finish would be more uniform and as good looking, or better looking than the mirror polished finish I am currently using on my 36" long, 2" square, 7 ga., 320 pre-polished 304 stainless steel tubing that we first have machined (a few holes, a slot at one end, and cut to 36" long, with no protruding areas) and then mechanically polished (machine sanded) to 400+ grit and lastly wheel buffed to a mirror #8 finish? Something that will equal the look of a good chrome plating, but that is not hard to get done within a 100 mile radius of Louisville. I am concerned that I might encounter problems with the plating peeling or flaking off later which would be disastrous for us to correct for our customers, as they are located nationwide. Essentially all of our motorcycle is stainless or marine grade aluminum. I would hate to use chrome plated steel, because of the ability for it to rust. Our forks are presently stainless steel. I have thought about continuing to have them mirror-finished and then electropolished, if it is the way to avoid the delicate surface of the polished stainless surface, cosmetically. I welcome and appreciate all suggestions.
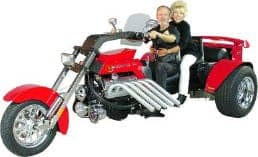
Tom Walters
product designer and corporate owner - Charlestown, Indiana
December 5, 2009
Ed. note: This RFQ is outdated, but technical replies are welcome, and readers are encouraged to post their own RFQs. But no public commercial suggestions please ( huh? why?).
A. Hi Tom. Although problems can sometimes be encountered in electropolishing (as in any process), if done right it is the perfect answer. It will smooth the tubing, keep it reflective, and powerfully deter rust.
Regards,
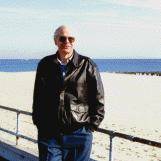
Ted Mooney, P.E.
Striving to live Aloha
finishing.com - Pine Beach, New Jersey
Q. Dear sir,
I am in India.
I am doing electropolishing of stainless steel tube. but I can't find good result after the electropolishing. Please suggest to me which acid I use for better smoothness and sign.
plating shop - Ahmedabad, India
December 16, 2009
A. Hi, Jatin. Please see the Electroplating Engineering Handbook ⇦ this on eBay, AbeBooks, or Amazon [affil links] as it has an excellent chapter on electropolishing of stainless steel, including many different acid formulations. But all of those many different acids have been used successfully, and I would guess it much more likely that your problem is in low current density, inadequate solution movement, insufficient cleaning, or excess water in the acid than that you managed to discover an unworkable acid formulation :-)
Still, tell us what formulation you are using because I suppose anything is possible, as well as th type of stainless steel, and whether you are doing OD only, ID only, or both ID and OD. Thanks.
Regards,
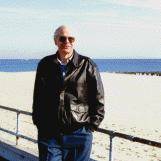
Ted Mooney, P.E.
Striving to live Aloha
finishing.com - Pine Beach, New Jersey
A. Jatin, there are many different types of stainless steels and many different types of electropolishing solutions for them. The basic formulation for stainless steel is a mixture of phosphoric and sulfuric acids; the major solutions are based on sulfuric acid contents of between 15% and 60%, with between 30% and 63% orthophosphoric acid, the remainder is water. The technology is relatively easy, but you do need to know what stainless steel you are treating! There are other solutions available, but they may not be as good as the sulfuric acid/phosphoric acid mixes. By the way, it is very difficult to successfully electropolish 400 series stainless steels.
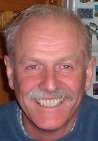
Trevor Crichton
R&D practical scientist
Chesham, Bucks, UK
On Trevor's comments:
Many years ago, I used a proprietary solution on Jetheat which is a modified 410 SS with excellent results. I tried to use the same parameters on a friends 17-4PH and nearly ruined it.
Different solutions work better than others on certain alloys.
See if you can find the series by Charlie Faust in Metal Finishing magazine, probably in the late 80's time frame. He was the accepted expert at that time. It will be a big help, if you can get it.
- Navarre, Florida
A. The results you say you get: are you talking about the inside of the tube? Usually the inner area of a tube are low-current density sites. depending of the size of the tube you can use auxiliary electrodes, if this is not possible you can use higher current density and stirring.
Hiram Gomezelectrochemistry student - GDL, Jalisco, Mexico.
A. I have very successfully demonstrated to a large US Corporation, the electropolishing of the ID of tubing, which is what I presume to be the nature of your enquiry.
I would like to raise a few points which might assist you with your problems. Gassing, seems always something that affects the surface of tubing. To reduce the incidence of this, short lengths can be processed vertically in the tank but should you have long lengths of tubing, then look to pumping the electrolyte through the ID during processing.
Then of course, you have to look at the parameters of your process and examine the current density to determine that your amperage is delivering what is necessary to achieve the results you are seeking
Test the efficacy of your results by looking at the chrome to iron ratio and surface profile after electropolishing.
To offer a more qualified answer we need more information regarding lengths, whether or not you are referring to the ID and the ultimate use of the tubing.
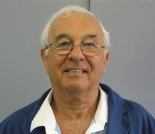
Joel Levinsohn
- Sydney, Australia
Q. My situation: Respected sir kindly suggest me the procedure to electropolish 20 ft x 2 inch dia stainless steel pipe to electropolish from inside.
Hanumant NavaleBuyer - Pune , Maharashtra, India
June 10, 2018
and Chemical Polishing
of Metals in
Research and Industry"
by W.J. Tegart
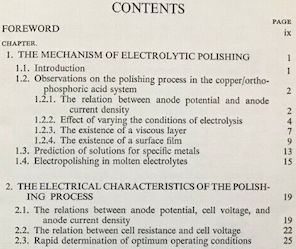
on eBay or Amazon
or AbeBooks
(affil link)
A. Hi Hanumant. As you can see from this thread, successful electropolishing of stainless steel requires a significant knowledge base; and even with that general knowledge base, the electropolishing of the inside diameter of a 20-foot long pipe requires knowledge, experience, and a proper plant, including an internal anode arrangement as well as an efficient method of pumping solution through the pipe.
Please tell us what alloy this pipe is. And can you please very briefly describe the facility you have on hand (length & depth of electropolishing tank, rectifier rating?) and your prior electropolishing experience (biggest pieces you've electropolished, any ID electropolishing experience?), so readers have a good starting point for trying to help you? Thanks!
Regards,
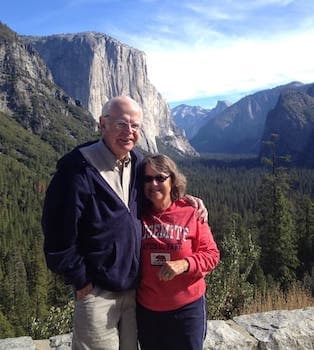
Ted Mooney, P.E. RET
Striving to live Aloha
finishing.com - Pine Beach, New Jersey
Q. I have SS304 Tall containers of different size. How do I electropolish inner section of containers?
(1) how do I setup cathode and anode?
(2) can only inner part be electropolished? or whole container would be electropolished?
- Daman, India
May 12, 2022
A. Hi Ashish. Large tanks are often electropolished on the inside by filling them with solution. That may be less practical for these smaller containers. They can surely be electropolished, but probably not with a single racking because the inside will require both an auxiliary anode and air agitation; and the logistics of having open end up during polishing, but open end down as the parts are trnsferred from tank to tank means that a lot of human effort and intervention will be required.
Luck & Regards,
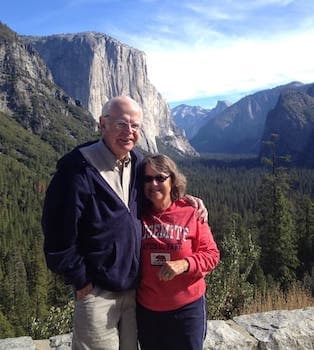
Ted Mooney, P.E. RET
Striving to live Aloha
finishing.com - Pine Beach, New Jersey
June 2022
⇦ Tip: Readers want to learn from your situation;
so some readers skip abstract questions.
Q. What are all the possible root causes for stain mark issue in electropolishing process?
CYCLE--(Degreasing, enough rinsing, Electroplishing process, enough rinsing, Neutralization, enough rinsing, Passivation, enough rinsing, hot water rinsing, oven treatment for drying)
Anyone help me out based on your experience?
Employee - Batam Indonesia
June 1, 2022
A. Hi JAISHANKAR. I suppose we could list substrate defects, equipment inadequacies, chemical inaccuracies, and operational errors as possibilities. It would probably be better for you to describe your situation and the specific stain via photographs. There are tiny white specs, black specs, whole areas of frostiness, water stains from not using DI water in your final rinse, etc. Tegart or Shchigolev might offer pretty good infromation.
Luck & Regards,
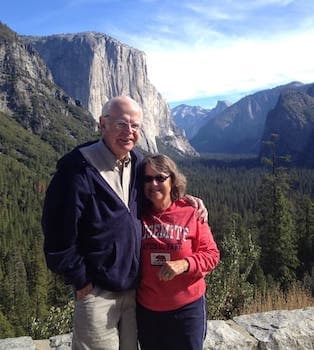
Ted Mooney, P.E. RET
Striving to live Aloha
finishing.com - Pine Beach, New Jersey
June 2022
Q. We do electropolishing here in Ireland and I'm currently electropolishing the inside of 1.5 elbows and I keep on getting a shadow inside. I'm presuming this is from the gas trapped inside. I have tried nearly everything to fix this but nothing works ... any ideas?
Craig StoranShop Manager - Limerick Ireland
June 3, 2022
Q, A, or Comment on THIS thread -or- Start a NEW Thread