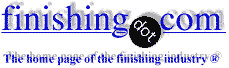
-----
Calculating Thickness of Oxide Layer Grown on Anodized Aluminum
I'm using 0.23 M oxalic acid bath to anodize high purity aluminum with a lead counter electrode at 15 V DC for 1 hour. Is there any way to determine the thickness of the porous oxide layer that'll be formed on the Al at the end of the process? Also, is there anyway to determine the etching rate of an etchant (say 0.1 M phosphoric acid) on the oxide layer?
Sibi SuttyResearch Student - Toronto, Ontario, Canada
September 21, 2009
First of three simultaneous responses --
Sibi, see letter 51564
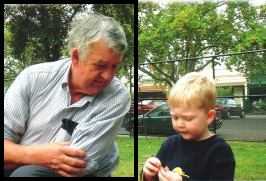
Bill Reynolds [deceased]
consultant metallurgist - Ballarat, Victoria, Australia
We sadly relate the news that Bill passed away on Jan. 29, 2010.
September 22, 2009
Second of three simultaneous responses -- September 23, 2009
Sibi
The thickness of an anodised layer is usually measured with an eddy current gauge. This needs to be calibrated and verified against thickness standards to be accurate.
If you have only a very few samples you could microsection them but this is destructive and slow.
Etch rate is best measured by weight loss - much more accurate than change in thickness.
Why not phone your local anodising company and speak to the chemist. He will have a thickness gauge and most are very helpful. You could also learn more about anodising than (almost) any course will teach
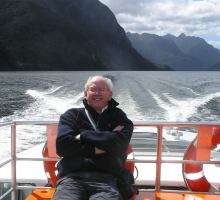
Geoff Smith
Hampshire, England
Third of three simultaneous responses -- September 23, 2009
Hi,
Someone may have the experience to be able to quote a thickness based on the voltage, acid strength, temperature and alloy type.
But if not, measure the surface area of the aluminium and the current applied. From this information calculate the current density. A CD of
1.2 amps/sq.dm will give about 1 µm in 2.5 minutes. Your voltage of
15 will give significantly less current density than the figure quoted and you should make the appropriate adjustments to the calculation. The rate of formation which I used is that typical of commercial oxalic acid anodising with a voltage of about 60 v at 5 degrees C.
With acknowledgements to Michael Faraday.
Harry
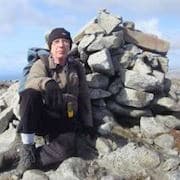
Harry Parkes
- Birmingham, UK
September 24, 2009
Thanks a lot for your help! I've managed to hook up an oscilloscope to measure the current passing through my anodizing cell. I then used Faraday's law to estimate the maximum thickness of the oxide layer.
Reaction at the anode: 2Al + 3O(2-) --> Al2O3 + 6 e-
1.71 mA is passing through my cell for 60 mins, so that's 1.71e-3A *
3600s = 6.156 C, which makes 6.38e-5 mols of electrons.
For every 6 mols of electrons 1 mol of Al2O3 is produced at the anode so, 1.06338 mols of Al2O3 is produced, which is around 1.08 mg. Using
4.1 gcm-3 as the density of alumina, the volume produced is around
2.64e-4 cm3.
My anodized surface is pure Al of about 0.5 cm x 0.8 cm, which makes my thickness around 6.61 microns. (Am I doing this right?).
I'm following the steps of a researcher before me who said in his journal paper that he got around 1.8 microns thickness (with 15V,
0.23M oxalic acid, 60mins, but no mention of current density).
Is it better if I specify my conditions for anodizing by current density? If that's true, would a galvanostat/potentiostat system lead to a much more controllable way of anodizing my samples?
- Toronto, Ontario, Canada
First of two simultaneous responses -- September 25, 2009
The variable that you left out is the amount of electricity used for generation of hydrogen and oxygen. You are far over their overvoltage potential.
Give up and buy or rent a testing equipment.
You can measure the part before anodize and after anodize and get the growth. Multiply this times 2 to get the true thickness of the anodize.
- Navarre, Florida
Second of two simultaneous responses -- September 26, 2009
Sibi
Nice try with the calculation but unfortunately life is a little more complex.
Take a look at http://electrochem.cwru.edu/encycl/ and follow the link anodizing fig 4 to get some idea of what an anodised film looks like. It is evidently not solid aluminium oxide. Since the pore structure depends on the thickness and anodising conditions, it is not a practical proposition to calculate (or even make a reasonable estimate) thickness.
Two other points.
Faraday calculations assume only one reaction takes place - no gas emissions, etc.
An oscilloscope for measuring current? It is not an appropriate instrument and is usually used to show rapidly varying voltage waveforms. What is wrong with a (calibrated) ammeter?
You should also know that the rate of oxide growth may not be linear and some electrolytes can attack the oxide, effectively limiting the thickness.
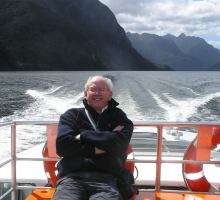
Geoff Smith
Hampshire, England
combo magnetic & eddy-current coating thickness tester
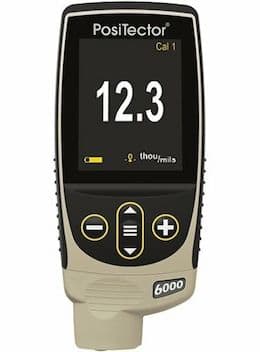
on eBay or Amazon
(affil link)
Thanks a lot for the advice. I'll begin my hunt for an eddy current gauge as someone suggested earlier. I also read in Electroplating Engineering Handbook ⇦ this on
eBay,
AbeBooks, or
Amazon [affil link]
that an eddy current gauge is the best measure of anodic film thickness.
An oscilloscope is an unconventional tool for measuring current but in my setup, it measures the voltage across a resistor connected in series with the circuit. From the value of the voltage, I can obtain current. I take the round about method because I want to capture the voltage vs time trace for the first 20 - 60s. I know that porous film formation is occurring if the voltage dips in the beginning and rises back up to a stable value.
Once again, thanks a lot for the advice!
- Toronto, Ontario, Canada

Q, A, or Comment on THIS thread -or- Start a NEW Thread