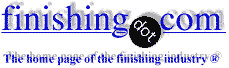
-----
My hard anodize is too fast
Can someone please tell me why I'm getting .003 mils so fast. I have a part of 6061 about a square foot, had 200 amps on it and in 12 mins I had .003. We can't keep up with the racking of parts. Why is it running so fast? I have done what I was told as far as temp and percent of acid. We have been told it is a good thing and to hire more people to rack. I was just wondering if someone knew why. Thanks
Terry SmithStarting out - CA
March 11, 2009
Hi, Terry. First things first: find out what the thickness requirement is and what thickness you are getting, and be very careful in expressing it. 0.003 mils is not hardcoat thickness -- it's not even a hundredth of the way, but .003" would an awful high thickness. Then do a Faraday's Law calculation, or the simplified version of it, the 720 rule: 720 = ASF x minutes / mils
How are you measuring the anodized thickness? Have you had a lab do salt spray, abrasion testing, etc., to make sure you're not just fooling yourself? I do not believe that it is possible to hard anodize at 200 ASF; you would have a fabulous heat rise -- what is your cooling and agitation system? What is your voltage? It's human for a beginner to believe they have accidentally invented a fabulous new technology, and it can happen, but odds are very strong against it :-)
Regards,
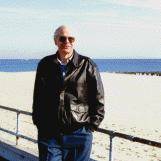
Ted Mooney, P.E.
Striving to live Aloha
(Ted is available for instant or longterm help)
finishing.com - Pine Beach, New Jersey
March 13, 2009
March 13, 2009
As you know, Ted, I keep my mouth shut on plating matters because while understanding the theory I've never done the hands-on. But I just had to apply your 720 rule (mils = ASF x minutes / 720) and Terry's numbers give 3 mils (0.003 inches) which is what he claims (assuming he was confused about mils being thousandths of an inch).
So what is happening in his tank?
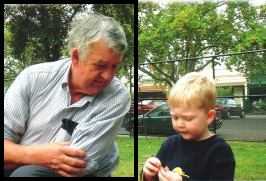
Bill Reynolds [deceased]
consultant metallurgist - Ballarat, Victoria, Australia
We sadly relate the news that Bill passed away on Jan. 29, 2010.
Normal hardcoating conditions are 35 to 40 amps per square foot at 32 °F. With the right part geometry, good racking, excellent cooling flow, and a receptive alloy such as 6061; it is possible to hardcoat at 200 ASF. This will result in a rapid build-up of coating. It might also result in "burning" which in the early stages could appear as a thick but soft coating. Warmer tanks will also form anodic coatings faster but with a corresponding loss of hardness.
Chris Jurey, Past-President IHAALuke Engineering & Mfg. Co. Inc.

Wadsworth, Ohio
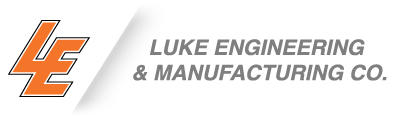
March 13, 2009

Q, A, or Comment on THIS thread -or- Start a NEW Thread