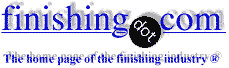
-----
Chromate, Alodine, Iridite?
Q. I've always been under the impression that chromate, Iridite, and Alodine were all interchangeable forms of chromate, but I have a customer that's telling me that there is a difference (I know that there can be a color difference depending on what type of chromating one is doing). Will somebody please confirm, or dispute, that these 3 processes are indeed the same, and that only the terminology is different? Thank you,
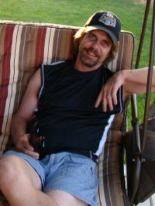
Marc Green
anodizer - Boise, Idaho
2000
A. Hi Marc. Chromate means a "chromate conversion coating" which can be put on an amenable metal with the correct parameters for that metal. The chromate conversion coatings are sometimes referred to as "chem film" when on aluminum.
Iridite is a proprietary name of a family of conversion coatings now owned by Macdermid. Alodine is similarly the proprietary name of a family of conversion coatings now owned by Henkel.
The exact capabilities and uses of a specific Iridite or Alodine formulation is determined by the numbers that follow as in -14.
James Watts- Navarre, Florida
2000
A. Right, Jim. I'd only add that specific Iridite products and specific Alodine products may be specifically 'qualified' for an application. For example, MIL-C-5541 chemical conversion coating of aluminum must--if it is to 'qualify'--be done with accepted, tested, 'qualified' chemicals. Alodine and Iridite are not the only accepted ones, but generic chem-filming chemicals are not acceptable.
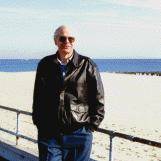
Ted Mooney, P.E.
Striving to live Aloha
(Ted can offer longterm or instant help)
finishing.com - Pine Beach, New Jersey
2000
![]() |
A. I have not looked at the QQP in several years now, but it seems to me that there was one or two stray products on that qualified list. My nickel would certainly go with Alodine or Iridite as they have the most experience with the product that is qualified. James Watts- Navarre, Florida 2000 2000 Q. So... let me just see if I understand this correctly. I am talking about clear chromating on aluminum. A customer came to me with a pot metal (aluminum) part he wanted clear Iridited. Of course, the part turned black after the etch, and would not desmut (I don't have a nitric hydrofluoric tank). But he told me if I applied an Iridite, it wouldn't have done that. Do you guys think, that if I skipped the etch, and just alkaline cleaned, and de-oxed the part, then clear chromated (generic), that I would get a decent coating?...I don't think that I would if I skipped the etch. ![]() Marc Green anodizer - Boise, Idaho |
![]() |
A. There are people hereabouts who are more qualified to answer your followup than I am, Marc, and I hope they check in to help out. But in the meanwhile, I would agree with your implied answer to your own question, that the conversion coating step is not the cause of the blackening, the etch is. Do you have a separate non-etch cleaner? I have seen shops that don't, and they find themselves confronted with the problem that getting the parts clean in an etch tank will turn them black. I don't have enough knowledge of your problem, or diverse enough experience with that problem to give an unqualified answer, but yes I believe you can clean the parts well, then not etch at all or etch very minimally, and produce satisfactory parts. ![]() Ted Mooney, P.E. Striving to live Aloha (Ted can offer longterm or instant help) finishing.com - Pine Beach, New Jersey 2000 A. I know this might sound like I'm being a little rude, but define decent? Is decent a coating good enough to apply a primer overtop without voids? Is it good enough to help the corrosion properties a little bit, or a considerable amount. Decent in my opinion is just that really, your opinion of what would pass. I have chromated cast parts without an etch, never had any problems/complaints/rejects from doing it that way. Some material it can be done on, some it can't, 368 is running in my head as a metal that was capable of going this route. It might not have been the most desirable finish, but it got the job done. Also, you can (although its not proper) you can desmut out of sulfuric. Matthew StiltnerToledo, Ohio 2000 |
2000
Q. Good question, Matt.
I don't have a good answer for your "decent" question. We were not given a spec to meet. These parts will not be painted. I think the customer just wants to retain the "look" of the pot metal. We have been applying a silver powder coat to these parts, and I'm getting the impression the customer just wants to find a cheaper route to go. On most of the aluminum we clear chromate, we get kind of an iridescent look to them, however, I wouldn't even know how to check for adhesion on these parts, without sending them out for testing. I guess maybe I should put it back on the customer to give me a spec to meet. Any other input from any of you chromate geniuses would be appreciated.
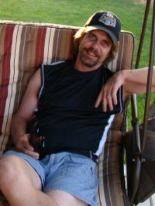
Marc Green
anodizer - Boise, Idaho
A. I suppose that one brand of chromate may be a little better than another for a specific application, but the biggest problem seems to be that you don't have the proper preprocessing cycle for the part. If I wanted that work, I would work out my own specification, then the job would be mine forever! Like a lot of jobshops, they keep a job because they can do the job better and cheaper than anyone else. A clear chromated piece of Al has lots of advantages over a silver painted part. Your customer may be happy just to have the part shiny and bright even without a conversion coating applied.


Tom Pullizzi
Falls Township, Pennsylvania
2000
A. Marc,
Sorry I took so long to get back to you with an answer on your response/answer. To check adhesion, just paint the part with a black paint, that's the easiest way I can think of.
Even though they won't be painted this will give you a very good idea of how well the coating is working. If you have bare areas, you have a bad finish in that area(s). Besides, where the finish is clear, slightly iridescent this will give you a dark area to see, that way there is no confusion as to whether or not the coating is applied to such and such areas.
If all they want is a cheaper coating over the powder coat, then heck I guess the options are endless there, you can always find cheaper, but can you find more reasonably priced with the same functionality, that's the big question in my opinion.
Matthew Stiltner- Toledo, Ohio
2000
A. Another basic adhesion test is the masking-tape pull test. Apply a strip of masking tape along the part, press firmly, and pull it off. If anything comes up, it fails. Apply the tape and pull in two perpendicular directions.
Variations on this test include the number of successful pulls, direction, orientation, type and width of tape, etc.
I'm sure each product and customer will have different adhesion tests they may want applied (or not).
- Arnprior, Ontario Canada
April 14, 2015
2001
A. Marc,
We run two types of conversion coating
1.Alocrom 1200 (Alodine 1200 in US)
2.Iridite 14.2
We use the Alocrom for commercial requirements as we do not control this to the same level as the Iridite. The Iridite is used to MIL-C-5541.
We often have a requirement for a clear conversion coating on aluminium and this can be achieved in a couple of ways.
1. There is a product, Alocrom 1000 which I believe is the clear version of Alocrom 1200
2. The Iridite 14.2 may be bleached using hot water to give a clear coating. The manufacturers data sheets will have the details.
It is worth noting that the bleaching effect reduces the corrosion protection! The cleaning process is important in achieving the desired results in any conversion coating.
Typically we use the following process, Vapour degrease, Nitric clean, rinses, de smutting, rinses, conversion coating, rinses. This gives us consistent results and the conversion coatings continue to pass the salt spray tests. However if you do not have a nitric tank try leaving the component in the de smutting solution for a longer period prior to coating. This works for us on alloys such as LM25 which the nitric would adversely effect i.e., 'over etches and brings out the grain'. Alternatively a light blasting with a glass bead media gives a good even finish without the requirement for nitric cleaning.
I hope this helps a little.
Cheers,
Richard Mosley- UK
Multiple threads merged: please forgive chronology errors and repetition 🙂
Explain chem-film process in depth
Explain Chem-Film process to me in depth.
Dr. Hillphysicist - P'cola, Florida, US
2004
2004
At your orders, Sir :-)
Chem-film is another name for chromate conversion coating of aluminum. See MIL-C-5541.
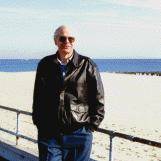
Ted Mooney, P.E.
Striving to live Aloha
(Ted can offer longterm or instant help)
finishing.com - Pine Beach, New Jersey
Setting up a plant to do Alodine process
Q. Hi dear,
I'll do Alodine in Canada and I want a set up my Alodine plant in India too. So can you tell me is this a good project or not? How much total it cost me if I start in large scale?
Nipun BrejaMETAL PRODUCTS - TORONTO, CANADA
2006
A. Based on the large amount of data presented, I know exactly what you need. The answer is quite obviously somewhere from $7 to $7,000,000. With some additional information, we might be able to refine that number down some!

Milt Stevenson, Jr.
Plating shop technical manager - Syracuse, New York
2006
A. Hi Nipun. Alodine is a tradename for a chromate conversion coating used in the MIL-DTL-5541 process. You would need an appropriately sized tank line for the sequence of alkaline clean, rinse, etch, rinse, desmut, rinse, chromate conversion coat, rinse, dry ... plus the appropriate auxiliary equipment like heaters, exhaust system, DI rinsing, waste water treatment, material handling, and laboratory. I would pretty confidently refine Milt's numbers by an order of magnitude on each end, down to between $70,000 and $700,000.
Regards,
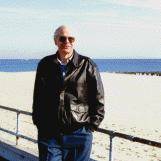
Ted Mooney, P.E.
Striving to live Aloha
(Ted can offer longterm or instant help)
finishing.com - Pine Beach, New Jersey
Chem-film process line
Q. Hi due to quality and delivery issues we want to investigate the possibility of setting up our own chem-film process line. We have no knowledge of how to do this or any understanding of the costs involved. The process would have to be carried out to Aerospace standards. Can anyone advise as to the most cost effective way to buy equipment and get started.
Regards
company owner - Dunstable, Beds., UK
December 15, 2009
A. Hi, Steve. A chem-film line is not something that can be bought from a catalog, but must be engineered based on the required production rate, the characteristics of the components, etc. You can start with your chemical supplier and have them recommend an equipment supplier, but both will be protecting their own interests first, each other's interests second, and your interests when they get around to it :-)
That was a little tongue-in-cheek because some successful installations have certainly resulted from that approach, but the right thing to do is to retain a consultant who is experienced in chem-filming and the design of chem-film installations. The early decisions are far more consequential than the tiny final details, so don't make the common mistake of trying to get halfway through the project first. A consultant whom you have painted into a corner can help you somewhat, but not nearly as much as one whom you haven't. Good luck.
Regards,
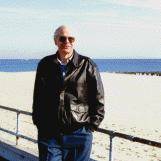
Ted Mooney, P.E.
Striving to live Aloha
(Ted can offer longterm or instant help)
finishing.com - Pine Beach, New Jersey
December 16, 2009
December 16, 2009
A. Hi Steve
Ted is a little hard on the suppliers. It seems that they are a possibly more aggressive in America. The plating industry UK is small and word gets round fastif you get bad advice.
But he is quite right that getting advice at the concept stage will save problems later, particularly if you need Aerospace accreditation.
I would start with the Institute of Metal Finishing (link on this page) or http://www.uk-finishing.org.uk/index.htm
They will put you in touch with plant and chemical suppliers.
Don't expect everyone to understand the term 'Chem-Film'. It is common un US but Europe refers to Conversion Coatings. This almost always means Alochrom.
The process itself is not difficult but you need to include provision for pre-cleaning, effluent disposal, chemical control, testing, documentation etc.
If you have no other wet chemistry processes on site, you may find it simpler to just look for a more reliable supplier. There are good ones out there.
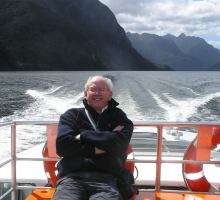
Geoff Smith
Hampshire, England
----
Ed. note: Actually, Steve had used a brand name which we edited to 'chem-film' so that the comments weren't directed towards any particular supplier. In retrospect, Geoff's "conversion coating" would probably have been a better term.
A. Steve,
Another thing to check is whether your aerospace customer requires NADCAP. If so, as Geoff will attest, this will make the process much more complicated and the use of one of the many reputable process houses in the UK would be strongly recommended.
Aerospace - Yeovil, Somerset, UK
December 17, 2009
Yellow and Clear Iridite coating process?
March 2, 2017Q. We are looking to add yellow and clear Irridite processes in our shop. Just trying to see if anyone knows the temps and what material tanks to use for each process. Based on what I have found, the process is as follows:
Cleaner(Steel)
Rinse (Poly)
Etch (Steel)
Rinse (Poly)
Nitric (Stainless)
Rinse (Poly)
Conv YEL(Steel)
Conv Clr(Steel)
Rinse (Poly)
Hot (Poly)
Any recommendations before I move forward and also does anyone know the recommended temps? Thanks
Plating shop employee - Rochester, New York
Ed. note: This RFQ is outdated, but technical replies are welcome, and readers are encouraged to post their own RFQs. But no public commercial suggestions please ( huh? why?).
A. Hi Ed. Although the sequence you show is quite a common one, it's not the only one; and please think about these points:
- the possibility of double rinses between all processes;
- your nitric acid step is known as the de-smut step and it's not always nitric acid, depending on the alloy you are desmutting;
- best to put the Conv Clr before the YEL because dripping clear into YEL is less of a problem that the reverse.
As for materials of construction, I'd probably use poly for the desmut because it might not end up being nitric acid. Also, although I saw one conversion coating tank made of unlined steel, I think it's asking for trouble; I'd use poly. And even the cleaner and etch could be poly if you wish. Good luck.
Regards,
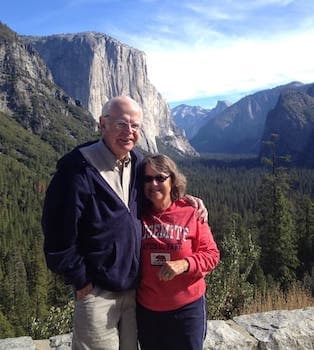
Ted Mooney, P.E. RET
Striving to live Aloha
(Ted can offer longterm or instant help)
finishing.com - Pine Beach, New Jersey
March 2017
March 3, 2017
Q. Ted,
Thanks for the info! Even given the chemicals the poly you think would be okay? I am looking to purchase tanks from a company called [ deleted by editor]. Would love to use just poly! Any idea the temps?
Thank you
- Rochester, New York
A. Hi. It's hard to give an exact maximum operating temperature for a polypropylene tank because the material gradually gets softer with increasing temperature. I would not use it above 150-160 °F, although I think some engineers might go as high as about 180 °F.
The cleaning tank is the only one where temperature might be a limit. Etches generally run around 140 °F. Chromate conversion processes probably should not be allowed to vary with the ambient temperature, because it becomes a process control issue, but are usually only heated to something like 80 °F.; perhaps sometimes to 110 °F.
But here's the thing Ed. You should be getting your chromate conversion chemistry from a vendor and they should not only recommend the cleaning cycle and offer their chemistry (etch inhibitors, desmut process), but run your test parts and advise you of the temperatures, need for agitation & filtration, etc. You don't build a process line and then try to get chemistry that will work within its limitations, you get the chemistry to work and then you build the line accordingly. If you haven't done chromate conversion coating before, and don't have complete confidence in a process vendor, you really should retain an aluminum processing consultant. Although I don't do it anymore, I did consulting for 30 years and was never once called too early, but was often called after the customer had painted himself into a corner. Good luck!
Regards,
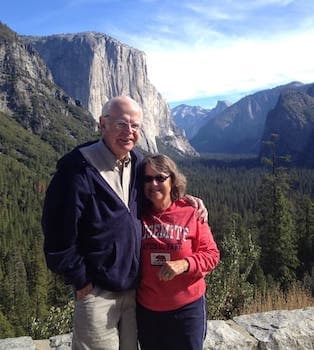
Ted Mooney, P.E. RET
Striving to live Aloha
(Ted can offer longterm or instant help)
finishing.com - Pine Beach, New Jersey
March 2017
Q. Thanks for the info Ted. Do you know of any aluminum processing consultants that are out there? Thanks!
Ed Jones [returning]- Rochester, New York
March 7, 2017
A. Hi Ed. For a number of reasons we try to avoid suggesting vendors or brands, and just keep things technical.
adv.
... but the site is made possible by supporting advertisers. Robert Probert is an aluminum processing consultant and the author of Aluminum How-To. Good luck.
Regards,
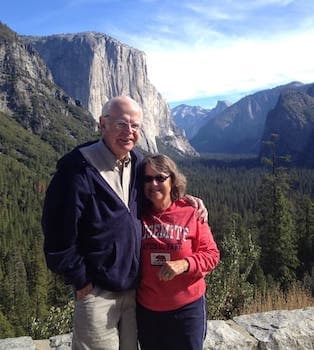
Ted Mooney, P.E. RET
Striving to live Aloha
(Ted can offer longterm or instant help)
finishing.com - Pine Beach, New Jersey
March 2017
Q, A, or Comment on THIS thread -or- Start a NEW Thread