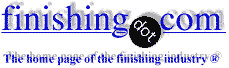
-----
Hard anodizing chiller sizing

Disambiguation / See also --
• Topic 58129, "Cooling of home/D-I-Y anodising baths"
Q. Hello everyone,
I am looking to switch to hardcoat anodizing of aluminum. I currently use a 19 ton chiller with a 24V/4000A rectifier. I am looking to anodize up to 5 ft^2 of area. Will it even be possible to get above 1 mil layer?
Thank you in advance!!
- Bloomfield, New Jersey, USA
November 30, 2023
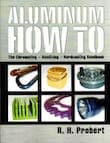
Aluminum How-To
"Chromating - Anodizing - Hardcoating"
by Robert Probert
Also available in Spanish
You'll love this book. Finishing.com has sold almost a thousand copies without a single return request :-)
A. Hi Ross. Robert Probert's book offers a great introduction to what is and isn't hardcoat according to different people's definitions. According to it I'd say you should be able to obtain 0.001" thickness but the coating may not necessarily be much if any harder than what you are presently getting.
If you're only looking to process 5 ft^2 at a time, that should only take about
120 Amps, i.e., 2880 Watts @ 24 Volts, i.e., 9825 BTU/hour.
Although it's necessary to 'derate' a chiller to about 50% of the label rating for operation at hardcoating temperatures, a ton of refrigeration is 12,000 BTU hour so chiller capacity is one problem you don't have :-)
Voltage is one problem you may have, but what alloy are you processing, as that can be critical to anodizing discussions.
Luck & Regards,
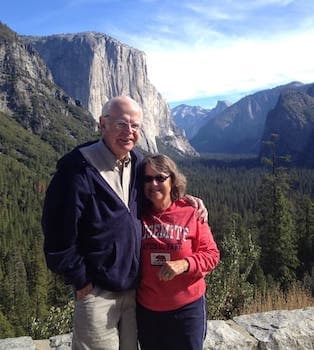
Ted Mooney, P.E. RET
Striving to live Aloha
(Ted is available for instant or longterm help)
finishing.com - Pine Beach, New Jersey
A. The difference between type II and type III is the density of the pores of oxide. To achieve a true type III hard coat you need more voltage. I generally recommend 75 volts but in some cases, you can work with 60 volts. So 24 volts will be a constant problem to get and pass most hard coat needs and testing.
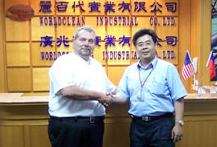
Drew Nosti, CEF
Anodize USA

Ladson, South Carolina
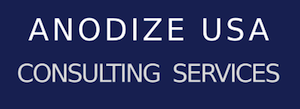
January 3, 2024
Q. Hi all,
I have gone through hundreds of threads and I know this question has been asked time and again but I really wanted a more precise answer, please help me out.
I am setting up an Anodizing type 2 shop, in which I will be Anodizing just 1 type of Aluminium Profile.
-Area of profile is 7.38 sq ft (perimeter: 132 mm length: 5200 mm).
-Coating thickness of 15 micron.
-Anodizing tank size : 19'10" X 5'00" X 5'00".
-No. Of Anodizing Tanks available: 3
-Quantity required per hour: 500 pcs
Please advise me as to if this quantity is possible while maintaining batch quality and if yes what would be the size of rectifiers and chiller.
Thanks in advance.
- India
August 22, 2024
privately respond to this RFQ
Ed. note: As always, gentle readers: technical replies in public and commercial replies in private please (huh? why?)
! Please someone help.
Harshit Baralia- Kolkata India
August 27, 2024
A. Hello Harshit,
I was a plating & anodizing installation consultant for decades and was nearly always called in after the design was well underway, with early mistakes already committed to. You should retain an anodizing consultant now, rather than later.
Your questions look like the simple arithmetic of multiplying surface area by current density to find required amperage, then picking rectifiers from this; multiplying amps x volts x conversion factor to determine BTU/hour for the chiller; and applying the 720 rule to determine thickness vs. anodizing time ... but they're not.
Actually your questions should be what shall be (or already is) the work schedule -- days per week & hours per day which will allow both ample maintenance time and minimal loss to startup and shut-down time? What will be the racking geometry and method? Are 3 tanks at 5 foot deep an appropriate target, or would (for example) 2 tanks at 7 foot deep or 4 tanks at 4 foot deep be better?
But if you will describe your racking scheme, hopefully with a sketch, we will do the mentioned arithmetic for you and tell you how many profiles you can anodize per hour.
Luck & Regards,
Ted Mooney, P.E. RET
Striving to live Aloha
(Ted is available for instant or longterm help)
finishing.com - Pine Beach, New Jersey
⇩ Related postings, oldest first ⇩
for Shops, Specifiers & Engineers
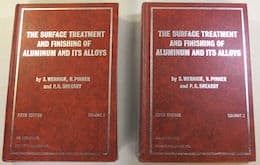
avail from eBay, AbeBooks, or Amazon
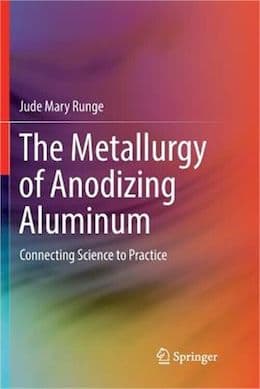
avail from eBay, AbeBooks, or Amazon
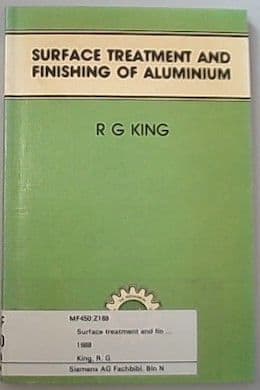
avail from eBay, AbeBooks, or Amazon
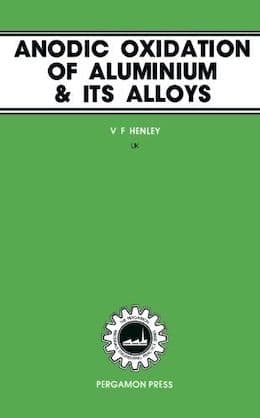
avail from eBay, AbeBooks, or Amazon
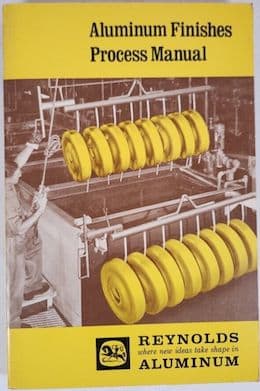
avail from eBay, AbeBooks or Amazon
(as an Amazon Associate & eBay Partner, we earn from qualifying purchases)
Q. Sir,
I am working in a Pvt Ltd company and wanted to know about the process of chilling plant, selection of pump, and spares required for Preparing New Chilling Plant and what books to be referred. FUNCTIONS OF CHILLER USED AND PARTS, PHE SELECTION AND PUMP, ETC., REQUIRED.
ADISESHAN- Mumbai, India
2002
Industrial Chillers on eBay (affil link)
A. Hi ADISESHAN. You start by sizing the chiller to remove the heat load impressed on the plating or anodizing tank by the rectifier. Multiply the Amps by the Volts times the percentage of time the tank is occupied and divide by 1000 to find the kiloWatt (KW) load. Then just apply the appropriate conversion factor to convert the KW to BTU/hour, or Calories/hour or Tons of Refrigeration as desired. Specify titanium and plastic construction. You can order a "packaged chiller" of a given Tonnage, which would include the required holding tank, cooling tower, heat exchanger, compressor, and pumps -- all properly sized together. Good luck.
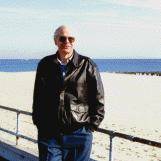
Ted Mooney, P.E.
Striving to live Aloha
(Ted is available for instant or longterm help)
finishing.com - Pine Beach, New Jersey
Q. I am sizing new hard anodizing chillers and am having a hard time reconciling what the math tells me I need and what experience tells me we need. First of all the math... I size the chillers according to engineering custom: rectifier running volts and amps and time converted to kWh converted to BTU/hr converted to tons of refrigeration. I reviewed the literature again as well as past Ted Mooney posts and verified that I was indeed doing it correctly. Now for the experience ... I logged power consumption on existing appropriately sized cycling chillers and found that they are using only about half of the power that would be expected by the calculation. I can only assume that much of the heat is removed by the air agitation of the bath rather than being transferred into the solution to be removed by the chillers. Does anyone have experience similar to this that has allowed them to effectively down-size their chiller equipment?

Jon Barrows, MSF, EHSSC
Kansas City
March 13, 2009
A. Hi, Jon. You probably already realize this, but for the benefit of readers who may not: cooling towers function by evaporating a portion of the recirculated water to cool the rest, and the process is governed by a principle called the "wet bulb temperature". If you take a thermometer, cover the bulb with a wet cloth, and put it in a cloth sling to swing it in circles to maximize the evaporation, the thermometer will show a lower temperature than a dry thermometer. The difference will be something like 10 °F, depending on temperature and humidity. Average wet bulb temperature data for various geographical locations and seasons is available. So, to my knowledge, no agitation system could, even at best, cool a tank to below the wet bulb temperature inside the shop -- which is probably significantly higher than the operating temperature of the hard anodizing bath. And I think, except in the case of a dry air-conditioned shop, this contribution towards cooling will be unreliable and fairly minor.
But remember that rectifiers rarely operate at their full rated amperage and voltage, that the tank is empty some portion of the time, and that during hard anodizing the voltage is significantly lower than the terminal voltage for a percentage of the processing time. Also, some of the power (maybe 5-10 percent?) is lost to bus bar resistance and resistance at the joints, and never makes it to the tank. Try to find the ramp curve, and the percentage of time the tank is in use, deduct a little of the power for bus bar losses, and maybe things will reconcile.
In my career as a plating equipment engineer I sized a lot of chillers, and re-sized a number of cooling systems that proved too small ... and I just never saw evidence that this simple calculation of Actual amps x Actual volts x % duty cycle is significantly overly conservative for cold tanks (although it's clearly conservative for hot tanks like chrome plating tanks which lose a lot of heat to the atmosphere). Good luck.
Regards,
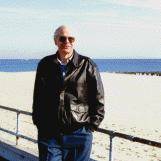
Ted Mooney, P.E.
Striving to live Aloha
(Ted is available for instant or longterm help)
finishing.com - Pine Beach, New Jersey
A. Assuming typical hardcoat bath operating conditions of 32 °F, Ted is correct. Air agitation would be a heat load due to the higher ambient temperature and the heat of compression.
If you use a water cooled condenser with a cooling tower, the compressor discharge condensing temperature will be lower than outside air due to the evaporative cooling described by Ted. If you use colder well or city water as a heat sink, your compressor will be even more efficient.
The low suction pressures required to cool a 32 °F bath will significantly derate a refrigeration compressor. One half of "nameplate" capacity would not be unusual. This will result in lower power consumption under normal operating conditions (i.e. 32 °F bath. If you let the bath return to room temperature, your power consumption will go up. Your motor and other electric gear needs to be sized for these higher load, startup conditions.
Luke Engineering & Mfg. Co. Inc.

Wadsworth, Ohio
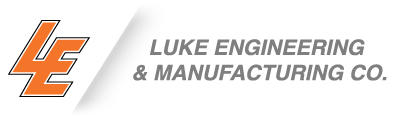
Thanks guys, I think I was hoping that I had overlooked something that would allow me to downsize the chillers and save some money. I had estimated an average load, but to really know I need to do as Ted suggested and measure volts and amps that I am putting in over time and see if it balances the power output of the chiller. I bet Ted is right and it will balance out.

Jon Barrows, MSF, EHSSC
Kansas City
Thank you Chris! I was confident that I was right but I couldn't really reconcile Jon's numbers. Although I knew that chillers must be derated to about 50% nameplate capacity for hardcoat cooling, I never made the connection that a derated chiller isn't going to draw its full nameplate electricity rating :-)
Regards,
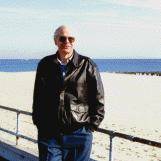
Ted Mooney, P.E.
Striving to live Aloha
(Ted is available for instant or longterm help)
finishing.com - Pine Beach, New Jersey
Process chillers
Q. Hello everyone, can anybody please help me with the calculation for a water cooled chiller, used for hard anodising. required temperature is -2 °C and inlet temp is 42 °C. Flow rate is 6000 lph. Please explain the calculations for the same.
shubham ghosh- noida, India
April 20, 2015
A. Hi Shubham.
You are trying to hold an anodizing temperature of -2 °C (28 °F), but the rectifier is putting heat into the tank whenever you are anodizing. The first step, as described above, is to multiply the actual Amps x actual Volts x an estimate of the duty cycle to determine the Watts which the rectifier is adding to the tank. Then you convert that to Calories per hour or BTUs/hour.
For example, if the actual current is 1250 Amps and the final voltage is 40 Volts, you are adding 50,000 Watts or 50 KW per hour at that point. But the tank is empty for a while after each load, and you don't reach the final voltage until the end of the cycle, so you might estimate, after looking at the ramping profile and cycle time, etc., that your duty cycle is 60%. So the actual heat input from the rectifier is 30 KW.
You convert this to Calories per hour by multiplying it by 860 or to BTU/hour by multiplying by 3412. So you need to remove 25,800 Calories/hour or 102,360 BTU/hour. If the flow rate of cooling water to the water cooled chiller is 6000 lph, which is essentially 6000 Kg/hour or 13220 lbs/hour, the temperature of the cooling water will rise by about 25800/6000 = 4.3 °C. or 102360/13220 = 7.75 °F.
A "ton of refrigeration" is defined as 12,000 BTU/hour, so your chiller consumes 8.53 tons. As Chris Jurey warns, the nameplate data on chillers applies to room temperature operations, not sub freezing temperatures, so the nameplate must be derated by about half for hard anodizing. So a nominal 15-ton chiller, certainly no less, would be about right. Good luck.
Regards,
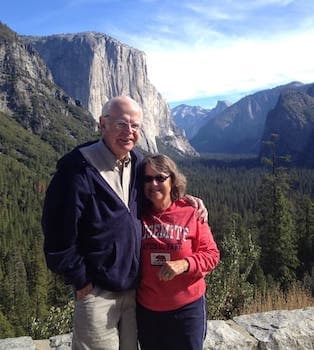
Ted Mooney, P.E. RET
Striving to live Aloha
(Ted is available for instant or longterm help)
finishing.com - Pine Beach, New Jersey
Q. Dear,
As per your calculation if flow rate of coolant is lower say 8000 liter per hour then we can achieve good chilling temperature, am right?
If yes then if we adjust the coolant flow rate then is there any adverse affect on chiller machine?
Am using glycol as cooling agent.
- Abu dhabi UAE
December 19, 2016
A. Hi Aijazullah. Please spend a paragraph or two explaining your actual situation. Sorry, but there are many arrangements and I am not understanding your description.
It is most common for the chilling system to incorporate two loops with a chilled water reservoir in the middle. In one possible arrangement, the first loop is comprised of the chiller cooling the water/glycol in the chilled water reservoir. The second loop is comprised of the water glycol flowing through cooling coils in the anodizing tank.
The idea here is that you can modulate the water/glycol flow to the anodizing tank for precise temperature control while still allowing the chiller to operate on a reasonable cyclic on-off basis instead of turning on and off every few seconds. Plus, since both loops are open to the atmosphere, no worries about expansion/contraction of the water/glycol.
Regards,
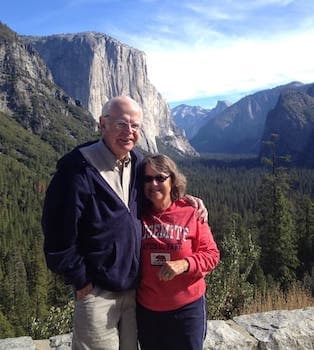
Ted Mooney, P.E. RET
Striving to live Aloha
(Ted is available for instant or longterm help)
finishing.com - Pine Beach, New Jersey
Q. Hi All,
We have to maintain -5 °C temperature for Hard Anodizing bath, For that how much temperature we have to maintain in chiller. And how to calculate heat absorption in Titanium coil, that we are using in anodizing bath.
Thanks & Regards,
- Bangalore, India
April 7, 2021
A. Hi Shankar. The heat exchange formula is
Q = U * A * ΔT
where Q is heat input, U is heat transfer coefficient, A is surface area of the coil, and ΔT is the difference in temperature between the solution in the tank (the outside surface of the coil) and the cooling fluid (the inside surface of the cooling coil). A complication there is that the cooling fluid has two temperatures, the temperature at which it leaves the chiller / enters the coil and the temperature at which it leaves the coil / enters the chiller. You can use the average/median/half-way temperature of the cooling water in your calculation.
But be careful with your units! If you look something up, make sure you stick with either Watts, BTUs or Calories, and square inches, square feet, or square meters, and degrees Fahrenheit or Centigrade throughout your calculation; do a units check. I always worked in BTUs, square feet, and degrees F.
So after you have determined how many BTUs the rectifier is adding to the tank (Q), and you get the U factor for the titanium coil from the manufacturer (titanmf.com implies that you can use 150 for BTU-square feet-degrees F calculations, although that strikes me as very high), you transpose to get
A * ΔT = Q / U
So you divide Q by U and now you have the product of A * ΔT
So if the area of the coil is already fixed, you can calculate the ΔT you must create. Or if the chiller manufacturer gives you the suggested operating temperatures, you can calculate the required coil area. Otherwise you can do the math to pick a reasonable pair of values. Remember that the flow of cooling water must be sufficient to remove Q as well. One final caution: chillers must be "de-rated" for such low temperatures; if you calculate that you need a chiller with "X BTU/hr" capacity, the chiller manufacturer may tell you that the chiller must actually be rated "2X BTU/hr" or so (see Chris Jurey's explanation below)
Some suppliers have on-line worksheets to get you started, for example,
https://www.titanmf.com/immersion-coil-surface-area-calculator-for-anodizing-applications/
Luck & Regards,
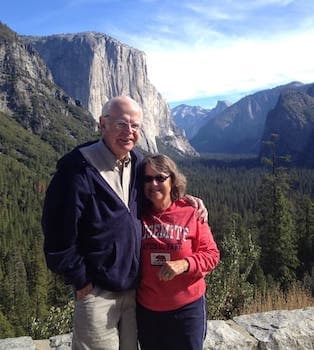
Ted Mooney, P.E. RET
Striving to live Aloha
(Ted is available for instant or longterm help)
finishing.com - Pine Beach, New Jersey
Q. Hi,
I'm interested in installing a Type III (hardcoat) anodizing setup. For that, I've been reading on this forum and many sources through the internet about the characteristics and parameters needed in order to carry on a Type III anodizing.
One of the requirements which has been giving to me most of the headaches is to choose an appropriate chiller. I have read that aquarium chillers with titanium coils (for corrosive purposes) is one of the most common equipment for this task.
But I want to be sure of what chiller must be got in order to reach a desired temperature, given the mass of liquid in the system, and the ambient temperature (and of course, the added temperature by the power supply for a time equivalent to that of the anodizing process).
Most of the sellers specify the COOLING CAPACITY of the chiller (given in Watts {W} or BTU/h).
I've made some calculations for 5 gal of anodizing mix (Sulfuric acid + distilled water), with a initial temperature of 32 °C (including the theoretical added temperature due to the power supply for the total anodizing process), and a desired final temperature of 1 °C.
Then I've found that a chiller of 270 W of cooling capacity would satisfy these needs, although with a waiting time of 2 hours.
Please do not worry for this time, I just want to be sure if the cooling capacity given by the manufacturer is sufficient in order to reach this temperature. I mean, Could I trust only in the given cooling capacity in order to achieve this?
If any of you have experience with Type III anodizing, I would appreciate your advice about getting a chiller, or any other method for such a little setup (just 5 gal, as stated). No matter how little or big is your actual setup, anything would be or help :)
Thanks in advance!
- Dominican Republic
July 24, 2021
A. Hi Pedro. I'm accustomed to hard anodizing tanks 100X bigger and more, and am not familiar with aquarium chillers. Still, I doubt that aquariums operate at 1 °C, so I don't think manufacturers' data will take into account the need for "derating" when operating at such low temperatures.
270 Watts sounds awfully low to me because, not even taking necessary derating into account, at 24 ASF and 50 Volts, you would consume that much wattage on a surface area of just 32 square inches (a piece 4" x 4" x 2 sides), but I can't do a closer reasonableness check until you tell us how much surface area you intend to anodize per load.
I also would not worry about the necessary power to get from 32 °C to 1°C because you have to cool the solution to 1 °C before you start the anodizing, and however long it takes it takes, but yes it looks like about 2 hours.
Luck & Regards,
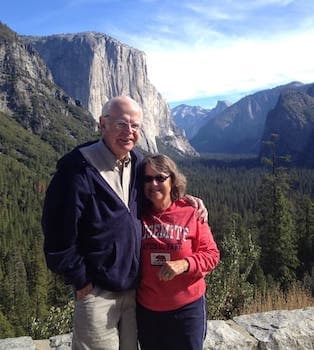
Ted Mooney, P.E. RET
Striving to live Aloha
(Ted is available for instant or longterm help)
finishing.com - Pine Beach, New Jersey
Q. Hi Ted,
First off, thanks for the reply! I'm planning to hard anodize near 1 ft2 of area as much.
Recently (a few hours after posting this thread) I've read somewhere else that a aquarium chiller of 1/4 HP would be enough for 5 gal of acid mix. But I'm not sure if this power unit is comparable with the cooling capacity of the chiller.
For what I've read from manufacturer's specifications, they provide with HP and CAPACITY (in BTU/h), but I don't know how to relate both of these. I'll keep searching for it (but I greatly would appreciate if any of you experienced readers could tell me a bit about).
In any case, what cooling system do you implement for hard anodizing (any chemical pump with refrigerators and whatnot)? Maybe I could get a down-sized equipment based on the techniques you are accustomed to.
Thanks in advance!
Mechatronics Engineer - Dominican Republic
A. Hi. Watts and BTU/hr are both measures of 'power', and readily converted. Multiply your Watts by 3.41 and you've got BTU/hr.
But a problem remains: if you anodize 1 sq. ft. of product at 24 Amps/sq.ft and 40 Volts, that's 960 Watts or 3275 BTU/hour. Further, chillers must be 'derated' perhaps by about 50% as Chris suggests below to work at hardcoat temperatures. That means you need a nameplate rating of about 6550 BTU/hr.
Further confusing the issue is that electric motors produce mechanical power which is measured in horsepower, but 'boiler horsepower/ chiller horsepower' is a different, crazy, measurement system where 1 'boiler horsepower' or 'chiller horsepower' is 33,470 BTU/ hour. So if the chiller is rated 1/4 boiler horsepower (8,370 BTU/hr) it ought to be okay. One final unit sometimes used in refrigeration systems is 'tons of refrigeration'; a ton is 12,000 BTU/hr. Hopefully you now have the conversion factors to be able to convert between Watts, BTUs/hr, boiler horsepower, and tons of refrigeration as necessary.
Luck & Regards,
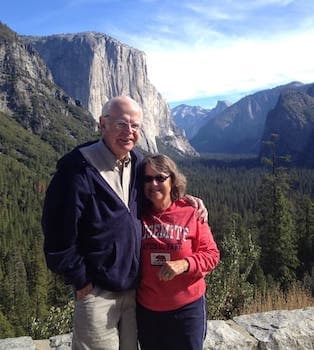
Ted Mooney, P.E. RET
Striving to live Aloha
(Ted is available for instant or longterm help)
finishing.com - Pine Beach, New Jersey
Q. Hi Ted,
Again, thanks for the information provided. Although both units that I said before (HP and BTH/h) are strictly power measurement, the seller provides them as different topics into the machine specs.
For example, for a aquarium chiller, the seller states that it has a compressor of 1/10 HP, and then says that the capacity is about 1270 BTU/h. If you convert 1/10 HP to BTU/h, it gives out 254.44 BTU/h, which are not the same.
Then, you mention the called 'chiller horsepower' which is equivalent to 33,470 BTU/h. In this case, 1/10 chiller HP would be 3,347 BTU/h, but I doubt this measurement unit is NOT the same as the provided by the manufacturer.
Sorry, but my confusion between CAPACITY and HORSEPOWER remains yet.
Take this link, for example:[deleted by editor]
They claim that a chiller is sufficient for the voltage and current they propose.
Finally, this is the example I have taken from. In fact, what matters me the most is to understand how to pick a correct chiller machine.
Sorry for the long statement, but I greatly appreciate your knowledge about the topic.
For general purposes, If you don't mind, what cooling system do you implement for hard anodizing (any chemical pump with refrigerators and whatnot)?
Thanks in advance!
Mechatronics Engineer - Dominican Republic
& Cooling Towers"
by Herbert W. Stanford III
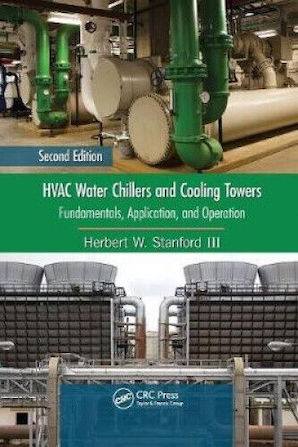
on eBay or Amazon
or AbeBooks
(affil link)
A. Hi again, Pedro. Kilowatts, BTUs/hour, tons of refrigeration, and boiler horsepower are all measures of how much heat a system can add or remove; and you can convert from any one of them to any other one with the conversion factors I mentioned. But it would be very unusual for a small chiller to be rated in 'boiler HP', so I'm confident your vendor is talking about the electrical horsepower of the condenser or recirculation pumps of the chiller.
If you will be purchasing a 30 Amp 30 Volt rectifier, it will be capable of generating 900 Watts of power or 3070 BTU/hr. If you want an aquarium chiller capable of handling the full power of your rectifier it must be capable of removing 3070 BTU/hr at 1 °C / 34 °F (or whatever operating temperature you are going for) -- that's what the chiller supplier must assure you.
There is so little similarity between a large automated hardcoat facility and your 5-gallon startup that it really doesn't make sense to talk about brine storage tanks, 3-way valves to minimize compressor cycling, etc., but topic 2995 "Chilling/cooling of anodising bath Q&A's" discusses that topic, and you can google for "industrial chillers", "industrial packaged chillers", "anodizing chillers" for illustrations and explanations. Another thing that might confuse you is that industrial hard anodizing is done at a current density of 24 or more Amps per square foot (ASF), while hobbyists might be doing their anodizing at as little as 6 ASF.
Luck & Regards,
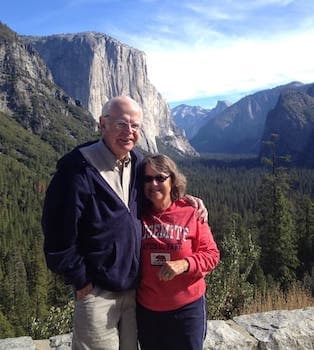
Ted Mooney, P.E. RET
Striving to live Aloha
(Ted is available for instant or longterm help)
finishing.com - Pine Beach, New Jersey
Hi Ted,
Again, I appreciate all of this information. I've messaged many suppliers about some chillers they have in their catalog, if one happens to reach near-freeze temperatures, taking into account the heat introduced by the power supply.
Additionally, thanks for the explanation about the difference between electrical horsepower and boiler HP, and the link you put in your comment. It will be of use in order to set the most secure way for cooling my system.
Best regards :)
Mechatronics Engineer - Dominican Republic
Q, A, or Comment on THIS thread -or- Start a NEW Thread