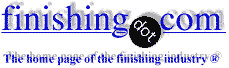
-----
Hardening EN8 & EN9 parts
Please see also --
Q. EN 8 MATERIAL OF DIA 7 MM HARDNESS 190 MAX. Want to achieve hardness to 350-400. Please advise.
SATCHIT BASU- DELHI, India
August 10, 2022
⇩ Related postings, oldest first ⇩
Q. With en9 material can I get hardness of 44-48 hrc on all over the part. If yes, then can you suggest the h/t cycle. Because we are manufacturing one product which has an elliptical broach in middle in which we can't get hardness 44-48 hrc and also we found that our broach dimensions has also get variation after final heat treatment. So can you help for getting hardness 44-48 hrc?
Vishal Sachde- Bhavnagar, India
March 2, 2009
March 6, 2009
A. En9 is a plain unalloyed medium-carbon steel. It therefore requires very severe cooling in the heat treatment cycle in order to get the sort of hardness that you want, and the thickness of the section in turn greatly affects the cooling rate that can be achieved.
Information that you must supply to get further with your query:
1. What section thickness is your component?
2. To what depth below the surface do you want 44-48 HRc?
3. Related to Q2, do you want through-hardening?
4. Do you have a soak-and-water-quench facility?
5. Do you have a flame-hardening facility?
Depending on answers to the above, there might be a heat treatment cycle that will give you what you want on En9, or it might be that you will need to change grade to one that has appropriate alloy content to allow hardening by less severe quenching.
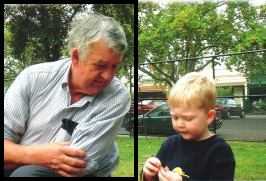
Bill Reynolds [deceased]
consultant metallurgist - Ballarat, Victoria, Australia
We sadly relate the news that Bill passed away on Jan. 29, 2010.
A. Good afternoon:
With limited information provided, it's going to be hard to tell whether 44-48 HRC is possible. Part dimensions, thickness, quenchant, quench agitation, variation of chemistry from heat to heat...these are some of the variables that should be considered.
And since this is a 0.50-0.60 carbon material, if the quench rate is too severe, warpage or quench cracking are possibilities. This might explain the variation in the broach dimension. If these are thin parts, you might be able to austemper or marquench them to reduce warpage.
If you buy steel with a guaranteed hardenability band, you could better predict the heat treat response.
If the part is too thick to achieve adequate as quenched hardness, a change in material may be needed.
Sorry there's no quick answer. Good luck.
- St Louis, Missouri
March 9, 2009
March 12, 2009
A. Obviously it is possible to get hardness 44-49 hrc in en 9, but please specify section thickness?
Please specify whether dwg. requires thru hardening and / or surface hardening?
We are doing similar components; also specify whether dwg. specifies core hardness too?
I would advise more quenching to avoid problem of distortion
Just for sharing, had manufactured EN king pins which were toughened to 25 Rc at core then surface was induction hardened in polymer quenching to give 55 hrc hardness at surface to depth of .5 mm thus achieving strength as well as wear improved surface life.
Regards,
vikas
- Chandigarh, India
Q. In EN9, C45 material Flats and Bars, we could not get the Hardness of our requirement of above 50 HRC as quenched condition in oil quenching.
DEVA RAJANHeat Treatment Manager - COIMBATORE, Tamilnadu, India
October 6, 2011
Q. Our Components fall within following dimensions-
LENGTH- 50 mm to 150 mm
WIDTH- 07 mm to 20 mm
THICKNESS- 0.8 mm to 1.5 mm
MATERIAL USED- EN9
Can anyone please suggest an appropriate Heat Treatment process to achieve an through 40-48 HRC?
- CHENNAI, Tamil Nadu, INDIA
March 10, 2012
A. Yes, apart from my experience 0.75 ~ 1.50 mm thickness EN 9 material can get easily 40 ~ 48 HRC by doing the components at mesh belt hardening furnace which will have not much % of Carbon enrichment and decarb due to continuous hardening. As quench condition the hardness will be 55 ~ 60 HRC then have to temper it 320 ~ 340 °C for one hour. Normally this will not have major distortion issue. Otherwise the same Mesh belt furnace with Austempering (quench at 350 °C) will give 42 ~ 48 HRC and there is no need of further tempering.
DEVARAJ [last name deleted for privacy by Editor]- KARUR, TN, India
January 2, 2013
Q. What is the Maximum Hardenability of EN9 material in Oil quench. Chemical composition are C - 0.55, Si - 0.15, Mn- 0.75, P-0.003, S- 0.005.
DEVARAJAN LAKSHMANAN- COIMBATORE, India
January 4, 2013
Q. Hi sir
I want the details of the EN8 steel hardness and it is used to take a wear test on the austempered ductile iron, and I have hardness of the material of 33 HRC.
student - madurai, tamil nadu, India
May 7, 2014
Q. I am a Commercial heat treater
We received one tube mill roll for heat treatment
The size is 520 mm Dia. X 320 mm
What maximum hardness can I get by Oil Quenching?
metal treatment services - Ahmedabad, Gujarat, INDIA
July 3, 2014
![]() |
Regards, ![]() Ted Mooney, P.E. Striving to live Aloha (Ted can offer longterm or instant help) finishing.com - Pine Beach, New Jersey |
Q. Hi sir,
I want to know the heat treatment procedure of EN-9 Material to get 36- 47 HRC through hardening. actually we are doing hardening with the temp of 820/840 °Cs but we are getting as quench hardness very low (18-20 RC). Kindly give the solution for this.
- Pune, India
April 10, 2016
Q. Material EN9, Hardness required 300 to 350 BHN, size Dia 680 mm thickness 200 mm with bore of 135 mm. Weight is approximately 300 kgs. Please suggest the feasibility of achieving the required hardness and the process parameters.
Vijayendra T R- Bangalore, India
April 17, 2017
How to achieve hardness up to 45-50 HRC on C45?
Q. With C45 material can I get hardness 44-50 HRC by case hardening?
Length is 91 mm. Pin diameter is 25 mm. And two steps are at both end with diameter 12g6. And surface treatment is hard chrome plating. Required case depth is 0.8-1.2 mm.
buyer - Pune, Maharashtra, India
May 8, 2017
A. Hello Rajkumar!
You need to case harden C45 up to 44-50 HRC, I should say you can achieve that hardness without difficulties.
That hardness is the case hardness or the core hardness? If it is the case hardness, is there any specification for core hardness?
If you already solved this, please let us know! Regards,
TEL - N FERRARIS - Cañuelas, Buenos Aires, Argentina
May 17, 2017
![]() |
Thanks! Regards, ![]() Ted Mooney, P.E. RET Striving to live Aloha (Ted can offer longterm or instant help) finishing.com - Pine Beach, New Jersey June 2017 |
Q. Hello,
I would like to know about the volume hardening of En9 to achieve the core hardness of 330-355 BHN. The forged shaft diameter is 45 mm and length is 400 mm with one end disc diameter of 250 mm and length 30 mm. If so, please suggest the H/t cycle.
Lakshmi Machine Works Limited - Coimbatore, Tamilnadu, India
June 17, 2017
Q. We have EN8 material of cylindrical(solid), length= 300 mm, diameter= 60 mm. Our hardening company person promises to harden it at 55C, but there is too much variation in the diameter after hardening. Is it because of continuous hardening more than its capacity? What is the optimum hardness we can expect?
SAURABH KUMAR- Noida, India
October 27, 2017
A. Hi Saurabh!
EN8, in my experience, is not a good material for hardening. In 60 mm thick you need, at least, some boron and chromium in your composition to improve hardening depth.
Hardenability is below 50 HRC for more than 6 mm from the surface, maybe you can get this number higher with brine quenching, but not 30 mm (distance from surface to the center).
Best of luck!
TEL - N FERRARIS - Cañuelas, Buenos Aires, Argentina
November 8, 2017
Q. Hello there, we make pins from 3 mm to 16 mm dia. and 8 mm to 150 mm length, only in EN8D material. We do hardening process with docking and cooling in salted water. Still we get variation in hardening. We want 48-52 hardness. But very few times do we achieve the target. So can anyone help me with the exact formula to get proper hardness?
Minimum size:- 3 dia x 8 length to 60 mm
Maximum size:- 16 dia x 40 length to 100 mm
PLEASE REPLY ME. THANK YOU.
Vijay Engineering works, Ahmedabad. - Ahmedabad, Gujarat, India
March 24, 2018
Q. Hi.
I want to know how to achieve hardening in material EN8D.
We did arc quenching and oil quenching. But it didn't help us.
If anyone knows, kindly help.
Rgds,
Prashant
- Rajkot. India
May 11, 2018
Q. Hi sir,
We are facing same problem re. hardness in EN8 round bar . The surface of the material is reaching 34-35 HRC but at the core of the material is getting 25-26 only. Please suggest how to rectify the problem.
Quality incharge - Coimbatore, Tamilnadu, India
July 19, 2018
Insufficient hardness achieved in heat treating C45 Material
Q. My situation:We have taken C45 grade 4.00 mm thick 70 mm wide material for hardening. Carbon % 0.425 and Mn% 0.66. In last lot used with same heat material hardness achieved 46 to 48 HRC, this month lot achieving hardness 37 to 38 HRC only. What are the probable reasons for non achievement of hardness?
Ashish kekreBuyer - Dombivli, Thane, Maharashtra, INDIA
July 24, 2018
November 4, 2018
A. We can achieve a surface hardness of 52-54 HRC in C45 material by laser hardening. We are sure about it.
ASHOK REDDY- Pune MAHARASHTRA, INDIA
Q. Hi sir, I'm Ghadge Dnyaneshwar.
We are using EN8 For washer, but point-to-point variation in 1 piece (32-44 hrc) at checking 180 direction on job. What is the problem?
KANAL ENTERPRISES - INDORE, MADHYPRADESH INDIA
August 2, 2019
Q. I want to achieve a hardness of 28 to 32 HRC WITH en8 d MATERIAL HAVING CARBON CONTENT 40% TO 45% AND mn TO .6 AND ABOVE buT UNABLE TO GET DESIRED HARDNESS SOMETIMES IT IS AT 18 HRC ,OR 22 HRC OR 38 HRC
CANNOT UNDERSTAND HOW TO MAINTAIN HRC.
- Mumbai, MAHARASHTRA, INDIA
January 17, 2020
Blacksmith's EN9 hammers aren't hardening right
Q. Hello I'm looking for some advice. I'm a blacksmith who is starting to make his own hammers I've opted for EN9. I've forged the heads & quenched them and had mixed results. I started with an oil quench and the end result of this seemed soft, leaving dings in the face when hitting high carbon chisels and such.
So I went for a water quench: the first one was successful, and I ended up with a lovely hard face that didn't dent. The three I made after this all suffered with cracking in the cheeks of the hammer. So I tried water quench with alternating between the face and the pen leaving the cheeks to cool slower, and this left me with what I felt was still too soft.
So my question is: what kind of hardness should I expect to achieve on a EN9 hammer, and are there any hints tips or advice on the heat treating process for hammer-making. Thank you in advance.
Fire Monkey Forge - SPALDING
March 12, 2020
Q. Hi
We are manufacturers of steel shoe shanks using EN9 material.
We always had problems in hardening process and quenching and rusting issues after few weeks.
Kindly give us expert advice to solve our problems.
Thanks
Sardhar
General Manager - Vellore, Tamil Nadu, India
March 15, 2020
March 2020
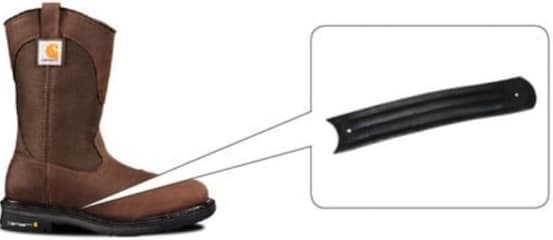
(courtesy of compositetoeboots.org)
A. Hi Sardhar. I'm not knowledgable in heat treatment and can't help you on that, but short of the readers referring you to a technical library, I'm sure it'll have to start with the specifics of your process sequence, not just "had problems in hardening process and quenching and rusting" :-)
Please tell us what you are currently doing for heat treating & quenching. You apply no corrosion preventative of any sort? Are you not allowed to? Thanks!
Regards,
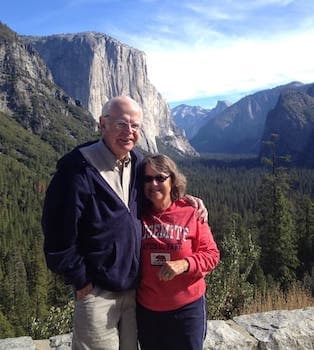
Ted Mooney, P.E. RET
Striving to live Aloha
(Ted can offer longterm or instant help)
finishing.com - Pine Beach, New Jersey
A. Just to answer a couple of questions about EN9 material. This is what we heat treaters call ****. It has very very variable hardnesses from basic hardening and tempering. You would benefit from case hardening the material; however, I don't think this would be great for hammers.
You need to be looking at high carbon steels (0.6% and above) and harden and temper them to a hard and strong condition.
Hope this helps!
- United Kingdom
August 19, 2020
Q. We are facing same problem re. hardness in EN8 round bar. The surface of the material is reaching 34-35 HRC but at the core of the material is getting 25-26 only. Please suggest how to rectify the problem.
Pandi Kattusamy- Chennai Tamilnadu, India
December 21, 2020
A. Hi Pandi. "Same problem" means that Bill Reynold's great legacy on this page should be great help. But please start with the dimensions of the round bar, and what you are presently doing which achieves the hardnesses you are reporting.
EN8 is quite a bit lower in carbon than EN9 so, in my ignorance of heat treatment, I assume that it is less hardenable. Thanks!
Luck & Regards,
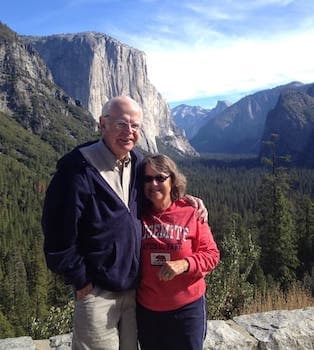
Ted Mooney, P.E. RET
Striving to live Aloha
(Ted can offer longterm or instant help)
finishing.com - Pine Beach, New Jersey
December 2020
February 18, 2021
Q. Sir I need your help to know the achievable hardness in material en8d having carbon 0.40-0.41 and manganese of 0.60 %
I need to achieve 56-60 HRC in induction hardening
But we are not getting more than 48-52 hrc
Please suggest is it achievable or not
Or which material we have to select in carbon steel to achieve above HRC
Regards,
Ashish
- Ludhiana/ Punjab/ India
⇦ Tip: Readers want to learn from your situation;
so some readers skip abstract questions.
Q. Is there any data sheet for different material with this hardness range?
bhavesh domadiyaSr R&D Engineer - ahmedabad, India
June 21, 2021
⇦ Tip: Readers want to learn from your situation;
so some readers skip abstract questions.
Q. C45 MATERIAL GETS MORE VARIATIONS IN WATER QUENCHING -- HOW TO ARREST IT?
Mani vannan- Hyderabad, India
December 12, 2021
Q. Hi sir, I'm THAVAMANI from Metz heat treatment services plant. My customer given to EN8D material hardness required 27 to 32 HRC (core and surface) both same specification. How to archived this requirement please give me suggestion.
THAVAA THAVAMANI. MANIHeat treatment services plant employee - Coimbatore, India
April 1, 2022
Q, A, or Comment on THIS thread -or- Start a NEW Thread