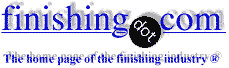
-----
Zinc boat anodes not working!
Q. Can anyone help? I have a 48' steel yacht which has the underwater sections coated in a 'water-based inorganic passivated zinc coating'. The manufacturer of the zinc product (META of Lyons, France) maintains that it needs no overcoating and no anti-fouling apart from overcoating with the zinc coating each year. I am concerned about rusting and the effects of stray electrical currents in the water. The boat is fitted with 22 zinc anodes, but why won't the zinc coating sacrifice? Should I go against the manufacturer's recommendations and overcoat the zinc with epoxy? (The manufacturer will not help). Can anyone recommend an overcoating treatment?
Dr. P. ClarkUniversity of East London - London, England
2000
A. Right, first statement - I'm not sure what the coating you've got on your boat is, Or how this will behave on boats. But, passivated zinc is much more reluctant to corrode than plain zinc. I've seen a study where passivated zinc displayed "white rust", the build up of zinc corrosion products took 20 times as long to occur, and the time to "red rust" where the underlying steel corroded, took twice as long to occur. This was a salt fog spray test, some what different to your situation, and the passivation was a chromate, what yours is - I don't know. The effects of differing aeration will be very strong with a boat. Simply the medium the zinc is in effects is corrosion potential, the area well below the water line will have a lower oxygen level in the water, compared to the area at the water line, where the oxygen level will be at a max', it's corrosion potential will also be higher, thus the water line zinc would corrode to protect the below water line zinc. I don't know enough about boats to say you've got enough zinc anodes, or that their distribution will be correct, but your manufacturer probably does. Does anyone out there actually experienced in this field?
Ian Brookeuniversity - Glasgow, Scotland
A. Dr. Clark,
By now you have already found the answer to this but just in case.... The passified zinc coating. I know when a zinc anode passifies that it no longer works or burns. I remove them and install new ones when that happens. Generally zinc anodes are not pure zinc, but have other trace elements in them such as cadmium. Anyway, the cadmium in zinc anodes keeps it burning clean, and when you wipe off the anode with your hand it reveals bright shinny metal.
On your steel hulled vessel with 44 anodes, which to me would seem adequately protected through sheer number, the anodes would protect the passivated zinc coating on your hull from deterioration. I believe that this is your question.
There is a meter you can buy that you can ground to your hull and measure the potential of the vessel to find out if in fact it is adequately protected. You drop the other end in the water which is a silver/silver chloride cell. I believe if you read 850 millivolts or above, that you are adequately protected. Too high and you will blister off coatings.
I will take the liberty here to assume that you worry to darn much, so you will probably need to buy one of these meters. You can also buy a reference electrode that can be attached to your hull permanently that has a readout in the boat. That is what you really need.
On the other hand, if you haul your boat out and see orange spots, or can see orange spots in the water, your hull is rusting and you are not adequately protected.
I have a 50 foot steel hull and have about 10 or twelve anodes installed, have had no problems.
As for the anti-fouling capability of your coating, I have serious reservations for anything that does not contain cuprous oxide. Preferably tributyltin-cuprous mix, except you cannot get the good stuff anymore.
As for overcoating, any good underwater metal epoxy should do, read the can. Regards, Dave
david walkercoast diving service - san pedro, California
A. Doctor Clark,
Regarding the lack of corrosion on your boat-hull, it is for two main reasons. Firstly, you have a great deal of protection from the anodes you have fitted. Most boat owners who have zinc-coated hulls usually only fit anodes on the stern around the propshaft/rudder areas due to dissimilar metals.
Certainly Secondly, certain zincs will absorb magnesium from the water in the North Sea and form a 'barrier' layer which passivates the zinc to a high degree. Once the anodes have worn away, as per your reply from a another devotee of this site, the zinc will indeed start to go quicker. The 'mapping' of your hull by placing an electrode in the water and walking the length of you vessel and taking resistance readings on the steel work is also excellent advice you have been given. This exposes any weak areas which are prone to early corrosion.
Being a chemist, I have been involved in the coating of marine vessels with zinc for many years and have been through many of the scenarios which can be encountered. The ideal system on top of a zinc-silicate is an epoxy MIO primer (micaceous iron oxide: small overlapping leaves of metal/aluminium contained within an epoxy medium to greatly retard the migration of water vapor to the surface of the steel) and a coat of anti-fouling paint. Most cuprous and trybutyltin coatings have been banned in many countries. In some cases the copper-based anti-foulings have reacted with the primer and/or the metal itself.
Rick Simpson- Irvine, Scotland
2002
!! Hi, "the good stuff", tributyl tin, is strongly discouraged by the Rotterdam Convention, and internationally banned by the International Maritime Organization because it is both highly persistent and bio-accumulative, with profound impacts in the unbelievably low parts per billion range. Whether we wish we knew then what we know now, or whether we wish we didn't know now what we didn't know then, the fact is now we know: it's horrendous stuff; don't even think about it.
More on tributyl tin:
Regards,
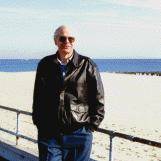
Ted Mooney, P.E.
Striving to live Aloha
(Ted is available for instant or longterm help)
finishing.com - Pine Beach, New Jersey
Many thanks to those that have replied to my earlier query. I have not been able to respond earlier because I have been out to the yacht which is currently in Spain. I can now report that there is no rust - good news, but now there is no zinc either - bad news!
Now overcoating the organic zinc silicate is a must, but what do I use. One kind guy recommends an MIO [micaceous iron oxide] epoxy primer. Any ideas where I can obtain this in the UK?
Dr P Clark [returning]- London, U.K.
2002
A. Hi Dr. Clark.
You can obtain a good MIO epoxy from companies like MG Duff International, Jotun Paints, International Paints, Leighs Paint, Sigma Paints, etc.
- Spalding, Licolnshire, U.K.
February 20, 2011
Multiple threads merged: please forgive chronology errors and repetition 🙂
Q. Dear sir/madam
I need sacrificial zinc anode for tank protection, but my zincs have 300 ppm lead impurity. What is it's effect on capacity or other property? How do I decrease lead in zinc, or add other metals to remove its effect?
Behnam T [last name deleted for privacy by Editor]- Tehran, Iran
2001
A. There are several companies in the USA that will custom make metals/metal alloys to your specifications, and I'm sure its the same overseas.
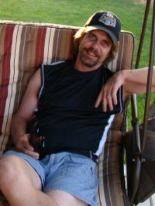
Marc Green
anodizer - Boise, Idaho
A. If you're looking to make your own anodes, beware of not only lead as an impurity, but other metals such as iron that will detract from the current output of the zinc anode. The military specification MIL-A-18001K allows for a maximum of .006% lead , and .005% iron content. With the higher levels of these impurities, the anode will become less efficient and may passivate depending on the amount of impurities in the anode. When cathodic protection is achieved with anodes, the protection is created by galvanic corrosion from one metal to another by a natural low voltage circuit. If this system is interrupted in either the short term, or the long term, your cathode (or structure) will receive the electrical current damage. A helpful website may be www.harboranodes.com
Wayne Alexander- Auburn, Washington
2004
Q. The previous posting was a well thought out common sense approach that I would like to ask a question about.
If the bonding point of the anode deteriorates would this cause the same type of "electrical damage" that is described in the response.
Is "electrical damage" referring to the passivating or neutralizing of the anodic surface?
Thank you in advance for any help that is offered.
Telecom Equipment Manufacturer - Shawnee, Kansas
2007
Won't a galvanized skeg become a sacrificial skeg?
Q. I have just had a new skeg fabricated out of steel for my 24 ft Eventide Sailing boat. The skeg is roughly 7 ft by 2 ft so quite a lump of metal.
I have been encouraged to have this galvanised.
Bearing in mind the fact that the keel is iron, the prop is bronze and the prop shaft is stainless steel, one would obviously fit sacrificial anodes before launching.
My own thinking is that the sacrificial anodes are made of "similar" material to the galvanising plating and - therefore all my galvanised metalwork - under water - would just become another large sacrificial anode.
I would prefer to prime the skeg with a "keel primer".
What is your view on this?
Thanks
Graham Paris- Colchester, Essex, UK
2001
A. The zinc galvanizing itself, not the whole zinc galvanized steel item, is what would become an anode in this situation. Because the coating is thin, if it remained unpainted it would not last long. But if it is galvanized and then painted, the galvanizing is not much exposed, and the coating will offer good protection because the steel under a scratch in the paint will be protected. But the galvanizing can't offer cathodic protection to the rest of the boat because it can't corrode.
So, galvanizing might be a fine pretreatment under paint, if done right, but it's utility as a sacrificial anode is probably pretty marginal.
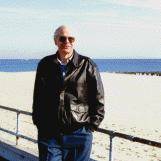
Ted Mooney, P.E.
Striving to live Aloha
(Ted is available for instant or longterm help)
finishing.com - Pine Beach, New Jersey
Multiple threads merged: please forgive chronology errors and repetition 🙂
Q. Is there any other way to prevent Boat Electrolysis besides zinc? And Zinc will only slow down the process -- is there any way to stop it all together?
Bill Jackson- Fort Myers, Florida, United States
2002
A. I believe Magnesium is even more susceptible to galvanic corrosion than Zinc, so that might slow the process more (or the Magnesium bars might just get eaten up faster).
Jim GorsichCompton, California, USA
A. I can't speak for the efficacy of any particular "impressed current system", and presumably it's possible to install them wrong. But the theory is sound--I believe they can stop electrolysis completely.
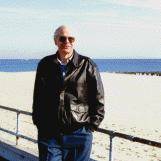
Ted Mooney, P.E.
Striving to live Aloha
(Ted is available for instant or longterm help)
finishing.com - Pine Beach, New Jersey
Need quote
RFQ: I WORK AT A STRUCTURAL STEEL COMPANY, I AM THE PURCHASING AGENT. ONE OF MY ESTIMATORS REQUESTED I GET A PRICE ON ZINC ANODES, THE SPECS STATE THAT IT SHOULD BE 2" X 2" X 48" LONG, AND WEIGH 50 LBS. EACH, QTY REQUIRED 100 pieces.
THANK YOU,
LAURIE K [last name deleted for privacy by Editor]Tampa, Florida
2003
Ed. note: This RFQ is outdated, but technical replies are welcome, and readers are encouraged to post their own RFQs. But no public commercial suggestions please ( huh? why?).
Does Dutch canal boat require zinc anodes for saltwater use?
Q. I have a Dutch canal boat that is made of steel. I am thinking of taking it from fresh water into salt water and I am wondering if I will need to install sacrificial zincs to the shafts below water? What is the policy regarding zinc anodes on steel-hulled vessels?
Paul M [last name deleted for privacy by Editor]- Alameda, California, USA
2003
A. Hi Paul. Regardless of how well painted, a steel hull vessel in salt water will profit greatly from zinc anodes.
Regards,
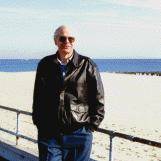
Ted Mooney, P.E.
Striving to live Aloha
(Ted is available for instant or longterm help)
finishing.com - Pine Beach, New Jersey
Galvanic corrosion of boat engine
Q. Hi all,
I have just built a heat exchanger for a fresh water cooled pleasure craft. This serves as a cooler for a car type V6 engine which has cast aluminium components and a cast steel block. The heat exchanger is made from copper. The exchanger does not touch the engine physically, and the only commonality they share is the fresh water passing through both. I am not sure whether this scenario has all the right qualities to cause galvanic corrosion or electrolytic corrosion. I was considering placing an anode inside the cooling system in contact with the aluminium components just incase.
Eternally grateful for your thoughts.
hobbyist - Perth, Western Australia, Australia
2004
A. The 'right qualities' needed for galvanic corrosion include a metallic current path as well as the liquid current path, so the copper exchanger cannot cause galvanic corrosion. The cast aluminum components will be anodic to the cast steel block though. Consequently, an anode could be beneficial. I understand that anodes must be magnesium rather than zinc to be useful with fresh water.
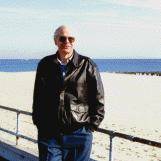
Ted Mooney, P.E.
Striving to live Aloha
(Ted is available for instant or longterm help)
finishing.com - Pine Beach, New Jersey
A. Anytime we have dissimilar metals and water we have set the stage for galvanic action to occur. Most all marine shops should be able to get zinc 'sticks' for you, these sticks can be found in various shapes and sizes, commonly used in the cooling system as a
'sacrificial metal' to help control electrolysis.
Replace a fitting or two in you plumbing with a similar fitting that also has a smaller hole for a 3/4 inch pipe plug, use the zinc stick that comes with a 3/4 pipe plug on one end. Buy spares, you can screw them on/off the special pipe plug.
Depending on the hours of service you will figure out the service life of the size sticks that you are using. Visual inspection alone is not enough, zinc can 'honeycomb', always tap the zinc to ensure it is still solid. Replace the stick if more than 50% used.
Do this on BOTH the fresh-water system and on the raw-water system. Preferably 2 places in each system.
I have further slowed the galvanic process on raw salt water plumbing by linking the pipes across the hoses with stainless cable and hose clamps, making a direct metal to metal path bridging the pipe gap formed by any hose.
- Wright City, Missouri, USA
Q. I have a 48' steel boat and was wondering if it is possible to overcompensate with the number of zinc anodes. Can it do any harm, apart from slow me down with all the bumps along the hull?
Paul FieldBoating Enthusiast - Sydney, Australia
2005
A. Hi Paul. I don't think it can possibly have any adverse galvanic effect.
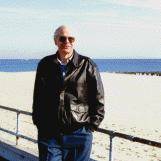
Ted Mooney, P.E.
Striving to live Aloha
(Ted is available for instant or longterm help)
finishing.com - Pine Beach, New Jersey
Q. I have a flat bottomed steel riverboat boat in freshwater & use magnesium anodes for sacrificial protection. I put some extra anodes on the baseplate of the boat because if mounted on the vertical sides they would quickly get knocked off. However someone has told me that galvanic action (including protection) can only work on line-of-sight and not around corners. Is this true?
Michael BoninI live on my boat - London UK
2006
No, it's not quite true, Michael, but anodes have to fairly close enough to the metal they are protecting because glavanic current needs to flow from one to the other through the water.
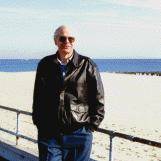
Ted Mooney, P.E.
Striving to live Aloha
(Ted is available for instant or longterm help)
finishing.com - Pine Beach, New Jersey
![]() |
It is the conductivity, I believe your protector to be as nearer as possible to corroded area. ![]() Khair Shishani aircraft maintenance - Al Ain, UAE So the anodic/cathodic potential difference is still in effect and the sides of the boat will be protected, even though the anodes are positioned on the bottom around a 90 degree corner and not within line-of-sight? MICHAEL BONIN- London, UK 2006 |
Cair is correct that you'd always like anodes as close as practical to the areas of concern (and several anodes if possible). But line-of-sight has little to do with it (as far as I know -- just an opinion, and not from a marine surveyor).
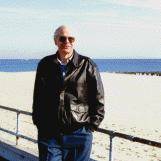
Ted Mooney, P.E.
Striving to live Aloha
(Ted is available for instant or longterm help)
finishing.com - Pine Beach, New Jersey
I found some line-of-sight references on the internet in relation to electroplating which also uses a galvanic/electrolysis process:
http://www.enthone.com/resources_detail.aspx?Page=characc.ascx ⇩
However, it also talked about line-of-sight dependent and non-dependent processes but I'm not sure which anodic protection of steel is?
- London, UK
Ed. update: The above link is broken. Thankfully, the Internet Archive preserved a copy here
Please consider a donation to The Internet Archive. Don't follow abandoned links, old URLs are sought out by hackers!
Q. I am the Boating Officer for a Research Station. We have a fleet of 8 boats, four of which are 5 meter aluminium RIB type dinghies. We have had the same anodes on their sterns for 2 years now and apart from some fouling from sea growth (which we grind off) they don't appear to be degrading. Two of the vessels have quite severe corrosion on the deck to hull weld joints, with the standard white powder and parts of the floor delaminating and lifting. The boats are powered by 30 HP outboards and have no batteries or wiring so we have eliminated stray current corrosion. The boats are connected to a mooring line via aluminium hooks at the stern and a stainless steel clip at the bow. Could this be causing some sort of galvanic corrosion? Any thoughts?!
Cheers
Skipper - Orpheus Island, Queensland, Australia
February 16, 2009
A. It is not really a wonder that your zinc anodes are not degrading as they are the more noble metal than the aluminium your boat is made from. This means your aluminium will corrode to protect your zinc . You should use magnesium anodes for aluminium, Zinc can used to protect steel.
Marcus Hahn- Lucerne, Switzerland
A. Must disagree with you, Marcus.
Contrary to your statement, zinc is in fact anodic to aluminium and provides protection in salt water.
In fresh water, the surface of the zinc doesn't remain clean enough and magnesium is needed to protect aluminium. But in salt water, zinc is the standard protection for aluminium.
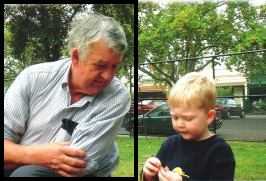
Bill Reynolds [deceased]
consultant metallurgist - Ballarat, Victoria, Australia
We sadly relate the news that Bill passed away on Jan. 29, 2010.
A. Hi. Bill is right; aluminum vs. zinc is one of those funny galvanic relationships ...
Although the first step in electroplating onto aluminum is almost always an immersion into "zincate", wherein the aluminum dissolves and the zinc plates out onto it, i.e., the aluminum is sacrificial to the zinc ... in more dilute solutions, i.e., the "sea water series", zinc is sacrificial to aluminum.
I always had zinc anodes on my aluminum engines (salt water boats) and they worked fine. Maybe you are expecting anodes on the outside of the boat to protect the inside of the boat when there is no continuous fluid path between the two. Or maybe proper electrical contact is not being maintained between the aluminum and the zinc for some reason. For sacrificial anodes to protect a given area of metal, you must have both a conductive fluid path and a conductive metal path between the two.
Good luck.
Regards,
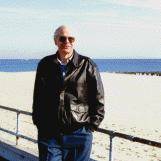
Ted Mooney, P.E.
Striving to live Aloha
(Ted is available for instant or longterm help)
finishing.com - Pine Beach, New Jersey
Q. Good day! I have a brief question which I hope you can help provide an answer to. I am involved in shipbuilding and we place several hundred zinc anodes within the tanks of our vessels. One of the recurring problems with these large anodes that are installed during early construction it the fact that the anodes crack for one reason or another and are therefore needed to be replaced. My question: Is there an epoxy or wrap which can be used to fill these cracks in order to save us from the process of having to install a brand new zinc anode?
Appreciate your help!
- San Diego, California, USA
November 5, 2013
Q, A, or Comment on THIS thread -or- Start a NEW Thread