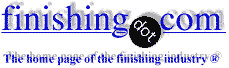
-----
Chromate passivation to keep brass looking natural
⇦ Tip: Readers want to learn from your situation;
so some readers skip abstract questions.
Q. Hi how do I strip chromic brass passivation from brass components?
PikesEmployee - Cape Town
July 25, 2024
Tip: This forum was created to help build camaraderie through sharing tips, opinions, pics & personalities.
The operator & those readers who want that might not engage with anonymous posters.
A. Hi.
Mechanical polishing is probably best if not impractical for some reason.
Luck & Regards,
Ted Mooney, P.E. RET
Striving to live Aloha
(Ted can offer longterm or instant help)
finishing.com - Pine Beach, New Jersey
⇩ Related postings, oldest first ⇩
Q. I manufacture a brass morse key for use in ham radio. At the moment I leave the brass natural and uncoated but after a year or so of handling the brass becomes tarnished and discoloured. I would like to keep the brass looking natural so nickel and other types of plating are out. Lacquering also causes problems because of the very fine threaded screws used; the smallest amount of lacquer prevents the screws from going in.
I have been reading some information about chromate passivation and have contacted several local plating company's for more information but sadly they don't seam to be able to offer any advice. Would chromate passivation leave the brass looking natural and give me the protection I need from sweaty fingers? Also would it be possible to setup the process in-house?
Robert KentBuyer - Eriskirch, Germany
October 4, 2008
A. It will help, but it will not eliminate the problem. Consider having the unit titanium nitride (TiN) coated. The stuff that they put on the gold colored drill bits. They can plug the holes so they will not fill up.
James Watts- Navarre, Florida
A. Passivating the brass with a hex chrome type material will prolong the time until the brass discolors (oxidizes) but it will be a variable based upon the conditions of exposure. Sweaty hands are a difficult area to estimate since each individual has a somewhat different chemistry to the sweat - some being more corrosive than others.
Some trivalent passivations have been formulated for this use. The same caveats would apply.
Since you would be using potentially hazardous chemicals, the process should be performed by those who are experienced in the use, storage and disposal of chemical products.
process supplier - Great Neck, New York
A. Your object looks like ideal base for old shellac based golden yellow dyed lacquers. In old German books you can find many recipes for that process (G. Buchners book on metal colouring / Berlin 1922; good new book is Werkstattrezepte by H.Hilpke). Old clocks and microscopes are some examples of that finish. Hope it helps and good luck!
Goran Budija- Cerovski vrh Croatia
Thank you for all the information and advice.
We have now tried titanium nitride (TiN) coating, the coating is very thin so no problems with threads and holes. The steel parts look great but it didn't look very good on the brass parts, they came out a very deep uneven yellow.
Shellac, we have tried this in the past but you can't coat the threads and it scratched easily. We have also tried some modern clear lacqers but it is time consuming masking all the threads and holes because again you can't coat the threads.
Trivalent passivation sounds interesting and we will take a look at this over the next few weeks.
Thanks again for all the comments.
- Eriskirch, Germany
December 16, 2010
A. Hi Robert
Nickel plating the brass before TiN would probably offer the right color, but it's starting to both get elaborate and get further from genuine brass :-)
Luck & Regards,
Ted Mooney, P.E.
Striving to live Aloha
(Ted can offer longterm or instant help)
finishing.com - Pine Beach, New Jersey
Q. Hello I am hoping some of you can help. We have a brass part that calls for an Iridite #7 finish. The print for this part was drawn in 1981. I can't seem to find any place that does Iridite #7. Not even sure it exists anymore.
Wanted to find out what finishes are available for brass that would have very minimal dimensional change.
The type of brass in question is 360 brass.
I have contacted several plating places and they all seem to say "We don't do any finishing on brass" I am not sure why.
Just looking for some ideas on what type of finishes can be done on 360 brass. Something similar to a chromate conversion. Thought about Nickel but that causes too much of a dimensional change. Looking for something like maybe a bright dip with some kind of post seal to help prevent tarnish.
Thanks in advance. I would really like to find places that can do the process.
Machinist - Ontario, California USA
August 1, 2018
Ed. note: This RFQ is outdated, but technical replies are welcome, and readers are encouraged to post their own RFQs. But no public commercial suggestions please ( huh? why?).
A. Hi Chris. Iridite #7 was or is a Macdermid offering, so you could inquire of them about its status and the names of shops offering it.
Brass parts can probably be bright dipped in a proprietary mix of sulfuric acid and hydrogen peroxide, and kept bright with sodium benzotriazole or a chromate conversion coating. If there is enough tolerance, following the benzotriazole with a brass lacquer sounds good.
Regards,
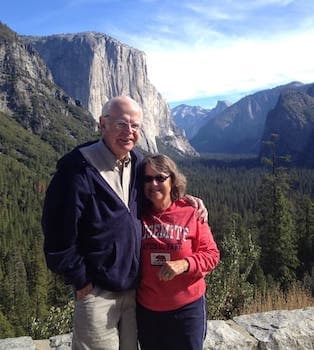
Ted Mooney, P.E. RET
Striving to live Aloha
(Ted can offer longterm or instant help)
finishing.com - Pine Beach, New Jersey
Q. Thanks Ted,
You mentioned Chromate Conversion? Do you happen to know what type of Chromate conversion? Everywhere I look, when I find chromate conversion, I can't seem to find anything for brass. Just asking so I have a specific keyword to search for or ask companies over e-mails or phone call.
Thanks again.
Ogaz Enterprises, Inc. - Ontario, California USA
A. Hi Chris. Herewith a 5¢ tour of chromate conversion coating:
Many metals from aluminum, through brass, cadmium, copper, electroless nickel, and on through zinc may employ chromate conversion coatings to deter corrosion. Like with most other metal finishing processes, research regarding exact formulation and additives can be beneficial, so major suppliers did such research and they market their formulations as proprietaries: Iridite is Macdermid's tradename for their chromate conversion products, Alodine is Henkel's, Chromicoat is Chemetall's for example.
The thing is, a formulation tailored for aluminum doesn't work as well on brass or zinc, and sometimes you want a clear finish and in other cases a yellow or black, so each vendor has a number of formulations. Whether Macdermid still has an Iridite #7 or some other product optimized for brass, I wouldn't know. And that still leaves you looking for a shop who offers it. So I'd start with those suppliers and ask them what shop offers brass treatment with their chemistry.
A further issue is that because of concern over 'hexavalent chromium' those older finishes may not conform to European RoHS requirements, automotive standards, etc., so you may want the coating limited to trivalent chromate.
It is possible to 'home brew' chromate conversion chemistry, and I believe it's sometimes done in India and some other countries but rarely in the U.S. And, since RoHS days, home brew is far more difficult because the trivalent replacement chemistries are more sophisticated than the older hexavalent formulations.
So you probably should determine whether you want to use hexavalent or trivalent chromates; then contact those process suppliers to find a shop which can do it on your brass parts.
Regards,
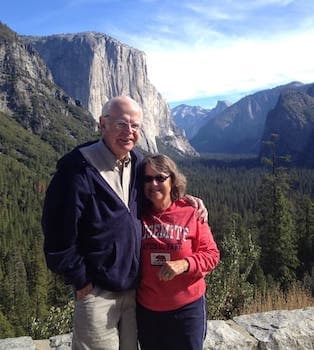
Ted Mooney, P.E. RET
Striving to live Aloha
(Ted can offer longterm or instant help)
finishing.com - Pine Beach, New Jersey
Q. I am currently trying to passivate brass parts that will be sent near a salt environment. The only formulas I can find are patents that require purchase or using an outside company. Does anyone have a decent formulation for passivating brass? I have read about a combination of citric acid ⇦ on eBay or Amazon [affil link] and hex chrome.
Luke Barth- San Antonio, Texas
March 21, 2022
by Biestek & Weber
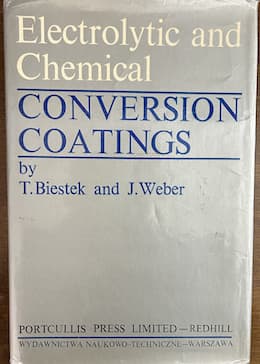
on AbeBooks
or Amazon
(affil link)
A. Hi Luke. If we were speaking of stainless steel parts, "passivation" would have a very well defined meaning, accepted in formal specifications and referred to in tables of electrochemical potential. But for other materials like brass, 'passivate' is slang with no formal, accepted meaning. So one reader may not envision the same need as another.
If you are trying to maintain a bright shiny surface on brass near a salt environment without a lacquer or clearcoat I think you'll find it hopeless. The closest you can get is probably treating the brass with sodium benzotriazole ⇦ on eBay or Amazon [affil link] preservative, then applying a 2-component automotive clearcoat -- but whether it will last a few weeks or a few years will depend on the environment.
I am not familiar with chromates that contain citric acid , but maybe another reader is. Most generic ones, I believe, are based on about 180 g/l chromic acid and about 50 g/l sulfuric acid, with additives including perhaps a fluorine compound.
However, Biestek & Weber quotes a study showing that chromate solutions will not form on brass without halides present and seems to believe that the best solution is 180 g/l chromic acid, 10 g/l sodium chloride, 50 g/l sodium sulphate, and 6 ml/l conc. sulfuric acid.
Please remember that hex chrome is not RoHS compatible and the whole world is trying to get away from its use.
Luck & Regards,
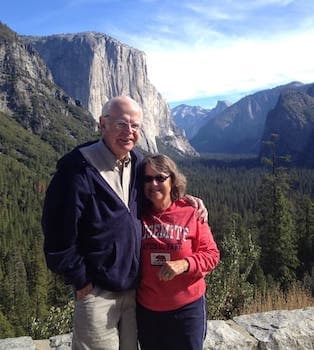
Ted Mooney, P.E. RET
Striving to live Aloha
(Ted can offer longterm or instant help)
finishing.com - Pine Beach, New Jersey
Q, A, or Comment on THIS thread -or- Start a NEW Thread