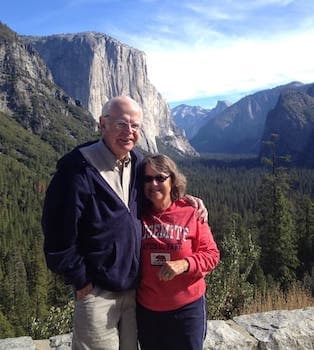
Curated with aloha by
Ted Mooney, P.E. RET
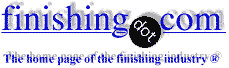
The authoritative public forum
for Metal Finishing 1989-2025
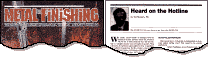
-----
Salt Spray Hours vs. real life exposure
Quickstart:
"Salt Spray" testing refers to various corrosion-resistance tests designed by standards organizations like ASTM and ISO, where sample parts are exposed to fogs or coatings of specific salt concentration, sometimes with additional corrosion-enhancing materials, to accelerate the corrosion to try to determine their corrosion resistance more quickly than in a natural environment.
The components must survive some specific number of hours of exposure like 96, 192, 1000, etc. without excessive corrosion as defined by the coating specification.
While such tests can be useful towards determining whether components have been coated properly or improperly, a typical misunderstanding is that salt spray test hours can be extrapolated to compare the corrosion resistance of one finish to another, or predict real life corrosion resistance in the general case.
[editor appended this entry to this thread which already addresses it in lieu of spawning a duplicative thread]
Q. Hi,
Hope you are having a good day.
We want to understand what is the correlation between SST testing hours and actual hours on the product during the product life?
How SST testing duration of 144 hours is established for automotive components with 5-8 micron coating?
Answering any of the above questions is helpful for us.
Thanks in advance.
- Bengaluru Karnataka
May 2, 2024
by Gustavo Cragnolino (ASTM)
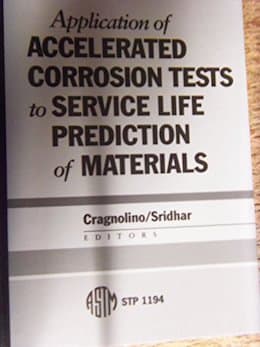
on AbeBooks
or Amazon
(affil links)
A. Hi Karthik.
This question has been asked hundreds of times on this site and the short answer is that the only real correlation is when discussing an individual finish on a specific substrate in a particular situation. For example, automotive manufacturers have decided that 5 microns for some components, 8 microns for others (zinc for some cases, zinc alloys for other cases) will meet their corrosion protection goals if properly done. Then they prescribe salt spray tests as the method to determine whether the coating was properly done. Plating shops will hopefully find that when they do the plating properly they pass the prescribed salt spray tests, but if something starts going South in their process, the salt spray test hours start deteriorating.
The salt spray test is an accelerated QA test, functioning on the hope that if the processing sequence degenerates in some fashion, the salt spray test will quickly catch it. On a case by case basis for one particular coating on one particular substrate a useful correlation between salt spray hours and real life sometimes exists.
Luck & Regards,
Ted Mooney, P.E. RET
Striving to live Aloha
finishing.com - Pine Beach, New Jersey
Q. Has anyone had real life experience with Anodized Al in C4/C5 categories.
How would one compare lifespans vs HDG, and would Anodised Al make a 10-20 year design life quideline?
- JHB
March 11, 2025
A. Hi Devlan. Some OEM automobile bumpers were made of bright-dipped anodized aluminum in the 1980s, which is surely C4 and probably C5. Scholar.google.com offers abstracts of many articles on the subject. Some aluminum truck bumpers are apparently still available. Some automobile trim was also anodized aluminum.
Although we must admire the yeoman effort put into ISO 12944, even it simplifies environments and corrosion tremendously. Aluminum automobile wheels for example, although clear coated rather than anodized, seem to hold up well in the same corrosion category as long as the brake dust is frequently and meticulously removed, but they pit quickly if not.
Anodized aluminum can probably perform to C4 or C5 as long as the pH is neutral but it is attacked by both acid and alkali and any exposure to more noble metals, which is virtually all of them 🙂
Luck & Regards,
Ted Mooney, P.E. RET
Striving to live Aloha
finishing.com - Pine Beach, New Jersey
⇩ Related postings, oldest first ⇩
Q. I'm seeking information on how the real life corrosion resistance relates to salt spray test time.
The products I am dealing with are mechanical fasteners (i.e. bolts). For example, if a zinc chromate plated bolt will not exhibit red rust in a salt spray cabinet for 72 hours, how long can it be expected to last in real life service in different environments? I understand that there will be great differences in performance for areas such as California vs. Indiana vs. Georgia, but are there any published data giving average plating life performance for any of these areas?
Ron TomalloLake Erie Screw Corporation - Cleveland, Ohio, USA
2001
A. Salt spray does not correlate to real life. Neither does any other corrosion test. In fact, corrosion tests do not correlate to each other. It's not a pleasant fact, but that's how it is. People have studied this and tried to make it work, but as of yet, there is no exact correlation. The standard procedure is to set a number of hours your part should resist salt spray exposure before white and/or red rust, and use this as a pass/fail criteria. The test then can do an ok job in weeding out bad parts.
You will need to draw upon past experience to know how long your parts will last in real life service. If you want better real life corrosion resistance, then you can use a stronger finish and/or raise your salt spray hours, but there is no direct correlation. The problem with corrosion testing is that one is trying to replicate a chemical reaction that takes years. A rusting process that takes a month instead of years is not the same reaction. You can get good data, but it will never exactly get the same result as you will in the real world. Don't you love chemistry?
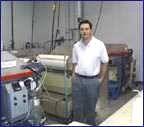
Tim Neveau
Rochester Hills, Michigan
Multiple threads merged: please forgive chronology errors and repetition 🙂
Q. I am trying to find out if there is a correlation between the amount of time a part lasts in a salt spray cabinet has any relevance to the amount of time a part will last in the real world. A rough rule of thumb would even be helpful.
Thanks.
Dan S [last name deleted for privacy by Editor]- Tualatin, Oregon, USA
2001
A. Dan - This is by far the most popular question asked regarding salt spray testing. The test is a process control tool. Meaning--if a part, when properly cleaned, pretreated, painted, etc, lasts 1000 hours in salt spray, if it does not, it is an indicator to check the process line. There is no correlation between the number of hours in salt spray and years in the "real world". Refer to the latest ASTM B117 for more info.
Cynthia L. Meade- Sylvania, Ohio, USA
A. Dan,
I echo Cynthia's comments. There is no correlation between salt spray and real life. In addition, different corrosion tests do not correlate to each other. To determine engineering specifications, I suggest using historical requirements and make increases or decreases from there.
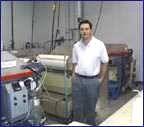
Tim Neveau
Rochester Hills, Michigan
Multiple threads merged: please forgive chronology errors and repetition 🙂
Q. What do salt spray hours represent in days? In an hour a week, month, year? Please advise.
Craig Schmuckerdistribution - Carrollton, Texas
2001
A. This is an often-asked question. The answer is that salt spray does not correlate to anything. Other corrosion tests do not correlate to real life or each other. Many have tried to study this and make a correlation, but nobody has done it yet. The problem is that the actual chemical reactions that make rust take years to occur. If you rust something in a few weeks, then you have obviously used a different chemical reaction!
Salt spray is only a predictor of real world results. This test is also good at detecting finish defects. The best one can do is to base salt spray requirements on prior history. If you want your part to last longer in the real world, look for finishes that will last longer in salt spray.
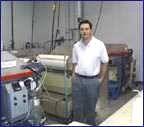
Tim Neveau
Rochester Hills, Michigan
A. I really enjoyed the discussion of salt spray testing and what it means in the Aug. 2001 edition of Metal Finishing. That is the one question that always comes up when one teaches a corrosion class. I answer it with the following question : Which one of the eight types of corrosion are you trying to duplicate? Generally the person asking the question does not know the type of corrosion that is being duplicated. I mention that salt spray is a continuously wet test and in the past has been used mainly for process control checks as one of your respondents mentioned. The continuously wet test is probably some indication of corrosion rate in 5% salt solution or some form of general corrosion.
Cyclic testing, however, was initiated to duplicate the crevice corrosion observed on cars at scratches in the coating. Crevice corrosion requires a dry cycle to accelerate the effect of alkali formation at the cathode to produce the underfilm attack at the scratch. Aluminum has an Exco test to duplicate the exfoliation corrosion observed on high strength aluminum alloys. Anodic polarization testing originated as a test method for evaluating storage tanks for sulfuric acid and susceptibility to pitting corrosion. I don't want to bore you with more test methods, but as you can see there are reasons for tests other than salt spray. My references indicate that approximately 100 hours salt spray is similar to one year outdoors based on OEM testing in the US.
I've seen similar data for Europe. That's the closest I can come to based on published data I have seen. A 100 hours in the salt spray cabinet was equivalent to a month exposure in the Panama Canal Zone when I evaluated coatings for belt links in the late 1960's. For that reason, I call the salt spray a "rubber yardstick" in that you need to know what environment you intend to compare it with. Obviously, 100 hours in the salt spray could also be 15 years in the desert.
Some day someone will write a book on salt spray testing and start a discussion on effect of thickness on plated coatings, effect of pretreatment on paint coatings, effect of surface roughness on oil coatings, etc. That's what is really important to know. . . . . how all these variables effect not only the salt spray results, but the actual results achieved in service.
Joe MenkeEd. note: Joe is the author of "A Study of Manganese Phosphating Reactions" and other important contributions to the literature.
A. Thanks, Joe!
I never really thought about 8 different types of corrosion 🙂
Additionally some surfaces are just fundamentally different from others. I had a hard time understanding how stainless steels were sometimes spec'd for a 10 hour salt spray requirement and sometimes for a 2000 hour one ... and then learned that those requirement are not nearly as different as I thought -- if stainless lasts 10 hours it's not unlikely to last 2000 🙂
And the perennial issue of hot dip galvanizing which corrodes in a salt fog cabinet but which, in the real world, can often build a glassy nearly impervious coating of zinc carbonate corrosion products and last 50, 75, even 100 years.
Luck & Regards,
Ted Mooney, P.E. RET
Striving to live Aloha
finishing.com - Pine Beach, New Jersey
Multiple threads merged: please forgive chronology errors and repetition 🙂
Q. I use salt spray fog chamber (according to ASTM B117) to determine rust resistance of flat products coated with chrome, zinc (galvanization), tin and rust preventive oil. How can I evaluate the test results when taking long term atmospheric exposures into consideration? Is there a rating scale; area failed versus resistivity time.
Ferhat Parlakemployee of iron and steel co. - Turkey
June 12, 2008
A. Hi, Ferhat. This question comes up at least once a month, so it has been answered here dozens of times in case you want to search the site and read some other responses. But the answer is that there is no correlation and there wasn't actually intended to be one.
Salt spray testing is a QA measure to help make sure your finishing process has stayed consistent and hasn't gone south. The corrosion mechanisms are very different in these accelerated tests than in real life, the finishes respond utterly differently than in real life, and there is no predictive value of one finish against another. Galvanizing, for example, easily lasts 50 years often 100 years in real life where the finish can properly interact with carbon dioxide in the air to form very stable intermediate corrosion products, yet it is quickly destroyed in a salt fog chamber. Rust preventative oils that may vaporize in the hot sun in real life, might theoretically last longer in the "accelerated test" than in real life :-)
Regards,
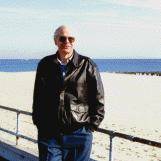
Ted Mooney, P.E.
Striving to live Aloha
finishing.com - Pine Beach, New Jersey
A. Ted is quite correct in stating that ASTM B117 is a method used by the coating trade as a QA tool. It can also be used to evaluate a new coating vs the current material. It can also answer very quickly the question; "does the new additive show some improvement?". However, I was informed by the labs of Cranfield University (UK military test labs) that ARTM G85 is now being evaluated by several labs around the world as a method that almost mirrors natural weathering. I would be interested if anyone else is evaluating this as the photo images did look comparable.
Terry HicklingBirmingham, United Kingdom
It looks like ASTM G85 contains five different modified salt spray tests, Terry; I suppose we'll have to see how it works out. It strikes me that developing an accelerated test that can the mimic the real life behavior of one type of coating ought to be doable.
But a test that properly compares the longevity of one coating to another is a pipe dream. Most coatings develop some of their corrosion resistance or their propensity towards corrosion from intermediate corrosion products of specific composition and structure; and it is impossible to imagine a single test that would allow every different metal and every different coating to mimic real life at accelerated pace. But progress is certainly a good thing even if perfection always seems a ways off :-)
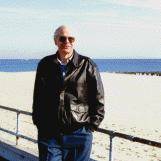
Ted Mooney, P.E.
Striving to live Aloha
finishing.com - Pine Beach, New Jersey
A. Hello,
salt spray test is a comparison and r&d test rather than Qc test, so it is easy to compare your current product with the past product, or new process with older one. I used it in comparison different coating supplier (painting) and to reach the best process parameters in hot dip galvanizing.
- Egypt
Hi, Haytham. We'll just have to completely & utterly disagree on this; I maintain that you cannot use salt spray tests to compare one finish to another. The corrosion resistance of many finishes (like the galvanizing you mention) is mostly due to the very slow formation of tight, adherent, glassy corrosion products, and tend to isolate the substrate from the atmosphere. These tight adherent corrosion products require years-long and decades-long reactions with ingredients in the environment like carbon dioxide in order to form.
As an example, rain water certainly doesn't cause rapid failure of galvanizing on real roofs in service, yet the same roofing sheet will quickly get "wet storage stain" if it is wet and can't breathe properly. That is because exposure to the atmosphere allows the proper corrosion products to form whereas wet storage and the salt spray environment doesn't. Galvanizing is an incredibly durable finish that performs poorly in salt spray and I do not see how you are going to know how altered galvanizing conditions will affect the growth of those zinc carbonate protective surface skins; it strikes me as entirely possible that a process change which slows corrosion in the salt spray chamber might even interfere with the growth of that zinc carbonate skin over the decades.
Then we get into stainless steel ... it can sometimes fail salt spray testing in 10 hours, but it's almost unimaginable that a zinc plated steel finish which lasts 196 hours would even remotely compare with solid stainless steel.
Regards,
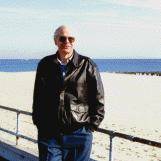
Ted Mooney, P.E.
Striving to live Aloha
finishing.com - Pine Beach, New Jersey
[editor appended this entry to this thread which already addresses it in lieu of spawning a duplicative thread]
Q. How does 100 hrs of humidity testing (not Salt spray) in a controlled cabinet equate to real shelf life in hours, days, weeks, months?
Quality Engineer Supervisor - Moberly, Missouri
January 5, 2010
A. Sorry, Ginger, it doesn't. Salt Spray testing and Humidity testing are QA measures used to insure that the process has not deteriorated; they are not a predictor of real life in service or on the shelf.
If processed parts survived 100 hours in the past and now they don't, something has gone south that must be investigated. But a galvanized part that survives 100 hours may outlast by decades a painted part that survives 100 hours. The corrosion mechanism in salt spray cabinets is fundamentally different than the corrosion mechanisms of real life, and the corrosion prevention mechanisms of different coatings is fundamentally different one from the other as well: some are barrier layer and non conductive, some offer barrier layer protection but are cathodic to the substrate, some are anodic to the substrate so they offer cathodic protection, etc. Sorry.
I believe that humidity testing is primarily used on materials that are stipulated to not be resistant to salt, like the lower grades of stainless steel.
Regards,
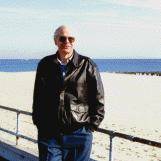
Ted Mooney, P.E.
Striving to live Aloha
finishing.com - Pine Beach, New Jersey
Salt spray test hours vs. humidity test hours
Q. I understand that there is no direct correlation between salt spray hours and hours in a real-life environment, but is there a known correlation between salt spray hours and humidity chamber hours? For instance, if I had a part spec'd to 240 hours no white rust in humidity, is there an equivalent salt spray duration I could use as an alternative test?
Dave Pawletki- ITASCA Illinois
September 8, 2016
A. As others have mentioned, there are different types of corrosion and they proceed differently on different substrates; there are different corrosion resistance mechanisms, ranging from barrier layer, to galvanically protective, to galvanically neutral, to galvanically destructive; sometimes the corrosion products are powdery and hygroscopic (iron rust) and accelerate the corrosion; sometimes the corrosion products are tight and glassy (galvanizing exposed to carbon dioxide over the years) and provide a relatively inert surface slowing corrosion to a crawl, etc. To expect accelerated testing corrosion rates to be proportional to anything against such a mix is a stretch, but, if you limit it to one specific finish on one specific substrate so you are substantially reducing the number of variables, maybe you can establish a correlation within some reasonable percentage of error ... maybe.
For example, you might be able to say if finish A of thickness X was found to last 48 hours in salt spray and 240 hours in humidity, and finish A in thickness 2X lasts 96 hours in salt spray, yes, I think it probably will last something like 480 hours in humidity testing. But this probably tells you nothing about the humidity chamber life or real life of finish B which also lasted 48 hours in salt spray :-(
Regards,
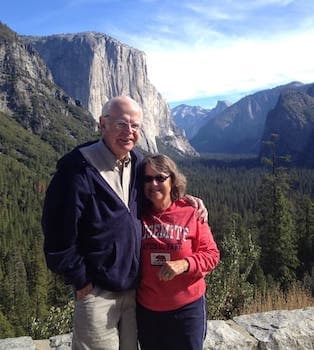
Ted Mooney, P.E. RET
Striving to live Aloha
finishing.com - Pine Beach, New Jersey
Q. Thanks for your response, Ted. The variation in reactivity across coatings and substrates is a great point -- this is a subject I will need to research further.
To the point of humidity vs. salt spray, I agree it would take a pretty substantial amount of testing to try and draw any kind of correlation, even if coating and thickness were held constant. I would be curious to know if there is any kind of published study out there for zinc coatings on low carbon steel, but even if there were, wouldn't geometry of the test sample play a role in corrosion performance as well? I imagine it would be difficult to draw any kind of conclusion about the results when trying to apply to other configurations.
- Itasca, Illinois
A. Dave,
If the spec requires something, you do what the spec requires. Don't go attempting to substitute something without the express permission of the purchaser or the "cognizant engineering organization" as some say.
The 240 hours in humidity was likely an arbitrarily chosen test and a somewhat arbitrarily chosen number of hours, but it's THEIR arbitrarily chosen test.
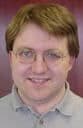
Ray Kremer
Stellar Solutions, Inc.

McHenry, Illinois
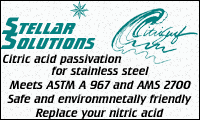
Q. Hi
This is Madhukar. I want to know about no. of hours of salt spray test and it's meaning with no. of hours of rust-free operation
Regards
Nimako - Pimpri chinchwad
April 21, 2018
A. Hi Madhukar. This might be the most frequently asked question on this site; so you can search the site for dozens of 'second opinions' ... but the answer remains that the purpose of salt spray tests is to give early warning if a finishing process is getting out of control. The assumption is that if the finish used to survive HHHH hours, and it no longer does, something has gone wrong which is likely to effect its real-world endurance.
Predicting real-world life is not the purpose of salt spray tests, and it definitely cannot be used to compare one finish against another -- for example, a hot-dip galvanized coating which will easily outlast the world's best paint job by decades is unlikely to match the salt spray life of even a mediocre paint job.
Regards,
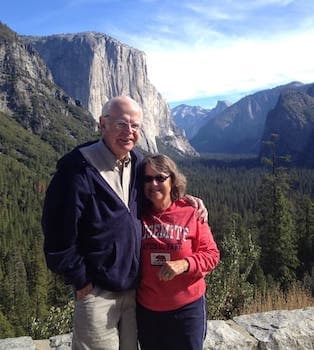
Ted Mooney, P.E. RET
Striving to live Aloha
finishing.com - Pine Beach, New Jersey
Q. It looks like Life expectancy from salt spray test are based on previous historical data only and no scientific justification. Standards based on the historical data. Please correct me if I am wrong. I totally confused on this to judge the part for prediction. So many standards and methods are there for reference but do not find crystal clear justification on life prediction.
Bala subramanianSun Mobility - Bangalore, Chennai, India
A. Hi Bala. It's not a question of "no scientific justification", it's a question of "was never intended or expected to". As Tim noted on the first response, salt spray testing can be "good at detecting surface defects", and that's what it's for. Perhaps the problem is that people try to turn this simple qualitative test, intended to uncover defects, into a quantitative test.
Imagine that you have been plating parts which exhibit sufficient life that you and your customers are happy with the finish. You want to open a second shop for additional capacity, but be confident that their plating will work well too. So you start subjecting sample parts from the first facility to a salt spray test and you see that they reliably survive 192 hours or more, but they often fail by 384 hours. So you instruct the second plating shop to not ship any parts until they test sample parts for 192 hours. If the second shop attains 192 hours you're probably ready to go. But if they reliably last 384 hours you know nothing additional about their predicted real-world life either.
Regards,
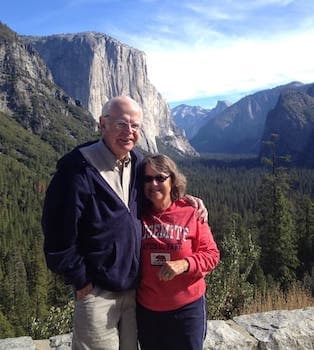
Ted Mooney, P.E. RET
Striving to live Aloha
finishing.com - Pine Beach, New Jersey
A. Hello
Adding to the previous commentary, the difference between a Salt Spray Test and real life expectancy is that in a NST test all parameters and conditions are controlled, therefore the results are somewhat consistent (not always the case) and in real life there are no controls.
For example, how can you compare life expectancy in a coastal town to life expectancy in the desert or in forest-like weather?
How much is a little humidity in Houston, Texas or how much is a salty atmosphere in south Florida?
How can you compare a life expectancy in a household where they clean the parts everyday with a mild alkaline cleaner and abrasive cloth, compared to a household that only cleans with a dry cloth once per month?
Do you get the idea? Only controlled test can give consistent results.
RECUBRIMIENTOS METALICOS DE MEXICO, S.A. DE C.V. - Mexico City, Mexico
Q. How many hours of neutral salt spray (ASTM B117) equal to five years of coastal area condition?
Denuwan Devendra- Western province, Sri lanka
August 30, 2018
Hi cousin Denuwan. Please refer to the previous responses on the page: there is no reliable relationship between salt spray test hours and real life :-)
Please post what kind of parts you are dealing with, what they are made of, exactly what finish they have (including pretreatment, thickness, and post treatment) and then people might be able to hazard a guess how long they will last and/or how many hours of salt spray they can survive. Good luck.
Thanks & Regards,
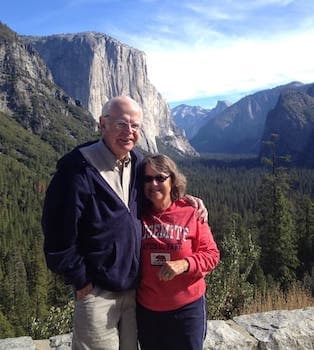
Ted Mooney, P.E. RET
Striving to live Aloha
finishing.com - Pine Beach, New Jersey
Q. Hi,
Low Temperature Powder Coated (Tiger Anodized silver 038/91020 used) aluminium plate around 5*8*0.25.
Powder coating thickness is not specified.
- Western province, Sri lanka
A. Hi again Denuwan. With no specification number, and no pretreatment specified, I doubt that they will last either 5 years in a coastal environment or 350 hours in a salt spray cabinet. But this is only a guess based on lack of information rather than based on information.
If you are confident that the components were properly chromate conversion coated, and have no sharp corners which the powder will pull back from, and no Faraday Cage areas (unlikely in such small parts), and inspection reveals no pinholes or orange peeling, or obvious under-curing or over-curing, my guess would be 350 hours salt spray and 5 years coastal environment. Hopefully other readers will guess if you feel such guesses are useful :-)
Regards,
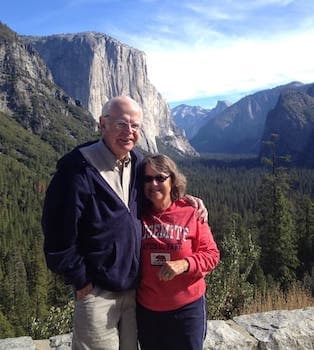
Ted Mooney, P.E. RET
Striving to live Aloha
finishing.com - Pine Beach, New Jersey
Q. Hello, how to correlate the salt spray test hour to life expectancy of product with only Nickel plating & with copper+Ni+Cr plating on M.S for student compass/divider of geometry components.
RAMESH NAIKkokuyo camlin Limited - Mumbai, Maharashtra, India
August 27, 2019
A. Hi Ramesh. Salt spray testing is unlikely to help you decide whether to only nickel plate vs. copper-nickel-chrome plate this component. Rather, you must determine whether you prefer the mellow tone of nickel plating or the brighter bluer look of nickel-chrome. Then you should follow an accepted standard for plating thickness and method, such as ASTM B456. The plating must be thick enough to be pore-free because nickel is cathodic to steel and will accelerate it's corrosion rather than retard it if any steel is exposed.
CASS testing ASTM B368 or Corrodkote ASTM B380 is probably better than salt spray testing, but there is no reliable correlation between test hours and real-life hours. Rather, if you consider this a "moderate" exposure condition, you follow the plating spec for moderate exposure; then you should probably be able to pass a 4-hour CASS or Corrodkote test.
These days a base of copper plating is not believed to substantially affect the corrosion resistance of nickel or nickel-chrome plated steel. Good luck.
Regards,
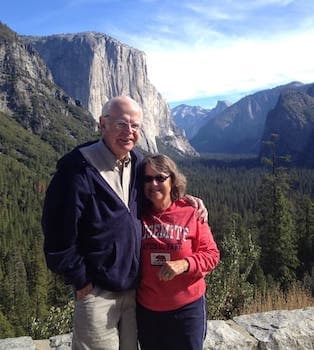
Ted Mooney, P.E. RET
Striving to live Aloha
finishing.com - Pine Beach, New Jersey
Q. Does having an epoxy coating of 80 micron guarantee 5000 hrs of salt spray test as per ASTM standards.
Uzair KhanEquipment Engineer - Doha, Qatar
January 31, 2022
A. Hi Uzair. Certainly not! -- especially because the main function of salt spray testing is as quality assurance, to determine whether you're doing it right or wrong :-)
But 80 microns is probably a good thickness, and 5000 hours of salt spray is an ambitious goal.
Luck & Regards,
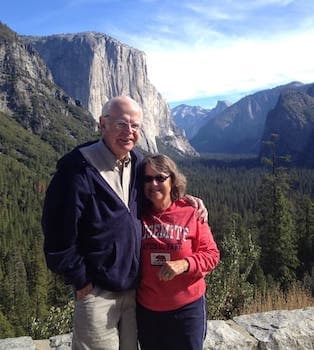
Ted Mooney, P.E. RET
Striving to live Aloha
finishing.com - Pine Beach, New Jersey
Q, A, or Comment on THIS thread -or- Start a NEW Thread