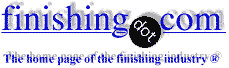
-----
Nickel electroplating on Copper electrode in a nickel sulfamate + boric acid heat bath
Q. Hello,
I am currently pursuing an engineering undergraduate degree and one of our modules involves designing a nickel electroplating project.
We are given nickel metal (not sure how pure it is but apparently it was electrodeposited professionally done by professor) and a nickel sulfamate + boric acid bath. We were asked to perform literature research by ourselves to determine the composition and every other physical quantities required. And finishing.com has been one of sites we are finding most of our information.
The heat bath that my group have prepared has a pH of about 4 (the pH meter wasn't calibrated accurately) and we are maintaining the temperature at about 46 °C. The concentration of nickel sulfamate is about 300 g/L. We have kept our current density to well below 40 amps/ft^2. The cathode used was a thin copper sheet which we decided to coat with a thin copper tape with the back part insulated by a special insulating tape which does not corrode in the solution. The experiment was ran for 30 minutes each time.
We have also introduced a small stirrer powered by a motor as mechanical agitation and have tried varying speeds but we have been unable to successfully remove the small bubbles on the surface of our cathode. The defects caused by the bubbles are very obvious when viewed under 40x magnification.
Our objective is to get a surface as shiny as possible.
From reading various posts on this site, the reason that I gather was that (a) the current density is too high; excess current were electrolysing the hydrogen and oxygen ions (b) the concentration of the nickel is too low (c) much better agitation is required.
A picture of my agitator is as follows:
Also, we are required to determine the efficiency of our heat bath, but I am puzzled as to how efficiency is determined. I wonder if anyone can help to explain this to me too.
Any help is greatly appreciated.
Thank you and best regards,
student - Singapore
April 6, 2008
A. Bubbles formation and their tendency to adhere are related to the surface tension (ST) of your liquid. To avoid this, you need to add a surfactant, substance that reduces ST. Suitable surfactants (also known as anti-pit additives) must be as inert as possible to the bath.
Efficiency is related to the valence of the metallic ions dissolved. For instance, hexavalent chrome has a very low efficiency because 6 electrons are needed to reduce 1 atom of Cr. Also, efficiency relates to the tendency of the particular bath to reduce hydrogen ions instead of metal which is a waste of electricity and a non-desirable effect.
Monterrey, NL, Mexico
A. To determine the 'efficiency' of the electroplating process you need to know the weight of the nickel you deposited and the number of coulombs (Amp-secs) you used to deposit that weight. You then use Faradays Laws of Electrolysis to calculate the theoretical weight you should have deposited and compare that with the actual weight. You should know how many electrons are used in the reduction process from the reaction equation. By the way, you cannot exceed 100% efficiency with your set up and remember you will also be depositing some hydrogen, so you won't get 100% efficiency in terms of nickel.
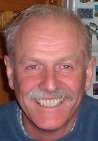
Trevor Crichton
R&D practical scientist
Chesham, Bucks, UK
April 15, 2008
A. Hi Dingyan,
Although proprietary ingredients are always best in electroplating applications, I think you will find sodium lauryl sulfate ⇦ on
eBay or
Amazon [affil link]
acceptable as your surface tension reducer. Not a lot is required.
Luck & Regards,
Ted Mooney, P.E. RET
Striving to live Aloha
(Ted can offer longterm or instant help)
finishing.com - Pine Beach, New Jersey
Q, A, or Comment on THIS thread -or- Start a NEW Thread