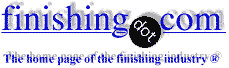
-----
Electropolish, Passivate, or Chemical Polish 4140 & 4340 Steel?
Current questions and answers:
Q. We have recently manufactured a part for passivation. The parts are made of Alloy steel 4340. After passivation process, now exhibiting various degrees of rust!
The drawing specifies passivation process, but can Alloy steel 4340 be passivated?
Project Engineer - Coimbatore, Tamil Nadu, India
July 20, 2021
A. Hi Sakthivel. Nothing wrong with circling back to see if anything has changed, but I don't think it has :-)
4340 has < 1% Cr & < 2% Ni -- it's not stainless steel :-)
Luck & Regards,
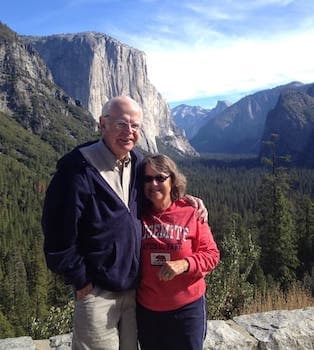
Ted Mooney, P.E. RET
Striving to live Aloha
(Ted can offer longterm or instant help)
finishing.com - Pine Beach, New Jersey
July 2021
July 29, 2021
Q. `Hello Sir,
I have carefully reviewed your comments on different questions with 4100 steel series passivation. But I could not find my Answer.
Can I ask you please review my question and provide me with some options?
I have sent some High Speed Shaft that has made of Steel 4140 By Cold rolling and Annealed (Hardness of 36 to 42) to be passivated as per 2700 spec.
Unfortunately, I did so relying on my colleague's experience and did not check the material spec before sending for passivation.
Now I got a Black colour on our Highly Expensive parts and very concerned about if they have gotten useless due to Hydrogen Embrittlement? So probably they are screwed up?
Thanks.
Repair and Design Engineer - Mississauga, ON, Canada
A. Hi Mehdi. I hope your colleague recovers from that bus incident :-)
Passivation is a treatment for stainless steel which dissolves the iron on the surface, leaving a chrome-rich oxide layer. Unfortunately 4140 is not stainless steel; and its very small chromium content does not allow for this passivation to occur.
To determine whether embrittlement may have occurred probably should involve a two-pronged approach consisting of a careful process audit (and at this point we don't even know yet what the passivation solution was: citric acid, nitric acid, or nitric plus chromic acid) plus notch testing.
In thread 11297, Brian Terry and Ray kremer seemed to agree (at least in 2015 -- check for updates) that passivation does not cause hydrogen embrittlement ... but this only reinforces the need for a careful process audit because the passivation step per se may not have been the only operation that was done on the parts.
If the components must resist corrosion, some possibilities for surfaces which would not be softer than the substrate include chrome plating, electroless nickel plating, or salt bath nitriding, but at this point I can't say whether your parts are recoverable -- "the moving finger having writ, moves on, ...", etc.
Luck & Regards,
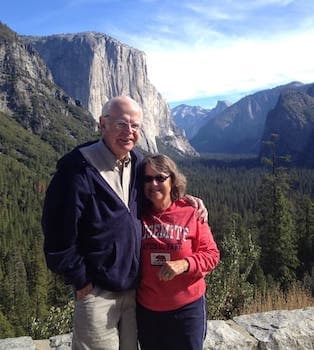
Ted Mooney, P.E. RET
Striving to live Aloha
(Ted can offer longterm or instant help)
finishing.com - Pine Beach, New Jersey
July 2021
⇩ Related postings, oldest first ⇩
Q. I have been tasked to help our customer with a problem part. We manufactured a prototype part from 1" diameter 4340 steel. It has a tapered bore thru the ~ 2.20" length and has a series of .017" wide slots running lengthwise most of the length of the part. When you look thru the part it looks like very fine "fins" along the I.D. The Slots were wire EDM'd and the part was subsequently Ion Nitrided and "Steam Treated" for wear resistance and corrosion resistance. Problem is, the surface finish in the slots is too rough and snags the yarn which must pass thru the part (very fine fibers). I can stand opening up the slots by only ~ .001-.002 and thought about using the help from a photochemical etching guy but he does not know how to remove the "Steam Treating" (oxide) without damaging the part.
Any ideas on how to A. remove the oxide , or B. improve the surface finish in the slots in some other way? C. Can this part be electropolished (selectively?)
Thank you!
Jim
Jim BrangWest Melbourne, Florida, USA
2000
A. The best way to approach this problem is with a "chemical polish". It is non-electrolytic and produces excellent results on mild steel. It is available from several sources.
Dan Weaver- Toccoa, Georgia
2000
A. Jim:
I don't believe chemical polishing can handle that job. Our company has electropolishing solutions for steel. We also have some experience with 4340.
Regards,
Ed BayhaMetal Coating Process Corporation - Charlotte, North Carolina
2000
A. I know that a company in Texas has very good luck electropolishing the bores of rifle barrels (mostly 4140). There shouldn't be too much difference between 4140 and 4130. Good Luck.
Howard Bailey- Flagstaff, Arizona
2000
Passivating 4340 Stainless Steel
Q. Hi guys, I'm currently working on some 4340 stainless steel parts but I haven't been able to find the right way to passivate them it's really hard, I'm following the AMS2700 guidelines but I can't make it work since the results are really bad, the parts are coming out from the bath all dark with this kind of smut all over them, I'm currently applying the type II nitric acid plus 2 to 3% v/v sodium dichromate.
Can someone guide me in the right direction please, I will appreciate it. Thank you in advance, best regards.
finishing - Anaheim California, USA
November 8, 2019
A. Hi Hassan. I think the main problem here is that you are calling 4340 "stainless steel" whereas it is a low alloy steel, not a stainless steel :-)
I'm not the stainless sheriff, but various sites say that a stainless steel must have "greater than 10%" / "11% or more" / 12-15%" chromium. There may be some highly specialized chemical formulations and operating conditions which can to some extent or other passivate or electropolish 4340 steel, but you're surely right that it isn't easy. But even if you accomplish it, what shall be your basis for calling it passivated or electropolished? When those terms are used there needs to be some performance expectation, not a mere claim that you exposed the parts to certain chemicals.
If I were you I might move directly on to trying to electropolish rather than passivate because after you achieve whatever is your goal for finish and appearance, now you have the problem of hydrogen embrittlement to deal with. You probably will not have achieved substantial corrosion resistance by passivation, but I think it's possible that electropolishing might measurably improve corrosion resistance :-)
Regards and good luck,
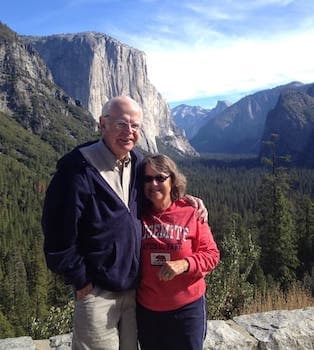
Ted Mooney, P.E. RET
Striving to live Aloha
(Ted can offer longterm or instant help)
finishing.com - Pine Beach, New Jersey
November 2019
A. I agree with Ted. Even-though we have some cool methods of passivating 400- ss (as we call it, or "surgical steel", if parts are stored not in the proper way, rust will appear sooner or later.
Electropolishing is the best way to create thick passivating layer on the surface of 400-series steel.
Barrel or basket electropolishing is the cheapest and fastest way to create strong anti corrosion layer.
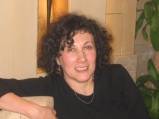
Anna Berkovich
Russamer Lab

Pittsburgh, Pennsylvania
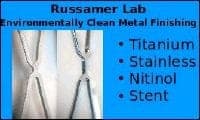
November 11, 2019
A. Indeed, 4340 is not a stainless grade.
Electropolishing increases corrosion resistance by virtue of the smoother surface (so does mechanical polishing), NOT the same as the passive chromium oxide layer that you get on stainless steel by removing iron from the surface in a citric acid or nitric acid passivation bath.
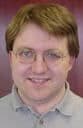
Ray Kremer
Stellar Solutions, Inc.

McHenry, Illinois
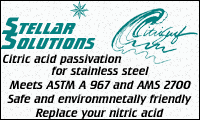
November 19, 2019
Q. We have recently sent a part we manufactured for passivation. The parts are made of AISI 4140 they have returned and are now exhibiting various degrees of rust!
The drawing specifies passivation but can AISI 4140 be passivated?
- Dublin Ireland
February 9, 2021
A. Hi Martin. 4140 is not stainless steel and it cannot be passivated in the sense that stainless steel is passivated, or according to the specifications for it. The drawing is wrong. Read the previous responses on this thread we appended your question to ...
However, there is a bit of a semantics issue that is sometimes confusing to everyone, viz., the word 'passivation' is just a word, not a specification ... and people who are involved in the passivation of stainless steel can't stop other people in other fields from using that word :-)
People sometimes call the chromate conversion coating process used after zinc plating 'passivation' (thread 55350); people sometimes call the final chromate or other chemical dip after zinc phosphatizing 'passivation' (thread 53135); and people sometimes call the processes done in carbon steel boilers to deter rust 'passivation' (thread 41786).
Luck & Regards,
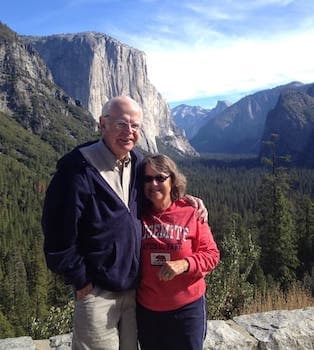
Ted Mooney, P.E. RET
Striving to live Aloha
(Ted can offer longterm or instant help)
finishing.com - Pine Beach, New Jersey
February 2021
A. Hi Martin.
We conducted various tests on passivation 400 series stainless steel, and came to a conclusion that only electropolishing provides the reliable corrosion resistant layer. Back in 2012 we provided our UE to Striker in Ireland. They were very satisfied with the outcome for surgical instruments electropolishing for burrs removal and corrosion protection. You can talk to Alan Ronan if he still works there. Also Medical Optics from Florida used this electrolyte after re-sharpening medical instruments of 400 alloy type.
We do not deliver this electrolyte retail, but if you find the shop nearby who is willing to obtain the solution composition and provide the service, contact me directly, please.
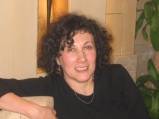
Anna Berkovich
Russamer Lab

Pittsburgh, Pennsylvania
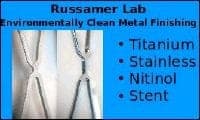
February 9, 2021
Q, A, or Comment on THIS thread -or- Start a NEW Thread