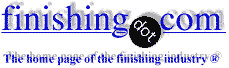
-----
How to nickel plate aluminum with good adhesion?
Quickstart:
It's generally not possible to electroplate directly onto aluminum because it instantly oxidizes, whereas plating has to grow onto raw metal for proper adhesion.
Usually the aluminum is "zincated" first -- immersed in a strong solution of zinc & caustic soda, forming an "immersion/replacement" coating of zinc on the aluminum; then the zinc surface is electroplated with any plating compatible with zinc. Adhesion is often improved by "double zincating", i.e., zincating the aluminum, stripping the zincate in nitric acid, and re-zincating. An alternative to electroplating onto the zincate is alkaline electroless nickel plating onto the zincate, and many people find this more reliable.
A lesser used alternative to zincating is phosphoric acid anodizing.
Q. Hello, I nickel plate aluminum after using double zincate.
I start with alkaline degreasing, then NaOH 5 percent at 40 °C, then aluminum activation in a solution of 3 percent HF and 3 percent sulfuric acid for 1 minute.
Then I zinc plate at 20 °C for 60 seconds, I remove zinc in a solution of HF plus sulfuric for 1 minute at 15 °C, 2nd zincating for 60 in a solution of 155 g NaOH 12g zinc oxide 0.5g iron chloride and 2.5g sodium gluconate. I rinse the detail between each stage in deionized water, then I put the zincated aluminum in a nickel solution with the composition of 180 g of nickel sulfate, 25 g of ammonium chloride, 50 g of boric acid, 10 g of sodium citrate, 1 g of saccharin and a pH of about 4.5-5 (I also tried lower pH); the solution temperature is 40 to 50 °C, the cathode current is 2-8 A/dm3 (I tried different ones).
After nickel plating the coating looks nice but it does not adhere well and during heating with an air heat gun you can hear knocking from the coating and the coating can be torn off with a sharp tool. the aluminum is PA38, i.e. 6060. after peeling off the coating, sometimes the zinc coating is not visible on some samples, and sometimes it is. P.S.: I do not allow the zinc coating to dry. I ask you for advice in order to obtain satisfactory thermal and peel adhesion.
Hobbyist - SANOK [Poland]
May 15, 2025
A. Dear Mr. Collins,
I'm a hobbyist like you but I have some notes on your method.
1- your zincate solution does not contain nickel salts or copper salts, so not suitable to go directly to nickel -- you should use copper strike before.
2- I'm not thinking that zincate is good method for good adhesion because first layer is chemical displacement layer.
So my advice is:
degrease your part. Etch it.
USE THIS SOLUTION TO PLATE ELECTRICALLY
NICKEL Chloride 400 Gm/L
BORIC ACID 50 Gm /L
HF (hydrofluoric acid) 8ml /L
ANODES NICKEL
TEMP. 60 °C
Current Dinsity SAME AS WATTS NICKEL
THEN RINSE & REMOVE IN
400 Gm/l HF
100 gm/l HNO3
RINSE
GO DIRECTLY TO SULFAMIC OR EVEN WATTS NICKEL
Feedback me about adhesion news.
HAVE A GOOD RESULT
Raafat
HOBBYIST - Riyadh saudi arabia
Q. Dear Mr. Albendary,
I also used alkali zincate containing 25g of zinc oxide 140g of NaOH 45 rochelle salts 2g of sodium nitrate 1.5g of iron chloride and 20g of nickel sulphate.
Previously zincating in the above solution without nickel sulphate and I obtained excellent adhesion of the nickel coating to the aluminium after zincating. I dare say that the cause lies somewhere else than in the zincating solution. I wonder if it wouldn't be better to nickel-plate in a neutral nickel strike solution after the zincate process and then neutral nickel strike and then main nickel plating?
From what I understand, your method involves nickel-plating the aluminum without zincating, then removing the nickel in HF and then nickel-plating again. If I understand correctly, this method will not provide good adhesion due to the oxidation properties of aluminum.
Best regards.
- SANOK [Poland]
June 5, 2025
A. Dear Mr Collins,
Using of nickel plating on aluminum direct as formula I sent to you, or
removing nickel but part still wet then going to Watts nickel is better in adhesion than any kind of zincate if this part is electrical part.
Aluminum is a light metal, vibration will be high, so ferritic corrosion will be high use. The two methods millions of tons we made with high adhesion and accepted quality in electrical section without complaint.
Try it and tell me. You will forget the long zincate procedure.
Raafat
- Riyadh saudi arabia
June 8, 2025
by Jack Dini
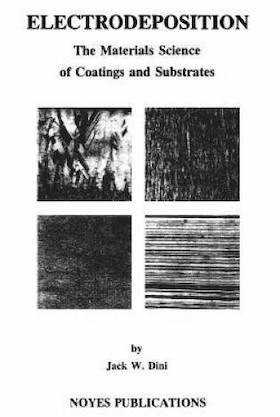
on eBay or Amazon
or AbeBooks
(affil link)
Thanks, Raafat.
Wiktor has not mentioned the alloy he is trying to plate, and the alloy is an important issue according to the "Adhesion" chapter in Jack Dini's "Electrodeposition" ⇨
Dini seems to have found that high copper alloys don't need a copper strike after the zincate and before nickel plating, but low copper alloys do. He shows the adhesion onto 2024 unaffected by whether a copper strike is used, but adhesion onto 6061 greatly increased with a copper strike.
-----
Wictor:
Please try Raafat's suggestion. Electroplating is still a developing science, and exactly what happens in the boundary layer at microscopic level is still poorly understood for most electroplating operations. Decades ago I saw a plating on aluminum operation which worked and did not involve zincating or anodizing. I don't remember whether it resembled Raafat's suggestion, but it did work, and we can't necessarily dismiss stuff just because it's not found in the textbooks. 🙂
But please be very careful with HF
⇦ why?
; it is the one chemical feared by many highly experienced platers.
Luck & Regards,
Ted Mooney, P.E. RET
Striving to live Aloha
(Ted can offer longterm or instant help)
finishing.com - Pine Beach, New Jersey
Thank you Mr Ted
I only want to help share our information through your respectable site. Yes, sometimes information is not familiar but electroplating is a progressive science and art. We have to be open to any new knowledge personally I learned many things from this site.
Please test and update us.
Thanks
Raafat
- Riyadh ksa
A. MR.COLLINS
NICKEL PLATE ON ALUMINUM [with] THE FOLLOWING STEPS:
(NOTE: DOUBLE RINSE BETWEEN EACH STEP
1 SOAK
2 TRI ACID
3. ZINCATE I
4 50% NITRIC DIP
5.ZINCATE II
6. ELECTROLESS ALKALINE NICKEL OR ACIDIC ELECTROLESS NICKEL
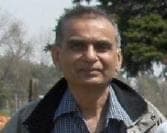
Popatbhai B. Patel
electroplating consultant - Roseville, Michigan
August 4, 2025
Multiple threads merged: please forgive chronology errors and repetition 🙂
Q. I am trying to electroplate a bright nickel coating onto aluminum. I have a zincate layer followed by a copper strike layer. I have tried adding brighteners to our nickel sulfamate bath but the plate is very brittle. I have also tried a Watts nickel bath but the same thing happens. Every bath that I have tried is always brittle. I need shine with great adhesion.
Molnar- Canada
2001
Tip: This forum was created to help build camaraderie through sharing tips, opinions, pics & personalities.
The operator & those readers who want that might not engage with anonymous posters.
A. Skip the Copper undercoat as this will give you adhesion problems contrary to popular belief. Double Zincate your parts carefully and directly plate in a normal Watts Bath.
Regards
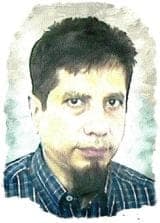
Khozem Vahaanwala
Saify Ind

Bengaluru, Karnataka, India
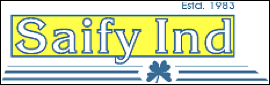
by Fabienne Delaunois et al
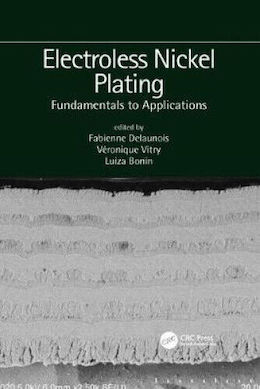
on eBay or Amazon
or AbeBooks
(affil link)
A. After the double zincate I would advise to use an alkaline electroless nickel and then you can use a Watts nickel. If you skip the alkaline EN then you will need a cyanide copper followed by a Watts nickel.
One more thing, are you sure that the problem is brittle nickel? Maybe it is a poor adhesion coming from inadequate pretreatment. You did not mention a deoxidizer prior to the zincate. I hope a deox is a part of your preplating processes otherwise you will have adhesion problems.
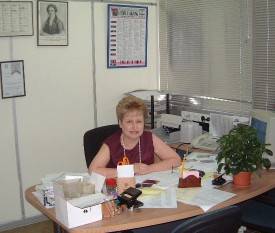

Sara Michaeli
Tel-Aviv-Yafo, Israel
Multiple threads merged: please forgive chronology errors and repetition 🙂
Q. I have just plated bright nickel on 6061 aluminum but the nickel peeled off after heating. My pretreatment can process A356 and ADC12 aluminum casting without peeling. What do I have to change : Etching, desmut or zincate?
Thank you for all answer.
electroplating co. - Bangkok, Thailand
2007
A. It needs a proper alkaline cleaning, a deoxidation/desmut, double zincate, a strike and then plate. I think that the alkaline EN strike is the best one for this step. If not that, I would look at the sulfamate nickel to strike (the Woods nickel strike is tough to use here, because it is a very very strong acid and slow to strike -- it will wipe out your zincate before it can get a good strike) and then immediately into a quick rinse and into the bright nickel tank
James Watts- Navarre, Florida
Q. Thank you for your advice. But I try to plate it with your recommendation, It does not work. I etch the Al with alkaline etching and go to desmut (Tri acid with Ammonium bifluoride) and double cyanide zincate then strike with Watts nickel strike for 10 minute and go to bright nickel and chrome. After heating it to 220 °C degree for 1 Hour ,the strike layer peeled off from the aluminum.
My customer confirmed that their aluminum is 6061 T6 for sure, they show me certificate for ensure these aluminum.
Does anybody have another to accomplish this case.
Thank you so much for your kindness.
[returning]
electroplating co. - Bangkok, Thailand
A. Tell me exactly how you do your double zincate step, including concentrations.
James Watts- Navarre, Florida
Q. Thank you James Watts who followed my question
I got better adhesion. There was not any peeling or bubbles after 1 hour baking but many bubbles came after 24 hours.Why
My zincate is 60% by volume and first zincate is 1 min and second zincate is 30 seconds.
Strip zincate with 50% nitric acid.
I notice that after desmut the aluminium is not stained or and smut; and there is no peeling of both first zincate and second zincate.
Someone told me that 220 °C may well too much, that 150 °C is more appropriate. What do you think, James, what should I do next for getting better adhesion?
Thank you again
[returning]
electroplating co. - Bangkok, Thailand
A. Hi Aon.
While many folks feel that a copper strike is not necessary, Jack Dini reports in "Electrodeposition" [on
AbeBooks, or
eBay,
or
Amazon
affil links]
that although this might be the case with high copper alloys like 2024 ...
"Most seriously affected by lack of the copper strike was the 6061 alloy (31 Mpa without the strike versus 184 MPa with the strike"
Luck & Regards,
Ted Mooney, P.E. RET
Striving to live Aloha
(Ted can offer longterm or instant help)
finishing.com - Pine Beach, New Jersey
Multiple threads merged: please forgive chronology errors and repetition 🙂
Q. I am having a strange issue with adhesion plating nickel onto aluminum. The substrate is extruded aluminum 6061(?) that is anodized prior to assembly to limit tooling marks in the substrate.
Our facility gets the final anodized product for Ni/Cr plating. The process is as follows.
-Strip the anodize off in a hot NaOH solution.
-Polish the high cosmetic areas of the part for any defects from shipping/stripping.
-Parts are cleaned in a mild alkaline cleaner solution 135F for 6 min.
-Immersion in 50% Nitric 30 sec
-Etch: Using EPi's Epik-232 solution 30-40 sec
-50% Nitric for 1 min
-Zincate 25 sec
-50% Nitric 7 sec (part takes on white appearance)
-Zincate 10 sec
-Electroless Nickel Strike (Alkaline) 10 minutes
-Proceed with Bright Ni plate followed by Chrome
Parts look good after plating with no visible abnormalities but during adhesion testing (bake 430 °F for 1hr, cold water quench) blisters appear everywhere some of them even "popping" off the part. I would say the problem is definitely in the cleaning of this particular part as we run other aluminum parts this way with no failures. We are just having trouble determining where exactly the problem is. One interesting thing to note is wherever the parts are polished there is absolutely no adhesion issues---those particular areas of the part are perfect every time. I would polish the whole part but it has recesses which are not accessible.
Is it possible we are not getting all of the anodize off the part in the first step leading to failures later on but where the part is being polished is getting down to the base aluminum?
plating shop - Middletown, Pennsylvania
2007
A. I'd say almost certainly the fault lies with the stripping of the anodic coating. NaOH does not strip uniformly, therefore there may be areas that are completely stripped and the NaOH has begun to etch the surface, and other areas where stripping is incomplete.
If possible, trial a phosphoric/chromic acid solution as used in MIL-A-8625 / MIL-PRF-8625
[⇦ this spec on DLA]F, which will allow complete stripping without etching the part in the manner of NaOH.
The other possibility is the microporosity created by the NaOH stripping is making rinsing more difficult, trapping solutions and causing blistering after plating. Once again, changing your stripping method may be able to help this.
The final option is - would it be simpler just to polish out any marks left on the substrate if not anodised prior to assembly? This is something you would need to discuss with your customer.
- Brisbane, Queensland, Australia
A. Your second nitric should be only 5% or so, and the second zincate time seems short. You may be getting a poor zincate prior to plating. Acid EN may work better.
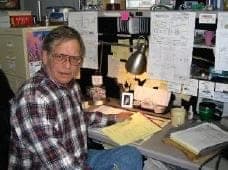
Jeffrey Holmes, CEF
Spartanburg, South Carolina
A. It looks to me as if the problem is with the stripping of the anodised layer. I know of a couple of ways of stripping this layer, one being 3% sodium hydroxide at about 35-40 °C. Other methods include a mixture of 10% sulfuric acid with 1% hydrofluoric acid (i.e., 100 ml/l H2SO4 and 10 ml/l HF), or 10% sulfuric acid with 40g/l potassium fluoride ⇦ on Amazon [affil link] (100 ml/l H2SO4 and 40 g/l KF). In all cases of stripping, the treated part must be rinsed in nitric acid to remove any residual surface debris. I suspect your polishing stage replaces the nitric acid dip, but where you cannot get to the surface, you leave some debris that later results in delamination. I would therefore try giving your parts a good dip in nitric acid prior to polishing with a lot of gentle agitation - hopefully that will solve your problem. By the way, it is NOT recommended that the sodium hydroxide route is used for stressed parts or anything for the aerospace industry - in fact I think it may be prohibited!
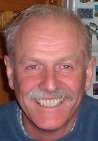
Trevor Crichton
R&D practical scientist
Chesham, Bucks, UK
? Have you considered the differences in the coefficients of expansion at 430 °F of all those metals you have in the sandwich?
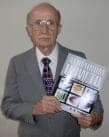
Robert H Probert
Robert H Probert Technical Services

Garner, North Carolina
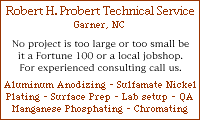
A. 430 °F. is expecting a lot for nickel on aluminum. Even when everything is done properly.
Frank DeGuire- St. Louis, Missouri, USA
A. We electroless nickel plated tens of thousands of aluminum PVC glove molds which are continuously cycled to 360 °F+. Not quite 430, but I don't recall a single adhesion failure, and these ran many thousands of heat/quench cycles.
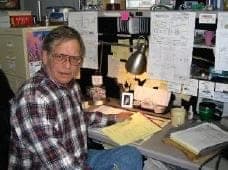
Jeffrey Holmes, CEF
Spartanburg, South Carolina
A. Dear sir,
please follow this sequence:
1 pre clean (mild alkaline)
2 hot soak (" " " ")
3 cathodic cleaning if decorative purpose, or for functional purpose it is only immersion
4 nitric acid 50%
5 zincating
6 nitric acid 50%
7 zincating
8 alkaline nickel (ENP)
9 bright nickel (ENP)
every step in between require rinse well.
Please use zincating solution which contains Ni ion composition .
- Mumbai, Maharashtra, India
The issue has seemingly been resolved but using a very thin layer of Electroless Nickel. With this thin layer we can achieve the quench test with little or no blistering of the parts. Thanks to everyone who replied.
plating shop - Harrisburg, Pennsylvania
Readers may also be interested in these related threads:
• Topic #464/76 "Electroless Nickel (EN) Plating on Aluminum"
• Topic #275/75 "Preparing electroless nickel surface for better adhesion"
Q, A, or Comment on THIS thread -or- Start a NEW Thread