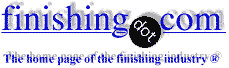
-----
Preparing electroless nickel surface for better adhesion
Readers may also be interested in this related thread:
• Topic #137/85 "Activating Electroless Nickel for additional plating"
Q. I am trying to prepare a surface for adhesive bonding using an epoxy resin. The surface is an electroless nickel coating with a mild steel substrate. This part will be joined to a larger (similar) part making up an assembly which will ultimately sit inside the cab of a road vehicle.
The epoxy manufacturer recommends a conc. nitric acid dip for 5 seconds. This appears to work really well. It leaves behind a bright nickel surface which adheres well to the epoxy. I later subcontracted the plating and the acid dip, only to find that the electroless nickel has gone black. I have discovered that the subcontractor uses a low-med phosphorous electroless nickel process, whereas I have used a high phosphorous process.
I assume that the black surface is nickel phosphate/phosphide? My question is this, how will the black finish fare when exposed to ambient atmospheric conditions, such as would be found in the cab of a road vehicle. Also how will this compare to the bright nickel finish obtained earlier under the same environmental conditions? i.e. which finish would give the best corrosion resistance.
Materials Engineer - Plymouth, Devon, England (UK)
2004
A. You have discovered the nitric acid test for EN coatings. The test is often used to distinguish between high phosphorus coatings and lower phosphorus coatings. Generally coatings containing less than 10 percent phosphorus will turn black in less than 30 seconds. High phosphorus coatings will stay bright for several minutes.
The black color is due the formation of nickel/phosphorus oxide AND to the formation of etch pits in the coating. Even without the blackening treatment, mid phos coatings are much less corrosion resistance than high phos coatings. After blackening (etching) the difference will be even greater.
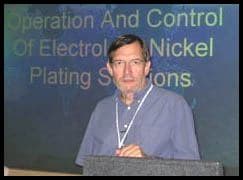
Ron Duncan [deceased]
- LaVergne, Tennessee
It is our sad duty to note Ron's passing on Dec. 15, 2006. A brief obituary opens Episode 13 of our Podcast.
Shelf-life of Pd activation
Q. Hi, I am a student doing some thesis work on the electroless plating process. In order to streamline the lab work I was considering creating a stock of activated substrates (mainly carbon fibers and alumina particles) but was unsure of the following.
When a substrate is activated with palladium from an Sn/Pd two-step process prior to Electroless Nickel plating, can a part be left out as activated for a while (say up to a month) or should the parts be plated immediately due to e.g. oxidation of the palladium or some other process?
student - Msida, Malta
April 12, 2011
A. Hi Robert,
Unfortunately you should immediately continue with the next layer.
Although the Palladium is a noble metal, it attracts organics to it's surface and you have a good change that you end up with bad adhesion or pores, etc.
Better don't take the risk, you can try to re-activate your samples, but this is not the preferred way to go, maybe your supplier of the electrolytes could tell you if that's a possible way to go.
Best regards,
Harry
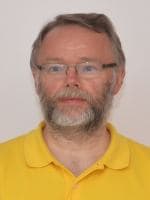
Harry van der Zanden
consultant - Tilburg, Netherlands
Hi,
Thanks for your reply. Since my samples were small enough, what I eventually did was keep the samples sealed until required. This seems to have worked out well enough as I haven't noticed a significant deterioration in the quality of the samples with regards to the interval between activation and plating, which was shorter than expected. This said, it's good to know about the problem with organics and I will keep an eye out for the effects you mentioned when looking over my results.
Thanks and regards,
Robert
- Msida, Malta
Q, A, or Comment on THIS thread -or- Start a NEW Thread