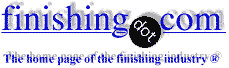
-----
Nickel Plating on Glidcop: Can't get good adhesion
February 14, 2022
Q. Hi, Vincent!
Recently, I try to electroplate Ni on Glidcop plate. However, the adhesion between Ni coating and Glidcop plate is very poor. Two kinds of solution: dilute sulfuric acid (200 g/L) and the mixture of dilute sulfuric acid and hydrogen peroxide were used for Glidcop substrate pickling. After pickling, the Glidcop substrate was cleaned by deionized water.
Can you give some suggestions for the pre-treatment of Glidcop plate prior to Ni electrodeposition.
Please comment! Thank you very much!
Yours sincerely, Yan Lin
Q. Hi, Rakesh Kaul!
I want to know the detail of the multi-stage proper cleaning procedure for electroplating Ni on Glidcop part. Because, I try to electroplate thick Ni layer (over 100 microns) on the Glidcop part recently. However, the adhesion between Ni coating and Cu alloy substrate is very poor.
My questions is: what is the right pre-treat procedure to achieve a good adhesion?
Your suggestion is always anticipated.
Please comment
Thank you very much.
Yours sincerely, Yan Lin
Hi Ted
Your comment is very useful.
Too much thanks.
Yours sincerely, Yan Lin
- Wuhan China
A. Hi Yan. I would suggest that you plate 100 microns (0.004") or more of your nickel plating solution onto plain copper or a standard brass Hull Cell
⇦ huh?
panel and see what happens :-)
That is a very, very thick plating layer and it could well be that your primary difficulty lies not in adhesion onto Glidcop, but in severe internal stress in your nickel plating.
Luck & Regards,
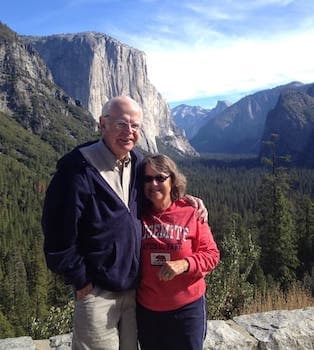
Ted Mooney, P.E. RET
Striving to live Aloha
(Ted is available for instant or longterm help)
finishing.com - Pine Beach, New Jersey
February 2022
Hi Ted.
Actually, I have plated the same thick Ni player on pure Cu and CuCrZr alloy substrate, and the corresponding adhesion is good. But, the thick Ni player (use the same plating procedure and parameters) on Glidcop only shows a poor adhesion. It is therefore reasonable to believe that internal stress is not the main problem.
Thanks for your suggestions again!
Luck & Regards,
Yan Lin
- Wuhan China
February 16, 2022
⇩ Related postings, oldest first ⇩
by Gautier Depambour
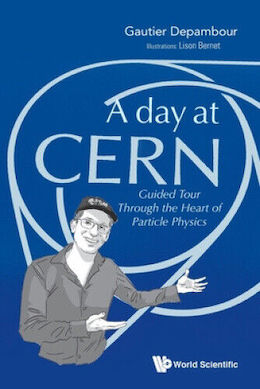
on eBay or Amazon
or AbeBooks
(affil link)
Q. I am a physicist leading a Technical Support group (on Materials and Mechanical Engineering) at CERN. We are witnessing a problem that we are not sure we really understand.
For the collimators of the new accelerator LHC at CERN, we braze cooling circuits on a Glidcop plate. For this process we use first a Woods bath to Ni them. Then we coat them with a layer of copper. In the first tries we coat the Glidcop with a thickness of Ni around 5-7 microns to insure the diffusion barrier. We understand that Woods bath are recommended for thicknesses of 2-3 microns however. We experienced two different situations:
1.- We put the Glidcop piece (around 1 m long,15 cm with) in our vacuum oven and do a normal brazing cycle (max temp around 815 degrees as if we were to braze with Ag and Pt). The cool down time is done gently, taking naturally over 10 hours. The result is quite ok and we do not observe any peeling off of the layers of Ni-Cu from the Glidcop bulk, although the Ni layer is 5-7 microns.
2.- At our contracted company the same Glidcop elements (same thickness of Ni and Cu coating)go through a similar temperature cycle, however from 400 degrees down, cool neutral gas is introduced in the oven to accelerate the cooling down of the pieces. The fall down of the temperature is then quite rapid. When doing that we observe a severe peeling off of the Ni-Cu layer.
My question is then: could this fast cooling down from 400 degrees down be the cause of the peeling off of the Ni-Cu layer ? And if yes, for what reason ?
Thank you very much.
CERN - Geneva, Switzerland
2006
A. First, what is "glidcop" ?
Based on what you are seeing, I would guess that the coating is cooling faster than the core is and causing the delamination by the difference in the coefficient of thermal expansion.
Another reason might be that company 2 has a very highly stressed plate relative to yours.
A Wood's nickel is very highly compressively stressed. This is one of the few cases that I would use a sulfamate nickel strike. Far less stress and because it is at a higher pH, it plates many times faster for the same thickness. With no brightener and absolute minimum antipit to get by, you should not have any problem plating over it, as long as it does not dry and passivate before the next tank.
This is a little knowledge and an educated guess. By no means fact.
- Navarre, Florida
2006
A. GlidCop® AL-25 is copper that is dispersion strengthened with 0.5 wt% ultrafine particles of aluminum oxide. It is produced using an internal oxidation powder metallurgy process whereby aluminum oxide is formed in the Cu matrix. The matrix is hardened while the Cu electrical and thermal conductivity are minimally lowered. The aluminum oxide particles are very thermally stable and remain effective in strengthening the copper matrix and resisting grain coarsening even after very long exposures to high temperatures as in brazing or high temp duty cycles.
GlidCop® is available with three different levels of Al2O3. Increasing the Al2O3 levels will increase strength but decrease conductivities.
Thermal shock is a standard way of testing adhesion of a plated layer. You say that both Ni and Cu peel together. Therefore it is the Glidcop/Ni interface that is suspect. The first thing to investigate is the pre-cleaning cycle. In view of the Al2O3 content of the Glidcop, it does not appear to be a promising substrate for obtaining perfect adhesion.
However I am surprised from your question that you have not tried the obvious experiment. Persuade your supplier not to force cool and see if the problem goes away.
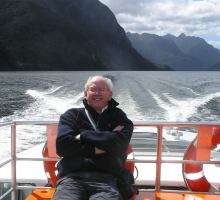
Geoff Smith
Hampshire, England
2006
June 14, 2012
Q. We are depositing Nickel over Glidcop (Copper with 0.15-0.25% alumina) for its vacuum brazing with copper for application in ultra high vacuum. Metallographic examination of as-electroplated nickel deposit exhibited sound plated layer with no porosity but after heating treating the electroplated component at brazing temperature (850° C. for 5 mins.) a continuous row of porosities were noticed at coating/substrate interface. This is responsible for its failure in helium leak test. We suspect that during electroplating, electrodeposit picks up hydrogen which after exposure to 850° C. diffuses to substrate/coating interface to form a series of hydrogen bubbles. Phenomenon of hydrogen liberation is well reported for nickel electroplating.
Glidcop part was subjected to multi-stage proper cleaning procedure before electroplating. The procedure adopted for nickel electroplating involved:
Watts' bath without additives
(additives are undesirable from brazing point of view):
Current density = 3 A/sq. dm
Air agitation: yes
Temperature = 55 - 60 ° C.
Plating time = 15 mins.
Kindly suggest remedial measures to avoid/limit hydrogen charging during nickel electroplating.
I have come across an old reference suggesting addition of sodium perborate in the bath (in place of hydrogen peroxide) for avoiding pitting or peeling of Ni deposit due to hydrogen liberation.
Please comment.
Yours sincerely,
- Indore, Madhya Pradesh, India
A. Hi all. Further comments on "Nickel plating/electrodeposition on alumina dispersion-strengthened Cu alloy" can now be found on thread 61388.
I recently had lunch with my old friend Berl Stein of NiCoForm [a finishing.com supporting advertiser]. Berl has spent much of his career electroforming very thin-wall nickel and nickel-cobalt bellows requiring successful helium leak tests. He related his decades of study of this issue and how he has solved it.
adv.
If anyone needs thin nickel or nickel-cobalt which will pass helium leak-testing, Berl can probably help.
Luck & Regards,
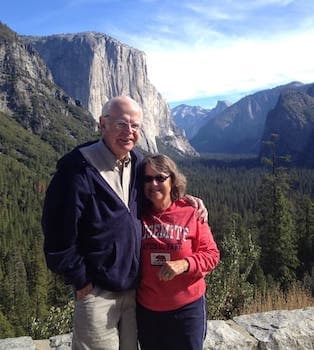
Ted Mooney, P.E. RET
Striving to live Aloha
(Ted is available for instant or longterm help)
finishing.com - Pine Beach, New Jersey
February 2022
Q, A, or Comment on THIS thread -or- Start a NEW Thread