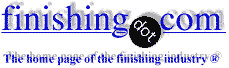
-----
Delayed Blistering in Alkaline Zinc Electroplating

Q. Hi.
Alkaline Non Cyanide Zinc. We get delayed blistering 4 weeks after plating.
Plated part looks perfect no sign of roughness, etc.
Hull Cell
⇦ huh?
test shows that brightener is not overloaded, i.e 5-40 ASF is bright, but the area of 60-80 ASF is semi bright . Does this rule out organic / brightener overload?
We have clean rinse before Nitric (Metex IT instead of Nitric), metex apparently cleans organics off surface. Then another rinse after Metex and DI water rinse before chromate.
I don't suppose incomplete rinsing after chromate can cause delayed blistering ?
Am not sure if blistering is happening in the chromate layer or the zinc layer
It is hard to diagnose because with delayed blistering like this we have to wait 4-6 weeks to see if blistering happens. Question - is there any step we can do right after chromating and drying, to see if this part will be prone to delayed blistering please, otherwise trial and error will take forever waiting.
Thank you.
- Perth, Australia
June 23, 2024
A. Hi Boris. How about a half-baked suggestion?
Although baking isn't appropriate for chromated parts, it is a good adhesion test and is often employed for other types of plating. If the parts are not valuable, baking a couple would at least reveal poor adhesion.
I'm not sure what goes on chemically or metallurgically that causes delayed blistering in alkaline zinc, but at least if you know you are starting that waiting period with good adhesion ...
Luck & Regards,
Ted Mooney, P.E. RET
Striving to live Aloha
finishing.com - Pine Beach, New Jersey
⇩ Related postings, oldest first ⇩
Q. We are having problems with delayed blisters in our zinc plated parts. The process is a rack operation with alkaline zinc, zinc content is 14-16 gr/lt and 120-140 NaOH. Client requires 15 to 35 microns and because of part configuration it is very difficult to plate, in order to achieve at least 15 microns in the lowest area, some areas are very close to 30-35 microns. We experienced delayed blisters 5 days after plating. 100% of parts where adhesion checked according to ASTM, tape test and were approved. Almost all the blisters have "popped" and we can see a black area underneath, but some blisters are "un-popped". What does the black area mean? We believe the pre-plating process is very thorough, parts are very clean. Base metal is Steel, hardened and tempered to 16-17 Rc, we don't consider this a hardened metal because of the low Rc value.
Some parts showed pitting in the finish; can these pits later develop into blisters?
We added agitation to the bath to improve efficiency and to renovate solution close to the plated parts.
Can bubbles from the anode be the culprit? There is a lot of gassing while plating is done. Plating at 4-5 Volts, 2 amp/sq. dm approx. for 60-70 minutes
Thank you for your help
plating shop - Mexico
2005
A. The problem could be excess brightener in the bath.
Anil Ramesh Barsani- Mumbai, Maharastra, India
Q. Yesterday my shop ran a bar through our alkaline zinc-iron electroplater line. It is a part we have run hundreds of times with little problems. Today I got to work and discovered that the parts had blistered post-production. This is the first time I have encountered this problem. I am not sure what caused this to occur. Stresses in the plating was my first thought but I don't know what could cause this. The part ran through trivalent black chromate after being plated. We have a new black on our line so I'm not sure if this could be part of the problem but I doubt it. Any insight into this problem would be appreciated. Thank you.
-Steve
Plating Shop Chemist - Grand Rapids, Michigan US
November 21, 2008
![]() |
SUGGESTED ZINC PLATING BOOKS
for Shops, Specifiers & Engineers ![]() from eBay, AbeBooks, or Amazon ![]() from eBay, AbeBooks, or Amazon "Alkaline non-cyanide zinc plating with reuse of recovered chemicals" by Jacqueline M. Peden (1994) from (U.S. EPA) ![]() from eBay, AbeBooks, or Amazon ![]() from eBay, or AbeBooks ![]() from eBay, AbeBooks, or Amazon ![]() from eBay, AbeBooks, or Amazon (as an Amazon Associate & eBay Partner, we earn from qualifying purchases) A. I doubt very much it's the chromate. Most often, this trouble is caused by organic contamination/too much brightener. ![]() Dave Wichern Consultant - The Bronx, New York A. Steve, process supplier - Great Neck, New York A. Dear Mr.Steve, ![]() P. Gurumoorthi electroplating process chemicals - Chennai, Tamilnadu, India |
Multiple threads merged: please forgive chronology errors and repetition 🙂
Alkaline Zinc Plating is blistering after two months
Q. DEAR ALL,
I'm Deepan. We currently face major blister issue, where the component is a plain sheet. The dimension of the component 300 mm length * 50 mm width & 3 mm thickness. The component is "s" shape. We are doing alkaline zinc plating; the variation in the regular plating is 1:2 where the component is fixed vertically;
In the month of December this material was plated, Major reason for blisters are IMPROPER PRECLEANING AND IMBALANCE IN ADDITIVES.
If improper cleaning may be the reason, the blister would form within 4 - 5 days, so we are suspecting an imbalance in brightener-booster additives.
If the addition level of Bri- booster level ratio changes, what would happen?
Pls help me to find the exact root cause for this issue.
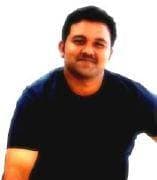
Deepan M
plater - Chennai, Tamilnadu, India
March 22, 2011
A. If they start as tiny blisters, I will guess that you are overcleaning/pickle of the steel, especially if it is a higher carbon steel.
If the blisters are larger, then it is normally under cleaning/ inadequate etch.
A thin oil film on the top of any of the tanks can also cause the problem.
- Navarre, Florida
A. Hi,
There may be many reasons in electroplating with terms of blistering problem, but in case of Non cyanide alkaline zinc plating, the delayed blistering is common and as Mr. James stated that if your base material is of some carbon mixture it will cause a blister problem; but as you mentioned it's sheet metal, so this won't be a problem; I strongly recommend you to discuss with your supplier about the additives you use, mainly the brightener or as you term it booster. If this brightening agent is higher you may face such problem of blistering, so try it by changing it after you give a carbon treatment. You don't need to wait for the delayed blistering you can check by building up higher thickness for just testing it and heat and cool the component -- I mean thermocouple test.
I guess it would be of help.
Regards
Praveen
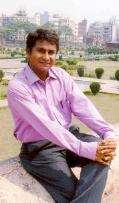
Praveen Kumar
plating process supplier
Mumbai, India
![]() |
![]() Deepan M plater - Chennai, Tamilnadu, India A. Too much secondary brightener and too little base brightener ![]() ![]() Sara Michaeli Tel-Aviv-Yafo, Israel |
A. Hi,
Oh yes, you can follow Ms Sara's advice with regards to the brightener/Booster, but anyway check the cleaning system in your line -- it's also very important factor for Non cyanide alkaline zinc plating., I am sure you have anodic cleaning, and also don't pass on too much of voltage, let it be within your recommended limit.
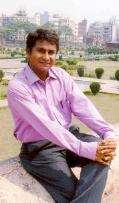
Praveen Kumar
plating process supplier
Mumbai, India
A. Testing by hot water quench will help you in identifying the problem in your end soon. You can try a few parts a day after plating. If it fails, it's organics issue.
S.V. Aurobindplating process supplier - Bangalore, India
Q. Dear Mr.S.V. Aurobind,
This hot water quench I heard it before, can you please explain briefly how this could helps, sir.
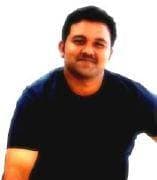
Deepan M
plater - Chennai, Tamilnadu, India
June 30, 2011
Multiple threads merged: please forgive chronology errors and repetition 🙂
Q. The blisters are observed not on the complete surface but on particular areas that is different part to part. Is the problem of blisters due to organic contamination behaving in the same or will it occur all over surface of component?
Sharma Narinder Kumar- Ludhiana, Punjab, India
May 7, 2013
9th Edition, Vol. 5
"Surface Cleaning, Finishing & Coating"
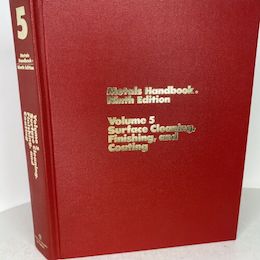
on eBay or Amazon
or AbeBooks
(affil link)
A. Dear Sharma: In our company we run alkaline zinc plating on
a daily basis; once in a while we have a delayed blistering problem. 95% of the time is due to:
A)The acid pickle getting weak, because of use.
B) Too much brightener in the bath.
To correct the problem,
A) Analyse and change your acid, if needed.
B) If you determined (using Hull Cell) that you have too much brightener in your bath, put steel panels in your tank and dummy it out 2 to 4 hours at 20 to 30 ASF.
I think this will help you. Good luck.
Nick Corderoplating specialist - New York, New York
A. Dear Sir,
The alkaline non-cyanide zinc plating is prone to delayed blistering. Organic additives are mandatory and bath cannot operate without them.The excessive accumulation of organic carbon in bath solution and consequently in deposit can result in blister formation.
Anodic alkaline cleaning prior to plating can help to some extent but additive chemistry is most important factor. Recently developed chemistry yielding more even almost equal LCD and High CD coverage/thickness has lesser tendency to blister. Highly bright deposits are likely to have blistering problems. Low exposure of substrate to mineral acids during pickling stage can help to minimize the blistering problem. Similarly higher carbonate level in bath beyond certain level reduces cathodic current efficiency adding further to blister forming tendency. In short the problem needs to be attacked from a number of angles.
Best of luck!
- Mumbai, Maharashtra State, India
Dear Nick Cordero /Dilip Thakur
Thanks for your valuable views. Definitely the problem occurred due to high organics from the brightener. After carbon pack and addition of ductilizer in spite of the brightener the problem is solved.
- Ludhiana, Punjab, India
May 22, 2013
Q. We manufacture fasteners, and regularly sub-contract parts for zinc plating & yellow passivation to various British Standards.
We have recently had some parts rejected on us from our customer due to blistering & flaking, however we are confident that the parts did not leave us in this condition. This would suggest to me that we are experiencing the same delayed blistering as mentioned previously.
Due to our customers' demands, we have asked our platers to increase the time in the passivation stage in order to offer a brighter finish.
Is it likely that the blistering is caused by excessive time in this stage, or would it be that the concentration of the chemicals in the bath is incorrect?
Many Thanks,
- Chesterfield, Derbyshire, United Kingdom
June 27, 2017
A. Hi,
Too much organics in your zinc solution. Carbon treat it. That is a common problem with alkali zinc.
If not, the steel is heat treated before plating.
Regards
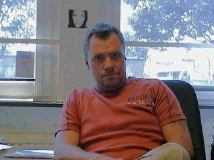
Anders Sundman
4th Generation Surface Engineering
Consultant - Arvika,
Sweden
A. Hi James,
Alkaline zinc peels because of too much brightener (organics) in the zinc bath, and parts are too thick, and parts are not clean (oil or grease coating on parts). Check your cleaning process.
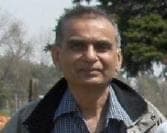
Popatbhai B. Patel
electroplating consultant - Roseville, Michigan
Ed. note: Peeling/blistering in alkaline zinc plating is a perennial problem! For yet more perspectives and experiences, readers may be interested in:
Thread 17233, "Alkaline Zinc Plating Delayed Blistering"
Thread 40868, "Zinc Plating with Trivalent Chromate is Blistering after Baking"
Q, A, or Comment on THIS thread -or- Start a NEW Thread