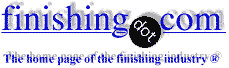
-----
Black spots in hot dip zinc coated wire goods
August 16, 2021
Dear Sir
Our company produces fasteners like bolts anchor bolts & stud bolts with hot dip galvanising. Problem is 'black spots'. How can we control? Please advise for solutions.
Best regards
Supervisor - Gujranwala
A. Hi Abubakar. We appended your question to a thread about black spots on hot-dip galvanizing. We have many other threads on the same/similar problem, including thread 56867 "Spotting, Staining, Blackening of Hot Dip Galvanized Finish", 57163 "Galvanizing surface defect (looking like black spots)", 61293 "Chrome-free galvanizing gets black spots" and others.
The problem is obviously ubiquitous, and you can read problems & solutions on all those threads. But, as you will see from other postings and pictures, the phrase 'black spots' can mean different things to different people, so it is usually best to send photos to mooney@finishing.com for posting here. But you will find many points to consider as you read these threads to enable you to sharpen up your query should you wish.
Luck & Regards,
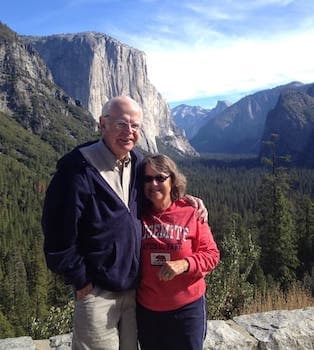
Ted Mooney, P.E. RET
Striving to live Aloha
(Ted is available for instant or longterm help)
finishing.com - Pine Beach, New Jersey
August 2021
⇩ Related postings, oldest first ⇩
Black Spots on Hot Dip Galvanized Pipes
Q. From a long time ago we have had the problem called "black spots" or "black stains" usually in the inner part of pipes. This happens more often in pipes of small diameter sizes (1/2" and 3/4"). We galvanize the pipes using the hot dip process. When our people who do the final revision of the pipe and they see this defect they reject the pipes and we have to re-galvanize again. Some hints will be helpful.
Morales Ernualdo- Apodaca n.l. Mexico
2001
2001
A. My comments may need further investigation by others more knowledgeable than me so kindly bear with me... My experience with hot dip pipes specially with small diameter 1/2 and 3/4 gives me several suggestions but I need further info from you, namely :
- what pre-treatment process do you employ before taking the pipes to be immersed in hot dip zinc bath?
- what type of metal is the pipes made of? Are they pickled with strong acids of what type? What about your degreasing?
- are these black spots only present inside the pipe? in particular which part of the pipe, near diameter opening or more in the middle of the pipe or random? How long are these pipes?
- how much time you use to remove the pipes from the molten zinc bath?
- what cooling system you use after you remove the pipes from the molten zinc baths?
- Are the black spots rough or smooth to touch? Do they look like burns or are simply spots that zinc didn't coat?
Larger diameter pipes are much have bigger openings to have the molten zinc flow out when the pipes are removed from the bath, so the molten zinc flow faster out unlike smaller diameter pipes. Also, check your zinc bath temperature if consistent on whole length of pipes in the bath.
Looking forward to your reply.
Anthony Austria- Philippines
2001
Q. Dear Mr. Austria:
Here are the replies to your request for clarification:
- What pre-treatment process do you employ before taking the pipes to be immersed in hot dip zinc bath? Degreasing alkaline, Rinse, Pickle, Rinse, Prefluxing.
- What type of metal is the pipes made of? Steel
- Are they pickled with strong acids of what type? HCl
- What about your degreasing? Alkaline type heated from 60 -70 °C.
- Are these black spots only present inside the pipe? Inside sometimes outside sometimes.
- In particular which part of the pipe, near diameter opening or more in the middle of the pipe or random? For the inside spots near the opening because it is the only part we usually check for outside in any part of the pipe but the outside spots are not a big problem.
- How long are these pipes? 6.4 meters
- How much time you use to remove the pipes from the molten zinc bath? 80 to 90 seconds
- What cooling system you use after you remove the pipes from the molten zinc baths? We use a solution of water and sodium dichromate.
- Are the black spots rough or smooth to touch? Usually smooth.
- Do they look like burns or are simply spots that zinc didn't coat? They look like burns black appearance.
Thanks for your help.
Morales Ernualdo [returning]- Apodaca NL Mexico
A. Dear Mr. Morales
As per my experience on the pipe galvanising line, these types of the black spot in inner side of the pipe may due to improper drying of pipe before entering into the zinc bath. The preheating must more efficient to avoid the same. My technical paper on it released in the Steel technology of Asia in the month of March' 99 edition, so, you may refer this article for solving the same problem.
Good luck.
G.D.PATANGE- Mumbai, Maharastra, India
2001
2007
Q. Dear G.D.PATANGE,
I have come across this thread and try to look the technical paper in "Steel technology of Asia" but unable to track this edition anywhere on net, please let me know from where I can get it and other technical papers and related literature on pipe Galvanizing.
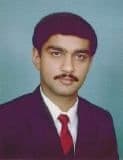
Qaiser Majid
Lahore, Pakistan
Multiple threads merged: please forgive chronology errors and repetition 🙂
Q. Sir,
I'm an importer/agent for Galvanized wire in Sri Lanka.Recently my client complained to me that about 200 Mtons of wire which he received through us was found to be unsuitable due to black spots found in various degrees.
The manufacturer/exporter refused to accept any liability though it was a production problem.
What would be the actual cause for this problem?
agents for G.I. wire - Colombo, Sri Lanka
2006
![]() |
A. BLACK SPOT ON G.I WIRE IS FOUND BECAUSE OF POOR PREFLUXING PROCESSES. THE ZINC POT ALSO SHOULD BE PROPERLY MAINTAINED. THIS IS A PURE MANUFACTURING PROBLEM AND CAN BE REMOVED TECHNICALLY. DR DIPANKAR SEN- Kolkata, India 2006 2006 A. Sir: Galvanizing Consultant - Hot Springs, South Dakota, USA |
Multiple threads merged: please forgive chronology errors and repetition 🙂
Black stains on hot dip galvanized Z purlin
2007Q. I wonder if you can help me to find out what is going on with a galvanised Z-Purlin that is showing surface defects as dark strips running parallel to each on one side of the piece only and at specific locations. Micrographs show that the coating is cracked and that the cracks run parallel to the substrate surface, more or less at mid coating thickness. The cracks never reached the base metal, so adhesion seems to be not a problem. Could you give any indication of the probable cause of this problem? I have to add that this is a new Purlin.
Thanks in advance for any help you can give me.
Mark Nuneshobby - Trinidad
![]() |
A. There are 2 main sorts of galvanizing, post fabrication hot dip galvinzing, and continuous sheet galvanizing. ![]() Geoff Crowley Crithwood Ltd. Westfield, Scotland, UK ![]() 2007 A. I think it is directly related excess aluminium amount. Check your molten zinc composition and increasing the zinc amount will prevent this appearance. Or this case can be related in Tin amount, but I am not sure -- you can check the tin amount in molten zinc. Due to dendritic structure (spangle formation) cracks can form. ![]() Hakan Esen, Material Engineer(BSc.) galvanizing plant manager - Bursa, Turkey 2007 |
A. Sir:
If you would post the zinc bath chemistry it could help to determine the cause of your problem. Also if you use a flux, then the composition of the flux solution could be helpful.
Regards,
Galvanizing Consultant - Hot Springs, South Dakota, USA
January 22, 2013
Q. Hi. I work for an automotive company and we are stamping some parts from hot dipped galvanized steel plate. On the latest batch of steel, we noticed two potential issues.
1) Some of the spangles are very dark in color. Does anyone know what might cause this and it it a cause for concern from a corrosion protection standpoint?
2) Some areas of the steel had very small spots. When viewed under a microscope they look very shiny. What might cause this and is there any cause for concern from a corrosion protection standpoint?
Thanks for any assistance.
Nick
product engineer - Detroit, Michigan, USA
A. Sir:
From your photographs it appears that the large spangle (crystals) are likely from alloyed elements in the zinc, for example lead, bismuth, tin, or perhaps antimony. In any case it is my impression that minimum spangle or no spangle is the usual for sheet galvanizing for forming into I presume automotive parts. The reason that low spangle is used is that it is normally a smoother coating and gives smoother finish when painted. The smaller white splotches seem to be "white rust" or sometimes called wet storage stain, which may interfere with painting. An assay of the zinc would be useful.
Regards,
Galvanizing Consultant - Hot Springs, South Dakota, USA
A. See there are two reasons; one is please check your flux -- 95% time it is because of the flux. Second, the black material should be checked after pickling if the surface is free from any defect such as Colour, Varnish,Oil.
Regards,
- Mumbai, India
February 23, 2013
Multiple threads merged: please forgive chronology errors and repetition 🙂
Q. Dear sir,
We are manufacturing Galvanized wire of 0.48 mm for detonators. We are facing the problem of black spots on the wire. Specifically in rain and cold weather seasons we are facing the problem. Flux temperature: how much we can maintain, and Zinc chloride, and aluminum chloride ratio. Please give the suggestion.
Regards,
- Hyderabad, Andhrapradesh, India
July 9, 2013
Q. Hello my name is dharma from Malaysia, right now I'm working as engineer in one of wire industry in my country, I face big problem that my wire many of black spots and makes my company business become down. Many of my customer rejected my order because of this problem. Can anybody help, suggest, advice, and give opinion about what should I do and check.
Thank you for your kind attention
- Kajang, Selangor, Malaysia
April 13, 2019
A. I assume we are discussing continuous strand galvanizing. A Lead kettle or fluidized bed with a caustic dip will remove the lubricant from the wire before pickling. Lubricant that remains on the wire is the most common cause of black spotting on continuous strand wire galvanizing. The acid by itself will not completely removed the lubricant. Another cause of black spotting is poor pickling-rinse-fluxing before the kettle. There is no information given on any of these issues, so I am just identifying the most common causes.
Bryan Cullivan- Beaverton, Oregon U.S.A.
April 15, 2019
April 17, 2019
A. If you fully test your flux solution, it may be possible to determine the source(s) of your black spots. For example: what is the pH of your flux solution, the density at room temperature, the % iron +2, the zinc chloride, the ammonium chloride, the non-traditional non-volatiles (e.g. NaCl, KCl, CaCl2, MgCl2, MnCl2). Do you use mono- double, triple, or quadra salt? From what country do you buy flux? What color is your working flux. How long have you used this same flux? Have you tried making up new flux? Is your drawing lubricant a mineral oil or an animal fat by-product? Is your caustic simply sodium hydroxide or a mixture of bases. Are you emulsifying or saponifying the drawing lubricant? If you post your test results perhaps solutions to your problems can be found.
Regards,
Galvanizing Consultant - Hot Springs, South Dakota, USA
May 20, 2021
Q. Hi,
I AM WORKING IN TRADING COMPANY AND WE SELL STEEL PRODUCTS. WE RECENTLY HAVE A CLAIM FOR THE HDG GOTHIC MESH. THERE ARE SOME BLACK SPOTS APPEARING ON THE MESH AND I WANT TO KNOW WHAT IS THE REASON FOR THAT. I AM ATTACHING PHOTOS:
ed. note: We added this enlarged view of the red-ish color area:
APPRECIATE YOUR COMMENTS/FEEDBACK.
MARJAN
- Sydney NSW Australia
June 23, 2021
A. This looks like flux staining.
The material is expanded mesh, cut from sheet and stretched in the manufacturing, it has cut edges that are not smooth. Also being mesh in the HDG process when removing the mesh from the liquid zinc, some of the mesh "windows" get a thin flake of zinc forming a bubble like film which solidifies to something close to aluminium foil used in household cooking. To prevent these actions, galvanizers throw sold flux powder at the work as it emerges from the zinc. The flux acts like a surfactant, and lowers surface tension, preventing the flakey thin "feathers". But if done too much, it leaves stains that look like this. The stains could have other causes, but on such material as this, I suggest its likely flux stains.
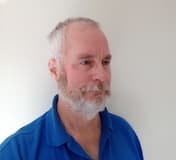
Geoff Crowley, galvanizing consultant
Crithwood Ltd.

Bathgate, Scotland, UK
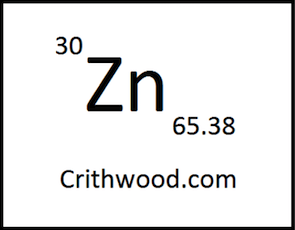
Q, A, or Comment on THIS thread -or- Start a NEW Thread