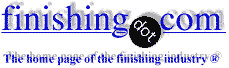
-----
Spotting, Staining, Blackening of Hot Dip Galvanized Finish

Q. What might be the cause of this discoloration?
The picture is of a section of a sculpture fabricated from 3 mm thick S275 mild steel. The view is of the top side, i.e., the part that came out of the zinc kettle first. Might this be flux staining?
Greg MeyerSculptor - Wilmington, East Sussex
December 16, 2024
A. This does look like flux staining. But a question is how did it get there. The steel is dipped in flux before being dipped in zinc. The zinc should remove all the water from the flux solution if it was not dried before immersion in the zinc. But excess flux, sometimes added to the steel by hand as a powder, can cause this type of staining. Often the flux sticks to the steel surface (galvanized), and if it the job gets wet the dried flux can recombine with rain water and run over the zinc surfaces. If the coating plant in question has a post zinc cooling tank (sometimes with passivation, sometimes just water), then this can wash off flux remnants.
The stain is an aesthetic issue, and doesn't mean the job is not galvanized. But a sculpture has a requirement for high aesthetics, and this doesn't look great. Did you discuss with the galvanizer? What did they say?
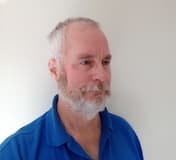
Geoff Crowley, galvanizing consultant
Crithwood Ltd.

Bathgate, Scotland, UK
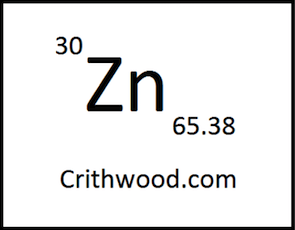
Hi Geoff, Thanks for your response. I have gone back to the galvanizer. After a bit of an argument they agreed to take the parts back and refinish them. The parts first go through a caustic bath, then a hydrochloric acid etch, followed by a flux dip, then into the zinc kettle. They do use a post zinc quench that has a passivization chemical added.
What does not show up very well in the picture(s) is the amount of dross/ash embedded in the finish. Of special note was the large amount of, what I presume were, dross/ash deposits I found on the inside of the sculpture. These consisted of soft crumbly variable sized "nuggets" ranging in size from a grain of coarse sand up to green pea size (1 mm - 10 mm diameter). In a weak moment the QC manager at the galv company admitted the sculpture may have gotten lowered to the bottom of the zinc kettle where it may have collected the debris.
The zinc kettle has a depth of 2.0 meters. The width of the sculpture is about 0.75 meters wide, 0.5 meters deep, and 3.5 meters long. It was lowered into the kettle with the 0.75 meter dimension in the vertical axis. I.E it was lowered in on its side.
Greg MeyerSculptor - Wilmington, East Sussex
December 31, 2024
⇩ Related postings, oldest first ⇩
Q. Hello, my name is Charles Stewart. I am a QC Inspector for a trailer mfgr. in Lebanon, Mo. The business offers powder coat and galvanized coating. Recently the galvanized finish has had dark spots that look like rain drops. Our customers do not like this. The spots are tough to remove.Scotts Brite Pads and water leave small scratches in the finish. It also speeds up the oxidation process. I tried using a weak solution of water and Clorox and then wiping dry. This turns the galvanizing black over a period of days. My question is four part:
1 Other than debris or carbon, what is causing the spots in the finish?
2 By using the Clorox (stopped when trailer turned black, about a week). Have I opened pores in the finish?
3 If so will they close?
4 If the problem cannot be resolved at the galvanizing plant, is there a product that will remove the black spots without damaging the finish?
Any suggestions would be greatly appreciated and thank you for your time.
employee - Lebanon, Missouri USA
March 1, 2011
for Engineers, Shops, Specifiers
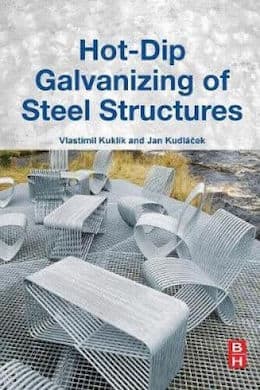
avail from eBay, AbeBooks, or Amazon
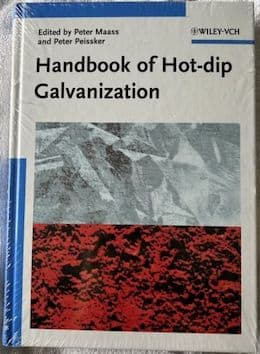
avail from eBay, AbeBooks, or Amazon
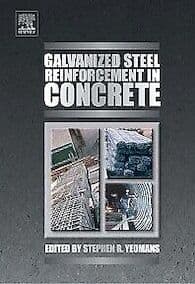
avail from eBay, AbeBooks, or Amazon
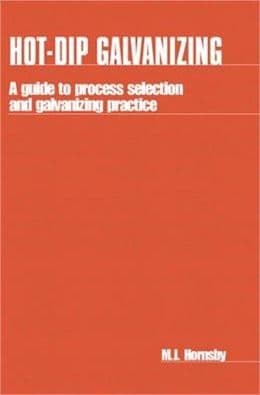
avail from eBay, AbeBooks, or Amazon
avail from Amazon
"User's Guide to Hot Dip Galvanizing for Corrosion Protection in Atmospheric Service" by NACE (1997 only rarely avail.)
avail from AbeBooks, or Amazon
(as an Amazon Associate & eBay Partner, we earn from qualifying purchases)
A. Staining or colour variation in galvanizing falls into two main categories.
1. Alloying variation. (a couple of your pictures might be this, but hard to tell).
Galvanizing is an alloying reaction between zinc and steel. The underlying part of the coating is alloy, which is dull grey, and the outer part of the coating is pure zinc which is initially bright silver. If allowed to, the whole coating will turn to alloy through its full thickness. By "allowed to", I mean that the steel remains at temperatures of about 450 or more. This is common in thicker steel sections, where residual heat allows the upper layer to also alloy. None of this is really avoidable, and is purely aesthetic, having no impact on corrosion protection.
2. Flux staining.
The majority of your images look like this.
An item to be galvanized is firstly cleaned chemically, typically in alkalis to degrease, then acid (hydrochloric or sulfuric) to remove surface oxides of iron. As the coating is an alloying one, it only happens with immersion in zinc of chemically clean steel.
Just before immersion in zinc, the item is immersed in a flux solution. This has similar effect to flux in other processes such as soldering, welding etc.
The flux is usually a mix of ammonium chloride and zinc chloride, and it is dissolved in hot water. Immersion of the steel and subsequent drying in air leaves a thin layer of these crystals on the surface.
During immersion this flux layer helps further deoxidize the steel, and the zinc at the interface between steel and molten zinc, and also acts as a "wetting agent".
But the flux can be to excess. Either wrong chemistry in the flux tank, or by the use of solid (undissolved) pure flux thrown by hand onto the zinc. This melts on the surface of the zinc into a black tar looking substance, and stains the work on withdrawal from the zinc.
ISO1461 is the international standard for galvanizing, and flux staining is a cause for rejection of the galvanizing. Flux deposits, ash deposits etc are not permissible. You might use a different standard, but its likely to say the same thing.
Ask your galvanizer which standard he works to, and ask to see that standard (its not a long document), and look for this, and suggest that this work doesn't comply, and ask him/her what should be done to resolve this.
If they don't know, or will not work with you to solve this problem, change supplier.
There is a solution to fix the problem afterward. Several proprietary brand citric acid based solutions are available that will wash this off, without causing the gross discolouration you have seen by using scouring pads.
Your scouring pad will not have caused "porosity" or similar, in fact its quite difficult to damage galvanizing, (except chemically).
Good luck
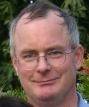
Geoff Crowley
Crithwood Ltd.
Westfield, Scotland, UK
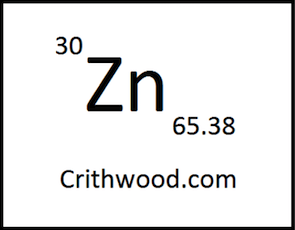
Q. Dear sirs,
I'm working in a company that galvanizes steels for power transmission towers. We're having a constant defect in our galvanized steel. It looks like black spots, but I believe it's something different and I don't know what it is.
We use these steps:
Acid degrease (10%-12%)
Chloridric acid (16% initial)
A tank for water rinse
Flux (29 °Bé)
Zinc (Zn 99,8%, Al <0,005%, Cu 0,12% I don't know why we have this much copper)
I really need some help because we're having this problem in all the big pieces.
Regards,
Chemical Engineer - Belo Horizonte, Brazil
May 14, 2013
A. Hi Daniel. I'm not a galvanizing expert, but we have many threads on line about black spots in hot dip galvanize, and people may describe different situations as 'black spots'' -- so a picture would probably help. Your email is bouncing, so I hope you see this.
Regards,
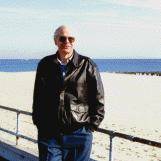
Ted Mooney, P.E.
Striving to live Aloha
(Ted can offer longterm or instant help)
finishing.com - Pine Beach, New Jersey
A. Dear Athayde,
Your problem is probably about flux baumé. Hold this baumé about 22-25 distance. Also it depends on product. Because other chemicals and foreign items aren't wanted in process. So they must remain in acid tank. Prolong the product's standstill.
- Bursa, TURKEY
A. Hard to say without the suggested pictures, but could be excess aluminium.
Your 0.005% sounds a bit high to me. I suggest <0.002 max.
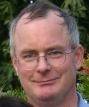
Geoff Crowley
Crithwood Ltd.
Westfield, Scotland, UK
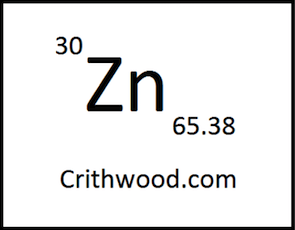
Q. Here are photographs:
Thanks,
- Belo Horizonte, Brazil
May 21, 2013
A. Looks like flux staining to me.
Have you measured the zinc thickness in the middle of a spot?
If it's normal, then I suggest flux stains.
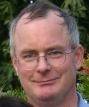
Geoff Crowley
Crithwood Ltd.
Westfield, Scotland, UK
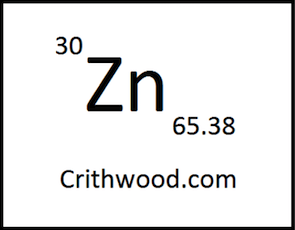
Q. Dear Geoff,
For this particular kind of piece, the zinc thickness needs to be over 100 µm (microns). In those black spots, the zinc thickness is about 30 µm and, after brushing with a wire brush, we could see the steel.
We found out that the inhibitor we were using may present a problem to the process because we needed to spend more time in the pickling solution. We stopped using the inhibitor and the black spots appeared less but it's still a constant problem in our line. We're facing about 1% of rework everyday because of this problem!
I hope you can help me with your advice.
Thanks!
- Belo Horizonte, Brazil
A. Given that these are now established as being bare patches with little or no zinc cover, then I suggest this is a problem with too short an immersion time in acid.
Do you use hydrochloric or sulfuric?
Not every part cleans at the same rate, and when the operator is too enthusiastic, and gets the job out of the acid too quickly, some parts will be still covered with oxides.
You do a trial by extending the time in acid by say 25%, for identified parts / jigs, and see what happens. If no improvement try +50%.
This simple test will check if this theory is right. If wrong, then we need to think again.
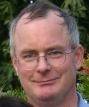
Geoff Crowley
Crithwood Ltd.
Westfield, Scotland, UK
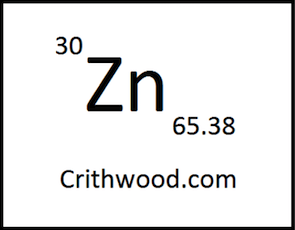
A. I believe you have a pickling problem. This could be from a multitude of things such as weak acid, high iron, too much inhibitor, contaminants on steel (such as oil, paint), too short dwell time in acid, poor racking, etc. I would take a batch aside in between acid rinse and flux that your pickle crew thinks is ready and look for spots. I suspect there will be areas un-pickled very similar to the post galvanizing problems you are having. You may very well have a flux issue as well, but I suspect pickling to be the bigger issue for this. always remember that the steel won't galvanize if it isn't pickled.
Angle iron like the ones in the photo should be able to pickle easily in 30 minutes. A good check-up of chemistries throughout your entire pickling/fluxing process should be done.
Houston, Texas
Q. Dear Geoff and David,
We solved the problem. It was the inhibitor that caused the problem, because the pickling rate was too slow. Only by stop using the inhibitor this kind of problem stopped.
My goal now is to make a research of the best inhibitor concentration in a way that we don't compromise the process and still maintain the inhibitor advantages.
One question about pickling time. I set up an experiment where I measured the speed of the reaction between the steel and the acid, but I don't believe the reaction speed is the same of the reaction between the acid and the rust!
So, is there a way to measure the reaction rate between the acid and the rust or, in other words, the speed that the acid clean the surface of the steel? Or the only way is visually?
Thanks for your help!
- Belo Horizonte, Brazil
July 8, 2013
Q. Hi,
We hot dip galvanise our own steel products and whenever we use 'weathering steel', we always see issues with black spot. We have tried variations in the time that the steel spends in the cleaner and pickling tanks, but this has not solved the problem. Our mild steel products process through the same galvanizing tanks without issue. It is just the weathering steel that gives us this problem.
Has anyone any theories in this?
- Scarborough, North Yorkshire, UK
July 17, 2013
A. Once saw this and found that light sweep blasting before processing eliminated the issue, but we never did understand the mechanism to know why.
(Assume you mean Corten, when you say "weathering steel"?)
But we've often wondered why people specify weathering steel, and then galvanize it?
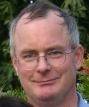
Geoff Crowley
Crithwood Ltd.
Westfield, Scotland, UK
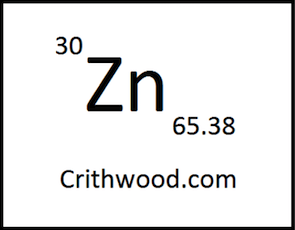
![]() |
Q. Hi Geoff, thanks for your comments. Yes we call it Corten steel. What do you mean by 'Light sweep blasting'? I've not come across this term before? - Scarborough, UK A. Sirs: Galvanizing Consultant - Hot Springs, South Dakota, USA |
A. "Sweep Blasting"
In shotblasting there are a variety of purposes / desired outcomes.
A standard for blasting often used is the one rating the degree of blast as SA2, SA2.5, SA3 etc. This refers to the amount of re-profiling of the steel and is altered by air pressure, grit size, length of time/exposure of any area to the moving grit etc.
SA2.5 is perhaps most common and is often described as having all traces of rust and scale removed, surface re-proofed/re-profiled, but not quite 100% white metal.
Sweep blasting is a light touch, where the blasting operator just sweeps the grit stream over the surface. It removes little, and re-profiles little.
But it seems to remove enough of something (I'm not sure what), that alters galvanizing effects.
For example in reactive steels (sometimes called Sandelin steels, and involving undesirable Si% composition), sweep blasting before galvanizing can markedly reduce the coating thickness from the galvanizing. I don't claim to understand the mechanism here, only experienced that it works.
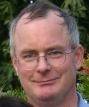
Geoff Crowley
Crithwood Ltd.
Westfield, Scotland, UK
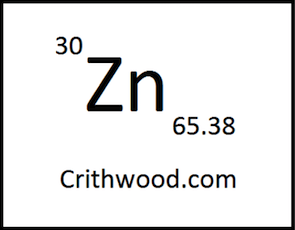
A. Phil,
If you are unable to sweep blast, here are some old-school and brutal methods for you:
1- Dip the material into zinc bath without doing any pretreatment, skim all the zinc, dip it into acid while it is hot, continue your normal process
or
2- Do the normal process, dip and withdraw the material after 1 min or so, sprinkle ammonium chloride on the material while on the kettle (especially to uncoated places) dip it again (don't forget, very nasty white fume will rise)
These methods are costly and unhealthy but sometimes useful when you are in a hurry.
- Doha, Qatar
Galvanised Poles with Black Patches
Q. We recently received lighting poles where we expected a good galvanised finished look to the poles similar to poles purchased in the past. These poles appear to have a lot of black staining which stands out to the silvery finish. Is this as a result of contaminates like too much flux or what is it that we are experiencing?
Will this get worse with time or will the life of the pole be reduced?
- Dublin, Ireland
March 23, 2015
A. Ed,
The vertical pole looks like silicon semi-killed steed (between 0.04 and 0.14% silicon; e.g. the Sandlin Curve). Upon closer observation there seems to be a "cook-off" problem. My experience indicates:
1) The product may be improperly pickled in HCl. HCl temperature must be above 70 °F for proper pickling.
2) Cook-off time in the kettle may be insufficient. The bubbles must nearly stop rising to the surface of the molten zinc.
3) Your flux likely contains non-volatile impurities which are not releasing.
I have submitted a manuscript titled "Nonvolatile Impurities in Galvanizing Flux" and submitted it to the EGGA for possible presentation at the Intergalva conference in Liverpool June 7.
On a scale from "1" to "10" your photos show a "1."
Answers to the following questions would be helpful in solving your problems:
What is the temperature of your HCl and what is the density of the HCl?
What us the density of your flux solution. (e.g., g/ml, Tw, or baumé)? And what is the temp. of the flux?
Galvanizing Consultant - Hot Springs, South Dakota, USA
A. I think there are several issues here.
1. There are what appear to be bare patches. This might be under-pickling (as Tom Cook says), which could be temperature of acid, (and its not warm yet in Ireland!), but that can be compensated for by longer pickle time in the acid. It's not warm in Scotland either, but we just pickle longer in winter.
This work does not meet the standard ISO 1461 if despatched with bare patches. It is not possible to be definitive from an image, but you could ask to have the thickness measured right on the black spot to see if it is really bare.
The standard does allow for repair of small bare patches by the use of zinc rich paint, but there are limits of size of repair, thickness of it, and the % of the total area that can be repaired.
2. The images indicate that elsewhere the coating is excessively thick. The second image with the "varicose veins" is one indication, and the porosity evident in another image (tiny pinholes even visible) is another example.
The most likely cause of this is the steel chemistry, which is an issue beyond the control of the galvanizer. It sounds like you purchased these, not being either the manufacturer nor the galvanizer. In that case you could ask the manufacturer, or perhaps the vendor for a certificate of conformity to the standard for such galvanizing (ISO 1461) and see what happens. If they refuse, be suspicious.
I think you have good grounds to ask for clarification that this galvanizing meets the standard. As a customer you cannot be expected to know the technical details above, you just want lamp posts that will last for maybe 50 years to first coating maintenance (depends on location and environment how long galvanizing lasts). That's why there are standards. So that the purchaser can have some assurance that why they buy is "right".
Ask for that assurance, and don't take any nonsense for replies.
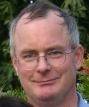
Geoff Crowley
Crithwood Ltd.
Westfield, Scotland, UK
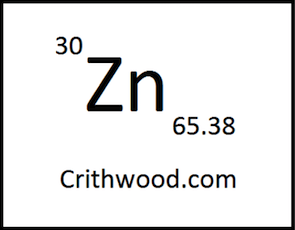
Q. I want to ask you what is reason of blackening the galvanized sheets after some days of manufacturing. Or I can put it another way, what is the reason of premature darkening of the galvanized sheets. What is the remedy of that problem? Is it related with passivation (Chromic acid) or alloys like Lead, Sb & Al or some other reasons?
Kantilal Trivedi- Baroda, Gujarat, India
January 2, 2016
A. Seems your problem is because of improper flux chemistry. Improper passivation problem can be seen as soon as the material cools down.
Nitesh Kumar Agarwal- Kolkata, India
Galvanizing rejected for poor appearance
Q. Client has rejected the grating due to poor appearance. Request you to please advise is it a valid rejection as per ASTM A123
METAL MANUFACTURING - Dubai UAE
June 27, 2017
A. As per any specification the goods cannot be rejected on the grounds of its appearance. Galvanizing is not at all a cosmetic coating. But it should look reasonably good, Galvanized in Zn 98 Min.
Umesh DalelaGalvanizers & Consultants. - New Delhi. India
A. You might ask the customer which clause of ASTM A123 they rejected the galvanizing under? It seems to be aesthetically poor, but the standard acknowledges that HDG isn't an aesthetic coating, it's a functional one.
The real issue in this sort of situation is often that the client reads a standard number off Wikipedia or some such place, then quotes it without having actually read the standard.
They have their own idea on what they expected, but didn't discuss and agree that expectation with the supplier (galvanizer), then blame the supplier when they didn't get what they thought they should have got.
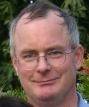
Geoff Crowley
Crithwood Ltd.
Westfield, Scotland, UK
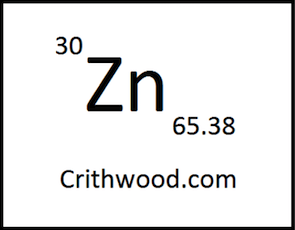
I think you nailed it Geoff! We have a number of threads here where a buyer wants to know what spec or standard to put on his P.O., but has no intention of spending the $30 or $50 to have a copy of the spec :-)
Regards,
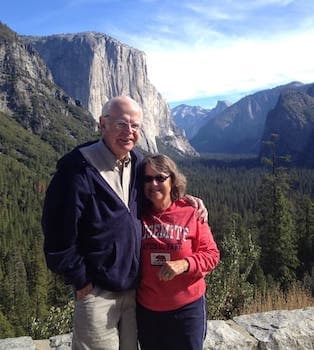
Ted Mooney, P.E. RET
Striving to live Aloha
(Ted can offer longterm or instant help)
finishing.com - Pine Beach, New Jersey
A. Mr. Dipu: the answer is your tank has too much of dross in it.
Vishal AgarwalINDANA STEEL PVT.LTD - kolkata, Westbengal, India
Galvanize Discoloration
Q. what are the common causes of discoloration of a galvanized metal?
Please see my photo:
- Rosario, Cavite, Philippines
October 16, 2017
A. Common causes of discolouration (like that in your image) include:
Variable steel chemistry
Variable dip withdrawal speed
Contamination on withdrawal from the zinc
Variable cooling after withdrawal from the zinc
Various different types of quench or passivate
Flux staining
Variable zinc chemistry (eg Ni, Pb, Al, Bi, Sn)
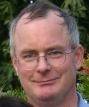
Geoff Crowley
Crithwood Ltd.
Westfield, Scotland, UK
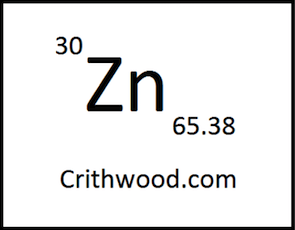
A. See in Asia this a common problem. Two primary reasons associated with this is:
1.High Zinc bath temperature.
2.High silicone content
Ideally bath temperature should not be above 450 °C.
Withdrawal rate has more to do with the zinc coating thickness.
- kolkata, Westbengal, India
A. Sirs:
The photo of the galvanized steel shows a result of zero aluminum in the molten zinc (as shown by the blue color). And the grey-black thick zinc is likely from reactive steel.
Regards,
Galvanizing Consultant - Hot Springs, South Dakota, USA
Thank you guys for giving your ideas :)
- Rosario, Cavite, Philippines
A. Dear
Along with the given issue I wish to add:
Remove the Galvanized goods from Galvanizing Plant as early as possible. Normally the Galvanizing Plant atmosphere is somewhat corrosive. And it affects the physical appearance of Galvanized goods.
And please mind it: Galvanizing Coating is not at all a cosmetic coating.
- New Delhi, India
Q. We have some problem for the delivered poles with some spots on the shaft of the poles. We want to understand what is the reason for this problem and how this problem can be solved.
- Delhi , India
November 4, 2018
A. From the pictures only (closer examination might reveal differently), there appears to be several issues here.
1. Liquid contamination. Some liquid, possibly flux has dripped onto the galvanizing, staining it. That its liquid is evident by the formation of the stain, the material has flowed under gravity.
2. In consistent bath skimming. During galvanizing the surface of the molten zinc continues to oxidise, and form a scum of zinc oxide. The steel being galvanized is withdrawn vertically through whatever is on the surface of the molten zinc, and if a lot of scum, then this transfers to the steelwork. Skimming of this scum minimises the effect, but inadequate skimming leaves it and it looks like your picture.
3 Black spots. Harder to determine this, but possibly a result of excessive Al% in the melt.
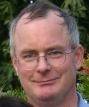
Geoff Crowley
Crithwood Ltd.
Westfield, Scotland, UK
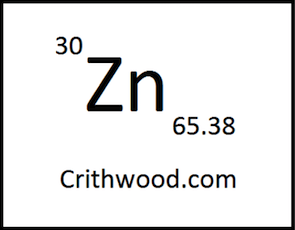
A. Sir: The black liquid is likely zinc chloride from zinc chloride rich galvanizing flux. The circular black spots are likely from zinc spattering from an adjacent pole.
Regards,
Galvanizing Consultant - Hot Springs, South Dakota, USA
Q. Please review these photos of steel expanded metal sheets. Panels were processed by hot dip galvanizing. The galvanizing has developed stains over time. We do know the panels were stored outside, uncovered and stacked on each other for approximately 6 months before install.
Supplier has indicated these are storage stains and stated stains should fade out as the corrosion layer matures. Can your confirm stains would in fact dissipate in time if storage stains? Is there a component that can be added to galv bath minimizing stains?
C Sayre- Tulsa, Oklahoma USA
October 28, 2019
A. The staining does look consistent with wet storage stains.
It is a combination of zinc oxides and carbonates, and forms where new galvanizing is stacked touching each other in wet conditions (such as outdoors in rain).
There is a treatment to slow down the incidence of this, but it has a limited lifespan. Mostly called passivation (even when technically it isn't), it can be by treating with chromate immediately after galvanizing,(passivation) or with a polymer at that same stage (not strictly passivation, more a clear coating). These give variable protection from west storage stains from a few weeks to a few months.
It is true that all galvanizing ends up the same colour eventually, and wet storage staining generally disappears with time. How long depends on the environment of the area, can be from 6 months, to 2 years in drier climates.
If aesthetics are a problem, west storage staining can be cleaned moderately well (but not completely) with dilute citric acid solution. Good galvanizers know about this and what to do.
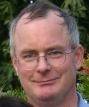
Geoff Crowley
Crithwood Ltd.
Westfield, Scotland, UK
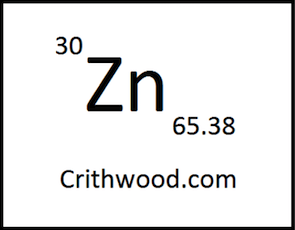
Q. Hi everyone.
We have been HDG etl items (angles, plates, class3 steel) for over 30 years.
We encountered some color differences/darker areas, and some cases yellow oxides, on the galvanized items Last year around July ... and after 2 weeks it disappeared. We thought our flux was bad and we reduced iron in the flux, and thought the problem solved.
A month ago these visual problems started again, and below is what we have tried:
- reduced alloys like nickel and Al to 0.
- prepared new flux bath
- dipping without flux -- only acid cleaning (%33 HCl prepared 70/30)
- dipping without acid cleaning (sandlasted and skip acid cleaning to directly flux)
- cleaning kettle with pure N gas after drossing.
- we test 1 sample/25 tonnes zinc ingot. In this case we have melted 10 zinc ingots and taken a sample from it. It's okay, no impurities.
- went to university about that problem. They say it's not in the literature and don't know what would be the cause.
Our kettle has 98.9-99.1 zinc, 0.700 Pb, normally 450 ppm Ni and 60 ppm Al.
Flux has a 1.5gr/lt iron. Salt percentage controlled every month. Baumé 25-27 pH 4-4.5. Double salt.
All dippings have been done at 450 -5 °C.
None of these tries solves that problem of ours and we can't find the root cause.
Is there anyone on the forum who has encountered same problem? I'm waiting for your valuable comments.
P.S. These darker areas are getting bigger with vertically hung items, with horizontal hung items it's more homogenous.
- Sincan Turkey
October 14, 2021
A. From what I see and what you describe, I wonder if you are using a passivation after galvanizing? and if that's Chrome based? It could be that this is over strength (too strong) and turning the material brownish. I remember a case of over strong chromic acid passivation which turned the silver HDG brownish. Do you passivate? Try just air cooling some bits and missing the passivation to check if this is having an effect.
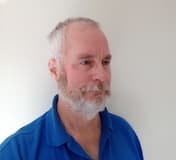
Geoff Crowley, galvanizing consultant
Crithwood Ltd.

Bathgate, Scotland, UK
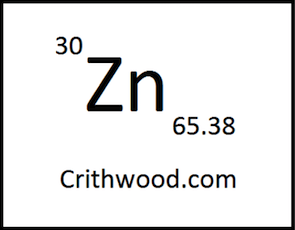
Q. I am a QC in charge of an organisation.
We have a hot dip galvanizing plant of fasteners. After hot dip galvanizing we saw that there are black spots on all fasteners.
We can't understand the reason.
Materials are perfectly cleaned and pre-flux, and we are using dichromate solution afterwards.
Employee - Howrah, India
July 16, 2022
A. The black spots could be from many reasons. To narrow down the possibilities, some questions to use.
• Is all work being affected or just some batches, or even some specific orders? (process issue or materials issue)
• Do the spots appear immediately, or develop after some time? (galvanizing issue or post galv treatment / storage / contamination)
• Is there zinc under the black spot? Can it be removed by scraping with a knife or sharp tool? (issue in pretreatment or in the zinc?)
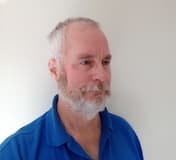
Geoff Crowley, galvanizing consultant
Crithwood Ltd.

Bathgate, Scotland, UK
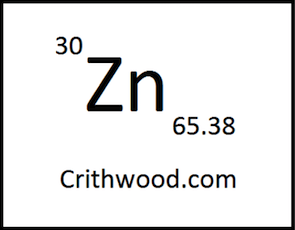
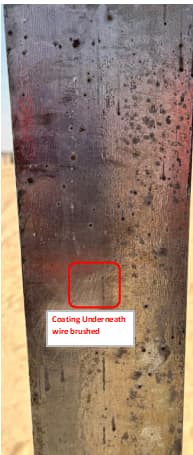
Q. We are galvanizer of structural steel. In last few months, we are facing problem of staining spots in some pieces of batch galvanized. There is no ash contamination. These spots underneath zinc coating. But, it is critical to wash out by SS wire brushed. These are found in some areas of whole surface. These are not ash contamination marks. We feel it is leaching effect.
We analyzed the pre-flux (Triple salt) solution. The results are as per below.
1) Zinc Chloride = 15.16% (Complexometric titration)
2) Ammonium Chloride = 15.75% (Kjeldahl method)
3) Free Zinc = 7.27%
4) Acid content = 7.69% as HCl
5) pH = 4.36
6) NiCl2 = 0.17%
7) MgCl2 = 1.24%
Advice how can eliminate such black/gray stain marks.
- Nagpur, Maharashtra, India
November 4, 2022
? Do you have a zinc analysis? Especially %Al dissolved in the Zinc?
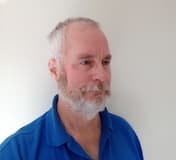
Geoff Crowley, galvanizing consultant
Crithwood Ltd.

Bathgate, Scotland, UK
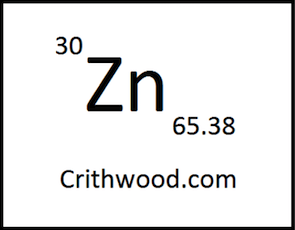
Q. Al % in the molten zinc bath is 0.0039. Generally, Al % is always observed between 0.0029 ~ 0.0040.
Those are not black spots. The zinc coating is available underneath the black stains. It needs big effort to rub by ss brush to make those fade. It is like suppressed because of heat in the material.
- Nagpur, Maharashtra, India
November 12, 2022
A. So we've eliminated excessive Al% in the Zn. And you've clarified that the black spots are on the surface of the zinc coating. That might suggest a flux/ash stain, but say it's not that? That would have been my next guess.
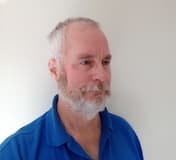
Geoff Crowley, galvanizing consultant
Crithwood Ltd.

Bathgate, Scotland, UK
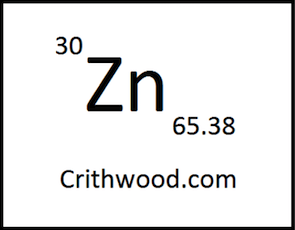
Q. There are yellow scale on the surface of the hot dip galvanized surface. Do you know what are this scales and how they can be removed or avoided?
Nesh Nesh
- Wichita, Kansas
March 30, 2023
Tip: This forum was created to help build camaraderie through sharing tips, opinions, pics & personalities.
The operator & those readers who want that might not engage with anonymous posters.
for Engineers, Shops, Specifiers
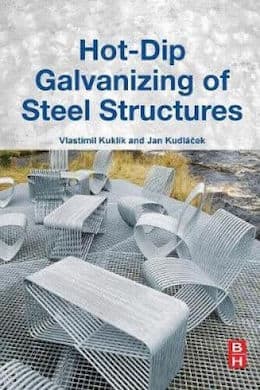
avail from eBay, AbeBooks, or Amazon
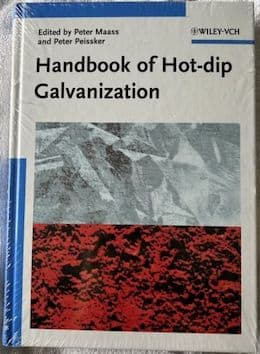
avail from eBay, AbeBooks, or Amazon
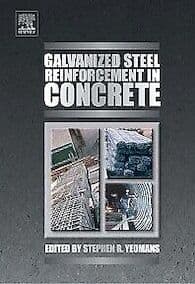
avail from eBay, AbeBooks, or Amazon
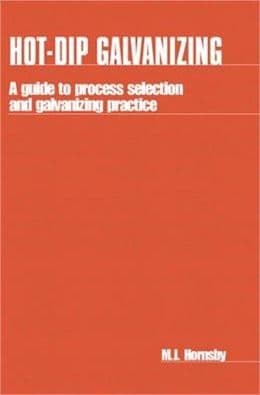
avail from eBay, AbeBooks, or Amazon
avail from Amazon
"User's Guide to Hot Dip Galvanizing for Corrosion Protection in Atmospheric Service" by NACE (1997 only rarely avail.)
avail from AbeBooks, or Amazon
(as an Amazon Associate & eBay Partner, we earn from qualifying purchases)
A. Hi. Usually it isn't possible to answer such a question from a single photograph without getting some follow-up data about the situation. Are you a consumer with such an item and wanting to know what you did wrong (if anything) in storing it, or an industrial buyer of a product line who has ordered your product to be galvanized and is unsatisfied with the galvanizing you're re-selling, or the galvanizing shop that is generating questionable product and needing to know what happened? Please give us that starting point, thanks.
Luck & Regards,
Ted Mooney, P.E. RET
Striving to live Aloha
(Ted can offer longterm or instant help)
finishing.com - Pine Beach, New Jersey
Q. Hi all. I just had some corrugated galvanized roofing delivered to my house for a siding project. It came with the black spots that look like mold in some areas. Haven't tried to clean yet. Wanted to get a professional's opinion on how to proceed. The plan was not to paint but that may change if can't remove spots. Thanks for your help.
Vince Di LorenzoHomeowner - California
July 1, 2023
A. Bit more info required or even better an image?
"Black spots" could be anything from something spilled on the zinc coating to bare patches in the coating. What size are they? How far apart? Covering the hole of each sheet? Both sides?
Try gently scratching one with something sharp to see if this is something on the surface of zinc (steel looks a slightly different colour of silver). If it's on the surface with zinc underneath, then likely contamination, something spilled.
If there' no zinc under the spot, and the spots are large, then you have faulty goods.
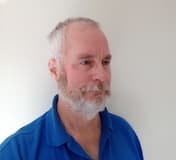
Geoff Crowley, galvanizing consultant
Crithwood Ltd.

Bathgate, Scotland, UK
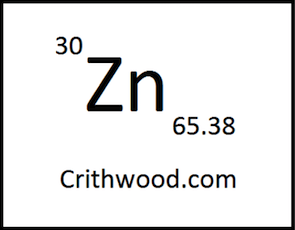
Q. What is the reason for flux/ash stain in dark grey or black?
Even though all the flux parameters are controlled within range, what imbalance in the preflux solution led to black stain?
- NGP
January 15, 2024
A. Hi cousin Pravin. I probably don't know enough about the subject to help, but while we are waiting for help, please read Geoff's reply to Charles' staining problem.
Also, please tell us your flux parameters, and send a few pics to mooney@finishing.com for posting here. Unfortunately, your question can be paraphrased as "all things are in balance; so what is it that is out of balance?"
Luck & Regards,
Ted Mooney, P.E. RET
Striving to live Aloha
(Ted can offer longterm or instant help)
finishing.com - Pine Beach, New Jersey
Q, A, or Comment on THIS thread -or- Start a NEW Thread