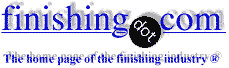
-----
Galvanizing defects: black spots / white haze

Q. Our company just established a HDG set-up and had just made up our baths (Flux and Zinc Bath) with proprietary products. We did several trials (~30 pcs) of our customer's product (about 20 * 40 cm * 1.5cm depth). But the results have been unsatisfactory.
Our latest Zinc Bath lab test result is as follows Al(<0.0005%), Cu(<0.001%), Fe(0.014%), Ni(0.015%), Pb(<0.015%), Sn(0.001%), Zn(99.9%).
We have done a total of 3 lab analysis on our Zinc Bath, and the Aluminum content varies greatly, from claimed being too high to too low ... reason given by our consultant was due to samples taken one at surface of zinc bath and other at deeper depth. We are experiencing several defects, such as black marking, black spots, streaks, lumps. I have attached a few photos of the imperfection of our finished goods.
Would be grateful if anyone could provide us some advice.
- Malaysia Penang [fictitious location]
February 2, 2023
Tip: This forum was created to help build camaraderie through sharing tips, opinions, pics & personalities.
The operator & those readers who want that might not engage with anonymous posters.
A. You didn't have any way to identify each image, so hard to reference them. But...
The two on the right and one at bottom left [ed note: B, D, & H?] are from poor skimming technique, nothing to do with bath chemistry.
The ash (scum on surface) that continually forms as a result of the zinc oxidizing with exposure to air, has been swept up onto the steel and that's what those lines and folds of surface zinc oxide are. That's avoidable with more frequent and closer skimming.
Some, those with black marks could be either excess aluminium (Al) or under pickling. (not in acid long enough and some oxides are left of the steel before it goes to zinc).
Excess Al (> 0.008%) can cause these. Al target is around 0.002-0.004% in the molten Zn.
But whosever told you about sampling technique has a good point. Al sits near the surface and if your Zn sample sent for analysis was taken deep it will be very different to taken from the surface. I'm amazed sometimes how little thought goes into taking a sample when we can get three decimal points or more of a % accuracy in the analysis, but no thought on how representative that sample was of the whole.
Your Ni looks low, but not so low to say you were not adding some. Did you add some? If you want Ni then 0.05 - 0.06% target. Its purpose is to modify the reaction between zinc and reactive steel (whose chemistry has awkward Si and P levels). The images with pimply finish could be reactive steel, and there's not enough Ni to stop that.
You can tell more about these black spots by scratching them to see if they are a deposit on top of zinc (like flux residues) or an actual gap in the coating - a genuine bare patch. If zinc under, then just remove the stain. If no zinc then look to acid pickling being under done, and or Al% being too high.
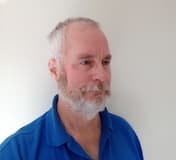
Geoff Crowley, galvanizing consultant
Crithwood Ltd.

Bathgate, Scotland, UK
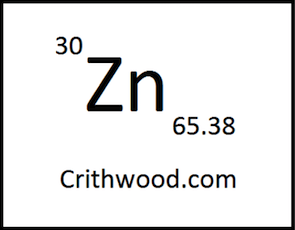
Ed. note: Sorry about lack of labels, Geoff. We've now added identification letters (location on page no longer works well in these days of cell phones & tablets where pictures flow to different spots depending on screen size). If readers don't see label letters please clear/empty your cache.
Q. Thanks Mr Crowley for your advice. Yes we did add nickel which was included in a proprietary additive product.
Regarding aluminium, should aluminium be homogenous within the zinc bath for it to serve its purpose, or being on the top surface of the zinc bath would do? For the Al target around 0.002-0.004%, which part of the bath should this sample be taken from? Our company uses shotblasting instead of acid pickling. As for the black spots, most of it seem to be removed easily just be scratching it. but how do you tell if its zinc underneath, by appearance or by thickness comparison with areas without black spots?
For lines and folds, which picture are you referring to?
- MALAYSIA PENANG [fictitious location]
February 7, 2023
A. Pictures D, B, H are from lack of skimming the surface during withdrawal of the steel from the zinc. This folds are zinc oxide. Once the steel is immersed in the zinc, and while they are still submerged, and when all turbulence is stopped, the surface of the zinc should be Swept / wiped / skimmed. A scum of oxide is continually forming, it must be swept back with a suitable tool to present clean shiny zinc, and then the steel raised. Target seed of raise is 1m/min. Then when fully out of the zinc, wipe the steel of drips before they solidify.
Shotblasting is never a very successful method of pretreatment in galvanizing. Chemical treatment using usually hydrochloric acid sometimes sulfuric, and rinses is far superior.
With the black spots: To test if its zinc under, use a coating thickness meter and measure the coating. All galvanizers should have one anyway, there are s=many manufacturers making them. Scrape away the black and measure the zinc underneath. If there is coating under the black spot, then its likely a flux residue, and could wash off with warm water. If no zinc under, then its a bare patch from unclean steel before dipping in zinc.
Take zinc samples from about 5cm under surface if possible.
If you're adding Ni, there's not enough. Some methods of addition are far more effective than others, and in each method some brands far more effective that other brands of same method. Powder the least effective, pellets not much better. Alloy and wax tablets good, via flux not great.
Target 0.05 - 0.06%
Al does not last long in zinc and needs " a little and often" additions. Many do 2 x / shift.
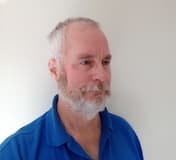
Geoff Crowley, galvanizing consultant
Crithwood Ltd.

Bathgate, Scotland, UK
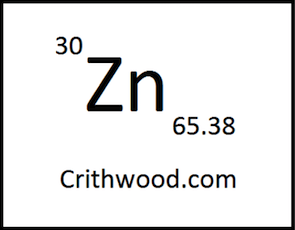
Q. Hi Mr Crowley, firstly thanks for your prompt replies to my enquiries.
When you say wipe the steel of drips, do you meant to knock/vibrate the excess zinc off the galvanized parts?
Few questions on flux residue, if the black spot cannot be washed off by warm water, does that mean it is not flux residue? Flux residue can result in either bare spot or coated zinc underneath?
Does insufficient nickel only cause aesthetic problem? If its not a criteria for rejection, I would not be overly concern about it, unless specially requested by our customer.
What happens to the Al when there is no activity in the zinc bath(zero production)? Is there any guideline to how much Al to be added per mass of galv. goods?
Do Zinc ash inclusions look rather similar to flux residue? Another observation I had while the parts are being galvanized was there were sparks on the surface of the zinc bath. May I know what is that phenomenon, and is it anything to worry about? Thanks.
Jackson Tan- Malaysia Penang [fictitious location]
A. Wipe the steel - yes remove the drips. Usually not by knocking but smoothly touching the skimming tool against the drips and wiping them off while still molten zinc.
Flux residue and bare spots are different. Bare spot is exposing raw steel, no zinc coating. Flux residue is flux on the surface of the zinc coating.
Nickel reduces the coating thickness in the cases of reactive steel whose %Si and %P cause it to be in excess. The result of no Ni in these cases leaves excess pimpling or coating thickness or both, sometimes so thick that the coating delaminates.
The Al when no production reports to the ash.
Ash inclusions as a true "inclusion" is rare. More often its a deposit on top of the zinc coating.
Sparks on the surface are hydrogen being evolved from flux reacting with zinc.
This is one of several reactions taking place...
2NH4Cl + Zn = H2 + NH3 + ZnCl2 :NH3
That H2 burns, but in the presence of ammonia
⇦ on
eBay or
Amazon [affil link] can sometimes appear as a spark. The chemistry happening on the surface of the zinc is quite complex with several simultaneous reactions happening. It's normal and not a concern.
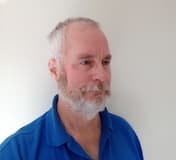
Geoff Crowley, galvanizing consultant
Crithwood Ltd.

Bathgate, Scotland, UK
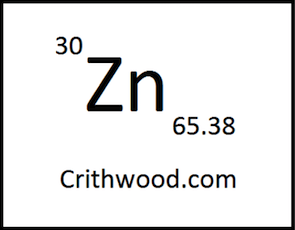
Q. Thanks Mr Crowley for sharing your knowledge.
Need to clarify, does "The Al when no production reports to the ash" means the Al will turn into ash and no longer useful and needs to be removed from the bath?
We have added 66Kg of ZAMAK/Brightener Master Alloys (zinc alloy with 4% Al) and changed our jig to stainless steel ones aiming to reduce dross(previously mild steel), which seemed to have very much eliminated the black spot issue. The samples are done @ bath temperature of 500 °C for 5 mins(supposedly to be 430 °C, but our thermostat had issue causing overheating). We found out the coated products had large range of thickness within a single piece ranging from 50 - 110 micron. Is this normal? What can be done to mitigate large difference in coating thickness within a single part.
- Malaysia Penang [fictitious location]
February 16, 2023
⇩ Related postings, oldest first ⇩
Q. We have a modern hot dip galvanizing plant.
For some days we've observed a defect in particular section.
Defect: unidentified material patches (pink colour) observed on surface only after pickling, & found that no acidic reaction done on particular patch (HCl Tank Strength 18%), after galvanising it look like black spot.
Some cases the patch over surface which can remove by fine grinding. But most of time it penetrated on surface which difficult to remove by grind & which created dip mark.
(Before fabrication it is not observed)
employee - India
May 16, 2011
A. Dear Nitin,
The problem you're facing is common in Hot rolled material like angles & channels.
Sometimes while rolling, some undercuts and laminations are developed in the material, which gets filled with thick Mill scale.These mill scales are found very hard to remove in pickling.
All I can say that there is nothing wrong with your process, the defect is in your steel.
I would suggest you consult your material supplier.
Regards.
towers - Jeddah, Saudi Arabia
![]() |
A. I agree, this looks like either slag inclusions in hot rolling, or laminations in rolling. ![]() Geoff Crowley Crithwood Ltd. Westfield, Scotland, UK ![]() A. Sir: Galvanizing Consultant - Hot Springs, South Dakota, USA |
(in German, French, & English)
by Dietrich Horstmann
on Amazon
(affil link)
Q. Hi friends,
We have problems about bare spots on galvanised surface of our products in continuous galv line. Dew point of furnace is about -36 but we have some problems with radiant tube (ss 310) some of them have leakage on weld lines. Is it possible this is the reason for bare spot? Also we change the Al % in zinc bath. and reduce from 0.3% to 0.2% but quality not more change. Does chromating process have any effect?
Please guide me.
- Tehran, Iran
December 24, 2013
A. Dear Mr. Mohammad Reza Ourang,
The dew point and Aluminum are not the cause of uncoated spots. It is possible for leaking radiant tubes to cause uncoated spots. The combustion mix in the radiant tube should be lean (4% oxygen in the exhaust flue gas) and this will oxidize the strip in the radiant tube section. An easy way to confirm this is to manually shut down the burners of the leaking tubes by shutting off both the air and gas valves. If the uncoated spots disappear, then the leaking radiant tubes are the culprit. Please remember that there are a lot more possible causes for such defects.
Happy New Year
Voo
- Shah Alam, Malaysia
Dust-like stain on galvanized steel
Q. Sir,
We are galvanizing plant of lighting poles in Thailand. Currently, our problem is that the poles developed a dust like stain about 3-4 days after galvanizing. The stain can be cleaned but will start coming back after a while. Our supplier suggests this is an acid corrosion, but since we never had this problem before, we believe it could be related to we started adding Zn-Ni alloy into Zn bath or changing passivation chemical from chromic acid to dichromate.
Here is Zn bath analysis (%wt):
Pb 0.9542
Cd <0.0001
Fe 0.0212
Cu 0.0062
Al <0.0001
Sn 0.0004
Ni 0.0335
We currently not sure what the problem is or how to solve the problem.
Immediately after galvanizing:
After 3 or 4 days:
Any suggestion would be appreciated.
Nattapong Suksudprasert- Bangkok, Thailand
August 23, 2017
A. This looks like "White rust", and your mention of the change in passivation sounds like the likely cause.
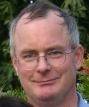
Geoff Crowley
Crithwood Ltd.
Westfield, Scotland, UK
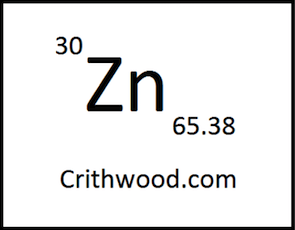
White shadow mark on hot dip galvanised material
Q. My situation:Dear Sir,
We have observed white shadow mark on hot dip galvanised material. The material size are 600 mm width and 1250 mm length plain surface & 450 mm width and 2500 mm length plain surface. We observed distortion on same materials. Our customer also inspected the material and rejected for the white shadow mark and distortion. We gave explanation for both NCs but our customer is not agreeing upon that.
Please advise can we control at galvanise end to eliminate the above NC during the galvanising.
Gopinath HarichandranEmployee - Thane, Maharastra, India
July 22, 2018
A. Those marks are NOT a cause for rejection of galvanizing if ISO 1461 is used as the standard.
The marks are caused by tension on the surface of the oxide payer as the steel emerges from the liquid zinc in the process. The zinc pool is continually oxidizing, forming a zinc oxide "scum" on the surface of the molten zinc.
The steel item being taken from that zinc vertically attracts some of that thin layer of zinc oxide and it sticks to the surface. But the rate of withdrawal of the steel exceeds the rate of deposition of the oxide, so the layer of oxide tears, leaving a gap where there's no oxide.
In time this mark will disappear, after perhaps 6 months outdoors exposure.
You could measure the thickness of the zinc at each point and find no difference.
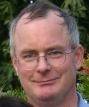
Geoff Crowley
Crithwood Ltd.
Westfield, Scotland, UK
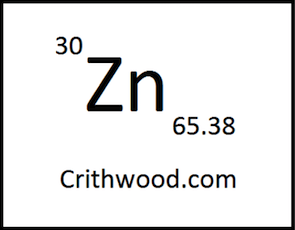
Q. Thank you for your reply.
But our customer is asking for very smooth surface on hot dip galvanized for aesthetic look, like electro-zinc plated or pre-galvanized. What can do to answer for customer. Please suggest any standard so we can show this standard to customer.
- Mumbai, Maharastra, India
August 18, 2018
A. Hot dip galvanizing should not be selected if an aesthetic look is aimed at. It's a corrosion protection coating, a functional coating.
The standard is already mentioned in recent post.
If you want the look of electroplating, then select that, but be aware that there's a huge difference in the corrosion protection afforded by these two quite different coatings.
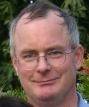
Geoff Crowley
Crithwood Ltd.
Westfield, Scotland, UK
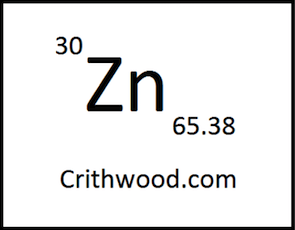
Thank you so much sir
- Mumbai, Maharastra, India
Surface defects in continuous galvanizing
by Kuklik & Kudlacek
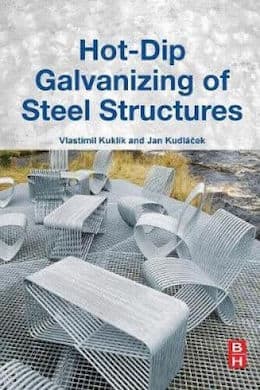
on eBay or Amazon
or AbeBooks
(affil link)
Q. Hi everyone,
I work in a continuous galvanizing line and we were surprised with a defect on the strip surface. It seems like it's dross adhered to the surface but it appears only in the sheet face that is in contact with the dip roll, which in some cases, causes some deformation in those spots, visible when the strip gets out of the pot and showing that it's provided by the contact between them.
We've already checked everything at the furnace, so our problem should really be in the pot.
The Al levels were a little unstable before the defect start to occur, but nothing that never have happened before, along these last years.
Another fact, that may help you help me, is that when we stopped the line for inspection the sink roll was very damaged (only the sink roll), presenting a lot of "holes" like pitting or cavitation's corrosion. The roll is 316L steel.
Has anyone already experienced this defect (only one face of the strip)?
Thanks,
- Porto, Portugal
July 10, 2012
A. Dear Mr. Pires,
For a defect that looks like dross and only appears on one side, it is usually zinc oxide (zinc dust
⇦ on
eBay or
Amazon [affil link]
falling on the moving strip.
Another possible cause is the accumulation of top dross floating inside the snout. Use nitrogen bubbling method to agitate the dross floating inside the snout. If there is an increased amount of the defect, it is due to the top dross inside the snout.
You mention you have been operating for some years now. It is possible that there is an accumulation of bottom dross plus scum at the bottom of the pot. Bottom dross / scum is mainly due to unstable Al control, unstable molten zinc temperature control or contaminated zinc ingots.
As for the pitting of the sink roll, have a discussion with your sink roll supplier. most probably the problem will disappear with the new rolls.
Best regards
Voo
- Karachi, Sind, Pakistan
A.
@ Joao Pires I think you should check some problems:
1- some alloy elements: Mn, Cr and Si that is present in zinc pot
2- Please check temperature of Top Roll at cooling Tower
3- I think you use some little Mg
4- protective gas Hydrogen and Nitrogen in Furnace.
Production manger - Dong nai, Vietnam
May 14, 2022
Q. I am facing problem of pin point black spot in continuous galvanizing line, particularly on the bottom surface (80% of area) and covering 20% on top in the form of small bunch. I have checked complete furnace, all parameters looks very healthy. Zinc bath chemistry looks perfect; I'm using antimony for spangle formation.
Pls suggest.
- HANOI ,VIETNAM
March 29, 2019
Q. Dear Sir,
we are manufacturing cable trays finish of hot dip galvanizing ,here after a month we observed black patches on the hot dip galvanized cable trays but fresh material we had not observed any black patches issue on fresh hot dip galvanized cable trays .
Please advise why it is happening.
Gopinath Nadar- Thane, India
May 19, 2022
Q, A, or Comment on THIS thread -or- Start a NEW Thread