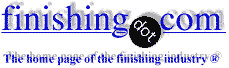
-----
Electroforming of Nickel -- Nickel sulphate & Sulfamate Experiments
2006
Q. I would like to recover the nickel from nickel sulphate solution (contain small amount of impurities, e.g. : 0.12 g/L of Fe), I do a small scale experiment and my experiment do not give me the satisfied result as the plating is thin (0.5 g obtained) and the Nickel that plates on the cathode is not pure (around 90% of Ni and 10% of iron).
The condition of the experiment was as follow:
- 3 voltage of power supply
- Stainless steel cathode and Pure nickel Anode immerse in 1000 ml of
- 65 g/l Ni in NiSO4 solution
- 10 g/L of boric acid used as Buffer.
- pH of electrolyte= 0.9 and temperature used = 40 °C.
- duration of electroplating = 7 hours
My aim for the experiment is to gain the pure nickel plating as thick as possible. Thanks for anyone who can give me comment on my experiment.
Metal Recycling - Malaysia
![]() |
A. SS anode will corrode and will decrease the purity of the plated material. Platinized titanium or similar insoluble anode would be needed. You need superior agitation as the plate rate will decrease as the amount of nickel in solution goes down. Your pH will rapidly go out of the desired range and basically stop plating. Raise the pH with a dilute caustic as required. Dilute or you will have a violent reaction. - Navarre, Florida 2006 A. Look up the composition of a Watts Nickel bath and try to replicate that with your chemicals. Your boric acid is too low, pH too low, temperature can be increased. You will need to remove the iron, so do a low current density plate-out. then you will be able to recover your pure nickel. ![]() Trevor Crichton R&D practical scientist Chesham, Bucks, UK 2006 A. If your objective is to recover Ni from NiSO4 solution, then you should use inert anode (such as platinized titanium anode), otherwise nickel keeps dissolving from anode into bath solution while plating out on cathode. ![]() David Shiu - Singapore 2006 |
A. Hi Hafel. Just to mention some 'semantics' in hopes that they might help you or others find what you're looking for faster: Recovering pure nickel from solution this way is often called 'electrowinning'; in fact that's how the anodes that are used in nickel electroplating are manufactured. When you are doing very heavy electroplating, with no intention of the nickel adhering onto the substrate, but you are planning to peel it off, it's often called 'electroforming'. So if you find yourself buried under too much inapplicable info about nickel 'plating', try those terms.
Luck & Regards,
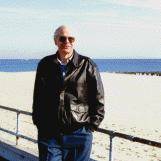
Ted Mooney, P.E.
Striving to live Aloha
finishing.com - Pine Beach, New Jersey
Multiple threads merged: please forgive chronology errors and repetition 🙂
High School Science Fair Idea: electroforming?
Q. Hello,
I am an 11th grade student looking for a science fair project. After searching for many hours I came across electroplating. This interests me not only because it involves chemistry but because it has a practical application. I was wondering if you could suggest a "High School Level" experiment. This could include varying the metals, varying the solutions, etc. I have access to my school's chemistry lab to conduct my experiments and can order the necessary chemicals, so technicality is not a problem.
Thanks for your time.
student - Middletown, Pennsylvania
2003
by Jay H. Newman
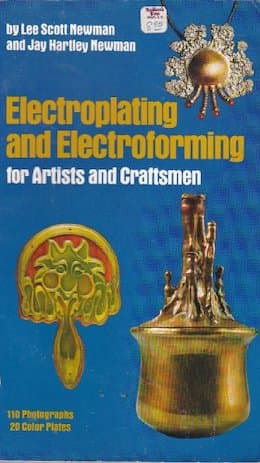
on eBay or Amazon
or AbeBooks
(affil link)
by Blum & Hogaboom
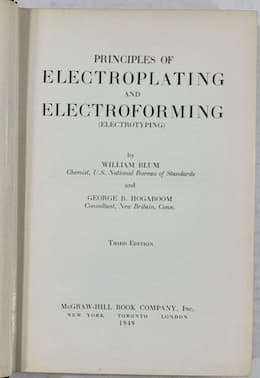
on eBay or Amazon
or AbeBooks
(affil link)
A. Our FAQs include a very simple zinc plating project and a very simple copper plating project, Adam. But these can be done by grammar school kids.
If you have advanced beyond that point, you might try copper or nickel electroforming. Electroforming is the same thing as electroplating except that the plating layer itself becomes the item you are making, and the object that you plated onto is discarded. With electroforming you can make parts that cannot be made any other way and which would baffle everyone who did not know how you did it. For example, machine a small aluminum rod or block with grooves or ridges of any sort you like:
Then copper or nickel plate it with a very heavy layer of plating. Dissolve away the aluminum with sodium hydroxide/caustic soda ⇦liquid caustic soda in bulk on
Amazon [affil link]
(under the watchful eyes of your chemistry teacher -- this part involves strong chemistry). And you'll be left with a hollow part with no seams or joints, but grooves/ridges that seem impossible. By the way, hollow gold jewelry is made by electroforming. Good luck!
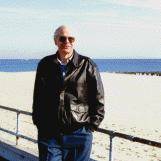
Ted Mooney, P.E.
Striving to live Aloha
finishing.com - Pine Beach, New Jersey
2003
![]() |
Chemistry experiment using sodium hydroxideQ. Hi, - Perth, Australia 2002 A. Hi, Stacey. As I explained to Adam, sodium hydroxide (caustic soda ⇦liquid caustic soda in bulk on Amazon [affil link] ) will dissolve aluminum, and that fact might give you some ideas. As another tack, please research how aboriginal people made soap, and then try your hand at making some :-) ![]() Ted Mooney, P.E. Striving to live Aloha finishing.com - Pine Beach, New Jersey |
Multiple threads merged: please forgive chronology errors and repetition 🙂
Treeing (dendrites) in Ni Sulfamate Electroforming
Q. I am a student attempting to create an electroformed Ni plate that is 4 x 10 cm and 1 cm thick. To do this I have created an acrylic frame to cover a Cu cathode, allowing plating only in a 4x10 area. At thicknesses over 1mm, I have been getting severe treeing around the inside edges of the frame and large nodules on the plated surface.
I am using a chloride free Ni sulfamate bath (Ni-speed) at 50 °C, using a magnetic stir bar for agitation. I filter my bath at 0.22 microns before each attempt. My surface tension is about 35dynes/cm and I have tried a current density of 10 and 18 A/dm2 with no change in dendrite formation.
I have added 0.2g/L of butyne diol. The plate became very shiny, but the dendrites still formed.
Any suggestions to at least decrease dendrite formation?
Student, Virginia Tech - Blacksburg, Virginia
2006
![]() |
A. In reality you are putting down one hell of a lot of nickel! The treeing and nodules are caused by microscopic asperities on the electroforming surface and these generate localised high current density spots; - once that happens the process starts to run out of control and produce unwanted growths. The art in electroforming is to try to prevent this happening. The science in electroforming is to get it right! Having looked at your conditions, they seem pretty good, although you don't give much detail of the bath composition. You may want to increase the temperature to the upper 50's or low 60's, but DO NOT exceed 70C. The asperities can be reduced by having a high filtration rate - I reckon on 10-12 tank turnovers per hour, but others will say less because filtration can take out additives. Nevertheless, my way has been quite successful. You will also get build up at the edges of the frame as this is an area of high current density - you may want top consider using a robber framework to help reduce it and divert the current back to the centre of the plate. I think that whilst you are trying to achieve such high thicknesses, you are bound to get surface asperities, so one way is to take out the electroform on a regular basis and machine the surface back to a smooth one. Then reactivate the nickel and continue electroforming. another alternative is to use pulse plating - this may well reduce the effects of the asperities, but it should be used with high filtration rates. Good luck. ![]() Trevor Crichton R&D practical scientist Chesham, Bucks, UK 2006 A. Your best chance will be to turn the cathode to a vertical position and increase the anode to cathode distance to 4 inches. - Navarre, Florida 2006 |
A. Ben, I misread your current density - it is way too high. I would recommend you run at 30-35 ASF (3-3.5 A/dm2), or even less. I presume the photograph is provided by yourself - it strikes me that one end is much worse than the other and the bad end shows a lot of "burning". There is something wrong with your anode-cathode relationship - either the electrodes are not parallel, there is a faulty contact somewhere, or there is electrolyte shielding. Good luck.
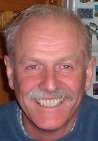
Trevor Crichton
R&D practical scientist
Chesham, Bucks, UK
2006
2006
Q. As for my bath composition:
600 g/L Ni sulfamate
16.5 g/L Ni Chloride (I added this since my orig. post)
35 g/L Boric acid
0.2 g/L SDS (surfactant)
50 °C
pH 3.6
In the meantime I have carbon treated my bath and discontinued the use of organic levelers. I have also decreased my current density to 8 A/dm2. This has left me with a fairly nodule free surface at thicknesses up to 2mm, except at the edges (high current density areas).
I will try the air agitation and a current density between 3-5A/dm2. My cathode position is vertical, sorry for the misleading picture. I cannot however filter my bath during plating as I plan to eventually add ceramic particles which I hope will become embedded in my Ni plate to serve as a reinforcement in the electroform.
I will experiment with a robber system, but today I tried adding a plexiglass shield between the anode and cathode. This shield has a rectangular hole in it, just smaller than the area to be plated.
Thanks guys,
- Blacksburg, Virginia
A. If you can't filter at high tank turnovers, you may well find further problems. The purpose of the high rate is to take out anything that may case asperities, as well as reduce the effects of ion depletion on the workpiece. You may want to consider setting up a very clean bath that has been highly filtered for some days prior to use and then add refined monospherical ceramics - any fines in it will cause you problems. You must also keep the tank form getting contaminated, so keep it covered.
You can still increase the solution movement by using a high pumping rate but not through a filter. Further benefit can be got from using adductors. These are available from Serfilco and have had lots of good things said about them.
Electroforming composites is very difficult and you will need to pull your ccd right back to (probably) about 20ASF (2A/dm2) or even less, irrespective of your using a high speed plating bath.
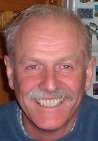
Trevor Crichton
R&D practical scientist
Chesham, Bucks, UK
2006
Q. Trevor and James,
Thank you so much for all of the help. I have been filtering the bath to o0.22micron prior to use and this has helped a lot.
One more question: Since I may need to use a ccd as low as 2 A/dm2, would it help to use a bath of lower Ni sulfamate concentration? Could this act to level my bath by making it easier for the solution to become depleted at the tips of nodules and dendrites, thus slowing them down?
Also, as a side note, are there any electroforming classes and/or internships that you could suggest?
- Blacksburg, Virginia
2006
A. Ben, In response to your questions, firstly, I am based in the UK (can't you guess by my "funny" spelling?!), so can only honestly suggest contacts here, but I know the AESF runs workshops in the USA. they are based in Florida, so have a look there. Alternatively, Ted may be able to suggest a few ideas.
Secondly, I would not advocate depleting the bath's nickel content as this may only cause more problems. You need to keep the ion concentration up in the immediate vicinity of the cathode. This is known as the Helmholtz Double Layer and its chemistry is critical to successful plating. The reason the high speed baths have such high nickel content is so they do not deplete this layer - you can only do so much with agitation! Lower ccd's do not need this sort of concentration, but then it is a matter of economics, not science. Good luck.
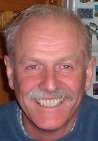
Trevor Crichton
R&D practical scientist
Chesham, Bucks, UK
2006
Multiple threads merged: please forgive chronology errors and repetition 🙂
Peeling problem with nickel electroforming
June 7, 2012Q. I am not a chemist nor am I a professional at electroforming. Circumstance has made me the person in charge of electroforming at my laboratory. I did not have a mentor nor a background in electroplating before I started.
I am operating the German-made electroforming unit.
The processing parameters are as following;
Temp : 52 ~54°
pH : 3.8 ~ 5
Total volume of electrolyte : 240 liters
Flow rate of electrolyte : 64 liters/minute
Concentration of Ni(NH2SO)2 4H2O : 345 ~ 355 grams/liter
Concentration of NiCl2 6H2O : 5 grams/liter
Concentration of H2BO3 : 35 grams/liter
One day I conducted few electroforming experiments and found that there were something wrong with my result.
The electroformed surface is not as good as before.
I do maintenance task regularly and do not know what to check for sorting out the problem.
For better explanation, I attached the pictures of the result.
Could anyone please check the result and give some feedback if anything has to be checked ( for example, electrolyte, cell, pH, Temp or else)
I have been electroforming for about one year and I have never had this kind of problem.
Any comments will be appreciated.
- Seoul, South Korea
A. Kim, this electroform, to be honest, is pretty rubbish. You seem to have a good control system in your bath, but I would recommend a couple of things. Firstly, the pH should be run between 3.8 and 4.3, certainly not as high as 5.0 for nickel sulphamate. Secondly, the filtration rate is rather high - I reckon you are doing about 16 tank turnovers per hour. I am a strong advocate of good filtration in electroforming, but I would suggest reducing it to about half this (8 turnover per hour).
I presume the temperature is in Centigrade and not Fahrenheit - if is it is OK, if it is fahrenheit, it is too low.
You do not mention the operating current density - I would suggest that your nickel bath would be best operated at about 20-30 ASF (2-3 A/dm2).
Next, I would check the bath composition - the deposit is clearly highly stressed and I wonder if you have accidentally added nickel chloride instead of nickel sulphamate. The bath is very basic and doesn't even have any wetting agent in it. I would suggest you check what the solution should be and make sure that all components are in there.
Next you should check the behaviour of the bath by a Hull Cell
⇦ huh?
- this will tell you if there is any contamination in the bath.
If you find anything wrong with the bath, in terms of wrong composition or contamination, I suggest you dump this bath and start again - it is producing such poor electroforms it is not worth trying to recover it. Your production manager will probably go apoplectic at the suggestion, but I think that is that is the best route in the long run.
Coming back to your filtration rate, is the return pipe from the pump anywhere near the plating area? It is possible that the high velocity of electrolyte coming from the pipe is impacting on the plating surface and causing surface disruption. The easiest option here is to move the pipe, if that is possible - if not, you will have to move the workpiece.
Hopefully, once you have worked through this list of suggestions, your problem has been resolved. Good luck
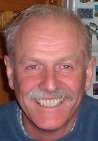
Trevor Crichton
R&D practical scientist
Chesham, Bucks, UK
Q. I am very thankful for your comments.
However, I have a question on your comment.
Could you please tell me the meaning of turnover?
Do you mean that I should decrease the flow rate of electrolyte by half?
Cheers mate! TA!
- Seoul, South Korea
June 20, 2012
A. Hi Kim.
A "turnover" is a filtration rate that is expressed in units of tank volume. If your tank volume is 240 liters, and your filtration rate is 64 liters/minute, it will take you 240/64 = 3.75 minutes to "turn over" the tank, i.e., to send all of the contents of the tank through the filter. Since there are 60 minutes in an hour, this is 60/3.75 = 16 "turnovers". It is recognized that this is just an "averaged" rate and that you are not necessarily sending each and every individual molecule of solution through the filter every 3.75 minutes.
Regards,
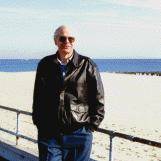
Ted Mooney, P.E.
Striving to live Aloha
finishing.com - Pine Beach, New Jersey
June 20, 2012
A. Hi
I think that temperature increases and maybe you are adding additive in your bath or adding waste to bath. But important for this problem is temperature, and you can give best electrodeposition in 1-1.5 A/dm^2. Other than this you have large stress. Good luck.
- Iran
June 29, 2012
September 24, 2020
Q. I have conducted an experiment of electroforming using stainless steel as a mandrel and nickel sulphamate as a solution using 1 L beaker [beakers on eBay or Amazon [affil links] . The size of stainless steel mandrel is 4 cm x 13.5 cm. Sodium Dichromate was used approximately 2 g and dissolved in 1 L of distilled water.
After 1 hour, mandrel was rinsed and it was detected that it builds up with crystalization at the side of the mandrel. Thus, using a sand paper to smoothen the side of the mandrel. Upon completion of sand paper, both side able to separate but the front surface are not the same as nickel foil.
It was also detected that anode basket rusted/corroded and effected the Nickel Sulphamate solution which turned cloudy and there was a residue.
Unsure whether this anode basket is made from SS or GI. Is the anode basket from SS rust? Is the solution able to use it again? Can an anode basket from SS can be used?
It would really be helpful if any of expertise can share any information and feel free to comment.
Thank you.
- JB Malaysia
A. Hi Sazlin. Is there a typo in your voltage? 20 volts seems impossibly high; are you sure it wasn't 2.0 volts (which sounds like a good number)?
The basket looks like it's stainless steel, and that is no good; it needs to be titanium.
Luck & Regards,
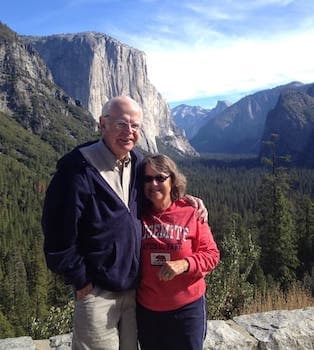
Ted Mooney, P.E. RET
Striving to live Aloha
finishing.com - Pine Beach, New Jersey
October 5, 2020
Q. Hi,
I have changed the material basket to titanium and have applied 2V, 0.2 A for the experiment. Here is my composition:
Nickel sulphamate: 350 ml
Nickel chloride: 10 g/l
Boric acid: 37.5 g/l
pH: 4.6
Temperature: 42 °C
Agitation: using magnetic stirrer
The stainless mandrel was cleaned using soap and acetone
⇦ on
eBay
or
Amazon
[affil links] Warning! Flammable!
. I also make a passivation layer using sodium dichromate 2 g/l for 2 minutes. After electroforming for 1 hour, the mandrel was immersed into a beaker of distilled water for 2 minutes. Unfortunately, the surfaces of electroformed nickel still look cloudy and dark.
Is there any usage of chemical after electroforming process? I managed to peel off the electroformed layer but the only issue that I'm facing now is the surface of electroformed nickel.
It would really be helpful if any of expertise can share any information and feel free to comment.
Thank you.
- JB Malaysia
Q, A, or Comment on THIS thread -or- Start a NEW Thread