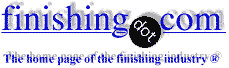
-----
TiN or ZrN coating on Brass using PVD
Q. Brass contains Zinc, which has a low melting point and is not considered for PVD processes that carry out TiN coating for decorative purpose. The PVD coaters generally do not have temperature below 200 °C and since zinc evaporates below this temperature there is peel-off of coating and even surface is destroyed. What's the best way to do a TiN PVD coating on a brass tool that has Zinc in it?
Kundan JavheriResearch, - Pune, Maharashtra, INDIA
2005
A. I confess I don't have any experience in the subject but it's been several days and you still don't have an answer. Maybe you could think in the line of dissolving the superficial zinc before (dezincification), then applying an intermediate layer of a higher melting temperature metal such as nickel, then apply the PVD layer on top of this layer. Obviously, lowest possible processing temperatures will help.
Guillermo MarrufoMonterrey, NL, Mexico
2005
A. The reason high temperatures are needed for PVD coatings is to keep the stress down in the coating while maintaining density. If you're interest in the PVD coating is strictly decorative, the coating can be quite thin, and stress will not be a problem. I believe the commonly-used process is to apply a thick layer of electroless nickel, followed by a thin layer of hard chrome, followed by a very thin PVD layer -- less than 0.5 microns -- deposited at very low temperatures, under 150 °C. ZrN is the preferred coating; TiN may still have stress problems, and doesn't provide as good corrosion resistance.
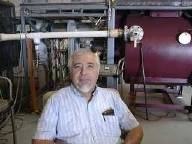
Jim Treglio - scwineryreview.com
PVD Consultant & Wine Lover
San Diego, California
2005
A. Sure, you can't put TiN coating (by PVD) directly on Brass due to Zinc poisoning. It requires a barrier layer that can avoid zinc poisoning and offer better corrosion resistance to the base material. Many people use Nickel layer of 10 to 12 µm (by Electroplating) as the barrier layer. But, you might encounter passivation of Nickel layer and peel off of TiN layer. To avoid this, on top of Nickel layer, a thin layer (0.5 µm) of Palladium-Nickel (PdNi) layer is deposited by Electroplating, before going for TiN deposition by PVD.
Regards,
- Bangalore, India
August 18, 2008
A. @Kundan Jhaveri The boiling point of zinc is 907 °C and melting point is above 200 °C, so this answer is not logical.
Hemang Doshi- Ahmedabad, Gujarat, India
January 12, 2015
January 2015
Hi Hemang. Although the boiling point of zinc is 907 °C at atmospheric pressure, it's 248 °C at 10-4 Torr, so the temperature might be an issue to be wary of in PVD/vacuum applications.
Regards,
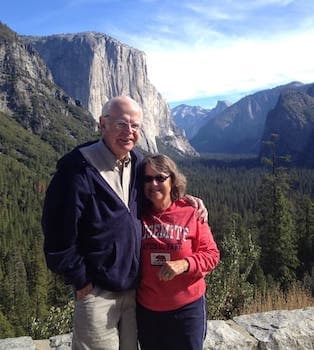
Ted Mooney, P.E. RET
Striving to live Aloha
(Ted can offer longterm or instant help)
finishing.com - Pine Beach, New Jersey
Q. 1. Can we do PVD coatings on brass material (alloy no. HPB59-1)?
2. Can we use DLC or CrN to coat on brass (HPB59-1) in order to solve PU sticky problem?
- China
July 25, 2012
A. Hi Danny. We appended your question to a thread where you can read that the answer is "yes, but only after applying layer of plating first".
Regards,
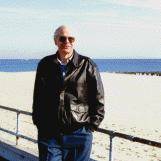
Ted Mooney, P.E.
Striving to live Aloha
(Ted can offer longterm or instant help)
finishing.com - Pine Beach, New Jersey
Q. To apply a bright brass PVD finish over clean non-scratched brass parts, should the chrome plating prep be "thin dense chrome" or "hard chrome"?
Donald Pepe- Granada Hills, California, USA
June 10, 2016
A. Hi Donald. You might inquire of the people who will be applying the PVD, but I think the answer is electrolytic or electroless nickel, followed by a decorative chrome layer, followed by PVD.
Regards,
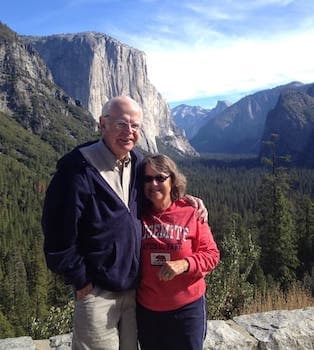
Ted Mooney, P.E. RET
Striving to live Aloha
(Ted can offer longterm or instant help)
finishing.com - Pine Beach, New Jersey
June 2016
A. The standard in the faucet industry is pretty much what Ted says -- electrolytic nickel base, a very thin layer of trivalent chromium, followed by the PVD coating. Note however that if the surface finish you seek it to be brushed or matte you'll want to deposit dull nickel. For the polished look you'll want bright nickel. For enhanced corrosion resistance you'll want a base of semi-bright nickel followed by bright or dull nickel.
June 15, 2016Check out ASTM B456 -95 for the nickel specs.
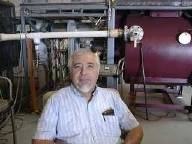
Jim Treglio - scwineryreview.com
PVD Consultant & Wine Lover
San Diego, California
June 10, 2016
Best temperature for TiN on steel, brass, aluminum, and ceramic tile
Hi Donald. Could you tell me what is the best temperature for applying TiN on steel? Is it different for brass or aluminum base alloy? Or ceramic tiles?
Esmaeil Shakib- Mashhad, Iran
August 21, 2017
August 2017
Hi cousin Esmaeil. We have found from many years of running this forum that abstract questions tend to chase potential responders away. Please try to explain who you are, and what you have done (or are doing) that is motivating this question about the best temperature for 4 different substrates. Do you have any experience in applying TiN to any of them? Thanks.
Regards,
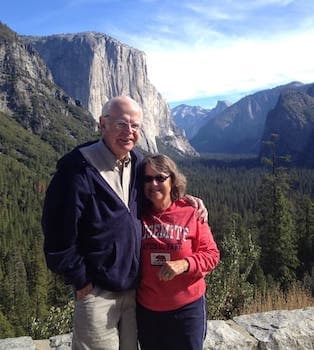
Ted Mooney, P.E. RET
Striving to live Aloha
(Ted can offer longterm or instant help)
finishing.com - Pine Beach, New Jersey
Q, A, or Comment on THIS thread -or- Start a NEW Thread