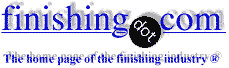
-----
Heating open-top tanks Q&A
[editor appended this entry to this thread which already addresses it in lieu of spawning a duplicative thread]
Q. Hello. I would appreciate your help with this. I am trying to calculate the BTU's of an alkaline cleaner of a specific density. Ultimately, I would like to be able to provide this information to others so they can determine the total amount of BTU's needed to operate the cleaner at a certain temperature. If other information is needed please let me know. Thank you for the help in advance.
- Cleveland, Ohio
August 25, 2023
A. Hi D. You can calculate the heat loss off the surface (which will be the bulk of the loss) and then off the four walls of the tank, and then -- if you wish -- add in the heat lost to heating up the cold work and racks/barrels that you're putting into that hot tank for a bit higher precision (most people would ignore this though).
If you continue reading you'll see that charts for those surface and wall losses are still available at
http://navalex.com/downloads/Tranter_Platecoil_Data_Manual.pdf
... but download it right now, it probably won't be available much longer.
Luck & Regards,
Ted Mooney, P.E. RET
Striving to live Aloha
(Ted can offer longterm or instant help)
finishing.com - Pine Beach, New Jersey
Q. Hello Ted. Update on what I am trying to accomplish. I am trying to determine how many kilowatts needed to heat an alkaline cleaning solution from room temperature to an elevated temperature. I am trying to show the potential energy savings in using a low-temperature cleaner compared to an existing cleaner at a higher temperature. Is there a formula to use? It does not have to be an exact number. Thank you for the help, Ted.
D Shoaf [returning]- Brunswick, Ohio
September 1, 2023
A. Hi again D,
A BTU (British Thermal Unit) is the amount of energy required to raise one pound of water one degree Fahrenheit, and a gallon weighs 8.34 pounds.
So if you have a 300 gallon tank, it holds 300 x 8.34 = 2500 pounds of water.
To raise its temperature from 70 °F to 170 °F (a 100 degree rise) would require 250,000 BTUs.
A kW-hour is 3412 BTUs, so it will take 250,000/3412 = 73.3 kW-hours to heat it.
Simple! Gallons x 8.34 x temp. diff / 3412 = kW-hours to heat it.
At 19¢ per kW-hour you've saved them $13.92 one time, let's call it $14 ... but probably not the answer you are looking for :-)
The problem here is that heating up the tank once is not the crux of the issue, keeping the tank hot is. And calculating that involves the more complicated procedures described in the previously referenced Tranter manual.
But consider this thought experiment. Suppose you heated the tank up in the morning, then turned off the heaters and started plating. Whether you operated for 24 hours or only for 8 hours, by the next morning the tank would have cooled down, not all the way to 70 °F, but to what, maybe halfway, 120 °F, perhaps?
So the next morning you'd need to spend $7 to heat the tank back up. So the final answer is that for a quick estimate you'll save them $7 a day, but it's probably more than that.
Another quick guess could be based on the kW rating of the heaters in the tanks. Electric heaters are expensive and are never greatly oversized; you can safely assume they are running more than half of the time, and therefore figure the kW-hours as the kW rating of the heaters x at least 12 hours.
Luck & Regards,
Ted Mooney, P.E. RET
Striving to live Aloha
(Ted can offer longterm or instant help)
finishing.com - Pine Beach, New Jersey
Q. Hello Ted. Thank you for the help. I should have been more clear in the beginning. This is regarding an industrial parts washer, not plating. The temperature is kept at a constant operating level. If we just focus on the amount of energy needed to heat the solution to the target temp, that is good enough. These are the values I have regarding the two cleaners:
Cleaner A
500-gallon tank: 482-gallon H2O and 18-gallon cleaner
Total weight of solution: 4,216 lbs
Starting temp: 80 °F
Final temp: 130 °F
Cleaner B
500-gallon tank: 475-gallon H2O and 25-gallon cleaner
Total weight of solution: 4,242 lbs
Starting temp: 80 °F
Final temp: 160 °F
Is there a way to calculate the BTU's needed to heat these two cleaners using the above information? Thank you, Ted. This site has always been so helpful.
- Brunswick, OH
September 2, 2023
A. Hi. The amount of cleaner vs. water really doesn't matter. It's 500 gallons of water as far as the calculations go.
So cleaner A requires:
500 Gallons x 8.34 x 50 deg. temp. diff / 3412 = 61.1 kW-hours to heat it once
And cleaner B requires:
500 Gallons x 8.34 x 80 deg. temp. diff / 3412 = 97.8 kW-hours to heat it once
I find it hard to believe that trying to sell this on the basis of an electricity savings of (97.8-61.1) kW-hour x 20¢/kW-hour = $7.33 for one-time heatup though. I still feel you're not looking at it right :-(
P.S. Tell your marketing people your feelings about "This site has always been so helpful". Thousands of other readers agree with you, and appreciate the supporting advertisers who make it possible for them, including process suppliers Accu-Labs, Inc. [a finishing.com supporting advertiser] & EPI / Electrochemical Products Inc. [a finishing.com supporting advertiser] :-)
Luck & Regards,
Ted Mooney, P.E. RET
Striving to live Aloha
(Ted can offer longterm or instant help)
finishing.com - Pine Beach, New Jersey
⇩ Related postings, oldest first ⇩
Q. I am a management consultant working with a large plating company with large tanks (up to 17'x5'x5') specializing in electroless nickel and hardcoat/anodizing. I have an extensive background in mechanical engineering, HVAC and energy conservation. I have easily identified huge savings potential by insulating steam lines and old ferrous tanks (as opposed to polypropylene) and using tank covers and/or floats (either balls or hexies). I have encountered overwhelming resistance particularly against floats. This resistance is based on the following concerns: (1) the insulation will get wet with chemicals and cause the pipes and other ferrous surfaces to rot, (2) the chemicals (particularly in the nickel tanks) will spoil if not fully ventilated, (3) the tanks cannot practically be completely covered (of course they can but some may have to be reconfigured), covers will not be used after a week, they will be mishandled and break, and they will generally take more time than they are worth, and (4) the floats will ruin the work if caught inside and not discovered. Though I concede that each issue may have some validity I can't help but conclude that the hundreds of thousands of dollars savings (gas, electric, chemicals, and water) more than compensate for the pain. Can anyone enlighten me? I would be interested hearing opposing views.
Gerald S. BermanManagement Consultant - Devens, Massachusetts
2005
A. Hi Gerald,
Ah, a Man of my own Heart ! Well done !
Energy conservation is to me a prime requisite ... and many moons ago I wrote a paper with the horribly exciting title of THE COST OF ONE SMALL INSIGNIFICANT CFM .
Have a look-see in the archives at #7794.
Yes, use PP balls ... available still I assume at up to 3" diameter. Damn the opposition !
Consider something else, too ... RECYCLE ...
This I've done even for chrome. But not your conventional mass transfer scrubber but a 3 micron horizontal blade type +++ inertial scrubber. Even Australia is copying this design.
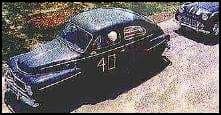
Freeman Newton [dec.]
R.I.P. old friend (It is our sad duty to
advise that Freeman passed away 4/21/12)
A. Gerald,
You have an interesting situation in which I have been involved in numerous times. The use of covers undoubtedly provides a tremendous potential for energy savings, including tank heat/cooling loss reduction, Exhaust CFM Reduction, Tempered Makeup Air Reduction, and more. The difficult part is convincing people to change the traditional way of designing a line and its required exhaust system, which is usually designed based on open surface tanks.
There is an article about energy conservation in the latest Nov. Issue of Metal Finishing Magazine that you may find interesting.
If you're looking for some hard data on energy savings, the EPA has an Environmental Technology Verification (EPA/ETV) Program which has studied the use of NON REMOVABLE mechanical covers on a particular tank line.
Retrofitting an existing line with covers integrated with the exhaust system is possible and proven to save lots of operational $$. But it must be done by professionals with extensive knowledge of the process, production requirements, and pollution control exhaust systems.
- Forest City, North Carolina, USA
A. Hi again Gerald,
Kyle said that retrofitting had to be done by professionals. Um. Is that so? After all, YOU are a true professional in reducing energy costs more so than any plastics' fabricator, or me, judging by your text.
I still think that, in certain cases, air recycle is a hellish good idea.
Let's take G.M. and Delco Remy for an example ... where they charge batteries containing 36% sulfuric acid.
What do they do? They recirculate the air BUT l0% only goes to atmosphere to get rid of excess H and O. That was THEIR idea.
Their chief chemist at their Oshawa plant didn't believe in mist eliminators ... so we made him a mini unit to test out.
Then ... a year passes by after the big installation ... and the test results stated that the eliminators had met and beaten the EPA standards and were far better than the crude mesh type scrubbers. Then Delco Remy in Anaheim and in Muncie copied this design. I vunder vy !
Food fer thought, eh? After all most ambient temperature emissions of acids are neither gases nor fumes, as the text books would have you believe, but invisible droplets.
And just now the mega gold mine of Yanacocha in Peru is ONLY using these designs in their labs ...+ PERpLAB fumehoods and plastic fans.
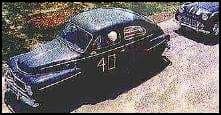
Freeman Newton [dec.]
R.I.P. old friend (It is our sad duty to
advise that Freeman passed away 4/21/12)
A. Hi once again, Gerald,
Whilst flipping through GOOGLE on the subject of the 4th Glosters, my father's old regiment, I came across thread 31383 "Solutions to heat loss from plating/rinse vats" ... which might be of some interest to you.
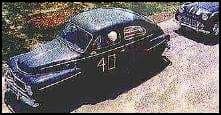
Freeman Newton [dec.]
R.I.P. old friend (It is our sad duty to
advise that Freeman passed away 4/21/12)
Ed. note: Thread 17485, "Tank Water Evaporation Estimates", may be interesting as well.
A. Re. the "Insulating the tank" issue. Double wall tank with insulation in the middle solves that issue. Standard configuration for steam jacketed kettles.
Jim Feig- Mansfield, New Jersey
Multiple threads merged: please forgive chronology errors and repetition 🙂
Heat Loss from Phosphating Chemical Tank
Q. Dear Sir,
I am currently running Zinc Phosphating on pipes with spraying type. The phosphating chemical is applied onto the thread of the pipe through spraying method. However, I have experienced tremendous heat loss from the phosphating chemical tank. I would like to know if there is any method to prevent the heat loss. What shall I do to the chemical tank in order to prevent heat loss? Please advise. Thank you.
Oil & Gas - Malaysia
2007
A. The principle of cooling towers, of which countless millions are in use, is that if you spray a solution there will be tremendous evaporative losses which cause dramatic cooling. So, as far as researching the principles, if you get a book on cooling tower design you can learn how to make your system more efficient (or in your case hopefully less efficient) in cooling. The most dramatic improvement you can make is probably to seal in the humidity in some fashion because it is evaporation into a drier environment which is causing most of the loss.
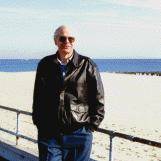
Ted Mooney, P.E.
Striving to live Aloha
(Ted can offer longterm or instant help)
finishing.com - Pine Beach, New Jersey
A. Dear Sir
If the heat loss is happening inside an open storage phosphating tank you can use solid polypropylene balls which can withstand high temperatures and form a blanket on the surface of the tank and thereby arrest the fumes which escapes thereby reducing the temperature and requires more heating. Also cover up the sides of the tank with asbestos rope or cloth. Phosphating is exothermic process whereby the heat is lost by evaporation. Solid PP balls are the best solution if the tank is open to sky.
C S Rajaram- South India
A. Hi C.S. Rajaram
I had only in my limited experience (40 years in the heavy plastics fabricating field) heard of hollow balls for reducing heat loss ... from 1"Ø to 3"Ø ... which would be far less expensive than solid ones BUT sometimes they perforated and sunk to the bottom. I used to like 2 layers of them.
HOWEVER, some years ago a certain Indian manufacturer came up with solid PP 'floats' which he called, going by memory, flying objects or space doohickeys ... and even sent me one.
So try the local industry, OK ...but insulating the tank is always a good idea.
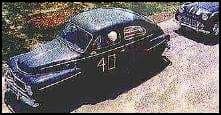
Freeman Newton [dec.]
R.I.P. old friend (It is our sad duty to
advise that Freeman passed away 4/21/12)
A. If you are talking about the loss of temperature of the phosphate during the actual spraying operation of the Zn phosphate onto the pin end of the pipe (Usually the box end is Manganese phosphate). Try flood coating using a pump and manifold system rather than spraying, we've used this successfully in a number of plants for both OCTG and drill pipe for both Zn & Mn. A lot less heat loss than spraying.
Regards,
- Lowestoft, U.K.
Multiple threads merged: please forgive chronology errors and repetition 🙂
Heating vats to temperature
Q. I am a manufacturer of industrial heating equipment, and I am not very familiar with chrome plating or any plating processes. A customer of mine was interested in using tankless water systems to heat their vats in the process through a radiant system. My concerns are heat loss, and being able to provide enough radiant heat to bring X process to Y degrees. I have not received too much information at all on this project at this time, but I am trying to determine if anyone can shed some light on what temperatures are required in the plating process for rinse applications or plating. Any HELP would be great, as this is a new venture for our company.
Robert Lisowskiindustrial heat systems - Woodstock, Illinois
April 15, 2008
A. Hi, what type of tanks /solutions are you hoping to design heaters for ?
you mentioned chrome vats, the type of heaters used in our vats are electric portable type. we wouldn't use a radiator type heater incase it burst in the tank and overflowed the chrome solution causing effluent problems, etc.
also you would need to know what materials to make the heaters for each solution as the chemicals could dissolve them.
also each solution will need different temperatures.
can you explain tankless water system, as I'm not sure what it is . and I may be able to more help
thanks
- Essex, UK
May 1, 2008
Multiple threads merged: please forgive chronology errors and repetition 🙂
How do I size a low pressure hot water boiler system for my plant
Q. I am moving from electric immersion heaters to a hot water boiler and really don't know how to size it. I am expanding my operation, so I cannot simply look at the heaters I have been using. Where can I get the best information on sizing my system and the heater coils for my tanks.
Thanks in advance for the help
Derek
Plating shop owner - Dalton, Georgia US
March 20, 2016
A. Hi Derek. In easy cases, it's easy: a BTU is the amount of heat required to raise one pound of water by 1 degree F. So if you calculate the gallonage of each heated tank, convert it to pounds, multiply by the difference between the operating temperature and room temperature, and divide by the heat-up time, you have the BTUs/hour that the boiler needs to provide. If you size things based on a two-hour heat up time, you'll almost always be safe. Three-hour heatup time, and you'll still often safe.
If you extend the heat-up time to say 6 hours, the boiler is a lot smaller, but things can get dicey. The problem is that there are operational heat losses as well as heat-up losses, and they can start becoming very significant if you don't have the safety factor of 2-hour heat up. Very hot tanks lose a lot of heat to evaporation, for example; all tanks lose heat thru the sidewalls; heavy cold parts or drag-in of a lot of cold water can suck up a lot of heat, etc.
Tranter Platecoil has a helpful design guide at
http://na.tranter.com/Documents/Platecoil%20Data%20Manual.pdf
and their competitors like Mueller offer similar guides.
Hot water heat is best when the tanks aren't too hot, and the material of construction of the heating coils is inexpensive. The hot water doesn't have the "phase change" that steam has, so the coils must be bigger, and depending on the operating pressure, the water is probably not as hot as the steam either. It's tough to heat a 190 degree soak cleaner with 195 degree water because there is such a limited temperature difference. Those coils are, at least, plain steel though. If you have a very hot tank with aggressive contents that requires Teflon coils, the cost of the coils can kill you.
Regards,
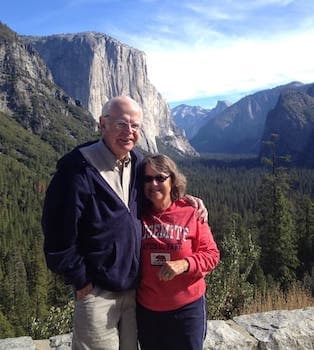
Ted Mooney, P.E. RET
Striving to live Aloha
(Ted can offer longterm or instant help)
finishing.com - Pine Beach, New Jersey
Ed. update September 2020: Sorry, that Tranter design manual link went bad, but we've found a copy of the manual at
http://navalex.com/downloads/Tranter_Platecoil_Data_Manual.pdf
Times are changing and suppliers don't generally offer their deep technical libraries like in the old days; plus the internet became more about commerce than data, so the old gray Google ain't what it used to be when it comes to searching for technical data. So download it right now or be sorry later!
Q. Thank you for the quick response
My main plating tanks are run at 193-197. I really didn't want to run the water heater much more than 205 to keep it below steam threshold. I am trying not to have to deal with steam, just from a safety and regulatory standpoint of high pressure systems.
Is this possible with hot water systems?
I sat down this weekend, and worked out the BTU's I would need.
The other issue is that my materials are highly caustic. We do chew through heaters quickly, even teflon lasts only about a year. I can get these coated from a stainless heater, but again I am looking at how to reduce cost overall.
Thank you for the quick, insightful answers.
Derek
- Dalton, Georgia US
March 21, 2016
A. Hi again. Most of my career was with suppliers and as a plating equipment consultant so I specified steam boilers many times, and hot water boilers several times, and don't have a strong preference for one over the other. The hot water boiler is slightly less expensive, and its piping is less expensive, but the need for larger heating coils cuts into those savings. If exotic coil materials are required and/or the tanks are very hot, those costs overtake the savings in boiler and piping, and then some.
Although there could be something in your local codes that make the regulations easier for a hot water boiler, most plating shops use low pressure steam boilers (less than 15 psi), and these normally do not require a fireman or anything really burdensome. I think you should talk to a steam boiler manufacturer like Cleaver-Brooks and investigate a 15-psi low pressure packaged steam boiler to make sure you're on the right track.
Regards,
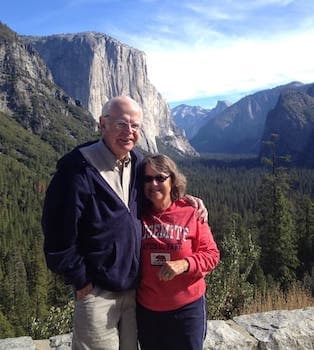
Ted Mooney, P.E. RET
Striving to live Aloha
(Ted can offer longterm or instant help)
finishing.com - Pine Beach, New Jersey
How to calculate chemical loss from open tanks
Q. I am looking for a reliable calculator for evaporation on open tanks. There are some great articles on finishing.com but they all seem to be either assuming ambient temperature or missing wind speeds. The Aloha is too complicated and more for outside applications and I wondered if anyone has a comprehensive calculator or formula.
Typically I am setting up a Zinc Phosphating tank 1.2 m wide and 3.8 m long. It is maintained at a constant temperature of 82 °C. If the ambient temperature is at 16 °C but the area is ventilated with fume extraction of 0.62 m/s (1.5 mph) then how much heat are we losing from the surface of the tank? We are not using Croffles or any form of cover.
Thanks Daniel
- Providence Rhode Island
September 4, 2020
A. Hi Daniel. We combined some of those threads which you refer to, and have appended your inquiry to that thread. You will see a link where you can download Tranter's Design Manual which, as a plating equipment & shop designer, I referred to for decades; for different employers I wrote computer programs to incorporate that data way back when.
But I also need to note that all you can do is an approximation based on general data. There will be dead spots on the tank surface, stray breezes at different times, loads going into and out of the tank to disrupt the air flow, unknown wet bulb temperatures based on this and that. If you also estimate wall losses, and losses to cold work entering the tank, you can get close to the total operational heat loss. Good luck.
Luck & Regards,
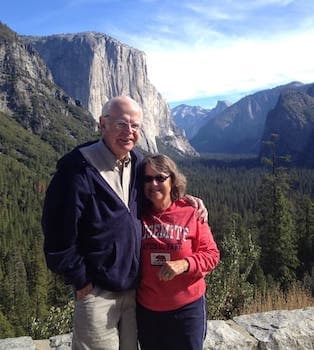
Ted Mooney, P.E. RET
Striving to live Aloha
(Ted can offer longterm or instant help)
finishing.com - Pine Beach, New Jersey
Q, A, or Comment on THIS thread -or- Start a NEW Thread