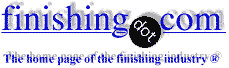
-----
Horizontal hard chrome plating plating vs. vertical
2005
Q. Hello,
My name is Neel. I am a part time researcher. We are a team of 4 researchers. We are helping a small entrepreneur in his research. He is a manufacturer of hard chrome plated bars and tubes.
1) We wanted to know the advantages and disadvantages of horizontal hard chrome plating over vertical hard chrome plating. The length of shafts is around 3-3.5 meters and plating thickness desired is 20 microns.
2) In the conventional vertical bath, we are getting plating taper at the bottom end. What is the reason for that?
3) Will there be any time saving in the horizontal bath?
Please help me with these 3 questions.
Regards,
researcher - Pune, India
A. Neel,
As a researcher you know that it makes a job easier when you are in possession of all the facts. Unfortunately, you are a bit vague as to what is being done by way of materials and processes.
As far as your points are concerned, regarding the orientation of a tank, horizontal tanks of this size will take up more floor space and will be more prone to solution evaporation. You will also have increased issues with fume extraction using horizontal tanks. In practical terms, the lower the exposed surface area of a tank, the easier it is to reduce losses, but there may be other effects you may want to minimize, such as foaming; a small surface area but high charge density per unit area could result in an unacceptable foaming level. With regard to the second point, I assume you are using hexavalent chromium and therefore suspect you have a problem with jigging - a 3.5 meter tube is one hell of a length to throw with chromium. You should consider using multiple connections onto the tube. As far as time is concerned, like all electroplating, Faraday's Laws dictate how much metal is deposited; the trick to success is to use Faraday's Laws to your advantage and to maximize deposit uniformity and minimize any electrochemical losses and wastage.
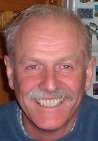
Trevor Crichton
R&D practical scientist
Chesham, Bucks, UK
2005
2005
A. Both arrangements are in very widespread use. Neither horizontal nor vertical is "better" -- each has advantages and disadvantages that can be weighed for the particular circumstances.
One potential advantage of horizontal plating is partial submersion so that you can measure the plating thickness and spot some gross defects as the plating is progressing. Another is much shallower tanks and more practical building shape
Advantages of vertical plating include simplicity (no need to rotate the shaft during plating), and much lower floor space and fume emissions.
As for the "taper" the first thing to look for is temperature stratification; if the temperature near the bottom of the tank is significantly lower than the temperature near the top, you'll get measurably thinner plating at the bottom. Make sure the heating coils are low in the tank and that you have plenty of agitation.
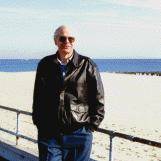
Ted Mooney, P.E.
Striving to live Aloha
(Ted can offer longterm or instant help)
finishing.com - Pine Beach, New Jersey
2006
A. Neel,
I read the Trevor and Ted's answer, they are good, but I would like you to know some practical points for this problem.
At first, there are some differences between these two procedures. Based on Cr(VI) plating, I can guess how do you it, but I don't know your equipment level. If I assume your solution was refined and with a normal condition --
1- Could you balance the temperature between bottom and top of the bath during your plating? For this tank, it's more important to getting a good result in the vertical and with this depth.
2- Do you have a fixture for preventing going near the anodes with the shaft at the bottom of the tank, or another mechanism for this?
3- With this vertical procedure, you had anodes about 3.5 meter minimum, were your anodes clean at all of this surface (for example at the ends of it).
Regards,
- Karaj, Iran
A. Neel:
Based on the answers you have received and the absence of this problem on the Internet, I can only conclude the parts can be plated vertically without taper. With a single connection at the top we had the same problem; and after checking everything we concluded the taper was due to voltage drop and thus less current density from top to bottom. However, like you, we are not certain. Copper core anodes possibly help but resistance in the part is still present with no practical way of multiple connections.
Can't see horizontal improving taper except anode current distribution potentially improved.
I hope we hear more on this.
Cliff Smith
- Oklahoma City, Oklahoma
July 25, 2009
August 18, 2010
A. Dear Neel,
1) We wanted to know the advantages and disadvantages of horizontal hard chrome plating over vertical hard chrome plating. The length of shafts is around 3-3.5 meters and plating thickness desired is 20 microns.
Major Advantage of horizontal Plating Equipment:
- Highest Metal Distribution along the whole length of the bar
- No impact of varying anode position
- Stable plating conditions
2) In the conventional vertical bath, we are getting plating taper at the bottom end. What is the reason for that?
-Already answered by Cliff
3) Will there be any time saving in the horizontal bath?
-YES: due to better less overplate and higher current density, horizontal equipment is more cost effective.
- Hamburg, Germany
A. Hi Neel, one thing used to fix the taper is baffling material, so protect the job with a non conductive material to shield it from the anode if your anode length is longer than the job. Another way is with the anodes shorter than the job to stop the high current density areas having a massive effect; plating tanks are meant to be designed that way, even though commonly they are not. There are other practical things you can do to reduce the effect of the tapers. Do have in mind that for heavier chrome deposits, beyond just a flash of a few thousandths or microns, the problems of an uneven deposit will occur even with precautions in place.
Q. I am actually trialing horizontal chrome plating now at work and we are curious how the chrome is effected with the job being out of solution, knowing that chrome needs an under 5% ripple rectifier to produce an adherent bright deposit.
Lewis Brierley- england
May 19, 2020
Multiple threads merged: please forgive chronology errors and repetition 🙂
Hard chrome plating bar of 11 mtr long
Q. Dear Sir
I am job plater I received an inquiry; component is steel bar of 11 Meters long & Diameter range of 30 mm to 180 mm. My question should I go for HORIZONTAL OR VERTICAL BATH. Can anybody guide me who is doing or had done in past?
Thanks
prasad
propriter - Pune, India
2007
2007
A. I have never seen a chrome plating tank deep enough to handle an 11 meter long shaft vertically; the deepest I have been involved with were about 18 foot (deep enough for about a 6-meter shaft. So I'd say horizontal :-)
Usually these shafts are continuously rotated during plating (assuming heavy hard chrome plating) and they are often plated with at least a small arc of the diameter above the solution level so that thickness can be easily measured magnetically.
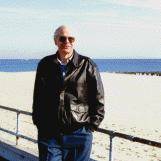
Ted Mooney, P.E.
Striving to live Aloha
(Ted can offer longterm or instant help)
finishing.com - Pine Beach, New Jersey
A. That is a challenge for anyone. If you plate a shaft that long and only 30mm wide, it will have to be supported in at least one place and probably 3 to hold down the shaft flex which will crack the hard chrome plate. Rotating the shaft will take some innovation also,but can be done. I will guess that it will require a conforming anode which will be a trick at 11M in length. You might try a lead lined box where the lead is the anode and is an inch or so from the part. You definitely will want the anode area to at least equal the cathode area. Another big question would be how thick a chrome coating do you need and how uniform you would like it to be.
Finally, is this a one or two operation or several a week?
It will require attention to heat/cooling and would work best if there was a plating tank to pump from to control the temp rise and be at the desired temp when you insert the part.
It will require electrical contact at both ends and possibly in the middle if the shaft is not a good conductor, as you are talking about 1,000 to 2,000 amps for good plating.
Bid high and do not cry if you do not get the contract.
- Navarre, Florida
2007
A. Hi,
I have seen in Middle East there are a lot of job platers who gets such enquiries to plate around 8 - 10 meters job for Hard Chrome, they do such jobs vertically mounted in a well type deep 11 meters tanks , I think they air agitate for movement of solution.
Thanks
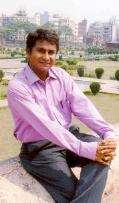
Praveen Kumar
plating process supplier
Mumbai, India
2007
May 2014
Thanks Praveen. I think you have the right answer! In view of the length of the shaft it first occurred to me that vertical plating would be difficult ... but as we examine the proposition, it seems horizontal plating would be even harder :-)
Regards,
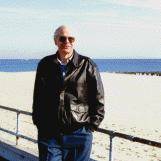
Ted Mooney, P.E.
Striving to live Aloha
(Ted can offer longterm or instant help)
finishing.com - Pine Beach, New Jersey
A. Actually there is another solution for this extra long product. The technology is named Continuous Plating or Through Feed Plating. With this system the bar is located horizontally and run through a plating cell coming out fully plated. There is no limitation in length. Online you can find more info.
Nicola Nisco- Milan, Italy
April 12, 2016
Multiple threads merged: please forgive chronology errors and repetition 🙂
Need advice on hard chrome plating equipment
Q. We have an inquiry from our client, a steel mill that has to build hard chrome coating shop to plate the rolls used in steel rolling operation. where can we find the list of major equipment manufacturers for this technology? Thanks in advance for your comments.
Michael KoganConsultant - Bellingham Washington
July 20, 2011
July 22, 2011
A. Hi, Michael.
There are many manufacturers/suppliers of plating tanks and the related accessory equipment like heaters, filters, rectifiers, exhaust systems and material handling equipment; you will see a number of them listed in our Equipment Directory. While I know many companies which specialize in the "whole package" for some types of plating, I personally haven't heard of anyone who offers a "package" for horizontal hard chrome plating of rolls. The few installations I dealt with over the years had to rely on consultant-designed or in-house designed equipment for holding and rotating the rolls during plating. If I am correct, you may want to retain a hard chrome plating consultant to put together the pieces, especially the material handling stuff.
If someone enlightens me to the contrary, we'll both learn something from your inquiry.
Regards,
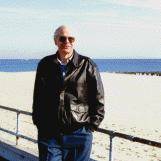
Ted Mooney, P.E.
Striving to live Aloha
(Ted can offer longterm or instant help)
finishing.com - Pine Beach, New Jersey
Hard chrome horizontal tank
Q. Hello,
Most hard chrome processes that I encounter are carried out in vertical tanks, mostly because of dimension of the workpiece and the ease of ventilation, heat loss, etc.
What if I need to carry the process in a horizontal tank? I struggle with the issue of suspending a workpiece in the process tank. How to solve the matter of anodes and auxiliary anodes?
Does the workpiece need to be completely immersed? If so, does it need to rotate between anodes?
Thank you for your support
- Bydgoszcz Poland
August 6, 2018
A. Hi Lucas. During the second world war, driveshafts for ships were sometimes conveyed to railroad sidings inside or next to chrome plating shops on flatbed cars for replating. In some cases, horizontal plating tanks were built on site on the railroad car and the shafts were plated without removing them. Necessity is the mother of invention. The platers who told me about this have all passed on and I've only seen pictures and sketches, but smaller scale, less ad hoc, horizontal plating is certainly still done.
For horizontal plating, the shafts are usually only partially submerged and constantly rotated. I think it is necessary to keep the portion which is out of solution wet. If you patiently search old journals and patents you should find some info.
Regards,
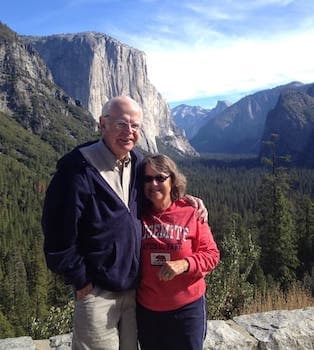
Ted Mooney, P.E. RET
Striving to live Aloha
(Ted can offer longterm or instant help)
finishing.com - Pine Beach, New Jersey
August 2018
September 7, 2018
A. Hi LUCAS, both techniques have their own plus/minus. All depends on job shape, quantity to be plated per batch and the uniformity of coat required.
A picture speaks louder then words. If you have a problem plating a specific part post a pic here; I am sure many experts here will be able to help you out.
I have plated long parts horizontally and small parts vertically in a horizontal tanks with success.
All the best.
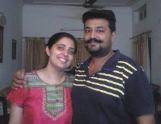
Vikram Dogra
Irusha India - Chandigarh, India
Plant for Continuous Hard Chrome on 4 mtr x 40 mm Dia
Q. I want to set up a plant for Hard chrome coating of Round bars of 40 mm diameter 4 mtr long. What maximum no I can plate in continuous coating set up? What kind of setup cost needs to be invested.
Kiran Nawathe- Pune in Maharashtra state in India.
June 19, 2020
A. Hi Kiran. I have seen zinc plating and copper plating done on shafts "continuously". i.e., the shafting rolling down a table like logs down a hill with electrification tracks on it, or similar arrangement ... but I personally haven't seen hard chrome plating done that way, although it sounds vaguely possible ... but I think it would only be a project for an existing chrome plating shop with experience. To limit the investment and issues, I'd want to see it done on shorter shafting first :-)
Or you can hang the shafts vertically. Good luck.
-----
Update August 2020
As we merged the threads, I noticed Nicola's posting, investigated a bit further, and now realize that "continuous" chrome plating doesn't refer to shafts oriented like logs rolling down a hill, but like logs going into a saw mill. Apparently in Italy (and in China) this is the new approach; and once you solve the problem of seals, it's easy to see the advantages.
Regards,
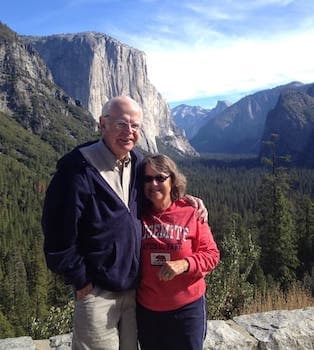
Ted Mooney, P.E. RET
Striving to live Aloha
(Ted can offer longterm or instant help)
finishing.com - Pine Beach, New Jersey
June 2020
Rotation setup for horizontal hard chrome plating
Q. We are putting horizontal hard chrome plating of piston rods of 6000 mm length, manually. We are manually rotating. Now We are planning to put 6000 mm rods in automated setup, lined up 4 rods, I would like to make all the jobs rotate automatically for continuous and equal thickness of plating . Can you explain me how to do this rotation setup automatically without power loss with fixtures and motors, I am not familiar with this rotation setup. Please help me how to do this.
Sunil Ravi- Chennai, India
August 6, 2020
A. Hi Sunil. What you are speaking of can be done at least three different ways: with the rotation mechanism extending straight through the wall of the tank, or over the top of the tank and back down via gears and/or sprockets & chain, or the rotation mechanism can hang from the crane.
But the mechanical arrangement, and brush arrangement to bring in DC plating current. is an engineering undertaking, not something anyone can explain in a paragraph or two. I think your choices are assembling an in-house design team, or retaining an engineering consultant to design it for you, or purchasing the system.
Luck & Regards,
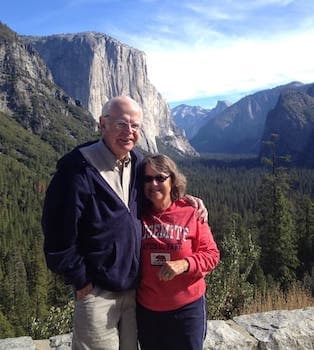
Ted Mooney, P.E. RET
Striving to live Aloha
(Ted can offer longterm or instant help)
finishing.com - Pine Beach, New Jersey
August 2020
Q. Can you suggest suggest some sources that sells this system or regarding this system, can you share some book/ reference/papers that gives this information about rotation of jobs in horizontal plating.
Sunil Ravi- Chennai, India
August 7, 2020
A. Hi Sunil. If you have access to very old 1940's-1950's metal finishing magazines you will see photos of such systems; I don't know of any recent publications showing a typical arrangement. You might search scholar.google.com, and old patents though -- this can be freely and easily done these days at uspto.gov or patents.google.com, and ought to give you some good graphics. Sorry we cannot offer commercial suggestions (why?) but patient application of google or other search engines should work.
Luck & Regards,
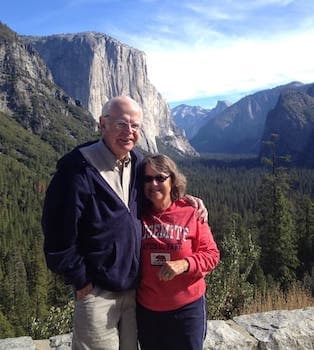
Ted Mooney, P.E. RET
Striving to live Aloha
(Ted can offer longterm or instant help)
finishing.com - Pine Beach, New Jersey
August 2020

Q, A, or Comment on THIS thread -or- Start a NEW Thread