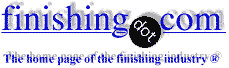
-----
Electropolish 202 & 304 stainless steel Q&A
2002
Q. We are manufacturers of gift and handicraft products in iron and stainless steel. We generally use 202 grade SS.
We are using locally made chemicals here, but what I am unable to determine is the following :
1. cost of electropolishing ( say per sq. inch ).
2. How to clean the electropolishing tank periodically since the chemical becomes very viscous and black with continuous use.And when to replace the whole chemical.
3. How to change the ratio of sulfuric acid, phosphoric acid and glycerine to enhance the shine on the product.
Thanks,
Sumex Exports Pvt. Ltd. - New Delhi, India
A. Dear Vibhor:
Giving all the information you ask is a huge task but I will try to give you some answers that may help you.
The cost of electro-polishing depends upon many factors that only you can answer. The first step is to keep good records of your costs and the number and size of your parts. I suggest that you spend a little time with your accountant discussing these issues. Without good records your accountant can only guess at what your true costs are and it may take you many months to achieve your objective.
Sludge will form at the bottom of the tank over a period of time. If it is not causing you a problem then leave it alone until you change your chemicals. In a simple system such as yours, running craft items, tank cleaning will not improve the quality of the electro-polish enough to show any profit.
When to change your acid? That is a good question. I have processes that require me to change the acid when it reaches an iron concentration of 2% and I have associates that leave it until it reaches 5.5%. If you are getting the quality you want in a reasonable time then why change the acid? If your run times are too long and your quality is not what it should be then it may be time to change the acid.
As for changing the formula. I advise against it unless you want to do it properly and run many, many experiments to determine what will produce the best results. I think that fresh acid will spice up your production and improve your quality more than experiments with different formulae.
Good luck,
- Elkhorn, Wisconsin
Multiple threads merged: please forgive chronology errors and repetition 🙂
Q. Can both 202 and 304 grade stainless steels be electropolished with the same mixture in the polishing tank?
If yes, what mixture to be used ? What are process parameters to be controlled (like what is the current to be passed, duration for which the current to be passed, temperature of the mixture in the tank
If not, why? and what are two mixtures to be used?
We tried 304 and 202 in Phosphoric Acid + sulfuric acid (proportion) 80:20 but are getting whitish layers in some of the area.
Manufacturer of kitchen Trolley drawers in 202 and 304 grades - Nashik, Maharashtra, India
2005
A. Both 202 and 304 stainless steels can be processed with the same electrolyte, which should be based on a mixture of sulfuric and ortho-phosphoric acids. Your mixture of 80/20 should be OK if they are the correct grade of acids and if you have the correct operating conditions. You do not give your process details, so we can only guess you are using the optimum ones. In the long run, it may be better to use a proprietary solution, as they contain other additives that prolong the life of the solution; they also provide detailed operating conditions, which will vary as the amount of dissolved metal in the bath increases. Making your own solutions is very good for one-off jobs, but to do it on a commercial basis is often a false economy.
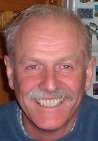
Trevor Crichton
R&D practical scientist
Chesham, Bucks, UK
2005
A. Your solution should work, for best working results your tank temperature should be between 130-150 °F.
Now your 'whiteish layers' maybe be caused by an imbalance of your specific gravity which should be between 1.70 and 1.78. Don't forget to make sure that you have good electrical contacts on all racks and cathodes.
electropolishing - Clearwater, Florida, U.S.A.
2005
![]() |
Q. What is the difference between grade 202 and grade 304 Stainless Steel? Laura DunkleyBuyer - Nashville, Tennessee 2007 A. Hi Laura. As Trevor says, no difference in terms of how to electropolish them. For more basic differences not related to this electropolishing thread, please see letter 50226, "Difference between Stainless Steel grade 304 and 202". Good luck. Regards, ![]() Ted Mooney, P.E. Striving to live Aloha (Ted can offer longterm or instant help) finishing.com - Pine Beach, New Jersey |
Q. I am looking for a non-electric bright dip solution for stainless steel products. I am a manufacturer of dental instruments.
Bilal AkramManufacturer - London, United Kingdom
October 14, 2009
Ed. note: This RFQ is outdated, but technical replies are welcome, and readers are encouraged to post their own RFQs. But no public commercial suggestions please ( huh? why?).
A. Hi Bilal. I am not personally aware of satisfactory "bright dip" / "Chemical polish" for stainless steel, and I think you might be better off looking into "electropolishing" (we have countless threads on that topic if you search the site).
Regards,
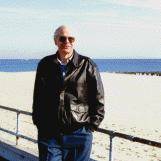
Ted Mooney, P.E.
Striving to live Aloha
(Ted can offer longterm or instant help)
finishing.com - Pine Beach, New Jersey
----
Ed. update note Nov. 2020: See entry below by Anna Berkovich regarding proprietary non-electric bright dip.
Q. I WANT TO KNOW IF ELECTROPOLISHING IS AVAILABLE ON STAINLESS STEEL HOME UTENSILS? IF YES, HOW LONG IT LAST (numbers of years)? WE MANUFACTURE 304 AND 202 QUALITY OF STEEL UTENSILS.
PLEASE PROVIDE US WITH THE CHEMICAL FORMULATION AND MACHINERY NEEDED?
I ALSO WANT TO KNOW WHAT IS CHEMICAL FORMULATION FOR COPPER PLATING AND BRONZE PLATING ON STAINLESS STEEL UTENSILS AND HOW LONG THOSE CHEMICALS LAST?
THE TERM LAST IS BECAUSE THEY ARE HOME UTENSILS AND BE USED IN DAILY USE THAT MEANS IT COULD BE WASHED 2 TO 3 TIMES MAYBE IN A DAY?
BUSINESS PERSON - INDIA
August 14, 2010
A. Hi, Abhishek. Yes, electropolishing is certainly available for stainless steel utensils. It is a smoothing and polishing process that would last essentially forever, except that a consumer can, of course, scratch the utensil regardless of whether it is mechanically polished, electropolished, or unpolished. Copper plating or bronze plating could last many decades or could wear off rather quickly depending on its thickness and quality. I have 60-year-old RevereWare copper-bottom pots that were manufactured by electroplating with copper.
But as for how to do these three different processes, and the chemicals and machinery involved, it's complicated and you'll have to take one problem at a time and commit to reading a lot of info whether here or elsewhere. Whole library shelves are devoted to each of the subjects you mentioned.
Regards,
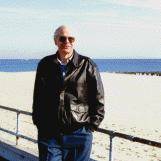
Ted Mooney, P.E.
Striving to live Aloha
(Ted can offer longterm or instant help)
finishing.com - Pine Beach, New Jersey
August 16, 2010
THANK YOU MR. TED
IT WAS NICE SEEING YOUR PROMT REPLY.
WE MANUFACTURE STEEL PLATE USING DOUBLE ACTION POWER PRESS, AND THEN FOLD CORNER IN SPINNING MACHINE.
THANK YOU ONCE AGAIN TED SIR; IT WAS REAL NICE SEEING YOUR GOOD RESPONSE.
- India
August 19, 2010
Electropolishing solution with glycerine attacks the cathodes
Q. In order to improve the stainless steel electropolishing I have used an electrolyte with glycerine (10% v/v). The finishing I got is better, but I have noted the electrolyte attacks the stainless steel cathodes even when there is no current flow. How can I solve this problem?
Tatiana Rios- Medellin, Colombia
December 26, 2013
Shining stainless
Q. Hi. I am manufacturing a tongue cleaner from 202 stainless steel. Generally we are buffing the pieces but it is very time consuming process. Now I want to know is there any chemical to shine stainless steel? I use a mixture for stainless of H2O2 + HCl. It works, but after etching of 5 to 10 pieces it is not working. Is any addition required?
Paresh dabhi- morbi, gujarat, India
March 5, 2014
A. Hi Paresh. H2O2 rapidly decomposes unless special stabilizers are added, and chlorides are murder to stainless steel, so I don't think it's a good idea to use that bright dip. Sorry, I am not personally aware of "bright dips" for stainless steel.
Regards,
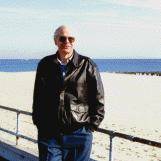
Ted Mooney, P.E.
Striving to live Aloha
(Ted can offer longterm or instant help)
finishing.com - Pine Beach, New Jersey
March 2014
adv.
We have installed the Brite Dip chemical processing for stainless steel in two locations - in USA and in Italy. The electrolyte does not contain HCl or hydrogen peroxide.
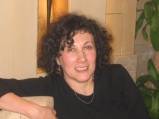
Anna Berkovich
Russamer Lab

Pittsburgh, Pennsylvania
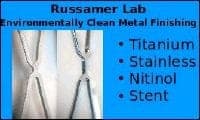
March 12, 2014
Q. Sir
I am using electropolishing stainless steel 202 grade using chemical of phosphoric and sulfuric.70:30 ratio. Wire of 5 mm gives good shine but wire of 6-8 mm does not give shine and has whitish layer. I am very confused and tried a lot but always fails. I am using lead cathode.
Anything to change? Please guide me
- Ludhiana India
February 16, 2017
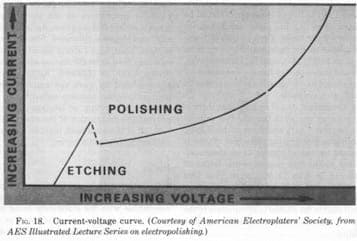
A. Hi Amit. If the material is the same, the problem is probably insufficient current density. You need sufficient current to move out of the etching range and into the electropolishing range. You cannot make up for it with longer processing time. Bigger wire needs more amperage! Good luck.
Regards,
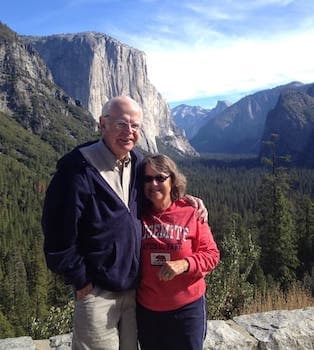
Ted Mooney, P.E. RET
Striving to live Aloha
(Ted can offer longterm or instant help)
finishing.com - Pine Beach, New Jersey
February 2017
Q. We electropolish SS steel scooter accessories in solution containing phosphoric acid and sulfuric in 1:1 ratio by 90 weight of solution and balance 10 percent water. After using solution for 10-15 [loads? hours?] specific gravity starts to increase.
And solution working capacity is not as before as iron is dissolved. Guide me How to maintain specific gravity or in which ratio which acid is to be added. And how can we find iron concentration in the acid
- Ludhiana,Indua
February 16, 2017
A. Hi Amit. See thread 44029, "Analysis of metals & acids in Electropolishing Baths for stainless steel" ...
But we want no abandoned shopping carts (of questions) on this site, and you didn't acknowledge the answer to your previous question on wire electropolishing :-)
Please respond to/ resolve that other discussion before moving on. Thanks! Good luck.
Regards,
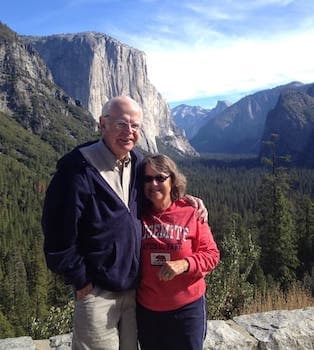
Ted Mooney, P.E. RET
Striving to live Aloha
(Ted can offer longterm or instant help)
finishing.com - Pine Beach, New Jersey
February 2017
Q, A, or Comment on THIS thread -or- Start a NEW Thread