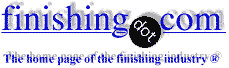
-----
De-rusting/De-scaling of Heat Treated Parts

Q. I am working on a zinc plated part that is made from Mild steel which has steel bushings that are copper brazed to the part. After brazing the part is heat treated with oil quench. Initial tumbling/ vibratory cleaning was used to clean the parts post brazing and heat treatment. This proved to be inadequate as plating adhesion was still poor. We tried media blasting the parts to clean the parts more aggressively. Samples of the blast cleaned parts turned out well with good adhesion and no bubbles. Larger trials of blast cleaned parts again resulted in poor adhesion.
Looking for some suggestions. Zinc migration around the braze joints is OK but poor plating adhesion is not. Will zinc plating these parts ever work with the residual copper around the joints from brazing? Is there another plating scheme that would be more appropriate (copper then tin, nickel, nickel and another top coat? Any cleaning methods to recommend? Keep in mind cost is a factor here. Glass bead blasting the parts to remove any sign of copper turned out to be quite expensive, close to the part cost.
Nikko Shilling- Milwaukee Wisconsin
November 9, 2021
A. Hi Nikko. I believe the burnt-on oil and its carbon is the cause of the adhesion problem, not the copper.
May we assume that it is the bushings that you are hardening? (because I don't believe a mild steel plate can be hardened). I could be way off, but I would have expected that you could heat treat the bushings, then vibratory finish or sand blast them, braze them in, and then send them through an acid zinc plating line with conventional cleaning, perhaps even a barrel plating line.
Luck & Regards,
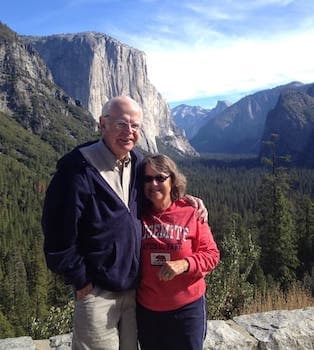
Ted Mooney, P.E. RET
Striving to live Aloha
(Ted is available for instant or longterm help)
finishing.com - Pine Beach, New Jersey
Q. The whole assembly is subjected to carbon nitriding to a hardness of 55-6 5HRC. As far as I can tell, all the pieces are made from plain/ mild steel. These are being barrel plated. The zinc looks ok right after plating. The post bake is 4 hours at 375-400 °. After baking the zinc is bubbling and flaking on the edges and other surfaces of the part. What is troubling is that even after blasting the parts prior to plating, adhesion of the zinc is still poor. These parts also seem to look worse over time. While in transit or storage some pieces develop a very dull cloudy appearance.
Nikko Shilling [returning]- Milwaukee Wisconsin
Q. I HAVE A SHEET METAL PART WITH ANNEALING PROCESS. THE SCALES ARE TOO MUCH, NEED TO DO ZINC TRIVALENT YELLOW.
BUT DUE TO HEAVY SCALES WE ARE GETTING HUGE UNCONVERAGE. SUGGEST THE BEST CLEANING PROCESS TO AVOID THE REJECTION.
- CHENNAI, TAMILNADU
February 28, 2023
⇩ Related postings, oldest first ⇩
Plating oil tempered spring wire?
Does oil tempered spring wire resist corrosion? I'm consulting for a company that is utilizing an oil tempered spring wire as a bearing strip. They are finishing it with an engineering grade hard chrome. But the hard chrome isn't sticking. Is there a better plating process for this?
Matt NadeauMechanical Engineer - Denver, Colorado, US
2003
I am not a heat treatment expert, but I think "oil tempered" just means that the quenching was done in oil. This would probably not impart any special corrosion resistance. I am not picturing the
"bearing strip" application, unfortunately. Chrome plating is brittle and will not accept flexure well, if that is the case, but it should stick just fine. If flexure is part of the application you may need nickel sulphamate plating, or tin-zinc plating, or some other somewhat malleable finish.
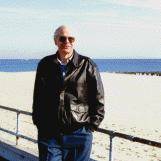
Ted Mooney, P.E.
Striving to live Aloha
(Ted is available for instant or longterm help)
finishing.com - Pine Beach, New Jersey
Q. Ted,
Your assumption is correct. Oil temper, simply means it was quenched in oil. My vendors are saying that because it is quenched in oil, the plating is not sticking. As far as the application goes: The wire is straightened out and laid flat. A bearing rolls along the flat wire.
Matthew Nadeau [returning]Medical Imaging - Denver, Colorado
A. Apologies -- my reply was misleading :-(
Once the scale has been removed, the plating should adhere fine, but removing the scale other than by blasting may be very difficult or even impractical :-(
Luck & Regards,
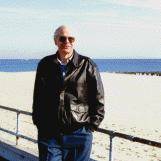
Ted Mooney, P.E.
Striving to live Aloha
(Ted is available for instant or longterm help)
finishing.com - Pine Beach, New Jersey
Multiple threads merged: please forgive chronology errors and repetition 🙂
Q. Sir,
We are using some Sheet Metal parts which are Direct Hardened (Spring Steel and EN 9 material). After Heat Treatment we observe Black Quenching oil deposits and thin Heat Treatment scales. These HT scales are not getting removed using various deburring/ vibro finishing techniques. Can we use an acid based chemical/deruster like Phosphoric acid based to remove HT scales? Are parts prone to Hydrogen Embrittlement when acid washed (HCl, H2SO4, HNO3, H3PO4) for cleaning purpose? Please clarify immediately.
- MARAIMALAI NAGAR, TAMILNADU, INDIA
2005
by William E. Bryson
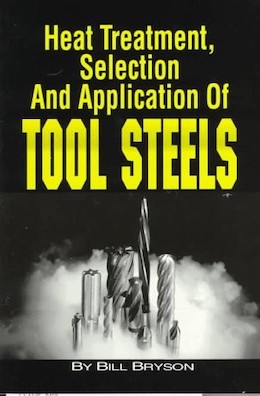
on eBay or Amazon
or AbeBooks
(affil link)
A. Dear Balaji,
Using any acids in to pretreatment will cause hydrogen embrittlement and it will weaken the strength of metal component.
Try to do dry pretreatment like shot blasting, shot blasting will remove all the excess material from substrate, then you have to do phosphating or other organic/Zinc/Aluminium coating 2/3 microns on your component. It will not allow rust to contact substrate for long time. By applying 8 to 10 micron of this kind of coatings you will achieve corrosion protection up to 1000 hours as per ASTM B117.
All it depends up on your budget and the requirement/end use of components. Please specify the end use of your components. Try Dacro, Delta Tone, Delta Coll or Magni kind of coatings (2-3 microns) for additional corrosion protection after sand/shot blasting. Automated blasting machines are available for small parts in bulk qty.
Best regards
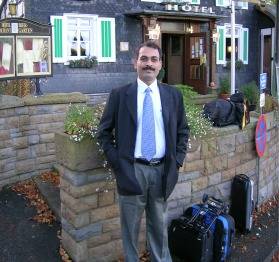
Kalyan Dhakane
Mumbai, India
Q. I would like to know other than mechanical cleaning if any chemical cleaning will loosen and remove the scales prior to zinc plating 5-8 microns?
R.Rajasekharan- CHENNAI, TAMILNADU, INDIA
December 21, 2008
A. Hi, Raja. If your question is the same as Belaji's, so is the answer. But if you are speaking of lightly rusted low carbon mild steel, rather than heat treat scale on hardened parts, mild acids will remove it. Good luck.
Regards,
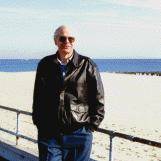
Ted Mooney, P.E.
Striving to live Aloha
(Ted is available for instant or longterm help)
finishing.com - Pine Beach, New Jersey
How can I verify heat treat scale has been removed prior to chrome plating? Heard of Open Circuit Potential
Q. Currently using a chemical bath to remove heat treat scale from our parts. Wish to go to mechanical means to remove the heat treat scale. The issue is that the cycle time required in our mass finishing mechanical method is too long. It is too long because I don't know how to predict if my parts will be good or not, so a long time is chosen. After chroming if the parts are bad, they are scrapped. It would be helpful if I knew the parts would chrome well before I chrome them. If there was a simple way to test a part after processing in the mechanical cleaning machine I would know if I need to put it in the machine for a longer period of time or if they are good to go. Help would be appreciated.
Paul DeBoerPlating operation supporting engineer - Guelph, Canada
October 8, 2009
A. There are high energy systems that are very aggressive and there are materials that are aggressive compared to others. So, it all depends on the system and the media.
James Watts- Navarre, Florida
Multiple threads merged: please forgive chronology errors and repetition 🙂
Scale removal from oil-quenched steel
Q. We have the carburising and oil quenching process of low carbon steels. but we are facing the problem of quench oil scale removal. we are washing these parts in hot water, and after that we are doing shot blasting -- but process is time consuming and results are not satisfactory.
so my question is there any method or solution or technique to remove that scale.
service - Belgaum, Karnataka, India
June 23, 2010
A. Hi, Shivaji. It can be expensive and time-consuming to remove scale no matter how you do it -- but let's start with: In what way are the results not satisfactory? Chemical removal adds a layer of complexity: possible hydrogen embrittlement, and a very active surface that may flash rust.
What do you do with the parts after the shot blasting? Is the QPQ process a possibility for you?
Regards,
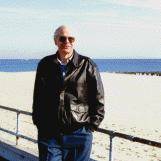
Ted Mooney, P.E.
Striving to live Aloha
(Ted is available for instant or longterm help)
finishing.com - Pine Beach, New Jersey
A. If you are quenching with a water-soluble oil, then part or all of the problem may be due to the salts in the water that you use. These tend to build up over time due to evaporation, and at some point start to split the oil from the oil-water emulsion.
I have seen people add versene (EDTA) to the soluble oil to sequester the calcium and magnesium, but this is a temporary fix. A better solution is to use RO permeate to make up the quench oil instead of tap water.
consultant - Cleveland Heights, Ohio
A. Dear Shivaji,
For removing the scales after oil quenching in the Heat treatment, blasting is the best & suitable method.
May be think for the better way of process in blasting or suitable media with pressure.
if, your selecting the acid pickling, this is very high risk on the part.
Mr.Lyle Kirman,
We never add any water in the quenching oil, adding water or RO permeate in quenching oil is risk on the part (possibilities of crack)
- Salem, Tamil Nadu, India
A. If this is not high volume, grit blasting is the most effective way to remove scale.
If it is very high volume, you might want to look at one of the permanganate solutions that crack the coating and set it up for a much faster acid pickle.
- Navarre, Florida
Q. Respected Sir:
I want to remove scale from spring steel rolled strip 3 ft long and 3 inch width approx., and connecting rod 4140 CARBON STEEL of tractor engine after hardening and tempering in salt bath. So which chemical is suitable for this purpose and its price and use period? We want production rate 500 pieces at least a day?
Which generates less fumes?
And is there any corrosion risk by using this product?
We are using HCl for this purpose but it is corroding the parts around by fuming action and by immersion parts in it.
I am waiting for your reply.
Regards,
- LAHORE, PAKISTAN
April 14, 2012
adv.
We have different gels compositions for carbon steel descaling, passivation. Some of them are tough and work fast, and some are "green" and also work fine but slowly. All of them descale in a passive zone, meaning that only oxides are impacted, the metal stays intact. We don't sell gels and electrolytes retail, but provide know-how of chemical compositions. If companies have large volume of descaling, do-it-yourself of such gels or liquids may make sense.
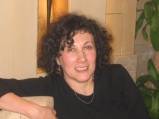
Anna Berkovich
Russamer Lab

Pittsburgh, Pennsylvania
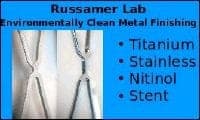
A. I think for removing the scale you can go for blasting (with suitable blasting media),
because acid or aqueous solutions may introduce the hydrogen penetration, this will be more brittle for the part.
If your part's hardness is more than 100MPA after heat heat treatment, do the blasting and go for non-electrolytic coating process.
- Salem, Tamilnadu, India
Q. We have a fine module 0.8 mm gear which is case hardened. This requires a grid blasting operation to remove mild scales after case hardening and tempering process. is there a process of removing the scales without corroding the parts. Parts should not impact each other during cleaning We require about 5000 parts per day to be cleaned.
Balasubramanian Ganapathyauto parts manufacturer - Chennai, Tamilnadu, India
September 15, 2013
![]() |
A. Descaling can be done in passive stage, when only oxides are impacted, and the actual metal is left intact. adv. ![]() Anna Berkovich Russamer Lab ![]() Pittsburgh, Pennsylvania ![]() A. The biggest problem I see is the volume of parts you need to produce in addition to the way you want to process the parts. It sounds as if you may have to use a pass through system, either automated or semi-auto. Suggest you look into some blast systems that are used to strip paint that use organic media even extreme high pressure water or CO2. ![]() AF Kenton retired business owner - Hatboro, Pennsylvania |
Descaling of normalised tubes
Q. Sir
I am manufacturing swaged tube ends by cold process. These tubes are used in boilers. After swaging the swaged end is normalised. After normalising scaling develops on the normalised part of the tubes. Can you please suggest a way in which I can remove the scaling after normalising? Further is there any way I can avoid scaling?
- Mumbai, Maharashtra, India
July 12, 2016
A. Shot blasting will remove the scale and oil spots too. After shot blasting you can dip the components in anti-rust oil to prevent rust.
Sachin JereHeat treatment case carburising - Pune, Maharashtra
Q. Sir, we are manufacturer auto electrical parts. We use high carbon cold rolled material (en42j). After heat treatment please suggest us cleaning method of components.
Mahender arsay- Fridabad Haryana , India
April 25, 2017
A. Hi cousin Mahender. I can't expand on the answers already offered unless you provide some info which sets your case apart from the others. Can you get back to us with what the next process will be: plating, painting, powder coating? And the size of the parts so we can consider whether individual handling vs. automated bulk processing is appropriate. Are the parts clean before heat treatment? Are they heated in a vacuum or controlled atmosphere or can they be? They sound like spring steel components -- are they oil quenched? Thanks!
Regards,
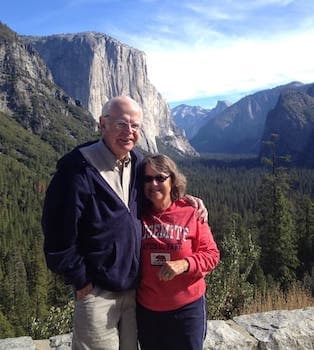
Ted Mooney, P.E. RET
Striving to live Aloha
(Ted is available for instant or longterm help)
finishing.com - Pine Beach, New Jersey
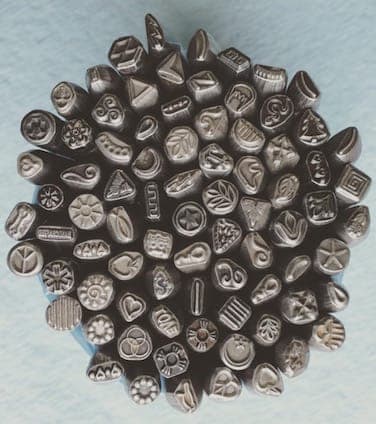
Q. I work for a stamp company where we make stamps for leather, metal, jewelry, etc. We use 01 tool steel and heat treat them ourselves. The problem we are having is obviously getting the steel cleaned up from the oil quench and decarb. We put images on 1/4" round tools approx. 3" long and there can be up to 1000 tools in a batch. For years now we have been cleaning them up by tumbling them (all approx. 1000 tools) in walnut shell media ⇦ on eBay or Amazon [affil link] . However, that process takes about 3.5 to 6 hrs and while it does clean them up great it does tend to "smear" the images we are putting on them. We have tried a Sonic cleaner with no luck. Just wondering if anybody had any ideas how we could get them clean and still maintain a nice crisp image?
Jason Hartley- Boise, Idaho USA
July 7, 2017
A. Hi Jason. One advantage of acid treatments compared to mechanical treatments is that the acid can be formulated (with inhibitors) to selectively attack the scale more aggressively than the base metal, thus not 'smearing' the images.
Luck & Regards,
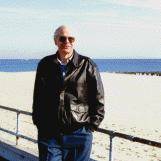
Ted Mooney, P.E.
Striving to live Aloha
(Ted is available for instant or longterm help)
finishing.com - Pine Beach, New Jersey
Q. We have SS316 finished components, due to solution annealing it's lost its surface finish and a little bit of scale on the surface, Suggest any chemical cleaning method except plating or any other mechanical cleaning method.
Sridhar ss- Chennai, tamilnadu, India.
August 13, 2017
A. Sridhar,
Pickling. Or nitric acid passivation, which is more or less still pickling.
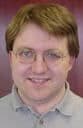
Ray Kremer
Stellar Solutions, Inc.

McHenry, Illinois
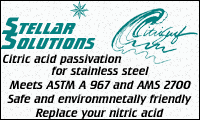
Q. Sir,
This is regarding engine valve surface cleaning. Valve material is SNB 16. After stress relieving, valves surface gets rusty even after pre shot blasting. What can be done (pre or post) to clean this rust without stress generation.
- Ghaziabad, up, India
August 2, 2019
A. Rupesh - investigate alkaline derusting. It's a quick process which can be done in bulk.
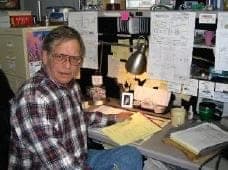
Jeffrey Holmes, CEF
Spartanburg, South Carolina
Q. We are using some Sheet Metal parts which are Direct Hardened (Spring Steel and EN 9 material). After Heat Treatment we observe Black Quenching oil deposits and thin Heat Treatment scales. These HT scales are not getting removed using various deburring/ vibro finishing techniques. Can we use an acid based chemical/deruster like Phosphoric acid based to remove HT scales? Are parts prone to Hydrogen Embrittlement when acid washed (HCl, H2SO4, HNO3, H3PO4) for cleaning purpose? Please clarify immediately. Before zinc plating only.
Mahendrakumar Raut- Pune, Maharashtra, India.
October 25, 2020
A. Hi Mahendrakumar.
Just a reminder that if you need "immediate" help you should retain a consultant. This is just a public forum where readers see your message only if they trip over it ... so requesting that people who aren't even seeing your message reply immediately can't be counted on :-)
Phosphoric acid is unlikely to do much, you'll probably need HCl. But yes, as Kalyan & Kannan said, it definitely will cause hydrogen embrittlement which can usually by removed by de-embrittlement baking before plating as well as after plating. If the parts can accept zinc plating, they can probably accept acid pickling, although it's not unheard of for spring steel parts to shatter right in the pickle tank.
Abrasive blasting may be a better approach than acid.
Luck & Regards,
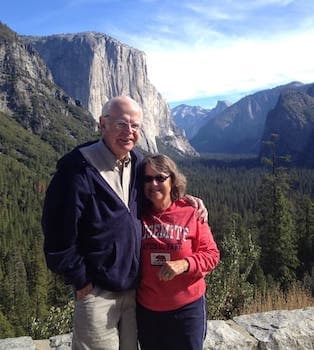
Ted Mooney, P.E. RET
Striving to live Aloha
(Ted is available for instant or longterm help)
finishing.com - Pine Beach, New Jersey
Multiple threads merged: please forgive chronology errors and repetition 🙂
Post treatment of steel after quenching process
Q. We have two stage cleaning after quenching process. 1st stage is alkali dip & spray and 2nd stage is hot water spray. Problem point is that, after hot water spray stains/marks observed on parts. We use DM water with temperature 70 °C for hot water spray process. Someone please suggest me which parameter I need to change in DM water so that we get parts with no marks.
Karthik Acharya- Bangalore Karnataka India
August 8, 2021
A. Hi Karthik. Hopefully someone who is also working with this problem will understand it better, but it's a bit vague for me. What are you quenching in -- some sort of oil? Why must you alkaline clean and rinse? What kind of marks do you get -- salt-like stains, black discolorations, rust? Can isopropyl alcohol be added to the DI water for better sheeting action? Is vapor degreasing/vapor drying a viable alternative? What are the aesthetic standards? Thanks.
Luck & Regards,
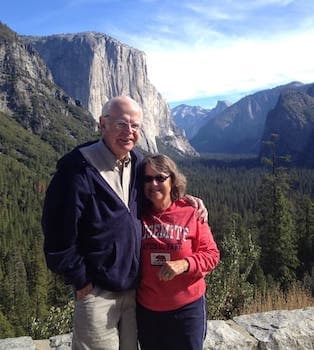
Ted Mooney, P.E. RET
Striving to live Aloha
(Ted is available for instant or longterm help)
finishing.com - Pine Beach, New Jersey
Q. Dear sir, thank you so much for your reply.
We use high temp X oil in quenching process. Since oil content is more on parts we perform alkali dip and rinse process and in order to remove alkali content from part we use hot water spray. But currently we are getting black marks on parts after hot water spray (will share a photo soon).
I tried skipping hot water spray, but alkali burn marks observed in tempering process hence hot water spray is necessary for me.
- Bangalore Karnataka India
Readers may wish to see also --
• Topic 15010 "Chemical removal of heat treating scale and oxides -- steel parts"
Q, A, or Comment on THIS thread -or- Start a NEW Thread