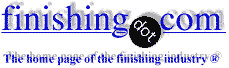
-----
Polypropylene / fiberglass tanks bulging: how to add stiffeners?
Q. Hi everyone !
Somebody, please, explain to me the plastic welding process -- what do I need for making PVC or PP plating tanks.
Now we use hot air and plastic "wire" (D = 3-5 mm).
Maybe somebody knows another way?
Can I use epoxy glue
⇦ on
eBay
or
Amazon [affil link] for making tanks?
"Epoxy resins are a blend of materials that strongly bond to other materials, and are set by a catalyzed chemical reaction.
The resulting hard amorphous mass is strong, highly corrosion resistant, and operates over a wide range of temperatures.
Pure resins usually serve as high quality glues. Glass fibers and filaments bonded together with epoxy resins are used to produce process piping systems which operate from -20°F to +300°F (-28 to 148°C). This material handles most acids, bases, and solvents"
- Tartu , Estonia
2001
A. Hi, Viktor.
No, to my knowledge you cannot glue polypropylene, and you will probably not be able to successfully glue (solvent weld) tanks from PVC. Freeman Newton explains why in thread 6775.
If you want to build polypropylene and PVC tanks, hot air welding is a good way to go, and fusion welding is another way.
Fiberglass tanks are made with glass cloth and resin, although vinyl ester resin is probably a better idea than epoxy resin for most plating shop applications.
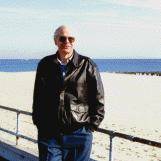
Ted Mooney, P.E.
Striving to live Aloha
(Ted can offer longterm or instant help)
finishing.com - Pine Beach, New Jersey
A. Victor,
Firstly, I want to thank (and so should you) Ted Mooney for saving me a lot of explaining !
Don't be led up the garden path! Epoxies are a S.O.B. to work with. They have a tendency to suddenly 'set' whereas the polyester and vinylester resins give you a better and a more predictable working time. Moreover they are very expensive and don't seem to 'wet' out as well.
As for corrosion resistance, be careful! The better resins will take temperatures up to boiling for some liquids and much higher for, say, chimney stack linings.
None of these resins can take strong acids! PVC will take commercial 93 percent sulfuric.
Plastic weld rods come in thicknesses for 3 to 5 mm, most are round, some are triangular. It all depends on what type of welding you are doing, if you are using a 'speed' tip or just a regular welding nozzle.
Cheers !
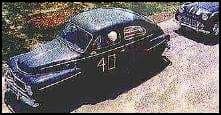
Freeman Newton [dec.]
R.I.P. old friend (It is our sad duty to
advise that Freeman passed away 4/21/12)
A. Yes you can glue PP and PVC. 3M has come out with a new glue that will glue PP with no pre-treatment.
Wayne Gaybba- Cape Town, South Africa
2003
Thanks for the update, Wayne! But even though the materials "can" be glued, I've never heard of a polypropylene or PVC plating or pickling tank being constructed by gluing, and I doubt that we soon will.
Luck & Regards,
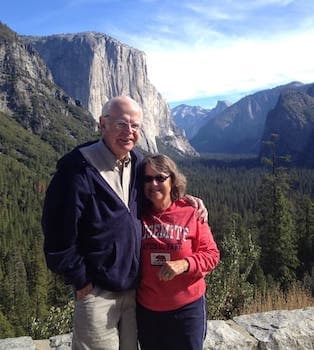
Ted Mooney, P.E. RET
Striving to live Aloha
(Ted can offer longterm or instant help)
finishing.com - Pine Beach, New Jersey
Multiple threads merged: please forgive chronology errors and repetition 🙂
Polypropylene tank for stainless steel pickling
Q. I work at a company that renders plastic welding services and I am trying to help a customer. I have a problem and I don't get answers, no matter how much I research! I would like to know if somebody can me help me. I have a customer who has a tank operating with nitric + HF + water, for stainless steel picking. This tank measures 66' x 8' x 3' deep. (It's a big tank). This tank is manufactured from 1-1/4" thick PP sheet.
This tank has operated 7 years now, and it presents weld flaws. This useful life was foreseen when it was installed. Now, this customer intends to manufacture another tank to substitute for the damaged tank, however, they don't have the specifications of the production of the old tank where the material is discussed. Which would be the best PP for this application? Random? Homopolymeric ? Copolymeric ? Does anybody have experience with similar applications?
Project - São Paulo, Brasil
2004
A. Hi Franz. Homopolymer.
Luck & Regards,
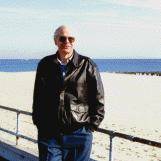
Ted Mooney, P.E.
Striving to live Aloha
(Ted can offer longterm or instant help)
finishing.com - Pine Beach, New Jersey
![]() |
A. Polypropylene is a poor choice since nitric acid oxidizes the plasticisers. The weld process has all ready burned out some of the plasticisers. I would look at polyethylene. It is harder to weld well and requires an inert gas to prevent charring around the weld. Another thought, would a vinyl liner work? A lot cheaper, but it will not take a lot of physical abuse. I would look at one that is 3/16" thick. James Watts- Navarre, Florida A. Hi Franz, ![]() Freeman Newton [dec.] R.I.P. old friend (It is our sad duty to advise that Freeman passed away 4/21/12) |
Q. Dear Freeman Newton
I would like to complete the information: The operation temperature is 149 °F that surpasses the suitable temperature for PVC (140 °F). Today the PP tank, with the resin used, presents oxidation of 0,06? / year. This PP is mattered and we don't know the composition. A similar tank was manufactured with material national PP copolymer and it presents an oxidation of 0,2? / year. We didn't get to discover what type of PP was used in the original tank.
part - São Paulo, SP, Brazil
2004
A. Hi Franz,
As mentioned above, if you use a dual laminate, the operating temperature CAN BE INCREASED.
For PVC:FRP it's not 150 but l75 ... and there was a case history of using the Trovidur red PVC at 195 degrees F ... Wow! But that PVC is probably the top PVC in the world, more brittle than others and certainly has a higher resistance to sulfuric ... where all PVCs excel.
As a matter of interest, after the war, a UK inspector was going through a German chemical plant and saw this red piping which flummoxed him completely ... all the then conventional materials were alloys or lead or glass. Yes, Germany invented PVC.
If you wanted corroboration on the operating temperature of the PVC:FRP dual laminate, contact Enrique Ginoccio, P.Eng. of Prolite.
By the way, the world's first successful dual laminates were made by Alcore Fabricating in Ontario back in the early 60's.
I hope that that puts your mind at rest! By the way, but this is something I'm sure you'd know, it's the bond between the thermoplastic and the FRP that is critical. We used to use conductive tape at all welds in order that the finished product could be easily spark tested.
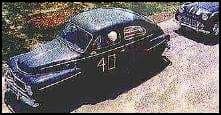
Freeman Newton [dec.]
R.I.P. old friend (It is our sad duty to
advise that Freeman passed away 4/21/12)
Multiple threads merged: please forgive chronology errors and repetition 🙂
Tanks are bulging dangerously. How to stiffen?
Q. Hello,
We are in plastic fabrication business. Some of the tanks manufactured by us in PP + FRP are bulging dangerously. We provide MS stiffeners embedded in FRP to all the tanks but they still are bulging. Size of tanks are 18 x 3 x 3 high with 5 mm PP + 3 mm FRP.
- Mumbai, India
2005
(Many decades later the editor fondly remembers the 1st book I consulted after graduation from engineering school ... the book that took me from theory to real-world practice :-)
A. You didn't include units of measure, Parag, but first off I feel your materials are bit too thin. I would not design such a tank with less than 1/4" (6 mm +) thickness for the polypropylene and 5/16"-3/8" (8-10 mm) for the fiberglass. If the tank is 18 feet x 3 feet x 3 feet, the bracing can be done with a couple of structural tubing belly bands, but adding one or two toe braces on the long side would be better. If you mean 18 m x 3 m x 3 m, such a tank size would be impractical to brace with girth bands (belly bands) alone, and toe bracing (together with girth bracing) is probably a much better idea -- but you definitely want to up the material thickness to at least 1/2" (12 mm+) for the polypropylene and 3/8" (10 mm) for he FRP.
An old book, "Design of Steel Weldments" by Omer Blodgett describes how to approach the design problem of bracing open-top rectangular tanks, and has been used as the basis for plating & anodizing tank designs by many suppliers for many decades. Although more advanced approaches have probably been described in the literature since (Finite Element Analysis didn't even exist back then), any builder of rectangular tanks would be very well served to get a copy while it can still be found.
Your real world problem will probably be that these tanks may cost several times the amount that was budgeted for them :-(
While that would be painful to hear, even worse would be to spend still more money playing around building completely unsatisfactory tanks. If these tank measurements are in feet it's possible that an experienced plastic fabrication shop foreperson can figure it out; if the dimensions are in meters, please retain an experienced engineer, as this is way beyond seats-of-the-pants design :-)
Good luck!
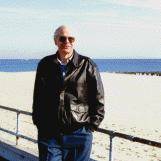
Ted Mooney, P.E.
Striving to live Aloha
(Ted can offer longterm or instant help)
finishing.com - Pine Beach, New Jersey
A. Hi Parag,
As Ted pointed out, some belly bands might well be necessary but that's not my cup of tea. Also he assumed you meant that the given 18 x 3 x 3 figures were metric dimensions ... but I've never, ever encountered a tank of that length (40 odd years in the plastic fabrication business and making the world's first successful dual laminates in the early 60's ... Alcore Fabricating) and even rarely in 'feet'.
The philosophy I used was to have a) a heavy longitudinal stiffener at 1/3 of the tank height plus, of course, a top flange. .... I wasn't much a lover of belly bands but just good adequate longitudinal stiffeners ... and they should do the trick.
Ted was also right to surmise that the material thicknesses were too thin ... it's NOT the PP thickness (heck, you could have used 1/8") but the fibreglass... and at a rough guess that should be min. 1/4" (6 - 7 mm) thick using alternate glass woven roving or cloth with matte in between.
It's the fibreglass that'll give you the structural strength ... and restrain the PP from expansion and buckling (presuming a good bond). Doubtless (I most sincerely hope) you acquired the PP sheets with the glass fibres already thermally bonded to it!
Didn't you check that tank before shipping it?
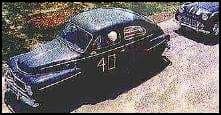
Freeman Newton [deceased]
(It is our sad duty to advise that Freeman passed away
April 21, 2012. R.I.P. old friend).
A. If the tank is dual laminate you may be able to use some heavy bore plastic pipe welded to the inside of the tank for extra stiffening.
Having read the post again I can answer the dimension dilemma I think. I believe it must be a rectangular tank. 3 mm thick FRP sounds disastrous for a rectangular tank of these dims. Heavy heavy stiffening will be required -- may work out cheaper to add a lot more layers of CSM to the walls. 3 mm works out at 2 Layers of 0.6 kg CSM. When I have designed rectangular tanks I was looking at 16 Layers up to 22 depending on the spacing between stiffeners required and this was for tanks. You really need to revisit your calculations as they really do not sound right for the application. Steel stiffeners may work for you but you will need a lot both horizontal and some vertical. As a guess I would suggest 10 stiffeners horizontally and maybe 1 stiffener each meter vertically. Rectangular tanks are real nightmares; the flanges are probably already fitted so you are limited to where to put the stiffening -- if flange clashes it may mean adding more laminate to the entire tank to avoid the clash. I designed a PP rectangular tank which started bulging I solved this by adding the internal stiffening as per my previous post. You are more than likely going to have to entirely redesign the tanks. I wish you luck.
- Belfast, Northern Ireland
June 1, 2009
Q. Dear All,
I want to weld a rectangular tank by PP sheets with 20 mm thickness.
Tank dimensions are as below: 3 m * 1 m * 1.5 m (L*W*H).
Would you please help me to choose the right horizontal stiffeners for this tank?
Thank you in advance
surface and electroplating technologies - Isfahan, Iran
August 15, 2014
A. Hi Jalal. I'd probably use two (2) 4 x 3 rectangular structural tubing belly bands (also called girths or horizontal stiffeners) located 23" and 42" down from the rim, plus a 3" angle iron rim. This is not a considered design by a professional engineer, just a free "feel" for typical designs from my experience.
Good luck.
Regards,
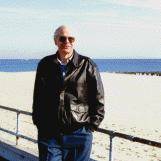
Ted Mooney, P.E.
Striving to live Aloha
(Ted can offer longterm or instant help)
finishing.com - Pine Beach, New Jersey
A. Dear Mr. Jalal.
Especially for P.P. Pickling tank there should be M.S. cage surrounding the tank based on its size. Generally for your size of tank we use 100 mm x 50 mm x 3 mm thick RHS duly fiber coated and insert the P.P TANK inside it. For your size of tank vertically you should have at least 6 supports @ 500 mm distance and Horizontally you should keep 3 support. first support at top of the frame, second one @ 500 mm from there and third one again @ 500 mm. you will get best result of it.
Regards.
Gunatit Builders

Manjalpur, Vadodara, Gujarat
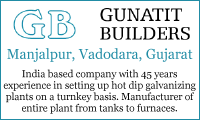
Q. Dear All,
Thank you for your answers.
As this is our first experience in tank fabricating.
Our base plate has 4 cm oversize from each side. How we can install vertical stiffeners? Would you please give me some references or Photos?
Thank you again
- Isfahan, Isfahan, Iran
September 6, 2014
A. Hi again Jalal. This is not a really large tank, and as long as you are not putting really heavy weight loads on its rim, I do not think vertical stiffeners are required. Rather I think you'll be okay with just horizontal stiffeners.
Usually you make a 1/4" thick polypropylene "cover" for the steel stiffeners to protect them from corrosion, and weld it to the tank wall to hold the steel stiffeners at the right height. This is, as I say, not a large tank, but it's not a really small one either and it's always better to start small since this is your first effort. Good luck. Regards, ![]() Ted Mooney, P.E. Striving to live Aloha (Ted can offer longterm or instant help) finishing.com - Pine Beach, New Jersey |
![]() |
Q. Dear Ted,
Thank you again for your nice support.
Which side of steel profile must be flange side? smaller or bigger?
Can we use screws to join steel profiles at 90 degrees together or just we must weld steel profiles?
Thank you in advance
Jalal
- Isfahan, Iran
A. Hi Jalal. Steel members are much stronger against bending "the long way" than "the short way". So the 3" dimension would be touching the tank wall, and the 4" dimension would be perpendicular to the tank wall. I can't imagine a practical bolting scheme for the steel tubing; cut them at a 45° angle and weld them please.
In America we do not design structures so casually. Rather, a plastic fabrication shop either starts small, and from long experience gradually develops a "seat of the pants" feel for good and safe designs for larger tanks, or they retain an engineer for designs that are not within their experience. Obviously there is no such thing as a "seat of the pants" feel for a good and safe design when something is significantly beyond your prior experience :-)
Regards,
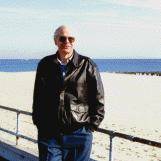
Ted Mooney, P.E.
Striving to live Aloha
(Ted can offer longterm or instant help)
finishing.com - Pine Beach, New Jersey
Q. Dear Ted,
Hope to be fine.
Thank you for your details and information.
So before we weld the top frame [rim] of PP, we must install steel stiffener and fix them on the right height and then top frame [rim] of PP?
Thank you again.
- Isfahan, Iran
A. Hi again. Yes, that would seem to be the way to do it. Alternately, you can lay the tank upside down, and slide the steel stiffeners down to their correct position (although if I understand you, the bottom plate on your tanks may be bigger, and may prevent that approach).
Regards,
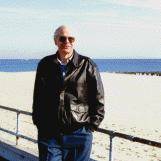
Ted Mooney, P.E.
Striving to live Aloha
(Ted can offer longterm or instant help)
finishing.com - Pine Beach, New Jersey
Q, A, or Comment on THIS thread -or- Start a NEW Thread