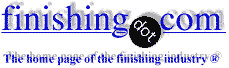
-----
Acceptance criteria after salt spray test
< Prev. page (You're on the last page)
Q. Hi, how are you.
We are producing mortise locks. We are using EN 1670 for salt spray test results. So I want to know about rust. It says that there cannot be any spots larger than 1,5 mm in 650 mm2.
I don't know how to interpret that because which 650 mm2 area will I choose. I mean if there is a big plate and there is just one spot with 2 mm, what should I say. It is ok or not?
Thank you so much
kalekilit - istanbul TURKEY
February 23, 2018
A. Hi Yunus,
I would reject the part, the 650 mm^2 you select should be a large continuous surface (in this case it's a big plate). The corrosion pit is larger than the standard and you should reject. The bigger the pit the sooner it started corroding or the plating / supplemental coating was not thick enough to inhibit the corrosion that you're looking for.
Cheers.
Vapor Bus International - Buffalo Grove, Illinois
Q. Hi, my name is Steven Sze. I'm an aluminium panel design engineer. The panels are mostly used for building cladding. Our company is about to have one of our steel panels tested (aluminium interior) against Salt Spray Test 1000 hours. May I know if there is any standard that we can refer to, to define if our product "Passed the test" or "Failed the test"?
Steven Sze- Brisbane, Queensland, Australia
March 16, 2018
A. Hi Steven. I assume these steel panels are painted or powder coated rather than galvanized? Hopefully a reader with architectural experience will understand your question better than I do, because I'm not "getting" this idea of an "aluminum interior". I don't think there is any possibility of a panel which is painted on one side but aluminum on the other passing a salt spray test which exposes both sides.
My reason for asking about the paint or powder coating is that the specifications for the coating, rather than the standards for how to conduct a salt spray test, is usually where to find the pass/fail criteria. So I don't think anyone can direct you to that pass/fail info until you describe the coating specification. Good luck.
Regards,
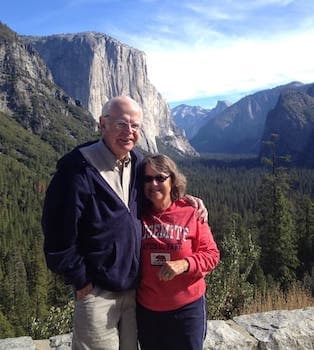
Ted Mooney, P.E. RET
Striving to live Aloha
finishing.com - Pine Beach, New Jersey
A. Hi Steven!
Maybe ISO 4628-3 (Paints and varnishes -- Evaluation of degradation of coatings: Assessment of degree of rusting) or ISO 4628-8 (Paints and varnishes -- Evaluation of degradation of coatings: Assessment of degree of delamination and corrosion around a scribe) can give you a reference to agree with your client the "fail" test.
You must always make an agreement with your client beforehand so you don't have problems in the future. I participated in many part developments (we make fasteners but I think it applies for everything) and when we had some problems with corrosion tests, it was about how the "fail" was assessed.
I think ASTM D610 (Standard Test Method for Evaluating Degree of Rusting on Painted Steel Surfaces) can help, too. In ISO 4628-3 there is a correlation chart so you won't need to get both standards for this one.
Best of luck and hope you solve this one!
TEL - N FERRARIS - Cañuelas, Buenos Aires, Argentina
Q. We are following ASTM B117 and NADCAP regulations on our chamber and I occasionally have parts that get a brown stain that I have failed previously as rust. However, on my most recent test pieces, I submersed them in copper sulphate
⇦ on
eBay or
Amazon [affil links] to plate them and they did NOT turn pink. We abrasive blast with aluminum oxide prior to passivation. Any ideas on what my brown stains are?
Thanks:)
- Boss, Missouri, United States
March 15, 2018
? Hi Kyle. I think we need to clearly understand what the substrate and finishing process are. Are we understanding these are stainless steel parts which have been passivated? Knowing the grade of stainless steel would be helpful.
Regards,
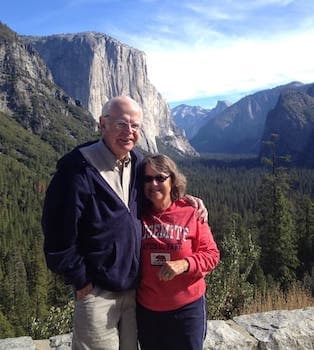
Ted Mooney, P.E. RET
Striving to live Aloha
finishing.com - Pine Beach, New Jersey
Q. The material is 300 series stainless steel that has been abrasive blasted and passivated.
Kyle Major [returning]- Boss, Missouri, United States
How to QUANTIFY the extent of failure in salt spray test
Q. My situation:
Anyone can help? How to quantify the failure in salt spray testing?
For suppose I found the failure at the last minute or if I see the failure at very little amount?
How to measure the extent of failure in the test.
Because I found the black coloured rust formation on the steel sheet within 140 hours.
Tester - Puducherry, India
August 11, 2018
A. Hi Sri. You tried to post this under the subject of "Salt Spray Test -- ASTM B117 Operational Problems", but we moved your question here because ASTM B117 tells you how to operate the test cabinet, but it does not tell you what constitutes failure of tested parts. You find out what constitutes failure in the specification that you are processing to. That can be totally different for aluminum parts, stainless parts, steel parts plated with different materials, steel parts phosphatized or black oxided, steel parts powder coated, etc.
It is not your job to build pass/fail rules, but to find out where that "140 hours" requirement came from, read the spec that dictated that 140 hours, and determine whether the parts complied with the testing requirements for that processing specification.
I am not saying that the spec will be 100% free of ambiguity. You may well come back to us and say that you are still not sure whether the parts passed or failed … but we can't talk about it until we know what spec you are trying to comply with and what it says about the subject. Good luck!
Regards,
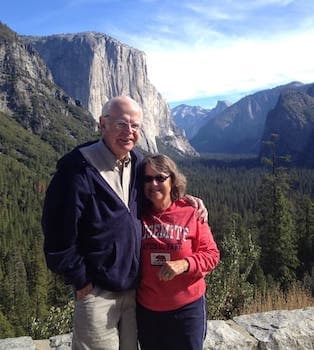
Ted Mooney, P.E. RET
Striving to live Aloha
finishing.com - Pine Beach, New Jersey
Q. Hi,
We have some bolts which are coated with Yellow dichromate. Does white rust appears in this case also?
- Syracuse, New York, USA
September 10, 2018
A. Hi Sandeep. Please tell us who you are and what you do (plating shop employee, salt spray test lab, buyer, designer) and why you want to know. Then we'll have a starting point towards understanding your questions in a more useful way.
May we assume the bolts are steel? You can't apply yellow dichromate to steel, but you can apply it on top of cadmium plating, zinc plating, zinc alloy, and tin-zinc plating. So we have to assume that those bolts are plated. And all of those platings can generate white rust. So if your question was understood, the answer is yes, if those bolts corrode, it is possible for them to get white rust. Good luck.
Regards,
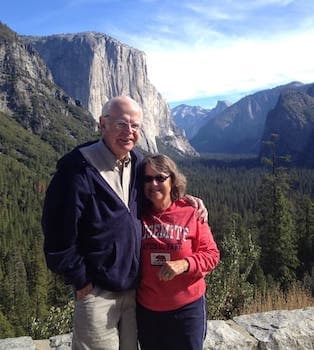
Ted Mooney, P.E. RET
Striving to live Aloha
finishing.com - Pine Beach, New Jersey
A. The only thing I can contribute is Cd or Ni plated bolts last a lot longer in salt spray when chromate coated. This is based on actual testing experience. Never had them in the chamber long enough to see a failure.
Ronald ZeemanCoil Coating - Brampton, Ontario, Canada
Q. Dear all,
Our company uses coating Fe/Zn12/A/T2 on steel and zamak hardware. We start a discussion regarding evaluation of white rust. My question: how should we treat changing of part of coating surface to matte and grey/black color. I don't mean black spots, but whole areas. One of our laboratories claims it is white corrosion but I have doubts.
- Gdańsk, Poland
November 15, 2018
Q. Dear sir,
Please share SST hours for Yellow Passivation of 8-10 micron thickness.
Also share details about what is top coat and why it is used
- Pune, Maharashtra, India
February 6, 2019
A. Hi Shilsagar. Please share who you are, what you do, and why you want to know, then people will probably be able to help you better :-)
Pending a response, 192 hours salt spray should be a safe specification.
The world largely shifted from hexavalent chromating to trivalent over the last few decades, and most trivalent chromates cannot match the corrosion resistance performance of the hexavalent chromates without an additional top coat, which may be a titanium, zirconium, or similar final dip which helps seal the surface away from the environment. Good luck.
Regards,
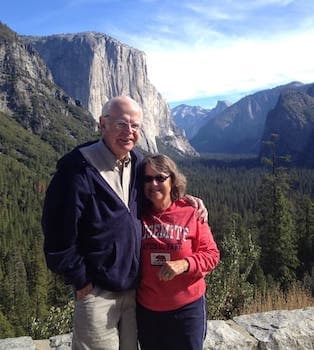
Ted Mooney, P.E. RET
Striving to live Aloha
finishing.com - Pine Beach, New Jersey
Q. Hi, All, I am Vinodh from a fabrication Industry, I would like to have the experts suggestion on the Structural Painting. We have to supply fabricated structures to the Coastal area. As our customer does not specify any requirements on the test hours, as a general practice how many hours we have to do the test and what is the acceptance criteria. Kindly suggest which standard to refer.
With Regards
- Hyderabad , India
March 21, 2019
A. Hi Vinodh. First things first, how do you intend to paint these structurals? Will you be blasting the steel to "Commercial" standard NACE No.3, SSPC-SP-6, Swedish Sa-2? Or to what standard will you be blasting? Then what: galvanizing, phosphatizing, e-coating, and finally painting or just painting?
A good starting point is probably ⇨
From this you should be able to specify what kind of coating system you are looking for, and after you have selected it, you can try to determine how to test compliance with your spec. Good luck.
Regards,
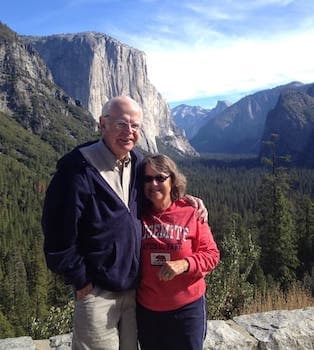
Ted Mooney, P.E. RET
Striving to live Aloha
finishing.com - Pine Beach, New Jersey
Q. Hi Sir, Thank you for the response. We would like to carry out the surface preparation as per BS 7079 SA 3. After surface preparation 2 coats of Primer, 1 Coat of MIO, 2 Coats of Finish Paint. DFT requirement is 325 Microns. For the above painting which type of test is suitable. Environment is coastal areas.
Regards
Vinodh
- Hyderabad , India
Q. Hi Sir,
My name is Isvaran. I'm a quality engineer in a zinc die-cast company. We are also specialized in plating including nickel-brass & nickel-chrome. For the first time we coated our zinc die-cast part with high corrosion resistance trivalent chromate. Process: deburring, tumbling, soak clean, acidic etching, chromating, drying at 35 °C for 5 minutes.
We sent 2 different samples (coating & without coating) for SST under the following condition:
1) According to ASTM B117-2018 modified
2) Testing chamber temperature: 35 °C ±2 °C
3) Saturation chamber temperature: 47 °C ±2 °C
4) Ratio 95% water (De-ionized water or Pure water) / 5% NaCl
5) pH = 6.5 to 7.2 (Measuring at 35 °C)
6) Air Pressure: 1 A ± 0.3 kg/cm square
7) Duration: 48 hrs
8) Test mode : Power off.
The result tested by us is failure due to white rust formation & discoloration on both samples.
But when the samples with the same condition tested by customer, the result was pass. No white rust formed & no discoloration. They just noticed some little black patches after 48 hours. Can you explain what could make the result different?
- Masai, Johore, Malaysia
April 26, 2019
A. Hi Isvaran. One sample part may not be enough to tell you much; you may need to repeat it a few times. But note that ASTM B117 tells you how to build and operate a salt fog cabinet, but it doesn't tell you what constitutes passing vs. failing. So, before you get into long discussions about how one sample can pass according to one testing house and another sample fail according to a different testing house, I think the first thing you need to do is to agree on exactly what constitutes passing vs. failure (rather than leaving it vague and subjective).
If you can't find a good recognized spec that covers trivalent chromate conversion coating of diecastings, there are several that cover chromate conversion coating of aluminum, and you could probably see how they define passing & failure and incorporate something similar into your spec. Good luck.
Regards,
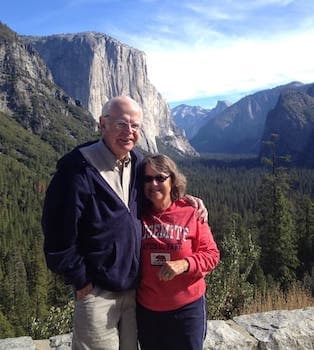
Ted Mooney, P.E. RET
Striving to live Aloha
finishing.com - Pine Beach, New Jersey
Q. Hello you beautiful people,
I am a manufacturer of turned components on traubs (automated lathes) and a recent product has me confused with the specifications for plating.
White rust appears 96 hours on a product which is 9 mm in diameter and 5 mm in length with a knurl all around the putter dia.
They have given that the part should must comply with JIS C 0023 for a period or 96 hours.
They do not define the failing criteria of the product clearly (is the 96 hours specifically for white or red rust) and JIS C 0023 simply tells how to do the test without any failing criteria.
Looking further down the thread I found that ASTM B633 States that appearance of white rust at edges does not constitute as failure, but a knurl is nothing but edges.
Am I correct in stating the above to the customer or is there a logical flaw in my thinking?
- - Gurgaon, haryana, India
September 27, 2019
A. Years ago I was employed at a testing lab. Salt spray testing was a speciality.
ASTM has illustrations of the two main criteria that could constitute failure, creepage and/or blistering. Creepage is measured on edges or a scribe in mm. Blisters are rated on size and density. The illustration uses a scale from 2 to 10 indicating the size of the blisters, and such as few-to-dense to indicate density.
Your customer needs to inform you of their requirements in these terms.
Unfortunately I no longer have access to the ASTM specifications, ASTM B117 should point you in the right direction.
Coil Coating - Brampton Ontario Canada
Thank you so much !
I'll try getting better specifications from the customer in the future.
This basically caused me to panic and assume I have messed up big time.
I really appreciate the quick assistance.
- Gurgaon , haryana India
Nut with black zinc coating fails 96-hour salt spray test
Q. Good Evening everyone,
I have a problem but I'm not finding the root cause of this problem ... a Nut with Zinc Black coating and it fails in SST test within 96 hours (Red Rust Problem)?
- RUDRAPUR UTTARAKHAND India
January 17, 2020
A. Hi Anup. On one level, that's an easy one: The root cause of it failing in the salt spray test is that it's not plated and chromated properly :-)
But the issue of exactly in what way and why it is not plated and chromated properly is, of course, far more complicated. What specification is it supposed to be plated in accordance with? Is it rusting solely within the threaded area or everywhere?
Regards,
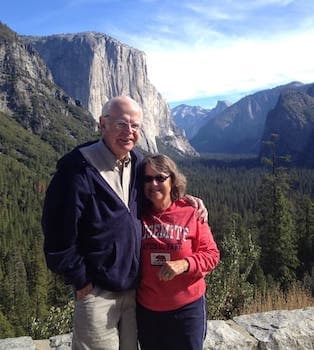
Ted Mooney, P.E. RET
Striving to live Aloha
finishing.com - Pine Beach, New Jersey
Q. Please let us know how to handle samples for salt spray test? Is it mentioned in any standard? If yes then please provide.
Mahesh Kenjale- Mumbai, India
July 15, 2020
A. Hi Majesh. More words please! Sorry, but I don't now what you mean by "how to handle".
What has your customer told you to do? If no one has told you to do anything, what would you like to learn from a salt spray test? Does your shop operate a salt spray chamber or would you send the parts out. What are you plating, and what specification are you plating to? Thanks.
Luck & Regards,
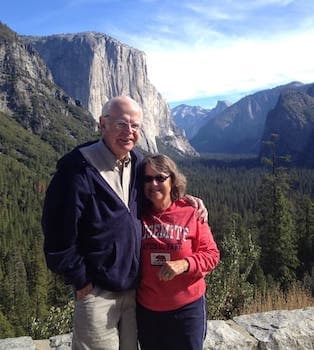
Ted Mooney, P.E. RET
Striving to live Aloha
finishing.com - Pine Beach, New Jersey
Q. I have a casting sample hub; I painted it.
My plate sample size (100 x 150 x 0.8 mm) has received 500 hours of salt spray test.
But the salt spray test on the actual casting sample is failing, even keeping the paint thickness at 200 microns.
Found red rust after 48 hrs.
- Pune, Maharashtra
August 7, 2020
A. Hi Sandip. Well, that's the main function of salt spray testing: to tell you that you are not finishing the product the way you should :-)
Unfortunately I am not quite understanding your situation. Are you saying that you painted a 100 x 150 test panel and it survived 500 hours, then you painted your actual product and it survived only 48 hours? You are calling this actual product a 'casting sample hub' -- does 'casting' mean that it's cast iron or sintered metal?
Please describe exactly what the component is, what general technology was used to manufacture it, and what cleaning and pretreatment preceded the painting. Failure probably has a lot more to do with pretreatment than with paint thickness. Thanks.
Luck & Regards,
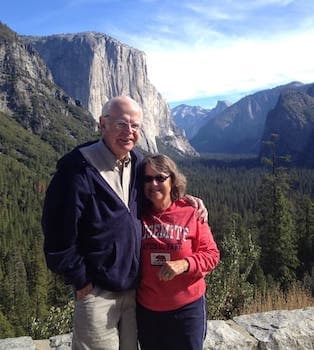
Ted Mooney, P.E. RET
Striving to live Aloha
finishing.com - Pine Beach, New Jersey
Q. What is acceptance value for rust creepage in SST method?
GP/ Prakash muthuCorrosion engg QA - Coimbatore, India
December 23, 2022
A. Hi Prakash.
ASTM B117, "Standard Practice for Operating Salt Spray (Fog) Apparatus", does not define the acceptance value ... only how to run the tests.
The components are presumably plated, painted, or otherwise finished according to some specification, and it is that specification which contains the acceptance criteria for compliance with the specification.
Luck & Regards,
Ted Mooney, P.E. RET
Striving to live Aloha
finishing.com - Pine Beach, New Jersey
Q. Hi, I do non-cyanide alkaline Zn plating with white silver passivation and sealer on ms square pipe. But I am facing a problem for last three months that Black stain is observed in 24 hrs. in SST, while impurity report of plating solution is okay, & solution of passivation & Sealer is also new. Please suggest that what is the reason for this?
Anupam Pandey- Noida, Uttar Pradesh , India
July 15, 2023
A. Hi Anupam,
Black stain in 24 hours may not be a problem: please see posting by Subramanian Ramajayam on this page. The spec you have agreed to plate to tells you and your customer what constitutes satisfactory plating vs. failure. If you are not plating to any specification at all, there is no good way to agree upon whether the plating is satisfactory or it isn't; but you could still look at specs like ASTM B633 to see what they say about it.
Luck & Regards,
Ted Mooney, P.E. RET
Striving to live Aloha
finishing.com - Pine Beach, New Jersey
Q. What is the ideal time to conduct the salt spray test after lacquer process, as observed parts getting ok results (120 hrs) if SST conduct after 48 hrs of lacquer process. Is there any standard available for that?
Kamlesh Sonar- Pune, India
September 27, 2023
A. Hi Kamlesh.
Are you agreeing to apply lacquer in accord with any particular standard? If not, then waiting for a 48-hour cure time sounds fine to me, especially if your objective is simply to pass the test rather than to use it as an early warning of the process getting out of control.
Luck & Regards,
Ted Mooney, P.E. RET
Striving to live Aloha
finishing.com - Pine Beach, New Jersey

Q, A, or Comment on THIS thread -or- Start a NEW Thread