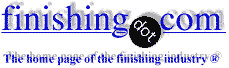
-----
Temperature limit for MIL-DTL-5541 chromate conversion coating on aluminum (Alodine, Iridite, chem film)
Quickstart:
Aluminum is often 'chromate conversion coated' as a corrosion resistant final finish or as a pretreatment for painting or powder coating. The process actually involves many steps, usually including alkaline cleaning, etching, deox/desmut, the chromate conversion step per se, and water rinses between each step.
MIL-C-5541 / MIL-DTL-5541 / MIL PRF-5541 is the most commonly cited spec. "Alodine" and "Iridite" are proprietary trade names from two suppliers of the process chemistry. "Chem film" is a slang term for the process often used in the USA.
Q. Greetings,
My question has to do with your previous posting as repeated here:
"In doing significant electrical bonding research, we discovered that class III Alodine is compromised by high temperatures even after curing.
The temperature limit is about 140 °F. If exposed to temperatures about 160 °F for more than three hours, the conductivity of class III Alodine is no better than class I Alodine.
The lapse of time between the plating and the test seemed to have no significant impact. We were told that Alodine "resides" as a gel with a certain amount of moisture in the solution.
As the moisture bakes out the corrosion resistance goes down and the electrical resistance goes up. The specific amount seems to only be able to be determined empirically and seems to have a host of variables.
In our case we were trying to get a colored anodize after applying the class III Alodine ..."
My question about this is as follows:
Our company builds high performance radio equipment, and we need Class 3 conductivity for our aluminum (6061-T6) shields to make good electrical contact to the gold plated ground areas on our PCB's.
Since I'm not sure how old your posting is, my first question is whether your experience and research with 60 to 70 °C post-curing temperature limitations for Class 3 Alodine was done with modern RoHS Trivalent chem films (for example: films like Metalast/Chemeon TCP-HF)?
If your research is/was with newer Trivalent chromium coatings, then can you direct me to websites and/or documents that give more details on Trivalent coatings that don't meet Class 3 conductivity at 60 to 70 °C (with test details), and also any Trivalent coatings that do meet Class 3 conductivity with that temperature range or even higher (and roughly how high)?
P.S. I've seen the relevant paragraph 6.14 in the MIL-DTL-5541F specs on the 60 °C temperature limitations, but at least one person has said that only applies to older hexavalent chromium coatings, and they said their Trivalent coating can handle 120 °C, but they can produce no proof of that, especially regarding Class 3 conductivity.
Thanks you so much for your help (and/or anyone who responds)!
- Mt Airy, Maryland
March 19, 2024
Q. So, the elevated temperature cooks the moisture out of the gel. I've got parts in a humidity chamber at 65 °C and 95% RH. Does this cookout still happen?
Jason Mansfieldmechanical design engineer - Oak Creek, Wisconsin
July 25, 2024
⇩ Related postings, oldest first ⇩
Q. I am a manufacturing Engineer in Wichita KS. We have been experiencing difficulties painting Alodine coated aluminum. We have been using a Zinc-zinc dust ⇦ on eBay or Amazon [affil link] er that does not want to stick good to the surface. We use the tape test and it always fails.
Is there any other primer that might work better? Would it adhere better at a higher temperature, like 80 to 90 °F? We are using Dupont 491-17 Etch-Primer.
Dale O [last name deleted for privacy by Editor]- Wichita, Kansas
2001
A. Hello Dale,
The Alodine coating should provide a decent surface for paint to adhere to without using a primer. Alodining is a chromate conversion coating, supposed to pass 150-hour salt spray. I'd say quit with the zinc-chromate and try to paint right over the Alodined aluminum. I'd also stay away from etching primers, the "etch" is usually an acid, which might negate the usefulness of the Alodine. If you can't get good adhesion, try an epoxy primer, providing you are topcoating with an opaque color (epoxies chalk outdoors if a clear or tinted topcoat is used).
Good luck,
Jake KochG. J. Nikolas &Co.,Inc.

Bellwood, Illinois
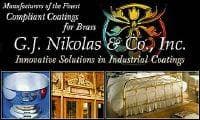
A. I do not think that your primer is the problem. The first two things I would investigate would be the Alodine film. Perform the test on the bare Alodine and see if any of the coating is removed. If so, then the coating may be too thick and powdery causing a failure at this interface. The second place I would investigate is the part handling. Are any soils accumulating on the surface? Is the Alodine coating given ample time to dry? When the Alodine is dried is it at an elevated temperature? Normally temps in excess of 150 °F begin to degrade the coating. I hope this gives you some direction in your investigation.
Best of Luck.
Ira Donovan, M.S.F.Kansas City, Missouri
2001
A. Dale - One important factor to consider is the amount of time from when the conversion coating was applied to when it is primed/painted. The surface tension of the coating changes as time goes on, thus increasing the risk for paint adhesion issues. General guideline is apply subsequent coating within 3 days for water-based paints; within 7 days for solvent-based. Best scenario is to paint as soon as the conversion coating dries.
Also, make sure the coating weight of the conversion coating is not too high, this will affect adhesion of any subsequent coating. Best of luck!!
Technical Rep - Brunswick, Ohio
October 28, 2021
Multiple threads merged: please forgive chronology errors and repetition 🙂
Q. My understanding of chromate conversion on aluminum is to promote paint adhesion, but that the chromate degrades at temperatures over 150 °F. I am also aware that studies have been done that show no degradation at higher temperatures. I need to powder coat a part at 400 °F for 10 min. The print specifies chromate conversion. Will this temperature degrade the chromate and cause loss of adhesion?
JAMES M. LISEFSKIAIRCRAFT - HAMMONDSPORT, New York
2001
A. Hi,
Chromating of alloy is the norm prior to powder coating. Temperature degradation refers to heating in air (i.e. no paint film). Green chromating is more tolerant of overheating, but yellow is better on alloys.
In short - no problems!
Roger BridgerWalterisation UK Ltd. - Croydon, UK
Q. Most, if not all, technical bulletins and specs state that chromate conversion coatings on aluminum are not to be dried at temperatures over 140 °F. Is there some point after drying when it would be allowable to subject the conversion coated part to temperatures over 140 °F?
We apply a chromate conversion coating to aluminum parts. Then we apply a lacquer maskant to mask selected areas prior to a subsequent anodize coating. After the anodize operation, we remove most of the lacquer maskant by soaking the parts in a solvent. I would like to remove the left-over traces of lacquer in a vapor degreaser, but the degreaser temperature is about 190 °F. Once the chromate conversion coating has "set up", is it allowable to subject it to the 190 °F degreaser?
Kent Kessler- Seattle, Washington, USA
2005
A. Even after the chem-film has "set up", it still exists in a somewhat gel-like form, and temperatures above 140 °F still have the ability to dehydrate it and significantly decrease corrosion resistance (I believe that Wernick, Pinner and Sheasby talk about this, but I don't have my copy at hand).
There are some exceptions to this rule, for example when used as a base for powder coating it is pretty typical to not see negative results during curing; but I think what your proposing would seriously compromise the chem-film coating.
Of course, you could always test it - take two identical pieces and process them the same with the exception of that drying step. Then get them tested to the requirements of MIL-C-5541 and see how they compare.
Good luck,
Compton, California, USA
A. Hi. The "Chemical Conversion Coatings" chapter of Wernick, Pinner and Sheasby's "The Surface Treatment and Finishing of Aluminum and Its Alloys" [on AbeBooks or Amazon or eBay affil links] runs 69 pages, so it can't be summarized into a paragraph, but as Jim says, it claims the protective value is reduced above 60 °C (140 °F).
Regards,
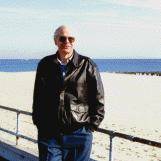
Ted Mooney, P.E.
Striving to live Aloha
(Ted can offer longterm or instant help)
finishing.com - Pine Beach, New Jersey
Quickstart:
Military spec. MIL-C-5541 is often used in specifying the requirements for chromate conversion coating.
The spec describes two classes of coating:
Class 1A, "For maximum protection against corrosion, painted or unpainted" and
Class 3, "For protection against corrosion where low electrical resistance is required".
A. In doing significant electrical bonding research, we discovered that class III Alodine is compromised by high temperatures even after curing.
The temperature limit is about 140 °F. if exposed to temperatures about 160 °F for more than three hours, the conductivity of class III Alodine is no better than class I Alodine.
The lapse of time between the plating and the test seemed to have no significant impact. We were told that Alodine "resides" as a gel with a certain amount of moisture in the solution.
As the moisture bakes out the corrosion resistance goes down and the electrical resistance goes up. The specific amount seems to only be able to be determined empirically and seems to have a host of variables.
In our case we were trying to get a colored anodize after applying the class III Alodine. We had to reverse our process and do the anodizing (with mask) first and the Alodining second in order to maintain the class III.
Larry Sickler- Rockford, Illinois, USA
2005
A. After the chromate conversion, allow the components to stand for 3 days before baking. We sometimes bake parts at 125 °C after a 3-day wait with no problems.
Chris Matthews- East Sussex, England
2005
350 °F bake to cure epoxy bonding on chromated aluminum
Q. Greetings,
We are a special process house performing conversion coating per MIL-DTL-5541
[⇦ this spec on DLA], Type I, Class 1A, and painting. We are having some paint adhesion issues with one customer's parts. On these parts we perform the conversion coating. The parts are returned to the customer for some assembly. This assembly includes some epoxy bonding where the parts are baked at 350 °F for an hour to cure the epoxy. The parts are then returned to us for painting.
We clean the parts using Isopropyl Alcohol and acetone ⇦ on eBay or Amazon [affil link] Warning! Flammable! to remove any grease or oils prior to painting. The parts appear to be very clean prior to paint and the paints are applied in accordance with the applicable specifications, but yet we are having some adhesion issues. We know that high temperature will degrade the corrosion protective qualities of the chem- film but will the high temperature also affect the surface to the point that will affect adhesion?
Peter Doylespecial processing - Phoenix, Arizona, USA
May 25, 2012
by Raj & Ali
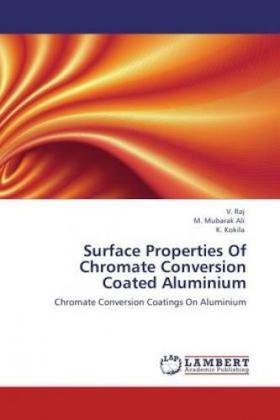
on eBay or Amazon
or AbeBooks
(affil link)
A. The chromate is on too heavy. For paint base, put the chromate on very light, just barely a color. If it is on too thick the baking dehydrates it and causes the paint to flake.
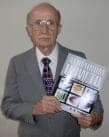
Robert H Probert
Robert H Probert Technical Services

Garner, North Carolina
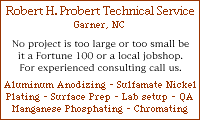
A. By most specifications and standard practice, baking chem film except the new RoHS-compliant one is not recommended above 140 ° F (60 °C). If you have baked it above this temperature and it is not completely covered by a paint you will lose most if not all if the adhesion characteristics of the film -- not to mention violating most of the specifications in the aerospace industry if the parts are used for that.
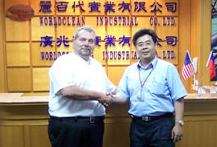
Drew Nosti, CEF
Anodize USA

Ladson, South Carolina
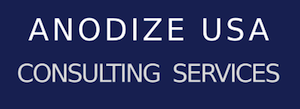
Temperature limits for RoHS-compatible conversion coating
"... chem film except the new RoHS-compliant one is not recommended above 140 °F. (60 °C)"
Q. What's a reasonable upper service temperature limit (for salt spray test and/or general corrosion resistance, e.g., occasional [acid] rain, seawater splashing, etc.) for the new RoHS chem-film (MIL-DTL-5541F Type II) vs. older hexavalent Type I? Will Type II hold up to say 70 °C vs 60 °C? Higher?
- Wilmington, Massachusetts, USA
June 26, 2012
A. Stephen
You could probably get this information from the Technical Product Bulletin for the material being used to produce the coating. Our Type I TPB recommends <160 °F and our Type II recommends <120 °F for maximum drying temperatures.
If your product is subject to elevated temperatures, your testing might include coupons with simulated environmental conditions.
- Colorado Springs, Colorado
Q. Which is the limit temperatures that Alodine 1200s or Iridite coating treatment over AA 7075 T73, Invar 36/32, and Ti6Al4V could withstand without degradation of performances?
Jorger Rueda Nuñez de VillavicencioRYMSA - Spain
2003
A. Alodine and Iridite are family names for chromate conversion coatings. Products are available for coating aluminum, and the USA MIL-Spec limits the temperature on bare coatings to under 140 °F. I do not know of any way to chromate Invar and Titanium. Iridite does not have products for Invar and Titanium.
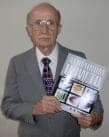
Robert H Probert
Robert H Probert Technical Services

Garner, North Carolina
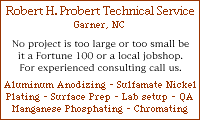
2003
Multiple threads merged: please forgive chronology errors and repetition 🙂
Q. Hello,
I have some requests concerning chromate conversion (Alodine 1200) on aluminum alloys (like 6061 T6):
- what is the higher temperature limit that can bear Alodine coated parts? what is the lower temperature at which properties of Alodine coat start to decrease or collapse?
- what is the behavior of Alodine coat when coated parts are placed in vacuum?
- what are the effects on Alodine coated parts when those parts are placed in vacuum at high temperature?
Thanks,
John J. Proctor- Los Angeles, California, USA
2003
A. Alodine or any chem-film is a very thin gel of aluminum chromate. It does not like temps above 140 °F and it does not like vacuum conditions as it dehydrates the gel too much and turns it to a powder. The longer it has been on the part, the longer the time it will take to degrade, but degrade it will. A good reason why they paint exposed surfaces.
James Watts- Navarre, Florida
A. Dear John,
I'm assuming you are asking this question for use in a space application. I am currently facing a similar problem with a space component which has to sustain high temperatures in low earth orbit. The problem with alternative finishes, as far as I've been able to gather, is that we need the finished part to retain high electric conductivity.
If you have found an alternative, or wish to discuss this matter, please leave a message at the board. I'd really appreciate some insight.
- São Bernardo, São Paulo, Brazil
August 31, 2009
Powder Coat over Alodine?
Q. We build an assembly consisting of a cast Aluminum part, tack welded to an Aluminum sheet metal part, epoxied to a formed Aluminum sheet metal part with stainless steel threaded inserts. We are presently Polyester Powder Coating the final assembly for corrosion and aesthetics reasons. We are having some corrosion problems in the field (this is an outdoor product) mainly with the Powder Coating flaking off cast Aluminum part. I have read several of the postings related to an Alodine undercoating to the Powder Coating but do not understand what happens to the Alodine at curing temperatures. Most Powder Coats require 300-400 °F to cure. What I have read about Alodine is that is not good for applications over 120 °F. Does the Alodine retain its corrosion resistant characteristics after exposure to high temperatures? Wet paint seems to on its way out in California and an Anodize under coating does not lend itself to the assembly process because of the epoxy and stainless steel inserts. Any further clarifications or suggestions for a corrosion resistant under coating would be appreciated.
John ConnerMech. Design Engineer - Sacramento, California, USA
2007
A. The temperature restrictions apply to unpainted Alodine®. The powder coating protects the chromate from dehydrating and cracking during the high temperature cure.
Adhesion problems due to improper chromating could be due to:
1) Poor aluminum pretreatment (e.g., over-etching, wrong deoxidizer for castings, dirty rinses),
2) Dirty post-chromate rinses; final rinsing in DI water is best (if not using a Deoxylyte® final rinse),
3) Excessively thick chromate; try Type II per ASTM B449 (twixt Classes 1A & 3 of MIL-DTL-5541
[⇦ this spec on DLA]).
4) Under-cured chromate (soft gel, lacking strength),
5) Over-cured chromate (powdered & cracked. Metal temperature shouldn't exceed 150 °F).
See the appropriate Alodine product bulletin or MIL-HNDBK-509 CLEANING AND TREATMENT OF ALUMINUM PARTS PRIOR TO PAINTING for more info. Final rinsing in Deoxylyte® (rather than DI water) is given. Most Deoxylyte versions are dilute chromic acid solutions; Henkel likely has a non-hex. chromium version by now.
What adhesion & corrosion testing is currently performed? In thread 45803, Sheldon Taylor describes D-I-Y testing of X-scribed painted samples in boiling water, similar to ASTM D870. Another quick test is adhesive tape testing of crosshatched samples, see ASTM D3359 or search this site. If successful with these, then do the more rigorous tests. E.g., have scribed samples tested by a lab per ASTM D2803, 'Standard Guide for Testing Filiform Corrosion Resistance of Organic Coatings on Metal,' either Procedure A or C (both are salt-fog followed by humidity). Thread 38976 "Specifications for Powder Coated Aluminum -- AAMA 2603, 2604, 2605" gives additional tests.
- Goleta, California

Rest in peace, Ken. Thank you for your hard work which the finishing world, and we at finishing.com, continue to benefit from.
A. Hi,
Your problem sounds more like a curing defect. Have you tried to re-bake a defective component for a second time? We had a customer with the same problem on cast aluminium - a longer bake cured the problem.
Birmingham, United Kingdom
Q. We are experiencing similar problems with paint adhesion on Alodined parts and cannot seem to nail the root cause.
Are there any other things other than above that we should be looking for? We have ran numerous test panels and found from that testing that letting the primer sit for more than 3 hours will result in a very high failure rate.
We have also found that flash times are not as important as we first believed.
If there is there something that we are missing we would appreciate your help.
Regards,
aerospace - Ontario, Canada
May 8, 2013
A. Hi Gary,
Ira's previous answer is a good starting point. I do not know which paint system you are using, so specific answers cannot be given.
Firstly I'd start by looking at the handling of parts, are all the operators wearing gloves? Is there any other way parts may get contamination on the surface? If there is any way that there may be a contamination issue you will need to have some form of pre-clean before you prime (something like a solvent clean using a clean solvent such as IPA
⇦ on
eBay or
Amazon [affil link] or acetone
⇦ on
eBay
or
Amazon
[affil link] Warning! Flammable!
).
Secondly look at any mixing. I don't know if you are using a 1 part or 2 part mix, but if it is a two part check that the right mixing ratios are used. Check that the correct viscosity is obtained and ensure the full induction time is used before application.
Thirdly look at your environmental conditions. Primers can be quite sensitive to atmospheric moisture, so if you are regularly going over 70% RH you will need to look at restricting painting during these times or consider introducing some environmental controls (that will mean considerable investment though).
Finally look at the curing cycle. Are you leaving it for a sufficient time? To be honest 3 hours seems to be far too quick for a room temperature drying primer. You will probably need to leave it for at least 24 hours and full cure will probably not be reached for 7 days. Most primers will be able to be heat cured, look at the manufacturer's Technical Data Sheet (TDS), this will tell you if it can be accelerated, alternatively talk to the manufacturer and see if they have a recommended heat cure cycle if there isn't one on the TDS.
That should get you started.
Aerospace - Yeovil, Somerset, UK
A. I suspect the chromate coating is too heavy. For painting, the chromate must be very thin, down in the iridescent area.
Robert H Probert
Robert H Probert Technical Services
Garner, North Carolina
June 19, 2017
Alodine 1200S lowest service temperature
Q. Hi,
What are the temperature limits for Alodine 1200 S? I only have found the upper limit, around 140 °F, but I also need to know the lower limit.
Best regards
Mechanical Engineer - Coimbra, PORTUGAL
November 28, 2013
A. The manufacturer recommends a lower limit of 70 °F. and a high limit of 100 ° F. The 140 °F you mention is not an application temperature, but the temperature at which the still wet or new coating will begin to deteriorate, meaning your rinses and drying should not exceed that temperature.
I have seen operations that work OK at room temp, down to 55 °F, but cooler temperature do interfere with the reaction, creating a poor coating. Salt Spray testing may help in establishing limits outside of the manufacturers recommendations.
- Cedar Rapids, Iowa, USA
December 6, 2013
A. Alodine (or Bonderite) 1200S:
If you're inquiring as to the temp of the bath, it's supposed to be between 70 & 100 °F. However, it also states to be oven dried at temperatures up to 140 °F. This high of a temperature can be problematic - causing the coating to become powdery & ineffective. Many reliable sources recommend to NOT use oven temps over 130 ° F, or to air dry - to not put them into an oven at all. This is especially true when using 2024-T3 aluminum, as it's unusually high copper content is uniquely affected by high temps and the copper molecules migrate to the surface causing corrosion - especially in salt spray corrosion chambers.
- Seattle, Washington, USA
December 9, 2013
A. Hi Juan,
As I read it you want to understand what temperatures an Alodined surface can survive in service.
Chromate conversion coatings are used extensively in the Aerospace industry. Typical operating temperatures will be down to -55 °C, in extreme cases it may be as low as -65 °C.
I am afraid I do not know what the performance would be like in cryogenic use (liquid nitrogen/liquid oxygen type temperatures).
Aerospace - Yeovil, Somerset, UK
January 4, 2017
A. Hi, I am now retired but spent many years in aerospace manufacturing as head of engineering and Manufacturing V.P.
If you have adhesion problems try increasing your Metal prep (phosphoric acid) immersion time. The surface must have a frosted look before Alodine. We followed the Boeing spec.
Harry
Aeromarine Consulting - Fonthill, ON, Canada
October 25, 2018
Hi Harry. I've heard of chromic-phosphate coatings for aluminum, but it sounds like either you are not correctly recollecting what what your "Alodine" was or you are introducing us to a technology I'm not yet familiar with :-)
Regards,
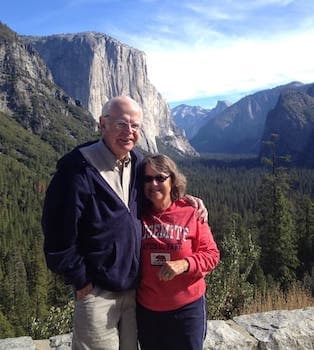
Ted Mooney, P.E. RET
Striving to live Aloha
(Ted can offer longterm or instant help)
finishing.com - Pine Beach, New Jersey
Q. We have been having adhesion issues recently with our primer (Amerlock 2) and top coat (PSX 700) system failing at the substrate. We conversion coat (Iridite 14-2) in a bath immersion application. After several days we bake in an oven around 200 °F for 5 hours in a bag under a vacuum for another process. After this, we prime and paint. I believe our adhesion failure is due to baking the Chem-film and "sucking" the moisture from it. If this is the case, where can I find supporting info to back me up that it not only degrades corrosion protection, but also its adhesion properties. I can't find many studies on the effects on adhesion and the TDS just states it may degrade corrosion protection. Thank you.
Alan Doan- Indianapolis Indiana USA
November 30, 2018
A. Please see this article:
https://www.pfonline.com/articles/chromate-conversion-coatings
Also, BAC5719 specifically states not to heat above 130 °F.
- Seattle, Washington, USA
Q. Fauna, thanks for your response, but the link you provided did not answer my question. It states a loss in corrosion protection values but does not state the effects on adhesion. Also I am looking for an academic article rather than a blog. Thanks again.
One would assume that if you "dry out" the Chem film by exposing a bare, coated part to Temps over 140 °F, it would affect adhesion of a future paint system.
- Indianapolis Indiana USA
by Raj & Ali
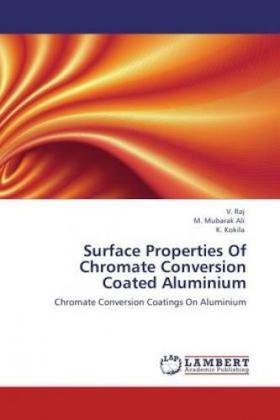
on eBay or Amazon
or AbeBooks
(affil link)
A. Hi Alan. This book looks like the most applicable one I can find .
but I haven't read it nor found any reviews. There is also an old book by Fred Perlstein, "Heat Resistant Chromate Conversion Coatings". A conversion coating book that I do have, Biestek & Weber "Electrolytic and Chemical Conversion Coatings" doesn't seem to cover it. Wernick, Pinner, & Sheasby [on
AbeBooks or
Amazon or
eBay affil links] simply says that MIL specs forbid unpainted conversion coated aluminum at above 65°C.
Metal Finishing Information Services / Finishing Publications in Birmingham U.K. offers their SurfaceQuery.com free search of metal finishing literature. A quick scan of that database seemed to indicate that you're going to have trouble finding a technical article with twenty seven eight-by-ten colour glossy photographs of the effects of temperature on adhesion for the various types of zinc plating and zinc brighteners, and the various proprietary trivalent and hexavalent chem films, and the various organic coatings.
Google scholar list some articles, but I don't know if any are applicable.
Regards,
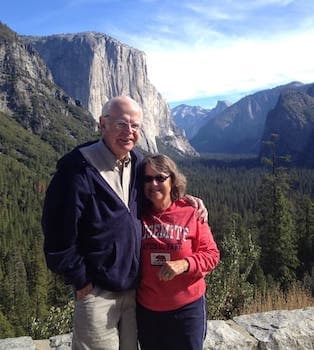
Ted Mooney, P.E. RET
Striving to live Aloha
(Ted can offer longterm or instant help)
finishing.com - Pine Beach, New Jersey
A. Alan,
Per chapter 16 of "Advanced Surface Technology" by Moller and Nielsen:
"The reason for this destruction [corrosion inhibition] is associated with a transformation of the hexavalent chromium compounds into insoluble compounds by heating. The formation of an insoluble chrome compound prevents the soluble hexavalent chromium compounds from acting as an anodic inhibitor."
I realize this is referring to the corrosion resistance but I would think any disruption in anodic activity on the surface could reasonably lead to primer/paint adhesion issues. I couldn't find any studies exploring this further but have you tried to perform an adhesion test before and after your bake? I've never used it myself but ASTM B201-80 has a soft gum adhesion test for chromates.
Ted: I see what you did there ;) Don't forget the circles and arrows and the paragraph on the back of each one.
- Agawam, Massachusetts USA
? Hi again Alan,
This is not really a response to your question, but thinking out loud and wondering if other people are thinking similarly. When a chromate coating is covered with a powder coating, not only is it less prone to drying out, but it's not directly exposed to the oxygen in the air, the decomposition into "... insoluble chrome compound ..." is probably significantly slowed.
You could be correct that your vacuum process is sucking out the moisture and creating a problem despite the paint layers. Can you bake a test part separately without the vacuum?
Jameson,
We'll
Regards,
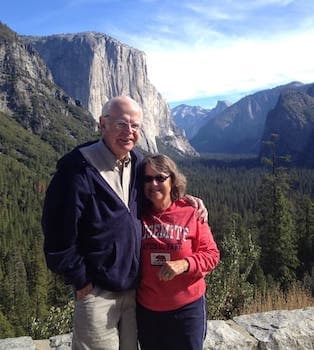
Ted Mooney, P.E. RET
Striving to live Aloha
(Ted can offer longterm or instant help)
finishing.com - Pine Beach, New Jersey
Q. I'm working on a part that is nickel plated aluminum (electroless nickel class 4 grade 1).
There are a few small regions, maybe 0.030" diameter, where the plating has come off.
We need corrosion protection and were hoping to spot treat the exposed aluminum with chem-film. However the chem film spec states that chem film can lose it's corrosion protection at 60 °C or higher.
Does anyone have experience with this temperature limit? The spec (listed below) is pretty vague.
The limit seems inconsistent with applications where chem film is used on parts whose temperatures easily run between 70-80 °C.
Also, one would expect gradual temperature degradation rather than a hard limit at 60 °C
6.14 Temperature effects on corrosion protection. Unpainted conversion coatings will
commence losing corrosion resistance properties if exposed to temperatures of 140 °F (60 °C) or
higher, during drying, subsequent fabrication, or service. As temperatures and exposure times
increase, the corrosion protection of unpainted conversion coated parts decreases. The reduction
is believed to result from the coating dehydrating and the resulting insolubility of the chromates
within the coating.
==
Paul Hiester
- Lancaster Pennsylvania
October 4, 2021
Q, A, or Comment on THIS thread -or- Start a NEW Thread