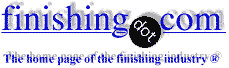
-----
Is type III hardcoating as hard to do as I hear?
2005
We have been sending out 6061-T6 parts for black hardcoating and have had mixed results. Some parts come back fine while others are very dull. We set up our own electropolishing line after similar problems with those vendors and now want to set up our own hard coat anodizing line. From what I hear, it is much more difficult to do than normal anodizing. I have read books but vendors who do the process keep the method "secret".
My questions are:
1) What do we do with the raw parts before anodizing? Existing vendors use something called "bright dip" which I think is 94% 85% phosphoric acid and 6% 42Be Nitric acid at 180-185F. Is this the correct mixture and first step?
2) Next, it seems that a bath of sulfuric acid is used at a temperature of about 39 deg F. I have heard of concentrations from 20% to 50%. What is the standard here?
3) Is there any simple means of chilling the tank (our tank is small 18" x 18" x 36"). I have seen big roof mounted chillers for sale but we just need a small unit. I was thinking of running a stainless coil inside with an mixture of water and car antifreeze that then passes through a heat exchanger cooled by a big air conditioner unit from Walmart. I would control the flow rate with a simple PID controller and thermocouple in the tank. Looking at the heat input Q from the power densities (say 30A per square foot) I think we could accomplish this. We just need to adjust the sensor in the air conditioner to allow it to drop below the set point (currently about 50F). Would be a whole lot easier if we could find a small chiller instead but so far no luck. Is there anything like this available or should we continue with our home made chiller?
4) After anodizing, we want a bright black finish. Vendors have had lots of problems with giving us consistent finishes. How can we get a bright black finish instead of a blotchy dull color on 6061-T6?
5) Honestly, should we just give up now and vow to the inconsistent vendors (with our fingers crossed every time) or is this thing doable for our small shop? We figured out how to make and set up an electropolishing system but this hard coating does seem to be more involved. The hard point for us is the chilling. What do you think?
Thanks for the feedback
Tim Tylaska- Mystic, Connecticut, USA
The first question you need to answer is why do you need Type III? To paraphrase Bob Probert (a regular here) if you think Type III is "harder" than Type II you're in for a disappointment, its not. Your reason needs to be that you need extreme mechanical wear resistance, where the higher coating density of Type III has the advantage.
Your second question is what is the surface area(s) of the work and how many pieces do you want to do at a time? The resulting total batch surface area will dictate equipment sizing.
Type II can be formed to the same thickness as Type III; as such its easier and cheaper to do, this can be done at room temp with less stringent agitation requirements and at about half the current density as Type III. This also means that it takes about twice the anodization time for the same coating thickness. You can further increase the CD if your cooling can handle it. The longer anodization time also means that controlling dissolution becomes more important. The resulting "Type II 1/2" can be dyed as well as conventional Type II, giving you this option. "Type II 1/2" due to the thickness; also looses the metallic look, so it looks like Type III, but usually the cosmetics are too good to be "real" Type III.
Paul Yursis [deceased]- Columbia, Maryland, USA
Ed. note: it is our sad duty to advise of the passing of Paul Yursis in August 2005.
Here is a brief obituary by Mike Caswell.
First of two simultaneous responses --
If you're now doing electropolishing well, you can do hard coat. It's no more difficult, although there are more steps. As to your questions about chilling, process steps, etc - well, there is always more than one way to skin a cat. Get a good book on the subject and go for it.
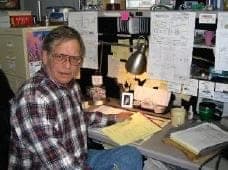
Jeffrey Holmes, CEF
Spartanburg, South Carolina
2005
Second of two simultaneous responses -- 2005
consistent hard coat from lot to lot is not easy, or everyone would do it. Some do it far better than others.
If you do a lot of internet searching, you can find chiller units all ready assembled with proven capability. Finding a good one at a reasonable price will take some doing. Check out all of the vendors in the metal finishing guide book and product finishing for starters. Also do not forget to check out the vendors that support this site. Buying used chillers is a lot cheaper but is a risk unless you know what to look for. You might want to look at used laboratory chillers--Think eBay for this. Excellent if you can find one large enough.
USEPA will get very excited if you have a spill of car anti freeze. (ethylene glycol) For a few bucks more a gallon, you can get propylene glycol which you will find in some foods like bread. Works very nearly as well and a spill is no big deal.
Stainless, even seamless 316SS is attacked by the sulfuric acid solution if the temp goes above 70F, so you will need to keep the temp below that or take the coil out of the tank when not in use.
Real hard coat is done at 32F with agitation, normally a small air sparger. That means that the entire run does not vary by more than 1 degree, or you will see visual differences in larger parts.
Before you get carried away with buying equipment, buy the book Light Metal Finishing by Grubbs and Montgomery from AESF. Written in layman's language. It is a notebook and only costs around $50 ±.
James Watts- Navarre, Florida
2005
Paul:
Thanks for the response Feb 9. We wanted to hard coat the parts because they are in a seawater environment. It seems that every other similar aluminum part made by different manufactures is indeed hard coated for corrosion protection. The alloy we are using is 6061-T6 (we had used 7075 but it delaminated). It would be great if the regular anodizing held up as good as the hard coat. We aren't sure. What we will do is put a few samples of anodized parts and hard coated parts in our salt spray tester and let them run for a few weeks. I will look at the surface with my zeiss scope to see if there is any difference. It would be great if we could just plain anodize longer.
From what I had read, anodizing longer doesn't really work as the thickness builds up to a point and then stops. We are going to use a ramp up power supply. Will have to try and find out what happens. Thanks.
Tim Tylaska- Mystic, Connecticut, USA
2005
James:
Thanks for the response. I have looked around for a small chilling unit and have had little luck. We are going to hard coat about 1 sf max at a time. We may run 5 or 6 of these cycles per day. Based upon a current of say 30 amps and a voltage of maybe 60V max, we would have a max input Q to the tank of 1800 W or about 6100 BTU/hr. Say that the cycle time is 45 minutes. Our Q input per run is 4600 BTU.
Based upon the conduction and convection coefficients of the tank walls and the free surface of the liquid, it looks like the steady state input would have to be more of about 10000 BTU/hr to keep things at say 39 F in a 70 F ambient with the max power input to the rack. What we plan to do is actually use a used household "stand up" type freezer instead of the air conditioner. We will run a coil through the tank and then drill a few holes through the side of the freezer. We are going to use a household furnace circulator pump to transfer the heat exchanging fluid. Inside the freezer we plan to make a tank full of brine and freeze the brine around the coils. Based upon the size of our tank (50 gallons) we need to melt 100 lbs of ice just to drop the temperature to to 30 degree range (based on 144 btu/lb for ice fusion ) from room temperature. Our main problem is that the heat transfer flux of our coil is not very good when the temperature of our working fluid (anti-freeze or better yet your propylene glycol recommendation) is close to the temperature of the anodizing tank. We can drop the freezing point down to maybe 20F, but at a 32F tank temp this gives us a delta T of only 12 F. When you calculate the heat exchanger performance at such a small delta T things get out of hand. It would be best if our fluid was colder (say 10 or even 0 F) but I don't have an easy way to do that with our indirect means. If we ran the freon coil into the bath itself we would run into more problems.
As far as 316SS being attacked by sulfuric acid, we found that 316L is quite resistant. We have had 50% H2So4 and 50% H3PO4 in a 316L stainless tank at 140F for 2 years now. There has been no measurable attack anywhere. ( I originally had planned on having to go with Hastelloy X. We found that 316L starts to turn brown and become attacked only at above approx. 230° F. HCl attacks stainless very fast but no real problems with H2So4. In a cold tank (say 70F to 30F) 316L should last more or less forever.
As far as the temperature control, we would like to use a simple control system to pump the water. I haven't calculated the response of the system yet so this is the only unknown here. A lot of thermal inertia for 50 gallons of fluid so I think we could control this system is the coil has a high enough DT/dt. Will simulate this on Matlab simulink if I can, or will just figure out the 2nd order equations if I can get a good idea of the coefficients for the constants here.
I appreciate your suggestion of the book. I will try to order a copy. Thanks.
Tim Tylaska- Mystic, Connecticut, USA
Tim,
I'm sure everyone here would be interested in the results of your salt spray test. Something to consider; the samples need to have about the same coating thickness for the test to be valid.
I have some data for a "Type II 1/2" coating on 6061.
90 minutes at 21ASF produced a coating measuring 70um thick (almost 3 mils). Electrolyte temp. 70-72 deg. F., traditional 165g/l electrolyte. Agitation and temp regulation was provided by recirculating the electrolyte (all of it) continuously through a chiller. No dissolution signs whatsoever, no dyeing issues.
I've heard that "anodize will only build up to a point" stuff too. I believe this to be another anodizing "old wive's tale", it does not hold up to either mathematical scrutiny or properly controlled experiment.
The layer will stop forming when electrolyte can no longer make electrical contact with the base metal via the electrolyte in the pores. This happens when either the anode connection to the work anodizes to a high resistance, or the required voltage to support the desired CD is not available. The bulk resistance of the anodic coating increases with thickness; the thicker the coating, the greater the resistance, and consequently the higher the required voltage for a given current.
In the example I gave above; for 21 ASF, 1 sq.ft. surface area, 41V was required at the 90 minute point. Anode connection degradation was eliminated by using Al wire fusion welded to the sample.
- Columbia, Maryland, USA
Ed. note: it is our sad duty to advise of the passing of Paul Yursis in August 2005.
Here is a brief obituary by Mike Caswell.
+++++
It is with great regret that I have to inform this site that Paul Yursis, also known on the Internet as Fibergeek, has passed away. This was a huge shock for all of us at Caswell Inc.
Paul was a genius. He developed the LCD Anodizing process for our company, which has been a phenomenal success for us. Our technical support problems faded away almost the day after we implemented the system.
Paul has allowed thousands of small prototype businesses and vehicle restorers to operate a simple, inexpensive and very safe system. He flew in the face of the 'establishment' and many a professional anodizer has taken note of his theories and techniques.
Paul had so many more things in the pipeline. His inventiveness was quite incredible. We are all going to be poorer for his passing.
It was an honor and a privilege to know you Paul Yursis. I wish there were more men like you on this planet.
Thanks for all you did for us Paul!
Mike Caswell
- Lyons, New York
Q, A, or Comment on THIS thread -or- Start a NEW Thread