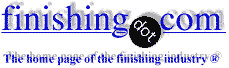
-----
Manganese phosphate coating: issues and answers

< Prev. page) (You're on the last page, older Q&A's)
(many of these are rare; the links will only sometimes work)
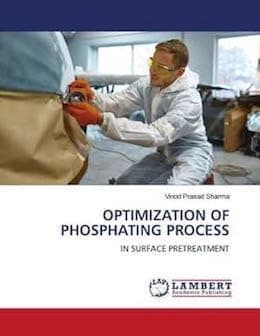
avail from AbeBooks, or Amazon
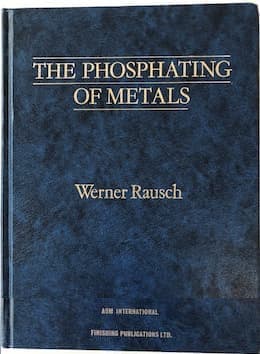
avail from eBay, AbeBooks, or Amazon
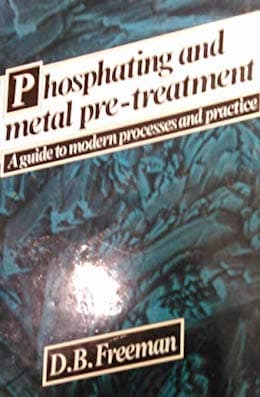
avail from eBay, AbeBooks, or Amazon
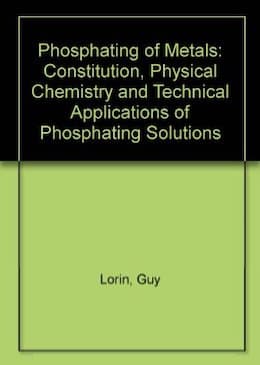
avail from AbeBooks, or Amazon
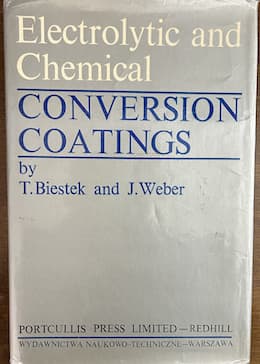
avail from AbeBooks, or Amazon
avail from AbeBooks, or Amazon
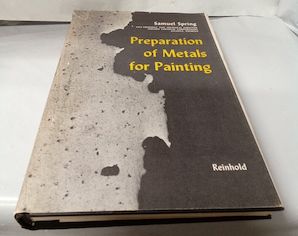
avail from eBay, AbeBooks, or Amazon
avail from AbeBooks, or Amazon
(as an Amazon Associate & eBay Partner, we earn from qualifying purchases)
Q. Reading this thread brought a bit more clarity for me regarding phosphating process. Thanks to everyone here.
My customer sent me some phosphated samples which had no oil coating, grayish tone and very smooth surface, kind of self lubricated finish.
I am told there's a lacquer available for such applications. Anyone have any experience in this?
Regards,
ASCO - Edmonton, Alberta, Canada
October 5, 2017
A. Hi Sukhjot. I think it is important to find out from your supplier what kind of phosphating process and sealer they applied if you don't know yet. I would not try to guess what a finish is from its appearance.
Although there are variations, phosphates are usually one of three general types:
1. Iron phosphates, which are thinnest, cheapest, least corrosion resistant and always painted.
2. Zinc phosphates, which are of middle weight, and usually painted, although occasionally oiled.
3. Manganese phosphates, which are heaviest, and designed to be oiled rather than lacquered or painted. Manganese phosphating is a well known "break in" finish for moving parts.
Unfortunately, 'lacquer' is slightly vague, it is often used to mean a water soluble final dip, or a clear 'paint' among other meanings.
Regards,
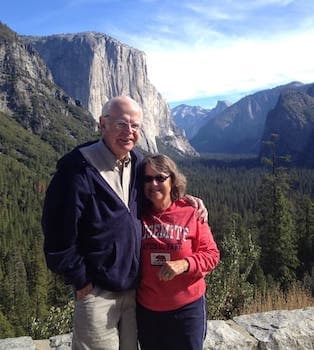
Ted Mooney, P.E. RET
Striving to live Aloha
finishing.com - Pine Beach, New Jersey
October 2017
October 31, 2017
Q. Dear professionals.
I need to know the actual reason and or need for the iron concentration test when testing the parameters of a manganese phosphate tank.
I have several vendors that all use different chemicals worldwide, some technical data sheets say nothing of iron concentration, however, the written coating specifications do have titration instructions for the analysis of the above.
Is it the variation of the different chemicals?
Is it an essential test?
What do the results tell us?
Thank you.
- Leeds. West Yorkshire. UK.
A. Hi Steve,
Manganese phosphate, in general, works with accelerant addition. This accelerant works by oxidizing all iron in solution, but iron dissolves from the parts you process, and this iron deposits with manganese in the phosphate crystals. Actual manganese phosphate coating has iron in its composition, but the actual solution has not.
If you mean the iron test strips for "iron concentration test", as I believe you do, I'll tell you: You don't want iron in solution because you want more manganese in your phosphate, you want to control the deposit and you don't want green if you are doing black phosphate. Manganese phosphate works without iron, and you test Fe(II) presence with the strips. You add accelerant in order to control iron, and control the reaction and grain size, and it works really well.
I don't know if I actually answered your doubt, so if I didn't, feel free to ask again maybe with an example.
Best regards!
TEL - N FERRARIS - Cañuelas, Buenos Aires, Argentina
November 1, 2017
Q. Hello Sir
We are doing Mn phosphating on AISI1208. After some components phosphate white and black spots observed on phosphate material. Due to this we do lots of quantity rework.
- Ahmedabad Gujrat
December 22, 2017
A. Hi Dhanjeet,
Please tell us how you clean your parts (alkaline degreasing? acid pickling? how many rinses?), parameters in phosphate coating (temperature, free and total acid) and sludge removal system you have so we can help you with some recommendation to improve your situation.
Best regards :)
TEL - N FERRARIS - Cañuelas, Buenos Aires, Argentina
December 26, 2017
Manganese phosphating coating failure on rub test what is the reason?
Q. We are doing manganese phosphate coating. Failure in quality during rub test sometimes; not forming the layer sometimes; failure with the black coat being removed. What are the reasons and how to maintain the quality? Please advise.
Rama Panfianoilfield services - Dubai UAE
April 7, 2018
A. Hi cousin Rama. Your phosphatizing is not being done properly if it is removed by the rub test or if it doesn't form. Rarely can anyone suggest one simple change to what you are doing when we don't know what you are doing yets.
But are you sure the parts are spotlessly clean before they get to the phosphatization tank? Are you carefully maintaining your free acid and total acid? Are you using a grain refiner as suggested on this page? Are you operating at 95 °C or at the proprietary vendor's recommended temperature? What spec. no. is the rub test, or what are its details? Thanks.
Regards,
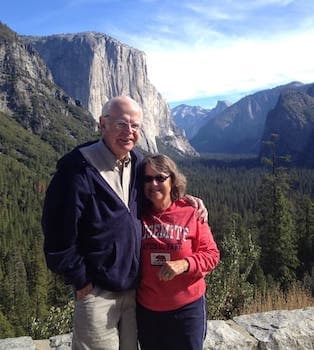
Ted Mooney, P.E. RET
Striving to live Aloha
finishing.com - Pine Beach, New Jersey
April 2018
Manganese Phosphate Coating Visual Issue
Q. I'm having an issue with the visual appearance of my product. One of the specifications from the customer is a uniform black coating, my company has two other sites around the world with identical lines to mine and are able to achieve this specification for the same product. The issue we are facing is black/grey dots. We control everything in the line, the concentrations of every tank, free/total acids, everything right down to the pH and conductivity of the rinse water. So my question is, what causes these visual defects and what would be the best option to fix them? Thanks
Samuel Hunt- North Vernon, Indiana, US
July 10, 2018
? Hello Samuel!
Can you describe the part you are coating (the material, if it is machined or forged, oiled or else…) and how you clean the parts? If you are controlling all your phosphate parameters, maybe the issue is where you are not looking…
If you can send some photos of the parts (after-before), maybe we can have an idea of what can be happening.
Best regards!
TEL - N FERRARIS - Cañuelas, Buenos Aires, Argentina
July 16, 2018
Q. Hello Daniel, thank you for responding; it is a pin end con-rod that is being coated, it is a machined surface with no oils. For the phosphate parameters, we monitor free/total acids, iron, and copper concentrations. Due to low surface area being run through the tank we do have an issue with iron concentration being low, we also use a pump to recirculate the fluid which introduces more air into the line, however this design works in two other locations without issue.
In the attached pictures you can see the black speckling and blotching on the part. We use an alkaline soak cleaner and an acid etch in our process line, both of which have are monitored for concentration and temperature. Thank you again.
Samuel Hunt- North Vernon, Indiana, US
July 17, 2018
----
Ed. note: Unfortunately the pics came through only as unreadable files from some application which we don't have and probably can't use on the WWW. Please re-send them in .gif, .jpg, .jpeg, .pdf, .png, or .tiff format. Thanks.
A. Hello Samuel, 'please send the images in another format because we are not seeing them...'
I'm really interested in what you call "blotching", because that would be entirely a pretreatment issue, but dots or "speckles" could be a phosphate issue because of sludge agitation, for example.
Best regards!
TEL - N FERRARIS - Cañuelas, Buenos Aires, Argentina
July 24, 2018
July 24, 2018
Q. Sorry about that, didn't realize they didn't go through. Part not run yet:
Parts with black speckling, gray dots, and streaks:
I'm not sure if it could be the sludge or not. We use a pump to agitate the process, but it's actually tilted to go towards the parts and don't face the sludge at all. It is possible to see to the bottom of the tank, even in full production. We have never seen or been able to detect any floating sludge either. Thanks
Samuel Hunt [returning]- North Vernon, Indiana, US
A. Hello Samuel, sorry but I had some issues to resolve and could not answer sooner.
I can assure that if you can see the bottom of the tank while you are in production, sludge is not the problem. Speckling, grey dots, and streaks are usually symptoms of poor cleaning (or too much sludge, but we have just ruled it out). I see it is a machined cast iron part, so I would seek:
1) What do the machining process to lubricate, or if it is a dry machining process. Is it the same design as the other locations?
2) Alkaline soak cleaner: Is it the same as the other two locations? See if it could be contaminated by silicones. We had some issue regarding foam production in this tank and silicone de-foamers used in wastewater, so the phosphated parts had marks on them. You can't see whether the alkaline cleaner has or not any silicone, but you could see if the addition of some product of the sort could end in this tank.
3) Grain refiner: Do you use any grain refiner between pickling and the phosphate tank?
Best of luck!
TEL - N FERRARIS - Cañuelas, Buenos Aires, Argentina
August 21, 2018
A. Two problems: (1) You cannot acid etch ahead of manganese phosphate. (2) You must use a titanium salt grain refiner.
Blast the part and use grain refiner.
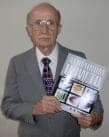
Robert H Probert
Robert H Probert Technical Services

Garner, North Carolina
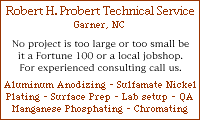
August 21, 2018
August 22, 2018
Q. Thank you both for the response,
To answer you Mr. Montañés:
1. All chemicals and designs of the lines are identical and purchased from the same manufacturers.
2. As stated above it is the same, I checked with process up stream and none of them use an silicone based chemicals. I don't see any other possible entry point for that either.
3. Yes after the acid there is a rinse and then it goes to the grain refiner,
To answer you Mr. Probert:
1. You can acid etch before, we've done it, and the coating is good. The main issue is it requires high temperature and causes rust on the rest of the part, even with RP.
2. Due to dimensional constraints, blasting is not an option, we've tried this as well already and seen the good results.
Again thank you for your feed back, I look forward to hearing from you.
- North Vernon, Indiana, US
A. Hi Samuel,
To me, this looks like leaching of fluids, post phosphating, from inherent porosity in the casting. Always looks more pronounced on machined surfaces.
If it is indeed porosity you could try alternate hot and cold rinses to try and remove residual acid in the pores; alternatively, prior to phosphating you could try vacuum impregnation, using sodium metasilicate
⇦ on
eBay
or
Amazon [affil links]
sealer, which could seal any porosity before you phosphate.
Aerospace - Yeovil, Somerset, UK
August 24, 2018
November 28, 2018
Q. Dear all,
I would like to thank you all for your enthusiastic contributions on every problem stated here in this thread.
May I submit this one:
We're Mn phosphating maraging forged steel in our company in order to get that specific deep black coating as we all know it.
Not so long ago we've noticed grey-white rather linear indications on the treated surface. We don't know where they come from. The flow of these parts upwards is made of roughly machining - heat treatment - polishing - Nittal etch - sandblasting (120/150 grit Aluminum oxide, 58 psi,12 inches) - water rinsing - degreasing - demineralized water rinsing (+ water break free) - Mn phosphating (Mn carbonate, phosphoric acid, Ti based grain refiner, acid ratio around 5) - heat treatment (de-embrittlement).
We have spotted these indications right after de-embrittlement, but also right after phosphating.
We've performed several analysis such as microhardness and SEM thinking that the problem was related to forged steel itself. Now, we're after contaminations in the process.
Can anyone help to orient our investigation? Any documentation on typical defects with phosphating maraging steel.
Best regards
- Zaventem, Belgium
A. Dear sir, to all,
Please don't use alloy sandblast media for cleaning the parts. Please use only sand which is from river or sea. Alloy media streaks or affects MS which is not good for MNP coating.
MNP chemicals react only on MS well. MNP is amalgamation of MS & Manganese.
If there's any other metal in between while process of MNP coating, we can't get good results.
Thanks.
- Pune Maharashtra India
January 31, 2019
A. In the firearm business, Aluminum Oxide is the preferred choice in blasting material. As is well known 90% of the problems with the bath occur in preparation so if cleaned correctly following the blasting you shouldn't have any problems with the Aluminum.
If you are really concerned, glass bead blasting is an excellent solution, although some results may vary depending on the shape of the material your'e blasting. With rounded objects the glass does not perform near as well as the Aluminum.
If your main problem is a lighter coating I sincerely doubt Aluminum is your problem. In MNP normally the coating is lighter with initial use and darkens over time.
If it is a fresh bath, that is your primary problem, it simply needs to be seeded first with Iron or even Titanium.
You are correct in your assumption as well. If the alloy itself has contaminants it can also lead to such a coating. If using Nitric Acid, you may want to check the content of that as well.
A. JUST A FYI -- Please Stop Using MnO2
While you will get a "coating" using MnO2. This compound is not a very good compound to use to get MNP. MnO2 does not readily dissolve in phosphoric acid. MnO2 is an old wives tale recipe as it is easily obtained from a D cell battery.
With MnO2 you are actually creating more of an Iron Phosphate coat then a Manganese coat which is more desirable.
A much better compound of Manganese to use is Manganese Carbonate which is just as cheap, readily available, and converts almost instantly and completely to Manganese Phosphate in an MNP bath.
Q. I am not quite sure which form of Titanium is best for the phosphate bath, activation or passivization.
I have plenty of titanium dioxide
⇦ on
eBay or
Amazon [affil links]
, but is this compound useful at all in anything regarding the Manganese Phosphating process?
Perhaps a conversion/ transformation into a Titanium Phosphate would be more useful, but what would be the best way to facilitate that? I have attempted with Phosphoric Acid, but as expected it did not seem to react, even boiling for hours.
Would a Sodium titanite be more useful? or a Titanium Salt (no chloride)
On a different note, would ZrSiO4 be useful in a post passivation process? If so else would possibly be required?
As I can create a Chromic Acid Rinse, should I stick with that?
From research the Chromic Acid on the Manganese Coating should be kept at a pH of 4-6. Is this true?
OuterGravity - Dallas, Texas, United States
September 9, 2019
Q. Hello,
We have installed a new manganese phosphating line in our plant with the intention of obsoleting an old line. In our new line we are using the same chemicals (cleaner, grain refiner, manganese) the same time and temperatures and are coating the same parts as in our old line. The problem is on some areas of some parts the coating appearance from the new line abruptly changes from black to gray in random patterns. SEM analysis shows the lighter colored areas have smaller and more rounded crystals. This color variation causes issues with our inspection camera systems at a subsequent operation.
The old and the new line are both functional, so it sets up a great opportunity for testing, and we have done a LOT of testing! From this testing I feel confident that I can rule out a lot of possible causes like; chemistry, cleanliness of parts, tank size and agitation, and part spacing. At this point I have no idea what else the issue could be. I have had many experts come in and review our situation with no luck. Even though I don't think chemistry is the 'problem', I have tested a few different chemicals in case that could be the 'solution' to the unknown problem.
Does anyone have any ideas what the cause could be? Is there any situation where some kind of electrical charge could influence the crystal growth?
Thank You.
shop employee - Saint Johns, Michigan, USA
A. Regarding the black and gray. Go back and study the agitation of the grain refiner to be sure the grain refiner is hitting all surfaces.
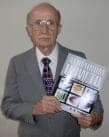
Robert H Probert
Robert H Probert Technical Services

Garner, North Carolina
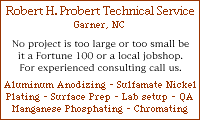
September 13, 2019
Q. Thank you Robert for the suggestion. We have a propeller mixer in the old line and the new line. I have tried varying the speed of the mixer and using intervals of ON/OFF within the cycle but did not notice a change to the coating.
It won't be too easy to do but I could perform a test where I add part oscillation to the Grain refiner step.
Generally speaking is it a good idea to have the parts oscillating in the grain refiner tank?
- Saint Johns, Michigan, USA
September 16, 2019
Double dipping in Manganese Phosphate
Q. I have a question: would there be any issues with double dipping a part in the Manganese phosphate solution that is too long for your tank.
Chuck Hawkins- Long Beach, California
September 12, 2019
Adhesion Loss in Manganese Phosphating
Q. Hello Everyone, we are having a Nihon Parkerizing Manganese Phosphate bath. We are suppose to phosphate AISI 4130 carbon steel material. We are experiencing loss of adhesion after phosphating. The phosphating layer comes off while rubber test and even when we rub by hand or cotton cloth. Please advise where we are missing the plot. Thank you in advance
subodh sawantShop Employee - India
September 19, 2019
March 17, 2020
Q. Hi,
I am working as Senior Process Engineer.
We are doing Mn Phosphating of Vibro-Finished steel parts and facing issue of black and white spots after phosphating.
Phosphating process:
Degreasing->Water Rinsing->Activation->Phosphating->Water Rinsing->Passivation->Dewatering->RP Oiling
Earlier we were preparing parts with shot blasting instead of Vibro Finishing and parts were okay by visual.
Please help.
Regards,
- Ahmedabad, Gujarat, India
A. Hi Keyur. Before you spend a lot of time trying to analyze the difference between the surfaces produced by vibro-finishing vs. sandblasting, I think you probably should make sure that you're definitely talking about a causal relationship rather than a coincidental one :-)
So please sandblast a few parts and run them through the line now, rather than relying on what happened before, and make sure that sandblasting makes the problem go away :-)
Only if it does is it worthwhile to undertake the bigger job of figuring out exactly what is wrong with your vibro-finishing process because it seems more likely to me that something went out of whack in your phosphating process in the interim than that vibro-finishing is incompatible with manganese phosphate for your parts.
Your posting is very similar to a posting from Abhishek Patel back in 2012, from Dhanjeet Singh who posted about black and white spots back in 2017. And I can see that you're with the same shop as Jeet Umre who described the fixturing of your parts back in 2016. If you're all from the same shop and this is one on-going problem since 2012, I can rearrange the stuff scattered across a half-dozen threads; surely a co-ordinated discussion will be more productive than a scattergun:
Good luck and Regards,
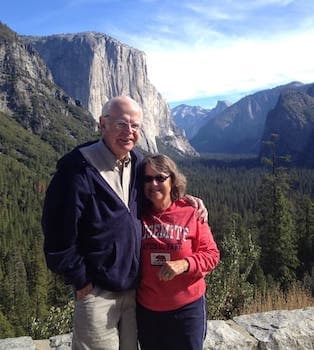
Ted Mooney, P.E. RET
Striving to live Aloha
finishing.com - Pine Beach, New Jersey
March 2020
Q. Thank you sir for your reply.
Yes, all names you mentioned are from same organization but some are not working with organization now ... [remainder of posting placed below the sidebar by editor]
Regards,
Harsha Engineers Limited - Ahmedabad, Gujarat, India
March 26, 2020
A. Hi again. Okay, before we continue then, I've moved all the related previous inquiries that I could easily find into the sidebar below so readers can see the whole picture:
Regards,
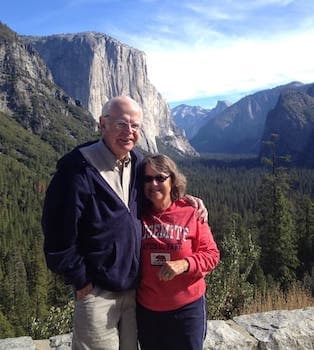
Ted Mooney, P.E. RET
Striving to live Aloha
finishing.com - Pine Beach, New Jersey
April 2020
![]() ![]() ![]() ![]() |
August 17, 2012
Q. Using S110 steel shots to do blasting on steel parts. Recently have been facing issues with regards to small pitting/denting on parts. - Ahmedabad, Gujarat, India November 19, 2013 Q. Hello, Ahmedabad, Gujarat, India November 19, 2013 A. Hi Abhishek, Aerospace - Yeovil, Somerset, UK November 21, 2013 Q. Hi Brian - Ahmedabad, Gujarat, India November 29, 2013 A. Hi Abhishek, Aerospace - Yeovil, Somerset, UK January 22, 2015 Q. We have done Zinc Phosphating process but we are facing visual difference in color. Parts are looking like they are processed through Mn phosphating means black. - Ahmedabad,Gujarat, India February 24, 2016 Q. Hi guys, - Ahmedabad, India December 22, 2017 Q. Hello Sir - Ahmedabad Gujrat December 26, 2017 A. Hi Dhanjeet, TEL - N FERRARIS - Cañuelas, Buenos Aires, Argentina |
Q. .... For Now we have already completed with shot blasting as you have said.
But now we want to eliminate shot blasting process and replace it with vibro finishing process.
So prior to phosphating we will have Vibro finishing plus dryer process and afterwards directly to Mn Phosphating.
With same process we are facing issue of black spot on our parts which is not 100% some parts are also found visually ok. Almost 50% is rejection.
Please give your guidance to proceed further.
Regards,
Harsha Engineers Limited - Ahmedabad, Gujarat, India
March 26, 2020
April 27, 2020
Q. Thank You for the reply.
Yes as per your suggestion we have completed with shot blasting but now onward we want to replace shot blasting with Vibro finishing to improve surface roughness which is customer requirement.
We are achieving surface roughness within spec with vibro finishing but we are facing below issue with same:
1. Black spots on some of the parts
2. Higher coating weight of 15 - 25 gram/m2
Please guide for the same.
Thanks in advance
Regards,
Keyur Solani
Harsha Engineers Ltd - Ahmedabad, Gujarat, India
April 2020
A. Hi Keyur. If you have run sufficient shot blasted parts this week to be confident that they all come out well, and your phosphatizing line is currently in fine tune, you can move on to examine the relationship between vibratory finishing and the decline in quality of phosphating.
Jeet Umre reported difficulty in processing the parts because they "nest" due to their cup-like shape. Do you have good reason to be confident that they are not nesting in your vibratory finisher, so all surfaces are being properly finished?
Although bead blasting is good prep for phosphating, it is not necessary for proper phosphating; in fact, probably only a small percentage of phosphated parts are blasted. But in addition to increasing the surface area, it serves to both clean and activate. When you skip it, a question becomes whether your cleaning and pickling is adequate without it.
I am personally not familiar with vibratory finishing before phosphating. My question then is why are you doing it? My impression is that vibratory finishing before phosphating would be for the purpose of deburring, not for cleaning or activating. What happens if you manually deburr a few parts as needed, then just clean, pickle and phosphate without any vibratory finishing? A good next step is to try to determine whether vibratory finishing is merely not helping or is actually interfering with the phosphating.
Satisfactory phosphating is complex, and everything is interrelated; sorry that it's not proving easy :-(
Regards,
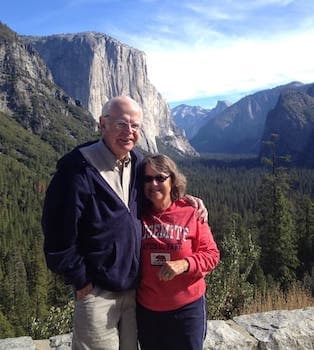
Ted Mooney, P.E. RET
Striving to live Aloha
finishing.com - Pine Beach, New Jersey
April 28, 2020
Q. Good Morning Sir,
Why are we doing Vibro Finishing?
Answer is our customer is having requirement of surface roughness of 0.5 Ra, to achieve same we shifted to vibro finishing instead of shot blasting where we were not able to achieve surface roughness as per customer requirement.
Addition to that, deburring and cleaning is other objective.
But as earlier said we are facing issue of:
1. Black spots on some of the parts
2. Higher coating weight of 15 - 25 gram/m2 with vibro finishing prior to phosphating.
Harsha Engineers Limited - Ahmedabad, Gujarat, India
Q. Hi, I am a hobbyist who makes items mainly from mild steel and have been experimenting with home brew manganese phosphate solutions.
Manganese dioxide appears to be completely insoluble in phosphoric acid at any concentration even at temperatures approaching boiling point. I have tried parkerising with solutions made up with manganese dioxide, iron wool, and phos. acid with reasonable results, have also tried phosphoric acid and iron wool alone and have still achieved what appears to be similar finish. I am wondering what role if any the manganese dioxide plays in the chemistry of these home brew formulations? I suspect that commercial metal finishers achieve superior finishes by using actual manganese phosphate dissolved in a phosphoric acid solution. This seems to be an unobtainable chemical, I hope that someone can advise me. Thanks.
Tim Davy- Hastings East Sussex England
October 4, 2020
A. Hi Tim. Brandon B said stop trying to use manganese dioxide because manganese carbonate is just as cheap & available, and dissolves readily. Two others readers on this thread recommended it as well. Good luck.
Luck & Regards,
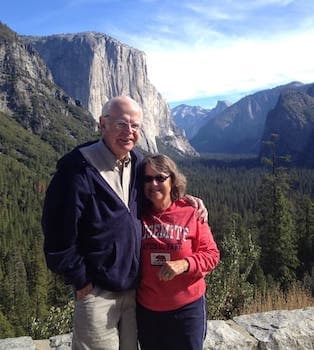
Ted Mooney, P.E. RET
Striving to live Aloha
finishing.com - Pine Beach, New Jersey
December 4, 2020
A. If you think that in a few hours of experimentation you can achieve what professional trained chemists have developed with tens of thousands of hours of research, you are probably overconfident. You can search scholar.google.com for guidance. Or - even better - you can search patents on patents.google.com. Earlier patents of manganese phosphating might very well be useful; the technology hasn't changed much. US patents are required by law to disclose the 'best mode' of practicing the invention; they can bury it in a plethora of other examples but it is a requirement. And you are free to practice any expired patents - that is the objective of the United States patent system. That being said, you would be better off buying a commercial product that incorporates many years of research by others who are expert in the field.
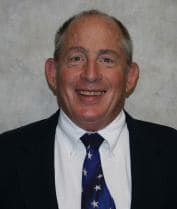
Tom Rochester
CTO - Jackson, Michigan, USA
Plating Systems & Technologies, Inc.

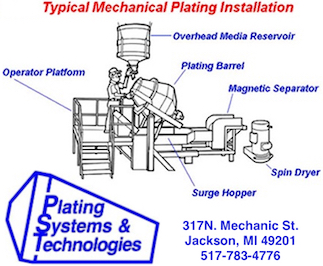
December 2020
Q. Hello Finishing community,
Is there a safe way to remove spot rusting from Manganese Phosphate without removing or hurting the Manganese Phosphate?
Thanks
Anthony
- Carterville, Illinois
December 5, 2020
A. Hi Anthony. I'd wipe it with 50/50 vinegar ⇦in bulk on eBay or Amazon [affil links] and water a few times; if that doesn't do it, straight vinegar. I don't think it will hurt the manganese phosphate but it can attack the underlying steel, especially at the spots, so rinse it well probably neutralizing the rinse water with baking soda [in bulk on eBay or Amazon [affil links] . Good luck.
Luck & Regards,
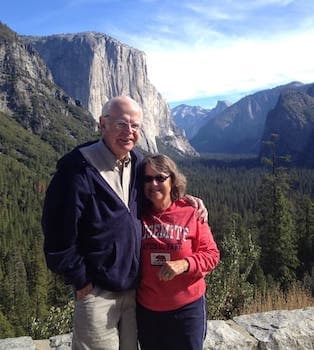
Ted Mooney, P.E. RET
Striving to live Aloha
finishing.com - Pine Beach, New Jersey
December 2020
Q. Hello,
I am a mechanical engineer and work on a lot of defense contracts. I have come to an issue with a vendor and I have hard a hard time finding out the importance of the process requirement in a mil spec that states that a single contractor must perform all phases of cleaning and coating process.
Common sense tells me this is smart. Reduce the ability to introduce foreign matter etc. But scientifically there must be a solid reason for this requirement.
What are the risks taken when the abrasive blasting is outsourced?
- Worcester, Massachusetts
May 28, 2021
A. Hi Dawn
I'm not sure what Mil spec you refer to, but any finishing or coating is applied on surface free from oil, grease, scale, rust, oxides, and other contamination. Usually the cleanliness of metal surface is achieved by some combination of steps: solvent cleaning, vapor degreasing, alkaline cleaning, mechanical cleaning (blasting), electro-cleaning, acid etch.
All these cleaning steps are performed immediately prior to the coating. If you perform these preparatory steps in different locations/times (different vendors), the surface will be contaminated and re-oxidized due to handling, shipping, exposure to environmental elements, etc.
(In theory, I can imagine some part preparation and cleaning in one location and after that transfer it with all possible caution in an inert atmosphere to another location for the processing, but practically...)
Good luck,
- Winnipeg, Canada
June 7, 2021
Acronyms:
MIM = Metal Injection Moulding
MnP = manganese phosphating
Q. Hi,
we make MIM parts in our plant and also do MnP for Medium Carbon low alloy steels (4605 & 4340) grades. recently we have got the issue of surface finish after the MnP process. Initially, we use to get a black color finish after MnP but now the surface looks brownish and our customers are not showing interest to accept the parts because of the finish & Brownish appearance.
Please let me know whether there will be an issue in bath concentrations or due to improper surface preparation (we do grit blasting as surface preparation).
Advice accepted.
thanks
Chanikya
R&D Specialist - Bangalore, India
December 10, 2021
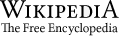
Soft nitriding
"Gaseous ferritic nitrocarburizing is also known as controlled nitrocarburizing, soft nitriding, and vacuum nitrocarburizing".
Q. I have a problem with gas soft nitrided parts. After coating Mn phosphate found defect: non-phos all surface some pcs.(50%/Lot) Could you advise the cause of this problem to me? We found this defect the first time after 5 years of production.
Dittakorn KamchanStudent - BKK, Thailand
February 18, 2022
A. A brittle ceramic-like layer (so called white layer) emerges as a result of nitriding process on steels. White layer does not contain free iron which you need to perform manganese phosphating. You need to remove white layer to be able to carry out manganese phosphate process to reach desired surface quality.
You can use electrolytic chromic acid etch or sandblasting with Al203 to remove white layer from the surface.
- Turkey
October 13, 2023
Q. My manganese phosphate bath has gone from dark grey almost black to a light grey and I have changed nothing with my process . . . still test the bath every morning before putting parts into it. Wondering what could cause this?
walker johnsonfinishing super - South Carolina
March 29, 2022
A. Hi Walker,
I suppose you test every parameter you need to know every morning as you say, but I would check total acid vs free acid ratio (TA/FA) because this would make more or less manganese to precipitate in your crystals. More manganese, more black colour. Less manganese, more gray color (could be a greenish tone on it, some iron on your solution).
If nothing works, then I would check if your bath could be contaminated with another metal. Co-precipitation of other metal phosphates would change the colour of it.
As we don't know what you phosphate and how you prepare your parts, I can't make anything more specific for your issue. Hope it helps! If you already know what did happen to your bath and solved it, please answer for we readers to know and learn :)
Best wishes,
Daniel
Process Engineering Manager - Cañuelas, Buenos Aires, Argentina
A. Daniel is 100% absolutely correct, but from experience I am going to elaborate. Start heating the solution, as you pass about 185 °F, then, at the tank (right now, not yesterday), titrate for total free and adjust, then keep the tank loaded as full as you can. A tank titrated yesterday and left hot and empty will run up the free acid and destroy the solution.
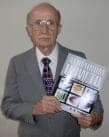
Robert H Probert
Robert H Probert Technical Services

Garner, North Carolina
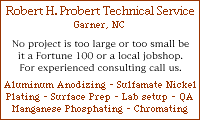
Q. So, on the contamination from other metals point I noticed that our cold water pipe cold and the one to the hot water heater were rusted. So I filled up a tank and let the water sit over night, and the next day the water had a reddish tint to it. I assumed that was causing some of the problem but my company has not yet got around to changing the pipes out so I have no test to run just yet.
I will get the metal data sheets and message back the types of material we phosphate just so the info is provided. Would love to be able to email someone on this subject if they had the time and were willing. Appreciate the reply, thank you.
- Aynor, South Carolina
July 26, 2022
----
Ed. note: Hi John, we have all the room in the world for anything you want people to see, but this site is not for private communications for several reasons ... including the fact that dozens of readers have similar problems to what you are experiencing and we don't want to string them along then cut them out from the resolution through you getting the answer in private. E-mail whatever you wish to mooney@finishing.com with subject 'thread 34052' for posting here. Thanks.
Q. Hello, I am doing a manganese phosphating and over the past month I have had the issue of keeping our FA within the 2.0-3.1 ratio that we use at my facility. My FA tends to float around the 1.2-1.7 range. My TA range floats around the 14-18 (which is what I need to do for my facility) and my temperature is around 200 °F. I am not sure how to improve my numbers. Something that is worth noting is we run for roughly 24 hours a day. We occasionally have downtime, but it is not super common.
Michael Hannes- Waterloo, Iowa
November 7, 2022
Q. We are establishing process for Manganese Phosphating line for coating on 4140H grade steel parts using Henkel Chemicals. We are not able to achieve even/uniform coating despite attempting different combinations of TA/FA Ratio between 5.5 to 9 (TA between 10.5 to 12.8 ) and FA between 1.2 to 2.4 ) and activation time from 15 secs up to 120 secs. Temperatures of the baths are maintained at 70-75 °C for Activation and 92-95 °C for Phosphating. Cleaning qualifies water break test.
Agam Thind
- Chandigarh, India
November 24, 2022
Q. Good Day,
We have a vendor that processed some material with Manganese Phosphate per MIL-DTL-16232 [from
DLA]
, Ty M, Cl 2. The finished part has areas that are black and areas that are gray, almost like they were masked off.
A second part has a mixture of black with gray streaking; and 7 parts have no adhesion on the ends, base metal is visible.
I just need some ideas on what the issue(s) could be.
Thank you
Employee - Milwaukee, Wisconsin
February 6, 2023
1. Ask him if he uses a grain refiner and how he controls it.
2. Ask him if he adjusts the total/free ratio immediately before putting the parts into the tank.
3. Ask him how he controls the powdery sludge from settling onto the parts.
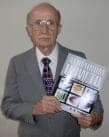
Robert H Probert
Robert H Probert Technical Services

Garner, North Carolina
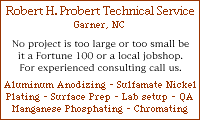
February 7, 2023
Q, A, or Comment on THIS thread -or- Start a NEW Thread