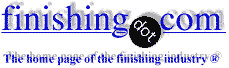
-----
Black spots in zinc plating

Q.
We are facing black spot or pill up issue for our steel components. Zinc layer is 5 to 15 micron blue passivation. After plating, wrapped with vci paper. When assembled after one/two month later, black spots or plating pill issue occurred.
We are using c-15 grade steel material, and customer requires zinc plating and yellow passivation. What is the problem? Can you help please.
k pravineng. - maharastra, India
November 6, 2022
A. Hi Pravin. I don't know the phrase "pill up issue", but I think you are saying that the plating peels? It could be that the parts were simply not clean enough, or it could be that the plating is so highly stressed that it peels off over time.
I would suggest that you observe the plating line in operation and see if you can detect any sign of water-break before plating, and that you also scrub a few parts with a scrub brush ⇦ on eBay or Amazon [affil link] and a water solution of powdered pumice ⇦ on eBay or Amazon [affil link] before putting them into the cleaning & plating sequence to see if these things indicate that cleaning may be the problem.
And I would suggest that you plate some Hull Cell ⇦ huh? panels or other test parts, and bend them to look for excessive stress in the plating. There is also a test device called "stress-tabs" which look like hull cell panels coated with maskant on one side and serrated like a comb where the serrated areas curl up to indicate tensile or compressive stress at different current densities.
Unfortunately you haven't yet told us much about your process and there are almost countless possible causes for black spots.
Luck & Regards,
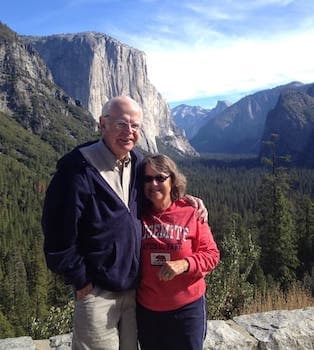
Ted Mooney, P.E. RET
Striving to live Aloha
(Ted can offer longterm or instant help)
finishing.com - Pine Beach, New Jersey
Q. Hi, experts.
I would like to ask about problem with my customer. Our customer uses ammonium zinc barrel and then finishes with blue chromating. But the result in some parts of materials is like black spot. Please give us some reasons that can make the material become black or like stained at that material's parts.
chemical analyst - Jakarta, Indonesia
August 12, 2023
A. Hi Ansan
Giving "some reasons for black spots" in acid zinc barrel plating is what the 50+ postings on this thread have been about for 20+ years. Readers would like to help you with your specific problem, but we would need data that distinguishes your problem from those other problems in order to move forward.
Yet we don't even have photos of those "like black spots" and "like stained in parts"; we don't know if this is a new startup which has never plated successfully, or a place where things went south when they switched to your chemistry, or a shop which has been using your chemistry successfully for years and suddenly encountered this problem; we don't know if it's a few dozen parts per month or every part in every barrel.
Probably the only thing we can offer without data is that if the black spots are in a pattern which looks like the pattern of the barrel holes, then it is 'barrel printout', probably caused by excessive iron in the bath.
But if you can give us some photos & data we'd be willing to try. Thanks.
Luck & Regards,
Ted Mooney, P.E. RET
Striving to live Aloha
(Ted can offer longterm or instant help)
finishing.com - Pine Beach, New Jersey
Q. Hi, Mr Mooney
Thank you for information and advice. I got a revision from my customer to use yellow/rainbow trivalent for their iron material product. As, I told in this forum that they use ammonium zinc barrel, and about they get the case about black spot after about 2 month in their customer's warehouse.
I show you the pictures about this case. Our chemical has been used a few years. They just want to make sure about that case and what the problem is so it can be prevented. Thank you and all experts.
Regards,
Chemical Analyst - Jakarta, Indonesia
August 18, 2023
A. Hi Ansan,
The first picture and the detailed view of it may well be a "black spot" ... but the 3rd and 4th pictures don't show "spots" they show very severe rusting with no plating at all in those rusted areas.
Unfortunately, figuring out whether the plating peeled off before the rusting occurred or whether the plating was there but got consumed on the way to rusting may not be easy to determine.
Still the answer is that this plating was highly unsatisfactory and it must be determined why. Some guesses to be further investigated include poor rinsing after plating or chromating, being packaged damp rather than dry, corrosive packaging materials, or inadequate cleaning & pickling.
Luck & Regards,
Ted Mooney, P.E. RET
Striving to live Aloha
(Ted can offer longterm or instant help)
finishing.com - Pine Beach, New Jersey
⇩ Related postings, oldest first ⇩
Q. We manufacture sheet metal parts using CR & HR steel sheets; in our workshop and then send them for Zinc-coating to an Electroplating supplier.
Recently we have noticed that some of the parts that had been zinc coated in May 2000 started developing black shady areas on the surface of the parts.These spots were first noticed on the parts kept in the stores and then there were a couple of complaints from the customers.
I would be very grateful if somebody could give me answers to the following:
1) What is the reason/cause for these black spots?
2) Can these spots be eliminated by us without damaging the zinc coating?
3) Will the entire lot of parts kept in the stores eventually suffer the same problem?
4) What can our supplier do to avoid this problem in future?
- Karachi,Pakistan
2000
A. Paul,
Problems such as you describe can come from within or from the outside. From within, is usually coming from porosity, and shows itself through the plated deposit. You did not say if parts had a chromate passivate or not. "Spotting In," results from storing the finished plated parts in an area where the air is laden with corrosive particles. This may happen right in the plating shop, in transit, or while in your storage facility. A good test would be to take one or more parts and segregate them. Seal them off and put them into another location. If they develop the same spots, look into a "Spotting Out," condition. Meaning: Reactive trace chemicals may be seeping through the pores to the surface and showing themselves as black spots.
Lastly, check out the plating bath. Examine bath to see if there is any kind of contamination present, either organic or inorganic. Under the correct condition, iron may show itself as black spots on a Zinc deposit from certain types of plating baths. Try to duplicate your results in a laboratory setting in a plating cell or Hull Cell.
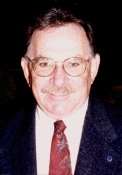

Ed Budman [deceased]
- Pennsylvania
With deep sadness we advise that our good friend Ed passed away Nov. 24, 2018
A. Your black spots tell me that perhaps the monsoon has set in Karachi already. The increased Humidity in the Air aggravates this problem which is not noticeable when humidity is less than 50 %.
I can bet that your parts are blue passivated and the best thing would be to switch to yellow chromate which protects the parts from humidity better . You will also notice that the CR sheet parts will have a better fate than the HR sheet parts which are more porous and if this is correct then try only to use CR grade material. Also run a plating thickness check on the spotted out parts as well as make your plater change his post plating rinses and post passivation rinses more frequently. Regards,
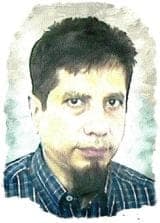
Khozem Vahaanwala
Saify Ind

Bengaluru, Karnataka, India
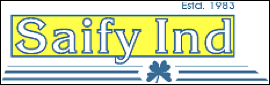
Q. Black spots appears on our barrel acid zinc plated parts, can anyone help us on this matter?
Process:
- 1.muriatic acid pickling
- 2.rinse
- 3.rinse
- 4.electrocleaning (5 mins)
- 5.rinse
- 6.barrel acid zinc plating (20 mins)
- 7.rinse
- 8.centrifugal dryer
Thank you for your time
andrew kaw- manila, philippines
2000
A. This sounds like it might be a classic case of iron contamination. See
"Improving Your Chloride Zinc Plating Operation" or send pics.
Regards,
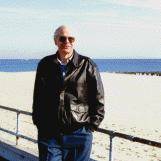
Ted Mooney, P.E.
Striving to live Aloha
(Ted can offer longterm or instant help)
finishing.com - Pine Beach, New Jersey
A. Dear Andrew,
Firstly (a) do read the article Mr Mooney has suggested. Meanwhile if after you treat the bath for iron and the problem still persists then
(b) try reducing the Voltage. If efficiency drops, then increase anode area.
If the reduced voltage has helped without any problems, then
(c) sigh with relief. If not then
(d) check the barrel rpm which may be too low. Increase the barrel rpm between 14 to 16 rpm whatever suits the hole size and current with giving your parts black spots.
If all the above efforts fail, then do the opposite of everything above and charge more for the black spots without giving them away for free!
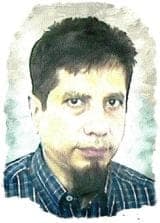
Khozem Vahaanwala
Saify Ind

Bengaluru, Karnataka, India
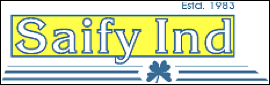
Multiple threads merged: please forgive chronology errors and repetition 🙂
Q. Zinc plated components 8-12 microns getting black spots after 15 days, shall you can please advise how to avoid this problem. Plating getting corroded while traveling in the sea for about an month.
RAJU- Chennai, Tamilnadu, India
2003
A. If you're running a Chloride Type Zn bath the black spots may be coming from a hi concentration of copper in your bath, compounded with hi organics in either Zn or Chromate rinses and as the chromate hardens or cures chromate is not adhering
Chris Snyderplater - Charlotte, North Carolina
Multiple threads merged: please forgive chronology errors and repetition 🙂
Q. I WANT TO UNDERSTAND THE REASONS FOR THE GREY / BLACK SPOTS IN THE ZINC PLATING.
SANJAY NARULAFASTENERS - Rohtak, Haryana, INDIA
2004
A. Sanjay,
You don't include enough information, but sounds like corrosion. Are you chromating? If you let the part(s) sit long enough I'm guessing the dark spot will turn to "white rust".
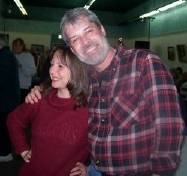
Trent Kaufman
electroplater - Galva, Illinois
A. Dear Sanjay,
Black spots in barrel acid chloride zinc plating is a common problem there are many reasons for that some of the important reasons are Iron contamination, low metal content, higher content of brightener "R" if you are using Indian Chemistry. If there is no iron contamination in the bath, check & adjust metal content above 30 gms/litre.
N K Praveen Kumar- Secunderabad, ANDHRA PRADESH, INDIA
Q. Dear Praveen,
I would like to know more about Iron Contamination in details.
Kindly respond to the same.
Sanjay Kumar- Bangalore, Karnataka, India
2004
A. Sanjay
These are possible causes of Black spots in Barrel Zinc plating from acid Zinc electrolyte:
1) Dissolved iron from dropped parts in solution.
2) lack of carrier or Wetter sold as "M" in India.
3) Lack of Chloride or low Chloride./ maintain 125 to 140 Gms/liter.
4) lack of Zinc as metal . maintain 25 to 28 Gms/lit.
5) Excess brightener too sometimes causes Blackish deposits.
6) Recast Impure Zinc anodes containing lead or Copper cause black deposits.
7) using Local impure "A" salt.
8) using Local impure "B" salt.
9) Proper pretreatment is essential.Clean parts plate good.
10) Continuous filtration is essential. Dirty Solutions don't plate well.
11) Passing higher volts than the solution can carry.
Like we said above this is a short list of POSSIBLE causes.
Good luck with your plating .
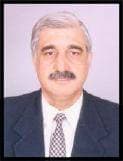
Asif Nurie [deceased] [deceased]
- New Delhi, India
With deep sadness we acknowledge the passing of Asif on Jan 24, 2016
A. Dear Sanjay ,
Following are the some of the reasons for Iron contamination in Acid Zinc Plating (barrel):
1. Parts falling into the tank during loading, unloading or during the course of plating.
2. As the current density in barrel plating will be very low, parts to be plated are exposed to acidic solution and hence Iron gets dissolved into the solution.
Apart from the above poor quality of anodes and chemicals also result in iron contamination.
Removal : Depending on the extent of contamination you should treat the solution with Hydrogen peroxide 100 vol, @1-2 ml/liter. Then filter the solution after settling the solution overnight, and discard the sludge.
Note brightener "M" should be added after the above treatment @ 2-3 ml/litre.
N.K.Praveen Kumar- Secunderadad, India
Multiple threads merged: please forgive chronology errors and repetition 🙂
Hello, I have a problem about electroplating: I have plated the axle wheel at my supplier but there are black spots on the surface of product especially on the shank area.
I have checked electroplating parameter and there is no problem with them but I am suspicious with rinsing water condition.
Test result shows : degreasing water rinse => TDS:521~617 ppm, pickling water rinse=>548~4710 ppm, electroplating water rinse 540~2270 ppm & chromating water rinse 513~516 ppm.
Based on the water rinse data, do you think our rinsing quality is proper enough? is there standard quality for water rinse of electroplating.
Regards Yudi W.
Engineer - Jakarta Utara, Jakarta, Indonesia
April 27, 2009
Hi, Yudi. De-ionized water is suggested for all plating baths, and for rinse water if affordable. A very general guideline is that a rinse tank before a process should dilute the contents of the previous process tank by a factor 500-1000:1
But you have not yet told us anything about the parameters of your plating process to enable anyone to advance the alternate theory that it is a plating problem. Low quality rinse water can certainly cause many problems, but "black spots" doesn't sound like a likely one to me unless iron from the pickle bath is being carried into the plating bath. I suspect the black spots are iron contamination of the zinc plating bath. Please tell us about your plating process.
Regards,
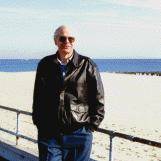
Ted Mooney, P.E.
Striving to live Aloha
(Ted can offer longterm or instant help)
finishing.com - Pine Beach, New Jersey
Q. We are one of the brake manufacturers in India and we are facing a problem of Black spots after Zinc Plating of SG castings. Please give me solution.... and also it will make any issue if I am using Aquagaurd-605 as a sealant (For protection)? I am expecting your valuable suggestions......
Jithin VCustomer of plated part - Tamilnadu, India
November 26, 2009
White patches after Barrel Acid Zinc Plating, Clear Trivalent passivation
Q. We are doing plating on steel balls after polishing them in vibrator. We are plating them in barrels for about 15 mins. It is acid zinc solution. Trivalent Clear passivation is used after plating. White patches are observed after the parts are placed for drying on table (we also do the drying process by rotating the parts in dryer for about 5 mins). Are these patches due to incomplete drying of parts or due to some other reason? Kindly help.
Raja Rupinder SinghMachinist - Ludhiana, Punjab, India
February 6, 2011
A. Hi, Raja
We need to do a hundred things right to get satisfactory plating, and just one thing wrong to get unsatisfactory plating, as Praveen and Asif and others have noted :-(
So it is often not possible to discern which of those hundred things is wrong based on a description of the unsatisfactory plating. My guess is that there is a problem with the brightener in the zinc plating bath, but it's only a guess ... but that is not to discredit the need for total dryness. Good luck.
Regards,
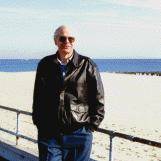
Ted Mooney, P.E.
Striving to live Aloha
(Ted can offer longterm or instant help)
finishing.com - Pine Beach, New Jersey
Dear Mr Raja,
You need to improve the plating thickness -- 15 minutes is too low since the steel balls have too much of surface area and my guess is that in a conventional plating system you will need an hour at least to achieve about 5 to 10 microns which should be a minimum.
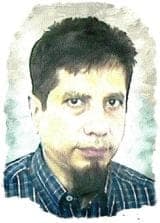
Khozem Vahaanwala
Saify Ind

Bengaluru, Karnataka, India
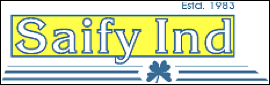
Thanks for getting right to the heart of the matter, Mr. Vahaanwala, which I completely missed: you can't really do proper barrel zinc plating in 15 minutes, it takes somewhat longer :-)
Luck & Regards,
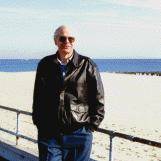
Ted Mooney, P.E.
Striving to live Aloha
(Ted can offer longterm or instant help)
finishing.com - Pine Beach, New Jersey
Multiple threads merged: please forgive chronology errors and repetition 🙂
Q. We found most of the plated parts received have black spot and yellowish color on the plating surface (as photos show) and this we are unable to solve or remove by our plating house process.
We wish to get an opinion if this all black spot will cause oxidation or rust after a period of time, and what caused this black to appear.
Product Quality Engineer - Butterworth, Penang, Malaysia
September 21, 2011
? What are you plating and what are you plating with? More detail of what you are doing will certainly help get a response
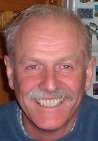
Trevor Crichton
R&D practical scientist
Chesham, Bucks, UK
A. Hi. It looks to me like zinc plating with clear chromate.
The discoloration may be lack of plating (and thus lack of chromating), and it is at an inside corner where we would expect it. But also possible is water damage (lack of drying), which again would be most likely at an inside corner. This is not acceptable aesthetically and will probably rust quickly. Either way it is unsatisfactory, although different steps are needed to correct it.
The smaller dots could be improper cleaning or acid dipping, which will be a big problem, or they could be fretting, which would be a smaller problem. Are the parts rack plated or barrel plated, and (as Trevor asks) what kind of plating is it? Thanks.
Regards,
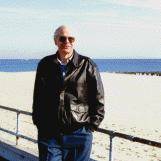
Ted Mooney, P.E.
Striving to live Aloha
(Ted can offer longterm or instant help)
finishing.com - Pine Beach, New Jersey
Q. Hi Mr. Trevor Crichton and Mr. Ted Mooney,
Thanks for your response.
The part is "U" frame, and material is CRS A.I.S.I. 1008. and the plating is clear blue trivalent Zinc.
We are using both methods (barrel and rack).
Thanks,
- Butterworth, Penang, Malaysia
A. Hi, Mr. Yuu.
The black marks could be scuffing/fretting if the parts are barrel plated, and this might not be a serious problem. But if the parts are rack plated, it is hard to envision what could cause the black dots except for serious problems.
Regards,
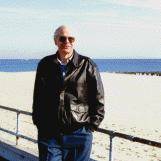
Ted Mooney, P.E.
Striving to live Aloha
(Ted can offer longterm or instant help)
finishing.com - Pine Beach, New Jersey
A. Check plating thickness near the spots. If the thickness is poor you either have a thew problem or cleaning problem. If your have this problem with both barrel and rack I'd lean toward cleaning. Try hand cleaning some parts wipe them really good. Then rack them up and see if you still get the spots. If this fixes the spot you then know it's a cleaning problem.
Jason Deible- Grand Rapids s, Michigan, USA
A. I think it is because of rust which was not been removed during pretreatment or it grew up underneath plating layer.
Faizul Azli- Negeri Sembilan, Malaysia
Multiple threads merged: please forgive chronology errors and repetition 🙂
Q. We are doing Zinc plating with trivalent yellow chrome passivation on Zamak 3/5 (Zinc alloy) casting.
In some cases black spots appear on plated casting.
What are these black spots? Why these black spots appear with time? Why not this problem is 100%?
- Noida, India
May 10, 2012
A. Hi Vikram.
We appended your posting to a thread about black spots in zinc plating which may help you. We have many other threads about the subject, which you can find if you search the site. But people will probably have trouble offering assistance tailored to your situation until we know more details: whether your parts are cyanide zinc plated? Spotting out of cyanide is common. Are your parts barrel plated? Black spots from iron contamination of acid zinc solutions are common. Please tell us whether you are doing barrel vs. rack plating, cyanide vs. alkaline vs. acid zinc plating, whether there are any pretreatments before the zinc plating, whether the castings are vacuum impregnated, whether the processes you use are from reputed suppliers or are home-brew, etc. And please send pictures because different people visualize very different problems when they hear 'black spots'. Thanks!
Regards,
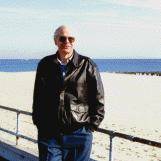
Ted Mooney, P.E.
Striving to live Aloha
(Ted can offer longterm or instant help)
finishing.com - Pine Beach, New Jersey
Q. We are doing barrel plating and the parts are alkaline zinc plated. The Zamak castings are not vacuum impregnated.
We are doing pretreatment before plating.The pretreatment includes Soak cleaning, cathodic cleaning, water rinsing, Acid pickling and water rinsing.
If you require I can send you the control plan of the complete process.
Regards
Vikram
- Noida, India
A. Hi, Vikram. Thread 30399 is about such problems in alkaline zinc plating, and Asif Nurie offers some good possibilities. First guess is that the current density is too high, causing burning in the areas exposed to the barrel holes. Do you have any evidence of such a pattern, such as hull cell panels showing burning in HCD area?
Regards,
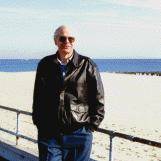
Ted Mooney, P.E.
Striving to live Aloha
(Ted can offer longterm or instant help)
finishing.com - Pine Beach, New Jersey
Q. Hi experts,
I'm running acid zinc barrel plating and currently facing the barrel holes mark on my plated parts.
I suspect this problem is caused by the barrel rotation speed! Is it true?
Lovely thanks for help.
- Penang, Malaysia
July 7, 2013
A. Hi Sng. We appended your question to a similar thread. This looks like a classic case of iron contamination in your acid zinc plating tank, not a problem caused by the rotation speed. Good luck.
Regards,
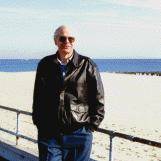
Ted Mooney, P.E.
Striving to live Aloha
(Ted can offer longterm or instant help)
finishing.com - Pine Beach, New Jersey
A. Black marks in barrel plating of acidic zinc are a results of too high divalent iron in the solution.
You have to oxidise the iron (by hydrogen peroxide or air) and filter the sludge.
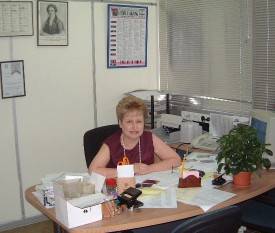

Sara Michaeli
Tel-Aviv-Yafo, Israel
Q. Are Black spots caused by any spillage of chemicals.? What chemical spillage will cause Black spots except Pickling Chemical.
MOHANAVELAVAN ElangovanAUTOMOBILE INDUSTRY - CHENNAI, INDIA
August 19, 2013
A. Hi cousin MOHANAVELAVAN. Please invest a couple of paragraphs in your question. Unfortunately your question is so brief that I have no idea what you are talking about :-)
Are you saying that you have zinc plated some parts, and they were perfectly acceptable, then somebody spilled something on them but you don't know what it was, and now they have black spots and you are trying to figure out what the chemical was, based on the black spots it creates on zinc plated parts? We do have a thread on line here that says a spill of Dr. Pepper soda discolored plated parts. Good luck.
Regards,
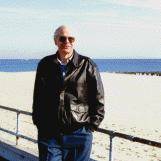
Ted Mooney, P.E.
Striving to live Aloha
(Ted can offer longterm or instant help)
finishing.com - Pine Beach, New Jersey
Q. Hello all
We are Automobile components, and our supplier performs Acid Zinc plated on Cast iron Surfaces.
We are facing the Issue of Black spots on the plating surface after 2 or 3 days. It is very difficult to judge whether current parts of Stock were OK, or if in the future they will get Black spots at a later time.
Can anyone suggest what are the precautions to be taken to get rid of Black spots and how to ensure that it doesn't occur.
- Gurgaon, Haryana, India
February 8, 2018
A. Hello R.,
Please consider retaining a consultant to visit your supplier's shop and resolve this. Alternately demand that the shop solve the problem or you'll take your business elsewhere; or send the parts out for salt spray testing, or require salt spray test results from your supplier. Best of luck!
Although Asif offers 11 possible causes, and although we can sometimes help a plating shop solve their problems, it usually takes a lot of back & forth, plus good access to details which your shop probably hasn't shared with you yet; unfortunately, it's hard to realistically suggest from a buyer's description of a problem exactly what the buyer should tell their plating shop to do next.
Regards,
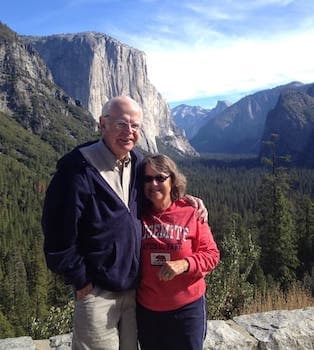
Ted Mooney, P.E. RET
Striving to live Aloha
(Ted can offer longterm or instant help)
finishing.com - Pine Beach, New Jersey
Q. We have been observing an issue in Acid Zinc Barrel Plated parts with trivalent clear passivation since last 2 years. Plating specification is 5.0 micron thickness minimum and corrosion resistance up to 75 hours.
During the receipt of material from plating, we check the parts for plating thickness, chrome thickness in XRF and check the parts visually by 100% to ensure no black patches/black spots.
We provide 24 hrs minimum for curing of plating before handling the parts for inspection and packing.
During packing of material, we do not find any black spots on the parts. The parts are packed in polythene bag with silica gel and put inside a carton box and sealed.
These parts are transported by Road in a truck for a duration of 5 days. When customer receives the material, we could see more than 50% parts appear with black spots. Requesting your help to come out from this issue.
Thanks & Regards,
Dinesh BabuSupplier Quality Engineer -- Chennai, Tamilnadu, India
May 28, 2018
A. Hi Dinesh. Five days on possibly rough roads sounds like -- and this looks to me like -- what is sometimes called "fretting corrosion".
You say the parts are packed in a polythene bag, but I'm betting it's not one part to a bag, and that five days of jouncing and vibrating against each other is rubbing away the chromate, irritating and hardening the surface of the zinc, and causing it to oxidize. I suggest leaving one of the carton on the dock instead of loading it on the truck, and seeing what the parts look like after that 5-day period.
If the carton left on the loading dock shows no black spots, my bet is that fewer parts per bag, some bubble wrap in the cartons, or some other practical measures that one of your people thinks up will easily solve this problem.
Regards,
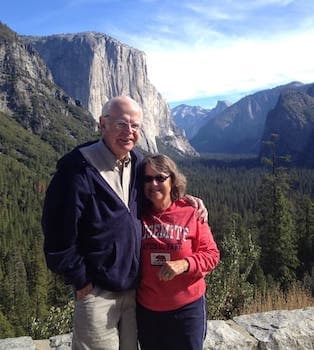
Ted Mooney, P.E. RET
Striving to live Aloha
(Ted can offer longterm or instant help)
finishing.com - Pine Beach, New Jersey
Q. Hi everyone,
We are automobile parts manufacturer,
Our supplier does acid zinc plating, about 13 to 15 microns on tube and brackets (10 mm dia. hollow tube). Recently we are having black spot issue on tube. Our supplier says it's due to tube material problem. After keeping it store for a few days we observed white salty surface which has black spots. Please suggest us the solution.
- Bangalore. Karnataka. India
July 28, 2018
A. Hi Mahesh,
To me, that looks like missing plating, not just black spots. This looks very much like a quality issue with the plating, rather than anything to do with the base material.
Have a look at other parts in the batch, is there any blistering on the surface? This would be an indication of poor preparation prior to plating.
Aerospace - Yeovil, Somerset, UK
A. Hi. I agree with Brian that this looks more like missing plating than black spots on the plating.
Four quick questions:
1. Are the pieces soldered or welded together before plating or plated separately?
2. The plating on the piece with the screw holes looks better; is it?
3. I assume the parts are steel, not brass or copper?
4. They are bent before plating, not after?
Regards,
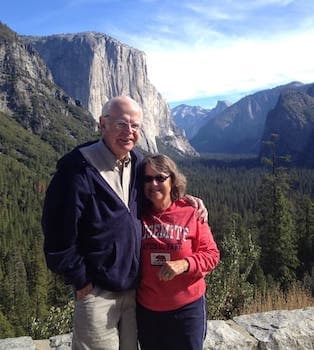
Ted Mooney, P.E. RET
Striving to live Aloha
(Ted can offer longterm or instant help)
finishing.com - Pine Beach, New Jersey
A. Hi Mahesh,
I saw black spot on part -- looks like to me real heavy smut that your cleaning process cannot remove. Then you plate over this parts causing black spots or plating layer may peel.
Try some part sand blasting, then run.
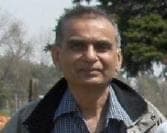
Popatbhai B. Patel
electroplating consultant - Roseville, Michigan
April 15, 2021
Q. I have 400 lit barrel plating, all parameters within control -- even still I am getting black spot on M12 bolt if voltage is kept above 5. If I am keep voltage less than 5, nut thread is not getting proper coating.
Bala subramaniEmployer - Chennai, TamilNadu, India
December 1, 2018
A. Hi Bala. Unfortunately there are all kinds of 'black spots', often with differing causes. If you can forward pics of the black spots we might have a better idea; also acid, alkaline, or cyanide plating?
But if you can plate a Hull Cell panel and show us or tell us what you get, it should be easier to figure this out. Thanks.
Regards,
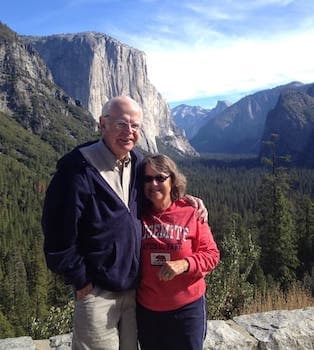
Ted Mooney, P.E. RET
Striving to live Aloha
(Ted can offer longterm or instant help)
finishing.com - Pine Beach, New Jersey
Q. I am getting black spots on threaded area of nuts, I have changed anodic cleaner and increased acid concentration of pickle -- please help.
- Ludhiana Punjab
April 2, 2021
A. PLEASE CHECK YOUR PRE-TREATMENT AS OIL RESIDUE LEFT IN THREADED PORTION LEADS TO THIS TYPE OF DEFECT.
DID YOU DEGREASE IN TUMBLER OR BY JUST DIPPING.?
IF YOUR SUPPLIER IS USING THICK OIL YOU HAVE TO DO FLASH PLATING AND DE-PLATE AND FOLLOW YOUR REGULAR PROCESS.
- PUNE MAHARASHTRA INDIA
Q, A, or Comment on THIS thread -or- Start a NEW Thread