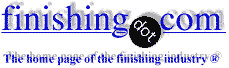
-----
Black spots on zinc plated parts with trivalent chromate
Q. Black dots on zinc plated parts after a week of plating?
We are doing zinc plating with trivalent yellow passivation, we are packing in poly cover and sending to our customer but, after a week time black dots found on plated surface. I want to know the root cause and remedy for this early reply will help me a lot.
Raghava Reddy- Bangalore Karnataka, India
December 4, 2020
A. Hi Raghava. This thread is just one of more than half a dozen , each with dozens of entries focused on the subject of black spots on zinc plating. You're welcome to search the site and study them, but if you would like your specific problem addressed please tell us whether you're doing acid, cyanide, or alkaline non-cyanide plating; rack or barrel plating; and what material the parts are made of so we can get beyond the cliches that the plating either is not thick enough/good enough or the parts were packed before they were truly dry :-)
Photos e-mailed to mooney@finishing.com for posting here will probably help.
Luck & Regards,
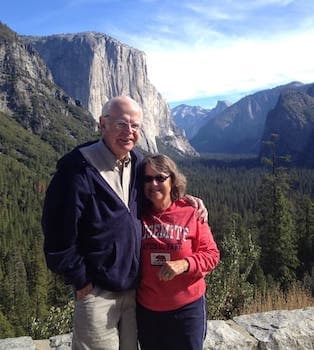
Ted Mooney, P.E. RET
Striving to live Aloha
(Ted can offer longterm or instant help)
finishing.com - Pine Beach, New Jersey
Q. Plating defect or raw or raw material defect?
The material is CRCA and plating done in rack and the thickness is 8-12 microns.
I have attached the snaps of a plating defect. It looks like white patches after plating but when I stripped the plating found the same issue; but before plating material was clear.
Raghava reddy [returning]- Bangalore Karnataka India
December 26, 2020
Ed. note: Apologies, Raghava, I don't know if I accidentally deleted your photos or you forgot to send them, but please email them (again?) to mooney@finishing.com.
You say "when I stripped the plating found the same issue". Do you mean those white patches were now visible on the stripped substrate? Or do you mean you replated them and had the same problem with the new plating?
We'd still like to know whether you're doing acid, cyanide, or alkaline non-cyanide plating, trivalent or hexavalent chromating, and to get some information about your cycle. We've already covered this over the years for various circumstances, but we have little about your particular circumstances to allow us to narrow that list. Thanks.
⇩ Related postings, oldest first ⇩
Q. I use zinc plating and blue bright chromating. But there are many black spots on the surface of our product. What should I do? What kind of trouble happened?
Thanks,
Mahfud [last name deleted for privacy by Editor]automotive manufacturer -Jakarta, Indonesia
2004
A. Hi, cousin Marfud. There are many different conditions that people call black spots, ranging from flea-size tiny pits to 1/4" dia. dark spots, so it would be a very big help if you attach some photos so we understand what you mean.
Sometimes, for example, it is iron contamination of an acid zinc plating bath (see our library article Improving Your Chloride Zinc Plating Operation) which results in "barrel print out", a dark spot pattern that echoes the hole pattern in your plating barrels.
But there are many possibilities. What are the parts? What is the alloy? Are they barrel plated or rack plated? Acid, cyanide, or alkaline non-cyanide zinc plated? Just trivalent chromated, or chromated and post-dipped? Has the line just started up, or have you been plating the parts for years? Are you sure the problem starts in the trivalent chromate step rather than the zinc plating step? Please try to give us some more input, and pictures if possible, and we may be able to help. Thanks!
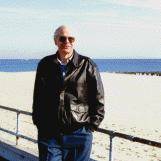
Ted Mooney, P.E.
Striving to live Aloha
(Ted can offer longterm or instant help)
finishing.com - Pine Beach, New Jersey
A. Black spots after trivalent chromate sometimes can be referred to as "cobalt marking". Japanese industrial standards and an International Organization for Standardization symbol of zinc plating have only criterion about white rust and red rust. Therefore, there isn't a criterion about black spots. It doesn't effect SST but it sure does need a fix. I have some questions about this matter.
1) Is this trivalent chromate new make-up?
2) Zinc plating condition? (Zn concentration, caustic soda ⇦liquid caustic soda in bulk on
Amazon [affil link]
concentration, thickness, impurity concentration)
When thickness of zinc is thin (less than 5 micron), corrosion resistance of trivalent chrome film deteriorates because there is derricking on the surface of materials more than 10 micron and when thickness of zinc is thin, a part remains as pin hole.
3) Drying condition after trivalent chromate?
- Jakarta, Indonesia
Multiple threads merged: please forgive chronology errors and repetition 🙂
Q. Has anyone seen black spots on zinc plating with trivalent clear chromates? We recently converted from hexavalent to trivalent and began seeing what appeared to be a white haze that turns into very small black spots. We use a silicate sealant over the chromate.
Gary ClyburnCaptive shop plating fittings - Dayton, Ohio
2006
? Is your zinc bath Alkaline or Acid Chloride? Rack or Barrel? Giving more details would narrow things down a bit.
JEFF W LENTZPlating Co. - Lancaster, Pennsylvania
A. Gary
There is a wide set of probabilities, which may or may not help. However..
A. If perhaps you are a cyanide zinc fan, the black spots are entrapped cyanide in porosities, bleeding out post-passivate and drying.
B. If you are an alkaline Zinc fan, try beefing up your post-plate nitric acid dip to ensure no caustic carry over into the trivalent passivate.
C. And if you happen to be an acid zinc fan, using a barrel here are 2 probabilities.
1. Your Current is too High and causes imprints of the barrel holes on the parts which is burning due to inability of solution to carry current. Check Zinc and Total chloride to data sheet levels. Reduce current.
2. If you run rack, it might be loose zinc particles co depositing and then corroding faster than the regular surface. (In alkaline zinc Rack too, such a possibility exists.)
Now Tell us what you do -- Rack or barrel; Cyanide acid or alkaline?
Regards,
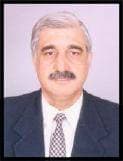
Asif Nurie [deceased] [deceased]
- New Delhi, India
With deep sadness we acknowledge the passing of Asif on Jan 24, 2016
A. Gary,
One more possibility exists.
Are you applying the Topcoat while the part is wet, or do you dry first, then Topcoat ?
If the second possibility is being followed, the parts will behave as described by you..
Check.
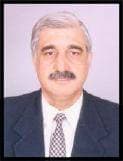
Asif Nurie [deceased] [deceased]
- New Delhi, India
With deep sadness we acknowledge the passing of Asif on Jan 24, 2016
2006
Q. Hi,
We are faced with black spots problem on Zn plated (15~20 microns) & trivalent chrome passivated (bright) parts. Black spots are appearing on surface within 24 hrs in salt spray test. Zn plating is getting done locally. They are following the following process: first components are cleaned with kerosene (scrubbing with saw dust), dipping in HCl, water rinsing, Zinc plating, water rinsing, passivation, water rinsing, drying.
I do not know much about plating. Can anyone help me to get out of this problem? Is trivalent yellow passivation better?
Production Manager - Hyderabad, India
September 22, 2008
A. Hi, Kunadha. I don't think kerosene is an adequate cleaner (plus, of course, it's very dangerously flammable). I think your plating shop should alkaline clean your parts. I'm not confident that that is the direct cause of the black spots (it could be iron contamination, the plating too thin, or something else), but there seems little sense in fine tuning the process until it's been roughly tuned with proper alkaline cleaning instead of kerosene :-)
In the old days of hexavalent chromating, yes, yellow passivation was better because it was thicker and higher in chrome content. But in these days of trivalent passivation, many "yellow" passivates are simply yellow dye added to the clear passivate. Good luck.
Regards,
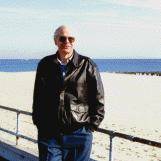
Ted Mooney, P.E.
Striving to live Aloha
(Ted can offer longterm or instant help)
finishing.com - Pine Beach, New Jersey
? HELLO SIR,
Are you doing acid zinc or cyanide zinc plating?.And what trivalent passivation you are doing yellow or blue? Tell clearly.
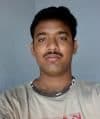
Shoban Kesarapu
plating chemicals supplier - Secunderabad, A.P., India
To Reduce the Failure Rate of Zinc Plated Components
September 27, 2008Q. 1. Most of my Suppliers are using Trivalent Zinc Technology for which sealant is mandatory to generate self repairing function. Now I don't have any procedure to cross check at my end whether the sealant was applied on the part or not. Please guide me how to check the presence of Sealant.
2. Also please reply for if Silicon has been added in Sealant in which form, Silicon-di-oxide or Silicon-tri-oxide.
3. As you know, during post treatment Zinc tends to dissolve in Passivation and the limit of Zinc Impurities has been given as 15000 ppm in Technical data sheet of Chemical Supplier. Now my query is How much ppm zinc dissolves in passivation bath by processing of one sq. ft area having 10 micron thickness of zinc coating.
4. My Plating Spec. is Thickness min. 8 µm and SST Life is white rust: 72 hours, and red rust:- 240 hours. Now please guide me for 4 years warranty: is the mentioned spec. right or do we have to enhance our spec?
5. Why do black spots usually occur before starting of White Rust during SST Testing of Zinc Plating? Is it due to the Co-deposition of Impurities along with Plating? If Yes, then how to control the impurities. Please guide me.
6. Why is Cyanide Zinc Technology banned for Plating. Is it possible to deposit cyanide with Zinc Coating on Components. If it is not, then why do we generally avoid the usage of Cyanide Zinc Bath. Please guide me.
two wheelers purchaser - Gurgaon, Haryana & India
A. Hello Mr Kaushik,
1. There is no hard and fast rule that a sealant must be used; most Chromates are of the self healing type with or without topcoats. It looks like you have been reading technical literature of a proprietary process that advocates this. Product Literature serves the interest of the product, I would only suggest that you use corrosion tests as usual.
2. Silica is not always automatically the best sealant material, I have found some polymers work far more consistently.
3. The dissolution of zinc may be up to a micron whilst Passivation; it depends on the total acidity, temperature, and dip time.
4. 72 hours to white rust will get you past one year without trouble in Central areas but not Coastal India. For Coastal areas you should target 240 hours to starting of WR. The mean corrosion rate in Coastal areas is about 3-4 microns a year quite easily.
5. Black spots are not impurities of plating but a natural by-product of chromate break down in a Salt Spray test. It doesn't happen in real world corrosion; only in a salt spray test, these are normally ignored.
6. There is no ban on Cyanide Zinc Plating; It is advisable to restrict use of Cyanide at the source, like it is advisable to restrict Hexavalent Chrome. If the use and disposal of cyanide is managed properly there is no ban that exists.
I conclude that you are meeting too many suppliers of Alkaline Zinc these days!
Warm regards,
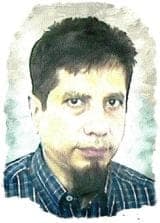
Khozem Vahaanwala
Saify Ind

Bengaluru, Karnataka, India
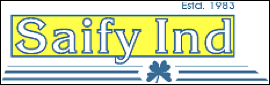
Wonderful response, KV, and the levity is appreciated. Thanks!
Regards,
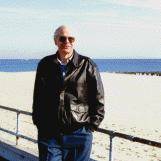
Ted Mooney, P.E.
Striving to live Aloha
(Ted can offer longterm or instant help)
finishing.com - Pine Beach, New Jersey
A. Hi Anil Kaushik,
My best suggestion is to use better (long lasting) trivalent chemistry with high iron and zinc tolerance (Zn 25 gm and Iron 300 ppm). This chemistry WITHOUT sealant will produce 160 plus Hrs in blue, 240 plus Hrs in iridescent towards white rust. Imagine that red rust will be over 500+ Hrs.
Black spot is due to poor cleaning, poor maintenance of plating chemistry and again low profile Trivalent chromates.
Yes cyanide is going out slowly due to environmental requirements. But Alkaline Cyanide-free process is available to do the needful -- much better way by various advantages.
Best Regards,
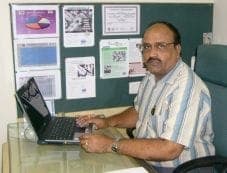
P. Gurumoorthi
electroplating process chemicals - Chennai, Tamilnadu, India
Q. Black spots observed on my Zn trivalent plated steel components along with white rust.
Voufique Qureshifirst timer - Mumbai, Maharashtra, India
October 2, 2009
Thanks for sharing!
Brian TerryAerospace - Yeovil, Somerset, UK
A. HI,
BLACK SPOT AFTER TRIVALENT CHROME , CHECK YOUR RACK CONTACT MAY BE BROKE AND HOLDING ACID . ANY ALKALINE CONDENSE DRIPPING ON THE PART OR HYDROCHLORIC AICD FUME OR HYDROCHLORIC ACID DRIP ON PART FROM YOUR WORK PROCESS.
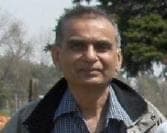
Popatbhai B. Patel
electroplating consultant - Roseville, Michigan
Black spots on Zinc plated brazed/hardened parts
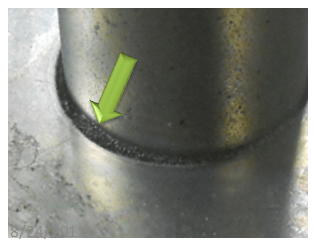
Why do black/purplish spots appear on Zinc plated, brazed and hardened parts?
I am a design engineer doing process engineer work, so bear with me as I describe the process:
2 Parts, Leaded cold drawn steel and 1050 steel
Parts oven brazed with copper, no flux
Heat treated to Rc40-Rc45
Hydrochloric acid cleaning, 10 minutes
Alkaline Zinc rack plate
Post baked 4 hours at 375 °F
Trivalent chromate for 40 seconds
The spots appear where the copper braze is, the fillet and areas where excess braze pools. They can be small in size to over a 1/4" (I have tried an acid zinc rack plate, which eliminated the black spots but there was poor adhesion). On inspection the black spots appear to be carbon? Any help?
Brent Sandstrom
- St. Paul, Minnesota, USA
August 24, 2011
A. Can you tell me: After Acid cleaning the problem area looks like? Has black powder? And what is the concentration of acid cleaning that you used?
If you have black powder, I suggest you clean it before plating.
As I know if you have good cleaning before plating, you will have less problems.
Sorry for my english if you read my message and not understand.
- Bangkok, Thailand
Q. Hello all.
I'm having a lot of problems with black spots (around 1-5 mm diameter) after zinc chloride bath in rack.
We have improved through installing more filtration, but root cause is not so clear to me.
Any idea on what is going on?
Thank you.
Process Engineer - Guadalajara, Jaliso, Mexico
November 23, 2013
Q. Sir,
We are getting Black patches and Spots during Salt Spray Test as per ASTM B117. Parts are Zinc Plated in non-cyanide Alkaline with Tri Chrome Yellow and Blue passivation. Require technical help.
- Jamshedpur, Jharkhand, India
February 24, 2014
A. Hi Arijit. Black spots during salt spray testing are not necessarily a problem, but please attach a photo or two and give us some data like how soon into the test they become evident, or how long the test is. Thanks.
Regards,
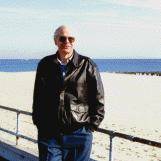
Ted Mooney, P.E.
Striving to live Aloha
(Ted can offer longterm or instant help)
finishing.com - Pine Beach, New Jersey
A. Dr. Sc. Mark Mertens of Enthone R&D, The Netherlands wrote an excellent paper entitled "Visual Degradation of Zinc Surfaces in Salt Spray Tests: Black Spots and White Haze." The paper is available in the Sur/Fin 2007 Proceedings (or you could get it from your Enthone rep). To summarize: Both black spots and white haze are normal characteristics of trivalent passivate behavior in the salt spray test. In my humble opinion, these should not be construed as failure unless the specifier specifically identifies them as such.
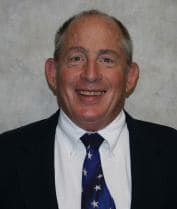
Tom Rochester
CTO - Jackson, Michigan, USA
Plating Systems & Technologies, Inc.

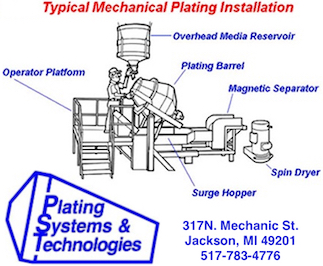
Q. I am facing problem of Black Spots during SST on Alkaline Zinc vat plating with trivalent passivation. Black spots are formed within 24 hours. Please suggest action ... where should I take actions?
RAMCHANDRA TALWANDEElectroplating of automobile parts - Aurangabad , Maharastra, India
September 30, 2015
by Larry Durney
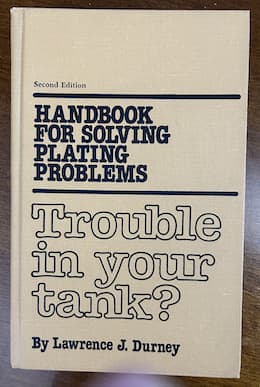
on eBay or Amazon
or AbeBooks
(affil link)
A. Hi Ramchandra. Thanks very much for giving us the facts of your case, but there are over a dozen previous postings with food for thought here ...
Rony, Khozem, and Tom have shared the knowledge that this probably doesn't represent failure; and Gurumoorthi suggests that the problem may be poor cleaning, poor bath maintenance, or a low-profile chromate. I have twice requested photographs to clarify similar discussions. Hopefully people can speak of the delay for you though. Thanks!
Regards,
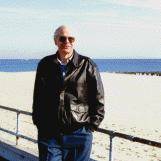
Ted Mooney, P.E.
Striving to live Aloha
(Ted can offer longterm or instant help)
finishing.com - Pine Beach, New Jersey
A. The delay in formation of the "black spots" is indicative of trying to apply typical weak solution trivalent chromate over an alkaline zinc film.
Make up a fresh 1/4%/vol Nitric Dip to neutralize the alkaline zinc, THEN try the tri-valent chromate.
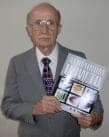
Robert H Probert
Robert H Probert Technical Services

Garner, North Carolina
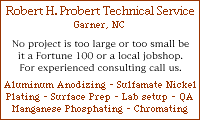
A. Many others, including myself, have seen this phenomenon in trivalent passivated acid chloride zinc and mechanically plated zinc.
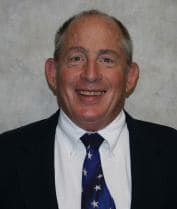
Tom Rochester
CTO - Jackson, Michigan, USA
Plating Systems & Technologies, Inc.

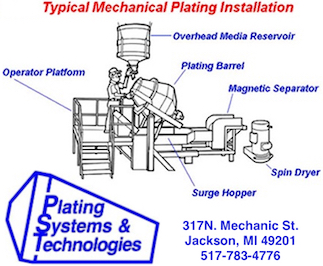
Q. Hi,
We are getting black spots on metal surface from zinc plating and trivalent chromate treatment process. We use barrel zinc plating to plate the metals. Out of 10000 pcs (17 mm diameter) of plated metal gaskets, about 15 pcs were affected by the black spots.
First, we clean the metals by degreasing process (includes acid HCl dipping; 20 kg of 30-40% HCl and 270 l of H2O). Next, zinc plating. Here is the description of the plating process:
chemicals:
ZnO: 42 gm/L
NaCN: 92 gm/L
NaOH: 38 gm/L
Brightener Asnite HT: 0.5 cc/L
H2O: 1800 L
plating time: 50 min
Room temperature
DC current: 250 A/ barrel
Last process is trivalent chromate process treatment (including nitric acid polishing, water rinsing, hot water rinsing, draining and drying)
The black spot is very small in size (about 1/6 of metal size). We are not sure what caused it. Is it because of poor cleaning of metal surface? The plating bath is cleaned every 10 days.
Any suggestion is much appreciated.
thanks
- Malaysia
December 7, 2015
A. Hi Tan,
It is possible these 10 pieces were stuck to the inside of the barrel during the plating process. Common with flat parts. This might be a high current burn or a barrel mark from iron.
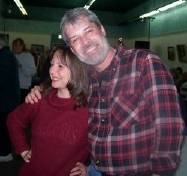
Trent Kaufman
electroplater - Galva, Illinois
A. Good day Tan.
I think Trent nailed the problem, regarding barrel plating. Parts will always "nest" with each other, or adhere to the interior of the barrel.
Either way, you have a 0.15% rejection rate, if your numbers are correct.
That is quite impressive for barrel plating.
I have barrel plated zinc belt buckles with CN Cu, acid Cu (which was a real challenge),Ni, brass.
I have found to add glass marbles to the 60 ft/2 load, as they do provide a measure of fill, to "break" up the load, reduce abrasion of the substrate, and provide a measure of burnishing ( lower brightener consumption), and they do not reduce the ASF requirements/consume metal.
I also modified the barrel, drilling a large "hole"( 6" dia.) in the side of the barrel side plate, and a series of consecutive smaller holes within the entire barrel side wall, to match up with the side plate "hole". I pumped filtered solution through this "hole", to maximize solution exchange, as barrel plating suffers with the exchange. This gave me higher ASF allowances, but the pH of the CN Cu went through the roof! The grocery store did solve the pH problem with an add of 1-2 L vinegar
⇦in bulk on
eBay
or
Amazon [affil link] (5% HC2H3O2) daily.
Hope this was helpful.
Regards,
Aerotek Mfg. Ltd. - Whitby, Ontario, Canada
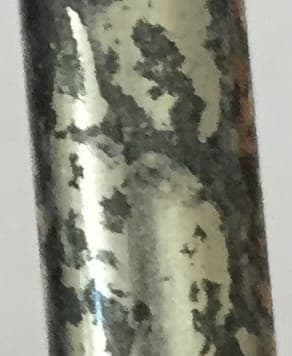
Q. We are manufacturing U clamps made from En8 material. These are then alkaline zinc plated and trivalent blue passivated. The customer specification is: thickness min 15 microns, and the plated part should pass a SST of 144 hours minimum for Red rust.
One such part was put in SST chamber and the part showed up black spot generation within 24 hours during the salt spray test. Could you please help by answering what could be the reasons for black spot generation and how we can avoid such a phenomenon? Also the customer is worried that he may have to recall the parts from his work site if these start failing on site.
Dhananjay Kadepurkar- Pune, Maharashtra, India
February 24, 2016
A. Hi Dhananjay. Please review the earlier entries on this thread, because most professionals consider "black spots" to be just an artifact of salt spray testing which does not constitute failure and will not happen in real life.
But I responded before I saw the graphic, and this is not what I think of when I hear of "black spots". I'll have to wait for someone more familiar with zinc plating of EN8 to offer an opinion of what we're looking at :-)
Good luck.
Regards,
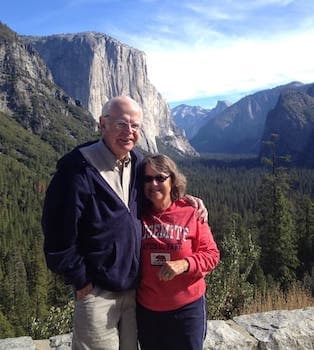
Ted Mooney, P.E. RET
Striving to live Aloha
(Ted can offer longterm or instant help)
finishing.com - Pine Beach, New Jersey
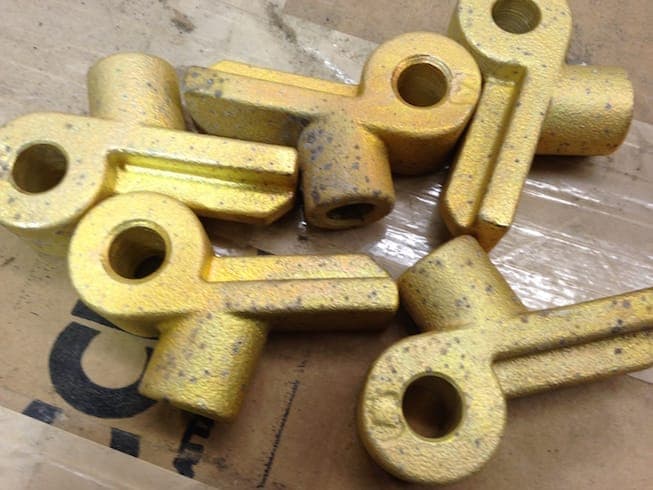
Q. Hello,
I am a Quality Technician for an Investment Casting Company and we have had parts stripped and re-plated with new yellow dichromate and there is the appearance of black spots and what appears to be mold looking spots, has anyone encountered this issue or know of the reasons why this has happened? We will now have to blast and re-plate again.
Terry Cisco
- Chattanooga, Tennessee, USA
April 1, 2016
A. BLACK SPOTS (BARREL MARKS) ARE FROM IRON BUILD UP IN ZINC BATH. CHECK FOR PARTS INSIDE (AT BOTTOM )OF ZINC TANK.
HERNANDEZ EDDIE- SAN ANTONIO, Texas
Q. We are experiencing the black spots in the Zinc plating with racked castings. They look great when they first come off the line and then the spots develop as they sit and dry/cure. We have 2 different cast suppliers as well as two different zinc platers and all parts end up the same. Can not find a common denominator in this problem other than the high humidity levels this time of year. This problem appeared last year as well but current plating shop changed their process a little and cleaned out the tanks with fresh chemical and problem went away. We determined last year is was silica left in the casting from the cast supplier not blasting good enough but now the problem is back. What are your thoughts and experience with RACK plated parts?
Sheila Onnen- Iola, Kansas USA
September 5, 2019
![]() |
A. After chromate, the plater must rinse back/forth/in/out/cold water/hot water at least three times to pump the salts that are trapped in the porosity of the casting. Line operators seldom understand this requirement on castings. ![]() Robert H Probert Robert H Probert Technical Services ![]() Garner, North Carolina ![]() A. I believe that the plater needs to leach the parts after plating, prior to the chromate being applied. This appears to be chemicals trapped in the porous substrate that are slowly coming out. John Johnson- Jamestown, New York USA |
Q, A, or Comment on THIS thread -or- Start a NEW Thread