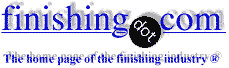
-----
Bright Dipping of Brass
Q. Hi, I'm a beginner and I had the pleasure of reading this very interesting discussion. I have some questions to ask you experts in plating and metal treatment.
Mr. Jim Conner proposes a mixture composed of:
25% acetic acid
⇦ on
eBay
or
Amazon [affil link] , 25% nitric acid and 50% phosphoric acid.
I don't understand these proportions. Let's say I want to make 1 LT of product. How should I adjust? Should I take my acids that have a higher concentration than required and dilute them and bring them to the required concentration and then mix them? And in what quantities?
Mr. Ed Budman (RIP) suggests a mixture of 85% by volume phosphoric acid and 15% by volume nitric acid. If he is referring to the concentration of the two acids, how much product should I take from the first and second to make 1 liter of product (it could even be a gallon)?
One last question to clarify my ideas, specific words are often used and I would like to understand what the differences are and when a treatment is right or not.
Activator
Pickling
Bright dipping
What I want to plate is essentially brass which I will work mechanically by polishing or shot peening with glass microspheres. Next will come the chemical part before plating. It is evident that many oxides will be removed mechanically. I also accept suggestions regarding degreasing. My idea is to use ultrasound, but I know for a fact that strong alkaline products are to be avoided with brass. What do you propose to me?
Thank you
- Poggibonsi Italy
December 21, 2023
A. Hi Marcello,
You probably can anticipate this first comment because you see it commonly on this site: "if you don't understand the measurement units people are talking about, you probably don't know enough to be working with those very hazardous chemicals". For example, if you spill a little of that nitric acid, how are you planning to wipe it up?
People really should have hands-on hazardous chemical training before working with this stuff. To tie that into your question about Ed Budman's and Jim Connor's comments: it is often unclear what units or purity or measurement method people are speaking of, and misinterpretations are commonplace, so it is best to have sufficient understanding and training that you don't do something really stupid based on a slipped decimal point or misunderstanding. But -- in general -- when people speak in terms of volume measurement they are probably not expecting you to use 100% concentrated chemicals, but the highest commonly available concentration. The phosphoric, nitric, and acetic acids are probably all of different concentrations. I think that's what Ed wanted, and Jim wants, you to use.
Moving on: when plating shops process parts they do not need to do the same primary "scale breaking" and "pickling" that a steel mill or foundry did. Rather, they use an acid to "activate" the surface by removing any light oxides so that the plating occurs on raw metal, not on oxide or tarnish films. But some people in plating shops will call this the "pickling" step. Because you will be blasting or polishing, "activation" is what you will be doing not any sort of primary pickling.
"Degreasing" is another piece of slang because the step is actually "cleaning". If you can afford the time to polish the parts, you can probably afford the time to clean them with a scrub brush, water, powdered pumice, and a dash of detergent rather than having to build a cleaning station and trying to formulate a cleaning chemical that will saponify, wet, emulsify, deflocculate, sequester, chelate, buffer, and inhibit :-)
So, blast or polish the parts, scrub them, rinse them, dip them in dilute sulfuric acid, rinse them, then plate them.
Luck & Regards,
Ted Mooney, P.E. RET
Striving to live Aloha
(Ted can offer longterm or instant help)
finishing.com - Pine Beach, New Jersey
⇩ Related postings, oldest first ⇩
Q. Hello everybody! I am currently bright dipping over brass parts. We have a very significant amount of rejects because of spots on the inside of the part (pocket shaped part). It is hard to tell before we bright dip if the part is going to be rejected or not, under microscope we can tell that the part before the bright dip is etched. Wherever we see the etching, is where the spot comes out after the process(bright dip). Changing oil is helping(stampings) has helped reduced the problem but we need to eliminate it completely since this part needs to be seam-welded after the bright dipping. Can some one help share with me the experiences and potentially help me eliminate this problem; we have had this problem for over 9 months now.
Alfredo F. GarzaBrownsville, Texas
1999
A. Dear Alfredo , I recommend that you contact Macdermid and look at one of their products called Kenvert K35 it is a chemical polish for Brass & Copper, they also have another product in the Kenvert range called K 30 PR which also works well but is Chromic Acid based. Without more technical information about the actual process you are using, it is very hard to give specific advice. Regards, J

John Tenison - Woods
- Victoria Australia
1999
Ed. note: Gentle readers -- This posting is quite old. We've since learned our lesson and we no longer post suggestions of specific brands or sources (huh? why?)
A. Are you using a leach pot in your rinsing after bright dipping? If not, try rinsing then dipping in a solution of about 2 lbs of caustic soda beads [caustic soda beads in bulk on Amazon [affil link] to 10 gallons of water, before a final hot rinse. Good Luck.
Phil Pace- Tulsa, Oklahoma
A. I am no expert when it comes to bright dipping of brass. Others could give a better answer if you listed the entire process with concentrations and temperatures. Also a better definition of your part and how you are racking it would help. Gut feeling is that you are not getting complete rinsing between the process tanks and a trace or film of the chemical is settling into a recess or low spot which is adversely reacting with the following chemical. Since the rest of the part is OK, it would be in the processing of the part as in agitation (solution flow) or rinsing. Stressed metal from forming could possibly be the problem. but I would expect the opposite side of the bad spot to be bad also if it were the problem. It could be a rough spot from the die that is holding the chemical also. No simple answer, a process of elimination. I would try one part at a time with different racking combinations to see if you could isolate the problem.
James Watts- Navarre, Florida
A. Here is a quick and efficient "old-time" bright dip for copper and brass. Make a mix of 85% by volume Phosphoric Acid, and 15% by volume Nitric Acid. Mix the two thoroughly. Use at room temp. When you put a part into it, as soon as the part becomes covered with fine bubbles - it is done! Although I would NEVER EVER recommend it, I have gotten my fingers in this solution and have had time to rinse it off before any burning was ever felt. This can make copper, "new penny bright." Good luck, and remember to treat the chemicals properly and with respect. Used carelessly they can injure, and cause safety issues.
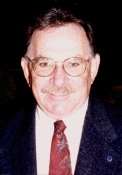

Ed Budman [deceased]
- Pennsylvania
With deep sadness we advise that our good friend Ed passed away Nov. 24, 2018
A. The bright dipping of brass really depends on the alloy. Leaded brass in the phosphoric/nitric mixture will pit.
I used to find that the phosphoric/nitric mixture worked best ... electroclean/water rinse ... dry. In some cases water on the surface will add to a etched surface. I would submerge the part in the bright dip solution (room temp) until fully covered then hold the part in the air until it was foaming from the chemicals (good ventilation required regardless of method) then follow with a complete water rinse until all visible signs of bright dip are gone -- might be a minute. Pull this out too soon and you will etch the surface unevenly as the phosphoric's viscosity will remain on the surface of the part. A 70 °F and warmer rinse would really helped.
Electrocleaning is a better alternative if it's just for plating purposes.
Todd huehn- coon rapids, Minnesota
1999
A. For good shine on blackened brass material, try 58% of nitric acid with some common salt.
Poonam chari- Maharastra India
April 8, 2010
Q. Hello again,
We have been asked to brighten Brass Key pairs and provide an anti-tarnish which will last for at least one or two years after our customer has manufactured and shipped the final lock assembly from India to USA.
We are presently Barrel Nickel plating and then wiring and gold flashing the brass keys. We have tried an electropolish followed by lacquering in an acrylic lacquer which does not work well on account of the key being supplied to us in pairs of two which causes problems like shadowing in electropolishing. Is there nothing else we can do but continue with Nickel/ Gold?
We are also not happy using conventional Nitric sulfuric bright dips on account of our wish to retain our lungs. In such a situation can anyone help us with a stable process to mass bright dip these keys and effectively anti-tarnish also.
For people outside India who are kind enough to assist; may we request for non proprietary solutions as bringing proprietary chemicals from outside India is next to impossible.
Many thanks in advance for your time and assistance.
Regards,
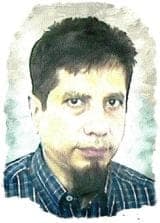
Khozem Vahaanwala
Saify Ind

Bengaluru, Karnataka, India
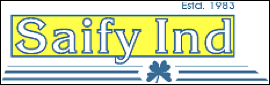
1999
A. Hello Khozem....I agree that the nitric acid based bright dips are rather nasty to work with as well as to treat. A good alternative is 25% acetic acid ⇦ on eBay or Amazon [affil link] , 25% nitric acid and 50% phosphoric acid. Warm it to 130-150 °F. This doesn't produce the deadly orange cloud we all know and love. It is also harder to over-etch the surface. The parts should be dry to avoid etching.
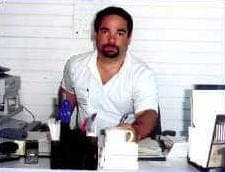
Jim Conner
Mabank, Texas USA
Dear Mr Jim Conner,
Many thanks for your special recipe, It really works well!
However we found that in normal room temperature of about 25 °C it works fine, But when we heat to about 50 °C we get reddish patches, so we're content using it cold. Any advice as to how long the bright dipping should take?
Thanks again and best wishes in advance for Christmas.
regards
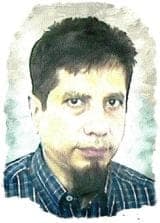
Khozem Vahaanwala
Saify Ind

Bengaluru, Karnataka, India
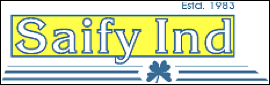
A. An alternative is to use 8 to 16 oz/gal chromic acid with 15 to 25% by volume sulfuric acid. Also proprietary materials are available.
Gene Packmanprocess supplier - Great Neck, New York
2000
A. Hi Khozem. As for preserving the finish once you obtain it, a dip in sodium benzotriazole
⇦ on
eBay
or
Amazon [affil link]
before brass lacquer might be ideal.
Luck & Regards,
Ted Mooney, P.E. RET
Striving to live Aloha
(Ted can offer longterm or instant help)
finishing.com - Pine Beach, New Jersey
Chemical polishing of brass
Q. We are in the field of ion plating (TiN + Gold) watch cases, straps, etc. Brass components tarnish in a couple of days after buffing bright. We would like to restore and improve the brightness before ion plating by chemical dipping. Looking for an easily available (in Bangalore) chemical or some chemical that can be cooked up without hassles!
H.R. Prabhakara - ConsultantBangalore Plasmatek - Bangalore Karnataka India
2003
A. Hi Prabhakara. Sodium benzotriazole is used as a preservative on record and CD masters and other brass and copper components and I don't think it will interfere with your ion plating process.
Luck & Regards,
Ted Mooney, P.E. RET
Striving to live Aloha
(Ted can offer longterm or instant help)
finishing.com - Pine Beach, New Jersey
A. It is possible to procure a brass bright dip from a plating supply house in Chennai that will brighten the brass base metal.
The part will need to be cleaned prior to dipping and rinsed well after the dip.
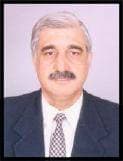
Asif Nurie [deceased] [deceased]
- New Delhi, India
With deep sadness we acknowledge the passing of Asif on Jan 24, 2016
Q. We manufacture free machining brass parts (360FC Brass), which we need to deburr. Because there are critical valve seat surfaces in these parts, we are considering thermal deburring.
The parts come out satisfactory, except for dark oxides on the surfaces. Since this part is used by a very particular customer for oxygen, we need to remove the oxidation from the thermal deburr operation. Is there a simple bright dip solution that will clean this oxidation without deep etching or pitting, and leaves no organic residue on the surface?
I have tried 20% phosphoric acid at room temperature and it seemed to do a great job after about a 1 minute dip. Is this a practical solution over time? What happens to the solution and what means should I employ to neutralize and dispose of the solution if / when it no longer is effective?
Jeff GotthelfEngineering - St. George, South Carolina, USA
2004
A. Jeff
The Phosphoric acid will need to be discharged per EPA regulations and the heavy metal in chemical form too.
Alternatively go for a Proprietary Peroxide based bright dip which leaves behind a very cosmetically appealing finish while creating a metallic powdery sludge which is metal, not chemical. Hence disposal is very simple, sell the sludge to a recycler. The chemical breaks down into slightly acidic water due to tiny sulfuric acid adds for pH control.
Regards,
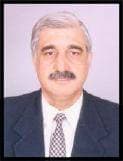
Asif Nurie [deceased] [deceased]
- New Delhi, India
With deep sadness we acknowledge the passing of Asif on Jan 24, 2016
A. There are a number of commercially available deoxidizers for copper and their usage depends on the final degree of brightness required. The maximum brightness can be obtained by using a peroxide based chemical polish which provides excellent luster and has good shelf life against further oxidation. This solution, when spent, is very easy to waste treat and remove copper metal.
Other non-peroxide processes will remove darken oxides but will not further brighten the surface. These processes generally require an anti-tarnish post dip to prevent further oxidation.
Regards,
Dayton Dailey- Lake Zurich, Illinois, USA
Q. I am evaluating Peroxide/Sulfuric as a bright dip for brass and need an inhibitor to slow down the dip. What are good candidates?
Frank WhitmoreSr. Chemist - Lonoke, Arkansas, USA
2004
A. Hi. You can buy that product as a proprietary which also includes a reagent to slow the peroxide's tendency to spontaneously release.
Regards,
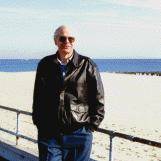
Ted Mooney, P.E.
Striving to live Aloha
(Ted can offer longterm or instant help)
finishing.com - Pine Beach, New Jersey
Q. We are currently using a Nitric Acid Brite Dip tank process to post clean copper, brass and copper/brass silver-brazed parts. Our plant manager would like to eliminate this process and replace with a non-toxic version, and to prevent excessive metal removal. Is there anything out there that will accomplish the same without very caustic chemicals? We do some acid brite dipping prior to brazing for cleaning purposes.
Matt DingeldeinWelding Equipment Manufacturer - Beecher, Illinois, USA
2006
A. It's hard to say whether it would work for your mix of parts, Matt, but sulfuric acid plus hydrogen peroxide is substantially less toxic than nitric acid.
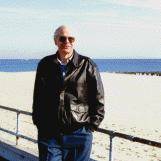
Ted Mooney, P.E.
Striving to live Aloha
(Ted can offer longterm or instant help)
finishing.com - Pine Beach, New Jersey
A. Instead of sulfuric or nitric acid you can use (maybe ... you must try) acetic acid /hydrogen peroxide solution (3 parts peroxide 3% ⇦ on eBay or Amazon [affil link] to 1 part vinegar ⇦in bulk on eBay or Amazon [affil link] /5%). Hope it helps and good luck!
According to some other sources even hot 10-25% citric acid ⇦ on eBay or Amazon [affil link] can be used. Hope it helps and good luck!
Goran Budija- Cerovski vrh Croatia
Q. Dear sir,
We are doing bright dip process on Brass and copper parts at sub contractor.
We observed black marks on those parts. Can you please give the detailed process of bright dip on Copper and brass.
- Chennai, Tamilnadu, India
June 9, 2012
Q. Hello everyone, I am looking for some information on Bright dip. We are currently induction brazing a series of copper tubes into a brass forging and the copper is oxidizing and turning black we were able to bright dip the parts and remove the oxidation.
Now I am looking for technical data to get the process approved with our customer.
What exactly is bright dip?
Exact Chemicals used?
Exact Process?
Exact chemical reaction with the part- intended Exact chemical reaction with the part - unintended reaction with copper, Brass Silver solder?
Would anyone know where I could find a resource to answer any or all of these question?
Thanks Steve
- Bloomington, Minnesota
June 20, 2012
A. Hi Steve. My understanding is that a bright dip for brass requires an oxidizing acid because copper does not readily dissolve in mineral acids. There are a wide range of different bright dips available, so unfortunately the readers are not going to know what you used. One of the more popular approaches is a mix of sulfuric acid and hydrogen peroxide, where the peroxide is the oxidizing agent, and this is available as a proprietary with stabilizers added which slow the spontaneous decomposition of the peroxide. But there are other bright dips based on nitric acid. And there are some discolorations that seem resistant to any bright dip except chromic acid. Better are proprietary mixes rather than home brews, and if you can find out what was used, your customer may already be familiar with it. Good luck.
Regards,
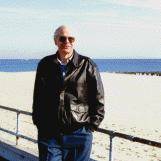
Ted Mooney, P.E.
Striving to live Aloha
(Ted can offer longterm or instant help)
finishing.com - Pine Beach, New Jersey
Q. I was wondering if staining/ etching is the only possible detrimental effect of bright dipping brass; are there any known chemical / physical changes that could be encountered?
Ruth Zelaya- Clifton, New Jersey, USA
September 12, 2012
A. Hi Ruth.
I'm not quite sure if I'm following properly, but bright dipping is only a surface treatment, and it should have no effect on the bulk of the metal. If done improperly it could somewhat etch or pit the substrate though.
Regards,
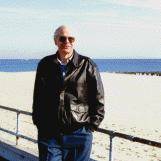
Ted Mooney, P.E.
Striving to live Aloha
(Ted can offer longterm or instant help)
finishing.com - Pine Beach, New Jersey
Pink Surfaces from Dichromate Brite Dipping of Brass
Q. Approximately 2-3 days after rinsing our parts in a solution w/ 50 lbs of sodium dichromate, 105 gallons of water, and 5 gallons of sulfuric acid, we are noticing a pink coloration on some of the parts develop. We believe that this could be due to dilution of our solution after completing multiple orders, however, we do replenish the solution approximately once a week. Could the dilution be the issue causing the pink surfaces, or is there another aspect to our process that we should adjust? Thank you for any advice!
John NurneyQuality Engineer - Burlington, North Carolina, U.S.
March 19, 2014
A. Have you considered the possibility of an immersion copper deposit? It may be that the copper concentration has increased too much.
Lyle Kirmanconsultant - Cleveland Heights, Ohio
Q. We think that is the main problem in that our brass forgings have higher copper concentrations than parts machined from bar stock, because I believe we primarily see the issue with our forged parts. Now, we are just trying to determine if we need to adjust our dichromate solution, or either of the other two acid solutions, to prevent this from occurring.
John NurneyQuality Engineer - Burlington, North Carolina, U.S.
? Please tell me what kind of brass you are using.
Regards,
- istanbul Turkey
October 26, 2014
Q. I have an historic building with steel casement windows. The handles are brass and 90 years old. Clearly I am small scale to you all, but am looking for a simple and safe chem dip to deoxidize the brass so it can be buffed and clear-coated.
Any thoughts?
General Contractor - Palo Alto California
November 30, 2014
A. Hi Steve. If the handles are not removable from the steel windows, I don't think chemical treatment is practical; then you might try buffing with a more aggressive polishing compound. If they are removable, most plating shops should be able to bright dip them for you if you wish. If you'd rather do it yourself, and you feel you are qualified to work with acids and oxidizing agents, there are suggestions above -- and Goran's idea for dilute acetic acid plus dilute peroxide sounds interesting to me, and safer than the alternatives. Good luck.
Regards,
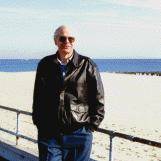
Ted Mooney, P.E.
Striving to live Aloha
(Ted can offer longterm or instant help)
finishing.com - Pine Beach, New Jersey
A. citric acid is a very effective and safe way to remove tarnish from brass. If you want to do it in place rather than by dipping, there are products that will let you do this. (They are sold as stainless steel passivators, but they work for brightening brass all the same!)
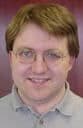
Ray Kremer
Stellar Solutions, Inc.

McHenry, Illinois
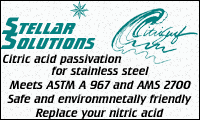
Q. I request you to suggest solution for getting shining (consistent) finish on brass and copper components .
We are cleaning brass and copper components as under
1-cleaning oil and other dirt in tub having kerosene and than cleaning with dry wood saw dust.
2-cleaning with water to remove wood dust
3- dip in nitric acid mixed with two parts of water
4-dip in chromic acid flakes dissolved in water (100 gms flakes in 3 litter of water
5-rinse in water to clean excess chromic acid solution
6-dry in open sun to clear water on the components
in above process we are getting inconsistent shine on components
Can you suggest any change in above by using some other chemicals
ass'y for electrical industries - mumbai India
February 20, 2017
Q. We currently use a distributor that doesn't offer much technical help when it comes to their immersion solution for polishing brass. I'm not sure if it's okay to ask, but have any of you had this problem? And have you had better luck with other vendors/homebrew solutions?
Thomas SwanPlating supervisor - Portland, Oregon
January 12, 2019
----
Ed. note: Hi Thomas. It's fine to ask for home-brew help, procedural suggestions, whatever. The only thing we don't post is suggestions/slams of specific brands and vendors (huh? why?)
One answer to the question of which brand/vendor of process chemistry is best that I often hear is: "the brand with the best local serviceperson". In my experience it is rather common that when a good local serviceperson changes employers, many of the shops he/she was servicing soon change over to the brand/vendor he/she now works for :-)
A. IMHO. If your distributor is not the manufacturer (as is implicit in your terminology) then ask the manufacturer for technical support. If neither the manufacturer or distributor can help you neither one deserves your business unless you are a very small shop.
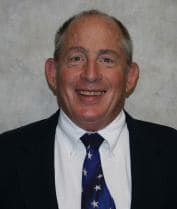
Tom Rochester
CTO - Jackson, Michigan, USA
Plating Systems & Technologies, Inc.

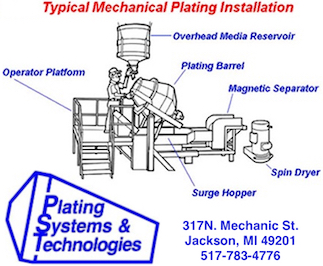
Q. We work on Leaded Brass. Copper content ranges from 57% to 61% and lead content ranges from 1.8% to 3.7%.
Post production we do nitric acid wash to provide product attractive aesthetics. But, more often we notice that after few days dark color spots like water marks appears on the surface of product. This seems very ugly and disturbs the appearance of product. However, it does not harm part's practical feasibility.
Could anyone please assist me on how to improve process so as to get rid of these dark water marks which is evident on surface after few days of nitric acid wash.
- Gujarat, India
March 19, 2022
A. Hi Arpit. Are you rinsing in deionized water? If not, you should. Even still bare brass will discolor over time, and it may be a vain hope that it will proceed uniformly, rather than start in spots which are 'different' for one reason or another such as not as cleanly rinsed, slightly different composition in this area, a galvanic hotspot due to stress, fingerprints after treatment, etc.
It's probably best to use benzotriazole to maintain brightness, plus a lacquer or clearcoat of some sort.
Luck & Regards,
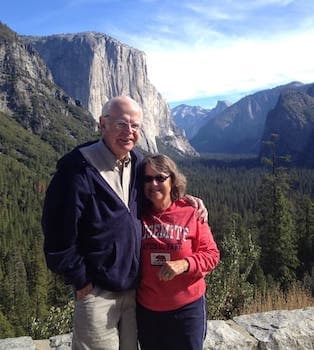
Ted Mooney, P.E. RET
Striving to live Aloha
(Ted can offer longterm or instant help)
finishing.com - Pine Beach, New Jersey
Q. We work on Leaded Brass. Copper content ranges from 57% to 61% and lead content ranges from 1.8% to 3.7%.
Post production we do nitric acid wash to provide product attractive aesthetics. But, more often we notice that after few days dark color spots like water marks appears on the surface of product. This seems very ugly and disturbs the appearance of product. However, it does not harm part's practical feasibility.
Could anyone please assist me on how to improve process so as to get rid of these dark water marks which is evident on surface after few days of nitric acid wash.
- Gujarat, India
[editor appended this entry to this thread which already addresses it in lieu of spawning a duplicative thread]
Q. Hi. We are covering in the field of textile buttons and accessories. How can I polish brass and copper products using chromic acid and sulfuric acid? What is the formula?
Thanks.
chemical engineer - BURSA TURKEY
March 13, 2023
A. Hi Ahmet. Gene Packman answers that question above. Good luck.
Luck & Regards,
Ted Mooney, P.E. RET
Striving to live Aloha
(Ted can offer longterm or instant help)
finishing.com - Pine Beach, New Jersey
Q. Thank you for your help. but I have a problem. When I mix chromic acid and sulfuric acid, it initially shines the brass and copper, but as the mixture cools, it dulls the brass and copper. Where am I going wrong?
Ahmet Davut [returning]chemical engineer - BURSA/TURKEY
Q. Hello. Is there anyone who can help?
Ahmet Davutchemical engineer - Bursa/TURKEY
April 5, 2023
Q. HOW TO POLISH COPPER USING COLD CHROMIC ACID AND SULFURIC ACID?
Ahmet Davut- BURSA TURKEY
April 24, 2023
A. Hi again. That solution is intended to be used cold rather than hot. The Canning Handbook ⇨
suggests 6 oz/gal Chromic acid, and 9 fluid oz per gallon of commercial sulfuric acid (sp. gr. 1.84) -- a little lower concentration than Gene suggests.
Is it possible that you are expecting this solution to deliver a full bright shine when that is not its intention or capability? The Canning Handbook says: "This solution is more restrained in its action than aqua fortis, but does not impart so bright a finish".
Maybe process some product through the chromic-sulfuric tank, then take it to the lab for some small scale experimentation with a sulfuric acid and peroxide mix? Although I would suggest that you use a proprietary sulfuric-peroxide bright dip, if it is not available, see Nigel Gill's detailed instruction on thread 49844.
Luck & Regards,
Ted Mooney, P.E. RET
Striving to live Aloha
(Ted can offer longterm or instant help)
finishing.com - Pine Beach, New Jersey
Q. Thanks for your help. Could you please write these ratios by converting them to g/l? Thank you.
Ahmet DavutChemical engineer - Bursa TURKEY
April 28, 2023
Q, A, or Comment on THIS thread -or- Start a NEW Thread